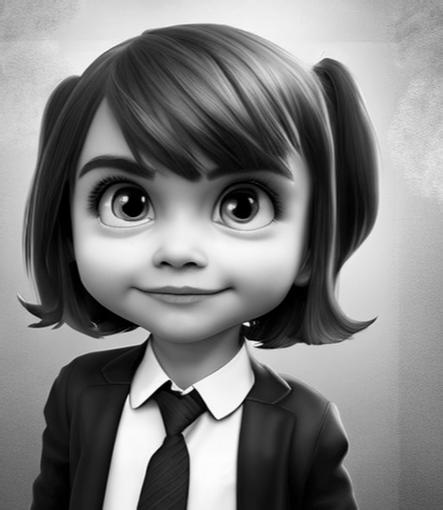
3 minute read
How to add aI art...continued
and after you pay for the hardware, there’s no additional cost. That said, it can be tricky to coax it to giving you the style you’re looking for. And of course if you need customer support, you’re on your own.
Option 3: Magic Canvas
Finally, there’s Magic Canvas. Magic Canvas is part of the Glowforge App available with Glowforge Premium, so while you’re building your favorite designs, you can easily generate personalized artwork. (It’s a great way to add a special touch to gifts.)
It’s fast, and you can make an unlimited number of images, with art styles that are designed for laser engraving. It also includes an image editor that lets you tweak the results like sharpening, contrast, and brightness before you print. Alongside Magic Canvas, you get all of the additional features of Glowforge Premium, including millions of fonts and images, plus thousands of ready-toprint designs.
The only drawbacks are that you have to own a Glowforge, and Magic Canvas only generates one image at a time.
Obviously I have a favorite. I subscribe to Midjourney and I’ve installed Stable Diffusion on my computer, but I use Magic Canvas the most because it’s the fastest path to something I can use. For example, last night I made ten co-workers custom-engraved notebook covers. I just typed their title into Magic Canvas, chose the “super cute” art style, and got back hilarious cartoon images. (My “CEO” image is below.)
That’s the power of AI-generated images: with a few words and in just a few seconds, you can have unique art that’ll elevate your laser work from good to great. It really is a magical tool, and I hope now you’ll feel ready to use it!

Dan Shapiro is the founder and CEO of Glowforge. Prior to starting Glowforge, Dan launched a variety of companies, including the best-selling board game, Robot Turtles, where he learned the joys and challenges of using complicated laser technology to create unique prototypes. Dan saw the major potential of bringing a beautiful, user-friendly laser to the market, and the idea for Glowforge was born. Follow Dan on Twitter
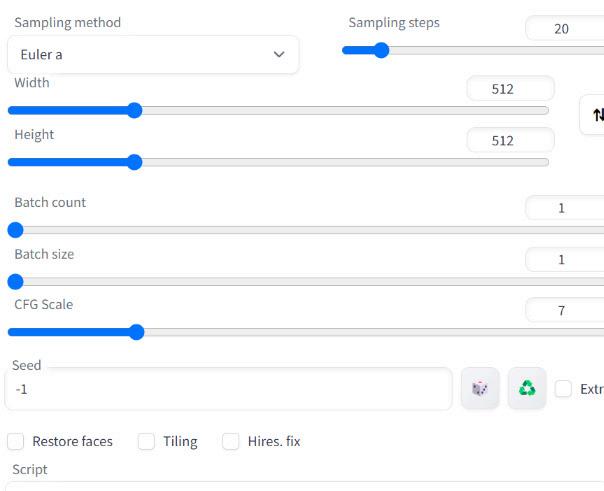
GUEST CONTRIBUTOR: Melody
Do you want to add color
to your laser projects, but don’t know where to start? Are you tired of paint filling your acrylic sheets, or just want more detailed prints? Read on to learn about sublimating acrylic and why it may be an option for you!
First things first, what is sublimation? At the core of sublimation and for our purposes, it is a chemical process that embeds ink into our substrate (acrylic) by using heat and pressure. You will likely want to invest in a heat press if you don’t already own one. (Personally I collect machines like I collect acrylic – a lot!)

Okay, so what else do you need? Sublimation prints- you can purchase a printer and make your own, or, and I would recommend this route- start by purchasing prints from someone on Etsy or another maker so you can test it out first and find out if this is for you before you invest in more expensive equipment.
And then of course you’ll need acrylic. But what kind of acrylic? The AWESOME thing about acrylic is that most any cast acrylic is sublimation friendly. There are no special coatings, no lamination to apply, nothing to do besides buy the acrylic you already purchase. And while most cast acrylic will sublimate, the results will
MATERIALS: Laser Beams and The Art of Sublimating
vary based on the acrylic color. I would stay away from darker colors and stick with light & bright for the best results!
The two biggest things I want to note here- 1) Clear acrylic will sublimate with a transparent image, and 2) not all white acrylic is the same. There are varying degrees of opacity within the range of acrylic sheets sold as white. For best results look for a 3015 white from your supplier as this is the industry standard most opaque. The more opaque, the less light comes through and the brighter your design will sublimate.
Alright so we have all of our supplies, what’s next?! Turn your heat press on and set it to 375-400 degrees Fahrenheit. This is really where you’re going to have to start getting comfortable and testing it out on your own. Trial and error is going to be your friend for finding the best settings for you- including pressure. I prefer high but have heard many have success with a lower pressure point. My recommendation is always to start low and work your way up!
While your press is heating up, if you haven’t already, I would suggest cutting your designs first. One of the biggest issues