
PLANNING
ARCHITECTURE
ENGINEERING
INTERIORS
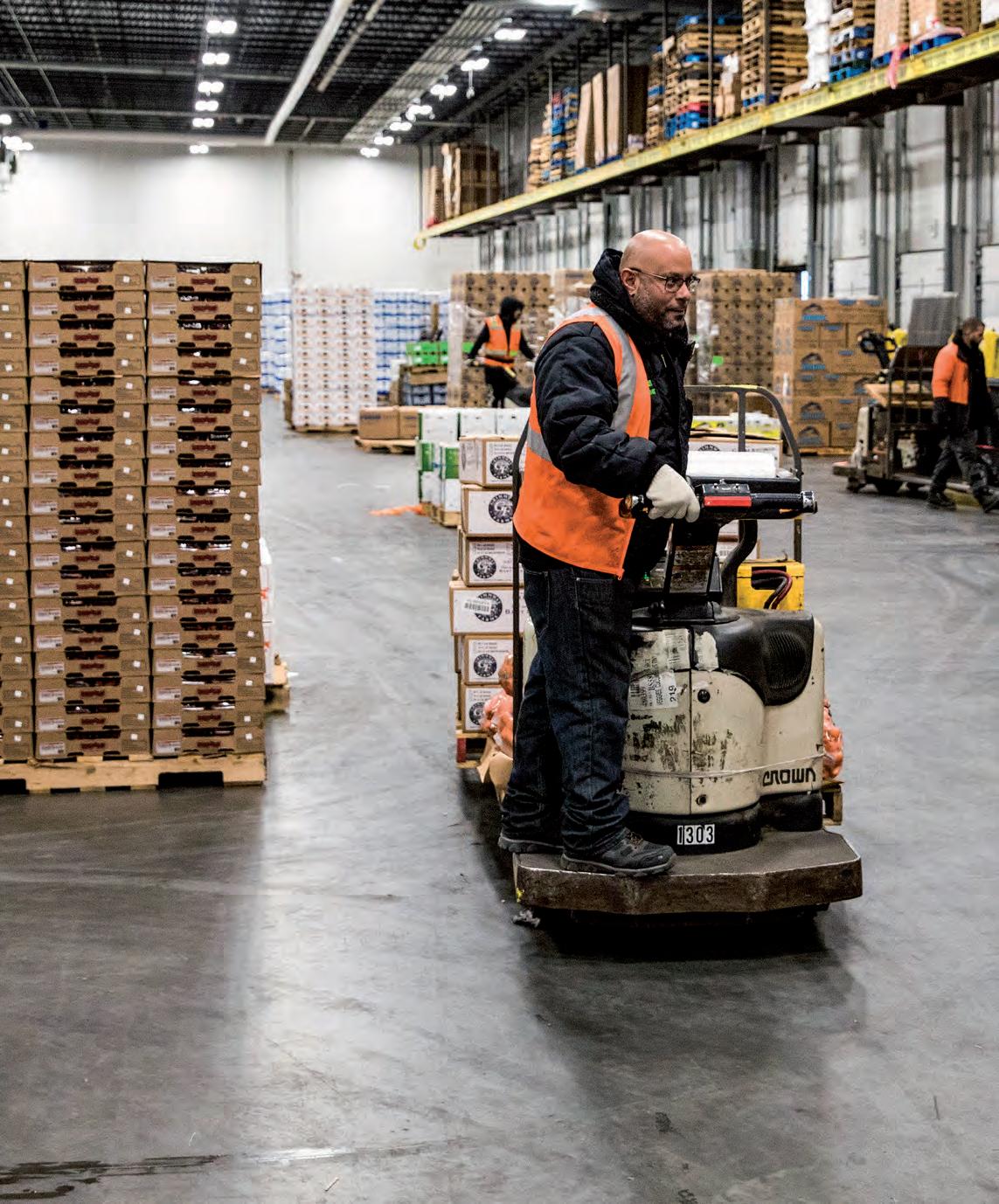
PLANNING
ARCHITECTURE
ENGINEERING
INTERIORS
For over 100 years, LEO A DALY has applied design thinking to solve the toughest challenges of our clients. Today, that means leveraging an international team of experts across design disciplines to keep logistics networks healthy.
COVID-19 has put new stresses on the global supply chain. Creativity and speed are needed to meet the facility needs brought on by skyrocketing e-commerce demand, emergency infection control measures and shifting manufacturing needs. Planners and engineers will need to work quickly with owners, contractors and government organizations across the nation to retrofit and expand logistics capabilities.
LEO A DALY offers a unique combination of skills and capacity in this effort.
• Our whole-team approach combines planning, architecture, engineering, interior design and program management to tackle complex problems at every scale, quickly.
• Our food, distribution and manufacturing design practice is deeply specialized in refrigeration engineering, food safety and infection control.
• Our experienced planners can evaluate, advise and implement upgrades and expansions to existing and new sites, even remotely.
• Our nationally integrated firm has the capacity to surge on multiple, complex task orders and deliver the right expertise, fast.
LEO A DALY has a long history of helping clients respond application of design resources.
Immediately after 9/11, we helped TSA plan and deploy across the U.S. under an extremely short deadline. Following Department of Veteran Affairs bring back the storm-ravaged
Responding to huge, complex challenges with an organized, ready to do it now as the supply chain adjusts to meet
At our core, LEO A DALY specializes in design thinking, and approach to problem solving focused on defining, iterating and testing solutions to slippery problems. This attitude permeates our approach to every project, regardless of scale or building type.
Design thinking places us in an advisory role, supporting clients before traditional professional services begin and after they end. We apply a broad array of tools and techniques to help our clients think first and think better, establishing project goals, defining requirements and optimizing performance. After project completion, we’re there to validate target performance and evaluate outcomes to direct future projects.
Our trained architects and engineers have provided facility condition assessments for millions of square feet of facilities across the United States. We go beyond simple observations to improve operations and efficiencies of equipment, systems and spaces.
LEO A DALY’s approach to the facility condition assessment process is best-in-class. This means that we will help clients collect information that will be useful long after the “boots on the ground” field work is complete. Our deep knowledge of building systems allows for confidence in moving forward into the planning and prioritization phase of the work.
respond to crisis situations with a massive, sustained
deploy security improvements in 447 commercial airports
Following Hurricane Katrina, we helped the U.S. storm-ravaged Biloxi Medical Center and Gulfport facilities
organized, creative response is what we do, and we’re meet new demands.
Beyond the drawing boards, LEO A DALY actively leads in the development of codes, standards, and best practices used throughout the world. We use this experience to our clients’ benefits, creating high performance spaces that are healthy, resilient and competitive. Our projects are used by Fortune 100 clients for research and development, production and manufacturing activities in a range of industries.
Our food distribution and manufacturing experts understand the facility needs of a rapidly changing supply chain. The COVID-19 crisis has accelerated the need for on-line fulfillment and the urban infrastructure to support it.
Adaptive reuse expertise allows us to quickly repurpose non-industrial facilities in urban locations as rapid-response fulfillment centers. Creative site selection and fast action will be critical to meet growing e-commerce demands.
Eliminating cross-contamination and touch-points is central to our design approach. Additional facility and operational changes can help control the flow of people and materials, limiting the spread of pathogens within facilities.
As FDA and USDA roll out new regulations to fight infection, our knowledge of food handling, packing and safety protocol gives us a head start on meeting new requirements quickly.
Spiking demand for fresh food delivery has created the need for additional refrigeration capacity. Our refrigeration engineering expertise delivers innovative solutions to meet facility needs and keep existing facilities running strong across the supply chain.
As needs change, good planning will help minimize disruptions and bottlenecks in trucking and operations flow. Our civil engineering and planning experts provide design thinking to maintain a well-functioning site.
Our teams include every specialization needed to deliver design quickly with minimal coordination. Planning, architecture, engineering, interior design and program management are part of every project from the beginning. We work together in one model for maximum coordination.
Digital design, reality capture and virtual reality allow us to minimize site visits and in-person meetings while delivering the same high level of design expertise. You and your employees will stay safe by limiting or eliminating additional guests in your facilities.
With 30+ offices around the world and a wide network of local partners, we deliver international expertise with local understanding everywhere it’s needed.
LEO A DALY revolutionizes food, manufacturing, and distribution facilities through smart, inquiry-based design. We are passionate architects and engineers specialized in translating the complex operational needs of supply chains throughout the United States into sustainable, efficient, human-centered facilities.
Whether you are considering a new facility or improvements to your existing facility, our passion is to evaluate and recommend the design and systems that provide the best solutions for you. The most efficient outcome often results from many solutions working together, rather than a single process or procedure. Together we establish the criteria to measure both the success of the choices made during the process, and the success of the entire project.
Experience, creativity and technical expertise come together in every service we offer. Planning, architecture, engineering and interior design, and program management are delivered by multidisciplinary teams hand-picked to provide the precise combination of expertise required for project success.
• Working closely with each client to discover the specific issues and operational needs
• Creating integrated, evidence-based designs to resolve critical issues
• Integrating all disciplines, including nationallyrecognized, accredited experts—architects, engineers, interior designers
• Working in collaboration with you we:
• Begin by listening and gaining a complete understanding of your needs and opportunities
• Achieve responsive facility planning outcomes
• Right-size your facility and operations
• Use industry-tested tools,methodologies and experience to analyze and achieve planned results
• Search out the unexpected and provide a basis to guide further decision-making
• Thrive on the complexities and subtleties of how best to make things work for you and your operational needs.
OUR SERVICES
Architecture
• Feasibility Studies
• Master Planning
• Site Selection and Evaluation
• Site Studies and Analysis
• Circulation Analysis
• Pre-design
• Design
• 3D Modeling and design
• Adaptive Reuse
• Code Analysis
• Interior design
• Space Planning
• Furnishing Selection
• LEED® Certification
Construction Administration
• Project Cost Control
• Construction Negotiation
• Contract Administration
• Owner Field Representation
Full-Service Engineering
• Civil
• Structural
• Mechanical
• Refrigeration
• Industrial
• Fire Sprinkler
• Electrical
• Technology Systems
• 3D Modeling and design
• Life Cycle Cost Analysis
• Process Safety Management
• Risk Management Program
• Energy Audits and Management
• Fire and Life Safety
• LEED® Certification
Delivery Methods
• Design/Contractor Assist
• Design/Bid/Build
• Design-Build
Our integrated approach combines experts from every design discipline: architecture, engineering, planning, and interior design. This harmony of design and process, pioneered by LEO A DALY, results in better project management and a more cohesive final design.
Design excellence permeates our thinking, defines our culture, and fuels our passion. We approach every project with an open, questioning mind, seeking to solve design problems in a way that serves clients, values the environment, and inspires users.
The foundation of our approach is client-centered. Working side-by-side with every level of stakeholder, we collaborate to serve your operational and business goals. Your vision, paired with our creativity and expertise, produces exceptional results.
LEO A DALY has a long history of providing clients with quality mechanical, electrical, plumbing (MEP), structural, and life safety engineering services. We offer a full range of services including consultation, surveys, studies, designs, cost estimates, bid documents, on-site construction support, quality assurance inspections, and systems commissioning assistance.
Our teams of highly-experienced engineering project managers, licensed professional engineers, technicians, and CADD specialists routinely provide MEP, structural, and life safety engineering services to clients both independently and as part of a full-service multidisciplinary project.
Our professionals are committed to providing excellence in service and delivering timely, innovative, high-quality, affordable, and sustainably-engineered MEP, and structural infrastructure support system solutions tailored to meet your specific needs and budget.
We strive for leadership in a competitive environment through superior application of skill and technology. We place special emphasis on a team approach that closely involves the owner in the decision-making process, and in a manner focused on mutual understanding.
• Partnering to understand your challenges and develop unique solutions
• Executing projects with a vision that reflects your story through a cohesive, harmoniously-designed environment
• Using an integrated design and management process to provide maximum functionality and cost effectiveness
• Consistently among the top 10 design firms in the nation
• Commitment to creative excellence and quality of service
• Creating designs that satisfy the specific challenges encountered in an environment
• Awareness of exterior architecture, interior aesthetics, and users’ needs to define the desired results
• Natural and synthetic refrigerant system design
• Transcritical CO2
• Skid design
• Existing Load analysis
• Dynamic energy modeling
• Condition surveying
• Performance surveying and analysis
• Cooling load calculation and verification Cold storage Process cooling Blast freezing / cooling
• Fault analysis
• 3D modeling
• Life Safety Code Consulting
• Life Safety Design
• Life Safety Master Plan Development
• Heating, Ventilating and Air Conditioning (HVAC) Design
• Building Automation and (Smart) Control Systems
• Central Plants/Campus Utility Distribution Systems
• Energy Analysis/Modeling/Audits and Energy Conservation Opportunity (ECO) Studies
• Existing Conditions Assessments
• Facility Surveys/Assessments/Feasibility Studies
• Industrial Ventilation
• Industrial Engineering/Management Engineering
• Industrial Refrigeration/Energy Management (Audit)/ Process Safety Management
• LEED Analysis of Mechanical and Plumbing Systems
• Life-Cycle Cost Studies/Cost Estimating
• Mechanical Equipment Replacement
• Medical Gas Systems
• Plumbing and Process Piping Engineering
• Preventative Maintenance Evaluation
• Grey Water and Rain Water Recovery
• Technical Studies
• Value Engineering
• Antiterrorism Force Protection
• Blast Analysis
• Deep Foundation Analysis
• Existing Conditions Assessments
• High Wind Resistance Analysis
• Progressive Collapse Analysis
• Seismic Analysis
• Value Engineering
• Storm Shelter Design
• Facility Condition Assessments
• Vibration Analysis
• Building Envelope
• Fundamental Building Systems Commissioning
• Enhanced Commissioning
• Retro-Commissioning
• Re-Commissioning
• Continuous Commissioning
• Energy Modeling
• Normal Power Distribution
• Emergency Power Generation and Distribution (Generators and UPSs)
• Medium Voltage Campus Distribution Systems
• Photovoltaic Design
• Lightning Protection Systems
• Lockout/Tagout Survey Analysis Procedures
• Lighting Development
• Daylight Analysis
• Computer Modeling
• Lighting Calculations
• Cable TV (CATV) Distribution Systems
• Security (Access Control, CCTV, Intrusion Detection)
• Public Address Systems
• Intercom Systems
• SYSCO PHILADELPHIA, PA
• SYSCO JACKSONVILLE, FL
• SYSCO MIAMI, FL
• SYSCO OCOEE, FL
• SYSCO ORLANDO, FL
• SYSCO NORTH LAKE, IL
• SYSCO MOUNDSVIEW, MN
• SYSCO NASHVILLE, TN
• SYSCO JACKSON, MS
• SYSCO FARGO, ND
• SYSCO PITTSBURGH, PA
• SYSCO LUBBOCK, TX
• SYSCO SAN ANTONIO, TX
American Foods Group
Braums Bakery
Cargil Swanson Meats
Cass Clay Dairy
Caterpillar
Cheney Brothers
Claas
Coca-Cola
Conagra Brands
Dairy Farmers of America
Dollar General
HEB
Jim Beam
Kemps Dairy
Lidl
Lunchbox Foods
MDI Merchants Distributors
MiMama’s Tortillas
New French Bakery
Second Harvest
SK Food Group
Smithfield
Spartan Nash
Stater Brothers
Sysco FreshPoint
Tree House
US Foods
Vantage Foods
Wenner Bakery
Cold storage is a vital component in the cold chain to maintain product integrity and quality. Our staff specialize in right sizing of systems for your specific needs to minimize your capital and operating costs.
LEO A DALY engineers have experience with:
• Natural refrigerants like ammonia, CO2 and hydrocarbons
• Plant design both remote and skid-based packages
• Environmental control including low humidity environments
• Integrated energy systems providing simultaneous cooling, heat and power
• Automatic storage and retrieval systems.
Refrigeration systems are the most expensive cost in a cold storage facility, using over 60% of the energy load of the building.
LEO A DALY’s experienced engineers understand the technical requirements for refrigeration systems and maintenance operations, along with the safety requirements of food processing facilities. Our work experience has allowed for the assessment and efficient renovation of these systems and can bring a large Return on Investment (ROI) to our clients.
LEO A DALY staff have experience with:
• Design of low energy refrigeration solutions
• Heat load reduction
• System efficiency
• Seasonal efficiencies
• Building expansion refrigeration system options analysis
• Optimization of existing refrigeration system through operational analysis and design.
Consulting-Specifying Engineer (2018, September). Designing industrial, manufacturing, and warehouse facilities. ConsultingSpecifying Engineer Magazine, 48-56.
Refrigerated & Frozen Foods, Mayer, Marina, (2018, September 10) How cold storage construction industry puts people first. Refrigerated & Frozen Foods
Refrigerated & Frozen Foods, Mayer, Marina, (2017, November 28) 10 tips for designing hurricaneresistant distribution facilities.
Refrigerated & Frozen Foods, Mayer, Marina, (2017, September 6) How automation, food safety, labor retention affect the future of cold storage construction.
As demand for fresh produce continues to grow, ripening rooms provide an increasingly important function in food storage and distribution facilities. Widening varieties of produce and de-greening compound the importance and complexity of these systems and their operation.
Our in-house, multi-discipline focus on specialized enclosures give our clients one less area of concern when it comes to insuring these systems are operating properly, efficiently, on schedule and within budget.
Our experience includes:
• Control systems
• Structural support systems
• Cooling and temperature control
• Air flow
• Vapor and humidity control
• Lighting
• Ambient conditions
• Regulatory requirements
• Operations
• Vendor coordination.
The food, distribution and manufacturing community thrives on the commitment to meet the needs of their customers. Our passionate team believes that smart design has big impacts to your bottom line. We simplify the design process by understanding your complex operational needs, commitment to customers, and your unique perspective to develop tailored solutions. We are experts in designing economically and ecologically responsible facilities, empowering the future of food and goods. Whether planning a new facility, repurposing an existing space, or optimizing building systems, we provide creative solutions that advance your commitment to your customers.
Philadelphia, Pennsylvania
Owner
Turner Construction Company
Size
390,000 SF
Cost
$28,000,000
Scope
Project Management, Design, Architecture, Interior Design, Engineering, and Construction
Administration
LEO A DALY was hired as part of a design/build team to complete the design of a new distribution facility near an existing Sysco warehouse on property the company owned. The new facility was designed to be based upon a company prototype and the location nearby was to minimize downtime of the operations. After completing initial studies and site review, the LEO A DALY team determined that the new site was not stable enough structurally to support the facility. The additional construction costs of site improvements and deep foundations that would be necessary to upgrade the site outweighed the benefits of the new ground-up facility.
The team identified the opportunity to expand and renovate the existing Distribution Center and Sysco decided to move forward with this option. The team conducted a building audit, code compliance review, zoning implications, fire access, property adjacency issues, and negotiated agreements with neighbor regarding property lines.
LEO A DALY worked diligently to phase the project in order to maintain operations through the process.
To minimize disruption to operations, the renovations/additions were phased:
Phase 1: Cooler/freezer expansion/operations office/new truck maintenance and fueling island stations/hydrogen storage yard.
Phase 2: New docks/will call.
Phase 3: Office renovation/business review test kitchen
Innovations / Challenges
• Conducted solar water heating payback study for truck maintenance.
• Cooler designed within middle of existing building while warehouse was still in use.
• Operations center converted where “box in a box freezer” existed.
• Hydrogen fuel cells for fork lifts.
Orlando, Florida
Owner
Publix Super Markets, Inc.
Size Perishable Warehouse
Total
SF
SF
SF
SF
SF
SF
SF
Site 110 Acres
Cost
$118,000,000
Scope
Programming, Site Planning, Architecture, Interior Design, Structural, Mechanical, Electrical, Refrigeration Engineering, and Construction Administration
Publix Super Markets Inc. is a privately-held company operating stores in Florida, Georgia, South Carolina, Alabama and Tennessee, founded in 1930. It is a Fortune 500 company with more than 1,000 stores and is one of the fastest growing employee-owned companies in the United States. Publix selected LEO A DALY to design a new refrigerated distribution center in Orlando, Florida, a site that had been redeveloped from agricultural to an industrial occupancy.
The site is situated directly north of the airport runways at Orlando International Airport, requiring particular attention to the vertical design components to meet FAA height restrictions.
The warehouse was designed with multiple roof heights, varying from 65’ to 40’, to accommodate flight paths. Roofing and structural systems were also designed to withstand highspeed winds. Electrical systems were designed to protect the building from lightning strikes.
The design of this high-tech center responds to logistics challenges to reduce cost of operation and maximize efficiency. This campus of buildings incorporates numerous utility saving measures such as patented air flow design for the freezers, 100% back-up power for operations, and motionactivated LED lighting to reduce electrical costs and maximize natural light. The refrigeration design also incorporates the latest energy-efficient controls to help monitor and reduce operational costs.
Greensboro, North Carolina
Owner
Publix Super Markets, Inc.
Size
2,000,000 SF campus
Cost
$150,000,000
Scope
Planning, Due Diligence, Architectural and Interior Design, Structural, Electrical, Mechanical and Refrigeration Engineering.
At nearly 2,000,000 SF, Publix’s new facility near Greensboro, North Carolina will be one of the largest distribution centers on the East Coast. The campus will include a 1,000,000 SF refrigerated warehouse, 200,000 SF of support buildings and a 1,000,000 SF dry warehouse. By teaming with LEO A DALY early in the design process, Publix will save $1 million in construction costs and about $250,000 in annual operating costs. The design team conducted early work sessions centered on establishing goals and priorities for the new Greensboro facility. Building off the design of the successful Orlando Distribution Center completed in 2014, team members vetted the pros and cons of the Orlando-based layout. They adapted the plan to the Greensboro geotechnical reports and civil drawings and then using historic data and discussions with contractors, probable construction cost estimates were generated.
The team also evaluated the spaces that cost the most per square foot to construct, office spaces, break rooms, locker rooms and dining areas. Working closely with Publix, these spaces were right-sized based on actual usage by employees — substantially reducing costs to build and operate the facility.
Virtual tours based on a 3D Building Information Model (BIM) allowed Publix to experience firsthand the manifestation of their goals and priorities, and chief among them was associate safety. Reducing foot traffic in the distribution center will decrease potential interactions with forklifts. Unlike any distribution center to date, the Greensboro facility will use elevated walkways to separate foot traffic between administrative areas, locker rooms, break rooms and dining areas, keeping associates on break off the distribution center floors.
Punta Gorda, Florida
Owner Cheney Brothers, Inc.
Size
375,000 SF
Cost
Confidential
Scope
Design, Architecture, Interior Design, Structural, Mechanical, and Electrical Engineering, Construction Administration
The new Cheney Brothers distribution center in Punta Gorda integrates storm-resistant construction, efficient mechanical design, and an innovative building shape to optimize resiliency, efficiency, and safety for the Florida-based broadline food distributor.
The 375,000 SF distribution center features 76,000 SF of freezer space.
One of Cheney’s biggest concerns was the ability to remain open even after significant storms have hit the area. LEO A DALY’s design uses reinforced concrete exterior panels capable of withstanding projectiles flying within the 150 MPH Ultimate Wind Speed environment.
To optimize operational efficiency, LEO A DALY worked closely with Cheney maintenance staff on the building’s mechanical design, which builds on established maintenance procedures and allows staff to cross-train at another Cheney facility in Riviera Beach.
The building’s L-shaped design was chosen to maximize safety and customer service. A will-call area is placed in the L’s middle hub at the central node within the building plan, allowing the distribution center to serve restaurant clients who run out of a product before their scheduled shipment. At the same time, visitors are kept separate from truck traffic to insure pedestrian safety.
Hudson, Wisconsin
Owner
Winnesota Regional Transportation
Size
46,000 SF
Cost
$8 million
Scope
Architecture; Structural, Mechanical, Electrical, Fire Protection, and Civil Engineering
In response to growth in perishables and last-mile business, Winnesota, a family-owned regional transportation company outgrew their existing facilities. With a purchase agreement on a 4.5 acre lot in Hudson, Wisconsin, the Eden Prairie based business intends to build a 46,000 SF warehouse beginning in 2020 with LEO A DALY to house operations and potentially third-party operations. The facility will have refrigerated storage and freezer space as well as ambient storage and office space.
Serving ever-evolving and hyper-competitive market sectors, the largely refrigerated building will be:
• Highly efficient operationally
• Highly energy efficient and resilient
• Low-maintenance
• Capable of adapting to changes in product requirements
• Capable of adapting to changes in storage systems
• Capable of handling a wide range of transport vehicles
The LEO A DALY will also design and implement special construction detailing to avoid damage associated with vapor drive increasing the stability of the refrigeration systems and temperature control.
Brooklyn Center, Minnesota
Owner
Second Harvest Heartland
Size
220,000 SF
Cost
$14,000,000
Scope
Programming, Pre-design, Architecture; Interior Design; Structural, Mechanical, Refrigeration, Electrical, and Civil Engineering
Second Harvest Heartland (SHH) is a non-profit that distributes nearly 90 million pounds of food and grocery products to the community every year. Their existing leased facilities were at capacity and did not support their goal of dramatically increasing their capacity to distribute 2x the amount of food to the community. They also needed a multi-functional facility that is welcoming to volunteers and community partners and lends to relationship building.
The LEO A DALY design team conducted an extensive needs assessment process with each department and facilitated several strategic and planning work sessions with multiple stakeholders to build consensus within and develop a cohesive design plan. The final list of goals was established and a 220,000 SF existing warehouse shell was repurposed.
The new facility includes areas for food sorting, prepping and packing by thousands of volunteers annually; cooler space and freezer space to increase capacity of fresh foods distributed; expanded ambient warehouse space; office and community meeting space; and an on-site food pantry.
SHH desired a design that conveyed a sense of community and connecting to their mission of ending hunger through community partnerships. The design features glass walls throughout the facility to connect the welcome center to the volunteer center and the food warehouse, creating a visual connection from the volunteers and staff back to the food. Office areas are open, and the staff break area is shared by office, warehouse and production staff.
Bessemer, Alabama
Owner Dollar General Corporation
Size Climate Controlled Warehouse 931,057 SF
Maintenance Facility 11,875 SF
Office 4,474 SF Receiving Guard House 413 SF Shipping Guard House 469 SF Pump House 1,413 SF
Total 949,701 SF
Cost
$64,000,000
Scope
Design; Architecture; Interior Design; Structural, Mechanical, Electrical, and Civil Engineering; Construction Administration
LEO A DALY has a working relationship with Dollar General and was retained for the design of Dollar General’s 10th distribution center, a design/bid/build project in Bessemer, Alabama.
The center, located on 106 acres consists of five new buildings completed in spring 2012. Five separate buildings total approximately 975,000 square feet of new construction. The buildings include a 958,000 SF Dry Storage Warehouse/ Administrative Office and Employee Welfare Building, 13,3000 SF Dispatch Office/Truck Maintenance Facility, 400 SF Receiving Truck Concourse Guardhouse, 300 SF Shipping Truck Concourse Guardhouse and 1,300 SF Pump House and 1,300 SF Pump House/Fire Protection Reservoir.
LEO A DALY also provided provisions for future expansion of 200,000 SF to the dry storage warehouse. Site work also included auto parking, truck circulation and parking, landscape, storm water detention/retention, perimeter security fencing/gates, site lighting and all site utilities (domestic water, fire loop/hydrants, sanitary sewer, storm sewer, electrical power distribution and duct banks between all buildings).
The design explores the relationship of scale through a dialogue between employee and warehouse space. Paths are emphasized; pedestrian paths are accented with vehicular patterns that support product shipping and receiving.
Janesville, Wisconsin
Owner
Dollar General Corporation
Size
Climate Controlled Warehouse 1,001,190 SF
Truck Maintenance Facility 15,781 SF
Dispatch Office 5,302 SF
Receiving Guard House 417 SF
Shipping Guard House 469 SF
Pump House 1,405 SF
Total 1,024,564 SF
Cost
$50,000,000
Scope
Design, Architecture, Interior Design,
Structural, Mechanical, Electrical and Civil Engineering, Construction Administration
LEO A DALY developed Dollar General’s prototype distribution center through a collaborative work session process. Dollar General Janesville, WI Distribution Center is the fourth building designed by LEO A DALY based on the prototype. We are currently designing the seventh distribution center in Texas. The site was a greenfield development with careful attention to site design for the six building campus.
Site design includes utility design, stormwater and sanitary design, concrete truck circulation and parking, concrete automobile paving and parking, truck scale, perimeter fencing, and detention ponds. All of the campus buildings are constructed with precast concrete panel walls. Precast was chosen because manufacturing of the system could be completed during the winter months, it exhibits good thermal insulating properties, is easily erected by construction teams, and is perimeter-bearing which reduces steel framing costs. In addition the concrete is durable and attractive.
The warehouse portion of the distribution center is complete with three-level pick module packed storage areas, shipping and receiving dock (161 dock positions), administrative offices, employee welfare areas, trucker’s lounge, battery charging, and shipping/receiving offices.
Sustainable features included low flow water fixtures and energy efficiency LED lighting fixtures throughout the facility significantly reduce overall consumption. The proposed lighting design reduces energy usage by at least 60% below typical warehouse design values.
San Antonio, Texas
Owner
Dollar General Corporation
Size
Climate Controlled Warehouse 932,900 SF Truck Maintenance Facility 14,000 SF
Office
Receiving Guard House
LEO A DALY has a working relationship with Dollar General and was retained for the design of Dollar General’s 12th distribution center, a design/bid/build project on a 110-acre undeveloped site in San Antonio, Texas.
The center is a slightly smaller and modified replica of the prototype in Alabama also designed by LEO A DALY. The facility is comprised of a Climate Controlled Warehouse, Dispatch Office, Truck Maintenance Facility, Shipping guardhouse, Receiving Guardhouse and Pump House.
SF
SF Shipping Guard House
House
SF
SF
Total 953,580 SF
Cost
$50,000,000
Scope
Design, Architecture, Interior Design, Structural, Mechanical, Electrical and Civil Engineering, Construction Administration
The warehouse portion of the distribution center is complete with racked storage areas, shipping and receiving dock (161 dock positions), administrative offices, employee welfare areas, trucker’s lounge, battery charging, and shipping/ receiving offices.
Site design includes utility design, storm water and sanitary design, concrete truck circulation and parking, concrete automobile paving and parking, truck scale, perimeter fencing, and detention ponds.
The central chilled water system is ammonia based and provides cooling for the large Climate Controlled Warehouse areas, significantly reducing energy use compared to commonly used package rooftop or other system types. The proposed system reduces annual energy consumption by 25% below ASHRAE 90.1 2007 baseline HVAC system types.
Hickory, North Carolina
Owner
Merchants Distributors, Inc.
Size
174,700 SF Freezer/Cooler Expansion
Cost
Confidential
Scope
Architecture, Civil, Structural, Mechanical, Refrigeration And Electrical Engineering and Construction Administration
Merchants Distributors, Inc. (MDI), a division of Alex Lee Company, Inc., a privately owned wholesale grocery distributor headquartered in Hickory, North Carolina, runs a full line distribution center of approximately 1,000,000 SF where they handle dry grocery, tobacco, produce, meat, dairy, ice cream and frozen foods. MDI selected LEO A DALY to design a 57,500 SF cooler expansion, 117,200 SF freezer expansion, and a renovation of existing space. The breakdown is as follows:
Cooler Expansion – Total 57,000 SF
• 27,000 SF expansion of 34 degree dairy/deli cooler space
• 20,000 SF expansion of 34 degree wet and dry cooler space
• 10,500 SF expansion of 34 degree receiving/shipping dock
Cooler & Freezer Reset (Interior Modifications)
• 11,900 SF of existing 28 degree cooler space is to be converted to 34 degree cooler space
• 13,000 SF of existing -10 degree freezer space is to be converted to 28 degree cooler space
Freezer Expansion – Total 117,200 SF
• 68,300 SF expansion of -10 degree freezer storage
• 36,400 SF expansion of -20 degree ice cream storage
• 12,500 SF expansion for 0 degree loading dock
Lenoir, North Carolina
Owner Merchants Distributors, Inc.
Size
33,000 SF Freezer Expansion
Cost
$4,900,000
Scope
Architecture, Civil, Structural, Mechanical, Refrigeration and Electrical Engineering and Construction Administration
Merchants Distributors, Inc. (MDI), a division of Alex Lee Company, Inc., is a privately owned wholesale grocery distributor headquartered in Hickory, North Carolina. MDI has an USDA-inspected meat cutting plant in Lenoir, NC with Vantage Foods (now operated by JBS USA) that produces case-ready fresh meat products for distribution along the Eastern U.S. The facility moves 24,000 cases of raw materials and 64,400 cases of finished goods a week.
LEO A DALY performed in-house, full-service architecture and engineering services, including architectural, civil, structural, mechanical, refrigeration and electrical engineering for a new 6,000 SF Raw Materials Freezer, a 27,000 SF Finished Goods Freezer. The facility also included new Battery Charging and Fire Pump rooms along with significant structural modifications to incorporate shipping and receiving dock modifications.
USDA guidelines were followed. The facility was located in a seismic zone which required a retrofit to the entire structural system in order to accommodate the potential seismic forces.
Site work included upgraded fire-protection supply piping and fire loop; surface parking expansions, truck circulation apron, pavement expansions and extensive storm-water mitigation structures. Processing and storage operation continued during construction and accommodations were made to ensure food safety at all times.
Lake City, Florida
Owner
Target Corporation
Size
470,000 SF
Scope
Architecture, Structural, Refrigeration, Mechanical and Electrical Engineering
Key features
ASRS, cooler, freezer and dry goods distribution center, high-bay facility, innovative thermal design.
Target desired a prototype building with reduced land requirements in order to relieve real estate cost pressures in urban markets. Concerned with labor shortages, they also wanted a system that would reduce man power requirements to afford flexibility in tight labor markets. Product integrity was paramount.
To serve Target’s diverse product range and set of demands, a hybrid distribution building was designed utilizing an automated storage and retrieval system (AS/RS) and conventional picking methods in refrigerated and nonrefrigerated spaces. This high-density packed storage system reaches over 80 feet high, which makes managing the thermal stratification and air flow difficult. LEO A DALY’s refrigeration engineers pioneered new methods to provide uniform air temperatures in this extreme environment.
In the frozen storage area, a first-of-its-kind AS/RS combined the cranes and the picking systems into one automated system. Due to the complexity of the product flow and the number of openings required, infiltration was a key concern.
LEO A DALY’s dedicated and experienced food distribution team paid particular attention to the thermal design in order to deliver a frost free and safe working environment. Additionally, LEO A DALY designed and incorporated an energy-efficient solution which included an innovative refrigeration system. The design saved 20% of energy compared to similar class distribution buildings.
The LEO A DALY team has completed the design of over 40 facilities that incorporate automated handling systems (AS/RS). We have great working relationships with suppliers such as Witron, Swisslog and Dematic. These systems are utlizied in facilities for Target, Publix, Sysco, and Supervalu.
The Target distribution centers at Lake City, Florida and Cedar Falls, Iowa included 18 AS/RS stacker cranes in the high-bay warehouse and a Swisslog picking system.
LEO A DALY also completed the structural and refrigeration engineering design for a Target distribution center in West Jefferson, Ohio. This fullyautomated perishables facility used a Witron system .
LEO A DALY designed the Orlando distribution facility for Publix in 2015. A Swisslog system was used for fulfillment of items in the freezer facility.
Blue Ash, Ohio
Owner
Kroger
Size
435,000 SF (total)
40,000 SF new freezer
90,000 SF remodeled dry grocery, maintenance, office and dock
150,000 SF existing Dry Grocery
Conversion to Cooler
100,000 SF freezer remodel
10,000 SF office remodel
Cost
$28,000,000
Scope
Design, Architecture, Interior Design, Structural, Mechanical, Electrical and Civil Engineering
Kroger is the largest supermarket chain and the second largest retailer in the U.S. and they continue to grow. A distribution center was needed in the Cincinnati area and they purchased a former Nash Finch warehouse for repurposing.
LEO A DALY led the design of the renovation of the existing 390,000 SF distribution center to suit Kroger’s unique program. The renovation included modernizing of approximately 217,000 SF existing dry grocery storage warehouse, truck maintenance space, office, employee break area, and dock. The team also converted approximately 150,000 SF of the facility to perishable cooler space and added a 45,000 SF of addition to include a freezer, cooler and mechanical room. The existing 1960’s warehouse posed a variety of code related challenges to the team including dated fire safety and fire suppression solutions.
Kroger had identified the crucial need to address the cost of employee retention within their new facility. Implementing a strong workplace strategy goal for the project was imperative. The team focused on increasing brand identity through a fresh and vibrant palette and emphasizing key employee amenities to increase pride-of-place.
When Kroger purchased the property, the existing building consisted of a 1960’s brick warehouse with a 1990s insulated metal panel addition. Kroger’s program required a new addition as part of the project. The complexity of the building systems required phasing for construction be carefully planned. Due to constructibility concerns and site constraints, Phase 1 included renovating the site and warehouse opening up of the distribution center allowing for critical business operations to get up and running. Office construction was conducted in Phase 2, after product was already moving in the DC.
Confidential Location
Owner Dairy Farmers of America
Size
53,690 SF
Cost
$15,900,000
Scope
Architecture, Structural, Mechanical, Electrical, Fire Protection Engineering, and Civil Engineering, Construction Administration
LEO A DALY, along with design-build partner, Big D Construction, assisted Dairy Farmers of America with a 53,690 SF addition to house their expanded filling and packaging line.
The addition to the facility included process filling lines, labeling and palletizing areas, packaging material storage, recycling docks, material handling equipment charging area, and various employee support areas such as break room, cafeteria, shipping offices and a Truckers Lounge. The design team worked with the client and a third party process engineering firm in understanding process equipment utility loads, installation and maintenance, along with building sanitation, and material and employee movements within the building. m
This project was a design|build delivery method and we included process layouts throughout our design process at the delivery of each design phase. Our end design for the building took into account building HVAC needs, electrical cable trays and power distribution, water loops and compressed air distribution, and sanitary and process waste water connections. Our integration efforts were able to provide design to code compliance for areas of specific chemical storage and refrigeration equipment, conveyor clash detection, assistance in constructibility and operations reviews, and even worked through standard operating procedure alignment to provide a safe working environment for employees.
Denver, Pennsylvania
Owner Supervalu, Inc.
Size
1,545,000 SF
Cost
Confidential
Scope
Programming, Site Planning, Architecture, Interior Design, Structural, Mechanical, Electrical, Refrigeration Engineering, Construction Management
This project, for a national food distribution company, involved an addition to and remodeling of an existing conventional warehouse facility. Both the addition and remodeled space will be used for ambient grocery storage. The 178,000 SF addition with 80 foot clear height, includes an automated high bay AS/RS tied to the 315,000 SF automated full-case sorting and picking warehouse. Receiving and shipping docks are an integral part of the remodeled warehouse portion of the project. Building lighting and environmental systems for the addition and remodeled space are totally new and independent from the remainder of the 1,545,000 SF facility.
Omaha, Nebraska
Owner Claas
Size
200,000-SF
Scope
Full Architectural and Engineering
Services; Interior Design; Construction Administration
Claas America LLC was originally a joint venture between the Caterpillar Corporation and the Claas Corporation of Germany to produce Lexion Combines for distribution to all of North America. In 2002, LEO A DALY designed the 200,000-SF facility to include 35,000 SF of office space and an assembly area of 165,000 SF. The office space has open and enclosed offices; product display area, and retail store, dining facilities; customer briefing auditorium; and information services which serves the entire office and assembly plant and is connected by a fiber-optic backbone.
The assembly area has a 27-foot clear height and includes a “flat floor” production line to allow for the use of air pallets; a test cell area for product testing; a wash booth area; a paint booth; paint oven area; a prototypical configuration area; and large open areas for parts storage. The assembly space contains cranes throughout for product movement and is also served by a large compressed air system for tool and equipment operation. The facility is constructed of a pre-fab metal building and precast concrete exterior. Natural light is introduced into the assembly area by north facing glazing. The roof is constructed of a standing seam metal and is configured to allow for no interior roof drains or downspouts.
LEO A DALY has been the design partner for Claas for over 20 years. We designed the original facility in 2000, and have designed two additions in the past two years.
The product display area contains a full height curtain wall system to maximize views of products at night from the adjacent interstate highway. The entire site was master planned to allow for a controlled truck entrance, truck marshaling, and exterior combine and parts storage. The site is planned to accommodate an additional 200,000 SF of future expansion. In 2018, Claas turned to LEO A DALY to design a 12,150 SF addition to the production facility to house a new production line.