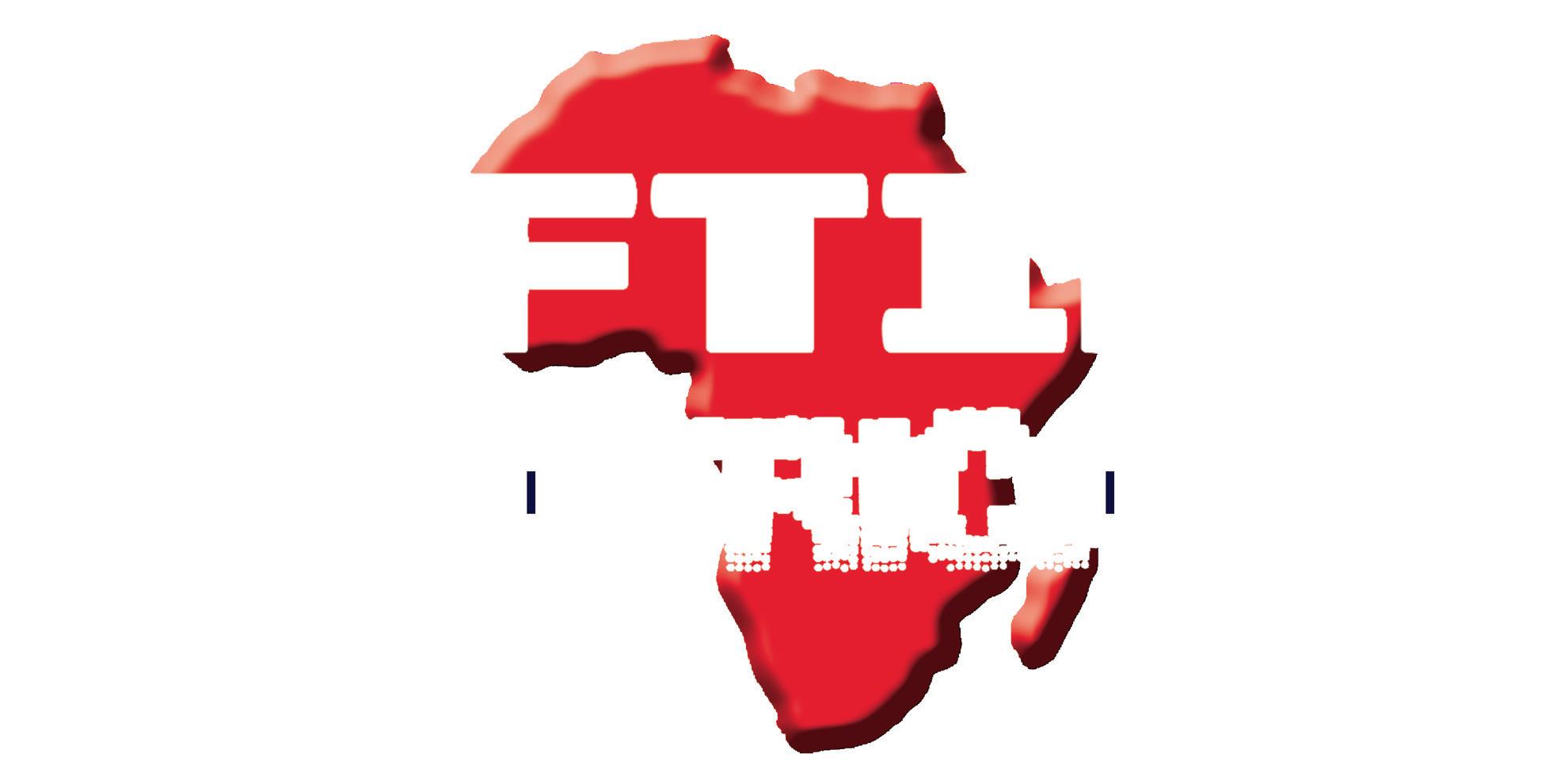
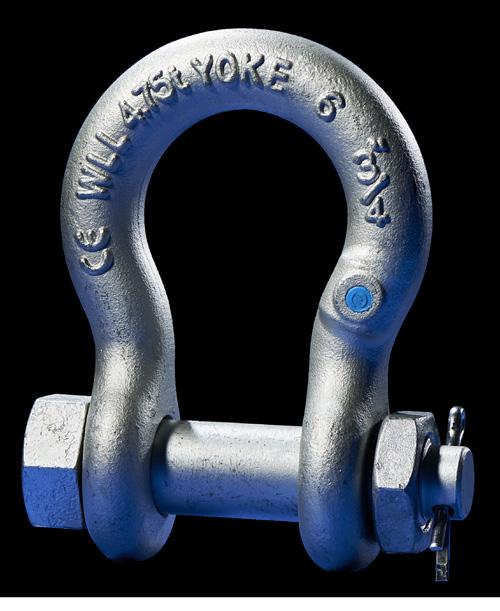
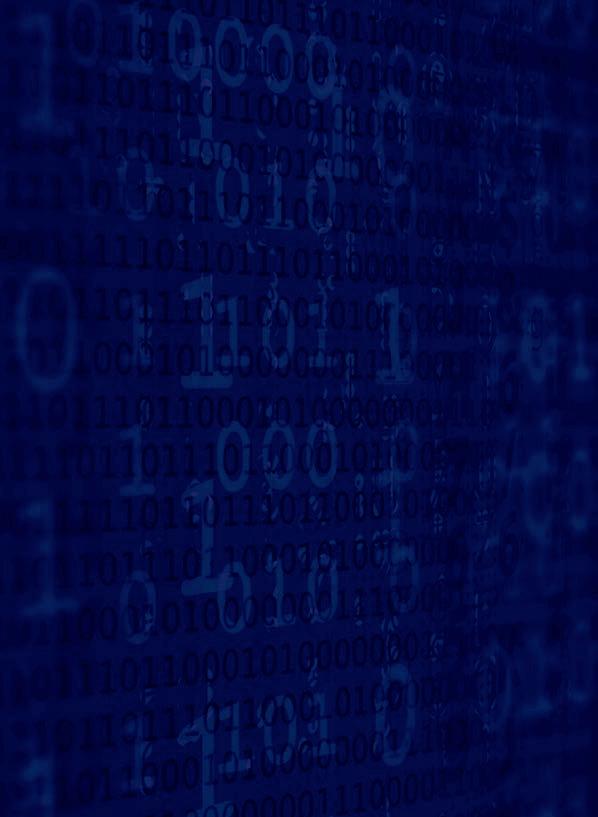
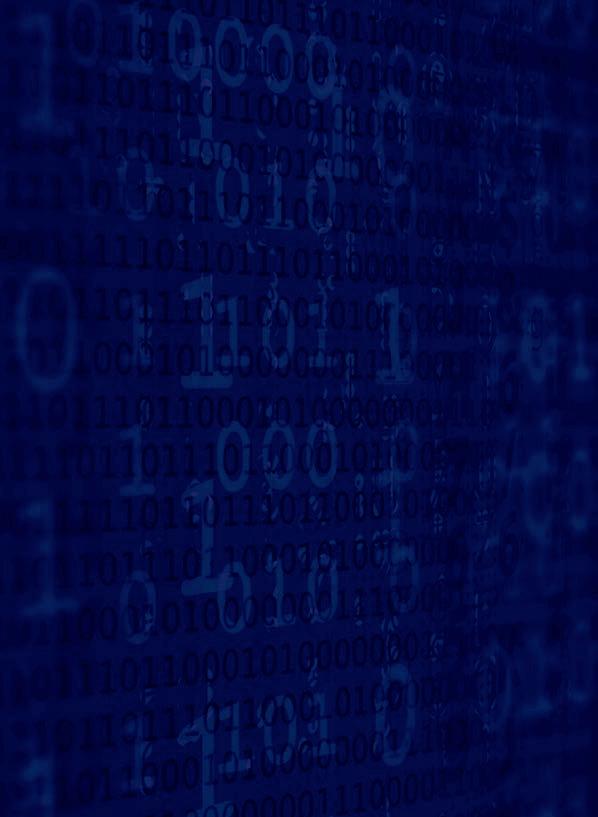
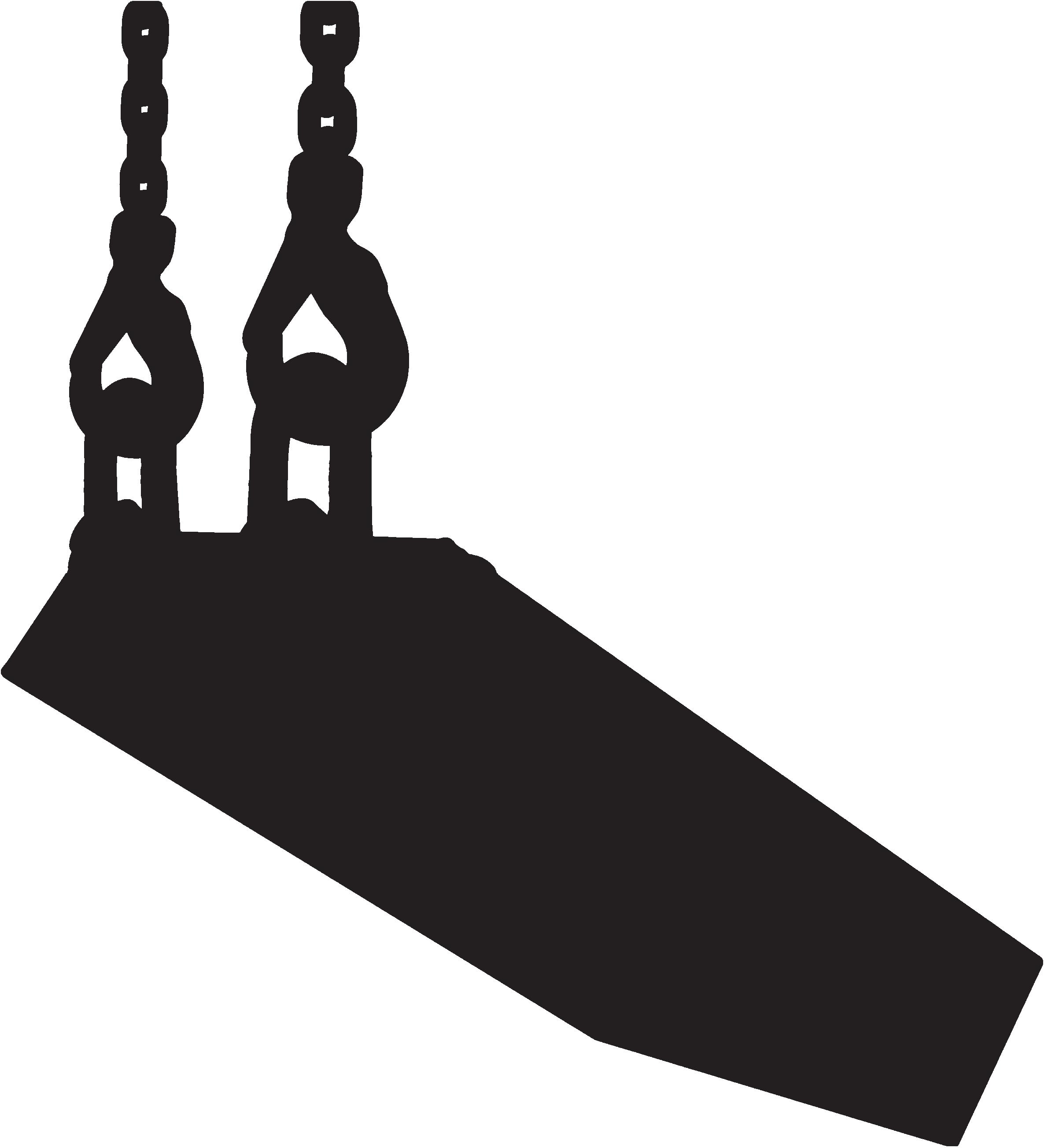
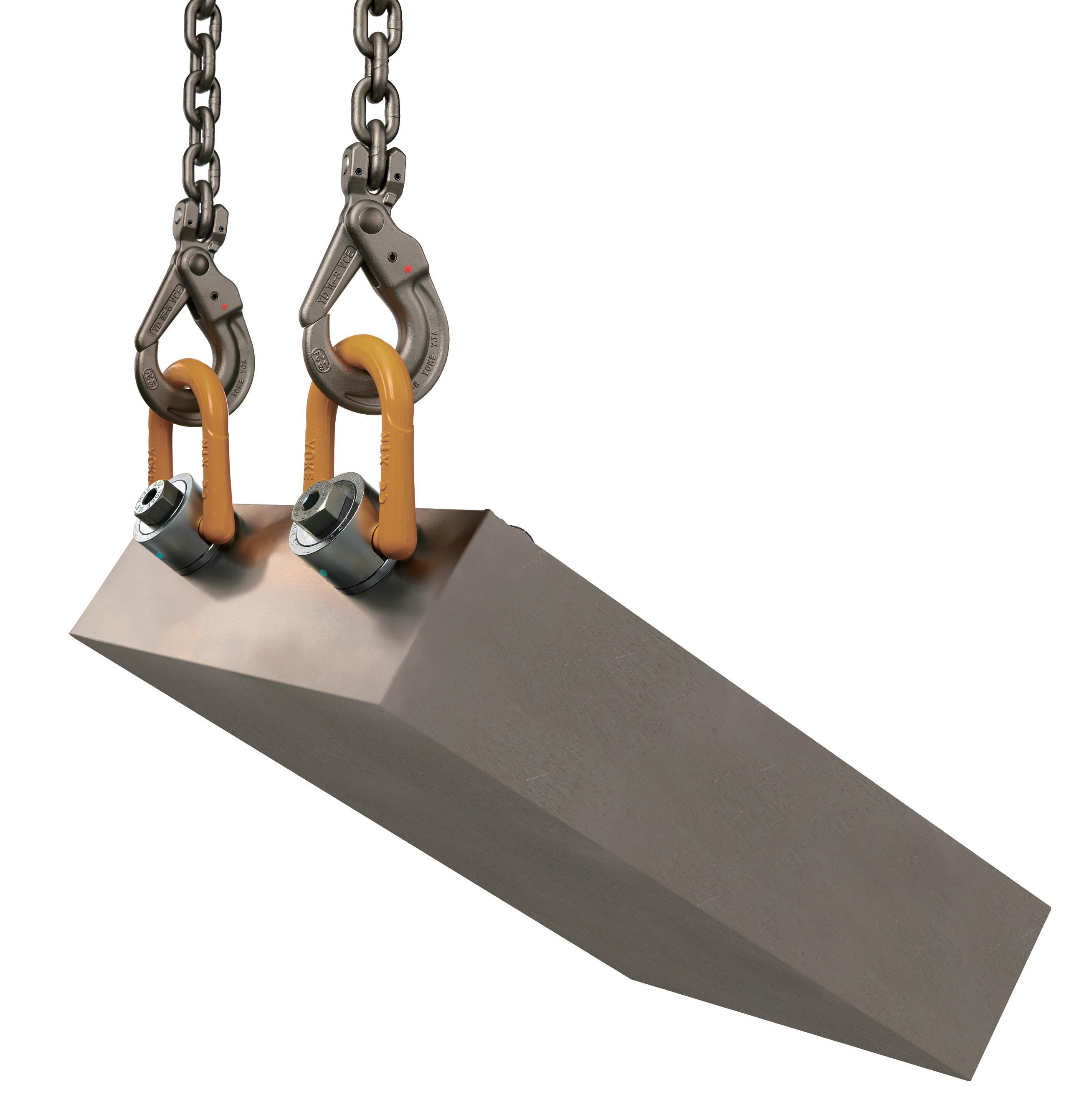
Lifting Africa’s annual Lifting Awards celebrate the outstanding achievements and innovations in the lifting industry, recognising excellence across various categories. These awards aim to highlight the significant contributions of individuals and companies that have set new benchmarks in safety, sustainability, innovation and technical expertise. By acknowledging these exemplary efforts, the Lifting Awards inspire continued growth and development within the industry, fostering a culture of excellence and advancement.
Apprentice / Technician of the Year Award
Excellence in Engineering
Excellence in People Development
Environment Award
Industry Leader Award
Innovation in Service Award
Innovation Award (Manufacturer Product
Innovation of the Year)
Project of the Year
Rising Star Award
Safety and Training Award
Services to the Lifting Industry / Lifetime
Achievement Award
www.liftingawards.co.za
much
We all know what hard stamping is: a type of punch that, when struck, creates an indentation on the surface of the product that can be read or understood by the item’s user.
It is about as far from state-of-the-art as you can get and, in an industry embracing the Internet of Things (IoT), Artificial Intelligence (AI), Blockchain, automation, the metaverse, etc., it’s remarkable that hard stamping remains so prevalent. We continue to visit rigging shops and see people at workbenches hard stamping batches of 1,000 shackles and preparing the individual certification that needs to be produced.
The major problems associated with this traditional type of marking product include:
• Time involved with hard stamping and paperwork.
• Potential damage it causes; without clear guidance on where to stamp or what tooling to use, it is possible to introduce stress raisers into the product, making it more susceptible to premature failure.
• Hard to read markings.
• A lack of control over font sizes and sharp-edge fronts.
There is also a large volume of equipment in industry that is marked with colour-coded tie-wraps that give a visible indication that the item is within its six-monthly examination period. However, that doesn’t mean that the item has been given its pre-use inspection. The wider problems associated with stamping and tagging begin to emerge, meaning that a wholesale move towards radio frequency identification (RFID) and Software as a Service (SaaS) can’t come soon enough — with pre-use checks, unique identification numbers, and the Machinery Regulation all at the fore of the revolution led by YOKE Industrial Corp. To back-up that claim, YOKE had a decision to make a few years ago.
We could have taken one or two RFID-equipped products and introduced them to industry to assess potential uptake, or fully digitalise our complete range, where size permitted, and state our intentions to change the way the industry works tomorrow. We chose the second option — and have never looked back.
Aligned with a mission to manufacture quality rigging and safety equipment to deliver superior safety protection, RFID drastically enhances safety and helps industry keep up with pre-use checks, unique identification numbers, and the move towards January 2027, when everybody is expected to be working to the Machinery Regulation.
That’s when the EU Machinery Regulation fully applies, and the Machinery Directive 2006/42/EC is repealed.
Eventually, the Machinery Regulation will eliminate all the different requirements across all of the EU member states, so they all follow the same regulation.
One of the most significant changes is the inclusion of original certification and manuals to be supplied digitally with products.
As the world moves towards a more environmentally friendly future, we are certain that by digitalising our full range of products, we are removing the need for any paper trail as the product will carry the history from initial supply through its lifetime of use.
What are the chips and how do they work?
RFID has been used for many years in industries such as agriculture, where cattle are tagged, for example, but it was always difficult to incorporate it into rigging due to complexities of manufacture and ensuring suitability for items where they can last decades if used properly.
With the additional work YOKE has carried out with Near Field Communication (NFC) technology, it means that today every user with a mobile phone capable of
paying a bill now also has the ability to at least check a component for a safe use instruction.
Already, several original equipment manufacturers (OEMs) are using BlueSupra. Put simply, BlueSupra is the brand name for the range of tags we produce and SupraNano is the encased NFC RFID chip.
For YOKE products, we pressure-fit the SupraNano directly into the steel, but for items such as a snatch block, we utilise a retrofit tag to permanently attach it. The equipment is extremely durable. Our BlueSupra retrofit tags are put through a series of tests covering impact and wear and the SupraNano is subjected to rigorous temperature (-30 / +125 degrees C) and water ingress (6,000m subsea) tests.
YOKE’s RFID chips are even in a 7mm connector and 1t capacity shackle. Using software from RiConnect, a SaaS provider, they can be read even on a regular smart phone or device, providing information not only like the unique identification number, but a full description, brand name, registration date, status, documentation, and any asset number or other serial number if added by the distributor.
We even supply these tags to competitors, removing any barriers where some manufacturers do not yet add the digital chip to their product.
Industry is thusly harnessing all the inherent benefits of the technology and, importantly, doing so in line with the Lifting Equipment Engineers Association’s (LEEA) ongoing guidance and industry standards. Consider how the duty holder gains too. While supply legislation does not require a manufacturer of lifting equipment to give it a unique identification — it simply requires them to mark one on the product if they have specified one — user legislation requires the duty holder to have lifting equipment inspected and / or thoroughly
examined and issued with a report of that inspection or thorough examination.
This report must identify the equipment without ambiguity so that defects can be remedied efficiently.
We frequently point people to LEEA’s guidance that where a duty holder has many items of a similar generic form of lifting equipment, it is considered best practice to give each piece its own unique identification number, which is then recorded on each thorough examination report, thus ensuring the report is traceable to the equipment without ambiguity.
All this can be achieved with RFID and SaaS — without hard stamping or colour-coded tie-wraps.
Hard stamping is not a favourable way to identify equipment; it can bring inherent damage, and logistical and inspection issues thereafter. Each inspector will inspect hundreds of thousands of items in their lifetime, cleaning off dirt and mud, just to be able to read the hard stamp. This can lead to mistakes as numbers and letters are not always readable.
Most inspection companies have transitioned away from pen and paper systems and equipped their inspectors with smart phones or tablets, so they do not want to be working in the mud with wire brushes trying to read hard stamped markings. It is expensive and not time efficient, when the technology is readily available in their hands.
Imagine never having to stamp a shackle or a sling tag ever again.
YOKE Industrial Corp, info@mail.yoke.net, www.yoke.net
have already renewed their annual memberships and who are in good standing. If you have not received your annual invoice, please check your spam folders or check your contact details with our admin department who will also gladly resend any required documents to you.
We have already by the end of January 2025 increased our membership take on compared to previous years.
The LEEASA board has been busy behind the scenes gearing up towards 2025 with some much-needed implementation of some strategic initiatives aiming to take the association into the next decade.
As you are aware the LEEASA board of directors is made up of strictly volunteers that all have there own responsibilities which include but are not limited to running their own companies, working in corporate environments, being an employee that has the responsibility of taking the day to day of there day jobs as first priority and in some cases even retires that should be spending the well-deserved time off with their grandkids..
Although each director gives the association their best efforts it is simply just not enough to give the membership base and industry the dedicated input that’s needed.
This is the biggest limiting factor the association has had over the past years, and it would be inevitable that the association would not have the continuity that it requires if this challenge was not addressed.
LEEASA has reached a turning point and what we believe will be a new era in the history of the association.
After much deliberation and strategy as well as collaboration with key industry stakeholders we are pleased to announce the appointment of Mr. Gert Oosthuizen as Association Development Manager, and he will report directly to the LEEASA Board of Directors.
Gert who has over 40 years’ experience in the lifting industry alone was one of the founders of LEEASA many years ago and shares the same vision, mission and values as the LEEASA board and is geared up to take on the challenge in a semi-permanent role.
Gert will initially be focused on some much-needed functions such as (In no order)
• Increasing Personal Members (PM)
• Increasing Company Members (CM)
• Implement QA Vetting for Companies (QAV)
• Increase Seminars / Events
• Increase Training
• CPD
• Lifting Product training
• LMI Mentoring – How to Test Machines Correctly
• LMI Candidates Upliftment
As well as other representation / dealings with
• Other Industry Associations
• DOEL
• ECSA
• SABS
• Client / Member / Public / Industry Feedback
We do not want to take all the glory and will allow Gert to introduce himself and give you all a taste of what we will be working on in the upcoming months to fast track LEEASA’s strategic initiatives.
Welcome to our Team Gert, we are all excited to collaborate with you and take LEEASA to new heights...
In the interim feel free to reach out to Gert on gert@ leeasa.co.za
Some good news that after a long period of inactivity at SABS meeting are back on and the first meeting of the year is being held on the 6th March 2025 for SABS/TC 096 “Cranes” and as usual LEEASA will be represented and are looking forwards to providing feedback on the meeting activities once completed.
We are finalizing our year planner for 2025 and please consider supporting us by saving the dates for the planned CPD conferences below:
• Durban - KITE: 23rd July 2025
• Johannesburg - Birchwood: 28th & 29th August
We currently have one open seat on the LEEASA Board of directors and are inviting nominees to contact us should you wish to be getting involved at this level.
Please contact kyle@leeasa.co.za if you have any questions.
Chairman: Kyle Graham: kyle@leeasa.co.za
Vice Chair: Ashley Davis: ashley@leeasa.co.za
Ordinary Members:
Francois Weideman: francoisw@leeasa.co.za
Roger Day: roger@leeasa.co.za
Katiso Mogaki: katiso@leeasa.co.za
Carlos Marques: carlos@leeasa.co.za
Administration: Desiré Davis: admin@leeasa.co.za
Marketing and Design: Xané Roestroff: production@leeasa.co.za
Feel free to reach out to the council members if the need requires.
Yours in SAFE LIFTING, Ashley Davis and the LEEASA team
We conduct the follow Lifting Equipment Training Courses:
• On line Management, Technical & Legal Compliance
• Lifting Tackle Inspection
• Chain Block and Lever Hoist Operation, Safety & Inspection
• Advanced Slinging & Inspection
We supply the following:
• Lifting Tackle Inspection Registers
• Lifting Tackle Wall Charts
• Lifting Tackle Plant Surveys, Audit & Reports
• Lifting Tackle Code of Practice
We will assist you to implement and
Mr. Aaldrik Graham Kiewiet
Mr. Akeal Ramraj
Mr. Alan Victor Botha
Mr. Alfa Janes Grouws
Mr. Amogelang Gilbert Mmusi
Mr. Amos Tulela
Mr. Andre van der Merwe
Mr. Andries Aucamp
Mr. Andries Gordon
Mr. Andries Josias Agenbag
Mr. Arnoul Spitsbaard
Mr. Ashley Mark Davis
Mr. Barend Andreas Lubbe
Mr. Bartholomeus Jakobus Erasmus
Mr. Bekezela Abel Ndlovu
Mr. Carel Gustavus Potgieter
Mr. Carel Hendrik Ferreira
Mr. Challe Andre Bonhamme
Mr. Charles Casgoigne
Mr. Christiaan Ernst Gerhard Schutte
Mr. Christiaan Hendrik Van Wyk
Mr. Christo Van Eyk
Mr. Christo van Huyssteen
Mr. Clifford Mubvuta
Mr. Coenraad Hendrik Heunis
Mr. Collin Kubayi
Mr. Cornelis Henry Cyrus Spamers
Mr. Cornelius Frederick van der Nest
Mr. Cornelius Johannes van der Walt
Mr. Cyril Raymond Laredo
Mr. Damien Oscar Stephen
Mr. Daniel Ntatenyane Mangwegape
Mr. Darrin Ian Cass
Mr. David Henry Cooks
Mr. Dean Edwin White
Mr. Dean Eppel
Mr. Deon Bonthuyzen
Mr. Desmond Errol Lloyd
Mr. Dewald Schutte
Mr. Diederik Arnoldus Dahms
Mr. Donavon Hugh Spamers
Mr. Drean Johannes Kotze
Mr. Dwayne Partridge
Mr. Edius Topera Mashamba
Mr. Edward Hall
Mr. Edward Kruger
Mr. Emile de Koning
Mr. Ernest Khanyile
Mr. Ettiene Pollard
Mr. Eugene Terence Redelinghuys
Mr. Ferdinand Pieterse
Mr. Francois Dewald Blignaut
Mr. Francois Frederikus Le Grange
Mr. Francois Weideman
Mr. Frederek Gerhardus Opperman
Mr. Frederick Johannes Jacobus Fourie
Mr. Happy Tafara Tati
Mr. Harris Naidoo
Mr. Hendrick Rapule Mahuma
Mr. Hendrik de Jong
Mr. Hermanus Barend Dahms
Mr. Ian O’Hara
Mr. Isaac Thupaakgosi Leshotho
Mr. Israel Mooketsi
Mr. Jacobus Rudolph Kruger
Mr. Jan Louis Venter
Mr. Janus Jacobus Van Biljon
Mr. Jetro Mzwandile Ngwenya
Mr. Joao Carlos de Freitas Marques
Mr. Johan Frederick Herselman
Mr. Johan Smith
Mr. Johann du Plessis
Mr. Johannes (Jaco) van Biljon
Mr. Johannes Gideon Kruger
Mr. Johannes Hendrik Snyder
Mr. Johannes Jurgens Marais
Mr. John Carsten Allers
Mr. John George Smith
Mr. Jonathan Rapetsoa
Mr. Joseph Johannes van Huyssteen
Mr. Juan Breitebach
Mr. Justin Henry Brown
Mr. Karel Johannes Francois Du Toit
Mr. Kebareng Daniel Molausi
Mr. Kevin Clive Reckas
Mr. Kevin Keith Godfrey
Mr. Khathutshelo John Phalandwa
Mr. Kobus Van Tonder
Mr. Kyle Graham
Mr. Leon Johan Snyders
Mr. Lesiba Willie Sebothoma
Mr. Linton Moodley
Mr. Luke Steven West
Mr. Makalele Selwyn Makofane
Mr. Malose Kenneth Mabela
Mr. Marius Marais
Mr. Marius van der Merwe
Mr. Mark Leonard Munnery
Mr. Mark Leslie O’Connor
Mr. Matthys Michiel Brink
Mr. Mboshoa Simon Skosana
Mr. Mgcini Khumalo
Mr. Michael Fernandes De Souza
Mr. Michael Henry Hassett
Mr. Michael Richard Slabbert
Mr. Milton Mhlanga
Mr. Mogakolodi Gregory Thamage
Mr. Mohamed Hoosen Dawood
Mr. Moses Karukwayo
Mr. Mthandeni Kunene
Mr. Napo Michael Noosi
Mr. Nathaniel Happy Sambo
Mr. Paulo Jorge de Freitas Marques
Mr. Paulus Stephanus Marais
Mr. Peter Abraham du Toit
Mr. Peter Jacobus Nel
Mr. Petrus Lafras Fritz
Mr. Phata Simon Mailula
Mr. Philip John Lourens
Mr. Philippus Stefanus Kruger
Mr. Phillip Demetrius Kemp
Mr. Phiwayinkosi Manazi Biyela
Mr. Pieter Albert Schoeman
Mr. Pieter Andries Engelbrecht
Mr. Frederik Wilhelm Stonehouse
Mr. Garth Vincent Barnes
Mr. Gavin Rayson
Mr. George Khehla Kuhlase
Mr. Gert Vos
Mr. Given Nyathi
Mr. Neil Naude
Mr. Nicolaas van Zyl
Mr. Nkosinathi Richard Mavimbela
Mr. Noel Nyamukoho
Mr. Octovias Lebakang Mabelane
Mr. Pastor Noosi
Mr. Ralph Errol Shamrock
Mr. Randy Mmoto Makeke
Mr. Raphael Letsema Shobane
Mr. Reino Schutte
Mr. Richard James Don Donaldson
Mr. Rishi Mungroo
Mr. Robert Du Toit
Mr. Rodney Bassingthwaighte
Mr. Roger Ian Day
Mr. Ronald Albert Innes
Mr. Ronald John Laing
Mr. Rudi Lansdell
Mr. Rudzani Collins Masiagwala
Mr. Russel Henning Boshoff
Mr. Rutendo Job Sadomba
Mr. Ryan Jerry Eeden
Mr. Samson Kamutasa
Mr. Schalk Willem Johannes Burger
Mr. Sello Jacob Sebiloane
Mr. Seth Laredo
Mr. Shaun Combrink
Mr. Shimane Martin Diutlwileng
Mr. Siegfried Schrader
Mr. Sifiso Ngwenya
Mr. Simphiwe Mosito
Mr. Stephen Andrew McGregor
Mr. Steve Harper
Mr. Steven Duvenage
Mr. Stuart Mark Love
Mr. Stuart Swart
Mr. Suresh Karan
Mr. Thulani Ndlovu
Mr. Timothy Tatenda Zindi
Mr. Tshisamphiri Moses Mukoma
Mr. Victor Manuel Batista Ferreira
Mr. Victor Thedor Sargent
Mr. Vincent Smanga Sithole
Mr. Vishay Ramkaran
Mr. Warren Naude
Mr. Weddington Chimbane Moyo
Mr. Werner De Bruyn
Mr. Werner Hermann Schroer
Mr. William Henry Pepler
Mr. William Peter Park
Mr. Wisdom Nhlakanipho Mkhomazi
Mr. Yogandren Soobramoney
Mr. Zenzele Siphamandla Ntshakala
Mrs. Ruwaida Mahomed
Mrs. Sandile Wyeth Mzimela
Ms. Naom Thobile Milanzi
“These records are up to date at the time of going to print”
With the new AC 5.250L-2, Tadano is literally going one better: With its 79-meter-long main boom, this 5-axle machine is at the top of its class. And the maximum main boom extension of 30 meters is also best in class.
Remarkably, all available main boom extensions from 5.8 to 30 meters are self-erecting. The available maximum system length of 109 meters makes the compact AC 5.250L-2 the ideal crane for urban applications, for example for lifting air conditioning units over obstructions onto tall buildings. Additionally, it is also ideally suited to the assembly of large tower cranes.
“Our AC 5.250L-2 is also top of the class when it comes to load moment, which at up to 736 tonne meters is one of the best on the market,” explains Peter Kleinhans, the responsible project manager, with pride. This high load moment is achieved with a working radius of 7 meters, a 13.5-meter-long main boom and a load weight of 105.2 tonnes. In addition, Tadano offers an optional heavy-lift attachment for even heavier loads up to 138.7 tonnes on the short boom with additional sheaves.
Economical use as a taxi crane
Like the basic AC 5.250-2 model, the “main boom long version” also
impresses with its outstanding transport configurations. The crane with 10 x 6 drive can be moved on cost-effective 16-inch steel wheels on public roads while complying with the 12-tonne axle load limit with a considerable amount of equipment including a 32-tonne Vario hook block and outriggers with a total weight of less than 60 tonnes, transport brackets for extensions, and up to 250 kg of equipment in the rear box.
In compliance with the 16.5-tonne axle load limit with a total weight of exactly 82.5 tonnes, the AC 5.250L2 can even be driven on public roads with a 10 x 8 drive on 16-inch steel wheels. It can not only carry a 32-tonne hook block, outriggers and a 12-metre extension including transport brackets, but also 20 tonnes of counterweight and up to 500 kg of equipment in the rear box.
Sophisticated counterweight concept
The AC 5.250L-2 can pick up its maximum counterweight of 80 tonnes in three lifts: 49.6 tonnes
with a radius of up to 6.8 meters at a full radius of 360° and two 15.2 tonnes with a radius of up to 13 meters, divided into 10 and 5.2 tonnes for hanging on the right and left of the basic package. If required, the counterweight can also be divided into smaller pieces. For example, the 5.5-tonne base plate can be picked up from a distance of up to 23 meters in a full radius.
“Thanks to the standard IC-1 Plus crane control system, the possible radius can be increased considerably in certain areas of the slewing angle,” emphasizes Peter Kleinhans. Maximum flexibility in transport logistics is also ensured by the division of the counterweight, with no element weighing more than 10 tonnes. This means that smaller trucks can be scheduled for transportation if space conditions on the construction site require it.
On board: IC-1 Plus and Surround View
Tadano has also equipped the AC 5.250L-2 with a comprehensive range of standard features that
benefit all current cranes in the Tadano AC family. This includes the innovative IC-1 Plus crane control system, for example. It determines the maximum load capacity of the crane in real time for each boom position depending on the slewing angle of the superstructure. This means that the crane can always use the maximum available capacity - especially when lifting over the outriggers.
This advantage literally comes to the forefront when the counterweight is reduced, and the outriggers are not fully extended. The AC 5.250L-2 benefits greatly from this, as its outriggers can be extended asymmetrically in five positions of 0, 25, 50, 75 and 100 percent.
The unique Surround View camera system is also available as an option for the Tadano AC 5.250L-2, making it easier for the crane operator to optimally position the crane on the construction site.
This patented system uses six cameras to display the maximum possible extension widths of the outriggers at the crane’s current position in a computer-aided display.
“With Tadano Surround View, the crane operator can see on a display in the cab exactly how he needs to position the crane on the construction site in order to extend all outriggers sufficiently and ensure the required slewing radius. This eliminates the need for tedious and time-consuming measuring and trial-and-error when searching for a location, so that the crane is ready
for use more quickly,” explains Peter Kleinhans. The system also helps to better recognize pedestrians and cyclists on the way to the construction site when turning.
Comfortable and safe workplace
When developing the AC 5.2502, Tadano did not disregard the needs of the crane operator - and the AC 5.250L-2 naturally also benefits from this: all noiseemitting hydraulic components are positioned away from the upper cabin, making it pleasantly quiet. In any case, the generous amount of space in both cabs ensures a high level of operating comfort and pleasant working conditions. Safety is ensured by well-placed access steps, attachment points for the driver’s personal safety equipment and a step that can be extended from the undercarriage for safe and convenient entry and exit to the upper cab.
The optional pendant light and a load view camera also ensure greater safety during operation. These can be mounted alternately on the boom head and on the extensions so that one system can be used for all configurations. When lifting over interfering edges with an extension, the repeater, which is also available, is recommended for mounting on the boom head to ensure a wireless connection to the camera in such cases.
On the engine side, the AC 5.250L2 has the same drive that already delivers a convincing performance in the AC 5.250-2: The modern
Mercedes-Benz engine with 530 hp output and a maximum torque of 2,600 Nm ensures decent propulsion and strong lifting performance. The HVO-compliant diesel engine meets the current EU Stage V requirements.
Thanks to Eco Mode, it is also particularly economical: the engine only delivers as much power as the crane needs at any given time. The corresponding calculations are made via the IC-1 crane control system, which also includes a fuelsaving start/stop function.
This switches off the crane engine at the touch of a button without deactivating the control softwareand the hill start assist, which is also fitted as standard, ensures stressfree driving when starting off and maneuvering on inclines.
With the AC 5.250L-2, Tadano has added a convincing variant to the proven AC 5.250-2 basic model, which significantly extends the range of applications of this already versatile crane even further thanks to the 79 m long main boom.
The high load moment of up to 736 mt in combination with the long system length of 109 meters makes this crane an extremely interesting option for many applications where heavy loads have to be lifted to great heights - and thanks to its good taxi crane properties, it is also definitely a convincing economic option.
Tadano Group, Damien.Bizjak@tadano.com, www.tadano.com
Condra is to manufacture a second overhead crane for Tongaat Hulett’s Maidstone sugar mill, KwaZulu-Natal, South Africa.
The order is for a 23-metre-span double girder electric overhead travelling crane with 25-ton main hoist and 8-ton auxiliary, to work in conjunction with the existing millhouse crane and a 10-ton Condra crane commissioned in the bagasse store in March 2024.
Maidstone is one of four South African sugar mills operated by Tongaat Hulett, a leading agriculture and agri-processing company.
In the bagasse store, the 10-ton crane is already used to move and position conveyors feeding fibrous raw residue (bagasse) into Maidstone’s secondary processing system.
Left over as waste after harvesting juice from the sugarcane, bagasse is used after processing as a biofuel, and in the manufacture of paper pulp and building materials.
The new 25/8-ton crane will help operate and maintain the mill house. Condra was able to meet Tongaat Hulett’s technical requirements for Maidstone’s new crane because of modular products that facilitate manufacture of a customised lifting solution; this instead of having to shoehorn a standard machine – often imported
– into the application, an approach frequently followed by rival firms. Such modular design comes very close to the theoretical ideal: all elements of the crane – hoist, crab, end-carriages, drives and controls – are themselves assembled from a wide array of component parts. Only the crane girders are manufactured from scratch.
For Tongaat Hulett’s new mill house crane, Condra precisely tailored its design to match the specification, paying particular attention to combinations of rope, drum and pulley to achieve the necessary hoist reeving arrangements for accurate load positioning over the considerable lifting heights of 12 metres on the main hoist, and 12,2 metres on the auxiliary.
A striking feature will be the airconditioned control cabin with docking station for the remote control instead of the more usual hard-wired control panel. This will allow the operator to use the same control unit for remote operation from the floor, from overlooking office, or docked within the cabin as an integral part of the cabin’s dashboard.
There will be digital read-outs
from hoist loadcells, while an independent pendant control will provide back-up and additional flexibility.
An ultrasonic anti-collision system will reliably prevent accidental contact with the existing mill house crane that will remain in the bay.
Other features include frequency drives on the long travel, cross travels and hoists, full-length walkways with fiberglass grating on both sides of the crane, IP65 brakes, IP65 panels, stainless steel fasteners, floodlights, safety lights and siren, full seam welds with rounded edges, lifting lugs and a special paint finish.
Besides the installed 10-ton crane and 25/8-ton crane on order, Condra has previously delivered a monorail hoist and crawl to Tongaat Hulett’s Zimbabwe mill.
Delivery of the new 25/8-tonner is scheduled for April 2025, with installation and commissioning to be executed by authorised agent Natal Cranes & Hoists.
Condra, +27 (0) 11 776 6000, sales@condra.co.za, www.condra.co.za
Manufacturing and Modification of Cranes
Erection, Servicing & Load Testing of Cranes
Sling Inspection
Designing of Electrical Panels
Factory Maintenance
Supply, Installation of Standard & Specialized
Radio Control Systems
Hiring of Mobile Cranes and Load Test Weights
A Service That Meets The Requirements of Our Clients
Provide Well Managed, Trained and Motivated Personnel
Meeting any Regulatory and Statutory Requirements
Applicable to Our Business
The Development and Maintenance of a QUALITY SYSTEM
Designed to Ensure Continuous Improvement and Meeting
The Requirements of CertX SA ISO 9001 : 2015
HENRY
DONAVON
Digitalisation is transforming processes across industries and changing how businesses operate. Around the world, organisations are increasingly embracing digital tools and platforms to enhance efficiency and innovation - and the lifting industry is no exception. Leading this shift is Mycrane with its newly launched Marketplace solution. Lifting Africa finds out more about this game-changing development.
As the world’s first global platform for online crane rental, Mycrane has been at the forefront of innovation in the lifting industry.
Three years ago, the company was founded with a clear vision: to unite global lifting equipment and create an ecosystem for the crane industry.
This is embodied in its innovative rental platform, which operates much like Uber - but for cranes, explains founder and CEO Andrei Geikalo.
“We were very ambitious in what we wanted to achieve, and that was to assemble the largest fleet of cranes available for hire globally,” he says. In 2024 the company announced that it had reached an impressive inventory of more than 12,000 lifting machines.
For Geikalo, however, it is about more than just the numbers. “It has been essential for us to change how crane rentals are conducted. We have more than 1500 registered crane rental companies offering lifting equipment on our platform, which has made doing business easier. Mycrane has eliminated the need for cumbersome offline inquiries by offering an easy-to-use, digital solution for finding the right crane for the job.”
More recently, the company has expanded its offering by introducing its newest platform – Marketplace.
It draws on the strengths of the Mycrane crane rental platform. Companies - or individuals - can now buy and sell used and new lifting equipment on the Mycrane Marketplace, which promotes a shift from low-volume and costly trades to numerous, cost-efficient sales transactions.
equipment,” says Geikalo. The Mycrane Marketplace sells lifting equipment, including mobile, crawler, tower, and speciality cranes, aerial work platforms and other lifting equipment.
“The Mycrane Marketplace is particularly valuable to individuals and small and medium-sized enterprises (SMEs), who will be empowered by the ability to source the right equipment at the right price – wherever they are internationally,” he says.
“The goal is to streamline the buying process, increase transparency and choice, and create a robust trading platform to benefit the entire industry.”
Unlocking Africa’s potential
Mycrane has achieved significant success across several emerging markets, with India and the Middle East standing out as fast-growing regions where Geikalo and his team continue to gain momentum.
Now, they have set their sights on Africa, recognising it as the next frontier for expansion and innovation in the lifting industry.
According to Geikalo, Africa presents a unique crane and lifting equipment industry opportunity. “The continent has immense infrastructure demand, driven by population growth and large-scale investment projects like LNG developments,” he says.
“Annual growth in the lifting equipment sector is expected to reach around 6%, with countries like Ethiopia alone projected to grow by 5% annually over the next five years.”
No subscription fees apply; only competitive fees are payable after a sale.
“Just as we’ve made crane rental easy and accessible for all, we now want to democratise the equipment sales process by supporting fast, global trading and providing access to a wide range of keenly-priced
However, Geikalo acknowledges the challenges businesses face in Africa. “Identifying suitable equipment can be chaotic due to limited local suppliers and fragmented markets. A lot of the equipment is prohibitively expensive, and brokers often dominate the industry,” he says.
Mycrane’s Marketplace is designed to address these issues by aggregating supply and providing a modern, user-friendly digital platform. “We’ve spent time in markets like China and now have a dedicated Chinesespeaking specialist to work with sellers,” says Geikalo. “This enables us to bring our users competitive pricing and better options.”
The platform allows African companies to connect with international equipment providers, streamlining the procurement process. “With our global footprint,
users can compare bookings, filter transactions by price, and choose exactly what suits their needs—whether it’s a five-year-old crane or a more affordable option from the Middle East,” says Geikalo. “It’s all about empowering businesses with the tools to make informed decisions.”
Addressing rising costs and lead times Geikalo emphasises that the high equipment and materials prices often inflate project costs in Africa.
“These factors exaggerate the rising project costs, but Mycrane can help reduce some of that burden,” he says.
One significant advantage the platform offers is access to used equipment. “Extensive lead times and shipping delays can be major hurdles in Africa,” says Geikalo. With Mycrane, businesses can find used equipment that is widely available and can be delivered to their sites much faster. This not only saves time but also significantly reduces costs.”
Further benefits include the ability to filter lifting equipment by age and condition, obtain inspection reports, and verify crane documentation.
“We are also able to offer logistics and transportation services, facilitating the sales process to final delivery at the customer’s project site anywhere in the world, as well as insurance and leasing (finance) to fund the purchase,” he says.
Geikalo, however, points out that Mycrane’s focus will always be on cranes. “While there’s a wide range of construction equipment, cranes are critical to lifting operations.”
“This market requires more engineering expertise and complexity than many others. It’s a significant target, with crane rentals accounting for up to 30% of overall site
equipment expenditure.“
“My team and I have hands-on experience in the field, allowing us to understand the market’s needs truly. By focusing exclusively on cranes, we can bring real value to our customers, offering a diverse range of cranes.”
He says that by providing a platform that connects businesses with equipment that meets their specific needs, they can streamline operations and alleviate some of the challenges often experienced when renting or buying cranes.
MYCRANE, Info@my-crane.com, www.market.my-crane.com
Now, more than ever, businesses operating in the materials handling sector are expected to reduce their carbon footprints by adopting more environmentally-friendly practices, especially when it comes to energy consumption.
Not only is this the right thing to do in a world where climate change continues to threaten livelihoods, it is necessary to ensure South Africa meets its legally binding commitment - under the Paris Climate Accords - to cut emissions from 442 million tonnes in 2020 to between 350 and 420 million tonnes by 2030.
For warehouses and mining and
industrial operations, this means streamlining work processes and using machinery that helps reduce carbon emissions and the time it takes to complete work.
This is where electric forklifts come into their own, offering several significant advantages over their diesel counterparts. Not only do they produce zero emissions during operation, they generate less
noise compared to diesel-powered machines.
Acting National Operations Manager of Heavy Lift, a division of CFAO Equipment SA, Lenny Naidoo, says the uptake of electric forklifts in South Africa has been fairly slow.
“Challenges with energy supply, due to load-shedding or load reduction, have played a significant role in this. With the country’s efforts to stabilise the energy situation and the Energy Minister’s recent announcement at Energy Africa Week that there will be greater focus on renewable energy, we expect to see more operations adopting eco-efficient machines.”
Not only do electric forklifts make sense from an eco-conscious perspective, they cost less to operate. This is because when electricity is stable, it generally costs less to charge an electric forklift than to refuel with diesel. They are also made up of less moving parts, making them less costly to maintain.
Naidoo says one of the eco-stars of CFAO Equipment SA’s Heavy Lift division is the Konecranes E-VER electric forklift, which
incorporates Ecolifting innovations that are aimed at reducing fossil fuel emissions without any loss in performance.
“The E-VER has a fully electric driveline that can help eliminate fossil fuels from any operation and cut energy consumption by up to 70%. With zero CO2 tailpipe emissions into the atmosphere, the forklift is more sustainable for people, the workplace and the environment.”
The machines use a lithium-ion (Li-ion) batteries that power the electric motors for traction and hydraulics. These batteries take less than an hour to charge, which means a battery break is as short as the average lunch break.
Naidoo says in addition to being quick to charge, lithium-ion batteries last longer – between five and 10 years – with opportunitycharging reducing the need for a full charge and extending battery life.
“They also have an almost flat discharge curve, meaning that full power is available until the battery is empty; require virtually no maintenance; and can be charged anywhere.”
A battery management system (BMS) constantly monitors battery condition and a thermal management system (TMS) always keeps it at the right temperature.
The latest BMS software allows operators to pre-heat or -cool the E-VER when connected to the grid and have it ready for operations whenever needed.
Naidoo says these heavy-duty electric forklifts are built with durability in mind. “Nothing has been compromised because the forklift is electric. The electric motor is powerful and delivers impressive lift capacity and speed, making the machine capable of handling a wide range of material handling tasks. Its strong lifting ability, even at maximum capacity, ensures that it can perform in
demanding environments, such as warehouses, manufacturing plants, and distribution centres.
“Moreover, the Konecranes E-VR forklift is designed for continuous operation, with fast charging times and long-lasting battery life, making it suitable for multi-shift operations.”
The E-VR’s low centre of gravity, along with its advanced stability control system, helps prevent tipping, even when handling heavy loads. The forklift also includes intuitive operator interfaces, with clear and easy-to-understand displays, which contribute to greater control and awareness during operation. In addition, its electric powertrain means fewer vibrations, resulting in smoother handling and reduced operator fatigue. This leads to a safer and more productive working environment.
Naidoo says the multitude of benefits offered by the E-VR make investing in the machine a nobrainer. “For businesses looking for a greener, more cost-effective and high-performance material handling solution that helps them comply with environmental regulations, it is the obvious choice.”
CFAO Equipment SA, +27 (0) 11 571 0200, info@cfaoequipment.co.za, www.cfaoequipment.co.za
Bobcat revolutionizes construction with new 1-2 t mini excavators at Bauma 2025
Bauma 2025 will host the world premiere of Bobcat’s new, groundbreaking 1-2 t mini excavators and the latest upgrade of the E88 mini excavator, the top-of-the-range model in Europe.
Bobcat will also demonstrate how it is bringing its world-famous, cutting-edge technologies to the jobsite of the future.
From the RogueX and RogueX2 autonomous loader concepts, the TL25.60e electric telehandler concept and electric machines such
as the T7X and S7X compact loaders and the E10e and E19e electric mini excavators, visitors can see how exciting developments are moving ‘from concepts to customers’.
Over 30,000 Units Retailed
“The new 1-2 t mini excavator models build on the successes
of the previous generation of machines with well over 34,000 units already retailed. After 3 years of development, the new models, featuring over 500 new components, will be available in the European, Middle Eastern and African (EMEA) markets later this year. A team of more than 50 engineers and designers have worked on the new designs, with over 80 customer visits to collect the scope, with ride and drive sessions with operators to validate prototypes, forming part of over 20,000 hours of testing and validation work,” said Robert Husar, Product Line Director for Bobcat in Europe, the Middle East and Africa.
The new generation of 1-2 t mini excavators includes the E16, E17z, E19 and E20z models. The line-up offers new levels of performance and features, a fresh look and is designed to meet the specific needs of EMEA customers. Moreover, the new generation comes with many new advanced features, so far only available on larger excavators.
New Engine and Load-sensing Hydraulic System
At the heart of the new 1-2 t mini
excavators lies a cutting-edge powertrain, featuring a robust, upgraded engine seamlessly integrated with a new, highperformance load-sensing pump bundled with a closed centre, flow sharing hydraulic system. This sophisticated combination, typically reserved for larger excavators, delivers unparalleled responsiveness and efficiency.
“The brand-new hydraulic system allows operators to smoothly operate multiple functions simultaneously. Even when operating attachments that demand substantial hydraulic power, such as a flail mower, operators can now seamlessly perform multiple functions simultaneously. This includes driving, slewing and lifting with smooth precision,” continues Robert Husar.
The E88 Mini Excavator: Reimagined and Refined
“Complementing the changes at the smaller end of our mini excavator range, we will be showing a new enhanced version of our top-of-the-range E88 9 t
mini excavator, offering enhanced operator comfort, an improved fit and finish, additional standard features and the availability of multiple predefined configurations,” highlights Robert Husar.
The increased level of operator comfort results from the use of the Fritzmeier cab also utilized on Bobcat’s popular E60, 6 t mini excavator model. This cab offers improved window and windscreen opening and closing, reduced noise and vibrations, as well as additional standard features and options. These include Direct to Tank and an intermittent wiper – standard in all configurations; a rear-view camera – optional for machines with a 7-inch display; and a new Radio FM/ AM/DAB/Phone Ready function –included in some specifications as standard.
Bobcat, the leader in innovation, is constantly pushing the boundaries of construction equipment. The company recently introduced the TL25.60e, an electric telehandler concept designed to exceed the
power and performance of its diesel counterpart while emitting zero emissions to offer a more sustainable solution.
Bobcat offers its electric mini excavators across global locations, allowing operators worldwide to accomplish more on environmentally sensitive worksites or indoors where exhaust fumes are restricted.
In North America, Bobcat offers the all-electric T7X compact track loader, designed for efficiency and versatility, as well as a zero-turn mower to enhance landscaping and groundskeeping operations.
Furthermore, at Bauma, Bobcat will present innovative concepts like the RogueX2, an autonomous compact loader, and the S7X, the world’s first all-electric skid-steer loader.
Both the RogueX2 and S7X remain in the research and development phase.
Bobcat, www.bobcat.com
For 25 years, Combilift has been revolutionising the way companies handle and store goods. Our pioneering product range of multidirectional, articulated and pedestrian forklifts, straddle carriers and container loaders allows you to manoeuvre long loads safely, reduce aisle widths and increase the amount of space available for storage.
To find out how Combilift can help you unlock every inch of your storage space.
The JLG® G5-18A telehandler has undergone a significant refresh. As part of the product changes, the model nomenclature has changed from G5-18A to 519.
The new 519 telehandler delivers a range of enhancements to boost productivity, operator confidence, and serviceability on the job site.
Improved load chart
The 519’s load chart has been optimized, expanding the working zone at maximum lift capacity and forward reach. This allows operators to work more confidently when handling heavier loads at extended reach.
Advanced control system
The new control system enables additional productivity-boosting features, including Load Stability Indicator (LSI), Seatbelt Engagement and Operator Presence (SEAOP) and enhanced diagnostics through JLG’s ClearSky Smart Fleet™ IoT (Internet of Things) platform.
LSI senses when the telehandler reaches forward load capacity, while SEAOP integrates seatbelt engagement assurance and operator presence functionality, using visual and audible alarms and limiting machine functions, as well as a high-visibility orange seatbelt.
Remote diagnostics and improved troubleshooting provide richer telematics and connectivity data.
Powerful yet efficient engine
The 519 is powered by a Deutz 2.2L 60 hp diesel engine, which delivers optimized performance while improving fuel efficiency by 10-20% compared to the previous model. This helps reduce operating costs and environmental impact.
Multifunction joystick
The electric over hydraulic joystick offers greater versatility, with auxiliary hydraulic function and attachment tilt capabilities. This enables operators to take on a wider range of tasks and attachments from a single control interface.
Redesigned cab
The completely redesigned cab provides operators with a more spacious and comfortable work environment. Options like air conditioning, a multifunction display with a backup camera, and tilt steering further elevate operator confidence and productivity.
Increased serviceability
Significant reductions in hydraulic hoses and fittings (44%) enhance serviceability by minimizing potential leak points. This helps reduce maintenance time and costs.
JLG carried many important features from the G5-18A into the design of the new 519, including:
• Excellent maneuverability: Tight-turning radius, narrow width and low machine height allow for exceptional maneuverability on crowded job sites.
• Versatility: Equipped with a universal skid steer adapter, operators can use various attachments, including carriages, forks, buckets, hooks and work platforms, to perform multiple job site tasks.
With these substantial upgrades, the new JLG 519 telehandler is well-positioned to meet the evolving needs of rental companies, construction firms, and independent contractors, like homebuilders and masons, who need a robust and reliable pick-and-place machine to handle job site materials. Its enhanced performance, productivity and serviceability make the 519 a compelling choice in the 5,500-lb telehandler category.
Eazi Access, +27 (0) 86 100 3294, info@eazi.co.za, www.eazi.co.za
Unrivaled Reliability
• Fuel Monitoring
• Eco Mode System
• Automatic Pump Disconnect
Hyundai Construction Equipment is introducing the HW250A MH, a dedicated materials handler for the recycling and waste handling industries. With a choice of booms and an elevating cab structure, the HW250MH combines productivity with fuel efficiency.
The HW250MH builds on the success of Hyundai’s popular wheeled excavator range. Weighing 26.1-tonnes, the machine comes as standard with front and rear outriggers, providing maximum stability when lifting.
Equipped with a 6.5m mono boom, the handler has a 4.5m gooseneck arm as standard, for use with an orange peel grapple or a clamshell bucket. Alternatively, customers
can opt for a 4m straight arm if using a sorting grab. Maximum working height is 12m with either configuration. Sitting on a 2.8m wheelbase, the materials handler has a parallel lift cab that delivers up to 2.9m of additional height, to allow operators to see into the working area. The support frame is constructed as a box structure for maximum durability. There is a manual lift control in the cab and a second control at ground level in case of emergencies. The robust upper structure is further protected by standard side bumpers, to protect against impact and a falling object (FOGS) guard is available as an option. Twin side-mounted main lift cylinders are used for the main boom, delivering increased stability and balance, when compared to a single central cylinder. The machine is equipped with additional steps on the front outrigger and on the cab, to make it easier for the operator to enter and exit safely.
The operator’s seat and controls can be adjusted to suit all sizes of driver, with independent height
options for the seat and console. There is a high-capacity air conditioning system and the wellknown Hyundai wheeled excavator cab has extensive glazing for maximum visibility.
A 7” colour monitor and toggle switch allow the operator to select individual machine preferences. The monitor also provides realtime operating data and various diagnostic functions and can be used to display the rear- and sideview camera feed.
The HW250MH builds on Hyundai’s presence in the market and pushes into new sectors across Europe, in demolition, recycling, forestry and dockside bulk handling.
The machine benefits from the company’s expertise in the wheeled excavator market, building on that experience to deliver a dedicated materials handling solution, with the backing and support of Hyundai’s European dealer network.
Hyundai Construction Equipment, pressoffice@hyundai.eu, www.hyundai.eu
In the lifting and rigging industry, one of the most significant hazards is the dropping of equipment and components from height. Such incidents not only pose a serious risk to the safety of workers but also can result in costly damage and project delays. To tackle this issue, Green Pin has developed a catch shackle. Lifting Africa finds out more.
The Catch Shackle, co-developed with the DROPS organisation, is one of those pieces of equipment that may seem innocuous at first glance but is truly extraordinary in what it delivers. At its core, the shackle is designed to tackle one of the most persistent and hazardous issues in the lifting and rigging industrydropped objects.
While shackles are a common and essential part of lifting operations, the Catch Shackle takes this simple tool to a whole new level of safety and innovation, says Green Pin Training Manager Dennie Goris.
“By incorporating the ability to tether all components - such as the body, pin, nut and even the spring pin - the Catch Shackle ensures that no piece of equipment falls, reducing the risk of injury or death on job sites.”
The design of this shackle includes a rotating washer that allows a lanyard to attach without twisting and its safety features include a split pin and safety bolt
combination, which prevents the accidental unscrewing of components. The ease of tethering, combined with longterm durability and a customisable wiring approach, makes it a highly effective and user-friendly solution.
According to Emiel van Norel, Green Pin product manager, while the catch shackle on the surface might appear to be a standard shackle, it is the simple yet innovative modifications to that transforms it into a critical safety tool for industries such as offshore and construction, where the consequences of a dropped object can be catastrophic.
The collaboration with DROPS - an organisation dedicated to preventing dropped object incidents – further underscores this product’s role in setting new standards for safety in lifting operations. Why prevention matters
To truly appreciate the value of the shackle, Goris says it is important to consider the physics of falling objects. “A nut weighing 400 grams dropped from 5 metres can impact with the force of 40 kg. At 30 metres, that force increases to 240 kg - equivalent to the weight of a small trailer. Even with hard hats,
the potential for severe injuries, including neck trauma or fatalities, remains high.”He says a study of workplace incidents revealed that impacts from falling objects rank among the most common causes of injuries at lifting sites. In the offshore environment it poses particularly high risks. “This shackle is designed to mitigate these dangers, offering peace of mind to riggers and operators,” he says. Some of the key benefits of the shackle include that it places safety first. “IT prevents the accidental dropping of shackle bolts, cotter pins and even complete shackles. By offering attachment points for individual components, users can securely tether each piece, minimiSing the risk of components falling and causing harm,” he explains. It also allows for customizable tethering as the shackles are supplied without wiring, allowing users to choose their preferred method of securing the components. “Whether you’re securing the shackle to a tool belt or other anchoring points, the flexible tethering options ensure safety is maintained throughout operations. It is furthermore designed for both one-leg and multi-leg lifting systems, with a
working load limit ranging from 2 to 9.5 tons. This makes it suitable for a variety of lifting applications, from construction sites to offshore rigs, where the risk of falling objects is high.”
Goris points out that the galvanisation of the product ensures long-term durability, even in harsh environments.
The shackle is equipped with a rotating washer that allows the lanyard to be attached without twisting. The safety lanyards can be connected to the body, pin and nut, ensuring that every component of the shackle is securely tethered. The pin can be tethered by a safety lanyard through a hole in the body and the washer on the nut allows it to rotate freely without the risk of winding the tethering wire.
The spring pin replaces the traditional split pin, further enhancing the safety and security of the shackle. The innovative design ensures that even under the harshest conditions, the components of the shackle remain secure and attached to the lifting system.
“Our shackles are known for their robust quality and versatility,
which makes them a trusted choice across a wide range of industries,” said Goris. “They are engineered to withstand the toughest environments and built to perform under high stress and harsh conditions, ensuring reliable and long-lasting service.”
He advises that shackles should be inspected regularly in accordance with the safety standards set forth in the country of use. “Routine inspections are crucial to ensuring that shackles remain in optimal
condition and are safe for use in lifting and securing operations.”
“Adhering to the local safety regulations helps to identify any signs of wear, corrosion or damage that could compromise the integrity of the shackle and, by extension, the safety of workers and the operation itself,” he said.
Green Pin, sales@greenpin.com, www.greenpin.com
Wire ropes are hard-working components in many different applications, from mines to lifts, ports, construction sites, and drainage systems.
Ron Byrnes, Senior Technical Sales Representative and Wire Rope Specialist at Lubrication Engineers (LE) South Africa, has over 30 years of experience working with wire ropes, including working directly on major Southern African mines and for a wire rope manufacturer. He says correct lubrication of wire ropes is “absolutely critical” because wire ropes are more than just cables – they are intricate machines composed of interdependent parts in constant motion. “Wear takes place, not only between the wires, but also the strands, as a result of the linear movement within the rope.”
Without lubrication, the insides of a wire rope will corrode. Byrnes says that corrosion doesn’t automatically equate to rust. “It is also the loss in steel or steel area within the rope as the rope components scuff and fret against each other,” he explains. Correct lubrication can significantly reduce this wear, extending the safe and useful service life of the rope.
“Rust corrosion is equally important, but It is more likely to see internal wear in a rope which is very difficult to contain; without lubricant, in fact, impossible,” adds Byrnes.
Improving general wire rope lubrication practices
At many sites and in various applications, lubrication of wire ropes can be quite “hit or miss” says Byrnes, as operational teams just keep an eye on their ropes and lubricate them as and how they think is needed, and
they are only able to really assess the state of a rope and the amount of lubrication required when running a non-destructive electromechanical test.
However, Byrnes advocates for an “application theory approach to the lubrication of wire ropes”. It includes two key aspects of understanding the rope: first, how it works, what function it plays in a particular application and how it moves, and second, how the lubricant works with that movement within the rope to diminish the effects of wear and corrosion.
The South African context
In South Africa, there are both locally manufactured and imported wire ropes in operation, and these have different construction and rope designs.
The lubricant that is applied to a rope at the time of manufacturing also differs. In South Africa, it’s usually a bitumen-based lubricant. This is a coating grease that has to be heated before it can be applied because it is very hard and thick. When it is heated, it can be poured onto a rope through a funnel.
In terms of how this affects the approach to lubrication once a wire rope is in use, Byrnes says that it’s important to have a lubricant that can work successfully for the rope, regardless of the type of lubricant applied at the point of rope manufacture.
“We can’t obviously change what manufacturers do,
but what we are looking for is a perfect fit: a match of our product offering that best complements and is also compatible with what is done at the time of rope manufacture,” he says.
He recommends LE’s Wirelife® Monolec® Penetrating Lubricant 2001, that has a Timken OK Load rating of 27,2 Kg and diluent additive, to enhance the penetration of the lubricant into the rope interstices, for imported high performance compacted wire rope as well as LE’s Wirelife® Almasol® Coating Grease 452 that has an NGLI 00 grade, for round, non-spin and 6-stranded triangular ropes. This provides a lubricant that is fluid enough to be able to be massaged between the outer strands and into the core of the rope using a Viper Rope Lubricator.
A Viper Rope Lubricator is a collar with seals that is strapped down and held in place so a rope can move through it. A wire rope cleaner can be attached to the front of the system, which spins against the rope as it moves through it, removing old lubricant and cleaning it. Then fresh lubricant is applied as it moves through the Viper Rope Lubricator.
Even on ropes that have previously had a bitumenbased lubricant applied, Byrnes says that the Wirelife® Almasol® Coating Grease 452 doesn’t fling off.
Byrnes also says that in sub-zero conditions, bitumenbased lubricants become hard and brittle and fling off the rope, which causes damage. However, Wirelife®
Almasol® Coating Grease 452 functions effectively in a wide range of temperatures, from -20oC to over 120oC.
Environmental benefits
Environmental impact is another critical aspect of rope lubrication. Bitumen-based lubricants, when exposed to fire, release toxic fumes that pose significant health risks. In contrast, LE’s products are designed to meet stringent safety and environmental standards, with high flash points and reduced emission of harmful substances during combustion.
Byrnes emphasises the importance of aligning lubrication practices with the Mine Health and Safety Act and OSHA regulations to ensure worker safety and environmental compliance.
The maintenance of wire ropes is a critical aspect of operational safety and efficiency in many industries and applications.
Adopting a systematic and scientifically informed approach to lubrication can have a positive effect on the performance and longevity of these essential components, as well as safety and environmental impact.
Lubrication Engineers (LE) South Africa, +27 (0) 11 464 1735, gavin@lubricationengineers.co.za, www.lubricationengineers.co.za
Steel wire ropes, renowned for their exceptional durability and strength, are indispensable in heavy-lifting industries such as construction, mining, and maritime. At the annual LEEASA conference, Donald Coward of Engineering Concepts provided valuable insights into optimising rope design and maintenance to extend their lifespan and reliability.
Designed to transmit high tensile loads over large distances efficiently, steel wire ropes demonstrate engineering at its finest.
However, to maximise their operational life, a careful approach to design and maintenance is essential. From initial wire drawing to combating wear and fatigue, every step in a rope’s life cycle impacts its performance and resilience, said Coward, emphasising the importance of understanding the complexities of steel wire rope design, deterioration mechanisms, and strategies to optimise their longevity.
Coward explained to delegates that the journey of steel wire rope begins with the production of steel, which is subsequently drawn into rods and wires. “The wire-drawing process not only reduces the wire’s diameter but also aligns its microstructure, thereby increasing tensile strength. Precision at this stage is crucial; over- or under-drawing the wire can negatively impact its integrity
and durability,” he said.Following drawing, the wires move to the stranding phase, where they are combined into strands. Stranding requires precision machinery where numerous bobbins feed wire into a central point, forming the desired strand.
Each strand is engineered to meet specific strength, flexibility, and load requirements, using configurations such as parallel, unequal and cross lay.
In Parallel Lay ropes, all wires are closed in a single operation, with each wire laid in the same direction. This design results in varying wire lengths across layers. If the the torque is unbalanced it will cause the rope to unlay under load.
In Unequal Lay ropes, each layer is added in a separate operation. The wire lengths are roughly equal, leading to improved load sharing. However, unbalanced torque remains a concern, and these ropes can also unlay under load.
Cross Lay ropes are constructed by adding each layer in an individual
operation, with machine rotation alternating for each layer. This method produces nearly equal wire lengths but generates high-stress points where the wires cross over one another.
According to Coward, steel wire ropes can be configured with various design features to meet specific operational needs. Factors such as the number of strands, lay type and wire layering all influence a rope’s suitability for different applications.
For instance, six-strand ropes, commonly used, bear most of the load on two strands. Conversely, eight-strand ropes distribute the load across three strands, improving fatigue resistance.
Rope designs also incorporate a core wire for added stability, with additional layers or fillers enhancing flexibility and load capacity.
Advanced rope manufacturing also leverages the geometry of circles and ellipses to calculate optimal wire and strand sizes.
The elliptical theory applies for small lay angles, where long lay lengths and elliptical cross-sections provide enhanced strength. For larger lay angles, ellipsoidal crosssections can be more effective.
“The key consideration is the load being lifted and how it is distributed within the strand. When lifting, slings are often angled, causing the load to decrease at the points of contact.”
“With parallel lay ropes, the tensile load is fully realised within the strand, but when the rope runs over a sheave, the strand may collapse and experience excessive friction.”
“To address this, we twist the strands together, preventing collapse, but this introduces spinning losses.”
“Using finite element analysis, we can now identify high-stress points in a strand or wire and modify the rope design to better distribute stress. The goal is to stabilise the strand design for improved performance and durability,” he said.
Coward said despite robust design, steel wire ropes are susceptible to wear and fatigue over time. “Routine inspections are critical for detecting signs of wear and damage before they compromise safety. “Tools like magnetic rope tests can identify internal breaks, while electronic monitoring can track stress points along the rope’s length.”
“Industry codes of practice mandate non-destructive testing to evaluate rope health, accounting for different types and functions of ropes,” he said.
He said to mitigate deterioration, both design and maintenance played pivotal roles.
“Abrasion is a major factor in rope deterioration, often caused by contact with rough surfaces. Design solutions include using harder steel grades, shorter lay lengths or larger outer wires. Installation practices, such as avoiding contact with abrasive surfaces
and ensuring proper lubrication, can further reduce abrasion.” He said fatigue sets in when wires undergo repeated stress, often due to bending over sheaves. Design adaptations like changing lay ratios or selecting high-grade wire steel could extend fatigue life. Maintenance practices such as periodically cutting and shifting the rope and ensuring proper lubrication at high-stress points would also help mitigate fatigue.
“Corrosion weakens ropes, especially in marine or industrial environments. Using galvanised or plastic-coated wires provides a barrier against moisture and chemicals. Regular in-service lubrication is also essential to combat corrosion over time, said Coward.
“Mechanical damage can also happen. Improper handling can introduce damage that accelerates rope wear. To prevent this, ropes should be unrolled carefully without forming loops, and lifting devices should be used to avoid dragging the rope over sharp edges.”
For 25 years, Combilift has been revolutionising the way companies handle and store goods. Our pioneering product range of multidirectional, articulated and pedestrian forklifts, straddle carriers and container loaders allows you to manoeuvre long loads safely, reduce aisle widths and increase the amount of space available for storage.
CONTACT US TODAY
To find out how Combilift can help you unlock every inch of your storage space.
Tadano, a global leader in the lifting equipment industry, will showcase its comprehensive line of mobile elevating work platforms (MEWPs) at Bauma 2025, marking a significant milestone in its strategic expansion.
The presentation follows the company’s successful acquisition of Nagano Industry Co., Ltd., a renowned self-propelled crawler boom lift manufacturer, in February 2024.
“This expansion into mobile elevating work platforms represents a natural progression in our journey to become the global leader in the lifting industry,” says Robbert Kreber, sales leader for Tadano Utility Products in Europe.
“By incorporating these highly regarded machines into our portfolio, we’re maintaining our 100% focus on lifting equipment while meeting the growing worldwide demand for versatile mobile elevating work platforms.”
The Bauma showcase will highlight the most-extensive crawler boom lift range available, reinforcing Tadano’s established crawler legacy on its pathway to own the crawler category. This launch marks the introduction of the first complete range of boom lifts offered to the market with a traditional crawler chassis, purpose-built to address applications that require the sensitivity only crawlers can handle.
The lineup will feature both articulated and telescopic boom models designed for maximum versatility and performance:
Articulated Boom Series
Tadano articulated, or AA, models deliver precise positioning capability, the ability to lift operators straight up along walls or structures, and exceptional manoeuvrability in confined areas. Both compact models in the series feature platforms that measure 0.92 x 0.73 x 1.1 m with 150 kg capacity, as well as a reduced-tail swing design, 360-degree continuous rotation, and a 5-degree allowable tilt.
● AA-9MC: This diesel-powered model delivers 8.8-m working height and maximum horizontal outreach of 4.5 m at an up-and-over height of almost 4 m, ideal for careful positioning in tight spaces. Weighing 2,620 kg, the unit features 230-mm grey non-marking rubber tracks, offering extremely low maximum ground bearing pressure at 75,84 kPa. This makes the AA-9MC well suited for sensitive indoor and outdoor applications.
● eAA-9MC: The electric version features high-capacity maintenance-free AGM batteries and a 3-phase AC motor delivering 5 kW of rated power, with battery life that allows it to operate for three days on a single charge based on standard usage. Weighing 2,740 kg, the quiet, zero-emission model provides the same level of crawler performance as its diesel counterpart, making it ideal for indoor, underground, and urban construction applications where noise and emissions are concerns.
Tadano telescopic, or AS, models offer superior stability and extended horizontal reach for accessing hard-toreach areas, elevated by their ability to deftly traverse a broad variety of challenging terrains, including mud and sand, with a maximum 5-degree tilt capability.
● AS-12MC: With an 11.7-m working height and a 7.9-m maximum horizontal outreach, the unit features 300mm grey non-marking rubber tracks, providing 151,68 kPa maximum ground pressure. Powered by a 14.4-kW Kubota D1105 engine, the model, which weighs 5,970 kg, can handle loads up to 200 kg and offers three travel speeds of up to 2.4 km/h for efficient site navigation.
● AS-15MC-1: This dual-capacity model (450/250 kg) has a working height of 14.7 m with a maximum horizontal outreach of 11.2 m. It weighs 9,060 kg and features 400mm steel tracks with grey non-marking pads that allow for 144,79 kPa maximum ground pressure. Powered by a 17.5-kW Kubota D1305 engine, the unit can travel up to up to 2.7 km/h with three speed settings.
● AS-15MCJ: The jibbed design of this model offers additional manoeuvrability for confined spaces and a platform capacity of 250 kg. Weighing 9,610 kg, it provides maximum ground pressure of 117,21 kPa.
● AS-20MC: Offering dual lifting capacities of 450/250 kg, the unit has a 19.7-m working height with 15.4-m maximum horizontal outreach. Featuring 500-mm steel tracks with grey non-marking pads, it weighs 11,550 kg and provides 132,04 kPa maximum ground pressure. Its three-speed range can travel up to 3.3 km/h, powered by a 23.9-kW Kubota D1803 engine.
New Product Launch
● AS-23MC and AS-23MJ (4WD): Making their debut at Bauma 2025, these two dual-capacity telescopic models achieve a 22.9-m working height. Further details will be revealed at the show.
The MEWPs will continue to be manufactured in Japan, renown for its high standards of design and engineering, producing reliability and durability that can extend the machines’ rental fleet life. “These machines represent the perfect blend of Nagano’s mobile elevating work platform expertise and Tadano’s commitment to quality and innovation,” explains Kreber. “The combination of
articulated and telescopic models, along with diesel and electric power options, ensures we can meet any lifting challenge our customers face.”
The established Tadano European sales and service network will fully support this new MEWP product line, ensuring the same high level of customer support for these machines that Tadano customers expect from the world-class brand.
“The market’s confidence in these machines is already evident, with major rental company Mateco placing an initial order for fresh machines to replace their current fleet of Naganos” concludes Kreber.
This move is followed by French construction company Sueur, which added two AS-15MC models to its fleet earlier this year.
“This acquisition was an obvious choice for us,” explains Hervé Sueur, managing director of Sueur, which also operates a 35-tonne Tadano all-terrain crane. “The machines, and the support from Tadano France, have been outstanding.”
Visitors to Bauma can experience the eAA-9MC, AS20MC, and AS-23MJ models from the lineup at Booth FS.1205, where product specialists will be available to demonstrate the machines’ capabilities and discuss specific application requirements.
Tadano Group, Damien.Bizjak@tadano.com, www.tadano.com
Thank you to our partners, authorities, and the public. On the 7th and 8th of December, a major milestone was achieved in the construction of the new Lancaster Bridge along the N3 highway.
The installation of 12 precast bridge beams, each spanning an impressive 33 meters and weighing 57 tonnes, was successfully completed under full highway closures. The operation, led by Bedrock Infrastructure, marked a significant step forward in the ongoing N3 upgrade project, an initiative aimed at enhancing the capacity, safety, and efficiency of this critical national corridor.
The success of such a complex operation would not have been possible without the unwavering support of several key partners.
Bedrock Infrastructure would like to extend their heartfelt gratitude to:
• Metro Police, for their efficient traffic management and on-site support.
• RTI (Road Traffic Inspectorate), for their dedication in ensuring the safe movement of equipment and personnel.
• KZN Transport, for their assistance in securing permits and facilitating the operation.
• SANRAL, for their oversight and support throughout the planning and execution stages.
Whose efficiency, friendliness, and positive attitudes created a spirit of collaboration that ensured the operation was not only safe but also completed on schedule. The presence of professionals who went above and beyond to make this project a success was truly inspiring, and Bedrock is deeply thankful for the efforts.
new lancaster bridge
The new Lancaster Bridge is a vital part of SANRAL’s ongoing upgrades to the N3 highway, designed to improve traffic flow and safety for one of South Africa’s busiest roads. Once completed, the bridge will provide a modern, robust structure capable of meeting the demands of growing traffic volumes while supporting the broader economic needs of the region.
The precast beams, manufactured and installed by local Kloofbased Bedrock Infrastructure, are a testament to cutting-edge engineering and meticulous planning. Each beam was transported using abnormal load trucks and steerable dollies, a logistical feat made possible through seamless teamwork and
careful execution.
A huge thank you to the public We would also like to take this opportunity to thank the public for their patience and understanding during the full highway closures over the weekend. We recognize the inconvenience caused by such closures and deeply appreciate your cooperation in helping us complete this critical phase of the project safely and efficiently.
The successful installation of the bridge beams brings us one step closer to completing the new Lancaster Bridge, a project that will benefit thousands of commuters daily. Bedrock Infrastructure is proud to be part of this transformative journey and remains committed to delivering infrastructure of the highest quality for the people of South Africa. Thank you again to all involved for making this milestone possible.
Bedrock Crane Hire, +27 (0) 31 826 2310, enquiries@bedrockgroup.co.za, www.bedrockgroup.co.za
Konecranes has launched the new Konecranes D-series electric chain hoist, designed to meet the demands of industries that require high-performance lifting equipment.
With its robust construction, advanced safety features and compact design, the Konecranes D-series is engineered to prioritize safety, boost productivity and deliver long-term reliability across a wide variety of industrial applications.
Initially available in the EMEA region, with global availability and additional options planned for release through 2026, the Konecranes D-series offers lifting capacities ranging from 80 kg to 5,000 kg across seven frame sizes. Its design delivers optimal performance even in challenging environments and where space is limited, supporting industries such as manufacturing, automotive and process operations.
“The Konecranes D-series reduces downtime with its modular design and low-maintenance components, enabling proactive maintenance that saves time and lowers costs.”
“Designed for seamless integration with Konecranes equipment — including KBK workstation lifting systems, jib cranes and overhead cranes — it provides a flexible and
efficient solution for a wide range of industrial applications. Starting in March 2025, we will also offer pre-configured quick-ship hoists with standard features, pendants and trolleys available directly from stock for fast delivery,” says Klaus Möllmann, Senior Manager, LLE Product Sales and Offer Support, EMEA.
Key features of the Konecranes D-series electric chain hoist include:
• Advanced safety features: Includes a slipping clutch with speed monitoring for automatic safe stops, 24V contactor control and operating limit switches for enhanced safety.
• Quick and easy installation: Featuring a height-adjustable control pendant, “plug & lift” and “plug & drive” electric connections, ensuring easy installation and userfriendly operation.
• Wide temperature range: Reliable operation from -20°C to +45°C with the ability to perform at up to 60°C (or even more), ensuring adaptability in various working conditions.
• Low maintenance: The gearbox,
slipping clutch and brake are maintenance-free for up to 10 years (in one-shift-operation), minimizing downtime and reducing lifecycle costs.
• Versatile suspension bracket: The flexible suspension system allows easy integration into trolleys and includes several options to meet customer needs.
• Compact design: Even with its advanced features, the Konecranes D-Series maintains a compact form factor, making it ideal for operations in tight spaces.
• Status display for easy service: The 7-digit status display is visible from the outside and shows you real-time information such as operating time, status, warnings and errors.
The Konecranes D-series incorporates advanced safety features like operating limit switches, a slipping clutch with speed monitoring for automatic safe stops and 24V contactor control, which help reduce the risk of accidents and unexpected downtime. Additionally, the hoist offers accurate load positioning
and controlled lifting for reliable, efficient operations – just what you would expect from Konecranes.
The ergonomic pendant control, standard with the hoist, provides smooth and comfortable load handling. Konecranes also offers an ergonomic single-handed operation with a Manulift control unit for loads up to 500 kg. The Manulift control unit enables operators to efficiently manage the chain hoist and guide the load using only one hand, enhancing load handling efficiency. Suitable for both right-hand and left-hand operation, the Manulift can be easily customized for various tasks with a variety of load handling attachments developed to meet the specific requirements of different industries. Optional radio control systems are also available for enhanced flexibility, further helping to improve both safety and productivity.
Environmental impact considered throughout the hoist’s lifecycle
As is standard with all Konecranes material handling equipment,
environmental sustainability aspects have been considered during the design and production process of the Konecranes D-series electric chain hoist. The hoist has been developed applying the Konecranes Design for Environment (DfE) concept principles that focus on minimizing environmental impact by emphasizing repairability, durability, material selection and energy efficiency.
Manufactured at the Konecranes factory in Wetter, Germany, the hoist is produced using 100% renewable electricity. Its modular design allows for easy maintenance of individual components, while key parts, such as the gearbox, slipping clutch and brake, are maintenancefree for up to 10 years, reducing the need for replacements and minimizing downtime. Primarily made from recyclable metals like steel, aluminum and cast iron, the hoist is engineered with sustainability in mind. Additionally, its packaging is made from fully renewable and recyclable materials, reinforcing Konecranes’ commitment to environmental
sustainability throughout the product’s lifecycle.
A strong focus on customers, commitment to business growth, and continuous improvement make Konecranes a material handling industry leader. This is underpinned by investments in digitalization and technology, as well as efforts to make material flows more efficient with solutions that decarbonize the economy and advance circularity and safety.
World-class, industry-leading forklift brands are available at competitive prices with quality guaranteed.
Goscor Lift Trucks, the first ISO and OHSAS accredited forklift company in South Africa, have established a powerful reputation of being one of the largest suppliers of forklifts and materials handling solutions to the Southern African market today.
RiConnect Inc.’s cloud-based Software as a Service (SaaS) offering includes Digital Product Passports (DPP), as industry adapts to the European Union’s Ecodesign for Sustainable Products Regulation (ESPR).
RiConnect is dedicated to simplifying and digitalising the processes around compliance and traceability for equipment management.
Having pioneered utilisation of radio frequency identification (RFID) chips, allowing end users of lifting and other equipment to keep up with pre-use checks and unique identification numbers, it has again pivoted towards global regulatory developments, specifically with customers and the ESPR in mind.
In short, the ESPR aims to significantly improve the sustainability of products placed on the EU market by enhancing their circularity, energy performance, recyclability, and durability.
Effective last year, it replaced the Ecodesign Directive 2009/125/EC and establishes a framework for setting eco-design requirements on specific product groups. It expands the Ecodesign Directive to cover virtually all physical products; and reinforces the range of eco-design
requirements that can be set. A DPP is a data management tool that records a product’s lifecycle information, including material composition, energy performance, maintenance guidelines, and recycling methods. A DPP promotes compliance and transparency, while improving resource efficiency and supporting circular economy goals.
Rob Whitehurst-Maiden, sales manager at RiConnect UK Limited, said: “We fully support the move to ESPR. It provides a critical legal framework for global digitalisation and sustainability, perfectly aligning with RiConnect’s DPP functionality.”
“We believe this is not only a regulatory requirement but also a significant opportunity to drive industry transparency and enhance resource efficiency.”
“RiConnect is committed to transforming compliance demands into business value, helping companies remain competitive in an ever-changing market.”
RiConnect’s DPP is based on four pillars:
1. Assignment: each product’s DPP
is tied to a unique identifier and automatically generated via RFID technology.
2. Update: DPP data is fixed upon generation, ensuring compliance by preventing manufacturers from altering product data post-sale.
3. Use: end users can access product information by reading RFID tags with a smartphone, without additional applications.
4. Disposal: the DPP provides clear recycling and reuse guidelines to maximise resource utilisation.
The breadth of the system reflects the ESPR’s wider scope beyond energy-related products including, say, anything from air conditioners to refrigerators. Practically, it means that every company must consider lifecycle compliance and transparency for their entire product portfolio.
RiConnect’s DPP solution is highly adaptable to different industries, offering complete product information management to address this pivotal regulatory shift. Whitehurst-Maiden said: “Inevitably, ESPR will accelerate the global shift towards digitalisation.
For example, industrial lifting equipment manufacturers have already adopted RiConnect’s DPP solution to ensure compliance with EU regulations, while significantly enhancing supply chain transparency and efficiency. These success stories demonstrate how [DPP] adoption will become a global standard.”
RiConnect employs a multi-layered approach to monitor global regulatory activities:
• Professional monitoring: using platforms like EUR-Lex and networks from international industry associations to track updates, focusing on environmental and sustainability regulations.
• Internal compliance experts: an in-house compliance team analyses and internalises the latest international regulations to ensure the platform remains aligned with global standards.
• Partnership collaboration: collaborating with patent firms and technical experts ensures that technological innovations meet current and future regulatory requirements. The strategy enabled the company to lead customers
on conformity with other global regulations, such as the U.S.’s Resource Conservation and Recovery Act (RCRA), focusing on waste management and resource efficiency; and Japan’s Basic Law for Establishing a Recycling-Based Society, which emphasises recycling and reuse.
Whitehurst-Maiden added: “While these regulations are impactful, the ESPR is the most comprehensive and influential, serving as a global benchmark. We encourage businesses to adopt RiConnect’s DPP solution to stay ahead of regulatory changes, enhance brand trust, and improve operational efficiency.”
ESPR compliance is another example of the versatility of the RiConnect Compliance Management System that can be applied across a myriad of products and applications, upheld by the CTSN — compliance, traceability, status, net zero — concept.
RiConnect, info@riconnect.tech, www.riconnect.tech
True to the motto “Go for Solution P”, PALFINGER showcases its full portfolio of lifting solutions, services, and latest innovations at bauma 2025 in Munich. Leading the lineup is the PK 880 TEC loader crane, making its world premiere at the event.
In addition, visitors can look forward to two world premieres within the TEC range of aerial work platforms, as well as another one in the FL range of truck-mounted forklifts. With these and many other product and service highlights, including the HP 20 A TEC hookloader, PALFINGER is setting the bar for lifting solutions. “At PALFINGER, we offer a full package of products, services, and digital solutions that go far beyond the physical product. During bauma 2025, we will present our latest innovations live to highlight the potential unlocked through the seamless combination of hardware and
software,” says Andreas Klauser, CEO of PALFINGER. “We are committed to providing our customers with the best possible solutions to their daily challenges. bauma in Munich will be the perfect platform to showcase what we do today and in the future.”
PALFINGER’s latest innovations take center stage at bauma 2025:
• World premiere of the new PK 880 TEC loader crane: Lifting above its class
The key highlight at bauma 2025 is the PK 880 TEC,
which is being shown to the global market for the first time.
This crane combines cutting-edge technology with the latest CONNECTED plus+ solutions to deliver bestin-class precision and lifting performance, as well as maximum uptime through valuable insights based on operational live data and additional features like advanced job planning for scheduling service work.
It will be showcased with advanced equipment, including the newly introduced tiltable crane fork, the new P6 radio remote control, and the EPU40 electric power unit that enables the crane to be operated in areas sensitive to emissions and noise.
• Aerial work platforms: The next level of platforms
In 2024, PALFINGER established its European hub for aerial work platforms in Löbau/Germany, aiming to strengthen this product line as a further strategically key product range.
The brandnew TEC range of aerial work platforms takes center stage at bauma 2025. Four models featuring working heights ranging from 19 to 28 meters will be exhibited, including two world premieres.
These powerful all-rounders in the 3.5-ton class are designed to set new standards in safety, quality, and performance standards and will be available immediately starting from bauma.
All models can be equipped with the optional eDRIVE battery pack for low-noise and low-emission operation.
• Truck-mounted forklifts: “Shift your perspective” with the FL range
Whether in urban areas or rough terrains, PALFINGER’s truck-mounted forklifts in the FL range combine performance, comfort, and safety.
As the only provider in the market, PALFINGER offers truck-mounted forklifts in all categories, enabling efficient and versatile material handling directly to the exact point of use.
Under the theme “Shift your perspective,” PALFINGER will present their updates to the FL range including another world premiere at bauma 2025.
• Hookloaders & Skiploaders: Built for any challenge
The lineup of PALFINGER hookloaders and skiploaders rounds off the product display, with the spotlight on the HP 20 A TEC.
Built for the toughest jobs, this hookloader sets a new benchmark in heavy-duty handling with advanced cab control, state-of-the-art features like memory position, and enhanced specifications.
Part of the POWER series, the HP 20 A TEC is specifically designed for efficient container handling on construction sites, making it an ideal solution for managing large waste containers and bulk materials like gravel.
Its robust, field-proven geometry eliminates linear sliding components, significantly reduces wear and tear
and minimizes maintenance requirements. Equipped with the new V Drive cab control, tailor-made, designed and customizable, it ensures intuitive operation and maximum safety for demanding applications.
Showcasing the full package of excellence in service
PALFINGER supports its customers throughout the entire product lifecycle with tailored, value-added services.
As products have become more powerful and enriched with digital solutions, PALFINGER’s service portfolio has also evolved.
At bauma 2025, visitors can experience a showcase of service highlights such as PALFINGER CONNECTED, a digital platform for efficient fleet management, which achieves maximum uptime by analyzing machine data and relevant usage information.
As well as PALFINGER’s hub for technical documentation and configuration PALDESK, the VR1 training simulator for optimized operator training, and service contracts.
Visitors also discover more about PALFINGER’s extensive partner network, which delivers a high level of service quality, speed, and expertise.
Find PALFINGER at bauma 2025
The PALFINGER main booth is located at FN.720/12. The aerial work platforms will be exhibited at FS.1203/4.
Palfinger Southern Africa, +27 (0) 11 608 3670, sales@palfingerafrica.co.za, www.palfinger.co.za
A cutting-edge rescue simulation centre at the University of Johannesburg is set to transform emergency response training in South Africa. Designed specifically to meet the complex demands of modern rescue scenarios, this facility provides unparalleled training opportunities for emergency personnel.
The centre’s development, however, would not have been possible without the advanced lifting solutions incorporated onsite, enabling realistic and rigorous training that mirrors real-world rescue challenges.
UJ’s simulation centre, situated at its Doornfontein campus, is a milestone in emergency medical training in Southern Africa. For Connor Hartnady, one of South Africa’s most experienced emergency services and responses specialists and a lecturer at UJ’s Department of Emergency Medical Care (UJ) it is a dream come true.
Addressing the annual LEEASA conference in Johannesburg, Hartnady highlighted the importance and need of such a centre particularly considering the increasing number of natural and man-made disasters around the world “Natural hazards are on the rise, compounded by unsustainable development paths and poorly planned urban growth. In response, our updated training model emphasises faster, more
effective deployment with the right equipment and resources, enabling emergency teams to reach disaster sites promptly and fully prepared.”
Hartnady said UJ recognised the urgent need for a dedicated training centre to address the complexities and needs of modern rescue operations.
“As an academic institution, we have a responsibility to intervene in the growing disaster landscape. By developing a world-class training environment for future emergency responders, we are able to train skilled professionals who can respond swiftly and effectively to real-life crises,” he explained.
“This centre enables us to equip our students with critical handson experience in complex rescue scenarios, preparing them to save lives and manage risks in any situation.”
The project received a R25 million macro infrastructure grant from the Department of Higher Education, enabling UJ to design and construct a rescue facility tailored to its
unique requirements. The centre serves as a critical resource for the university’s one-year and two-year emergency medical programmes, the flagship four-year bachelor’s degree in Emergency Medical Care, and advanced postgraduate degrees, including a master’s and doctoral programme.
This state-of-the-art facility is not only designed for students but also accommodates short learning programmes and specialised rescue training, contributing to the enhancement of emergency response across Southern Africa.
A multi-phased, advanced training environment
The project began in 2015 and has had to overcome significant hurdles over the years, including space constraints, funding challenges, the COVID-19 pandemic and fluctuations in material costs.
After facing numerous delays, including an increase in steel prices and difficulties with contractor turnover, the project is being tackled in phases with the first
phase completed this year.
The Centre has been designed to cater for teaching, learning, assessment and research of a multitude of specialised rescue disciplines. The four-storey structure includes a five-metredeep pool for aquatic rescue and survival training, helicopter underwater egress/escape training (“and dive rescue.
Fifteen metres above the pool, a helicopter fuselage suspended on a gantry crane allows for both “wet” and “dry” hoist training. It can also be adapted to provide a platform for safety training around rotorwing aircraft and patient care within the confines of a helicopter.
Within the basement of the structure, an urban search and rescue area with space for configurable confined space tunnel systems, sacrificial concrete slabs, technical search props, shoring jigs and heavy lifting props has been created. Another three-metredeep concrete trench simulator will provide a safe area for the teaching of trench rescue.
Hartnady said phase two, expected by early next year, will introduce the aviation and Helicopter Underwater Escape Training (HUET) capabilities, and phase three will expand training to cover offshore survival and SAMSA maritime rescue.
The Centre’s engineering features are groundbreaking, especially its helicopter rescue simulator, said Ronleigh du Raan, a crane designer and project manager. The simulator integrates an overhead gantry crane capable of lifting and rotating a helicopter fuselage, enabling trainees to practise realistic emergency scenarios with lifelike dynamics. “The helicopter rescue simulator is a unique design, built not just for standard crane tasks but for specialised loadhandling and full rotation,” du Raan explained. Engineered with a Safe Working Load (SWL) of 4 tonnes, it incorporates essential safety features such as emergency brakes, down-draft fans to simulate rotor effects and a mechanism for
realistic 360° rotation.
Constructed from a donated Airbus AS365 fuselage, the simulator can carry up to four people and replicates both dry and wet rescue conditions. This allows responders to practise crucial skills like safe entry, exit, hoisting, and landing, all under authentic conditions.
“The simulator isn’t just a crane,” said du Raan. “It’s designed for both conventional lifting and airborne, underwater rescue simulations. With multiple attachment points, it can support a range of training needs, providing an experience that builds confidence and prepares students for diverse real-world rescue situations.”
The crane features a swivel crab arrangement with a 15.5m span, achieving maximum speeds of 31 m/s for long travel, 24 m/s for cross travel, and 8 m/s for hoisting. Given its role in personnel lifting, the crane’s structure, crab and hoists are built with a higher safety factor than standard cranes of the same SWL. Its crab includes dual hoists, each using a 2X2/1 reeving
setup, and the ropes securing the swivel crab arrangement are independently anchored to enhance safety. In the event of a rope failure, the load remains supported by the remaining three ropes.
Electrical and compressed air are fed from the crane’s crab to the swivel arrangement via cable reel drums, powering the slew drive, down-draft fans, and HUET control, enabling a comprehensive, controlled training environment.
LEEASA director and engineer, Francois Weideman, said from the outset of the project it was important to identify risk. “Risk management was imbedded into the desigh from the start to foresee and address potential hazards, from structural integrity to operator safety. The project has employed meticulous planning, quantification of risks and strict adherence to safety standards.”
LEEASA, francoisw@leeasa.co.za, www.leeasa.co.za
ECSA’s revised CPD regulations: What engineers and industry professionals need to know
In April, the Engineering Council of South Africa (ECSA) will implement updated Continuing Professional Development (CPD) regulations, which were officially published in the Government Gazette at the end of 2024. These updates are crucial for professionals in the engineering sector. Industry stakeholders are strongly advised to familiarise themselves with the changes. Lifting Africa finds out more.
The updated CPD regulations are designed to enhance the ongoing development of professionals in the various engineering disciplines, including the lifting sector.
According to Lynnette Greenwood Harris , CEO of the LMI Academy, the revised regulations will have a significant impact on the compliance process, registration renewals and the overall approach to professional development.
“It is essential for all registered engineers and relevant practitioners in the lifting sector to stay informed and ensure they meet the new requirements to maintain their credentials and stay aligned with current industry standards,” she says. “It is aimed at fostering a culture of lifelong learning ensuring that industry practitioners remain at the forefront of industry developments.”
The revisions reflect a stronger emphasis on participation in industry events, self-study and mentorship, with clear criteria set for earning CPD points over a five-year cycle. As these regulations evolve, they aim to provide a
more structured framework for professionals to remain competent and adaptable in an ever-changing industry landscape.
According to Greenwood Harris, the revised rules will impact any person who is applying for registration, re-registration or renewal of registration with ECSA. It also applies to institutions, organisations and societies. Under the new rules, all registered professionals, including engineers, technologists, lifting machine inspectors and technicians, must accumulate a minimum of 25 CPD credits over a five-year cycle to renew their registration.
These credits must be obtained in at least two of three CPD activity categories, and professionals must earn at least five credits from validated educational or developmental activities (Category 1a). According to Greenwood Harris , credits can also be earned through self-study work-based activities and contributions to engineering communities of practice. She notes that it is important for industry to know that they are expected to
record their CPD activities annually on the ECSA portal, with final submissions at least 30 days before the cycle ends.
ECSA will do random audits to ensure compliance, assessing the validity of submitted CPD credits and supporting documentation.
“CPD is a critical aspect of professional registration, as it ensures ongoing learning and adaptation to changes in the industry,” said Greenwood Harris. The changes have been designed to streamline compliance while encouraging participation in developmental and educational activities. CPD is essential for renewing your registration.
Without fulfilling the CPD requirements, your license to practice could be at risk. Noncompliance can also result in deregistration.”
The revised CPD system categorises activities into three primary areas, each with specific point requirements over the five-year period:
Category 1 (Developmental Activities):
• 1a: Attending industry events, training sessions and seminars is mandatory. These activities must be formally registered with a voluntary association or accredited provider. Participants earn 1 point for every 10 hours of learning, with 5 points required in 5 years and requires to provide proof.
• 1b: Self-study activities such as reading or online learning are now credited, with participants needing to provide proof, such as certificates of attendance. Five points are also required in this subcategory. This is a new sector in its entirety.
Category 2 (Work-Based Activities):
• 2a: Participants earn 1 point for every 300 hours of work, with a maximum of 10 points claimable over 5 years.
• 2b: Mentoring contributes 1 point for every 50 hours of mentoring annually, encouraging knowledge sharing within the industry.
Category 3 (Individual Activities):
• 3a: Membership in ECSArecognised voluntary associations
earns 1 point per year, with 5 points and requires to provide proof.
• 3b: This newly expanded category includes research, course evaluation and development, and learning facilitation. Participants must prove their involvement in these validated CPD activities. Greenwood Harris notes that the updates emphasise education and participation.
“Some may find these requirements intimidating, but they provide clear guidelines and encourage a wellrounded approach to professional growth,” she says. These changes make it easier to stay current with developments in your field, which is vital in a rapidly evolving industry.”
For lifting machinery inspectors, the changes represent an opportunity to engage more actively with their profession. By participating in structured events, mentoring, and research, LMIs can contribute to the broader industry while meeting their CPD obligations. According to Greenwood Harris , those registered with international bodies that have reciprocal agreements with ECSA may comply
with either ECSA’s CPD rules or those of the international body. In such cases, compliance with the international body’s requirements will suffice for ECSA registration renewal. “However, they must annually declare compliance and submit relevant documentation to ECSA. Exemptions are also available for professionals facing extenuating circumstances, such as unemployment or health issues.”
She says all registered persons must apply for exemptions annually and supporting relevant documentation will be required to be excused from full CPD compliance.
Greenwood Harris emphasises the importance of complying with CPD requirements. “Each individual is responsible for their professional development,” she says. “Don’t become complacent. CPD is not just a requirement; it’s an opportunity to grow and contribute to the knowledge base of the industry.”
LMI Academy, +27 (0) 11 475 5876, info@lmi-academy.co.za, www.lmi-academy.co.za
Secure energy supply for slewing cranes up to 10 metres travels. No more cable loops
The cable carrier guidelok swing GLO.S increases the safety in the operation of swing cranes. The cost-effective alternative to cable loops reliably protects the cables and thus prevents them from getting tangled and tearing off. The space-saving system thus ensures increased system availability and reduces downtime costs.
LEEASA
T: +27 (0) 64 507 6857
E: admin@leeasa.co.za
W: www.leeasa.co.za
Kempston Controls
T: +27 (0) 140 776 2888
E: holyhead@kempstoncontrols.co.uk
W: www.kempstoncontrols.co.uk
Condra Cranes
T: +27 (0) 11 776 6000
E: sales@condra.co.za
W: www.condra.co.za
Elephant Lifting Equipment
T: +27 (0)12 661 6105
E: info@elephantlifting.co.za
W: www.elephantlifting.co.za
Johnson Crane Hire
T: +27 (0) 11 455 9222
E: PeterY@jch.co.za
W: www.jch.co.za
Liebherr Africa
T: +27 (0) 11 365 2000
E: info.laf@liebherr.com
W: www.liebherr.com
Bell Equipment Southern Africa
T: +27 (0) 11 928 9846
E: susanmy@bell.co.za
W: www.bellequipment.com
Bobcat
W: https://www.bobcat.com/mea/en/ industry/material-handling www.bobcat.com
Goscor Lift Trucks
T: +27 (0) 11 230 2600
E: lifttrucks@goscor.co.za
W: www.goscorlifttrucks.co.za
Jungheinrich
T: +27 (0) 10 596 8460
E: info@jungheinrich.co.za
W: www.jungheinrich.co.za
H&H Specialized Services
T: +27 (0) 82 446 2899
E: werner@h-hss.co.za
W: www.h-hss.co.za
Morris Material Handling SA
T: +27 (0) 11 748 1000
F: +27 (0) 11 748 1093
E: sales@morris.co.za
W: www.morris.co.za
HOISTS
H&H Specialized Services
T: +27 (0) 82 446 2899
E: werner@h-hss.co.za
W: www.h-hss.co.za
Elephant Lifting Equipment
T: +27 (0)12 661 6105
E: info@elephantlifting.co.za
W: www.elephantlifting.co.za
Yale Lifting Solutions
T: +27 (0) 11 794 2910
F: +27 (0) 11 794 3560
E: crm@yalelift.co.za
W: www.yale.co.za
Yale Lifting Solutions
T: +27 (0) 11 794 2910
F: +27 (0) 11 794 3560
E: crm@yalelift.co.za
W: www.cmco.com
GregBev Enterprise
C: +27 (0) 82 854 5143
C: +27 (0) 72 395 4342
T: +27 (0) 53 285 0842
E: admin@gregbev.co.za
W: www.gregbev.co.za
H&H Specialized Services
T: +27 (0) 82 446 2899
E: werner@h-hss.co.za
W: www.h-hss.co.za
Kiloton
T: +27 (0) 861 707 707
E: sales@kiloton.co.za
W: www.kiloton.co.za
YOKE Industrial Corp
E: info@mail.yoke.net
W: www.yoke.net
Yale Lifting Solutions
T: +27 (0) 11 794 2910
F: +27 (0) 11 794 3560
E: crm@yalelift.co.za
W: www.cmco.com
IY Safety & Inspections
T: +27 (0) 82 773 7019
C: +27 (0) 82 956 3176
E: bianca@iysafetyinspection.co.za
W: www.iysafetyinspection.com
Kiloton
T: +27 (0) 861 707 707
E: sales@kiloton.co.za
W: www.kiloton.co.za
Morris Material Handling SA
T: +27 (0) 11 748 1000
F: +27 (0) 11 748 1093
E: sales@morris.co.za
W: www.morris.co.za
LOAD TESTING AND RE-CERTIFICATION
3 60 5 Services
T: +27 (0) 72 207 7443
T: +27 (0) 64 687 7270
E: sales@3605services.co.za
W: www.3605services.co.za
Cranecor Africa
T: +27 (0) 10 446 5790
E: info@cranecor.co.za
W: www.cranecor.co.za
GregBev Enterprise
C: +27 (0) 82 854 5143
C: +27 (0) 72 395 4342
T: +27 (0) 53 285 0842
E: admin@gregbev.co.za
W: www.gregbev.co.za
IY Safety & Inspections
T: +27 (0) 82 773 7019
C: +27 (0) 82 956 3176
E: bianca@iysafetyinspection.co.za
W: www.iysafetyinspection.com
H&H Specialized Services
T: +27 (0) 82 446 2899
E: werner@h-hss.co.za
W: www.h-hss.co.za
Margisia Lifting Solutions
T: +27 (0) 14 763 1849
C: +27 (0) 83 992 2222
E: info@margisia.co.za
W: www.margisia.co.za
Shosholoza Consulting
T: +27 (0) 14 495 1994
C: +27 (0) 79 391 2990
E: info@shosholoza.africa
W: www.shosholoza.africa
Yale Lifting Solutions
T: +27 (0) 11 794 2910
F: +27 (0) 11 794 3560
E: crm@yalelift.co.za
W: www.cmco.com
J Express Crane Services
T: +27 (0) 11 864 8402
M: +27 (0) 83 425 5535
F: +27 (0) 11 864 8408
E: jexpress@telkomsa.net
Kiloton
T: +27 (0) 861 707 707
E: sales@kiloton.co.za
W: www.kiloton.co.za
Kempston Controls
T: +27 (0) 140 776 2888
E: holyhead@kempstoncontrols.co.uk
W: www.kempstoncontrols.co.uk
Cranecor Africa
T: +27 (0) 10 446 5790
E: info@cranecor.co.za
W: www.cranecor.co.za
Morris Material Handling SA
T: +27 (0) 11 748 1000
F: +27 (0) 11 748 1093
E: sales@morris.co.za
W: www.morris.co.za
FB Cranes
T: +27 (0) 11 902 3271
E: info@fbcranes.co.za
W: www.fbcranes.co.za
HP Cranes Consulting
T: +27 (0) 11 740-9725/28/33
F: +27 (0) 11 740 8416
E: admin1@hpcranes.co.za
W: www.hpcranes.co.za
IY Safety & Inspections
T: +27 (0) 82 773 7019
C: +27 (0) 82 956 3176
E: bianca@iysafetyinspection.co.za
W: www.iysafetyinspection.com
CSIR
T: +27 (0) 79 887 2218
E: mininglabs@csir.co.za
W: www.csir.co.za/mechanical -and-rope-testing-laboratory
T: +27 (0) 84 506 1209
E: ndt@chimaera.co.za
W: www.chimaera.co.za
By Carpel SRL - Italy
T: + 39 (0) 39 532 0952
F: + 39 (0) 39 532 0825
E: info@bycarpel.it W: www.bycarpel.it
Condra Cranes
T: +27 (0) 11 776 6000
E: sales@condra.co.za
W: www.condra.co.za
J Express Crane Services
T: +27 (0) 11 864 8402
M: +27 (0) 83 425 5535
F: +27 (0) 11 864 8408
E: jexpress@telkomsa.net
Kempston Controls
T: +27 (0) 140 776 2888
E: holyhead@kempstoncontrols.co.uk
W: www.kempstoncontrols.co.uk
KL Cranes and Lifting Equipment
T: +267 397 4853
C: +267 71344438
E: annelieze@klcranesbot.com W: www.klcranesbot.com
Morris Material Handling SA
T: +27 (0) 11 748 1000
F: +27 (0) 11 748 1093
E: sales@morris.co.za
W: www.morris.co.za
V & S Automation/Cranes
T: +27 (0) 10 442 7478
C: +27 (0) 82 787 2343
E: victor@vsautomation.co.za
W: www.vandsautomation-cranes.co.za
RACKING &
ACROW
T: +27 (0) 11 824 1527
E: info@acrow.co.za
W: www.acrow.co.za
Lifting Placements
C: +27 (0) 61 063 1687
E: info@liftingplacements.co.za
W: www.liftingplacements.co.za
Kempston Controls
T: +27 (0) 140 776 2888
E: holyhead@kempstoncontrols.co.uk
W: www.kempstoncontrols.co.uk
Giovenzana International
T: +31(0) 20 441 3576
E: giovenzana@giovenzana.com
W: www.giovenzana.com
Kiloton
T: +27 (0) 861 707 707
E: sales@kiloton.co.za
W: www.kiloton.co.za
H&H Specialized Services
T: +27 (0) 82 446 2899
E: werner@h-hss.co.za
W: www.h-hss.co.za
RiConnect
E: info@mail.yoke.net
W: www.yoke.net
CB Lifting
T: +27 (0) 22 719 1437
E: info@cblifting.co.za
W: www.cblifting.co.za
Haggie
T: +27 (0) 11 601 8400
E: Johannesburgsales@haggie.co.za
W: www.haggiedistribution.co.za
Umholi
T: +27 (0) 11 914 2210/11
F: +27 (0) 11 914 2209
E: umholi@umholi.co.za
W: www.umholi.co.za
Combi Lift
T: +27 (0) 11 900 8010
E: victor@solutions-4u.co.za
W: www.combilift.co.za
MH Dawood Plant Services
T: +27 (0) 11 496 1007
F: +27 (0) 11 496 1198
E: info@mhdawood.co.za
W: www.mhdawood.co.za
LMI Academy
T: +27 (0) 11 475 5876
Kanu Equipment South Africa (Pty) Ltd
T: +27 (0) 11 826 6710
E: fransv@kanuequipment.com
W: www.kanuequipment.com
Manitou
T: +27 (0) 10 601 3000
E: info.msa@manitou-group.com
W: www.manitou.com
Liebherr Africa
T: +27 (0) 11 365 2000
E: info.laf@liebherr.com
W: www.liebherr.com
E: info@lmi-academy.co.za
W: www.lmi-academy.co.za
MCLS Training
T: +27 (0) 82 506 5899
T: +27 (0) 73 089 0624
E: sinky@mclstraining.co.za
W: www.mclstraining.co.za
Phakamisa Safety Consultants
T: +27 (0) 11 462 9620/1
F: +27 (0) 11 462 9620
E: potto@icon.co.za
W: www.phakamisasafety.co.za
Crane Clinic
T: +27 (0) 11 902 7379
E: reception@craneclinic.co.za
W: www.craneclinic.co.za
Palfinger Africa
T: +27 (0) 11 608 3670/1/2/3/4
E: sales@palfingerafrica.co.za
W: www.palfinger.co.za
Smith Capital Equipment
T: +27 (0) 11 873 9830
E: mail@smithcapital.co.za
W: www.smithcapital.co.za
Dymot Engineering
T: +27 (0) 11 970 1920
F: +27 (0) 11 970 1979
E: pa@dymot.co.za
W: www.dymot.co.za