
4 minute read
Special Industrial Supplies
Thorington adds that from an Original Equipment Manufacturer (OEM) perspective, in Eazi Access, Linde Material Handling saw an opportunity to leverage their service model, as well as their South African footprint to provide an unparalleled service experience to its customers.
Thorington also reveals that some two years ago Eazi Access recognised the downward trajectory of the local construction market, which has always been the company’s bread and butter. Consequently, the need to diversify was apparent, and Linde Material Handling fits into the strategy of further diversifying the product range to be able to offer integrated solutions to the market.
Green adds that one of the key strategic aims is to gain a strong presence in heavy sectors like mining. “We have been able to penetrate the mining and heavy industrial sectors, which, in recent years, have offered us an opportunity to diversify our target markets,” he says.
Thorington says a major success driver in the mining market, for example, has been the company’s approach. “We are based on customer sites, where we have integrated ourselves into the business of the customer to be a valued partner, rather than just an equipment supplier,” says Thorington.
From a support point of view, to be able to offer quick turnaround on parts supply for the new and existing brands, Eazi Access has refurbished its National Distribution Centre in Midrand which will service both South Africa and the sub-Saharan market.
The parts stockholding is around R40-million at any given time. According to Thorington, parts stockholding is a key enabler of the Eazi Access business.
“It’s a service acumen that we have developed from our rental business. When you have got so many machines out in the field, you have to develop a structure that allows you to better service and maintain them,” concludes Thorington.
Eazi Access, +27 (0) 86 100 3294, info@eazi.co.za, www.eazi.co.za
Implications of an LMI leaving
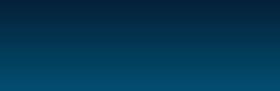
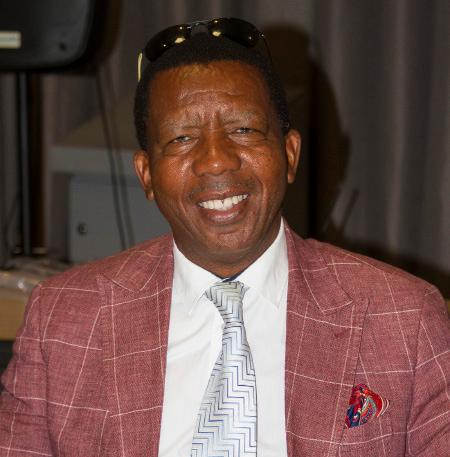
At the annual LEEASA/Lifting Africa conference Department of Employment and Labour (DEL) Director: Electrical and Mechanical, Jakes Malatse, gave clarity on what is required from Lifting Machinery Entities (LME) when LMIs leave.
Competent people are not always easy to find considering the skills challenges in South Africa. Even more so in the lifting industry where LMIs are highly sought after.
It is understandable that LMEs are concerned about what to do when LMIs leave their employ.
“As a government department we approve and register LMEs of which the criteria is known. It is not every Tom, Dick or Harry that can become and LME,” says Malatse. “You need to meet every single piece of criteria that is required and there is no way around that. The criteria is there to ensure scrutiny in terms of competence.”
He says each and every LME, when acquiring the status, need to immediately recognise and understand the value of what they have been granted. “LMEs need to therefore take care of their status or they will lose it.” Realising responsibility
Malatse said the DEL was often asked what the impact was on an LME if its LMI resigned or was no longer employed.
“The criteria determines that there must be a key LMI to be registered as an LME,” says Malatse. “The reality is that the DEL won’t know if there is a change in the company’s scope. The onus, however, is on the company to notify the Office of the Chief Inspector about what has happened, what the LME is planning to do and what the requisite competence is amongst your staff especially in terms of the LMI.”He said this clearly indicated that if an LMI left the DEL had to be informed immediately.
“Whether they are leaving of their own choice or because you have fired them or because of death. It does not matter what the reason is for them leaving.
According to Malatse the DEL is in the process of developing a code for LMEs. “This will mean that anywhere in the country or in the world for that matter when you come across a South African registered LME you will know exactly how they operate and that this is the code it follows.
It conducts itself in this manner and has these very specific standards.” What is important is that the DEL be informed,” he says. “We cannot register you without a key LMI as an LME. If you then notify the department and explain the situation, we can try to assist. Should you not notify us you can and will run into problems.”
He says any LME visited for an inspection that has not had a discussion with the department about not having an LMI will lose their LME registration immediately.
Malatse says it is therefore advisable to rather engage with the DEL about the lack of an LMI than trying to operate without one hoping that nothing goes wrong and one is not being found out. “Should anything go wrong and an incident occur there could be very grave consequences,” he says. “Should anything happen it is important to remember that the legal responsibility is on the approved and registered LME who must have an ECSA registered LMI performing the lifting tests. We will go after the LME responsible.” His advice to industry, however, is to avoid such a situation by continuously training staff.
“When you register as a LME you agree to a programme of training and development for young people coming into the industry. The key LMI in a company must be the mentor to young upcoming LMIs. Should this person then leave there is no need for extraordinary arrangements to be made. You would have been training and developing meaning you should not be running out of skill.” Department of Employment and Labour, +27 (0) 12 309 4000, www.labour.gov.za
