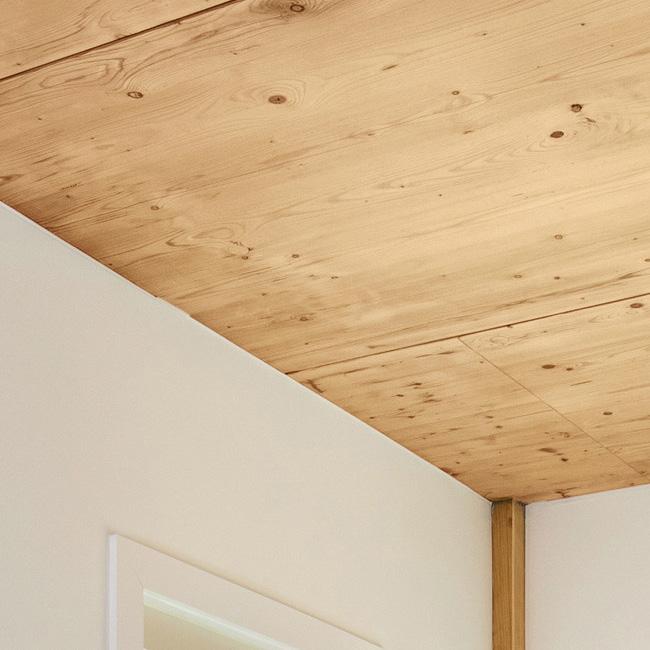
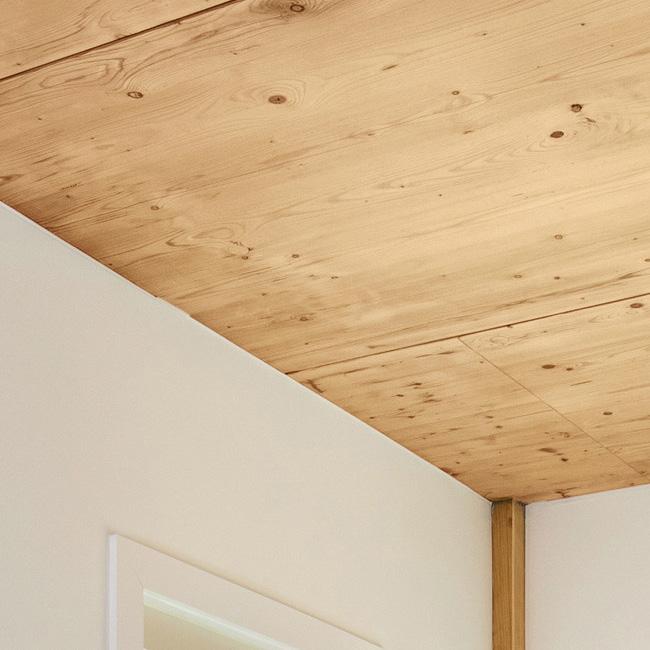
CrossLaminated Timber DESIGN INVESTIGATIONS
What is cross-laminated timber construction?
Cross-laminated timber, often referred to as CLT, is a mass timber construction method in which layers of smaller pieces of wood are glued together in perpendicular layers to create a solid panel. Though timber has been a historically popular construction type across many cultures and eras, CLT is a more recent technique developed in Europe in the mid1990s. CLT is quickly gaining in popularity due its sustainable characteristics, ease of construction, and the appeal of wood as a finish material; as building codes evolve and manufacturers and suppliers come online, CLT is becoming an increasingly attractive option in the US market as well.
A typical CLT panel contains three layers: two parallel layers on the outside and a transverse layer rotated at 90 degrees in the middle. Two layers is the minimum, and more layers can be added where greater strength is required. Once glued, the panel is largely monolithic. CLT can be used as a primary construction material, or in conjunction with other construction types such as concrete and steel. (It’s important to note that “CLT” and “mass timber” are not interchangeable terms: mass timber is the umbrella term for a variety of engineered wood products, so all CLT is mass timber but not all mass timber is CLT.)

Cross-Laminated Timber (CLT) composed of smaller pieces of wood glued into perpendicular layers (typically three layers) to form a monolithic panel
Dowel-Laminated Timber (DLT) assembles smaller pieces of wood into larger into composite shapes using dowels instead of glue or nails; lack of nails means DLT can be machine sawed
Glue-Laminated Timber (glulam) laminates smaller wood members into columns or beams using glue; creates strong, stiff, and versatile structural members
Heavy Timber both a construction type and a material. Refers to solid-sawed wood members which may or may not be used in conjunction with engineered wood products
Laminated Strand Lumber (LSL) composite wood product assembled from glued veneer flakes to create structural members
Laminated Veneer Lumber (LVL) panelized product resembling plywood in which thin layers of veneer are glued together with grains running parallel; often used as headers or beams
Mass Plywood Panel (MPP) panelized product in which thin layers of wood are glued together with the grains running perpendicular in alternating layers; often used in beams or columns
Mass Timber an umbrella term which encompasses a variety of engineered wood products made from smaller wood members
Nail Laminated Timber (NLT) creates composite wood forms by nailing smaller wood members together, either in a factory or in the field. Can be used in a variety of configurations
Parallel Strand Lumber (PSL) uses waste from other engineered wood products to create a panelized project by adhering longer pieces of veneer in layers of parallel strands
Tongue and Groove Decking solid or laminated product with wood members that interlock for ease of assembly; often used as walls, flooring, or cladding
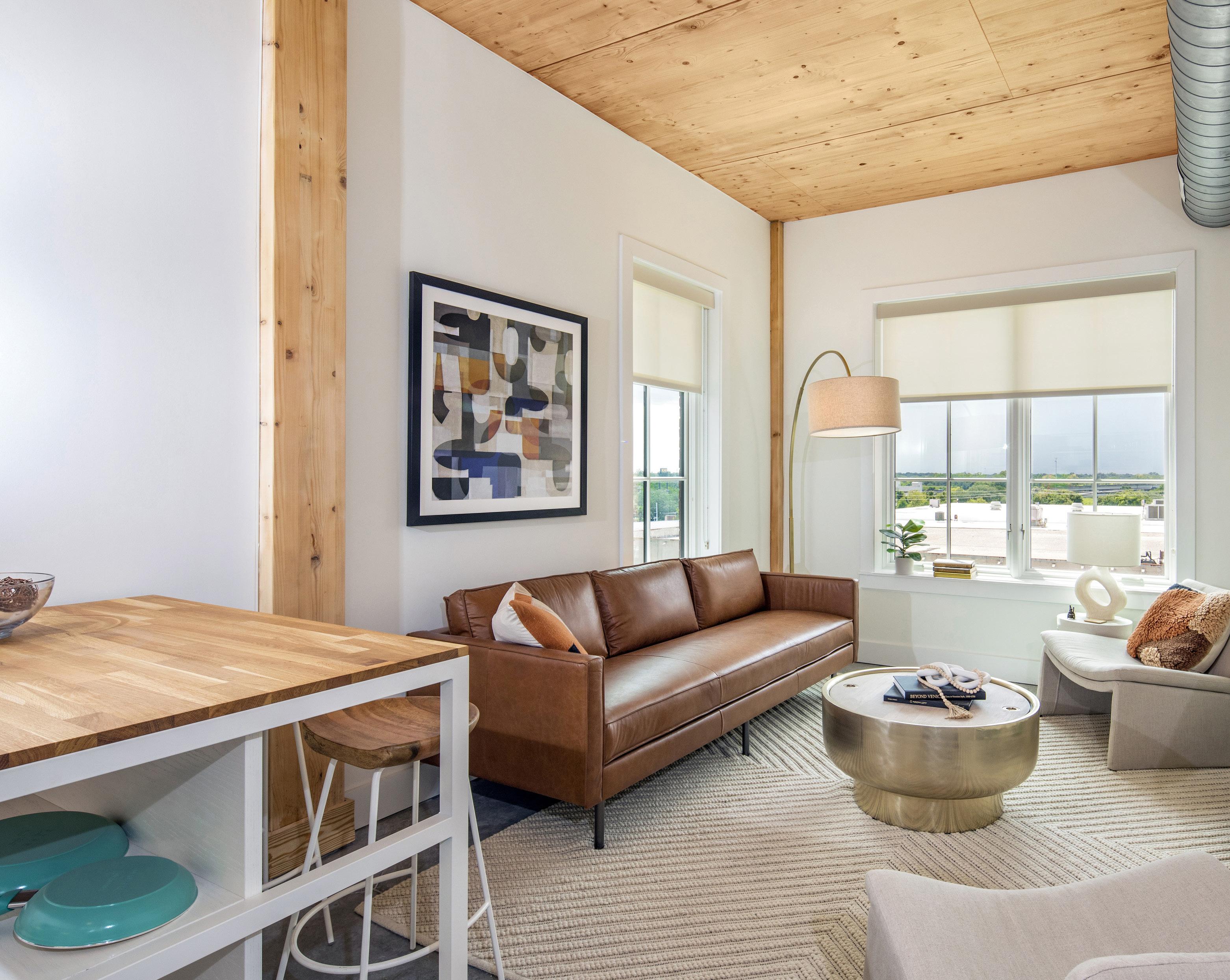
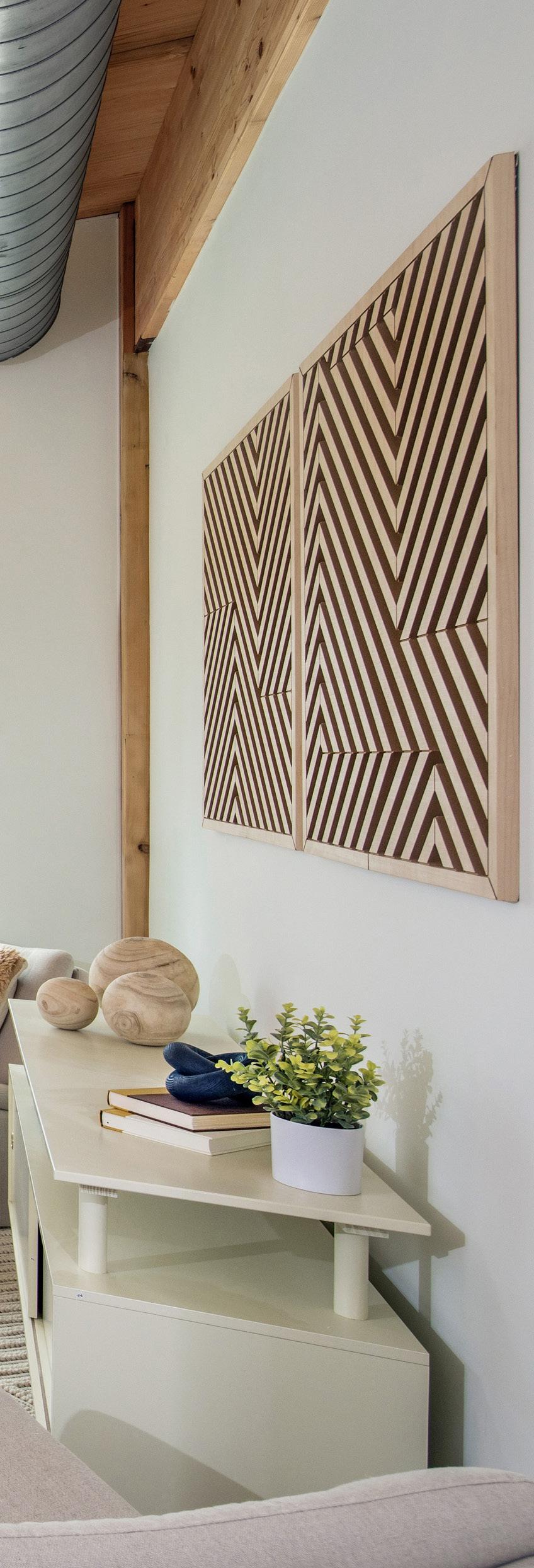
A Fast-Growing Market
CLT is gaining in popularity in the US. The market is expected to grow from $179.4 million in 2023 to $655.6 million by 2032, a compound annual growth rate (CAGR) of 15%.i Over 2,000 mass timber projects have been completed or are in design in the USii; and CLT’s sustainable benefits, flexibility, and speed-to-market are all drivers for continued growth.iii
In the Southeast, CLT is also gaining momentum. The region has an ample supply of southern yellow pine, and is in the process of retooling from an already robust timber economy to one more focused on capabilities for engineered wood.iv Changes to the 2021 International Building Code (IBC) enable the use of mass timber in IV-A, B, and IV-C construction in buildings up to 18 stories for some occupancies,v expanding the possibilities for CLT use in a variety of projects.
CLT: It’s Not All or Nothing
It’s important to note that CLT doesn’t have to be the only structural system used in a building; hybrid structures in which CLT is paired with steel, concrete, or other types of mass timber such as glulam are common. The hybrid approach can allow a project to integrate CLT for select areas or targeted uses as appropriate.
Why Choose CLT?
CLT’s popularity stems from many benefits and advantages over other construction types. Benefits can include:
Smoother, Faster Construction
For an experienced contractor, CLT can be installed relatively quickly, safely, and efficiently. Because panels are shipped to the site in prefabricated sections, the material is conducive to rapid construction and tight schedules – after the intensive initial design and coordination phase. The panels are relatively light and can be installed by fewer crew members; fewer specialized tools are required, and the mechanical fasteners eliminate the need for welding. Because panels are fabricated in a factory setting with openings and penetrations created offsite, the job site is cleaner and quieter during CLT installation, and produces less dust and waste. The lightness of the material means that smaller cranes are needed, so CLT can be a good choice for a constrained urban site.
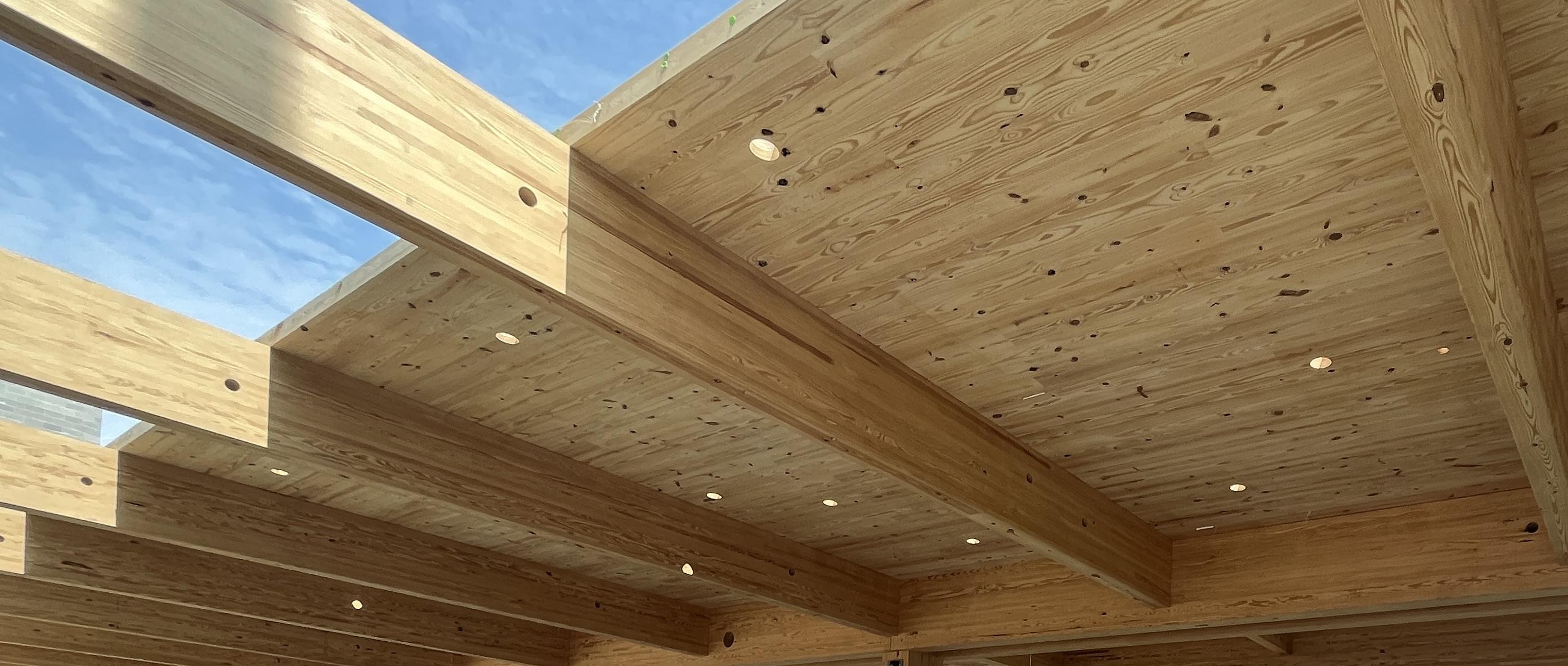
Due to their simple connections, CLT panels can be installed up to 30% faster than a comparable precast concrete structural system.vi Adding to the efficiency: using CLT eliminates the drying time associated with castin-place concrete, so vertical construction can be faster. CLT may be a good choice for a two-way spanning structural system for flooring systems that can double as a ceiling finish for the floor below. It can also be used for shaft walls
with the addition of Type X gyp board for fire rating, and can potentially speed up early stages of construction (Note: mass timber shaft walls do require intensive coordination with the elevator vendor and MEP consultants up front to avoid potential heartache later in the process.) When used in ceiling applications, CLT is self-supporting as it is installed, and can be finished as a visible surface to save an additional step.
An up-front investment in design and coordination means that CLT panels can be manufactured and installed with a high degree of precision. Panels, including perforations, are fabricated to very tight tolerances – 1/16” – 1/8” – using CNC tools in a clean, controlled factory environment.
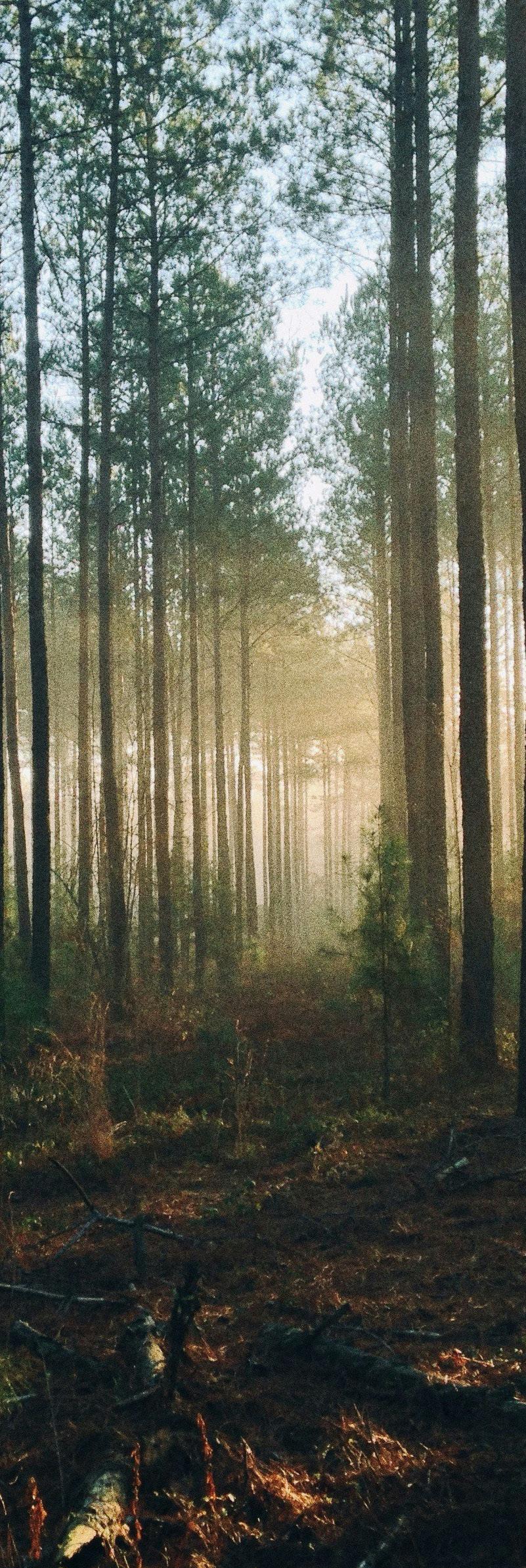
Sustainability
CLT can be an important tool in helping owners meet environmental, social, and governance (ESG) goals. When sustainably harvested, CLT is a 100% renewable, carbon sequestering resource. For projects striving to achieve net zero carbon emissions, timber is an effective carbon sink Species such as spruce and pine absorb the most carbon from the atmosphere during years 10-80 of their lifespan; beyond this stage, it can be beneficial from a carbon perspective to harvest older trees, store their carbon in buildings, and plant more trees which will absorb carbon more rapidly.vii
Sustainably harvested
CLT products also have a significantly lower global warming potential (GWP) than conventional concrete and steel structures. A 2024
study found that mass timber buildings showed an 81-94% lower GWP as compared to concrete buildings, and a 76-91% lower GWP than steel buildings.,viii though the actual reduction will vary by building typology, geographic factors, documentation methodology, particular concrete mixes, and many other factors. In addition to a lower GWP, CLT and other mass timber projects can significantly reduce building embodied carbon - by 22-50% over concrete structures.ix
CLT production also comes with minimal waste. The manufacturing process is engineered for precision cutting, so every part of the tree is used. Even the sawdust generated from cutting can be collected and repurposed. CLT panels can also be easily disassembled and reused at the end of a building’s lifecycle. One recent study found that the Recycling Potential (RP)
of a mass timber building is around 73%, substantially higher than the 34% RP of reinforced concrete.x
CLT is roughly five times lighter than concrete, but has a similar strength-to-weight ratio.xi The lightness of CLT
panels yields additional sustainability benefits. Lighter materials reduce the cost and carbon of shipping and can greatly reduce structural loads; this also reduces the size and embodied carbon of the foundation. A smaller foundation requires less
excavation, less backfill, and less time required for footings to cure. Smaller dead loads can also result in smaller structural members and smaller lateral load resisting systems.
RELATIVE GLOBAL WARMING POTENTIAL (GWP) BY CONSTRUCTION TYPE

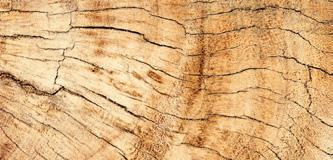
Mass timber buildings have a significantly lower carbon footprint and global warming potential (GWP) than other common construction types, bolstered by the fact that wood is sustainably harvested wood and effective at sequestering carbon.xii
Aesthetics
People are naturally drawn to the beauty and warmth of wood, which has a calming and grounding effect that has been linked to human health and wellness. Biophilia, a design strategy that deliberately brings natural elements into the built environment to help connect people with nature, creates healthier buildings with measurable impacts on health and productivity.xiii Wood is a common and desirable material used in integrating biophilic design into a space as a familiar, comforting, natural element with organic patterns and textures. Where it is appropriate to expose CLT panels within a space, structural elements can be specified for visible faces to double as a finish surface. Exposed CLT is often paired with exposed MEP systems for an industrial aesthetic. CLT generates a positive tenant response and boosts marketability.
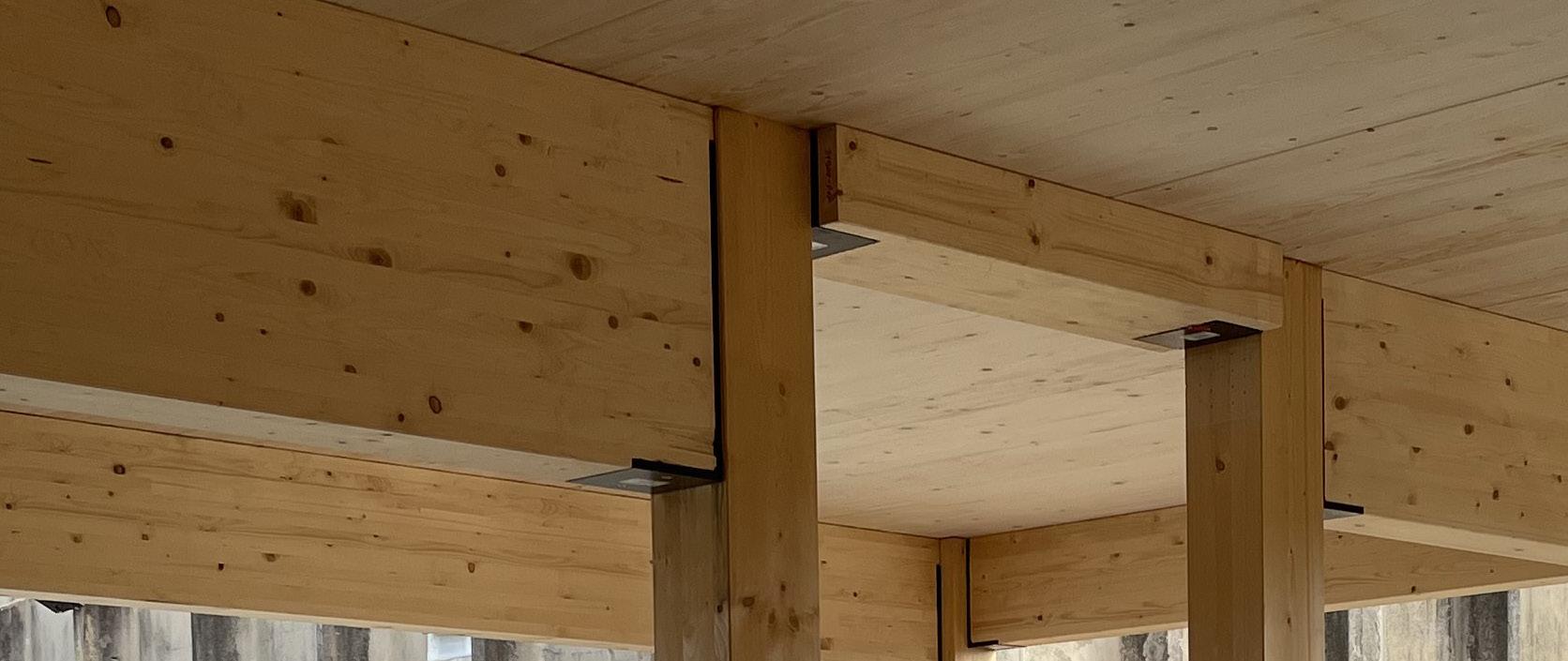
Structural Performance and Durability
CLT’s structural performance is similar to that of concrete, and it can be used for similar applications such as bearing walls, shear walls, floors, roofs, and deep beams. Panels are very stiff and accommodate loads from multiple directions, essentially acting as a two-way slab. CLT has an excellent weight-to-loadbearingcapacity as compared to other materials and carries 14x as much as steel by weight. CLT performs very well in seismic tests due to its strength and lightness, making it a potentially desirable material in areas prone to earthquakes (including parts of the Southeast US).xiv CLT buildings also have a longer expected lifespan (75+ years if properly maintained) than concrete (26-50 years) or steel (25-50 years). xv
Safety
Because CLT panels are manufactured in a factory and all openings (doors, windows, penetrations for piping and ductwork) are pre-cut, CLT reduces the potential for accidents in the field. Where necessary, CLT panels can also be modified in the field. Panels are attached with mechanical fasteners and assembly does not require welding, further reducing jobsite risks. Additionally, CLT contributes to better jobsite and tenant air quality because it does not emit harmful levels of volatile organic compounds, and where used as a finish material, does not require additional VOC-emitting treatments like paint.xvi CLT may support LEED, WELL, or other third-party certification efforts due to its positive impacts on air quality.
Indoor Comfort
Timber has long been associated with a comfortable, cozy indoor atmosphere. This attribute is partly due to aesthetic preferences, but also due to its ability to moderate humidityxvii and its low thermal conductivity. Because wood surfaces minimize thermal bridging, occupants may feel comfortable in the space at more energy-efficient temperatures.xviii Wood also has natural properties which allow it to absorb and release moisture in the air, which can help to regulate fluctuations in humidity and further support human comfort within a space. CLT buildings tend to be more breathable than other types of construction, which can reduce the risk for mold growth. In terms of indoor air quality, CLT’s composition of simply wood and no-VOC adhesives means that no toxins are being added to the indoor environment, which supports occupant health.
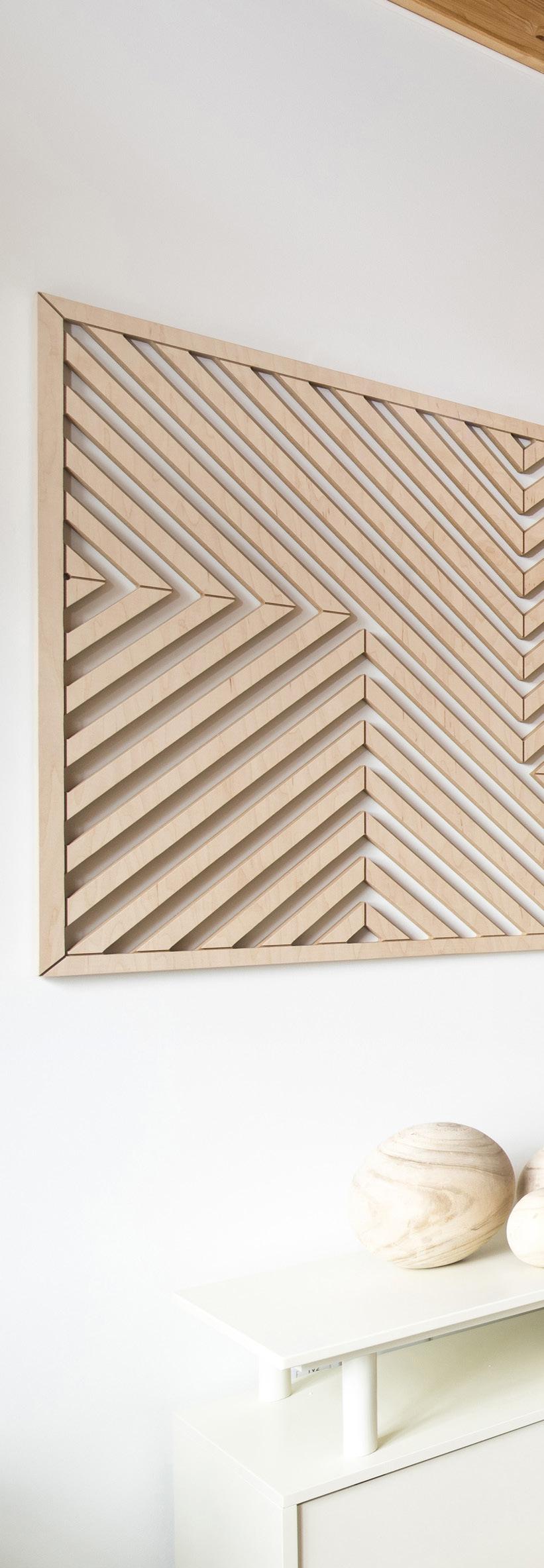
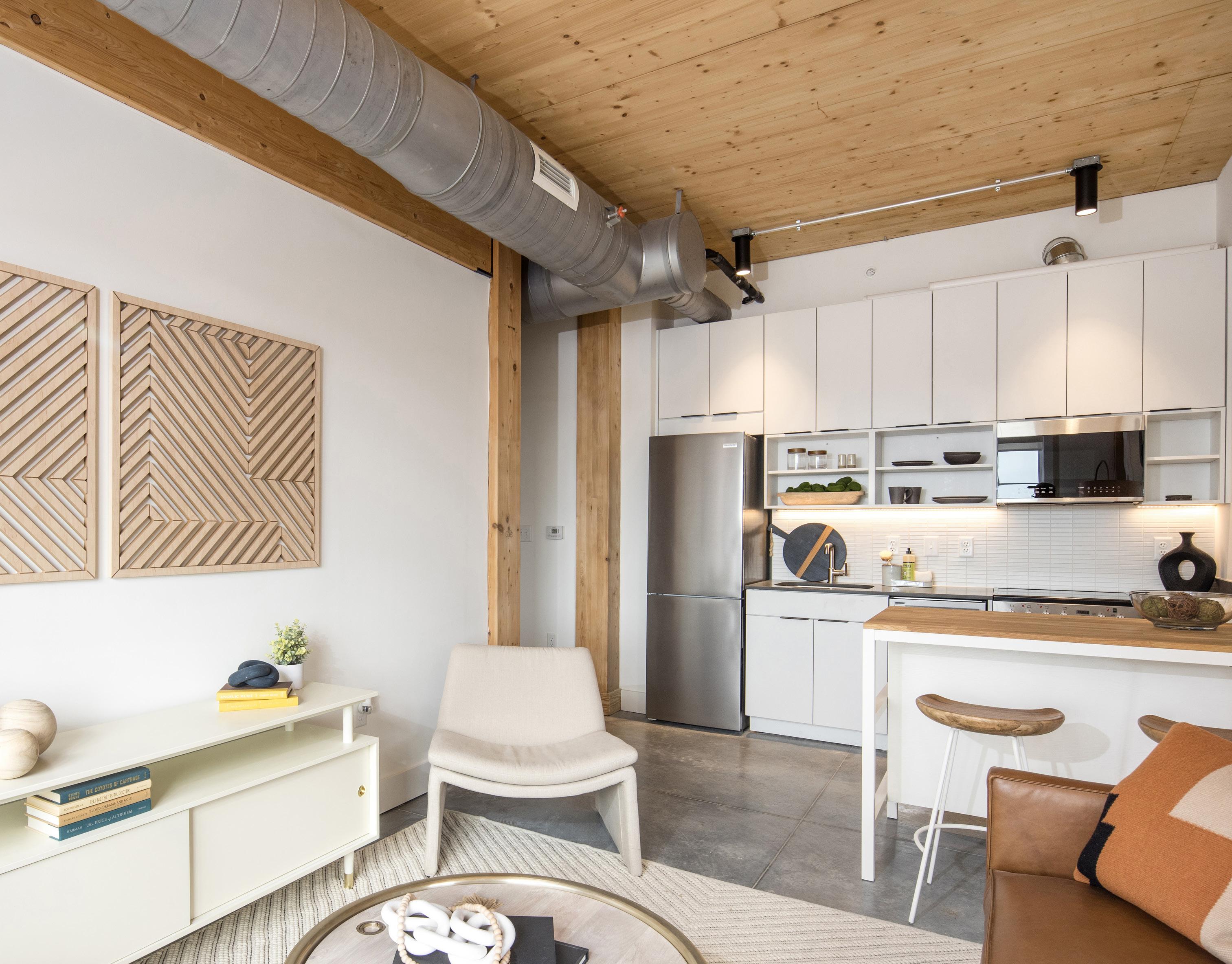
challenges of building with CLT
Acoustical and Thermal Properties
Because wood is not ideal for managing sound transmission between spaces, acoustical strategies such as sound mats, gyp or concrete finishes, or wood/concrete composite floors will be required where noise is a concern. CLT may be a poor choice for partitions for this reason. CLT panels have a low R-value and are typically paired with rigid perimeter insulation for exterior use. The thicker the panel, the lower the U-value; thicker panels may require less insulation.
Vulnerability to Water
CLT panels are vulnerable to water damage and must be protected from the elements during staging and construction to avoid staining or warping.
Possible Supply Chain Issues
Supply chain issues can impact schedule and cost; note that the closest supplier is not always the least expensive or most sustainable due to the costs and carbon impacts of shipping over land vs. shipping overseas. As more factories come online in the Southeast, more options are becoming available.
Fireproofing Requirements
As a newer material, CLT may encounter more questions from code officials or contractors and may be subject to evolving codes. In some applications, CLT panels will need to be covered with Type X gyp board for fire ratings, negating the aesthetic benefit of designing with wood.
Size Constraints
Dimensions of individual CLT panels will be constrained by allowable shipping dimensions, and building heights will be constrained by local codes (limited to roughly 18 stories.) The typical thickness of the panels means that CLT is not an ideal material for interior partitions where strength is not needed, as it leads to inefficient space use. Panel thickness will also impact floor-to-floor height, so dimensions must be communicated and coordinated with structural and MEP consultants. Penetrations should be designed and coordinated before the fabrication process begins, as creating openings for thick panels in the field is more difficult than in the factory.
key considerations
In planning and designing for a CLT project, owners and designers will need to be aware of factors which are unique to CLT construction. These include:
Code Requirements:
In the US, codes are evolving to allow for more widespread use of CLT, in more applications. The International Building Code (IBC) 2018xix allows CLT to be used in three construction types: Type III – non-combustible exterior walls, limited height and area, exposed structure and fasteners (fully sprinklered), concealed spaces
Type IV – specifically addresses mass timber /tall wood buildings
IBC 2018 W amendments: Type IV-A, Type IV-B, Type IV-C, Type IV-HT;
Exposed structure, concealed or protected fasteners, no protected/ concealed spaces
Type V – most restrictive height and area. (Almost) anything goes, fully sprinklered. Owners and designers should note that the taller the building, the more CLT will need to be covered with fireproofing materials. With current codes, CLT may be most appropriate for buildings that are mid-rise or shorter;
this may change as codes evolve. For projects where the aesthetics of exposed wood are a primary consideration, the reality might not match expectations. Teams should identify goals and priorities at the beginning of the project to determine whether code allows for full expression of the material. Many detailed resources exist for addressing code requirements, including the ANSCI/AWC NDS National Design Specification for Wood Construction and Special Design Provisions for Wind and Seismic (SDPWS), along with guidebooks provided by industry partners. Engaging local code authorities early in the design process is strongly encouraged.

Aesthetics
Manufacturers typically offer panels in multiple finish grades, and the nomenclature may vary from vendor to vendor. Designers will need to specify the type of panel required for each application and select an appropriate visual grade and desired wood species where panels will be exposed. Additional staining or finishing may not be required, but can be considered if desired. Where CLT panels
are exposed, the design of joints and detailing will also be critical, especially where firesafing is required. Some code applications will require concealing the fasteners or finishing with intumescent paint. Owners should expect a two-year maintenance cycle for exposed CLT surfaces and should check the fine print on the warranty provided by individual vendors. CLT is generally not suited to any application where panels will be exposed to the elements;
any exterior structural timber elements such as glulam columns should be sheltered under awnings or cantilevers. Some species of wood will silver over time; owners should be aware of this property and decide whether to encourage this natural process, or treat the wood with stains or sealants. The CLT Handbookxx provides detailed guidance on aesthetic considerations including visual grades, fasteners, and maintenance.
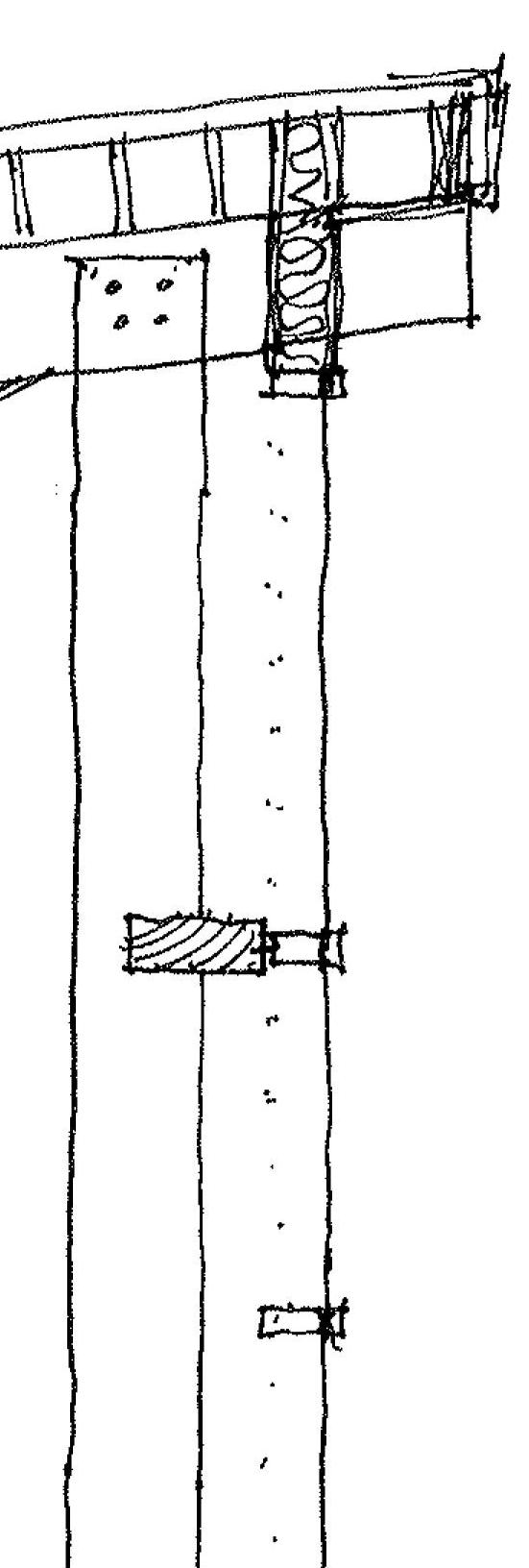
Coordination Process
Because CLT involves precision fabrication of panels in a factory setting, the up-front design and coordination process can be intense. Engaging key collaborators – including structural engineers, MEP consultants, and fabricators – early in the process is critical. All penetrations and openings must be designed before fabrication begins. To facilitate this process, teams must communicate early and often and agree on how to handle and share Building Information Modeling (BIM). If the fabricator is based in Europe, measurements will need to be converted from imperial to metric. Teams will also need to consider dimensional standards, tolerances, and shipping limitations (over both land and sea). Once the panels are installed, penetrations are
laborious to alter, and changes become time consuming and expensive; time invested in careful coordination up front will minimize issues in the field for a smoother construction process.
Fire Resistance
Due to its density, heavy timber is naturally fire resistant as it develops a char layer which can protect the underlying wood. Heavy timber structural members are typically overdesigned to include this char layer; even without additional protection, CLT can provide 30, 60, or 120 minutes of fire resistance.xxi Fire rating requirements will vary according to local codes, construction type, building height, and other factors, but with proper detailing the natural fire resistance of mass timber make CLT a safe and attractive option.
Storing/Staging
CLT components should leave the factory clean, securely packaged, and arranged in an organized manner to facilitate assembly. Up-front coordination between all project entities is necessary to communicating the order in which panels and other components will be assembled, so that they can be unloaded in the order required. Panels may arrive shrinkwrapped to protect against
moisture during transit. Items should ideally be installed as they are removed from the truck to minimize the need for storage and sorting.
Where the schedule does not permit immediate assembly, storage should be shaded to avoid uneven temperatures that could lead to splitting or warping. CLT must be protected from the elements to avoid water intrusion and staining; panels should be elevated off of the ground
for adequate ventilation, and supported at multiple points to prevent bowing. xxii Wood members should be protected from the elements until the building is dried in. This process may include wrapping exposed columns or panels to avoid water staining and other damage from moisture, or more stringent water protection measures as needed.
Shrink-wrapped CLT panels await installation at Live Oak Bank in Wilmington, NC
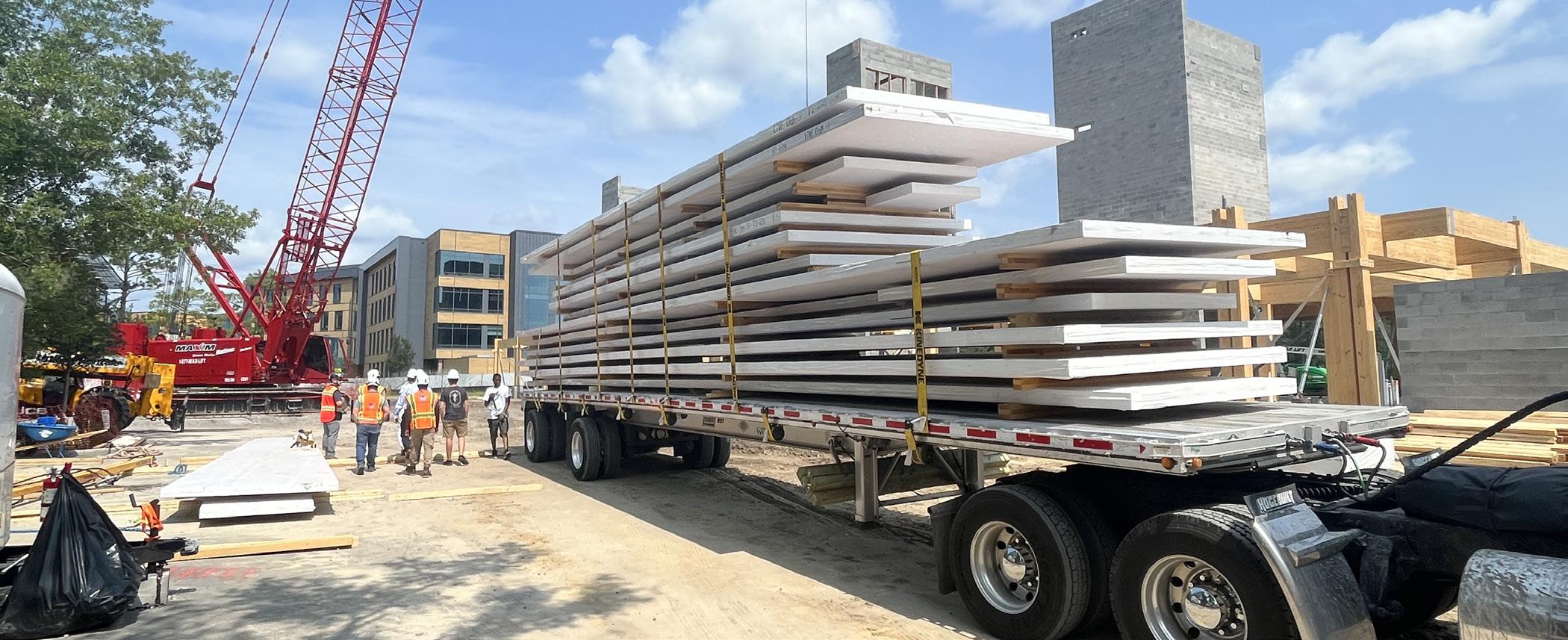
Moisture
Individual wood members for CLT panels are dried before assembly, so shrinkage should not be a significant issue. Panels are typically not glued together along the perpendicular to allow for normal expansion, and floors in a CLT building are typically suspended off the column system to allow them to move independently. Panels will naturally acclimate to the relative humidity of their environment; a structural engineer should carefully review any conditions where temperatures might vary greatly from one face of the panel to the other and design to minimize any potential bowing.
Sound Transmission
Designers and consultants should determine appropriate strategies to mitigate noise, as
CLT panels are not effective at resisting sound transmission. A thick sound mat installed across floor panels, coupled with a substantial concrete topping slab (preferably decoupled between individual spaces such as residential units), will reduce sound transmission. Gyp board on either side of the wall panels, which may be required for fire separation in some applications anyway, will further reduce noise.
Composite Floor Structure
In addition to reducing sound transmission, a composite CLT slab with a concrete floor topping structure will provide additional stiffness and stability, allowing for larger spans and better distribution of wind loads across the structure.xxiii Where desired for aesthetic reasons, the CLT slab can remain exposed to serve
as a ceiling condition for the floor below.
Detailing
The National Design Specification for Wood Construction (NDSWC) is a good resource for detailing CLT assemblies, and WoodWorks offers a library of connections (the most common fastener is self-tapping screws). CLT wall assemblies should be designed for breathability.
Cost
As a rule of thumb, buildings between six and twelve stories can be cost-competitive with concrete and steel due to the potentially accelerated speed of construction, lower labor costs, and less material required. Items that can reduce CLT costs over concrete and steel construction also include some material savings where CLT can double as
a structural and a finish material; potential reduction or elimination of masonry and concrete for fewer trades; reduced or eliminated need for tower cranes; lighter overall structure and therefore less foundation work; and up to 30% less time investment for the contractor. However, noteworthy additional costs of CLT over concrete and steel construction may include the cost of additional design assistance for coordination, the cost of the timber package and fabrication, the cost of any water/moisture protection measures, and onsite adjustments as needed.
The potential cost of a CLT project may vary depending on market conditions, building type, supply chain health, and other factors; cost estimators can provide a unique life cycle cost analysis at the beginning of a project to support informed decision making
and determine whether CLT is the right fit. Grants may be available through the US Forest Service, the US Department of Agriculture, or other entities to support CLT projects.
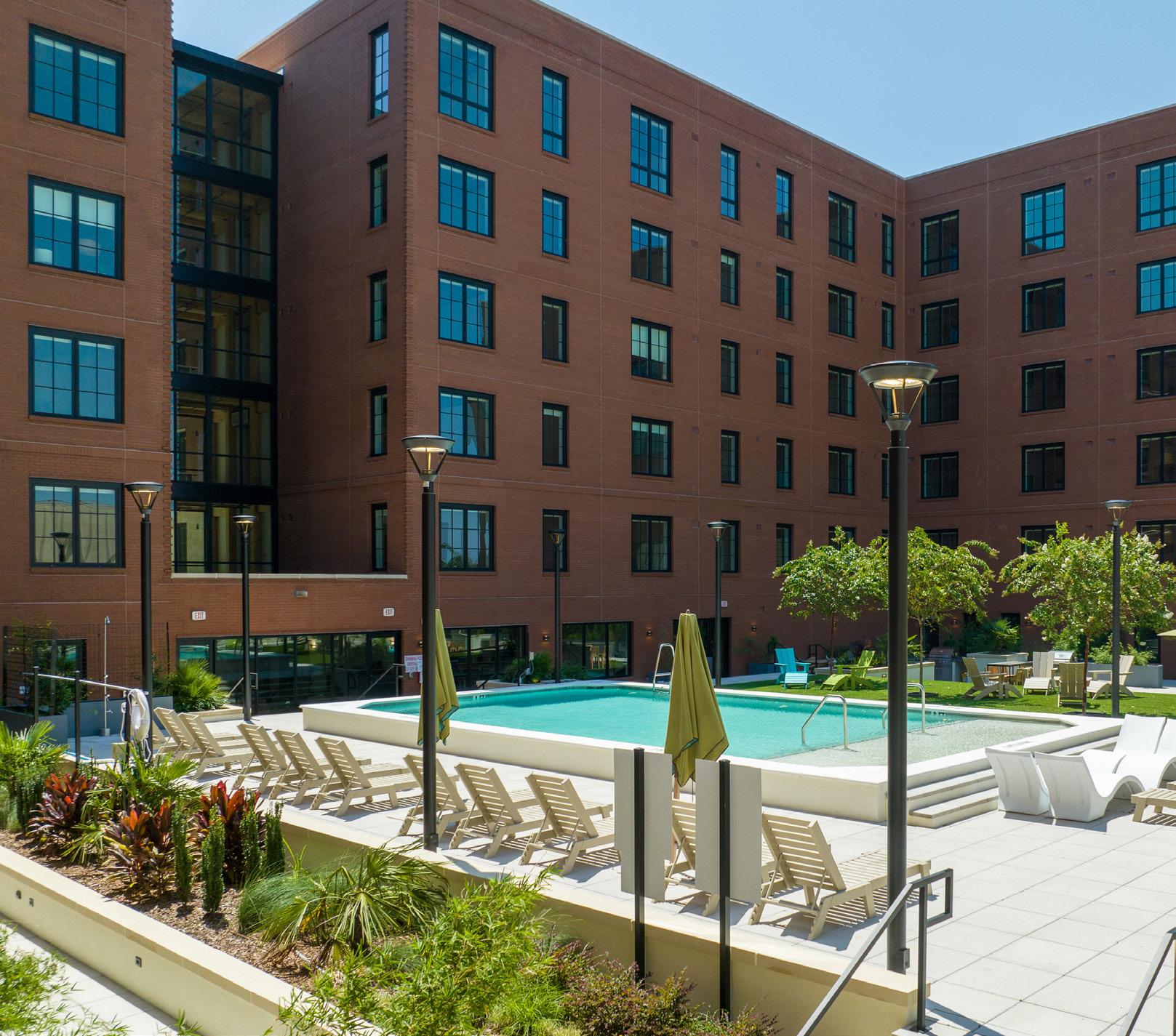
CLT structure with brick exterior cladding at Ann Street Lofts in Savannah, GA
Sourcing
Sustainability is a significant priority for many owners choosing to build with CLT. As such, teams should source sustainably harvested timber products verified by third-party certification organizations. The Forest Stewardship Council (FSC), for example, helps to verify that wood products are harvested in a way that protects the human and environmental health. The LEED rating system fosters transparency through innovation credits like Timber Traceability, which requires genetic testing of wood verified as the appropriate species ordered.
In choosing a supplier, owners should also consider travel distances, both from the manufacturer and from ports where products shipped overseas may arrive. In some cases, the carbon required
for shipping across an ocean is less than that required for shipping over land, so the closest fabricator might not be the best choice from a carbon and cost perspective. As more factories come online in the Southeast (such as Timberlab in Greenville, SC and other manufacturers in AL, AR, and IL, procurement options should continue to increase.)
The South currently has more than 245 million acres of forest, 86% of which is privately owned. Private foresters are also generating 43% more wood than they harvest,xxiv meaning that sustainable forests serve as an important carbon sink and a renewable resource that benefits the ecosystem. As the demand for timber
grows worldwide, bamboo is also increasing in popularity as a building product: crosslaminated bamboo (CLB) panels may be a viable option in the future.
The earlier in the process the fabricator is selected, the better; engaging the fabricator while the design is underway will facilitate smoother coordination and knowledge transfer and help the design team work with the fabricator’s standard dimensions and other considerations.
Contractor Experience
A contractor experienced in CLT construction – along with a team of qualified and experienced subcontractors – will bring valuable knowledge to the project while shortening the learning curve associated with a newer construction type.
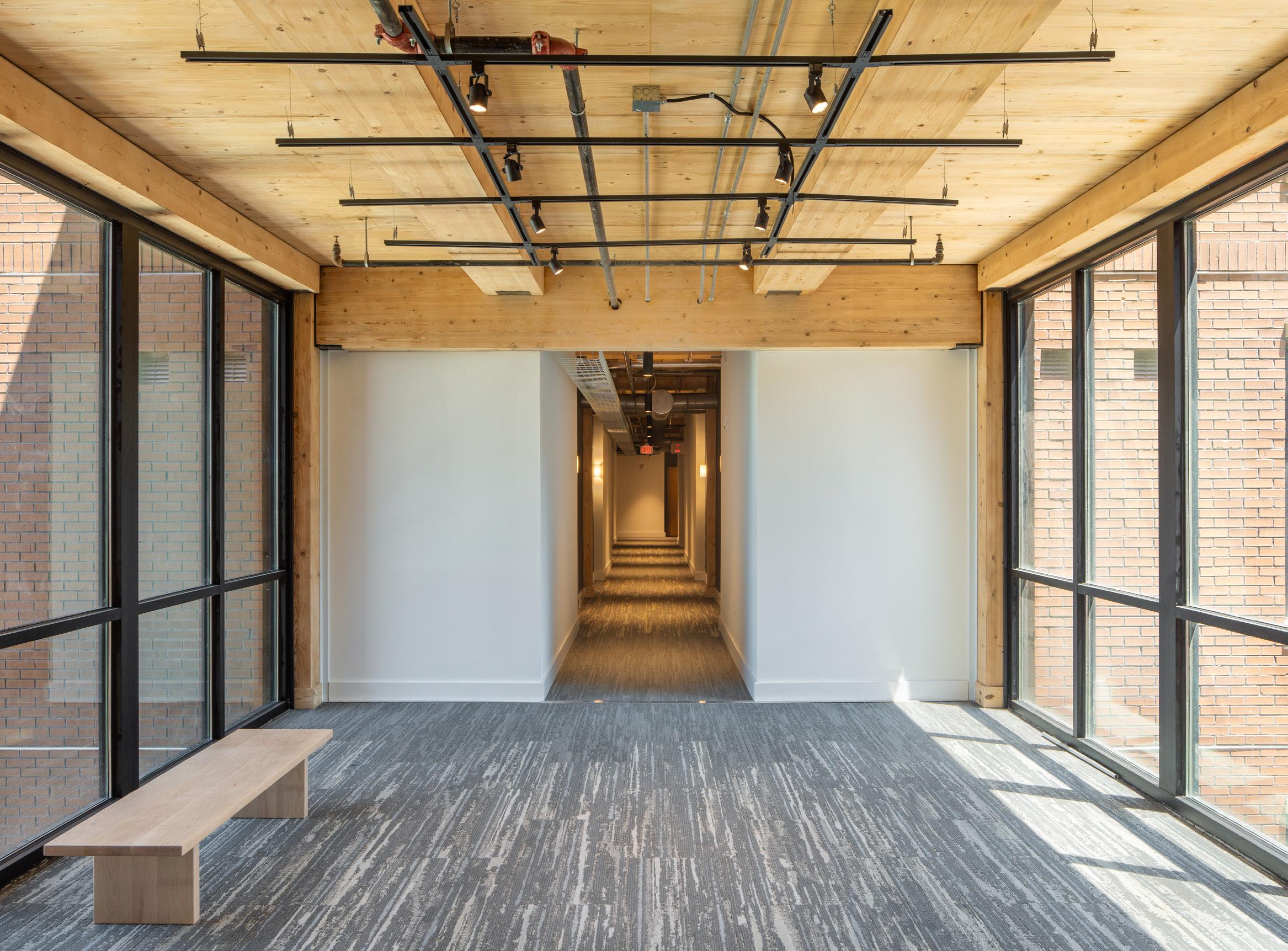
case studies: bringing the forest inside
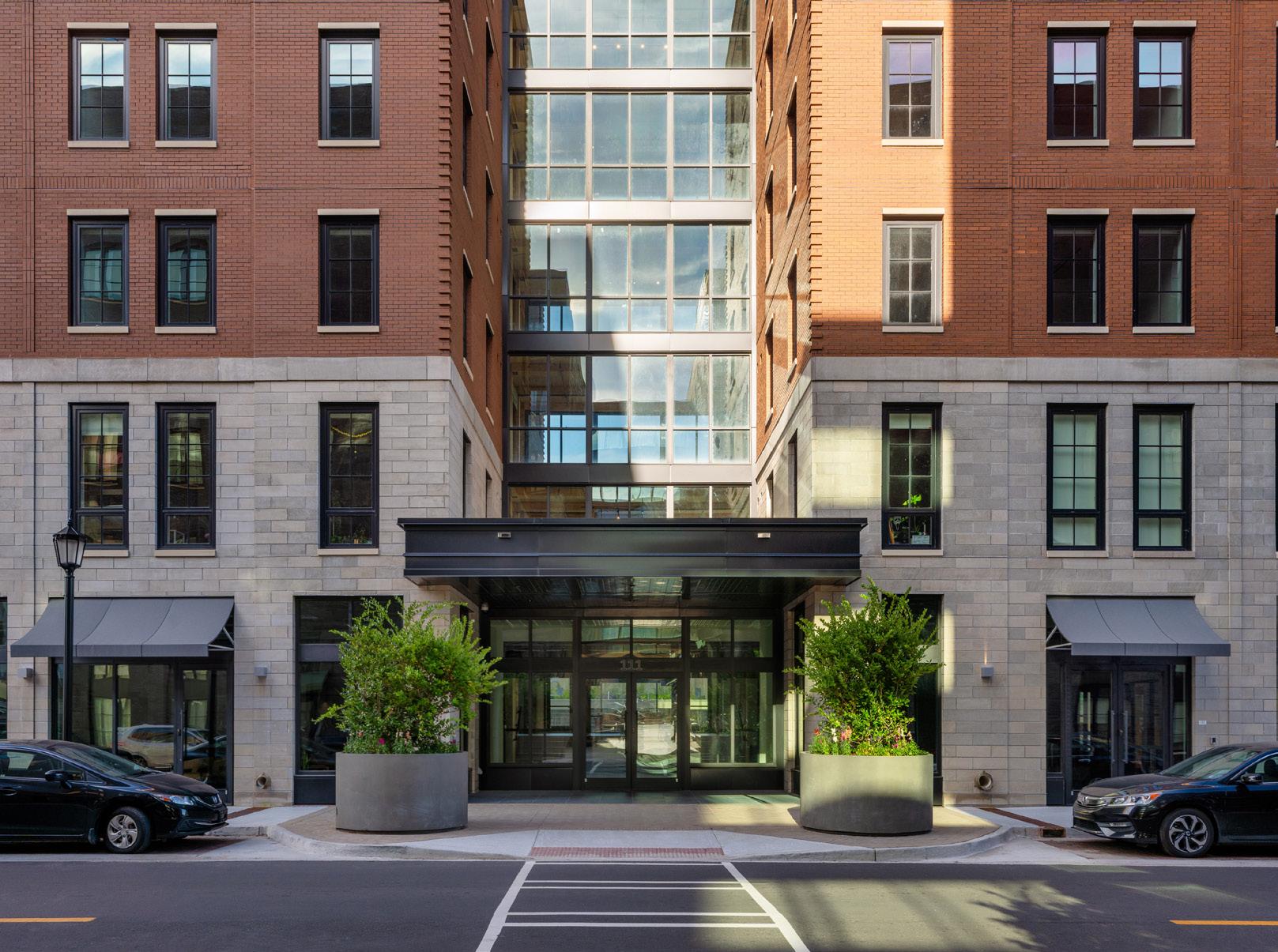
Ann Street Lofts
Savannah, GA
Developed by Tidal Real Estate Partners and designed by LS3P, the two multifamily buildings that make up Ann Street lofts are among the first CLT projects in the region at this scale. 110 and 111 Ann Street span three city blocks in Savannah’s historic district to accommodate 390 residential units as well as parking, mixed-use, and amenities such as a shared courtyard, pool, fitness center, art studio, retail, lobby, and leasing area.
The developer chose CLT as the construction system due to its anticipated speed to market. Designed and permitted under IBC 2012, the hybrid structure is five stories of glulam beams and columns/ CLT shear walls over a threestory, post tensioned concrete podium. The R2 occupancy allowed for permitting as a heavy timber structure, so members are sized to include charring ability. The lower floors are construction Type 1-A.
The team considered about a dozen fabricators, but ultimately engaged Binderholz, an Austrian company, for sustainably harvested wood components due to the company’s experience and capacity. LS3P also worked with US engineering partner Holzpak, experienced in collaborating with Binderholz, for timber engineering consulting. The
site’s convenient location near the port of Savannah minimized overland shipping requirements.
The design showcases the CLT panels at strategic locations; all ceilings (except in bathrooms, per code) are exposed CLT specified with a higher visual grade lumber.
Corbeled beams in corridors, rotated 90 degrees, also create visual interest. CLT is also used in shear walls (in four vertical cores and 15 vertical wall planes) but not exposed at these locations. The brick facades complement the warmth of the wood, and the timber is visible from the street in the transparent connector element that anchors the building. Concrete floors add to the “industrial chic” aesthetic while helping to reduce sound transmission and vibration.
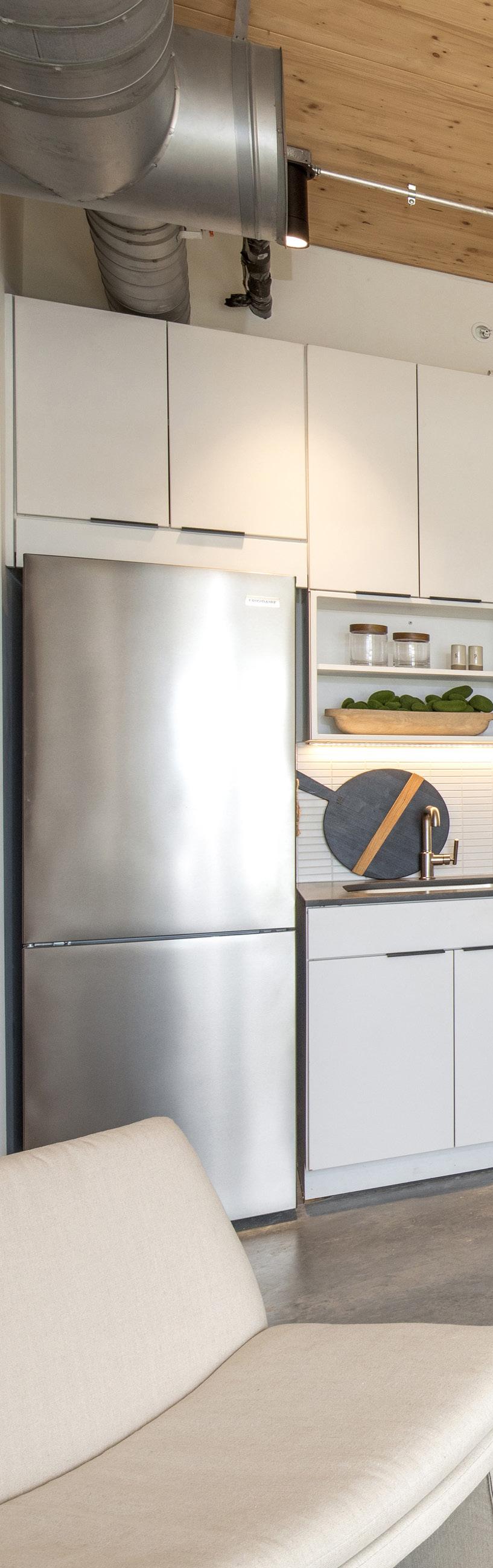
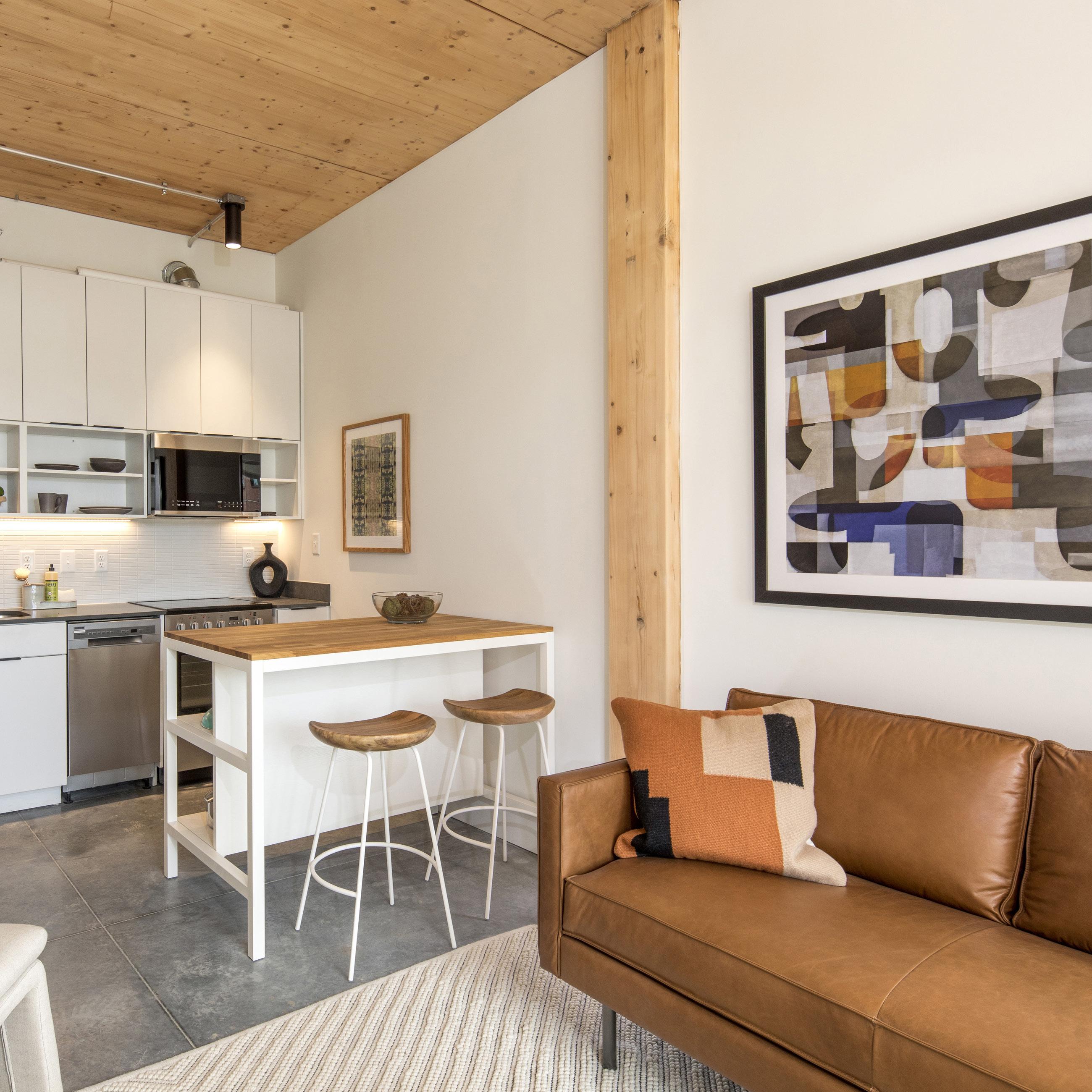
CLT panels create an attractive ceiling finish within these residential units.
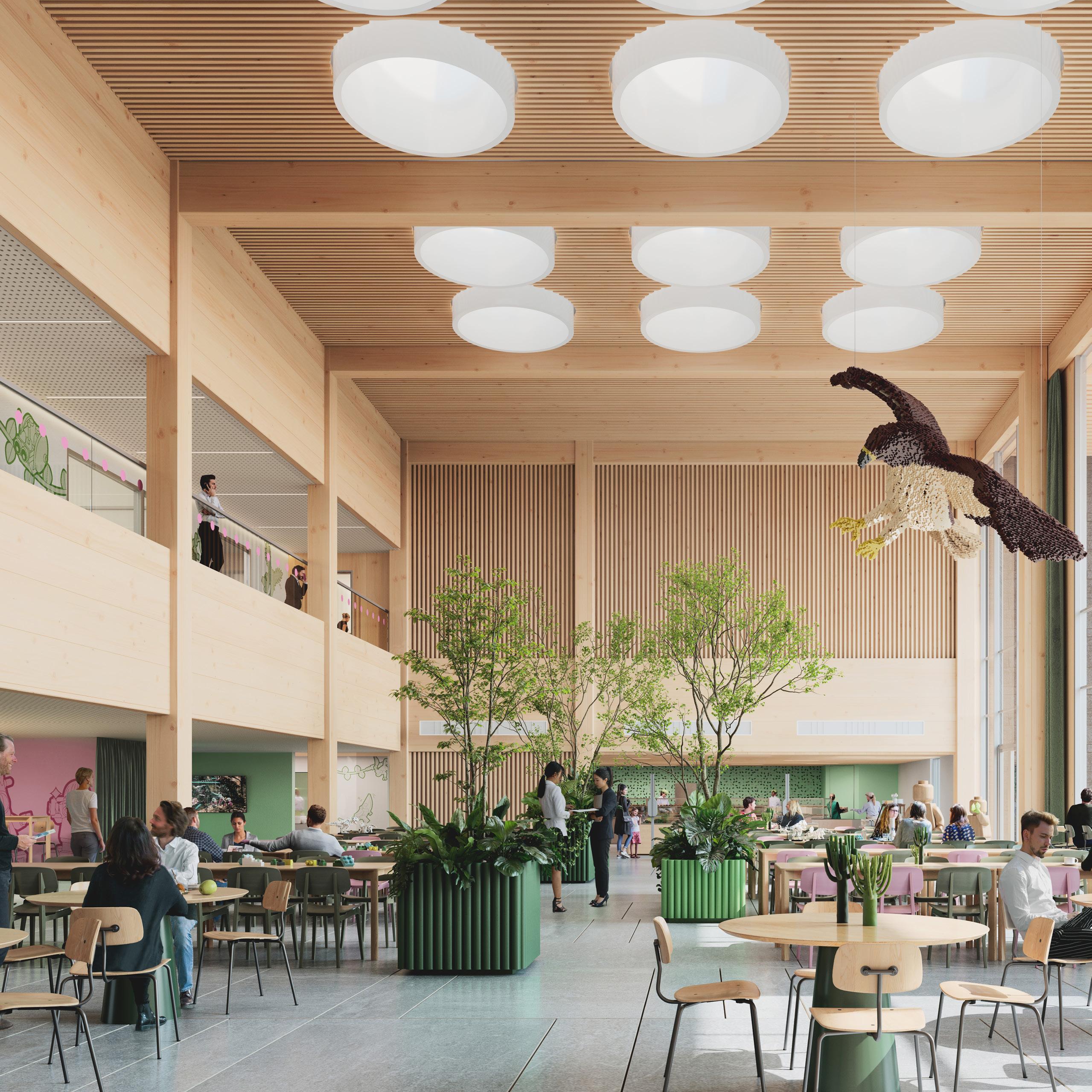
Design rendering: glulam beams and columns support CLT floor plates with an additional decorative wood ceiling finish.
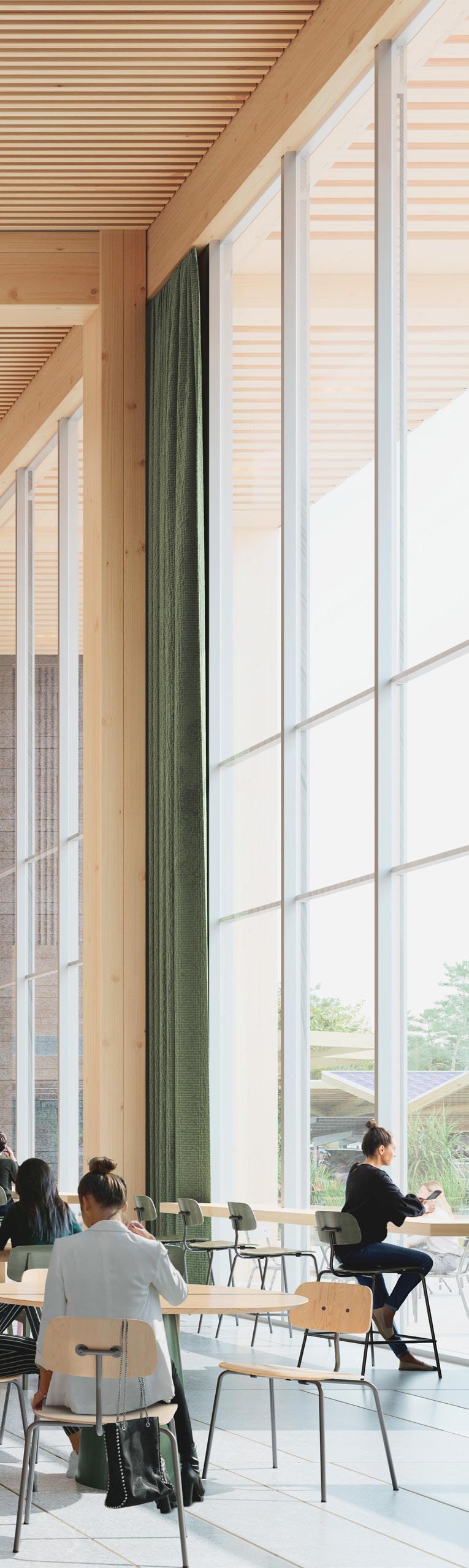
Confidential Industrial Facility Virginia, USA
The international client for this industrial facility selected mass timber for the 40,000 SF office portion of the project with the goal of lowering embodied carbon. The primary floor plates are CLT with a concrete topping slab; a slip sheet in between the CLT and concrete will allow the concrete to be removed and the CLT panels to be recovered at the end of life. Columns and beams are glulam with a repetitious connection; the sizing and layout are standardized for ease of construction and the client’s commitment to eventual disassembly and reuse. A disassembly plan will accompany the design and guide the contractor. CLT is also used in shear walls (mostly covered with drywall for this application). The layout of the office space is an east/west rectangle with double height spaces throughout, including the lobby and canteen areas.
Live Oak Bank Building 4 Wilmington,
NC
This unique campus for a bank headquarters originated from the owner’s desire to create a superior workplace environment for employees, and is inspired by the idea of buildings which “sit lightly on the land.” The resulting design disturbs as little earth as possible, integrating native features of the coastal landscape and capturing views to nature from every office while preserving the site’s longleaf pines and live oaks. The materials palette for the campus has always been centered around mass timber, with the first three buildings making extensive use of glulam columns and beams and cypress siding.
The fourth office building on campus, however, is the first to employ a 100% mass timber structure. The glulam and CLT structural members for the 67,000 SF building were fabricated of southern yellow pine in Timberlab’s new Greenville, SC factory. The project team includes LS3P as designer and Swinerton and Monteith construction operating as a joint venture team.

Top image and bottom left: renderings of Live Oak Bank's Building 4, which features CLT and other forms of mass timber. Bottom right: CLT panels being installed over glulam columns and beams.
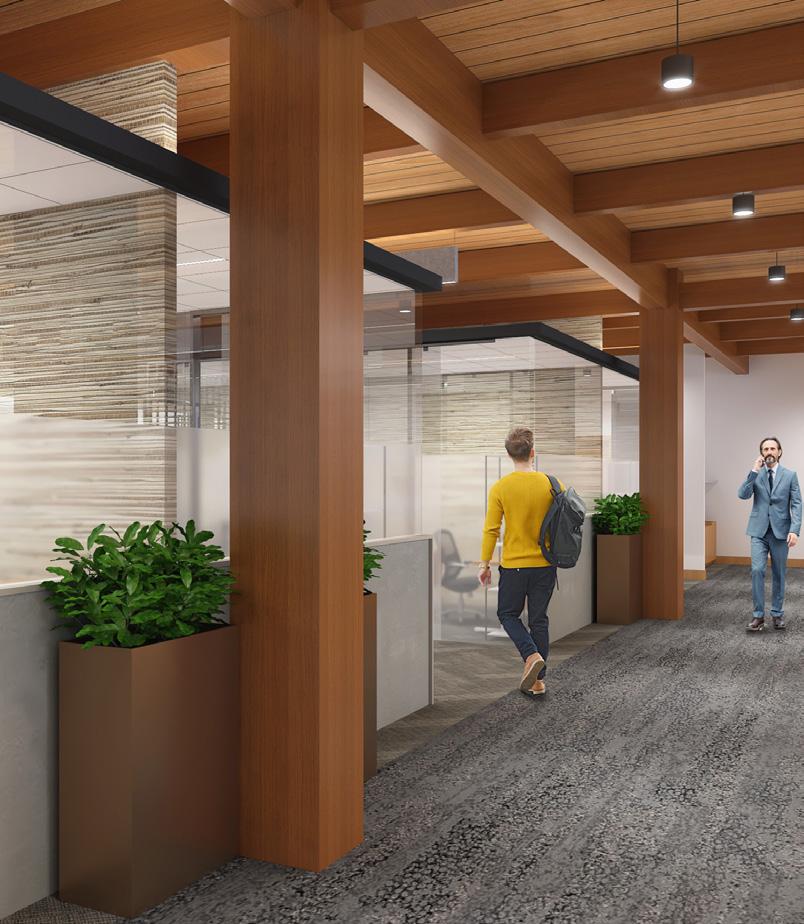
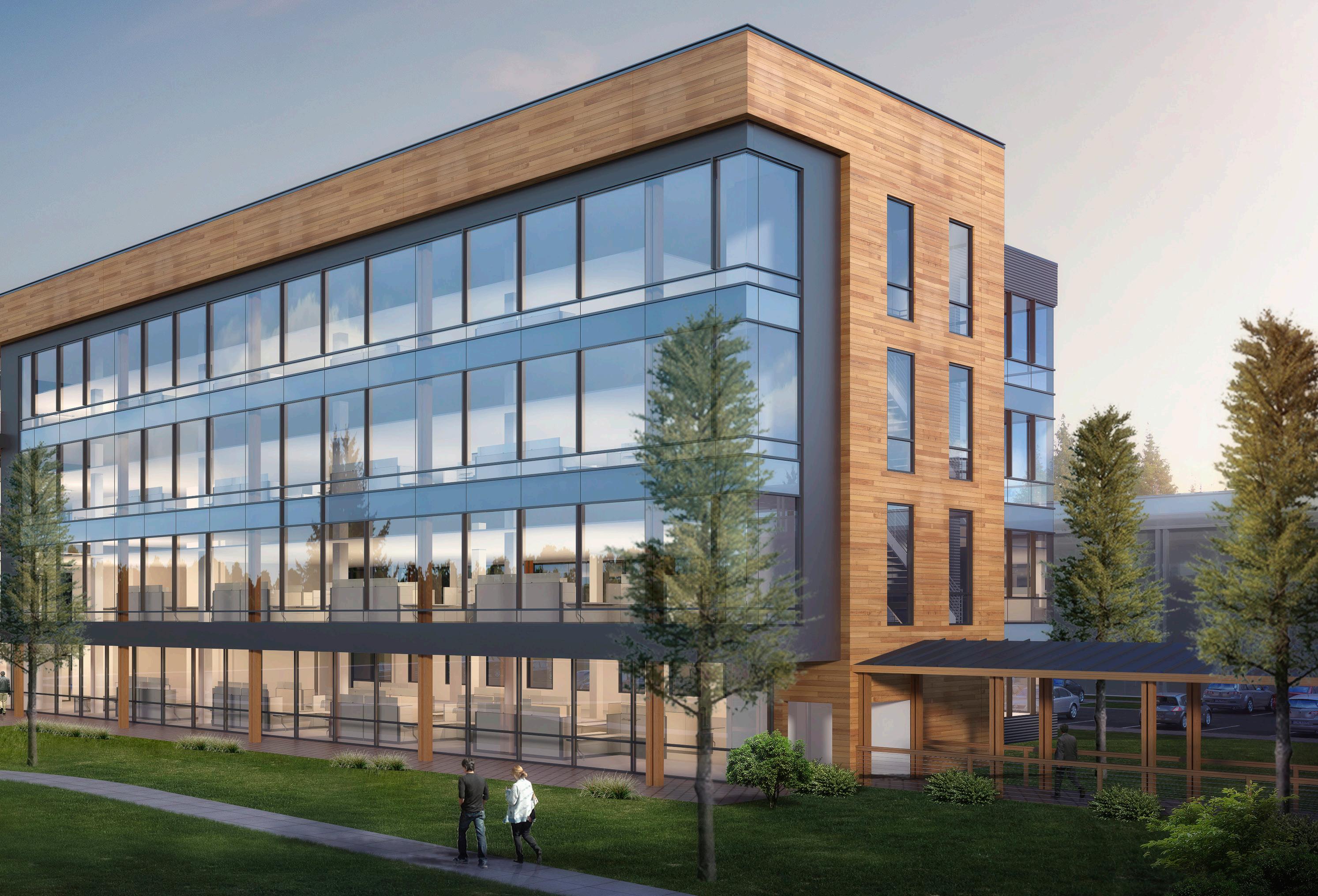
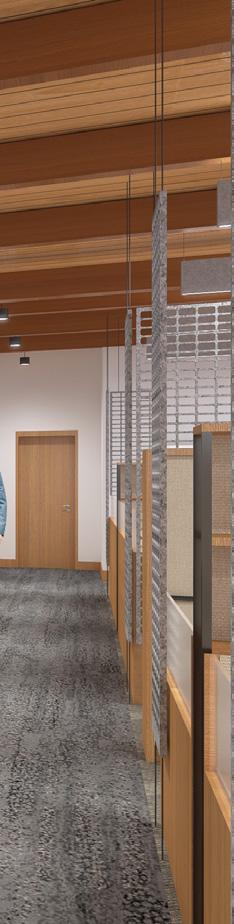
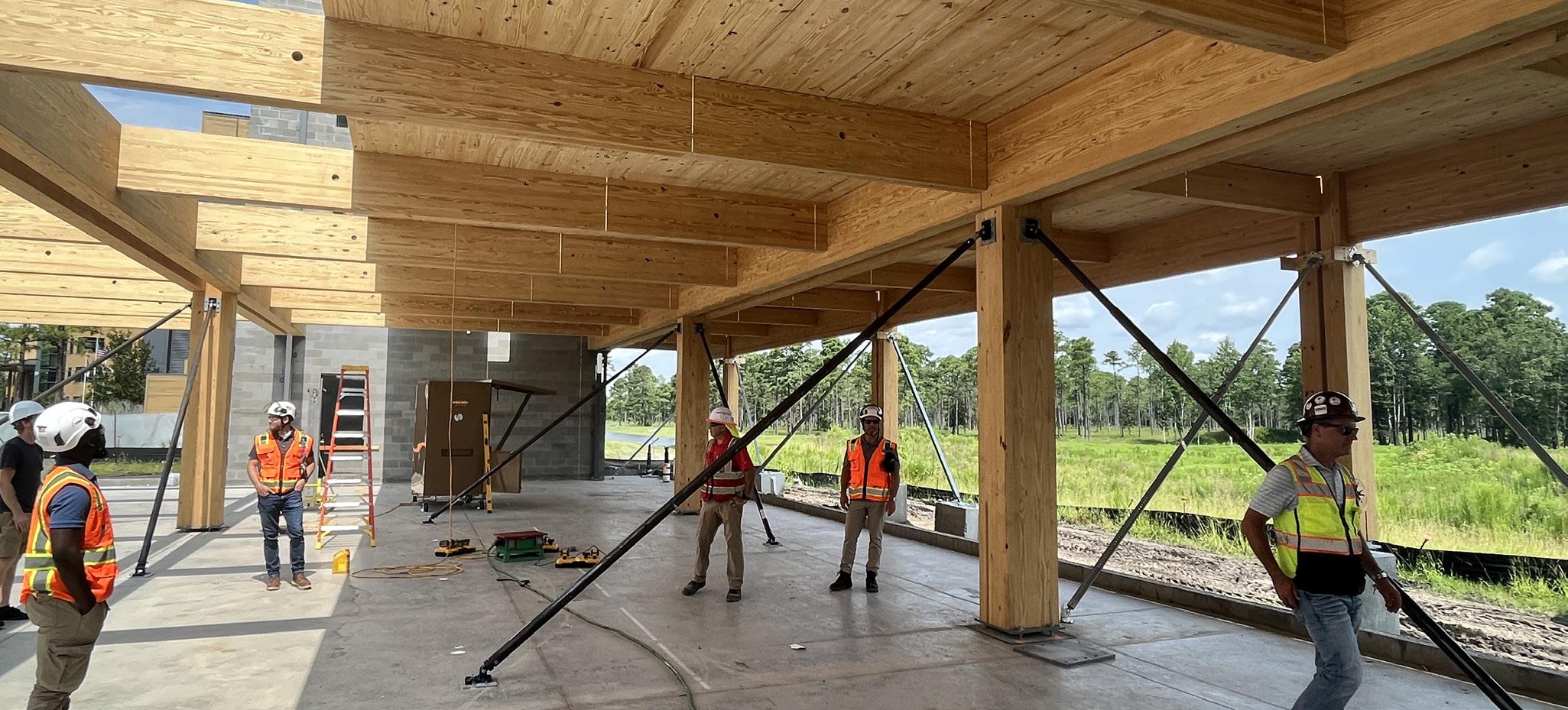
The Live Oak Bank campus in Wilmington, NC uses many timber products in its buildings which provide a connection to nature and harmonize with its forested site. The most recent campus building makes use of CLT as well as glulam in it materials palette
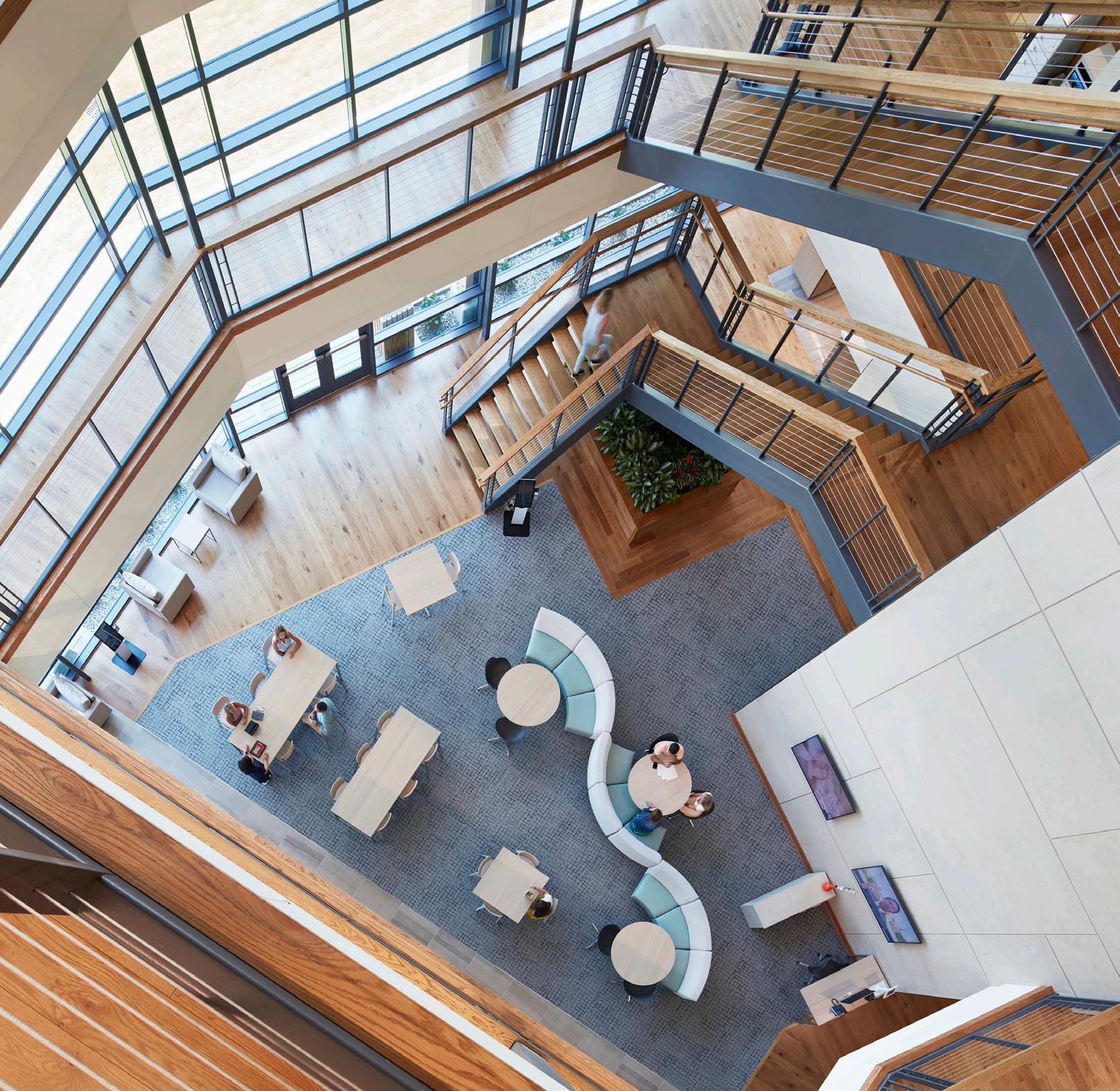
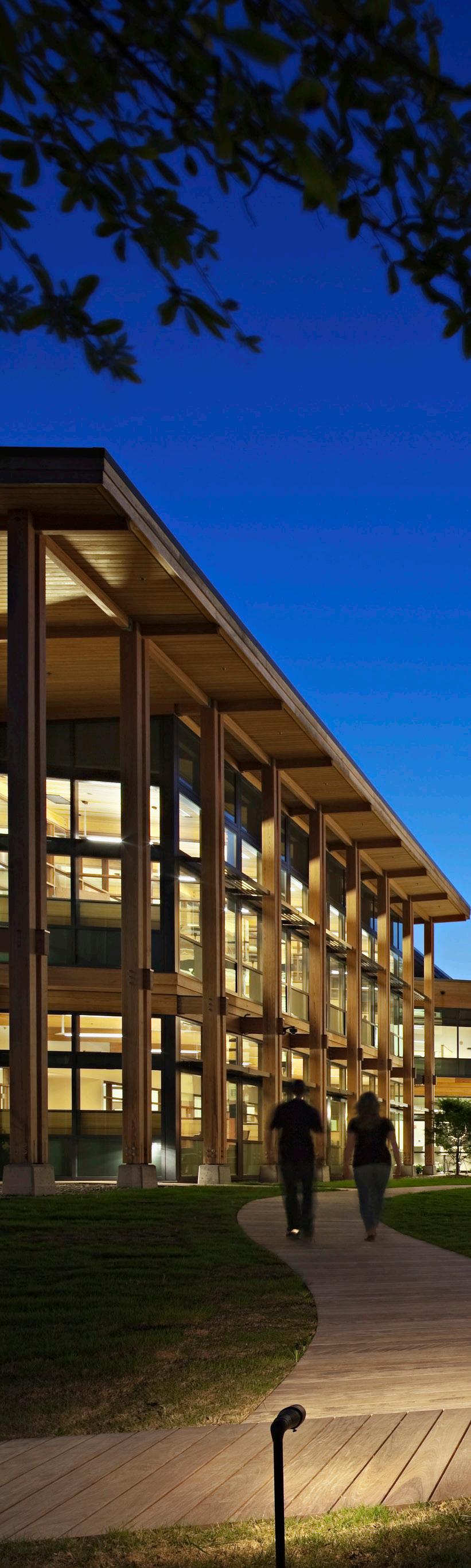
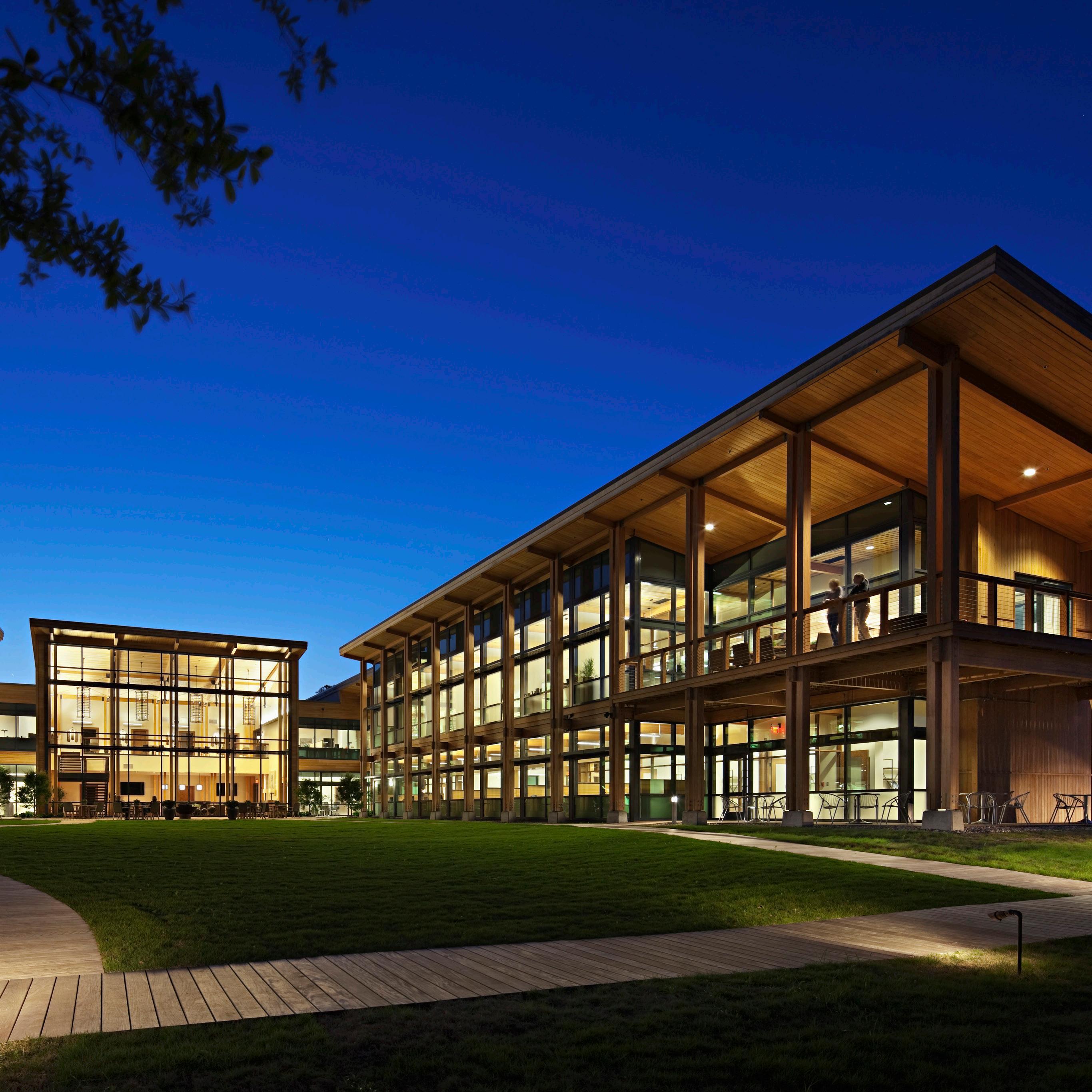
The Live Oak Bank campus in Wilmington, NC uses a variety of mass timber products to harmonize with its forested site, including glulam and cypress siding.
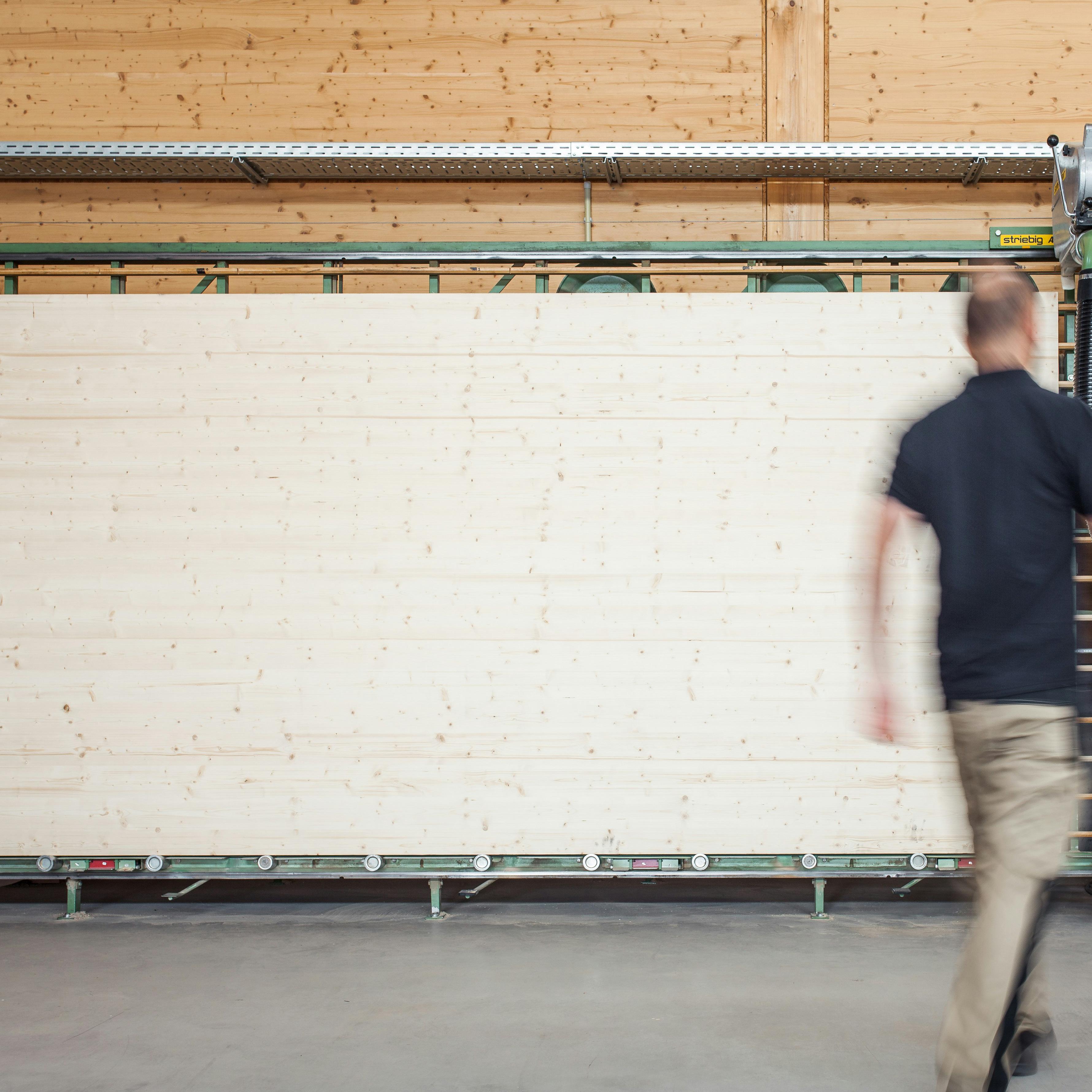

Binderholz Enfield, NC
Binderholz, a mass timber manufacturer headquartered in Austria, has three US locations, including a new nominal lumber sawmill factory in Enfield, NC. This project incorporated CLT panels manufactured at a German Binderholz plant in an interior support building within the sawmill. This interior building features CLT walls and roof structures, and the exterior CLT panels are sandwich panels with insulation inside. All openings and perforations were pre-cut at the German plant.
A new unbinding station at the Enfield factory includes CLT walls and roof panels atop a concrete slab; the exterior panels are also sandwich panels with insulation. Because the exterior panels will be exposed to the elements in this application, an exterior clear coat finish will be applied for weather protection.
drawing conclusions
While CLT is an increasingly popular construction method, many factors will influence whether it is the right choice for any particular project. Sustainability, cost, speed to market, supply chain issues, moisture control, local code requirements, project aesthetics, and many other factors must be carefully weighed at the onset of a project to determine the viability of CLT compared with other options. The popularity of CLT and other mass timber options, however, is likely to continue to rise in the coming years; the growth in this market, particularly in the Southeast US, should lead to more local suppliers, more experienced contractors, and more supportive building codes which continue to allow innovation in mass timber projects.
Selected Resources
CLT Handbook | Swedish Wood
CLT Toolbox (calculators)
Forest Stewardship Council
Mass Timber Projects CLT Handbook | Re-Think Wood
Solid Timber Manual | Binderholz
Timberaid (calculators)
WoodWorks | Wood Products Council
Works Cited
i IMARC. N.d. “North America Cross-Laminated Timber Market Report by Application (Residential, Educational Institutes, Government/Public Buildings, Commercial Space), and Country 2024-2032.” Accessed April 23, 2024. https://www.imarcgroup. com/north-america-cross-laminated-timbermarket#:~:text=The%20North%20America%20 cross%2Dlaminated,15%25%20during%20 2024%2D2032.
ii WoodWorks. N.d. “Mapping Mass Timber.” Accessed April 23, 2023. https:// www.woodworks.org/resources/ mapping-mass-timber/
iii Fabris, Peter. December 1, 2022. “Cross Laminated Timber Market Forecast to More Than Triple by End of Decade.” Cross laminated timber market forecast to more than triple by end of decade (bdcnetwork.com)
iv Abrams, Amanda. March 17, 2023. “Popularizing Mass Timber Construction in the Southeast.” https://urbanland.uli.org/planningdesign/popularizing-mass-timber-constructionin-the-southeast
v WoodWorks. N.d. “Tall Wood Buildings in the 2021 IBC- Up to 18 Stories of Mass Timber.” Accessed May 2, 2024. https://www.woodworks. org/resources/tall-wood-buildings-in-the-2021ibc-up-to-18-stories-of-mass-timber/
vi Silva, Catarina; Branco, Jorge; and Lourenco, Paulo. 2013. “A Project Contribution to the Development of Sustainable Multi-Storey Timber Buildings. Universidade do Minho: A project contribution to the development of sustainable multi-storey timber buildings (uminho.pt)
vii Booth, William. October 31, 2023. “This OldSchool Building Material Could Take Over City Skylines.” Sustainable wooden skyscrapers could soon take over city skylines - Washington Post
viii Kumar, Vaibhav et. al. March 1, 2024. “Environmental impact assessment of mass timber, structural steel, and reinforced concrete buildings based on the 2021 international building code provisions.” https://www. sciencedirect.com/science/article/abs/pii/ S0360132324000374
ix Puettman, Marianne, et. al. December 18, 2021. “Comparative LCAs of Conventional and Mass Timber Buildings in Regions with Potential for Mass Timber Penetration.” https://www.mdpi. com/2071-1050/13/24/13987
x Sun, Qiming; Huang, Qiong; Duan, Zhuocheng; and Zhang, Anxiao. May 2022. “Recycling Potential Comparison of Mass Timber Constructions and Concrete Buildings: A Case Study in China.” https://www.researchgate.net/ publication/360741381_Recycling_Potential_ Comparison_of_Mass_Timber_Constructions_ and_Concrete_Buildings_A_Case_Study_in_ China
xi Moore, Andrew. August 1, 2022. “5 Benefits of Building with Cross-Laminated Timber.” https:// cnr.ncsu.edu/news/2022/08/5-benefits-crosslaminated-timber/
xii Kumar, Vaibhav et. al. March 1, 2024. “Environmental impact assessment of mass timber, structural steel, and reinforced concrete buildings based on the 2021 international building code provisions.” https://www. sciencedirect.com/science/article/abs/pii/ S0360132324000374
xiii Browning, William; Ryan, Catherine; and Clancy, Joseph. N.d. “14 Patterns of Biophilic Design.” Accessed July 26, 2024. https://www. terrapinbrightgreen.com/reports/14-patterns/
xiv Moore, Andrew. August 1, 2022. “5 Benefits of Building with Cross-Laminated Timber.” https:// cnr.ncsu.edu/news/2022/08/5-benefits-crosslaminated-timber/ .
xv WGI. July 13, 2017. “5 Reasons Wood Would Be Good for Your Next Project.” https://wginc. com/5-reasons-wood-would-be-good-for-yournext-project/
xvi Passive House Accelerator. N.d. “A CLT and Passive House Case Study.” Accessed May 17, 2024. https://passivehouseaccelerator.com/ articles/a-clt-and-passive-house-case-study
xvii Binderholz. February 2023. “Introduction: Solid Timber Manual 2.0.” https://www.binderholz. com/fileadmin/user_upload/books/en/ solid_timber_manual_2/12/#zoom=true
xviii Swedish Wood. May, 2019. “The CLT Handbook.” https://www.
swedishwood.com/publications/ list_of_swedish_woods_publications/ the-clt-handbook/
xix International Building Code. 2018. “International Building Code 2018.” https://codes. iccsafe.org/content/IBC2018P6
xx Swedish Wood. May, 2019. “The CLT Handbook.” https://www.swedishwood.com/publications/ list_of_swedish_woods_publications/ the-clt-handbook/
xxi WGI. July 13, 2017. “5 Reasons Wood Would Be Good for Your Next Project.” https://wginc. com/5-reasons-wood-would-be-good-for-yournext-project/
xxii Swedish Wood. May, 2019. “The CLT Handbook.” https://www. swedishwood.com/publications/ list_of_swedish_woods_publications/ the-clt-handbook/
xxiii Swedish Wood. May, 2019. “The CLT Handbook.” https://www. swedishwood.com/publications/ list_of_swedish_woods_publications/ the-clt-handbook/
xxiv Southern Group of State Foresters. N.d. “Forest and Woodlands Management.” Accessed May 19, 204. Forest & Woodlands Management - Southern Group of State Foresters (southernforests.org)