Working Smarter, Not Harder
3D Building Capture Tools Streamlining Documentation and Coordination
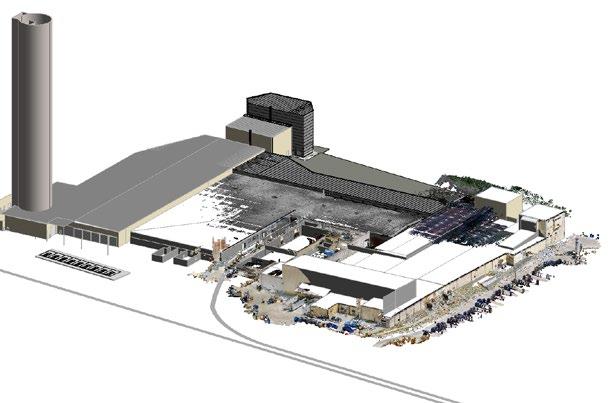
Designing for a renovation project has always come with a degree of uncertainty. Record drawings which were accurate the day of the grand opening may be wildly outdated decades later; walls may have been reconfigured and interior details may have changed over time, and small details can make a big difference when it comes to code compliance, change orders, and surprise deficiencies in a building’s condition. In years past, navigating this
uncertainty meant sending designers to the site with tape measures and clipboards to check very wall, door, and window. This measurement and documentation process often took weeks. Laser measuring tools sped up the process (sometimes at the expense of accuracy), but documenting existing conditions still meant piecing together photographs and measurements to establish trusted working drawings impacting a host of design decisions.
Invariably, a critical detail or two was missing, so verifying details meant driving back to a site and taking more photographs or measuring a forgotten element.
Today’s tools for 3D building capture have changed the landscape entirely. Using picture-to-picture scanning and/or “Light Detection and Ranging” technology (commonly known as LiDAR), designers can walk through a building with a tripod and a
scanner and capture a complete 3D “marionette” model accurate from 1” to 1 mm, depending on the tool. This model can be shared with the entire design team to streamline coordination and verification –without anyone else having to leave their desk. LS3P Associate Clay Horney, an in-house expert, uses a variety of tools to capture existing conditions, depending on the size and complexity of a project. “These tools are a game changer,” he says.
“The data capture process and software are quick and relatively easy to use, depending on the complexity of the system, and we now have options that will work for documentation for a wide variety of project needs.” The tool selected might depend on whether a virtual walk-through is needed, and the degree of accuracy required.
Picture-to-Picture Scanning + Matterport
The simplest process uses a camera, a tripod, and an iPad with Matterport software. With photos taken at 15’ intervals and stitched together in Matterport, this technique creates a 3D model accurate to between 1/8” and 1”. Accuracy is dependent on the distance of the object from the scanner; however, this tool is still more accurate than a laser measurer which assumes a wall is straight. With this tool, if a wall is out of plumb, that will show up in the model.
Matterport will convert the images into a point cloud model for a nominal fee; this point cloud model can be loaded into Autodesk Recap, exported as a unified point cloud, and loaded into Revit to help streamline the design process. The cloud-based 3D model is easily shareable with clients via a website link, and allows team members to virtually walk through the building

from a laptop. (Matterport will also provide extremely inexpensive floor plans with a 24 hour turnaround; these may be less accurate than the unified point cloud, but a significant timesaver for a proposal or schematic design meeting.)
Leica BLK360 Scanner + Leica Software
This newer LiDAR-based system, also compatible with Matterport, works the same way but delivers accuracy from 1/8” to 1 mm. Each scan takes about a minute longer, but with the level of detail provided, 1/3 fewer scans are needed as compared to picture-to-picture scanning. This tool offers everything that Matterport can do, with the ability to scan most exterior conditions as well; the model is also available on a website.
The Leica software is more complex than Matterport’s, which can be learned in a few minutes. Leica’s tools require a couple of days of training, but come with the ability to move building components as
needed. (This is risky for people who aren’t sure how it works, but can be useful in some situations such as working around sensitive building areas which can’t be scanned.) Once the images are aligned, the model is once again exported to Autodesk Recap, which can be uploaded to Revit.
Leica RTC360
The RTC scanner takes the process to the next level: if it can see it, it will scan it, up to about 400 feet away from the device. This range allows a quick and efficient capture of wholesite conditions, and is exponentially faster than walking the site. The model is built in GPS; it doesn’t provide website walkthroughs, but does provide a significant amount of site detail. The RTC scanner isn’t compatible with Matterport, but when accuracy is critical, this tool is an excellent choice.
Drones for Site Documentation

LS3P architect Eric Rueger, the firm’s licensed drone operator, has also used drone technology for largescale site documentation. While this method isn’t as high resolution as a handheld scanner on the ground, it can be used to create a 3-D mesh for site development, saving valuable project time. “Depending on the site, drones can be a very helpful documentation tool,” he says. “Accuracy improves at lower heights, and the information gained can be invaluable for understanding site conditions which might not be evident from a two-dimensional map.
LS3P’s 3D capture experts have learned a few things along the way: always bring a bunch of doorstops to facilitate moving through the space. Traffic cones are also an inexpensive and portable tool for creating an anchor point in, say, a long blank hallway; the software will use the cones as a reference for stitching images together. And, when working with unified point cloud models in Revit, it’s helpful to place them on a separate work set, and turn them off as a default. It’s easy to turn them on for reference, but these complex data sets can slow down a model for everyday use.
There’s No Going Backwards
Scanning a building might take an hour for every 2,000-4,000 SF, depending on the complexity and whether the space is occupied at the time of scanning. According to Clay, a recent 750,000 SF industrial project took about 2 ½ days to scan, as opposed to the three weeks or so this process would have taken by hand. It’s not just about the time saved in measuring, however; the 3D building
capture yields saving in terms of time and budget every time someone is able to open the model and verify a detail instead of traveling to the site to capture needed information on a deadline.
Project managers like Scott Greenman of LS3P’s Raleigh office believes that 3D building capture is essential to success for a renovation
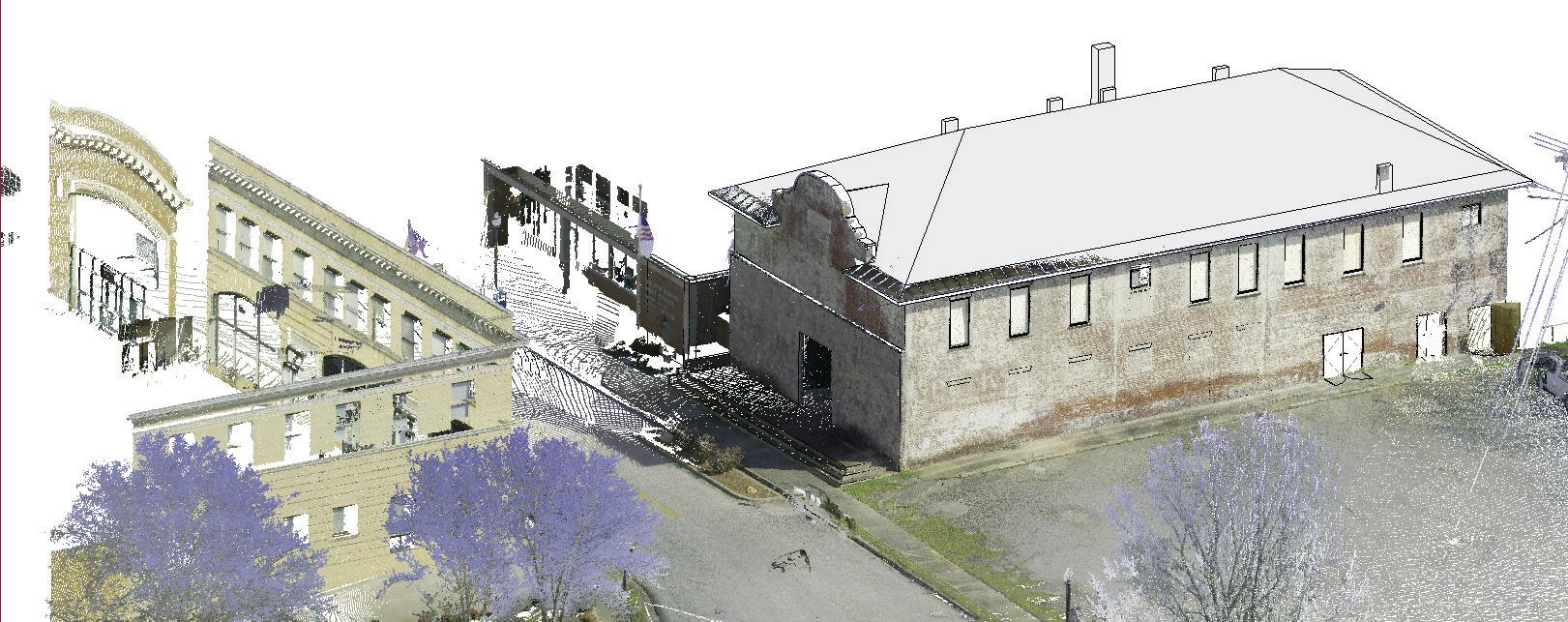
of any complexity. Scott has found this to be an invaluable tool for coordination across distributed teams, travel time and billable hours spent tracking down details, and the ability to spot critical elements such as water damage or bearing walls to inform next steps and design decisions. “Using our old methods of building documentation, we inevitably would miss a detail causing the
team to go back out to verify or scramble to find a solution in CA,” he explains. “With these technologies, we can have more confidence in our documentation by capturing every aspect of the building at the time of the walk through, saving time and fee.”
LS3P’s bench of 3D building capture experts is growing steadily, and
teams across the firm are finding that Matterport, in particular, is easy and intuitive to learn quickly. As more and more teams experience the benefits of these tools, adoption is becoming more widespread and workflows are becoming increasingly efficient.
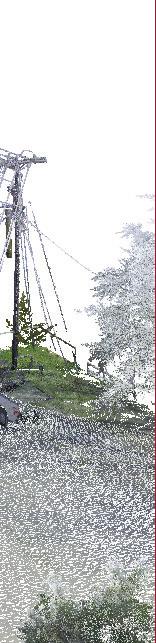
About the Contributors
Practice Professional Associate Clay Horney is a Practice
Professional in LS3P’s Greenville office. Clay earned a Master of Architecture from Clemson University; he also holds a Bachelor of Architecture and a Bachelor of Science in Construction Management from Appalachian State University and an Associate of Arts from Mayland Community College. Since joining LS3P in 2016, Clay has worked primarily in the Faith sector; he applies his passion for details and functionality to his clients and their ministries.
Eric Rueger is an Architect in LS3P’s Greensboro office with more than 10 years of experience at all phases of design and construction. His previous experience was focused on healthcare design in and around the Virginia and Washington, DC areas. In 2021, Eric joined the LS3P team to continue building his healthcare experience portfolio. He is well versed in many areas of architecture from new construction to renovations.
Scott Greenman brings over 10 years of expertise in higher education, commercial and public projects. An experienced project manager and architect, he is skilled at executing all phases while ensuring all client expectations are set and met at every stage of the project. Scott is a creative thinker who enjoys collaborating and solving problems with diverse teams to meet the client’s needs. His passion for sustainability aids him in designing functional spaces that yield lasting value for the clients and the environment.
CLAY HORNEY Associate ERIC RUEGER , AIA Architect SCOTT GREENMAN, AIA, LEED AP BD+C Associate Raleigh Workplace Sector Leader