
7 minute read
Magnesium 3D printen voor verderlichte fiets
Unieke technologie ontwikkeld in Limburg
De 100% Limburg Bike toont aan dat je in de Benelux gepersonaliseerde, oersterke en tegelijkertijd superlichte racefietsen kunt maken. 3D printen van magnesium trekt helemaal de aandacht.
Advertisement
Het innovatieproject wil vooral via co-creatie nieuwe materialen én productiemethoden hun weg laten vinden naar de markt én het midden- en kleinbedrijf. “Je hebt niks aan nieuwe materialen en verwerkingsmethoden als ze niet tot nieuwe producten in de markt leiden; als ze niet hun weg naar de markt vinden”, steekt Menno Smeelen, New Business Development manager bij Brightlands Chemelot Campus van wal.
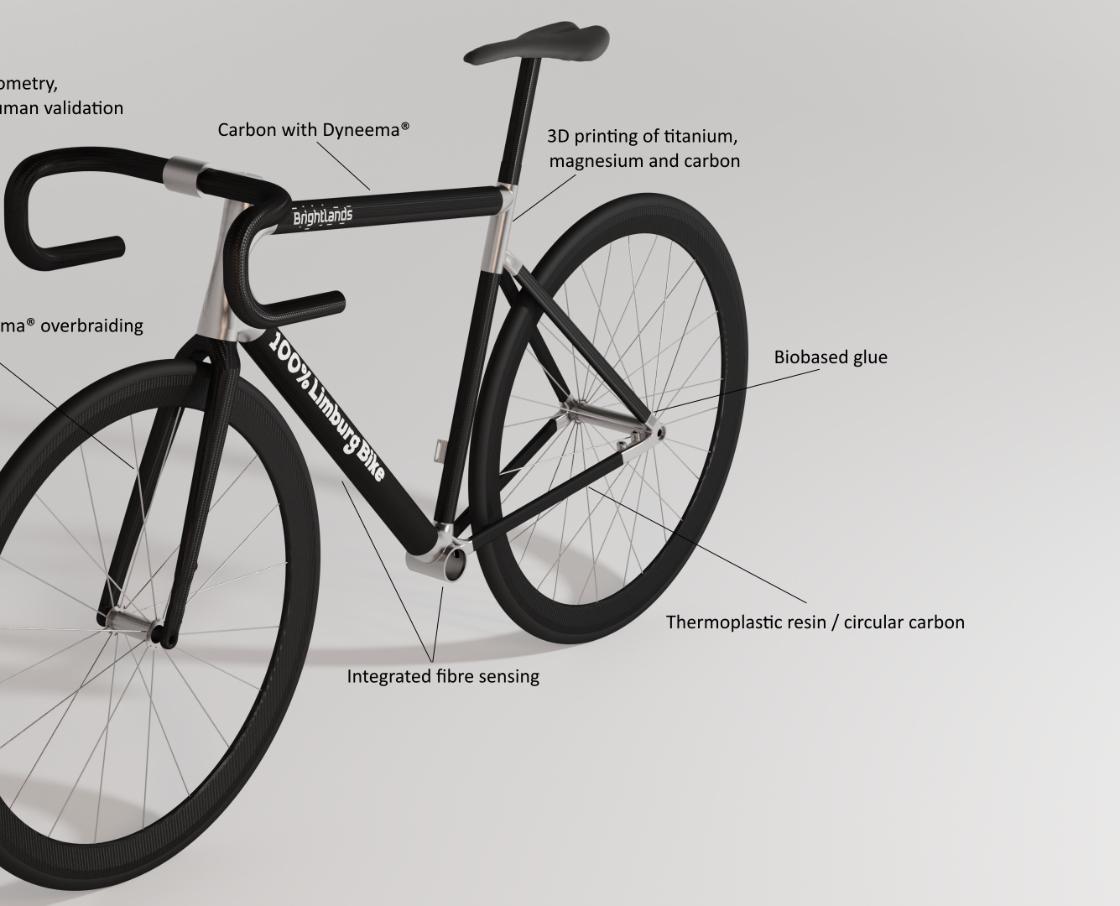
Maatwerk fiets
De meeste fietsframes voor de Europese markt worden in Azië geproduceerd. Ook de frames van de lichtgewicht carbon racefietsen. Een cruciaal onderdeel in dat productieproces zijn de dure mallen. Hierdoor heb je per definitie grote aantallen nodig om de kostprijs betaalbaar te houden. Centimetermaten, zoals vroeger toen de stalen fietsframes nog in WestEuropa werden gelast, zijn onhaalbaar, laat staan als je een gepersonaliseerd frame wil. S, M en L, dat zijn de confectiematen waaruit de fietser kan kiezen. Dit doorbreekt de 100% Limburg Bike. “3D printen is de technologie waarmee we een uniek product kunnen maken, op de millimeter nauwkeurig afgestemd op de fietser en custom made. En hier geproduceerd”, zegt Menno Smeelen. Na een kleine drie jaar ontwikkelen door het consortium van mkbbedrijven en kenniscentra, is de 100% Limburg Bike klaar voor testritten, onder andere door oudprofwielrenner Bram Tankink.
Frame van 1000 gram
3D printen speelt een sleutelrol in de productie van het frame, dat ongeveer 1000 gram weegt, vergeleken met 750 gram voor de lichtste carbonframes in de handel. Dit gewicht kan nog verder omlaag, denken de ontwikkelaars. In het project is er niet voor gekozen om de complete frames te 3D printen. Het frame wordt opgebouwd met buizen van Dyneema-vezel gecombineerd met carbon. Een buis van carbon kan
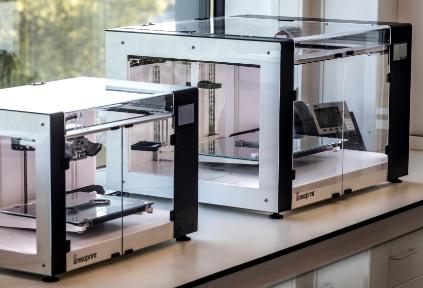

breken, maar omwikkeld met de vezel kan het frame niet meer volledig doorbreken. De personalisatie van het fietsframe gebeurt door de koppelstukken (lugs) voor de buizen te 3D printen, ofwel in magnesium ofwel in titanium. Hierdoor kan men de buizen zo efficiënt mogelijk produceren. De hoeken van deze koppelstukken en de lengtes van de framebuizen zijn variabel waardoor je perfect op je fiets zit. In het project heeft men ook 3D printen met continue carbonvezel toegepast bij een onderdeel, waarin tevens een sensorfunctie in het materiaal geïntegreerd wordt. De sensoren meten de krachten op het frame continu. Dit onderdeel wordt geprint op Anisoprint 3D printers bij Brightlands Materials Center.
Magnesium 3D printen
Qua 3D printtechnologie is het project er al in geslaagd om in de markt interesse te wekken voor een nieuw materiaal. De lugs, die de buizen verbinden, worden namelijk niet alleen in titanium geprint maar ook in continue carbon vezel versterkt composiet én magnesium. Dit laatste materiaal wordt buiten onderzoekslaboratoria nog nergens 3D geprint, vanwege de risico’s van het reactieve materiaal. “Nog niemand print functionele onderdelen van magnesium”, zegt Menno Smeelen. Op één printerfabrikant na, werd de vraag vanuit het consortium om een 3D metaalprinter voor magnesium te leveren, dan ook negatief beantwoord. De fabrikant die wel positief reageerde, is het Duitse Aconity3D, een spin-off van het Fraunhofer ILT in Aken. Menno Smeelen: “Aconity3D is de enige 3D printerfabrikant die een 3D metaalprinter bouwt die geschikt kan worden gemaakt voor magnesium. Andere fabrikanten die we hebben benaderd, durfden het niet aan. Te gevaarlijk.” De 3D printer van Aconity3D werkt met overdruk in de bouwkamer. Het beschermgas Argon drukt, dankzij de overdruk, het zuurstof uit de bouwkamer. De restdeeltjes gaan doordat zuurstof lichter is dan argon naar de bovenkant van de bouwkamer, waardoor het risico op explosie wegvalt. De fabrikant van de 3D metaalprinter heeft een extra zware seal aangebracht, zodat er geen Argon kan ontsnappen uit de bouwkamer. De printer zelf staat in een volledig dichte box, voorzien van afzuiging voor het geval er toch iets mis gaat.
Een complete set lugs geprint in titanium. Op de foto de eerste set die geprint is.
Beter dan extrusiedelen
Op de Limburgse materialencampus zijn de parametersettings voor 3D printen van magnesium geoptimaliseerd. Hieraan hebben onder andere de onderzoekers en studenten van CHILL, de leeromgeving van onder meer Zuyd Hogeschool op de campus, gewerkt. Het resultaat is dat de geprinte magnesium koppelstukken betere eigenschappen hebben dan extrusiedelen, de gangbare productievorm voor magnesium. Doordat het sterker wordt, kan men dunwandiger printen, zodat de onderdelen nog lichter zijn. Menno Smeelen: “De druksterkte van magnesium is zeer goed en de specifieke sterkte komt in de buurt van die van titanium, waarmee we eveneens lugs 3D printen, terwijl het gewicht per volume bij magnesium lager is. Magnesium heeft als voordeel
Corrosie voorkomen
Een groot nadeel van magnesium is dat het erg corrosiegevoelig is. Een gewone coating volstaat niet, omdat de geringste beschadiging daarvan alsnog tot corrosie leidt. Daarom worden de magensium onderdelen voorzien van een keramische coating, die aangebracht wordt door CeraCarbon, een van de mkbbedrijven in het consortium. Deze coating functioneert als een seal rond het magnesium onderdeel. Menno Smeelen bestempelt het 3D printen met magnesium als een van de veelbelovende resultaten van het innovatieproject. “Dat we hier magnesium printen en dat het betere eigenschappen heeft dan extrudiedelen, opent de deur naar andere toepassingen. Precies daarom hebben we deze showcase ontwikkeld, zodat het midden- en kleinbedrijf profijt heeft van de campus en we nieuwe toepassingen voor de materialen vinden.” Het 3D printen met magnesium heeft inmiddels de aandacht getrokken van Defensie, dat de 3D printer wil inzetten voor onderzoeken. Daarnaast hebben zich twee Limburgse bedrijven gemeld, die toepassingen zien voor het 3D printen met magnesium.
Medische toepassingen
Dat deze metaalprinttechnologie juist op de campus die bekend staan om kunststoffen ontwikkeld is, vindt Menno Smeelen niet verrassend. “In onze visie werken we aan circulaire materialen en duurzame, energiezuinige processen. Het gaat om de generatie na ons. Deze circulaire materialen hoeven niet per se kunststof te zijn. Magnesium is een high performance materiaal, die ontwikkeling hoort hier eveneens thuis.” Want, zoals in de 100% Limburg Bike, vaak gaat het om een combinatie van materialen. Van de meer dan 100 bedrijven op de materialencampus, kijken er dan ook meerdere naar metalen. Menno Smeelen: “We hopen dat uit de 100% Limburg Bike een spin off voortkomt die het magensium 3D printen verder ontwikkelt voor medische toepassingen. Voor implantaten is het een ideaal materiaal.” De combinatie van materialen- en designkennis met de maker space omgeving, maken de campus een aantrekkelijke plek voor dergelijke innovatietrajecten.
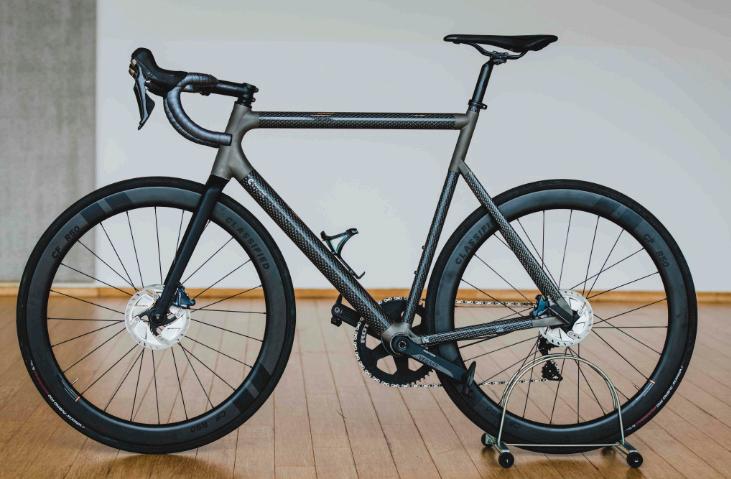
Circulaire fiets
Terug naar de 100% Limburg Bike. Omdat de geprinte koppelstukken de standaard maatnauwkeurigheid hebben van 3D geprinte componenten, gebruikt men bij het verlijmen van de buizen een speciale lijm die de eventuele ruimte tussen de wand van het koppelstuk en de buis opvult. Deze lijm kan men, mocht toch een buis vervangen moeten worden, weer week worden gemaakt zodat men de reparatie kan uitvoeren. Uitgangspunt bij de start van de ontwikkeling van het frame was immers dat het een duurzaam en circulair product zou worden. Dat is grotendeels al gelukt. De Dyneemavezels en het carbon kunnen ontvlecht worden. De vezels kan men shredderen en dan bijvoorbeeld in filament verwerken of andere toepassingen waarvoor korte vezels nodig zijn. Voor het hars wordt nog gewerkt aan de ontwikkeling van een thermoplastisch materiaal dat sterk genoeg is. Het 100% Limburg Bike consortium heeft het prototype van de lichtgewicht fiets gedemonstreerd in het innovatiepaviljoen op het WK Wielrennen in Leuven. Dat heeft veel positieve reacties opgeleverd, inclusief het inzicht dat er blijkbaar een grotere groep fietsers is die zo’n maatwerk fiets wil dan enkel de huidige kopers van highend fietsen. “Meer mensen blijken af te willen van de confectiemaat fiets.” Dat gegeven maakt de kans dat de 100% Limburg Bike volgend jaar daadwerkelijk in productie gaat, groter. In de komende maanden zal blijken of een van de consortiumleden het concept gaat vermarkten. Als dat gebeurt, zal de productie in Nederlands of Belgisch Limburg gebeuren. En niet in China.
In tegenstelling tot andere composieten wordt de combinatie van de vezel met carbon uitgebakken bij 130 graden C.

Menno Smeelen bij de Aconity3D printer waarmee de magnesium koppelstukken worden geprint.