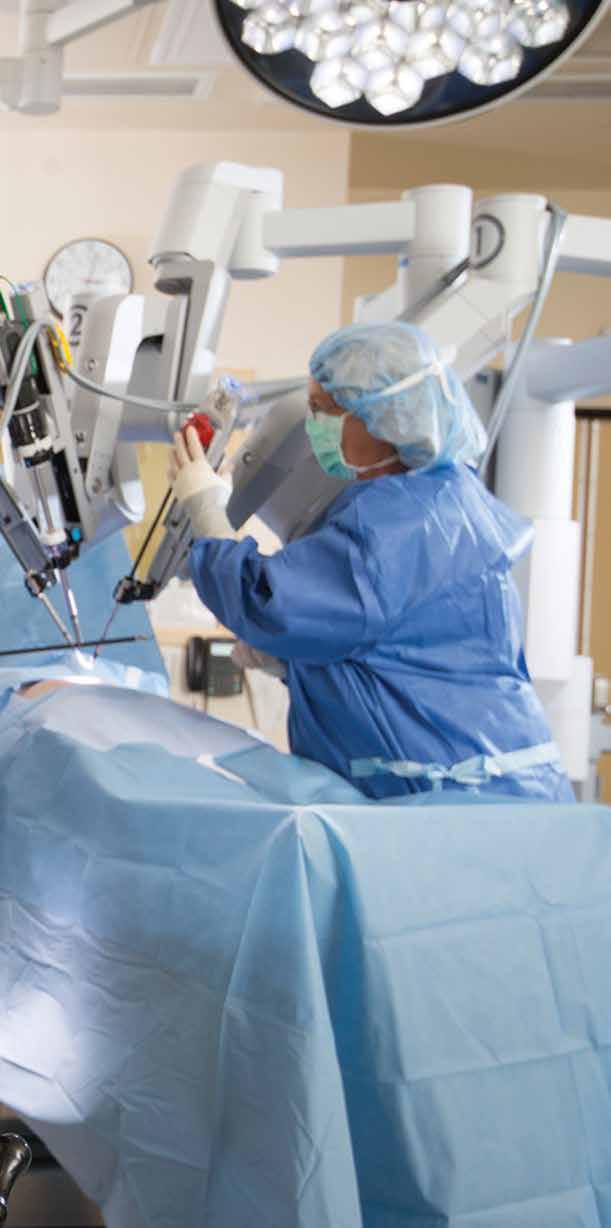
31 minute read
DOSSIER Automatisation dans les soins
Ces systèmes compensent la pression croissante et le vieillissement du personnel dans les soins de santé À l’instar de la tempête parfaite en météorologie qui résulte de causes se renforçant mutuellement, la tempête dans l’automatisation des soins de santé vient d’un enchevêtrement d’évolutions interactionnelles. Il y a l’augmentation de la pression démographique dans le monde qui a un impact majeur sur la capacité en lits requise et le nombre de mains spécialisées dans les soins. Ajoutons à cela l’augmentation du niveau de vie dans de nombreuses régions du monde non occidental où on veut bénéficier de soins de santé de niveau de soin correct ou supérieur.
Actuellement, dans les soins de santé, on remarque une énorme demande en personnel associée à des coûts de main d’œuvre en forte hausse. Parallèlement à la pression accrue sur le personnel, le vieillissement de la main d’œuvre devient problématique. Le résultat de ces évolutions est qu’il faut faire plus avec moins. Si on ajoute les attentes croissantes en matière de qualité, il est alors logique que l’automatisation soit la première option avancée pour apporter une réponse à cette tempête parfaite.
Advertisement
Mais comment l’automatisation – au sens le plus large – peutelle relever ces défis ? Une première réponse réside dans la diversité : l’automatisation est un passe-partout pour les applications dans le secteur de la santé. Quelques exemples : depuis longtemps les salles d'opération s'équippent de plus en plus en robots chirurgicaux. Leur précision et flexibilité se prêtent parfaitement à la chirurgie de précision. On perçoit aussi des applications intéressantes dans les systèmes de mammographie où des freins basés sur des aimants permanents permettent de conserver le positionnement exact pour réaliser une image parfaite. Les appareils à rayons X sont une autre application pertinente. Ici aussi, l’image doit rester stable et la réponse est une automatisation. La pneumatique est omniprésente dans l’hôpital : dans les lits, les pompes, les respirateurs artificiels et les applications nécessitant de l’air comprimé. Nous y reviendrons plus en détail dans un instant, mais commençons d’abord par un bel exemple de fine mécanique.
photo © Vithas Vigo
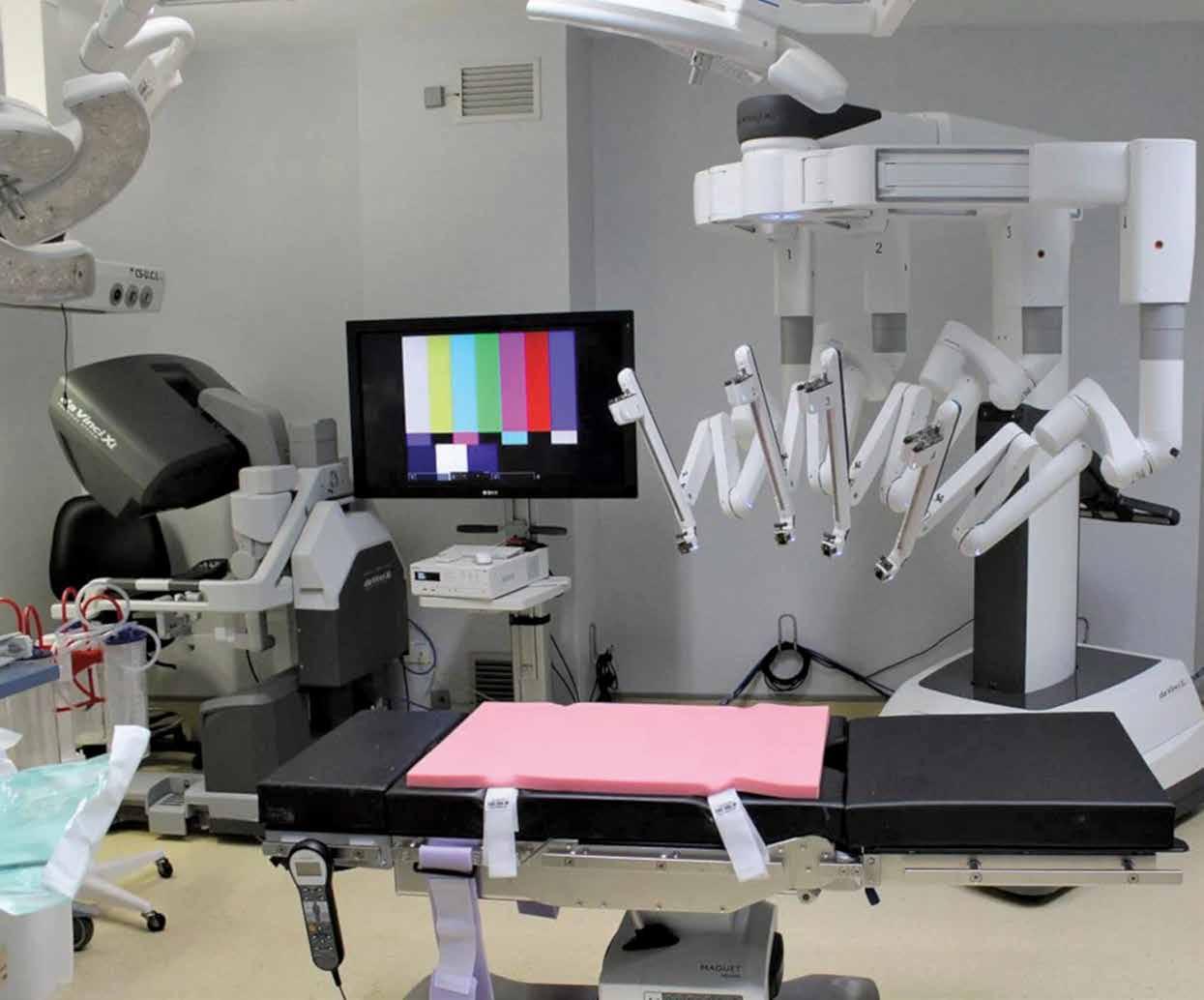
Nous ne pouvons pas trouver une meilleure intégration dans une salle d'opération : air comprimé, commande à distance, système de vision et bras robotiques
Conception précise de vis à billes
Outre l’hygiène, la précision est un terme clé qui revient dans pratiquement toutes les solutions. Les solutions électromécaniques répondent à cette exigence. Les vis à billes sont un bel exemple de cette technologie. Dans les applications de mouvement linéaire, les solutions sont nombreuses.. Cependant, pour garantir des mouvements précis, fiables et répétitifs, on opte plus souvent pour des vis à billes. Cela n’a rien de surprenant car cette solution est parfaitement adaptée au traitement de charges dynamiques variables. En outre, les vis génèrent peu de vibrations et de bruit, et ont peu d’impact sur les autres instruments médicaux ou la perception du patient. C’est aussi la raison pour laquelle on les retrouve souvent dans des applications comme les pompes à sang et les systèmes de transport automatisé d’échantillons.
Si on se penche brièvement sur la technologie, on remarque qu’une vis à billes, dans sa forme la plus simple, se compose d’une vis, d’un écrou et d’un mécanisme permettant aux billes de circuler. La vis a un filet hélicoïdal sur toute la longueur de l’arbre et l’écrou un filet correspondant. Ces filets servent de chemins de roulement intérieurs et extérieurs le long desquels les billes métalliques circulent pour créer le mouvement linéaire de l’écrou et du chariot associé. La construction est efficace, le coefficient de frottement est faible et le couple est transmis avec précision. Bref, d’excellentes propriétés pour le secteur des soins de santé.
Les vis à billes possèdent un certain nombre d’avantages marquants et il faut accorder une attention particulière à leur dimensionnement correct lors de la phase d’ingénierie. Comme pour les autres systèmes, les vis à billes sont disponibles dans diverses qualités, avec une précision et un comportement sous charge variables. Pour vous aider à comprendre cela, il faut d’abord vous expliquer quelques termes.
Le ‘lead’ de la vis à billes est la distance axiale parcourue par la vie à billes par révolution. En théorie, il doit être égal au produit du pas et du nombre de révolutions de la vis, le pas représentant la distance axiale entre les filets. On peut donc dire que la précision d’une vis à billes est la différence entre le lead théorique et la distance axiale réellement parcourue. Tant les organisations de normalisation internationales (ISO) qu’allemandes (DIN) appliquent cela pour établir les classifications des roulements à billes pour le positionnement (P) et le transport (T). Par exemple, la précision de P5 ou T5 est de ± 23 microns sur une course de 300 millimètres, la précision de P7 ou T7 est de ±52 microns sur une course de 300 millimètres; la précision de P10 ou T10 est de ± 210 microns sur une course 300 millimètres.
Un autre facteur important suivant dans l’utilisation des vis à billes pour les applications médicales est le comportement du système par rapport aux charges. Outre la charge statique, des charges dynamiques élevées et importantes se produisent. Ceci est renforcé par le fait que les applications actuelles ont moins d’espace pour la technologie interne. La charge statique est principalement due à la pression exercée par l’écrou à billes. La charge dynamique peut être attribuée au déplacement de l’écrou le long de la vis, aux vitesses variables, aux accélérations et aux cycles, de même qu'au couple d’entraînement associé. Il faut veiller à ce que la vis à billes ne cède pas sous les charges de traction dues à l’étirement ou les charges de compression agissant sur l’arbre. Il convient aussi de se poser d’autres questions. Il peut, par exemple être nécessaire d’utiliser une vis à billes préchargée d’une certaine force entre l’écrou à billes et la vis pour éliminer tout jeu axial et radial éventuel. Dans les applications médicales en particulier, un ingénieur doit aussi contrôler la rigidité de l’assemblage pour maximiser le positionnement et la stabilité du servo-entraînement. L’assemblage de la vis à billes est-il suffisamment rigide pour une application donnée ? En établissant un profil de charge détaillé pour la vis à billes selon l’application dans un appareil ou un système, des erreurs coûteuses peuvent être évitées et la bonne vis à billes peut être sélectionnée. Un certain niveau d’expertise est donc requis dans la conception d’équipements pour le monde médical.
L’air comprimé est incontournable dans un contexte médical
L’air comprimé occupe une place particulière dans les établissements de soins. L’air médical est simple en soi: il se compose principalement d’azote et d’oxygène, est inodore, ininflammable et en théorie exempt de particules, d’huile, d’humidité et autres traces de contamination.
Dans les hôpitaux, les cabinets dentaires et autres établissements de soins, l’air comprimé est fourni de la même manière que dans l’industrie : via un système de conduites pour les gaz médicaux, un compresseur étant utilisé pour produire et distribuer l’air filtré. Quand les systèmes d’alimentation par des conduites ne sont pas réalisables ou disponibles, les bouteilles d’air médical fournissent l’air comprimé utile aux applications critiques comme la chirurgie, l’anesthésie et l’assistance respiratoire.
Il va sans dire que les exigences posées à l’air médical, notamment pour l’assistance respiratoire, sont d’un tout autre niveau que l’air utilisé pour un marteau-piqueur dans l’industrie. Voyons quelques exemples d’applications de l’air comprimé.
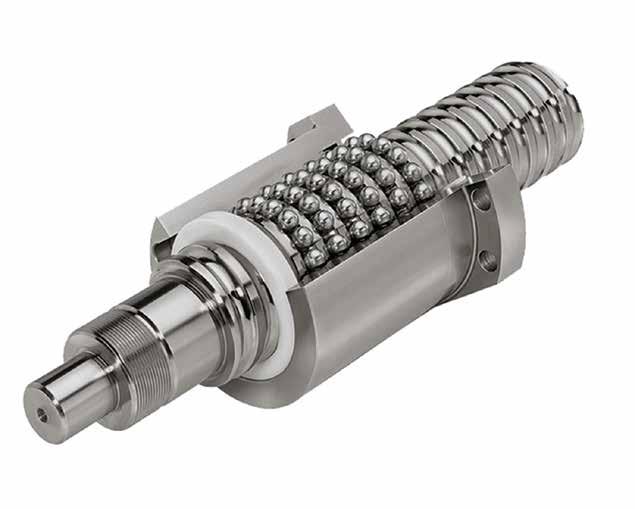
Grâce à leur efficience, leur précision et leur faible résistance au frottement, les vis à billes sont appréciées dans les applications médicales.
PRODUCTION SÉCURISÉE D’ÉCOUVILLONS
Du côté de l’offre, on remarque comment la vague d’automatisation inonde les usines. Le besoin soudain de plus de capacités n’y est pas étranger et la pandémie de coronavirus a tout accéléré. À cela s’ajoute la difficulté liée aux exigences plus strictes en matière de tolérances de ces dernières années. Une tolérance admis autrefois ne l’est par exemple plus aujourd’hui. Tout d’un coup, il faut aller plus vite et produire une très haute qualité.
L’automatisation est parfaite pour maximiser la qualité, éliminer les causes affectant négativement la fiabilité, réduire les coûts et accélérer le temps de mise sur le marché. La répétitivité et la traçabilité sont d’autres avantages de l’automatisation dans les soins de santé.
Un bon exemple d’une mise à l’échelle est la production des fameux écouvillons. Ces écouvillons nasopharyngés ont une forme spécifique par rapport aux écouvillons conventionnels utilisés notamment dans le traitement des plaies. Ils sont fabriqués dans un matériau médical de haute technologie et doivent être longs, fins et partiellement souples pour atteindre l’arrière du nez.
À l’instar des autres dispositifs médicaux, ces écouvillons et le processus de production sont réalisés dans des environnements de salles blanches coûteuses qui doivent être conformes aux exigences légales très strictes. Un problème supplémentaire est que les écouvillons precorona n’étaient produits que par un nombre limité d’entreprises et la demande était alors stable. Les processus de production correspondants n’étaient absolument pas conçus pour faire face à l’énorme augmentation de la demande.
Un des plus grands fabricants d’écouvillons médicaux a alors décidé d’adapter et d’équiper son usine de production aux Etats-Unis. Le département a rapidement eu besoin de 40 nouvelles machines pour répondre à la demande. Un des composants essentiels est le Super Clutch/Brake (SCB), un système d’accouplement/de freinage ayant un temps de réaction de 45 millisecondes, ce qui permet d’obtenir les temps de cycle exigés. Le modèle SCB sélectionné, le Super CB-6, peut atteindre un régime de maximum 500 tr/min et un couple statique de 56,5 Nm.
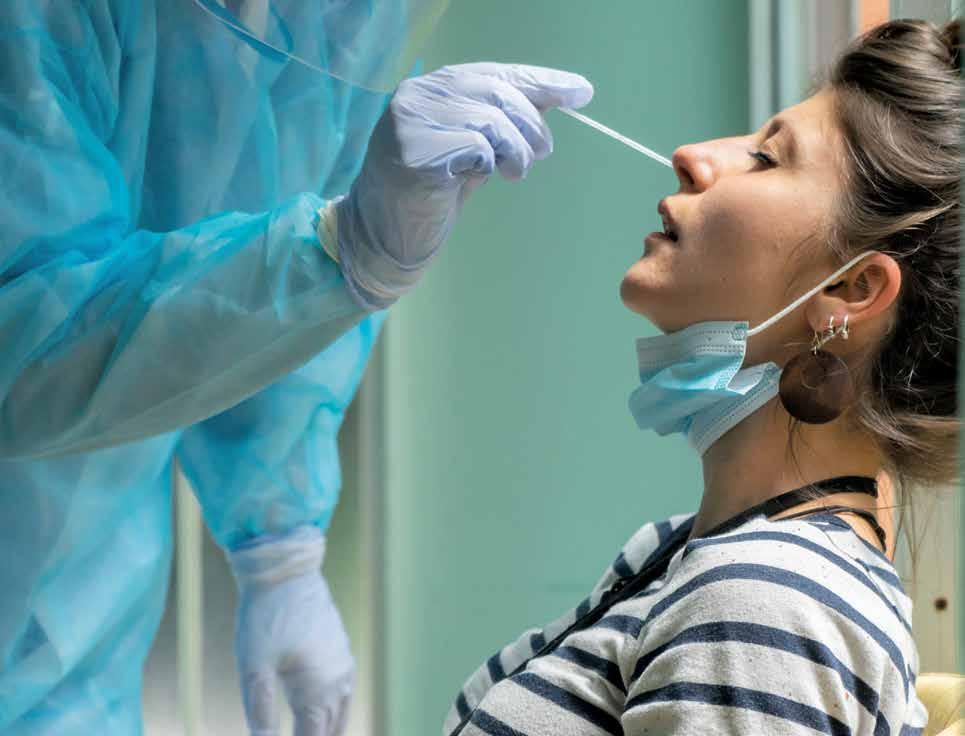
1. Fluide porteur pour l’anesthésie
L’air comprimé est utilisé comme gaz porteur de médicaments inhalables et d’anesthésiants avant et pendant une intervention. Mélanger l’air médical à un anesthésiant permet de garder la dose administrée sous contrôle, tandis que le patient est confortablement installé et respire normalement.
L’inhalation de gaz anesthésique mélangé à du protoxyde d’azote ou un autre air médical est considéré comme un composant fiable de l’anesthésie générale grâce à l’air comprimé pur. Du fait de sa faible teneur en oxygène, l’air médical est un gaz porteur anesthésique plus sûr que le protoxyde d’azote, en particulier pour les patients sensibles à l’empoisonnement à l’oxygène. Les cas délicats de risque d’arrêt respiratoire peuvent nécessiter des traitements avec des concentrations spécifiques d’air médical pour maintenir les niveaux d’oxygène précis et contrôlés. L’air comprimé est alors une ressource cruciale.
2. Assistance respiratoire lors d’interventions chirurgicales
Les médecins et les chirurgiens comptent sur l’air médical pour aider les patients à respirer confortablement au bloc opératoire et autres zones de soins critiques. L’air comprimé médical offre un air de qualité pour les patients sous sédation, les patients ayant des difficultés à respirer de manière autonome et les patients sous traitement pour diverses affections respiratoires. Un apport constant d’air médical pendant une intervention contribue à une respiration uniforme.
3. Air propre pour la respiration artificielle et les couveuses
Les ventilateurs et les couveuses doivent fournir un air propre et contrôlé pour garantir la santé et la sécurité du patient. Les nouveau-nés ont certainement besoin d’un air le plus propre possible lors des premières heures de respiration – surtout après d’éventuelles complications à la naissance. L’air médical doit être exempt de toute trace de virus ou de bactéries. Voilà pourquoi on retrouve aussi l’air comprimé dans les couveuses. Via une régulation de débit à compensation de pression, la distribution d’air médical est réglée idéalement dans les ventilateurs, les masques faciaux, les nébuliseurs, les tubes endotrachéaux, les chambres hyperbares et les unités néonatales de soins intensifs. Les besoins individuels du patient sont satisfaits. Si l’air ambiant présente un risque pour la santé du patient, un air médical de qualité doit être disponible pour maintenir une fonction respiratoire saine.
4. Pour les instruments chirurgicaux pneumatiques
L’air comprimé est utilisé comme source d’alimentation exempte de contamination pour les instruments chirurgicaux pneumatiques dans les blocs opératoires, les cabinets dentaires et les établissements médicaux de première ligne. L’air comprimé alimente les instruments pneumatiques pour notamment la ponction, le perçage, le sciage et autre interventions chirurgicales nécessitant un flux d’air précis et une pression uniforme. Il y aussi les instruments de chirurgie buccale, les instruments orthopédiques, les scies et les perceuses chirurgicales, (l’entraînement de) l’outillage médical, mais aussi les outils et les systèmes de nettoyage et de stérilisation des instruments médicaux. Dans les laboratoires, l’air comprimé est utilisé pour entraîner les instruments mis en œuvre dans l’analyse du sang, pour générer de l’oxygène et de l’azote et autres activités de recherche.
Comment obtenir un air comprimé de qualité ?
Toutes ces applications le montrent: un air comprimé propre est indispensable dans un établissement de soins contemporain. Mais qu’est-ce qu’un air comprimé ‘propre’? Et comment l’obtient-on ? Comme l’air comprimé est populaire dans l’industrie, il est parfois fait référence aux classes ISO ; mais ce n’est pas tout à fait correct dans le contexte médical.
Tout d’abord, il faut établir une distinction entre l’air comprimé à usage médicinal et non médicinal. La différence est relativement facile à expliquer : l’air comprimé utilisé à des fins médicales (respiration, alimentation d’appareils dans les blocs opératoires) est médicinal et tout ce qui ne peut affecter directement la santé du patient est non médicinal. Un exemple est l’air comprimé utilisé exclusivement au sein du service technique. Les deux formes ne peuvent absolument pas entrer en contact.
Monographie de la Pharmacopée européenne
La préparation d’air médicinal implique de suivre les directives de la Pharmacopée européenne. Ces règles ont été élaborées pour normaliser la méthode de production de toutes sortes de médicaments. En d’autres termes, l’air médicinal est considéré comme un médicament et la méthode de production associée doit être réalisée selon des procédures précisément définies.
Un mélangeur, dans un hôpital, qui produit de l’air médicinal à partir des deux éléments primaires, l’oxygène médical (22%) et l’azote médical liquide (78%), doit par exemple répondre aux exigences de pureté définies dans la Pharmacopée européenne.
La Pharmacopée européenne impose des exigences strictes, par exemple les exigences pour l’air medical (voir cette image).
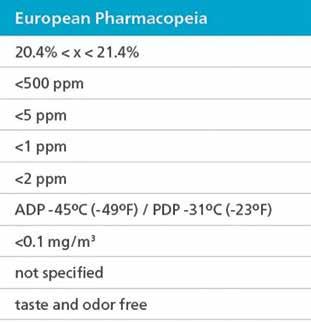
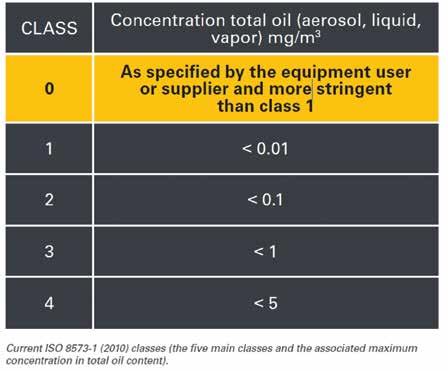
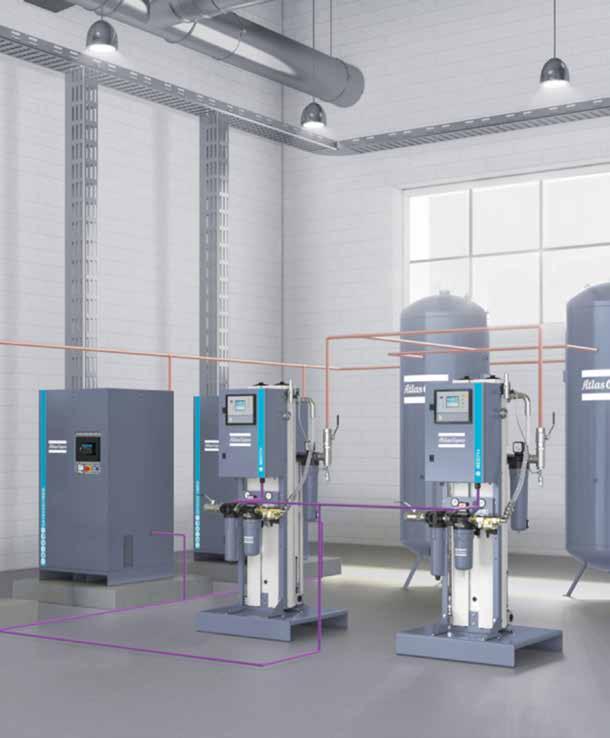
photo © Atlas Copco
L’air certificié peut être garanti via ces systèmes de traitement de l’air. Depuis une mise à jour de la norme ISO 8573-1:2010 une classe 0 a-t-elle été ajoutée à la classification qui permet la mise sur le marché d'appareils avec des fonctionnalités spécifiques.
Les trois piliers de l’ISO-7396-1
La production d’air médical est une chose et son utilisation dans un établissement de soins est liée à des règles spécifiques. On peut les résumer autour de trois piliers : la redondance, la surveillance du CO et la surveillance du point de rosée.
La redondance est obtenue par l’obligation de fournir au moins 3 sources d’air comprimé dont au moins une via un compresseur. Il y a donc toujours la garantie d’avoir assez d’air comprimé. Pas question de repousser une opération parce que l’on travaille sur l’installation. De plus, la troisième source doit être installée dans un local différent, également pour des raisons de sécurité.
La surveillance du CO évite d’avoir des valeurs trop élevées. Une mesure continue et une alarme des niveaux de CO sont obligatoires depuis fin 2016 pour les nouvelles installations ou les rénovations d’installations.
Enfin, la surveillance du point de rosée évite que le point de rosée ne devienne trop élevé car un condensat peut se former dans les conduites et rendre l’air comprimé inutilisable. La quantité maximale de vapeur d’eau dans l’air comprimé médicinal est de 67 ppm, ce qui correspond à un point de rosée atmosphérique supérieur à -45°C. Le développement bactérien s’arrête à un point de rosée sous pression inférieur à -26°C.
www.atlascopco.com www.altramotion.com www.geveke.com
POURQUOI L’ISO 8573-1:2010 RESTE IMPORTANTE : CLASSE 0
La norme ISO 8573-1:2010 est divisée en trois groupes de contaminants : les particules fixes, l’eau (liquide et vapeur) et l’huile (aérosols et vapeur).
Chacune de ces catégories comporte jusqu’à dix classes de pureté (huit pour les particules, dix pour l’eau et cinq pour l’huile). Plus le numéro de la catégorie est bas, plus l’air doit être pur. Ce qui signifie que l’air de classe 4 peut contenir plus d’impuretés que l’air de classe 3. Pour chaque classe de 1 à 10, la norme impose des limites sur le nombre de particules par m³, la taille des particules.
Pour l’eau, les classes les plus strictes sont répertoriées en fonction du point de rosée sous pression et de la teneur en liquide dans l’air en grammes par m³. Concrètement, cela signifie que le point de rosée de l’air de classe 1 doit être d’au moins -70°C, tandis que l’air de classe 9 peut contenir entre 5-10 g/m³ d’eau et/ou de vapeur d’eau. Enfin, la classe ISO pour l’huile est définie par la teneur en huile en mg/ m³. La classe 1 ne doit pas contenir plus de 0,01 mg d’huile, tandis que la classe 4 peut contenir de l’air ayant 500 fois cette quantité (5 mg/m³).
La classe 1 est-elle donc la classe la plus stricte possible ? Non, et c’est précisément pourquoi la norme ISO est importante pour l’air comprimé médicinal. Depuis la mise à jour de la norme en 2010, la classe 0 a été ajoutée à la classification. Celle-ci diffère des autres classes car aucune limite chiffrée n’est formulée, seules 2 conditions sont avancées : ‘comme spécifié par l’équipementier ou l’utilisateur’ et ‘plus strict que la classe 1’. L’illustration ci-dessous montre à quoi ressemble un tel système.
Un système par étages comprenant notamment un séparateur d’eau avec un filtre supplémentaire (1) et (2) élimine les particules d’huile. Un sécheur (3) réduit ensuite le taux d’humidité, éliminant tout risque de condensation, de développement bactérien et de moisissures. Une double filtration (4) et (5) avec un filtre au charbon actif élimine les hydrocarbures (vapeurs d’huiles, odeurs, etc.). Un catalyseur transforme ensuite le CO en CO2. Enfin, un filtre bactérien (6) en sortie élimine les bactéries.
© Atlas Copco
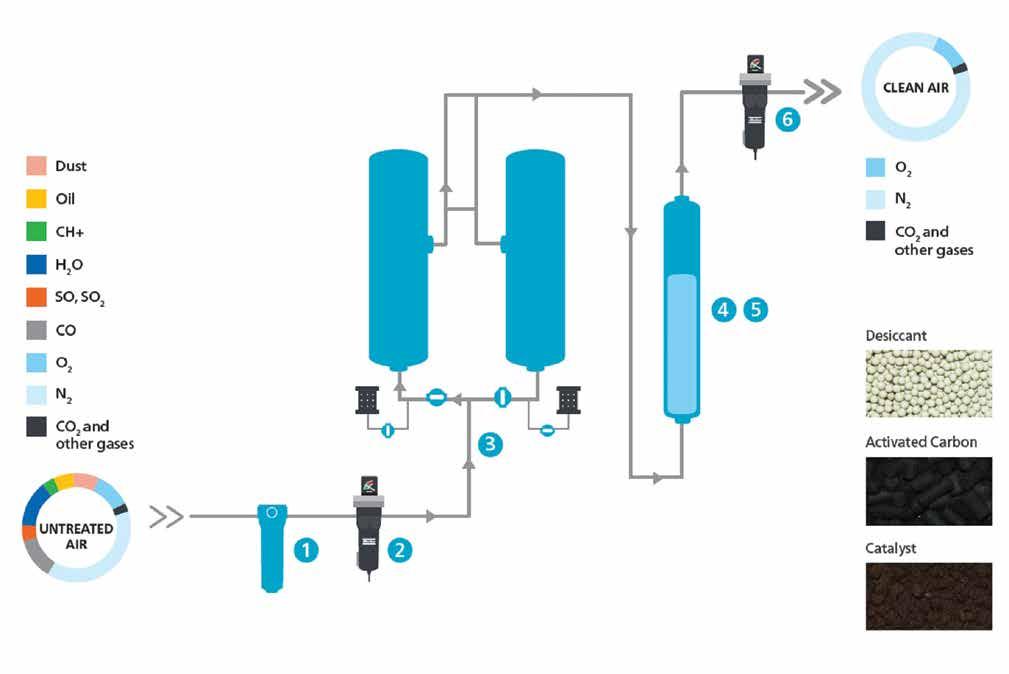
WEG DÉVELOPPE UN REVÊTEMENT ANTIVIRAL POUR SE PROTÉGER CONTRE LA COVID-19
WEG a développé un nouveau revêtement antiviral dans son unité Revêtements et vernis au Brésil. Développé pour l’utilisation sur les machines professionnelles et les équipements hospitaliers, les laboratoires et les environnements médicaux en général, ce nouveau revêtement rend 99,9 % des coronavirus inactifs en quelques minutes de contact avec la surface.
Ce revêtement en polyuréthane W-THANE APA 501 a été développé pendant la pandémie de coronavirus pour les nombreuses industries servies par WEG et qui cherchent toutes à mettre en place des mesures d’hygiène et sécurité plus efficaces. La création de ce revêtement suit les recommandations de l’Agence nationale de surveillance de la santé du Brésil et il a été fabriqué selon les méthodologies définies par la norme internationale BS ISO 21702:2019.
Il est recommandé pour protéger les équipements industriels utilisés dans les environnements à haut risque, notamment les hôpitaux, les centres médicaux et les laboratoires, ainsi que les équipements industriels utilisés sur ces sites. Il n’en reste pas moins adapté à d’autres marchés, tels que les machines et les équipements industriels, et les transports publics.
Ce nouveau revêtement est le fruit des travaux de recherche et de développement de l’unité Revêtements et vernis de WEG, une filiale du groupe WEG. Les agents antiviraux de ce revêtement garantissent la destruction des coronavirus en contact avec sa surface et a fait l’objet de tests poussés avec la souche MHV-3. « Nous ne ménageons pas nos efforts de développement de technologie pour combattre la COVID-19 », souligne Reinaldo Richter, directeur général de WEG Coatings. « Nous pouvons compter sur une équipe de chercheurs très qualifiés pour ce projet et avons atteint nos objectifs en un temps record. » Comme pour tous les revêtements et toutes les peintures WEG, le nouveau revêtement antiviral est disponible sous différentes couleurs pour s’intégrer aussi bien dans les environnements médicaux qu’industriels.
www.weg.net
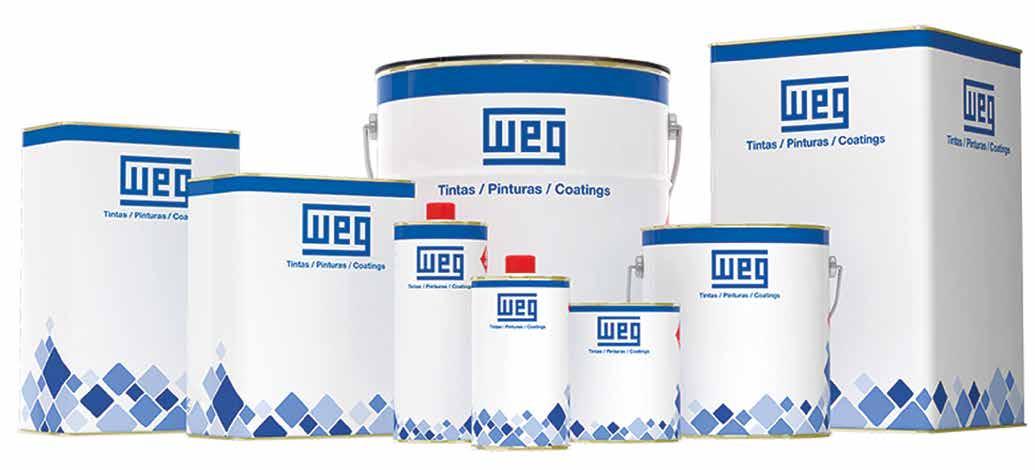
UNE ALTERNATIVE RENTABLE AU DOSAGE
Les systèmes de manipulation de liquide à pression contrôlée sont une manière simple et rentable de doser des volumes de fluides à l’échelle du nanolitre, déclare Paul Kendall, Industry Sector Manager Lifetech chez Festo NWE.
Les maladies infectieuses sont une menace omniprésente pour notre société comme en témoigne l’épidémie de coronavirus. Les laboratoires d’aujourd’hui dépendent de plus en plus de systèmes de manipulation de liquides automatisés pour développer et produire rapidement des nouveaux vaccins pour protéger la population. Si les avantages de ces systèmes sont connus, ils ne sont cependant pas bon marché et représentent un investissement important pour les laboratoires. De plus, ils sont livrés avec une multitude de fonctionnalités qui dépassent les exigences de nombreuses applications, ce qui signifie des coûts inutiles.
Dans de tels cas, il existe une alternative plus rentable: les systèmes de dosage de liquides à pression contrôlée. Ces systèmes sont une solution simple et rapide pour doser des volumes de fluides de l’ordre du nanolitre au millilitre avec précision, fiabilité et évolutivité. Leur concept flexible leur permet de surmonter les nombreuses variantes des propriétés des fluides et leur composition et ils conviennent à des substances aussi liquides que l’alcool ou aussi épaisses que le miel. Ils offrent également une résistance aux substances corrosives et acides. Mécaniquement simples, ces systèmes possèdent un minimum de composants, ce qui simplifie le nettoyage. Un régulateur de pression, couplé à une vanne de sécurité, pressurise le récipient contenant le liquide. Cette pression entraîne ensuite le liquide à travers le tube et l’électrodistributeur. Enfin, la buse distribue le liquide dans le conteneur via une aiguille doseuse dont l’orifice est étalonné (voir figure 1). Il est important de considérer les facteurs suivants lors de la conception d’un système basé sur la pression car ils affectent la quantité et la qualité des doses :
1. Résistance à l’écoulement
La vitesse d’écoulement du système est définie par la pression ainsi que par la résistance globale du trajet du fluide. Cette résistance dépend du diamètre intérieur du tube (ID), de sa longueur, de la géométrie du distributeur et des raccords. La taille de l’aiguille doseuse a une influence directe sur la vitesse des liquides. Contrairement à la pression et au temps – qui peuvent être contrôlés et modifiés logiciellement – la bonne taille doit être sélectionnée dès le départ.
2. Pression
La pression a un effet significatif sur les volumes de dosage et – plus important encore – aide à contrôler la vitesse du fluide lorsqu’il passe dans l’aiguille doseuse. Elle peut aussi être utilisée pour contrôler les viscosités des fluides afin de réaliser des dosages propres et sans éclaboussures. La pression peut être générée de plusieurs manières, via, par exemple, une source de gaz externe comme l’azote, ou un compresseur pour pomper de l’air dans le réservoir de liquide fermé. Les plages de pression dans les systèmes de dosage automatisés sont généralement faibles - à peine 100–250 millibars. Néanmoins, il est important de mettre en place des mesures de sécurité pouvant relâcher la pression en cas de fuite ou de défaillance technique.
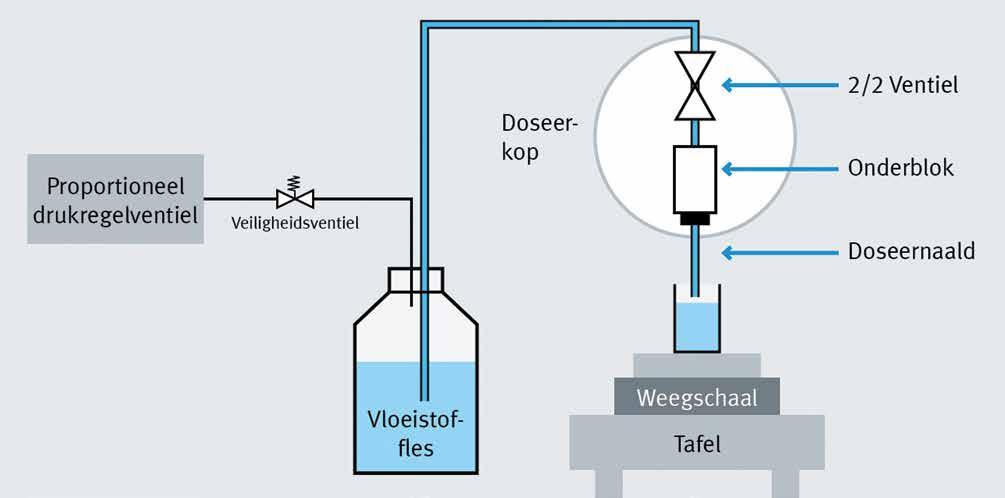
Figure 1 : Mécaniquement simples, ces systèmes nécessitent un minimum de composants, ce qui simplifie le nettoyage.
3. Temps de distribution
Les quantités à distribuer sont contrôlées par l’électrodistributeur, le volume de fluide dosé étant principalement influencé par le temps de cycle du distributeur (voir figure 2). Les distributeurs ayant des temps de réponse courts et hautement reproductibles offrent une bien meilleure précision de dosage à des vitesses plus élevées. Il est important de noter que les électrodistributeurs génèrent de l’énergie lorsqu’ils sont ouvert et leurs performances changent souvent au fur et à mesure qu’ils s’échauffent. L’usage d’un distributeur ayant un débit supérieur pour des temps plus courts réduit le développement de chaleur mais cela requiert un système ayant une excellente reproductibilité, comme la tête de dosage VTOE de Festo (voir image ci-dessous).
L'un des grands avantages des systèmes de distribution basés sur la pression est leur évolutivité. Les têtes de dosage individuelles peuvent être aisément combinées pour créer des têtes de dosage multi-canaux pouvant traiter différents volumes d’aliquotes, de fluides et de pressions. Les fluides ayant différentes classes peuvent être dosés via un montage de têtes de dosage multi-canaux sur un axe électrique, créant ainsi un système de portique. En ce qui concerne les systèmes multi-canaux cependant, d’infimes différences entre les entrées, les distributeurs et les buses peuvent amener certains canaux à doser des volumes plus élevés que d’autres – selon une variabilité intrinsèque d’aiguille à aiguille de l’ordre de 4%. À des résolutions de 1 ms ou plus, il est difficile de compenser ces variations à l’aide du processeur qui contrôle le temps de dosage de l’électrodistributeur.
Une meilleure manière de procéder consiste à étalonner les canaux séparés en faisant varier le courant d’appel et de maintien de l’électrodistributeur afin que tous les canaux distribuent la même quantité en utilisant les mêmes temps de distribution. Festo facilite cela avec son module de contrôle de distributeur VAEM qui utilise un logiciel convivial pour réduire la variabilité d’aiguille à aiguille à moins de 1% dans la plupart des cas. Les améliorations apportées à l’échelle, à la rapidité et à la qualité des procédés pharmaceutiques et biotechnologiques grâce à la manipulation automatisée des liquides ont permis de réduire les délais et d’obtenir des résultats plus rapidement tout en rendant la découverte de médicaments plus efficace. Les systèmes de distribution de liquides sous pression peuvent aider à optimiser le rendement dans les tâches d’automatisation de laboratoire pour une fraction du coût d’une robotique complexe.
www.festo.be
Image 3 : La tête de dosage VTOE distribue des petites quantités de produit sans contact.
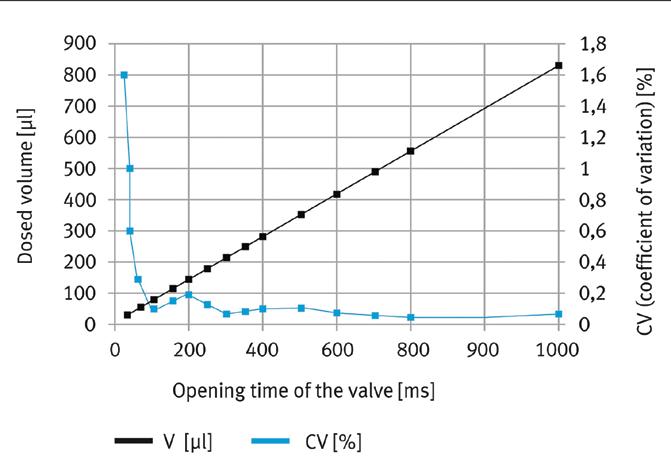
Figure 2 : Le volume de fluide dosé étant principalement influencé par le temps de cycle du distributeur.
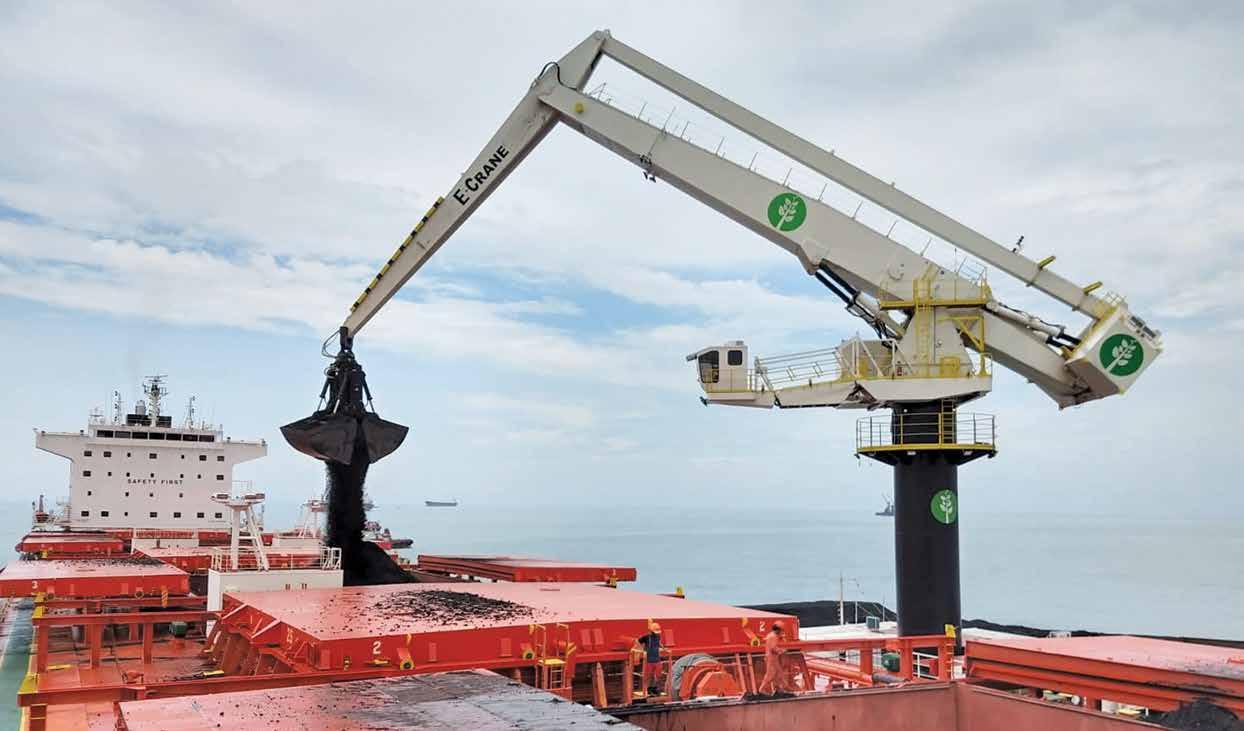
E-CRANE ET BOSCH REXROTH : UN PARTENARIAT ENTRE DEUX ENTREPRISES AVIDES D’INNOVATION
Cinquante ans de Bosch Rexroth Belgique, c’est aussi cinquante ans de coopération étroite avec nos partenaires et clients, dans le but de trouver ensemble la meilleure solution à leurs défis. Parmi ces relations étroites, citons E-Crane, fabricant et fournisseur de grues à usage intensif conçues pour le traitement du vrac et de la ferraille. « La coopération entre deux entreprises avides d’innovation aboutit souvent à d’excellents résultats. »
E-Crane est un fabricant international de grues de pointe regroupant plus de 550 collaborateurs répartis dans des succursales aux quatre coins du monde. Ce n’est pas un hasard si le « e » figurant dans le nom de l'entreprise signifie « équilibre ». En effet, E-Crane se démarque de la concurrence en recherchant continuellement le meilleur équilibre possible pour ses grues. C’est surtout au niveau des contrepoids qu’elle fait souvent la différence, déclare Sven De Vriendt : « Nous utilisons des contrepoids mobiles placés à l’arrière. Ils peuvent ainsi s’adapter de manière dynamique à la portée de la charge à déplacer. Cette façon de faire permet d’économiser beaucoup d’énergie et d’argent. » Il est essentiel que les grues soient dotées de systèmes hydrauliques fiables. Depuis sa fondation, E-Crane a toujours fait confiance à Bosch Rexroth à cet égard, et ce depuis plus de 25 ans. Le succès de cette coopération réside en partie dans la proximité de Bosch Rexroth. Cela explique pourquoi le lien entre Bosch Rexroth et E-Crane va bien au-delà de la relation traditionnelle client/fournisseur. « On peut parler d’une coinnovation », déclare Erik Staes, responsable des applications mobiles chez Bosch Rexroth : « Ensemble, nous nous penchons sur les possibilités de rendre les grues encore plus performantes, efficaces et économiques, et nous élaborons les conceptions qui permettent de concrétiser ces solutions. Cette approche a déjà porté ses fruits. »
Bloc de distribution doté d’une section de cumul
Parmi ces grandes avancées, citons le nouveau bloc de distribution qui a été développé pour E-Crane après que son prédécesseur a été retiré de la production en 2014. « Erik Staes explique : « Lors d’une visite conjointe d’E-Crane et de Rexroth Belgique à notre département d’ingénierie à Lohr, en Allemagne, nous avons finalement décidé d’utiliser un
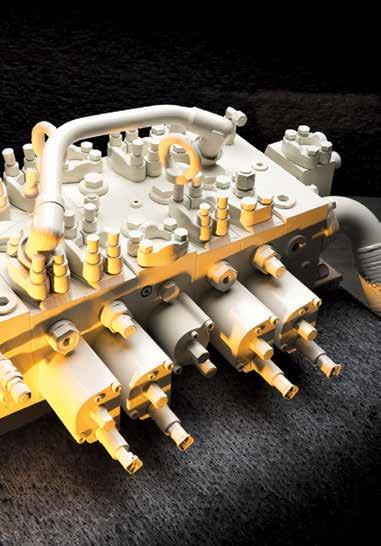
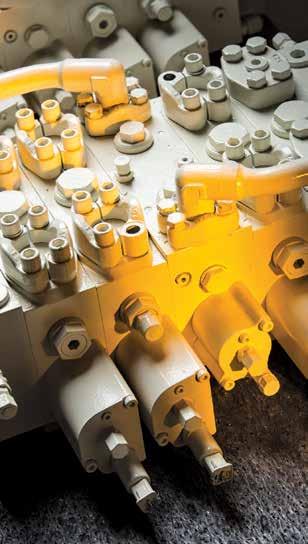
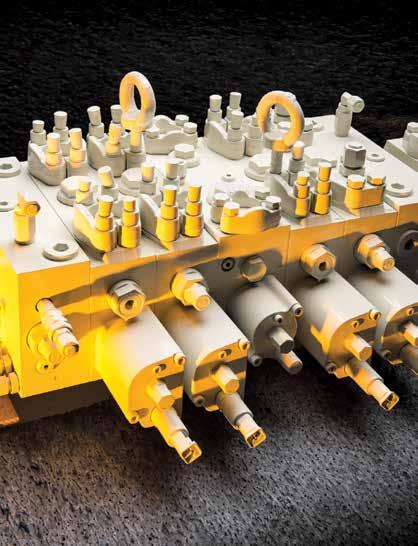
bloc de distribution M7-25 doté d’une ‘section de cumul’ supplémentaire. L’avantage de cette dernière est qu’elle peut être fermée. Autrement dit, les flux des deux pompes ne sont plus constamment cumulés à la plus haute pression requise. Actuellement, les pompes fonctionnent la plupart du temps chacune à une pression différente, ce qui permet de mieux répartir l’énergie disponible et d’augmenter la performance de la grue de près de 25 %. La section de cumul n’est ouverte que lorsque l’on a besoin d’un débit élevé, permettant de cumuler les deux pompes comme dans le bloc d’origine. »
Sven De Vriendt partage cet avis : « Ce qui semblait poser problème au départ a finalement abouti à une amélioration technique significative de la grue, offrant au grutier un rendement horaire nettement supérieur. » Mais ce n’est pas tout, souligne Sven : « Nous avons mis en œuvre leur solution (par le biais de raccordements externes), ce qui a permis de répartir encore plus de fonctions entre les deux sections qu'à l’origine. Bosch Rexroth a découvert cette addition lors d'une visite et nous a indiqué qu’il était également possible d’intégrer ce raccordement à l'intérieur du système. Et voilà comment la volonté d’innover des deux entreprises a abouti à un résultat encore meilleur. »
La relation entre E-Crane et Bosch Rexroth se caractérise par des innovations résultant d’une coopération et réflexion commune : il ne s’agit pas seulement d’une relation fournisseur-client, mais d’un partenariat étroit visant à trouver à tout moment la meilleure solution aux défis techniques et métiers. Cela permet à E-Crane d’être encore plus efficace et productive. « Autrefois, toutes nos grues étaient construites sur mesure. Désormais, nous partons souvent d’un modèle standard que nous adaptons ensuite aux besoins de nos clients », explique Sven de Vriendt. « Cette approche reflète la façon dont nous travaillons avec Bosch Rexroth : nous leur expliquons ce que nous souhaitons atteindre en tant qu’entreprise, puis ils nous présentent les solutions possibles. Nous commençons ensuite à perfectionner ces solutions ensemble jusqu’à ce qu’elles répondent parfaitement à nos besoins. Cette approche est totalement différente de celle de l’époque où nous devions nous procurer systématiquement les produits d’un fournisseur et nous charger seuls des modifications. »
En route vers le projet suivant
Travailler ensemble à la construction de meilleures grues et d’une meilleure organisation est non seulement bénéfique pour les affaires, mais c’est aussi très agréable. « Il faut reconnaître que tout se passe plus aisément grâce à la présence depuis le tout début des experts techniques de Bosch Rexroth. C’est toujours plus facile de parler entre ingénieurs », plaisante Sven De Vriendt.
Les deux entreprises semblent loin de se lasser l’une de l’autre. Le prochain grand projet est déjà en route, mais ils ne peuvent pas nous en dire plus pour l'instant. À suivre !
www. boschrexroth.com www.e-crane.com
LE CETOP A 60 ANS: ENTRETIEN AVEC STEFAN KÖNIG
Le Comité Européen des transmissions oléohydrauliques et pneumatiques souffle 60 bougies cette année. Au cours de ces 6 décennies, le secteur a connu une énorme évolution et l’avenir va sans aucun doute apporter d’autres développements aussi passionnants sur ce marché innovant et en mouvement. Autant de raisons d’aller discuter avec Stefan König, président du CETOP depuis 2016.
Automation Magazine : Qu’en est-il de l’organisation de CETOP anno 2022?
Stefan König: « Nous pouvons affirmer que nous sommes une organisation européenne largement soutenue. Le Comité rassemble 18 fédérations nationales, dont Indumotion. Si nous additionnions toutes les entreprises membres des organisations nationales, nous arrivons à plus de 1.000 entreprises actives dans le secteur des transmissions oléohydrauliques et pneumatiques qui représentent 70.000 salariés et un chiffre d’affaires d’environ 13 milliards d’euros. Nous bénéficions d’un large soutien dans le secteur et nous avons un bon mix de petites et de grandes entreprises. »
AM : Quelles activités menez-vous pour atteindre l’objectif?
« Outre la fonction faîtière pour les organisations nationales, le Comité est actif sur la scène internationale et donc membre de l’International Statistic Committee (ISC), ce qui nous permet de fournir à nos membres de l’information ciblée sur le secteur dans le monde entier. Une autre tâche importante consiste à suivre et à évaluer les normes, les législations et les directives du secteur. Via nos ‘position papers’ diffusés sur le site web, nous faisons connaître nos points de vue jusque dans les plus hautes sphères. »
« Grâce aux connaissances techniques et à l’expérience que nos comités et nos membres ont à leur disposition, nous remarquons parfois des manquements dans les directives et autres, qui sont peu claires ou qui exigent de la nuance. Via nos position papers, nous clarifions notre point de vue et nous faisons des recommandations. »
« On peut citer deux exemples avec la Directive Machines et la Directive sur les récipients sous pression. Outre cette position, nous influençons directement les décisions politiques pouvant être pertinentes pour nos membres. Nous jouons aussi un rôle pour que nos organisations nationales regardent dans la même direction afin d’être plus forts au niveau international. »
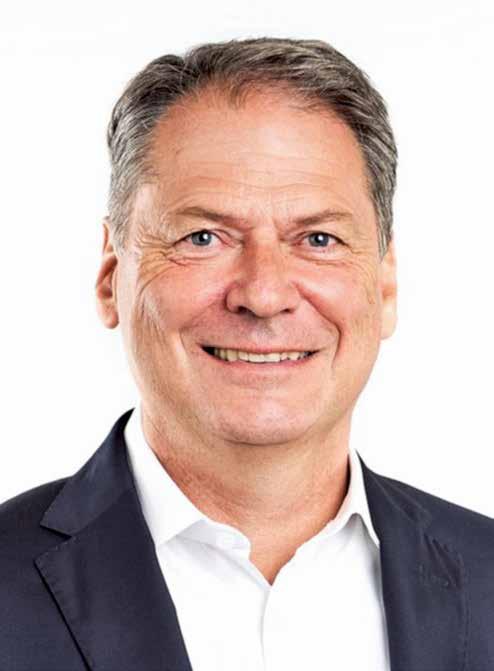
AM : En termes d’innovation, nous remarquons que l’industrie se focalise sur les évolutions orientées IT comme la digitalisation et l’intelligence artificielle. Quelles sont les grandes évolutions technologiques dans le domaine des transmissions oléohydrauliques et pneumatiques ?
Stefan König
Stefan König « Ne vous y trompez pas : parmi toutes les innovations, les transmissions oléohydrauliques et pneumatiques sont et restent incontournables. Il suffit de mentionner quelques secteurs où nos systèmes sont au cœur de l’action, au sens propre comme au figuré : l’industrie automobile, les machines de construction et agricoles, le transport, les machines alimentaires et d’emballage, le travail du bois, l’électrotechnique, la construction navale, la production et la transformation des métaux, l’aéronautique et l’aérospatiale, le secteur médical, les technologies environnementales, … »
« Je pourrais continuer pendant une demi-heure mais vous voyez où je veux en venir. Il est impossible de citer une ou deux innovations car notre marché est tellement diversifié et fascinant qu’il y en a des centaines. »
« Nous vivons des temps incertains, vos lecteurs l’ont certainement remarqué. Il y a une pénurie mondiale d’énergie et de matières premières et il faut faire face aux conséquences de la pandémie, aux défis logistiques et aujourd’hui à une guerre à nos portes. Toutes ces raisons conduisent à de fortes hausses de prix. Dans l’industrie, l’efficacité énergétique des machines et des installations va devenir cruciale. Les transmissions oléohydrauliques et pneumatiques et autres
AM : Nous remarquons parfois que les connaissances en pneumatique et en oléohydraulique régressent. Est-ce aussi votre sentiment ?
« Je ne dirais pas que les connaissances déclinent mais qu’elles sont moins bien diffusées. Nos écoles et nos universités font de l’excellent travail mais il n’est pas facile – si pas impossible – d’apprendre tous les aspects de chaque secteur aux jeunes. »
« C’est une tâche importante qui incombe à nos fédérations qui doivent prendre l’initiative de former les individus audelà du contexte scolaire, jusqu’à ce qu’ils disposent des compétences utiles. La formation continue n’est pas un effet de mode, c’est une nécessité. »
www.cetop.org
formes de haute technologie jouent un rôle majeur dans l’optimisation continue des solutions d’entraînement. Heureusement, le changement est amorcé: nous sommes de plus en plus conscients du coût total de possession d’un produit. Nous pouvons limiter le coût en réduisant notamment la consommation d’énergie, ce qui peut se faire par une efficacité énergétique meilleure. Pour moi, c’est une évolution globale très importante dans le secteur. »
AM : Quelle est la meilleure voie à suivre pour cela?
Stefan König: « Je pense que nous devons travailler plusieurs pistes à la fois. Il faut par exemple limiter davantage les pertes par frottement dans les systèmes, travailler avec des régulations de vitesse variables et créer des systèmes optimisés dynamiquement. Les opportunités d’économies sont infinies. »
« Pour tous les types d’entraînements de machines, il existe – outre l’efficacité énergétique de l’entraînement – d’autres manières de limiter les pertes : par exemple l’optimisation des puissances consommées dans le cadre de l’objectif de la machine (l’usinage de pièces, par exemple) et la capacité utilisée par la machine proprement dite (pour l’élimination de l’inertie du moteur, le déplacement des grappins, …) . »
« Un effet secondaire bienvenu de ce processus d’optimisation est que le système plus léger qui en résulte devient nettement plus dynamique. »
À PROPOS DE STEFAN KÖNIG
À l’issue de ses études d’ingénieur à la Hochschule à Bremen et d’une première expérience professionnelle, Stefan König est entré chez Danfoss, le spécialiste de l’entraînement.
32 ans plus tard, il travaille toujours au sein de l’entreprise où il a occupé plusieurs postes. Le fil conducteur de sa carrière est le caractère international de ses fonctions. Il a ainsi occupé des fonctions de vente sur le marché chinois et dans les zones EMEA et APAC (Asie et Pacifique).
Aujourd’hui, il cherche à se rapprocher de chez lui et est responsable de la région Europe centrale. Stefan König n’est pas un inconnu au CETOP car il en était le viceprésident depuis 2013. En 2016, il a été nommé président de l’organisation.