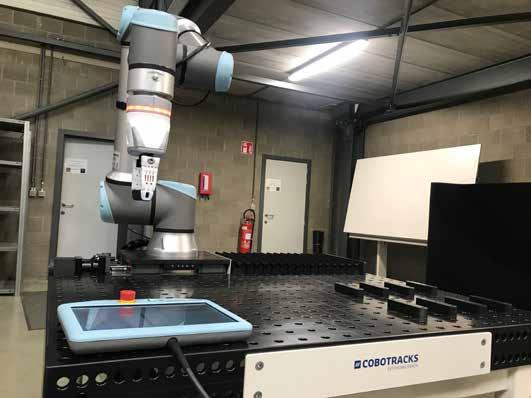
21 minute read
Uitbreiden van cobot werkgebied met lineaire as
De cobot weet dankzij een servomotor met encoder exact zijn positie. Bij de verticale uitvoering wordt omwille van de veiligheid overgeschakeld op een kogelomloopspindel.
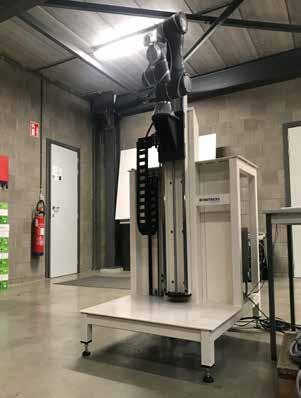
Advertisement
U las het al in dit dossier: cobots veroveren steeds meer marktaandeel. Niet alleen de vooruitgang in cobottechnologie zorgt hiervoor, ook de producenten van de ‘periferie’ maken deze verbreding mogelijk. Een goed voorbeeld hiervan is het Genks bedrijf Cobotracks, dat via een lineaire track de cobot een ‘zevende as’ bezorgt.
Het is bedrijfsleider Pieter Vansichen die ons wat meer vertelt over de activiteiten van het bedrijf: ‘Ons zusterbedrijf Vansichen Lineairtechniek kan bogen op een schat aan ervaring in de productie van tracks voor traditionele industriële robots. Via deze tracks beschikken ze over een zevende as, waardoor hun actieradius aanzienlijk uitgebreid wordt. Op een bepaald moment kwamen op vakbeurzen en in de vakmedia steeds meer cobots in ons vizier. Ook wij voelden aan dat dit een sterke groeimarkt zou worden. Daarom wilden we ook een oplossing voor dit segment, maar omdat deze markt zo specifiek is beslisten we om dat via een apart bedrijf te doen.’
‘De situatie was op dat moment zo dat één speler - Universal Robots - een uitgesproken sterke positie had. In eerste instantie wilden we daarom specifiek voor hun cobot een oplossing uitdokteren. Maar om voor UR een track te ontwikkelen, moet je oplossing UR+ gecertificeerd zijn. Die UR+ certificatie kan je zien als een soort appstore, maar dan specifiek voor de cobots van het bedrijf. Elke onderneming kan in principe een oplossing ontwikkelen voor Universal Robots, maar daarvoor moet je wel beantwoorden aan enkele strenge kwaliteitseisen. Zo moesten we een prototype bouwen, die door hun ingenieurs zeer grondig getest werd op alle mogelijke details. Het is ook niet alleen zaak dat je ontwikkeling werkt op hun cobots, het moet ook compatibel zijn met de andere UR+ componenten en accessoires die andere bedrijven maken voor Universal Robots. Daarnaast verwachten ze van bedrijven zoals ons ook kwaliteitseisen van onze klantenbenadering, zoals het ter beschikking stellen van duidelijke handleidingen en kwalitatieve catalogi. In ruil krijgt onze oplossing met een zevende as een plaats in hun UR+ platform, waardoor onze producten een bredere visibiliteit krijgen.’
Plug & play zorgt voor gebruiksgemak
‘Er is al een andere speler die een zevende as aanbiedt voor Universal Robot, maar onze oplossing gaat nog een stuk verder. Vooral de software beschikt over meer functionaliteiten, zodat de integratie van de robot makkelijker verloopt. Het systeem werkt volgens het plug-and-play principe wat drempelverlagend werkt en bovendien kunnen we de cobot gerichter besturen, dankzij de uitgebreide mogelijkheid om meerdere stopplaatsen en variaties in de snelheid te realiseren. Hét verkoopsargument voor een cobot is zijn gebruiksvriendelijkheid. We wilden die filosofie ook verder uitdragen in onze oplossing.’
Breed palet aan applicaties
‘De mogelijke applicaties voor deze toepassing zijn zeer divers. Wij denken vooral in de richting van lastoepassingen en logistieke palletiseeropdrachten, maar we zijn ook bezig met projecten om lange werkstukken te verlijmen. Een cobot zonder zevende as heeft hiervoor een te beperkte reikwijdte. Ook voor montagetaken zoals bouten aandraaien op lange werkstukken krijgen we aanvragen. Ondertussen zijn er al units verkocht aan quasi alle buurlanden: Duitsland, Denemarken, Spanje, UK, Zwitserland, Italië en Luxemburg. Er is dus duidelijk een grote markt voor, want onze oplossing krijgt veel bijval. Nochtans is door de COVID-19 uitbraak ons systeem op nog geen enkele vakbeurs getoond.‘
Opbouw
Pieter Vansichen: ‘We hadden via ons zusterbedrijf uiteraard al veel ervaring met de ontwikkeling van een zevende as voor industriële robots. Het grote verschil in de benadering is dat het in dit geval geen puur mechatronische oplossing is. Ook de software en de communicatie met de cobot moesten we volledig uitdokteren. Dat is een proces dat toch zeer veel inzicht in de werking van een cobot vraagt.’
‘We opteerden voor een stalen constructie, al kunnen we ook aluminium aanbieden als de klant daar om vraagt. Met een stalen uitvoering kunnen we langere afstanden overbruggen dan met aluminium. We kunnen in principe tot 50 meter gaan terwijl ook de stijfheid beter is. De lineaire beweging verloopt standaard met een tandriemoverbrenging, maar voor langere lengtes schakelen we over op een tandheugel. Een tandriemoverbrenging wordt iets minder nauwkeurig bij die lange lengtes, een hinderpaal waar tandheugelsystemen niet mee geconfronteerd worden. Als de beweging in de verticale richting gaat, maken we dan weer gebruik van een kogelomloopspindel, omdat dit veiliger is.’
De aandrijving van de lineaire beweging gebeurt standaard met een servomotor en bijhorende drive van SEW. In theorie zouden we ook met stappenmotoren kunnen werken, maar dat doen we niet omdat de werking met een servomotor meer secuur en compacter is. De stuurmodule van een stappenmotor telt het aantal stappen om zijn positie te bepalen, er is geen terugkoppeling van de exacte beweging van de motor. Bij hoge snelheden kunnen stappen verloren gaan en verliest de installatie zijn kennis over de correcte positie. Bij zeer lage snelheden kan er een oscillerend gedrag optreden. Onze servomotor werkt met een resolver waardoor we veel nauwkeuriger kunnen werken. Dit zowel wat betreft de positioneernauwkeurigheid als herhaalnauwkeurigheid. Daarbovenop heeft de servomotor een breder snelheidsbereik waardoor we dit aandrijfsysteem kunnen inzetten in meerdere oplossingen. Hiermee beperken we het aantal benodigde spare parts en kunnen we een hoge servicegraad garanderen.
Ook voor andere cobots
‘Dat we eerst een oplossing uitdokterden voor Universal Robots was ergens logisch, omdat zij de marktleider zijn in de cobotwereld. Ondertussen zijn we volop bezig om ook voor andere producenten oplossingen met een zevende as te ontwikkelen. Zo zijn we bezig met een as voor Techman - ook een zeer grote speler - en Doosan en FANUC komen ook aan bod. Het is een boeiende markt die voortdurend groeit en in beweging is. Omdat we al de ervaring opgebouwd hebben via Universal Robots, kunnen we meteen van op een hoger niveau starten en van daaruit terug meer specifiek naar de fabrikant in kwestie toewerken. Dat vergt wel de nodige openheid van de cobotproducenten. We hebben niet alleen de mechanische afmetingen nodig, we moeten ons echt kunnen inwerken in de werking van de cobot: welke signalen worden er gecommuniceerd, via welke poorten gebeurt dat, hoe zitten de sturingen in elkaar?’
Veiligheid?
‘Universal Robots legt ons in principe geen maximumsnelheden of -versnellingen op. We kunnen installaties bouwen zonder beperkingen. De cobot blijft volledig functioneren zoals hij dat zou doen zonder track. Wel moet de eindklant zelf de veiligheid van zijn installatie evalueren. Net zoals hij dat moet doen voor een andere machine en dat hangt volledig af van zijn applicatie. Klanten vragen wel eens of een cobot met een zevende as ook nog collaboratief kan werken, maar ook hier ligt het antwoord in de toepassing van de klant: welke risico’s zijn er bijgekomen, wat is de snelheid, wat zijn de genomen veiligheidsmaatregelen… Soms kan gewerkt worden met veiligheidslaserscanners, in andere gevallen is een hekwerk vereist.’
‘Voorts is specifiek onderhoud niet nodig, tenzij wat bijsmeren bij uitvoeringen met een tandheugel of kogelomloopspindel. Het is dus zeker een onderhoudsarme oplossing’, besluit Pieter Vansichen.
www.cobotracks.com
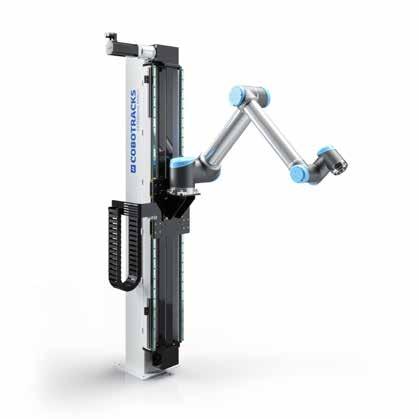
Via een lineaire as wordt het bereik van de cobot sterk uitgebreid. Ook een verticale uitvoering is mogelijk.

ESCO VERHUIST EN LANCEERT EEN COBOT
Goede vooruitzichten voor Esco voor het eind van 2020, want het bedrijf neemt nog voor het jaareinde zijn intrek in de nieuwe gebouwen in Ghislenghien. Daarnaast is er nog meer goed nieuws, want Mitsubishi lanceerde onlangs zijn eerste cobot. Meer dan genoeg voer voor een gesprek met sales manager Koen D’Haese.
‘Mitsubishi staat al lang bekend om zijn lijn industriële robots voor middelgrote en kleine payloads. In Japan, produceert het bedrijf sinds 1980 robots met vier en zes assen. Ondertussen werden er al meer dan 120.000 robots geïnstalleerd wereldwijd, vertelt Koen D’Haese van Esco. ‘We volgen al een tijd de evoluties in de cobotsector op de voet, want we zien toch veel potentieel in deze toestellen. Bij de klassieke robots zijn wij vooral actief in het segment met een payload van 1 tot ongeveer 12 kg, cobots opereren ook deels in dit lichtere segment. Vandaar dat Mistubishi deze uitbreiding van het gamma belangrijk vindt.’
Veiligheid door Safe Torque Range (STR)
‘Mitsubishi draagt veiligheid en nauwkeurigheid hoog in het vaandel en dat weerspiegelt zich ook in de ontwikkeling van deze nieuwe cobot, die Melfa Assista gedoopt werd. Om de cobot veilig te laten werken in zones met menselijke aanwezigheid wordt gebruik gemaakt van de veiligheidsfunctie safe torque range (STR). De cobot weet welk koppel er in een bepaald gebied moet gemeten worden. Bij de minste aanraking of blokkering zal dat koppel niet langer kloppen en stopt de cobot onmiddellijk met werken. Een tweede veiligheidsfunctie is de statusindicatie via ledaanduiding: groen staat voor ‘in werking’, oranje voor ‘teach mode’ en rood voor ‘alarm’. Dat geeft personen in de buurt van de cobot meteen visueel duidelijke informatie over de status van de cobot.’
Een derde veiligheidsfunctie is de mogelijkheid om verschillende speedmodes in te stellen. Afhankelijk van de risicobeoordeling kan de cobot ingesteld worden in verschillende snelheidszones in functie van de aanwezigheid van personen. Dat laat toe om ze sneller te laten werken bij de afwezigheid van werknemers in de ruimte, wat stevig bijdraagt aan de productiviteit. Er zijn 3 mogelijke zones: Highspeed Mode (1000 mm/s), Standard Mode (250 mm/s) en Low Speed Mode (50 mm/s).
Programmeren
Voor eenvoudige taken hebben we een intuïtieve en tactiele grafische programmeertool “RT Visual Ox” ontworpen. Door het gebruiksgemak kunt u uw programma’s met eenvoudige blokken bouwen, zonder voorafgaande programmeerkennis. Met behulp van een stapsgewijze grafische wizard kunt u alle benodigde parameters definiëren. Voor complexere taken kunt u Assista met “RT ToolBox3” op precies dezelfde manier programmeren als onze andere robots.
Nieuwe generatie motoren
De servomotoren van de J5-serie zorgen voor een veilige samenwerking tussen mens en robot zonder extra kracht- of koppelsensoren. Alles wordt beheerd in de drive dankzij het real-time beheer van de stroom die naar de motor wordt gestuurd. Deze motoren en drives zijn ook beschikbaar voor specifieke automatiseringsprojecten van onze klanten.
Samenwerkingen
‘Klanten zijn vragende partij voor complete oplossingen. Daarom is Mitsubishi ook een aantal samenwerkingen aangegaan met leveranciers van grijpers, krachtsensoren en

Mitsubishi lanceert de Melfa Assista, de eerste cobot van het bedrijf
De veiligheid wordt onder meer gewaarborgd door Safe Torque Range, verschillende snelheidszones en een visuele statusaanduiding
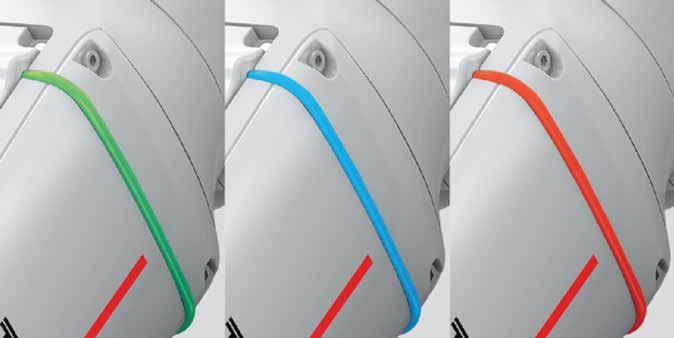
visionsystemen. Daar zitten best wel bekende namen bij. Voor de grijpers gaat het onder meer over Schunk, Zimmer, Schmalz en SMC, bij de visionsystemen is Cognex een klinkende naam. Hun product wordt in een standaardoplossing mee geïmplementeerd in de software, waardoor het instellen veel makkelijker wordt. In het geval van Cognex wordt de camera bijvoorbeeld automatisch gekalibreerd via onze software, wat de gebruiker tijdrovende instellingen achteraf bespaart.’
Nauwkeurigheid met nieuwste encodertechnologie
Koen D’Haese: ‘Mitsubishi staat ook alom bekend om de grote nauwkeurigheid en dat is bij dit toestel niet anders. Zo beschikken de servomotoren over de nieuwste encodertechnologie. Die hebben een resolutie van 26 bit, wat betekent dat er per omwenteling liefst 67 miljoen pulsen uitgestuurd worden. Dat leidt tot een nauwkeurige feedback over de positie en een zeer nauwgezette controle over de motor. De herhaalnauwkeurigheid bedraagt 0,02 mm. Het is bij onze cobot ook niet nodig om batterijen te gebruiken om de absolute positie te kunnen onthouden, zelfs bij langdurige spanningsvallen. Tot slot is de cobot robuust uitgerust om in de industriële omgeving zijn mannetje te staan. Er is ook een versie voor de voedselnijverheid met foodgrade smering.’
Nieuwe ontwikkelingen bij de 6-assige robots
Mitsubishi heeft, om tegemoet te komen aan de vragen uit de markt voor groter lasten met snelle en nauwkeurige positionering, zijn gamma van 4-assige en 6-assige robots, momenteel beschikbaar tot een last van 3 kg tot 20 kg, intussen verder uitgebreid met een 35 kg, 50 kg en 70 kg type in een 6-assige uitvoering. Beschikbaar met een bereik van 2050 mm, snelheid tot 13 m/s en repeteernauwkeurigheid van +/- 0,07 mm, dit in een IP40 of IP67 uitvoering, vormt dit een bijkomende uitbreiding in het robotprogramma van Mitsubishi.
Tevens is ook intussen de RV-8CRL 6-assige robot gelanceerd, een prijsgunstigere oplossing met een bereik van 931 mm voor belasting tot 8kg, snelheid tot 10,5 m/s en repeteernauwkeurigheid van +/- 0,02 mm, dit in een IP65 uitvoering.
Verhuis naar site in Ghislenghien
Esco verlaat de gebouwen in Diegem en betrekt vanaf eind 2020 een nieuwe site in Ghislenghien. U vindt het bedrijf voortaan in de Rue des Foudriers 14 te 7822 Ath (Ghislenghien).
www.esco.be
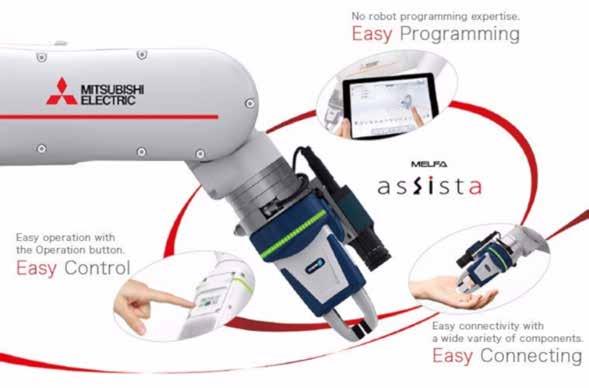
Door het aangaan van partnerships met grijperen visionfabrikanten verloopt de implementatie een stuk makkelijker.

Exclusief dealer RADICON BENZLERS® reduktoren Dealer DAVID BROWN® reduktoren
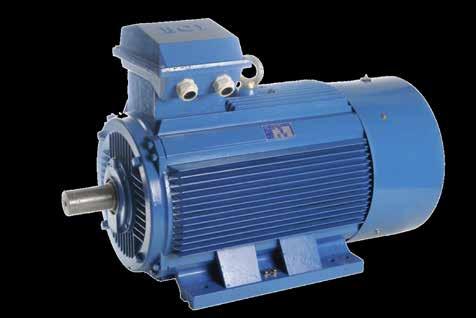
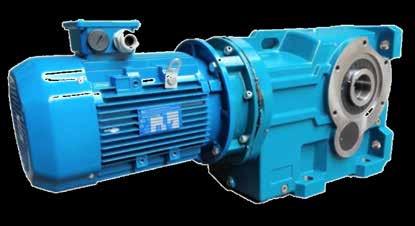
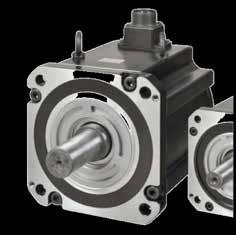

þ Alle motoren - reduktoren - ven�latoren þ OMRON® Servomotoren - Drives þ OMRON® Frequen�esturingen þ Alle herstellingen þ Speciale wijzigingen in eigen werkplaats þ Grote voorraad, snelle service þ Motoranalyse - uitlijnen - uitbalanceren
Gentstraat 187 B-8770 INGELMUNSTER www.bci.be Tel: +32 (0) 51 30 49 73 +32 (0) 51 30 98 63 info@bci.be
NIEUWE DATA VOOR INE XL EN MACHINEERING
Team Industrialfairs verandert de timing van INE XL (Indumation Network Event) en van MACHINEERING in functie van betere marktomstandigheden en meer vertrouwen door bezoekers en exposanten na een periode van verstrengde maatregelen wegens het coronavirus. De eventorganisator heeft iedereen gemeld dat INE XL 2021 zal plaatsvinden op 27 mei 2021 (Kortrijk Xpo) en MACHINEERING van 8 tot 10 september 2021 (Brussels Expo).
Beide events worden hybride: de ‘on-site’ beurzen worden aangevuld met een interactief online platform. Op die manier kan tijdens deze events iedereen opnieuw veilig, gezellig en efficiënt ‘live’ netwerken, aldus de organisatoren. Ze hopen dat tegen die tijd het coronavirus meer onder controle is.
Zoals eerder reeds bekend werd, is er in 2021 ook geen editie van INDUMATION.BE. De organisatoren Industrialfairs, InduMotion vzw en Agoria hebben beslist om INDUMATION.BE, de grootste industriebeurs in ons land, meteen uit te stellen naar februari 2022.
www.industrialfairs.com
Zo snel. Zo compact. Zo goed. AMCAP
tot wel 50%
ruimtebesparing met AMCAP
Het automatische AMCAP hoge capaciteits palletiseersysteem palletiseert de meest uiteenlopende producten uit de voedingsindustrie en retailsector met de hoogste capaciteit per pallet. Zo verzorgt het systeem de optimale opbouw van de pallets voor de betreffende fi lialen. AMCAP vraagt niet alleen 50% minder ruimte dan vergelijkbare systemen, het laat zich ook perfect in bestaande ruimtes integreren. Dat betekent voor u: maximale ruimtebenutting bij de hoogste productiviteit en daarmee grote voordelen ten opzichte van uw concurrenten.
www.dematic.com
Power the Future of Commere
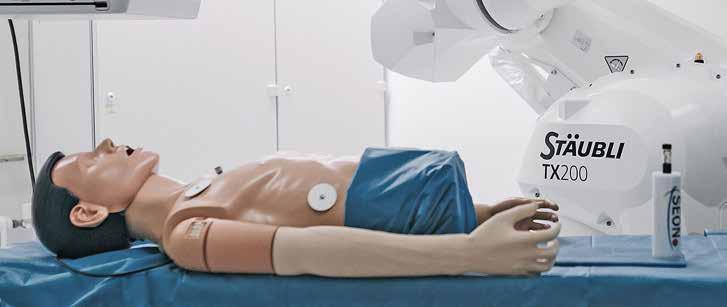
De TX200 robot kan via de magneetkop de actieve partikels veel beter op de kankertumor richten. Het resultaat is een efficiëntere behandeling.
ROBOT LOOPT VOOROP IN STRIJD TEGEN KANKER
De inzet van robots voor de behandeling van patiënten is niet evident. De zeer hoge eisen rond veiligheid, hygiëne en nauwkeurigheid maken de medische sector tot één van de meest veeleisende applicaties voor robots. Toch slaagde Stäubli er in om een revolutionaire behandeling van kanker te verfijnen met een TX200 robot. De gevolgen voor patiënten zijn enorm.
Robots zijn voor alle duidelijkheid niet nieuw in de medische sector, maar veelal blijft hun inbreng beperkt tot het automatiseren van labotaken of het veilig produceren van geneesmiddelen in de grote productiebedrijven. In de ziekenhuizen en operatiekwartieren zijn ze nog eerder een zeldzaamheid. Enkel voor sommige zeer gespecialiseerde chirurgische ingrepen wordt weleens gebruik gemaakt van robotica, maar stilaan richt de sector zich ook op andere medische toepassingen. De behandeling van kanker is daar een voorbeeld van.
Wie ooit geconfronteerd werd met deze ziekte, weet welke impact ze kan hebben op de patiënt en zijn omgeving. Om tumoren aan te pakken zijn er meestal 2 hoofdopties: ze operatief verwijderen of via een chemobehandeling weg proberen te werken. Bij die laatste methode zijn de problemen bekend: het is heel moeilijk om gericht de kankertumoren aan te pakken, ook gezonde cellen over het volledige lichaam worden getroffen. De patiënt krijgt daardoor vaak te maken met erge bijwerkingen van de hoge doses chemo.
SEON onderzoeksproject
Onderzoekscentra en ziekenhuizen zijn al langer bezig met de zoektocht naar een gerichte behandeling die enkel de tumoren aanpakt en de gezonde cellen met rust laat. Eén van die veebelovende onderzoeken is het SEON project van het universitaire ziekenhuis van Erlangen. Vorsers ontwikkelden magnetische nanodeeltjes uit ijzeroxide die de actieve stoffen transporteren. Door deze via een magnetische kop te bewegen richting de vaste tumoren (metastasen) kan een meer effectieve, snellere en minder pijnlijke behandeling gerealiseerd worden. Deze methode werd Magnetic Drug Targeting gedoopt. In een eerste fase werd de magnetische kop door de behandelaar manueel naar de juiste posities gebracht en over de tumoren bewogen. Al snel bleek deze methode tegen limieten te botsen. Onderzoeker Christoph Alexiou licht toe: ‘Op zich werkte de methode wel goed, maar er zijn grenzen aan de menselijke motoriek. Het spreekt voor zich dat een zesassige robot deze taak beter kan vervullen, want hij kan probleemloos het complete magnetische veld behappen en vanuit alle mogelijke hoeken de probleemzones benaderen.’
Positionering via terugkoppeling MRI
‘Belangrijk in onze benadering is het gedrag van de magnetische partikels. We kunnen via de MRI technologie (magnetic resonance imaging) achterhalen wat de impact was van de behandeling, want de ijzeroxide deeltjes veroorzaken een verschil in het terugkerend signaal. Zo kunnen we achterhalen hoeveel partikels de tumor bereikten en hoe effectief dat gebeurde. Door die informatie te koppelen aan de robotcontroller openen zich ongekende mogelijkheden. De robot is via de terugkoppeling voortdurend op de hoogte van de exacte locatie en omvang van de tumor. Zo kunnen we het robotpad zeer nauwkeurig berekenen en de magnetische kop op de robot nog veel beter richten op de tumor. De nanopartikels zullen zo via de kortst mogelijke weg hun doel bereiken. Het lichaam van de patiënt wordt stukken minder belast en de behandeling wordt draaglijker. Bovendien is ook de foutenlast een pak minder.’
TX200 van Stäubli
De robotkeuze viel op de TX200 van Stäubli, die ook bestaat in een cleanroomuitvoering klasse 5 voor medische toepassingen. De herhaalnauwkeurigheid van de robot bedraagt 0,06 mm en de reach 2194 mm, wat voor deze toepassing meer dan voldoende is. Omdat er in deze applicatie geen sprake kan zijn van een hekwerk rond de robot, werden verder de nodige maatregelen getroffen om de veiligheid van de patiënt te waarborgen. Ook het gebouw zelf onderging de nodige aanpassingen om de toegenomen belasting van 2 ton te kunnen dragen.

De verbeterde servogestuurde doseerfunctie van Yamaha met de RCX340-controller.
EFFICIËNTERE PRODUCTIE DOOR SNELLE PRECISIEDOSERING
Het gebruik van robots bij het doseren van coatings kan de productiviteit aanzienlijk verbeteren, vooral wanneer de servo- en doseerbesturing zijn gekoppeld om een optimale snelheid en een gelijkmatige coatingdikte te garanderen.
Producenten over de hele wereld schakelen almaar meer over op hogesnelheidsautomatisering om de huidige productiviteitsuitdagingen het hoofd te kunnen bieden. Het wordt echter almaar moeilijker om het rendement met behoud van kwaliteit te verhogen door middel van de conventionele automatisering.
Het verhogen van de snelheid van een proces zoals doseren kan de nauwkeurigheid en herhaalbaarheid in het gedrang brengen en de meest complexe aanpassingen vereisen om de gewenste kwaliteit aan het einde van de productielijn te bereiken. Normaal gesproken is slechts een klein aantal gekwalificeerde en ervaren technici in staat om dergelijke processen op te zetten en te begeleiden, wat soms de introductie van nieuwe producten vertraagt en leidt tot de stilstand van productielijnen.
Een hoge productiviteit combineren met precsiedosering
De ervaring van Yamaha Robotics met klanten in uiteenlopende sectoren als de auto-industrie, de elektronica en de medische sector is een garantie voor succes. Voegkit aanbrengen op de rand van gegoten metalen of kunststofonderdelen, zoals afdekkingen en te monteren behuizingen, wordt vaak uitgevoerd met conventionele aandrijvingen om de lineaire beweging en het afdichtingsproces te coördineren.
Om een ononderbroken voeglijn af te zetten, moet het bewegingscontrolesysteem precies een vooraf bepaald traject volgen langs de rechte randen en in de hoeken. In het algemeen moet in de hoeken de snelheid worden verlaagd, zodat de lijn op die plek voldoende nauwkeurig is. Omgekeerd verdient het de voorkeur om de snelheid van de verplaatsing langs rechte randen te verhogen om zo de totale procestijd te verkorten.
Om ervoor te zorgen dat er op elke locatie een constant volume aan voegkit wordt afgezet, moet het doseermechanisme zodanig worden ingesteld dat de stroom aan voegkit in de hoeken - waar de snelheid laag is - wordt verminderd en weer wordt verhoogd bij een snellere beweging. Deze regeling is moeilijk uit te voeren en bedrijven zijn vaak afhankelijk van een klein aantal medewerkers met de nodige knowhow.
Bij een slechte instelling kunnen defecten optreden, zoals een te groot volume aan voegkit in de hoeken, waardoor uiteindelijk meer onderdelen worden afgekeurd aan het einde van de productielijn. Als alternatief kan de keuze voor een langzame, constante aandrijving en doseersnelheid de procesbesturing vereenvoudigen, maar met een langere cyclustijd en een lagere totale efficiëntie.
In het algemeen is het doel van de producenten om een hoge kwaliteit te combineren met een hoge snelheid zonder dat er gespecialiseerde vaardigheden nodig zijn. Dit vereist een oplossing die in staat is om de doseersnelheid van de afdichtingen automatisch aan te passen aan de variaties in de bewegingssnelheid, zodat het gewenste volume van het product wordt aangebracht op de maximaal mogelijke snelheid voor elke positie.
Automatisering en robotisering
Meerdere industrietakken maken tegenwoordig gebruik van robotisering om hun productiviteit te verbeteren en
flexibiliteit te verkrijgen om zo in te spelen op de toekomst. Yamaha Robotics heeft ook gewerkt aan het gebruiksgemak van de RCX-serie robotbesturingen en hun grafische programmeertools om gebruikers te helpen ten volle te profiteren van deze technologie.
De RCX340-controller van Yamaha heeft verbeterde bewegingsmogelijkheden en vereenvoudigt de configuratie van het robotsysteem. In het bijzonder kan de doseerfunctie worden aangesloten op de servobesturing, waardoor de RCX340 de doseersnelheid kan regelen als functie van de snelheid om een hoge nauwkeurigheid, hoge snelheid en gelijkmatige coatingdikte te garanderen. Deze ‘servogestuurde dosering’ (foto 1) is toegepast op SCARA en op de cartesiaanse robots van Yamaha.
Bovendien maakt deze controller het mogelijk om meerdere robots tegelijkertijd eenvoudig aan te sturen en is hij compatibel met een uitgebreide instructieset, inclusief speciale vision-instructies die het programmeren vereenvoudigen en de opstarttijd van de apparatuur tot een minimum beperken. De programmeeromgeving RCX STUDIO 2020 bevat debuggingfuncties die veel taken bundelen en functies die de invoer en instellingen van programma’s versnellen.
Tot slot maakt het gebruik van communicatie-interfaces die vaak worden toegepast in de industriële automatisering een eenvoudige integratie in de bestaande omgeving van een fabriek mogelijk. Naast de RS-232C- en Ethernet-poorten accepteert de RCX340 gemeenschappelijke veldbussystemen: CC-Link, EtherNet/IP™, DeviceNet™, PROFIBUS, PROFINET en EtherCAT. Aansluitingen op algemene servoversterkers of externe vision-systemen zijn ook eenvoudig te maken en vereenvoudigen de introductie van robottechnologie in bestaande productieprocessen.
Snelle dosering in de praktijk
Onlangs heeft Yamaha Robotics een klant uit de automobielsector geholpen om de precisie van vloeibare voegkit op aluminium gietstukken te versnellen met behulp van de RCX340-regelaar en Yamaha-robots. Deze fabrikant slaagde er niet in om zijn efficiëntie te verhogen door de aandrijfsnelheid van zijn bestaande doseerautomaat te verhogen. Door simpelweg de snelheid te verhogen, raakte de controle van de dosering van de voegkit in de war, met als gevolg de vorming van grote vloeistofhoeveelheden daar waar de aandrijfsnelheid trager was. Het bedrijf was daarom gedwongen om de apparatuur met een constante snelheid te laten werken, wat de cyclustijd verlengde.
De projectverantwoordelijke, die op zoek was naar een snellere en eenvoudige oplossing die kon worden geïmplementeerd zonder een beroep te moeten doen op bekwame technici, wendde zich tot Yamaha om te zien of hun robottechnologie een praktische oplossing kon bieden. Na een demonstratie van Yamaha’s servogestuurde dosering, installeerde hij snel een pilootsysteem in zijn fabriek om de mogelijkheden ervan te onderzoeken.
“Naast de verhoging van de productiesnelheid toonden onze analyses aan dat de kwaliteit van de coating ook perfect was”, merkt hij op. ‘’We vroegen Yamaha ook te kijken naar het doseringsproces dat we eerder zelf hadden opgezet vanuit onze eigen ervaring. Hun deskundigheid stelde ons in staat om zeer snel de beste instellingen te berekenen, wat resulteerde in een drastische vermindering van de werklast van onze ingenieurs.”
Na het bereiken van de gewenste snelheid en een stabiele kwaliteit voerde het projectteam eindcontroles uit en introduceerde dit proces op de productielijn. Toen deze taak eenmaal voltooid was, begon het team meteen de mogelijkheden te onderzoeken om Yamaha-robots te gebruiken om andere processen binnen de fabriek te verbeteren.
Besluit
Fabrikanten in de automobielsector en andere industrietakken moeten hun automatisering versterken om de productiviteit te verhogen door de cyclustijden te verkorten, met behoud van de kwaliteit. (Foto 2)
Robots kunnen op dit probleem een antwoord bieden door te worden verbonden met de nieuwste motion control-technieken en praktische tools om te helpen bij het programmeren en configureren. Gebruiksgemak is essentieel om gebruikers te helpen snel nieuwe processen in hun industriële omgeving in te voeren.
www.yamaha-motor-im.eu

Autoproducenten moeten een evenwicht zien te vinden tussen duurzame productiviteit en uitstekende kwaliteit.