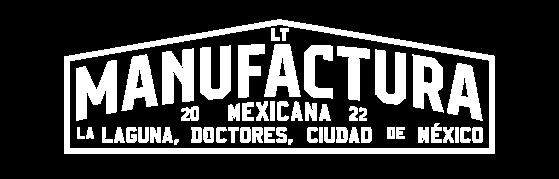
Portfolio 2024

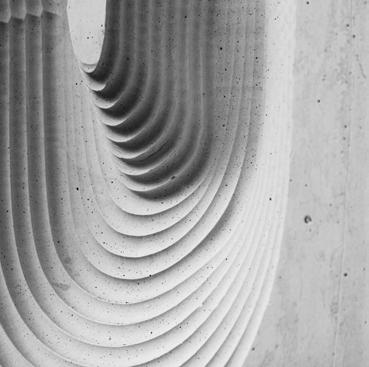
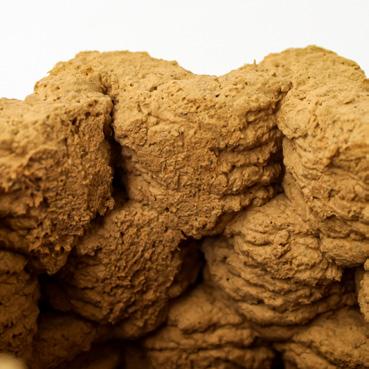
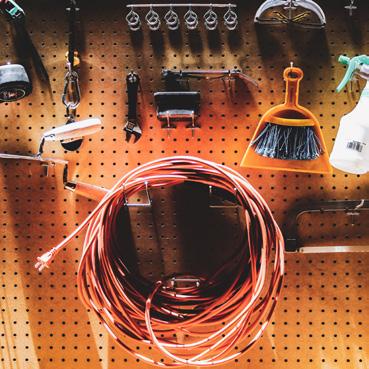
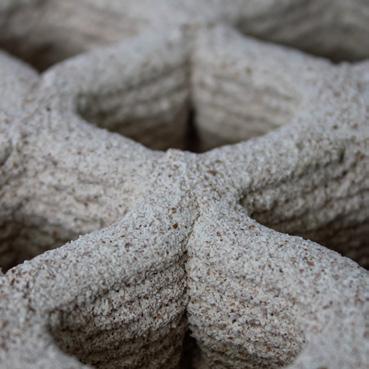
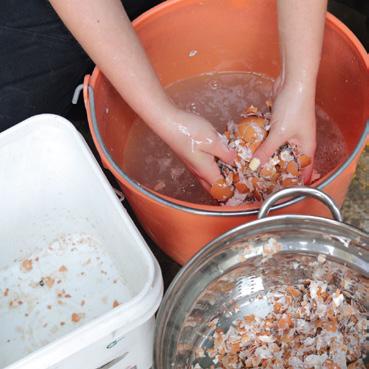

We are a multidisciplinary research and production factory that studies and questions manufacturing through innovation from tradition, providing new alternatives to fulfill a sustainable built future.
Mexico City, Mexico.
Year: 2022
Location:
Material: 3D Printing PLA
This project is a research and artistic endeavor that employs 3D printing and photogrammetry scanning techniques to meticulously replicate the geometric characteristics of natural objects, specifically stones collected from various environmental contexts. These replicated forms are subsequently integrated into a singular piece or column, aligning precisely with the original geometry.
This innovative approach allows for the creation of a comprehensive documentation, preserving and presenting vestiges of these natural objects, which have been faithfully reproduced across diverse scales and textures, thanks to the integration of cutting-edge technology.
INÉDITO Design Week Mexico + Zona MACO 2023
Year: 2022 - 2023
Authors: Dinorah Martinez Schulte and Edurne Morales.
Team: Santiago Rangel, Aleida Rahel Merkel , Natalia Juan
Location: CDMX, Mexico.
Material: Recycled Eggshell
Collaboration: Monsterrat Ayala (Material Research)
The Eggshell Project / Un Proyecto de Huevo, is a research project that seeks to take advantage of and transform our waste to turn it into a buildable material and open up a new possibility to create our living in an environmentally responsible way. In this project we create a bioceramic made from eggshell and combine it with sustainable aggregates, resulting in a new materiality, which seeks to reduce food waste and generate new opportunities.We decided to reevaluate the potentials of ceramics, keeping the connection between materiality and nature, extensive access to raw materials, geometrical freedom and strength. But reducing some of the harmful traits by using a locally sourced largely found lightweight waste product: egg, together with bio-binders that allow the mix to solidify without the need of firing.
Our process is based on 3D printing with a KUKA KR-150 robotic arm, an extruder and additive fabrication process, which allows us to shape our blocks with different geometries and project them into different architectural applications. allows efficient use of material (less waste), geometrical freedom, precision and repeatability, project them into different architectural applications.
In this research we have made two applications: A wall (Eggshell Bricks, presented in the INÉDITO collection by Design Week Mexico 2022) made of a total of 105 different blocks that are assembled based on their geometry, and a column (Eggshell Column, presented in
the DISEÑO EMERGENTE collection by ZONA MACO 2023) made of 26 pieces that embrace each other and create stability through their shape. Each brick is made in a 100% sustainable and circular way since the raw material was obtained through the collection and donation of waste from more than 2 months of production from various restaurants in Mexico City such as Rosetta, Rosetta Panadería, LARDO and Rancho Rio Blanco.
Technology allows us to innovate in the current markets in terms of construction, which economically and culturally has a great weight in society because it opens up new possibilities for construction and materiality in our habitat, generating a circular system from where it is obtained to its use, by giving a new life to our waste.
This project was achieved thanks to the mixture of computational design and the opportunities offered by digital manufacturing, technology and materials innovation to transform our waste and raise awareness, questioning our manufacturing methods and creating centuries of circular life, generating new sources of employment since you recycle it, sanitize it, until its manufacturing with robotic 3D printing and its placement on site; having to look for new talents to produce this material and product in series and opening up new opportunities in the construction of future architectural spaces, creating a new dialogue between machines and humans.
The development of manufacturing strategies based on the material behavior allows an integration early logics of manufacture in the design process and an exploration of new structural typologies.
MEXTROPOLI 2022
Year: 2022
Authors: Dinorah Martinez Schulte and Edurne Morales.
Location: CDMX, Mexico.
Material: Local Clay (Oaxaca + Zacatecas)
Collaboration: MIT Architecture, MIT Digital Structures, ECHALE, NEW STORY, ANFORA Studio.
A participatory, architectural installation featured in the Mextrópoli Architecture and City Festival (September 21-25, 2022), Sueños con Earth/Concrete unfolds stories about Mexico City through four materials, their provenance, and their promise for the future. Through its critical adaptation of traditional papercraft, creative reuse of recycled wood, and innovative use of earth and concrete, this site-responsive installation invites us to recognize the palimpsest of Mexico City’s histories and imagine new possibilities.
Sueños con Earth/Concrete explores the future of affordable housing in Mexico by minimizing the material impact of existing construction methods.
This pavilion has been developed in partnership with New Story, an international non-profit organization that pioneers solutions to end global homelessness, and Échale, a social enterprise based in Mexico that offers housing solutions through the integral development of communities.
The horizontal roof structure takes the existing vigueta y bovedilla system as a starting point, optimizing the shape of the precast reinforced concrete beams to minimize the use of material and its associated environmental impact by 50% compared to conventional systems. This elegant geometry, sculpted by varying width and depth along the beam’s span, is enabled by recent computational design methods developed in MIT research.
3D-printed clay blocks vault between beams as lost formwork that enables the casting of a topping slab manufactured by MANUFACTURA and ANFORA Studio.The use of tepetate, a local soil with high contents of clay, allows for fabricating compressed, sun-dried blocks that constitute the pavilion walls.
This affordable, low-carbon solution, which has been successfully applied in the construction of housing communities around Mexico for more than 30 years, is reinterpreted here with a posttensioning system that allows for assembly and disassembly. Sueños con Earth/Concrete lies at the intersection of local construction techniques and new digital fabrication technologies, resulting in a collaboration between industry, social enterprise, and academia as a model toward a more sustainable built environment.
Sueños con Earth/Concrete lies at the intersection of local construction techniques and new digital fabrication technologies, resulting in a collaboration between industry, social enterprise, and academia as a model toward a more sustainable built environment.
Mexico City, Mexico.
Year: 2023
Authors: Dinorah Schulte Rodrigo Escobedo, Edurne Morales, Fabricio Vazquez and Brando Marín
Team: Santiago Rangel, Jared Zarate
Location: CDMX, Mexico.
Material: Recycled Sawdust
Collaboration: La Metropolitana + Montserrat Ayala
In Mexico, approximately 102,895 tons of trash are generated daily, from which 83.93% get recollected, 83.93% are taken to final disposal sites, and only 9.63% gets recycled, according to Mexico’s Environment and Natural Resources Department.
Annually the volume of timber production in Mexico reaches approximately 9 million cubic metres. From which 70% gets destined to the sawmill industry, and 45 to 65% of this volume becomes sawdust, shavings and bark, becoming waste elements of little or no economic value. (Fragoso-Madueno 2)
Currently the main ways to handle this waste are based on: generating new woodbased materials such as composites and conglomerates, nevertheless due to sourcing difficulties not all wood gets recycled in this way; the second main type is based on demolition, combustion and landfilling, practices which generate methane, carbon monoxide, nitrogen oxide and a toxic smoke atmosphere, all of which in sufficiently high concentrations present a hazard to exposed animals, humans and in general to the environment. (Lin)
These effects make it necessary to look for alternatives for the utilisation of these waste products. This text proposes a way of extracting and reutilizing the waste products, with the idea of reducing the impacts previously mentioned.
The Wood Project / Un Proyecto de Madera, is a research initiative in collaboration with La Metropolitana, a conscious furniture manufacturing and design workshop with more than 15 years of experience in the search for the link between nature and human beings through creativity and design. The workshop combines traditional woodworking techniques with cutting-edge technology in its furniture manufacturing processes, managing to increase efficiency and offer high-quality and competitive proposals.
The project focuses on using the wood and the development of multiple transformation techniques based on the natural processes of the material. Responding to the current problem faced by the workshop, the daily production of up to 5-6 bags of sawdust of different species, equivalent to approximately 40 kg per bag per day.
The overarching goal is the meticulous construction of 3D printed structures, seamlessly manufactured through the precision of a robotic arm, starting a process of circular economy and decarbonization.
During this development a bio-composite has been generated mainly conformed by sawdust. The selected tree species is the Tzalam tree (Lysiloma latisiliquum), native to the southeast of Mexico and highly prized in the Mayan region due to its appearance and high hardness. The wood itself is distinguished by its sober presence, pronounced grains and an attractive reddish colour that adapts to various design styles. The matrix of the composite is based on organic binders and lime to avoid humidity and fungal development.
Several mixing experiments informed of the changes in physical state and binding behaviour during drying, which depended in great measure on the machine used to generate the sawdust, as it modifies the sizing of the particles. After a prototyping process, it was determined that the sawdust coming from the calibrating machines and the CNC router presented the most optimal physical conditions to allow the 3D printing process.
Our setup is based on an extruder for semiliquid materials mounted on a KUKA KR-150 industrial robotic arm. The 3D printing process is based on following a trajectory that allows specific laying of the material coming from the extruder. This process allows the generation of diverse, precise, and intricate geometries based on digitally adjusted parameters, providing an efficient use of material, waste reduction, geometrical freedom, precision and repeatability, opening new possibilities for the design and architecture fields.
The demonstrator for the material developed was based on 3 partition walls of architectonic scale composed of 72 pieces of 20 x 20 cm fabricated during a lapse of 3 weeks between printing and drying. The pieces are easily replicable and assemblable among them, allowing to increase the scale of the elements easily. These bricks are produced sustainably and in a circular manner, utilising raw materials sourced from waste at La Metropolitana and processed to attain their finest sizing.
Most of the sawdust is rich in cellulose, hemicellulose, lignine and other substances of low molecular weight, characteristics usually wanted in the industrial applications. Additionally, the resulting components exhibit
remarkable lightness, with each brick weighing an average of 207 grams, leading to a total weight of 15 kg for the entire structure.
The material analysis is an ongoing collaboration with the Laboratory of Materials and Structural Systems (LMSE) at Mexico’s Autonomous National University (UNAM). Microscopic inspections and compressive tests have been conducted on the material.
Under compression, the material showed limited flexibility, leading to its failure before reaching the fracture point due to defragmentation. However, it still demonstrated an average resistance of 836.5 kg and a maximum average resistance of 20.15 kgf/cm2. These values are comparable to fired clay bricks, which typically exhibit resistances ranging from 13.34 to 39.50 kgf/cm2 (Piscal Arévalo et al. 15). Further exploration and refinement are needed to fully understand the material’s properties and possibilities for practical use.
The use of these materials and processes opens new possibilities for our current sustainability, culture and economies. The project proposes an innovative focus for the production through circular systems. This strategy covers various stages starting from the extraction of raw materials of recycled origin coming from collaborations with multiple industries, followed by the generation of new materials based on natural additives with biodegradability potential, and the subsequent utilisation of a method based on contemporary technology that optimises the quantity of material and precision granting a new life to the residues and establishing a new circular durability that transcends generations.
Moreover, the versatility of this method extends to the construction industry, offering new prospects for thermic isolation, semistructural elements, furniture, and other architectonic systems. Throughout the process, the integration of diverse talents and abilities has proven essential, spanning from recycling and cleaning to robotic fabrication and element installation, creating new training and job opportunities. The innovative potential of this system opens doors to a new construction of architectonic spaces, arising a new dialogue between humans and machines.
by
“The inverse relation between quantity and quality expressed itself through waste.” - Richard Sennett
Year: 2023 - 2024
Authors: Dinorah Schulte and Edurne Morales
Team: Jared Zarate, Erick Marín
Location: Puebla, Mexico
Material: Talavera Mexican Pottery
Collaboration: Uriarte Talavera
Redesigning the way of making between tradition with innovation, through humanizing automation and robotics fostering economic equity.
In Mexico, artisans occupy population is 12.6M. Their working conditions are limited: having an average salary of 6.09k per month, where 30.1% are women and 69% are men. They are disappearing due to multiple causes: globalization, mass production, climate change, demanding learning, lack of economic support and not transferring innovation. s (Trabajadores Artesanales: Salarios, Diversidad, Industrias E Informalidad Laboral | Data México, n. d.).
Digital fabrication combines the customization of craftsmanship with the cost efficiency of mechanical production, thanks to modern digital technologies. This makes it possible to mass-produce products without additional costs, enriching tradition that not only preserves our cultural identity, fostering new opportunities in the conscious preservation and sustainabilty. The fundamental purpose is to make visible the synergy between tradition and innovation, to create a new sustainable way of making. They have the same technological impact and are not replaced, rather, they dialogue with each other to allow more sustainable manufacturing, where heritage and customs shouldn’t be erased by machines.
The Talavera Project / Un Proyecto de Talavera, is a research initiative executed by MANUFACTURA in collaboration with Uriarte Talavera, a workshop established in 1824 and recognized as the first producer of talavera in Mexico and to obtain certification under the Mexican Official Standard, which grants it the Denomination of Origin (DO4-1). Located in a historic mansion in the heart of the historic centre of the city of Puebla, this workshop fully preserves the process of making tinware, introduced in the sixteenth century in New Spain. As of 2019, this process is part of the Intangible Cultural Heritage of Humanity (Uriarte Talavera, n.d.). The Uriarte artisans, shares with us two major problems they suffer today: the lack of innovation and the high level of waste they have in their production, being a material and process of denomination of origin and protected by law.
The fundamental purpose is to make visible the synergy between tradition and innovation, to create a new sustainable way of making. They have the same technological impact and are not replaced, rather, they dialogue with each other to allow more sustainable manufacturing, where heritage and customs shouldn’t be erased by machines.
Our design solution works by challenging the conventional linear production model, instead of a one-way manufacturing process, we embrace a closed-loop system that incorporates automation.
This shift benefits all participants involved, especially our target beneficiaries, the artisans. The importance lies in fostering sustainability, both environmentally and socially. By preserving traditional craftsmanship, promoting social justice for artisans, and incorporating automation, we not only prevent their disappearance but also contribute to the preservation of our cultural heritage.
The circular model ensures that all contributors in the process derive advantages, making it a more inclusive and sustainable approach for the long term.
“Technology should not replace human contact; there can be no community without physical proximity.”
- Mario Carpo
This intervention comprises two elements addressing the mentioned issues: an 80-piece column replicated from a mold created through Robotic 3D printing and the second element is a carpet made from the production waste, prompting a reconsideration of recycling strategies to transform it into a higher-quality, ecologically valuable product.
Mexico’s greatest wealth lies in its cultural heritage. We envision echoing this initiative with all indigenous, protected materials and vulnerable artisans societies, reshaping production lines for efficiency, thwarting extinction, fostering employment, and revitalizing the economy for Mexican artisans. Our ambition is to forge a novel economic paradigm, seamlessly blending 3D printing technology and innovation with the artistry of hands, elevating production efficiency, understanding their processes while safeguarding age-old skills. Together, we forge a path toward a vibrant and sustainable tomorrow.
01
Printing process with local clay.
3D Printign process with a KUKA KR-150 robotic arm in a time of 10:00 min.
Stage 05
First oven: Jahuete or sancocho
Firing at low temperature (850ºc). Both words are used to denote that the piece is cooked, biscuit or partially cooked.
The process of making smooth finish handmade ceramics by hand.
Stage 06
Handmade modelling by a certificate and local craftsman from a 3D Printed piece.
Stage 07
The piece is moulded by hand with clay from the region of Amozoc and white clay from Valsequillo.
Stage 08
Second kiln session and final finish Enamelling and glazing
The entire surface of the piece is raised by immersion to apply the paint. The enamel gives the traditional shine and colour of the authentic Puebla Talavera.
blue paint
The paint is obtained from natural minerals, handmade with mule hair brushes.
The pieces are introduced to a burner (1050ºc) so that the enamels and paints react together and we obtain the piece with its final finish.
With this ongoing research we seek to promote environmental awareness, job generation and efficient use of resources, contributing to a more sustainable and conscious future.
Year: 2024
Author: Dinorah Schulte
Team: Jared Zarate, Erick Marín and Jorge Orduña
Location: CDMX, Mexico
Material: Bee Wax
Collaboration: GENSLER Mexico
“Type-form evolution occurs when a new material condition suggest the new use of a new tool.”
- Richard Sennett.
Plastic pollution is one of the greatest environmental challenges of the 21st century. Since 1950, 9.2 billion tons of plastic have been produced, of which approximately 7 billion tons have become waste that ends up in landfills or in the natural environment, affecting ecosystems and limiting their capacity to adapt to climate change, harming millions of people in their food production and social well-being. In addition, 8 million tons of plastic are dumped into the oceans every year, and it is estimated that by 2050 there will be more plastic than fish in the sea (Contaminación Por Plásticos, n.d.). Mexico is among the largest producers of polyethylene terephthalate (PET) due to the high consumption of soft drinks and bottled water, generating around 200 PET bottles per person per year (Con-Su-Mismo Plástico Comisión Nacional De ÁReas Naturales Protegidas | Gobierno | Gob.mx, n.d.).
by
Faced with this alarming situation, the search for sustainable alternatives is becoming imperative. Natural waxes, obtained from the processing of vegetable or animal oils, are gaining ground in the coatings industry, particularly in the wood coatings market (Wax Market Size and Share Analysis - Industry Research Report - Growth Trends, n.d.). Beeswax, a biomaterial secreted by honeybees, is notable for its moisturizing, emollient and softening properties. Its complex chemical structure, composed of esters and fatty acids, makes it an exciting alternative to replace plastic and acrylic materials in construction and other applications.
The Wax Project / Un proyecto de Cera, is a research and fabrication project, where we have explored the use of beeswax in architecture, developing a 13 x 13 cm lattice prototype made of cast beeswax from a prototype made with 3D printing and silicone molds to allow its mass production. These lattices have translucent properties, allowing the passage of light and, at the same time, have a rigid surface, which makes them suitable for use as construction elements. Unlike acrylics and plastics, beeswax allows for easy reuse, since in case of damage, a new panel can be produced in less than 30 minutes, significantly reducing the carbon footprint.
The manufacturing process of these lattices consists of several stages: the natural wax is ground, heated and stearic acid is added to improve its rigidity. The mixture is then poured into the silicone mold and left to cool for 40 minutes. The result is sustainable panels ready for indoor use.
This project was done in collaboration with GENSLER Mexico, where the value of their work comes from its positive impact on the human experience. They are a dynamic and collaborative design firm that unites creativity, research and innovation to solve complex problems for our clients. The panels were integrated into a prefabricated wooden structure made in collaboration with MATERIAM, complemented with LED lighting to highlight the lattice in the interior of their office located in Torre Chapultepec 1 in Mexico City.
A supplier of natural beeswax was obtained to be collected on site.
Wait half an hour to melt the wax with the stearic acid.
Once the wax is melted with the stearic acid, it is poured into the gaucho silicone mold made with 3D printing.
The beeswax is pulverized to obtain its smallest grain to facilitate 3D printing.
of the wax into the silicon
The temperature of the wax is used to empty the mold slowly until it reaches the top of the mold.
Heat the beeswax at a high temperature above 100 degrees Celsius to melt it.
Drying session
Allow the pieces to dry for 30-40 minutes until hardened
Once the wax is melted, 15 grams of stearic acid are added to improve its hardening.
Final beeswax panels
After drying at room temperature, the panels are ready for use.
This work not only demonstrates the feasibility of using wax in architecture, but also emphasizes environmental responsibility by substituting polluting materials such as acrylic, contributing to a more environmentally conscious and respectful design.
Using beeswax in architecture is not only a technical or functional solution, it is a declaration of principles. This material invites us to rethink the way we build and live, prioritizing harmony with the environment and respect for natural resources. Unlike acrylic, wax is not only sustainable, but it brings a handcrafted and warm dimension to the spaces it transforms. With wax, we create a future where beauty and environmental responsibility go hand in hand, showing that it is possible to design a world where innovation and nature are not in conflict, but in perfect harmony.
“The humanizing language bred in turn one of the great dualisms of modern material consciousness; the contrast between naturalness and artificiality.”
- Richard Sennett
Year: 2024
Professor: Dinorah Schulte
Team: Students from Universidad Iberoamericana, Mexico City.
Location: CDMX, México.
Material: Earth.
Collaboration: Taller de Fabricación Digital / Universidad Iberoamericana.
Parametric Adobes made with 3D printed molds. Final Project of the Digital Fabrication Workshop at the Universidad Iberoamericana, Mexico City.
Adobe, a word that comes from the Arabic al-tub, is an unfired brick, a building material made from a mass of mud (clay and sand), sometimes mixed with straw, molded into the shape of a brick and dried in the sun; they are used to build various types of construction elements, such as walls, walls and arches. Its history has been recorded from 11,000 - 7,000 years ago from the ancient Assyrians and Chaldeans, Persians, Egyptians, Eastern and American and Mesoamerican cultures.
In this research we explore a new way to manufacture and make earthen adobes, leaving the traditional mold that has dimensions of 20 x 40 x 10 cm approximately, entering a new form of manufacturing experimentation making the original geometry with a 3D printed mold in PLA and removing the negative with a silicone mold to later prepare the mixture of raw earth and natural fibers, to allow a circular economy cycle and to reuse these pieces as many times as necessary.
by
The work team was divided into 3 groups: the design group, where this team focused on developing the most optimal geometry with curvatures and slopes to get the most out of 3D printing, using computational design tools such as Rhinoceros and Grasshopper. The main geometry was based on the replication of 9 circles where they were interspersed to find the curvature formed at the junction of the circumferences to push the geometry to the limit with this materiality. The second team focused on the development of the material, where the students developed 5 different types of mixtures in order to test the potential of the soil with different aggregates and to see its limits by playing with their weights. The sites where the material was extracted were no more than 60 km from our university.
The mixture was composed of the following aggregates:
1. Pine sawdust from Zinacantepec, State of Mexico from Innova Forestal.
2. Soil from Calimaya, State of Mexico
3. Soil from Contadero, Cuajimalpa de Morelos
4. Gravel extracted from both soils by means of a 5x5 mm mesh.
Finally, the fabrication team explored different mold making strategies to allow the original geometry to be projected and to choose the most efficient and optimized process for its construction and mass production. They used a 3D print made from PLA with an ULTIMAKER printer and then cast the negative in silicone rubber to facilitate de-molding. The production time was based on 1 day of production of mixing and pouring the soil into the mold, then 3 days of drying and the piece was ready. A total of 20 pieces were produced in a production time of 4 weeks. The potential number of possible pieces to be created considering the useful life of the molds, was 270 partitions. Considering the reduced time and labor, the total number of parts created was 20. The total cost for the 20 parts corresponds to only 7.40% of the total use of the initial investment.
With this project we seek that students can create their own criteria on the use of technology and innovation in the face of different geometric, material and manufacturing challenges to materialize different projects, be aware of where the materials we use come from and what is their impact on the environment and thus, be applied on a larger scale in living spaces and architectural scale as walls, lattices, columns, among multiple combinations that allows its geometry to be replicated and assembled on site and generate new spatial experiences, out of the mold.
Color gradient with blue pigment
“Digital Fabrication might transform the political economy of everyday life.”
- Adam Greenfield
@manufacturamx www.manufacturamexica.com