
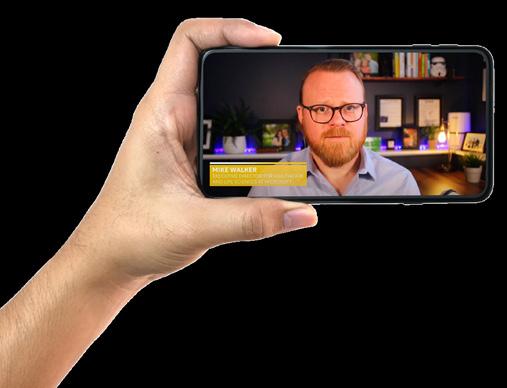


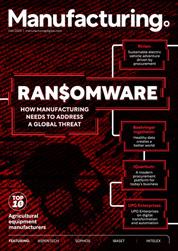
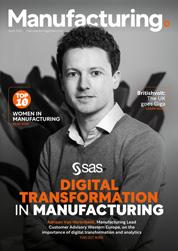

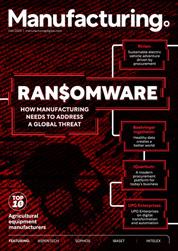
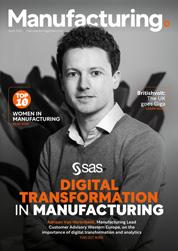
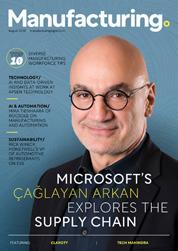
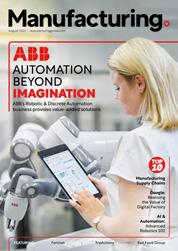
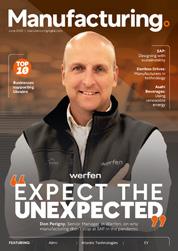
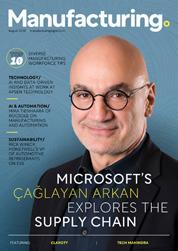
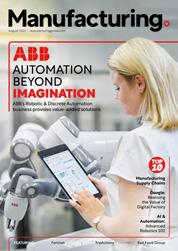
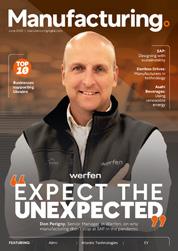

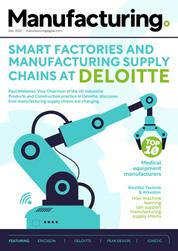

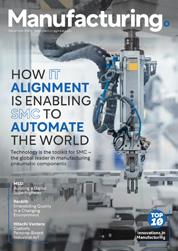
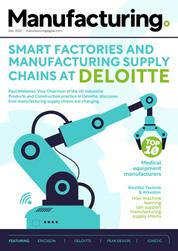


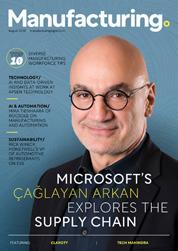
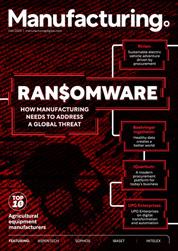
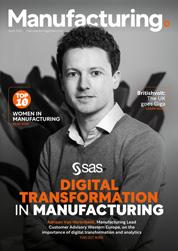
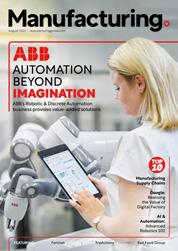
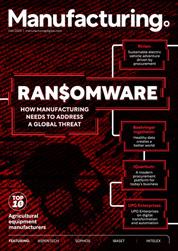
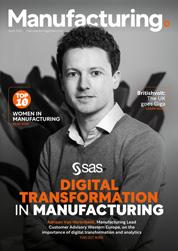
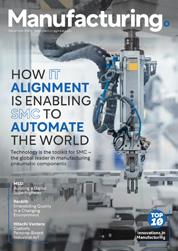
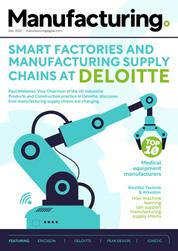
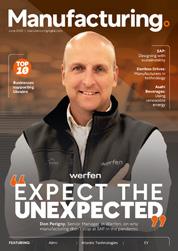


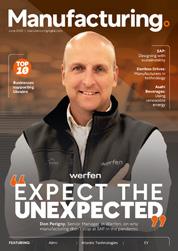


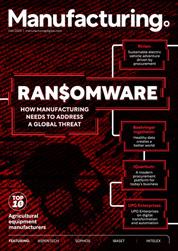

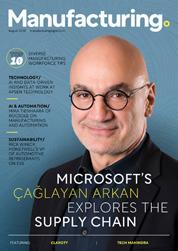

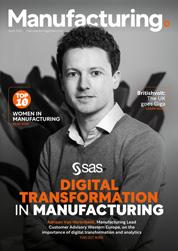
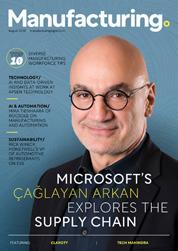
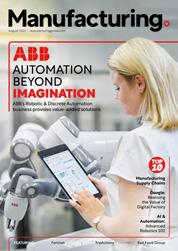
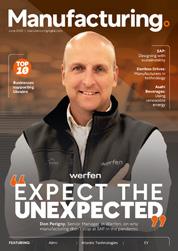
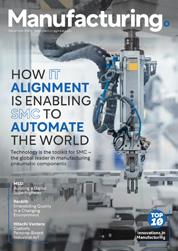
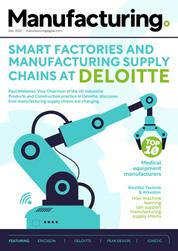

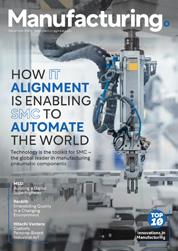
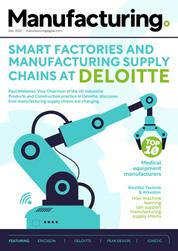


Manufacturing magazine is an established and trusted voice with an engaged and highly targeted audience of 2,000,000 global executives
Digital Magazine
Website Newsletters
Industry Data & Demand Generation
Webinars: Creation & Promotion
White Papers & Research Reports
Lists: Top 10s & Top 100s
Events: Virtual & In-Person
WORK WITH US
Welcome to October’s edition of Manufacturing Digital - read on for the latest from Schneider Electric, EOS, NVIDIA, Dexory and read our pick of the Top 10 manufacturing cities
In this issue of Manufacturing Digital, we hear from Oana Jinga, CCO of Dexory, on how she is leading women in technology with mentorship programmes, Ludwig von Reiche, Managing Director of NVIDIA’s German companies, about manufacturing businesses using the metaverse and transforming the 3D internet. Elsewhere, Senior Additive Minds Consultant at EOS Dave Krzeminski shares how EOS' commitment to sustainability through 3D Printing is building a greener future, while Andre Marino from Schneider Electric shares how IoT devices are impacting commercial real estate and helping buildings become more sustainable.
Shanghai, Mumbai, Beijing, Dubai, Johannesburg, São Paulo, Los Angeles, Seoul, Tokyo and Manchester are our top 10 manufacturing cities - read on to find out why. Do you work in one of these cities? Or have we missed yours off the list? Let us know on our LinkedIn @ManufacturingDigital or Twitter @ManufacturingDg
Keep looking up,
HELEN ADAMSHelen.Adams@bizclikmedia.com
“Shanghai, Mumbai, Beijing, Dubai, Johannesburg, São Paulo, Los Angeles, Seoul, Tokyo and Manchester are our top 10 manufacturing cities – read on to find out why”MANUFACTURING GLOBAL MAGAZINE IS PUBLISHED BY
14
16
22
3 0 TOP 10 Manufacturing cities
42 FACTORY OF THE FUTURE
Dexory is transforming logistics with real time data & AI
52 SAS
Optimising energy use in manufacturing with data and AI
68 DIGITAL MANUFACTURING NVIDIA explores the metaverse & AI in manufacturing
78 SUSTAINABILITY EOS is leading sustainable manufacturing with 3D printing
READ NOW
6th December 2023
1,000+ Virtual Attendees
1 Day Learning and Networking Event
30+ Acclaimed Speakers
6 Interactive Panel Discussions
The Manufacturing stage is here, and it’s putting on an exclusive virtual event for the industry.
Join Manufacturing Digital LIVE on 6th December for a two-day virtual event, where the brightest minds in Manufacturing will grace the stage.
Experience a unique opportunity for knowledge sharing, learning, and networking with industry professionals from all corners of the globe.
Dive into the innovative networking platform, Brella, to build meaningful connections, schedule meetings, and prepare yourself for the immersive LIVE stream about to unfold.
There are more than 30 internationally acclaimed leaders that you can’t afford to miss!
Covering five key themes, the event will showcase engaging presentations, interactive sessions, panel discussions and fireside chats, facilitating deep learning and exploration: Factory of the Future, Sustainability, Digital Manufacturing, Tech & AI and Women in Manufacturing.
Mark your calendars, set your reminders, and get your complimentary pass to Manufacturing Digital LIVE!
It’s time to connect with like-minded professionals who share your passion for innovation and growth.
Bangkok, Thailand
With 8bn mouths to feed, efficient food production is getting increasingly lucrative. The manufacturing sector is keeping the food supply chain running, but faces disruptions outside of the supply chain.
From Saudi Arabia to the USA, baby formula manufacturers have been warned about safety standards after a series of failings.
ABB is an automation machinery manufacturer based in Zurich. The company builds electrical components, robotics and motion control solutions, as well as power grids. Virve Viitanen, Head of Global Customer Care and Support, tells us about her role at ABB
Q. HELLO VIRVE, PLEASE INTRODUCE YOURSELF AND YOUR ROLE.
VIRVE VIITANEN
TITLE: HEAD OF GLOBAL CUSTOMER CARE AND SUPPORT
COMPANY: ABB MOTION SERVICES
LOCATION: ZURICH, SWITZERLAND
Virve Viitanen is based in Helsinki, Finland. She is the Head of Global Customer Care and Support at ABB Motion Services. Viitanen has spent 17 years at ABB and is responsible for customer support and on-demand services to customers worldwide. Viitanen studied at Tampere University of Technology where she earned a Master’s Degree in Industrial Engineering and Management. She later earned an Executive MBA at Aalto University Executive Education and Professional Development.
» “As Global Head of Customer Care and Support at ABB Motion Services, I am responsible for customer support and on-demand services to customers worldwide. This includes reactive as well as preventive maintenance services, including repairs and technical support for electrical motors, drives and generators. Having spent 17 years at ABB, I have seen first hand how the industrial technology landscape has evolved and how our industry is looking at new operating models that minimise downtime and increase profits.”
Q. WHAT IS ABB MOTION SERVICES?
» “We are the servicing arm of ABB Motion, the largest supplier of electric motors and variable speed drives globally. We have manufactured and serviced motors and generators for over 130 years, and drives for more than 40 years, across a wide range of industries. As the service arm of the business, our key objective is to keep customers’ operations running profitably, safely and reliably. We create value by maximising the uptime and extending the life cycle of our customers’ electrical motion
“We have manufactured and serviced motors and generators for over 130 years”
solutions, while optimising performance and energy efficiency gains across the entire lifetime of their applications.”
» “The impact of unplanned downtime for any company is severe. According to ABB calculations, in the food and beverage sector for example, downtime can cost from between US$4,000 and US$30,000 per hour: a substantial amount when you consider that up to 12 hours can be lost in a single incident if cleanup operations are required. Paper producers, meanwhile, lose up to US$25,000 every hour when a key asset breaks down, with the steel industry averaging around US$300,000 in losses per critical machine failure. On top of the obvious direct financial costs, downtime also presents businesses with several indirect costs, like reputational damage, health and safety risks, loss of team morale and insurance premium rises.”
» “Traditionally, service partners charge their customers based on labour and material costs. At best, they may specify a minimum time to fix any failures. Instead, an outcome-based service model is one that shifts the focus towards the intended outcome – such as uptime or energy savings. The service partner charges based on successful delivery of that outcome – for example, certain uptime in a given period. In many ways, outcome-based service models
represent an insurance-style model that lowers or removes the risk of industrial operations away from the business and onto the service provider. Some early adopters see it as an opportunity to ‘climb the reliability ladder’.
“The first step is a reactive maintenance strategy where the business takes the risk of fixing equipment only when it fails. The second step would be to have a predetermined maintenance schedule, which is referred to as a timebased or condition-based strategy. The third step is an outcome-based model where a long-term service partner
guarantees an outcome, for example uptime or energy savings, lowering risk for their customers.”
» “Customers all want increased reliability of their operations and this contributes to it directly. In addition, cost effectiveness is incremental with every step – for example, a conditionbased maintenance strategy, including condition-based services, provides 40% savings over a reactive maintenance
“Digitising equipment also enables it to be used in the most energy efficient way”
strategy, according to the US Department of Energy.
“A 2015 study on UK companies found that initial adopters of outcomebased service models have experienced significant cost reductions of 25-30%. Against a backdrop of inflation, budget squeezes, on time delivery and productivity challenges, the ability for industrial enterprises to maximise uptime by carrying out cost-effective, data-driven maintenance schedules is crucial but very beneficial.”
» “Digitalisation and long-term agreements are both critical if we are to progress to outcome-based service models.
“Without connected assets, we cannot deliver outcomes. Tracking the performance of digitally connected motors and drives, for example, is enabling a shift towards predictive maintenance informed by data. Early warning signs of equipment failure – like changes in vibration, temperature, or pressure – trigger
early interventions and help to prevent downtime. This approach, also known as condition-based monitoring, is helping to transform maintenance operations across a range of industrial sectors.
“Digitising equipment also enables it to be used in the most energy efficient way. For example, we are working with CERN, the world’s leading particle physics laboratory, to digitalise assets in its cooling and ventilation systems for condition monitoring purposes. Motors used to power pumps, fans, compressors and cooling towers – which account for about 20% of CERN’s energy consumption – now relay data back to remote operators for them to optimise energy usage. The aim is to achieve an improvement
of up to 15% in the energy efficiency of the cooling and ventilation systems.”
» “Yes, Statkraft – Europe’s largest generator of renewable energy – recently installed two new ABB synchronous condensers in Liverpool, England. The system helps ensure that the UK grid remains stable as it integrates more variable sources of energy – like wind and solar. To ensure that this vital system is available around the clock, ABB and Statkraft entered into a 10-year service agreement that will ensure uptime by providing a full range of planned and quick response maintenance services.”
Jim Umpleby is the Chairman and CEO of Caterpillar, a manufacturer of construction and mining equipment, based in Irving, Texas
D. James Umpleby III, known as Jim, is the Chairman of the Board of Directors and Chief Executive Officer of Caterpillar Inc.
He leads a team of over 109,100 employees across 63 countries and is responsible for the company’s strategy for profitable growth and its execution, which focuses on ‘operational excellence, expanded offerings, services and sustainability and driving positive change on every continent’.
He is leading the company in a sustainable direction – here, we take an in depth look at his career and what’s next.
In 1925, Caterpillar Inc. was founded in Deerfield, Illinois, to help customers ‘build a better world’, by manufacturing construction and mining equip ment, diesel and natural gas engines, industrial gas turbines, and dieselelectric locomotives.
98 years later, the company is making sustainable strides across the world and in various sectors, including construction, energy, transportation and more, with Chairman and CEO Jim Umpleby at the helm.
“With nearly a century of sustainable innovation, Caterpillar has a legacy of providing products and services that
continually improve the quality of life and the environment by helping our customers fulfil society’s need for infrastructure in a sustainable way,” says Umpleby.
At Caterpillar, sustainability is more than just a buzzword, it’s a code of conduct. Caterpillar’s philanthropic organisation, the Caterpillar Foundation,
TITLE: CHAIRMAN AND CEO
COMPANY: CATERPILLAR
LOCATION: USA
D. James Umpleby III is the Chairman of the Board of Directors and Chief Executive Officer of manufacturing company Caterpillar. Umpleby studied At the Rose-Hulman Institute of Technology, he earned a bachelor’s degree in mechanical engineering. He then studied an executive leadership program at the International Institute for Management Development.
In 2010, Umpleby became Vice President of Caterpillar, where he led Caterpillar’s Energy & Transportation business segment as Group President 2013 – 2016. Umpleby became Caterpillar’s CEO in 2017 and was elected chairman of Caterpillar’s board of directors in December 2018.
recently celebrated its 70th anniversary. In recent years, it has helped partners to respond to disasters, from the tornadoes in Kentucky, to flooding in China.
Following Russia’s invasion of Ukraine, Caterpillar stopped its manufacturing operations in Russia and has donated to support the victims of war – receiving warm gratitude from the American Red Cross for the humanitarian relief.
“Caterpillar’s Values in Action are the foundation for our work, guiding us on our sustainability journey,” said Umpleby. “Through the Caterpillar Foundation, we have engaged in sustainable infrastructure programmes, workforce development and disaster relief in 40 countries.”
Jim Umpleby’s 40 years of experience
Umpleby studied mechanical engineering at the Rose-Hulman Institute of Technology, where he earned a Bachelor’s degree. He later completed an executive leadership programme at the International Institute for Management Development, in Switzerland.
In 1980, Umpleby began working at Solar Turbines, a Caterpillar subsidiary, as an Associate Engineer. He was later promoted to President of Solar Turbines and Vice President of Caterpillar in 2010. Umpleby led Caterpillar’s Energy & Transportation
business segment as Group President, from 2013 to 2016. He became Caterpillar’s CEO in 2017 and was elected chairman of Caterpillar’s board of directors in December 2018.
Umpleby is active on various boards, including the Chevron Corporation, the US-India Strategic Partnership Forum, the US-China Business Council and the Peterson Institute for International Economics.
He is also a trustee of RoseHulman Institute of Technology, a member of Business Roundtable, The Business Council and the National Petroleum Council.
“We are committed to fostering a workplace that respects and celebrates our employees’ diverse backgrounds and perspectives”
At a time when diversity is essential for businesses – from supporting working mothers to ensuring people with disabilities can work comfortably in the workplace – Caterpillar is ‘harnessing the power of everyone’.
“We are committed to fostering a workplace that respects and celebrates our employees’ diverse backgrounds, experiences and perspectives and encourages a culture where employees feel valued and included,” said Umpleby. “This heightens the opportunity for greater team
performance and strengthens us as a company, enabling us to provide superior value for those we serve.”
In October 2022, Caterpillar’s Board of Directors waived a policy requiring its CEO to retire at age 65 – and kept Umpleby on.
Umpleby leads
109,100 employees across 63 countries
“Waiving the mandatory retirement policy for Jim provides the Board greater flexibility with its CEO succession process,” said Debra Reed-Klages, Presiding Director. “Jim has provided strong strategic and operating leadership for the company and we look forward to his continued leadership of the Caterpillar team.”
2022 revenues of US$59Manchester is the birthplace of the first industrial revolution, whose technology spread across the globe. In 2023, megacities Beijing and Shanghai lead the world.
Next door, the city of Mumbai is heading up the ‘Make in India’ initiative. Across the Arabian Sea, Dubai’s radiance offers businesses hot weather and a zero-tax sanctuary.
Seoul manufactures food and upcycled fashion, while rival Tokyo is focused on smart manufacturing. Former gold-mining hub Johannesburg, is a manufacturing and financial epicentre. In the Americas, São Paulo’s food giant JBS and Los Angeles’ SpaceX ambitions are keeping the Western Hemisphere on its manufacturing toes.
Manchester has a rich history of invention. It was the birthplace of the first industrial revolution in 1760 with the spinning Jenny, which led to an increase in slave labour to keep up with demand. The world’s first stored computer (inset) ran in 1948 at The University of Manchester and now The Advanced Machinery & Productivity Institute in Greater Manchester aims to future proof the UK’s manufacturing sector by creating new jobs and opportunities, ready for the next stage of industry evolution.
Johannesburg started out as a gold mining settlement in the 1880s. Now, it’s a business hub and the financial capital of South Africa, responsible for 17% of the country’s GDP. The city is the headquarters of chemical manufacturer AECI, which was founded in 1896 and works across mining and agriculture, in the development of various chemicals and explosives.
Africa’s largest packaging company, Nampak, is based north of the city and provides packaging for food, beverages and industrial goods.
São Paulo is the biggest city in the Southern Hemisphere, in the world’s sixth most populous country. Although easily outshined by the bright lights and beaches of Rio de Janeiro, São Paulo has the brains of the country, which is in part due to its coffee production. Food manufacturer JBS is the largest nonfinancial company in Brazil’s private sector and the second biggest food company in the world, popular for its frozen and ready-to-eat food.
In the 1996 ‘Escape from LA’, Kurt Russell arrives in the city via a torpedo sub, and soon, the city may be open to arrivals from space. Elon Musk’s private rocket company SpaceX has its research and manufacturing plant based in Los Angeles. The world’s richest man also has a vision to build a tunnel network underneath the city for flying Uber’s. The city is also known for its food manufacturing, such as Golden State Foods which is based in Irvine.
Confectionary giant Lotte was founded in 1967, in Seoul. Lotte’s products, such as the stick biscuit Pepero, have benefitted from the Korean Wave (known as Hallyu). Lotte is the third largest gum manufacturer in the world.
The Hyundai Motor Company’s ‘Re:Style’ upcycling fashion project uses materials discarded during the vehicle manufacturing process for clothing. Launched in Seoul and Paris, Hyundai has partnered with L’Eclaireur and Boontheshop to highlight the automotive manufacturers commitment to sustainable manufacturing and creative outside collaboration.
Mitsubishi Electric Corporation is headquartered in Tokyo and develops electronics and electrical equipment, employing smart manufacturing technologies to optimise its industrial processes and enhance productivity. IoT and edge computing are used for connectivity. Mitsubishi Electric also offers factory automation solutions which integrate robotics, control systems and software.
Meanwhile, the University of Tokyo has combined 2D printing, with traditional origami and chemistry in order to create a method of rapid 3D object fabrication, without creating waste.
Dubai’s glowing infrastructure and zero-tax regime make it a superb business location. Despite its size, the manufacturing sector in Dubai is advancing. Keeping the city cool is soft drinks manufacturer Dubai Refreshment. Founded in 1959 as the first bottling company in the UAE, the company brought non-alcoholic beverages into the region, including Pepsi Cola. Ducab Group has six manufacturing facilities in the UAE and manufactures cable products and overhead conductors for many sectors, including energy, construction, defence, rail transport, marine, mining and automotive.
Megacity Beijing is home to 21m people. The China National Tobacco Corporation (CNTC) is the largest cigarette manufacturer in the world. CNTC manages various tobacco manufacturers, in addition to suppliers and farmers. While 50% of Chinese men smoke, China’s youth instead favour e-cigarettes and vapes.
Military technology manufacturer
Norinco is also based in the city and builds auto parts, engineering machinery and equipment, railway products and petrochemicals, while Xiaomi Corporation manufactures smartphones and smart hardware connected by an IoT platform.
Narendra Modi, Prime Minister of India, hopes to create millions of new jobs in the manufacturing sector for the ‘Make in India’ programme. A lot of this work will take place in the coastal city, Mumbai. A bustling city, Mumbai saw the country’s first train run in 1853, the first bus service in 1926 and the first airport, which took off in 1928. As a result of this well-developed infrastructure, Mumbai became the wealthiest city in India, the country’s finance and entertainment capital and a manufacturing powerhouse.
Tech Mahindra, a part of the Mahindra Group, is working hard to promote digital transformation across manufacturing. Mahindra Group has recently announced a dedicated platform in the USA.
“This step aims to enhance global manufacturing and supply chain solutions for American companies,” said Anish Shah, MD & CEO of the Mahindra Group. “We are committed to leveraging our experience, capabilities and expansive scale thereby strengthening the global manufacturing landscape.”
The Global Supply Chain Awards 2024 will be celebrating the very best in Procurement & Supply Chain with the following categories:
Procurement Transformation Award
–Digital Supply Chain Award –Global Logistics Award –Supplier Diversity Award –Supply Chain Innovation Award –Supply Chain Sustainability Award –Procurement Technology Award
Procurement Consultancy Award –Future Leader Award –Executive of the Year Award –Project of the Year Award –Lifetime Achievement Award
Almost one-third (28.7%) of global manufacturing is completed in China, with the coastal city of Shanghai its largest hub. Each month, 2,000 container ships leave the port with cars, electronics and more. Over the pandemic, work was suspended, leaving the 25m population in a city-wide lockdown. Now, the city is back to work.
China’s construction totaled 25.9% of China’s GDP back in 2020, with Baosteel at the helm exporting high-strength steel across the world, where it is used in transportation and nuclear power. Technology company
ABB Engineering builds safe and sustainable robots and automation systems for use across the automotive and electronics sectors, in addition to plastics and packaging. Meanwhile, pharmaceutical group Shanghai Pharmaceuticals Holding supports healthcare services in their research and development, distribution and retail, as well as pharma manufacturing. The company had a revenue of US$26.5bn in 2019, making it one of China’s heavyweight healthcare forces.
Oana Jinga, CCO of Dexory, is leading women in technology & robotics with mentorship programmes, as the company revolutionises logistics
WRITTEN BY: HELEN ADAMSIn a world that is constantly upgrading, the logistics sector is busy managing torrents of data and adapting to new methods of working that saves workers time and helps ensure their safety.
Autonomous robots are one such method. These tools can operate with high precision, collect data in real-time and
use AI to generate insights using that data. Such insights empower logistics companies to make informed decisions and identify inefficiencies in their supply chain and one company is helping to revolutionise logistics and warehousing to become more efficient and profitable.
Dexory is a data analytics and robotics company based in London. Its technology
provides detailed insights to top logistics companies in the world such as Maersk, Denso and Menzies, to name a few.
Dexory helps them to measure, track and locate goods, all in real time, across vast warehouses without any workflow disruption. The company has developed advanced intelligent systems that empower organisations to manage and monitor their
supply chains, reduce costs and streamline the logistics process as a whole.
In 2015, Oana Jinga co-founded the company, alongside CEO Andrei Danescu and CTO Adrian Negoita. As the Chief Commercial Officer of Dexory, Jinga leads on sales, marketing, and partnerships, as well as investor relations with her co-founders.
“One summer, over a barbecue, my housemates (now co-founders) and I were having a conversation about wanting to find a way to keep a better eye on our house while we were away. We started playing with the idea of creating a camera on wheels that monitored indoor spaces autonomously.
“I’m keen to help women in the industry. I’ve consciously carved out an approach at Dexory with our female staff”
OANA JINGA CCO & CO-FOUNDER, DEXORY
TITLE: CCO & CO-FOUNDER
COMPANY: DEXORY
INDUSTRY: SOFTWARE DEVELOPMENT
LOCATION: LONDON
Jinga is originally from Romania and moved to the UK in 2009 to study Public Relations and Creative Industries at King’s College London. After completing her education, she worked at Telefonica and Google, before co-founding Dexory in 2015, where she leads sales, marketing, partnerships and investor relations.
We all decided to take the plunge and turn our passion for robotics and technology into a career path and our business together.”
Jinga is originally from Romania and moved to the UK in 2009 to study Public Relations and Creative Industries at King’s College London. After completing her education, she worked at Telefonica and Google.
“Not long after I completed the Telefonica Leadership programme,
I was headhunted by Google to manage strategic partnerships across EMEA.”
Jinga spent over six years at the company and had the opportunity to work across different regions.
“This experience has been quite valuable for my current role as CCO at Dexory, where I work with a diverse range of clients and partners, leading all sales, marketing and partnerships. I was part of the team that helped launch some of the
“There aren’t too many women in robotics, so that posed some challenges, but also opened up exciting opportunities”
OANA JINGA CCO & CO-FOUNDER, DEXORY
company’s most innovative products like Google Pixel phones, Google Home and Nest products.”
Dexory’s autonomous mobile robots take on a variety of tasks, such as lifting heavy loads and performing time-consuming tasks that are often avoided by staff and managers. Although robots help save time in logistics, 300,000 new logistic-related jobs are created each year.
“By relieving manufactures of these duties, our robots allow for a more efficient workflow in warehouse operations,” Jinga explains.
With continuous inventory monitoring, misplacement errors are minimised and the right stock is always available in the correct locations and at the appropriate time. This results in hundreds of hours saved and increased productivity, enabling teams to focus on the important task of moving goods around.
In essence, these robots serve as a valuable tool to enhance the capabilities of warehouse staff. Moreover, the robots enable our customers to have full visibility of their stock across different plants.
“This ensures that all necessary parts are in place to support production lines,
Dexory’s autonomous mobile robots take on a variety of tasks, such as lifting heavy loads and performing timeconsuming tasks that are often avoided by staff and managers.
without any impact on the manufacturing process or delays,” says Jinga. “In other words, our robots facilitate just-in-time manufacturing, making the entire process more streamlined and efficient.”
Jinga sits at the intersection of three highly male-dominated industries: robotics, tech and logistics.
“Although it might be challenging at times, I refuse to let the raised eyebrows deter me from my mission. Instead, I remain focused on improving the value that our tech brings to our customers, striving to make it better each day.”
For Jinga, her journey in the technology and robotics world has been an incredible journey so far.
“There aren’t too many women in robotics, so that posed some challenges, but also opened up exciting opportunities,” she says. “I started my career in PR but was always interested in the technology sector. Through a leadership scheme in O2 Telefonica, I was able to pivot into the tech world. This programme was very competitive, with over 2,500 candidates applying. I was very pleased to have made the cut.”
As a result of her experiences, Jinga has a passion for mentoring and coaching other women in Technology.
“Having come from outside tech myself, I am keen to help other women in the industry too. It can be challenging to balance that with competing priorities, but I have consciously carved out an approach internally at Dexory with our female staff.”
Jinga works closely with them, to try and understand them better
– what their needs are, what challenges they may be facing. “We bounce ideas off each other,” she says. “It is never about telling them what path to follow or what to do and how to do it, but more about finding the answers together with them.”
300,000 new logistic-related jobs are created each year
Externally, Jinga is building mentorship schemes and programmes that she can attend,
as there is more to learn. “This also really helps me understand things from a mentee’s perspective, which I am able to apply to my mentoring role at Dexory. It’s really about managing time efficiently, whether as a mentor or as a mentee. Preparation from both parties can make the entire process very efficient.”
Over the next 12 months, Dexory expects to continue its rapid growth.
“We were able to double our team last year and have plans to expand further – by another 50% by the end of the year.”
Dexory also has a number of exciting partnerships in the pipeline, which will allow the company to expand its reach even further and bring its technology to new markets, all the while, Jinga will continue in her mentorship work as a mentor and coach for women in technology.
Now more than ever, manufacturers are looking for new ways to save energy. Optimising energy use was always important, now it is vital for the sustainability of the organisation. The pressure is on to do more with less, while also maintaining quality and yield.
Cost is just one significant factor. Energy prices surged 60% in 2022, sparked by supply chain disruption and geopolitical tensions, and while those highs have fallen slightly, prices remain higher and are only likely to increase.
The International Energy Agency (IEA) has stated that the current global energy crisis is of ‘unprecedented depth and complexity’.
Yet market rates for energy are only one ‘cost’ that CEOs, CFOs and COOs of manufacturing companies have to consider. Increased regulation around emissions, ESG requirements, public pressure, investor expectations – not to mention favourable financing available for ESG-compliant companies – all mean businesses have to do more to reduce the amount of energy that they use, and also switch to cleaner, more sustainable, energy sources.
This is a significant challenge, but also an opportunity.
In this White Paper, experts from SAS – a global leader in artificial intelligence (AI) and advanced analytics – share their insights and learnings from helping both process and discrete manufacturers globally to optimise their energy usage by implementing AI in a real world setting.
TITLE: EMEA & AP MANUFACTURING LEADER COMPANY: SAS
TITLE: SENIOR MANAGER, INDUSTRY CONSULTING, IOT COMPANY: SAS
TITLE: DATA SCIENTIST & INDUSTRY ADVISOR, IOT COMPANY: SAS
The War in Ukraine is only one factor that has impacted energy prices. As the world emerged from COVID-19 restrictions in 2021, supply of energy was slow to meet surging demand. Gas, electricity and oil all hit record highs.
When Europe’s over-reliance on Russian gas was exposed, and European Union nations tapped into LNG from other markets, that had a knock-on effect that drove up global prices as demand simply outstripped supply. It is basic economics in action.
Countries that had been turning away from fossil fuels and shutting down nuclear power plants were having to rethink their
Adopting advanced data analytics and using the latest AI software can help manufacturers optimise their energy usage, often delivering double digit cost savings by shining a light on ‘hidden’ opportunities
strategies due to energy security concerns – and these continue to impact energy prices. The World Economic Forum’s Fostering Effective Energy Transition 2023 report states that after a decade of progress towards, clean, sustainable energy – those efforts have stalled as countries are shifting their focus towards energy security.
Businesses face the same challenges –securing energy at a manageable price point and maximising their efficiency to reduce total cost.
Cheap and stable energy tariffs are a thing of the past, which means that real cost optimisation requires dedicated action and more efficient and sustainable processes –especially for heavy industries with a high energy burden.
Part of that action is securing supply, especially for those heavy industries that still rely on non-renewable energy sources. The transition to clean, renewable energy is a long-term challenge – realistically 10 to 20 years – especially for these heavy industry manufacturers, so reducing consumption overall can assist in that transition.
Changing regulations around emissions are also driving the need to optimise energy usage and reduce an organisation’s carbon footprint. Failure to meet targets can mean heavy fines or even plant shutdowns.
In Europe, crucial pieces of legislation are in the pipeline, including the Green Deal Industrial Plan and the EU Net Zero Industry Act. These are driving the need for traditional industries to adapt and drive
rapid change in how they consume energy and resources.
In the US, the Inflation Reduction Act of 2022 offers advanced manufacturing production credit and energy-efficient commercial building deduction to promote sustainability in business. Additionally, company boards are making ESG commitments to shareholders, with bold statements on how they will become more sustainable. However, these often remain goals and rarely become actions – in part because it is difficult to break down such principles and goals to individual plants, production lines and processes. Perhaps the biggest challenge manufacturers face is an internal one. With the ‘low hanging fruit’ of energy monitoring already picked, many plant managers and engineers may feel that
there is no more that can be done when it comes to making their operations more efficient. Instead, they may look solely for cheaper energy procurement to deliver incremental gains. When beginning an energy cost optimisation exercise across manufacturing operations, one of the main challenges that arise comes from trusting that advanced analytics and AI can do a good job. As engineers are typically conservative, working on operational excellence causes them to resist the analysis of a computer programme.
Manufacturers need to explore new ideas. Adopting advanced data analytics and using the latest AI software can help manufacturers optimise their energy usage, often delivering double digit cost savings by shining a light on ‘hidden’ opportunities.
Many manufacturers are sitting on a data gold mine – the operative word being sitting. Companies need to take that data out of silos and bring it together in one unified analytics solution. Today, engineers are missing hidden insights that can improve upon process parameters by analysing the relationship between key metrics and the energy consumed. These insights will enable them to reduce energy consumption while maintaining or improving quality, yield, and throughput.
Energy monitoring and optimisation can complement each other, particularly if data is yet to determine the greatest energy consumption and the potential areas for reduction. Manufacturers could see variations in energy consumption due to inefficiency of their production schedules or from fluctuating raw material specifications, changing ambient conditions, etc.
Not all manufacturers are created equal. Process industries, or energy-heavy industries are more aware of where the biggest energy consumers are.
In discrete manufacturing, it must first be understood where the high energy consumption is, as well as the biggest variation in energy consumption – an area where there is great room for optimisation.
Monitoring will provide key insights into energy consumption across a variety of operational factors, from equipment to administrative aspects, to determine an overall baseline. In the process, datasets will be formed to pinpoint energy-intensive processes. Advanced analytics helps customers analyse factors they may have overlooked. By deploying a prepackaged software solution in an agile way, manufacturers can see quick results.
By deploying a prepackaged software solution in an agile way, manufacturers can see quick results
For any transformation, it is essential to get buy-in from the C-suite to the factory floor. That is a challenge in itself.
A lot depends on the maturity of the manufacturer and willingness to trust in the data and AI solution. While the concept of AI has been with us for some time, it has recently entered the public consciousness as a perceived threat to jobs and livelihoods. This needs to be tackled, and AI embraced as a business tool that improves efficiency, profitability and, therefore, economic
sustainability and viability. Allowing engineers to experiment with the technology will help to build trust and deliver long-term benefits. Engineers may be sceptical of tweaks and solutions being suggested by the algorithms at first, but the data seldom lies.
Building this trust is essential to a successful and efficient adoption. By combining a deep understanding of multiple variables, AI can simply find solutions that humans may fail to identify and improve through no fault of their own.
Manufacturing is complex, especially when it comes to variability in combustion processes that are energy-heavy.
Being able to identify and mitigate variance between shifts or batches will deliver significant savings.
Not only that, being able to accurately measure and track progress is essential for optimising sustainability benchmarking and reporting.
Advanced analytics avoids the disruption manufacturers would face if they were upgrading machinery or equipment to achieve efficiency gains. Using advanced analytics is faster and more risk-free than traditional transformation projects.
By combining a deep understanding of multiple variables, AI can simply find solutions that humans may fail to identify and improve through no fault of their own
SAS recognises that AI has the ability to find the needle in the haystack and help leaders learn from past processes in a more scientific way. When compared to more traditional approaches like upgrading equipment to save energy, AI enables control of a number of variables to ensure the optimal settings for the machines at scale, very quickly, and with lower risk.
Furthermore, proof of concepts (POCs) are reliable for testing the effectiveness of energy cost optimisation products, but there are barriers to success.
SAS has proven that the approach works if customers are ready to go along on the journey. SAS has the tools that enable customers to quickly connect the real data sources in a few weeks via cloud technology.
The best approach to minimise time to value and maximise the benefit is to look at how much energy can be saved. This should be the main driver.
The role of data availability and data quality in a successful energy cost optimisation programme is to provide a backbone – this is the most important part. Unfortunately, for some customers who have a low degree of connectivity in their operations yet, it’s also the most expensive part. But with use cases like energy cost optimisation, investment in connectivity really pays off.
It is important that insights are relevant and actionable for a process or industrial engineer to ingest. There is a strong need for process knowledge to ensure engineers are able to take data-driven actions on the factory floor. This will enable them to understand the process variables and the potential areas available for improvement.
A major part of SAS’s go-to-market strategy is to establish purposebuilt ecosystems, which are designed to fulfil a customer’s need or solve a complex business problem in a very specific vertical
When process engineers have a mindset of continuous improvement, one of the great skills they can learn and apply is root cause analysis to find underlying issues within processes and then implement appropriate corrective actions.
Transitioning to a data-driven culture, especially from a conservative starting point, requires acknowledging it as a journey rather than a sprint. This involves setting clear business objectives, gaining buy-in for the change process and sometimes modifying standard operating procedures.
However, it is important to start simple – intelligent people often want to tackle the most challenging problems, but that can create a scenario where manufacturers try intellectually stimulating projects that have a long time to value while there are low hanging fruits that are much easier to harvest.
SAS says an energy cost optimisation pilot should be achievable in three months for an industrial pilot that already works 24/7. The main factor to consider is always data –if the data is not correct and prepared in the right way, it will take longer.
A major part of SAS’s go-to-market strategy is to establish purpose-built ecosystems, which are designed to fulfil a customer’s need or solve a complex business problem in a very specific vertical.
Microsoft, for example, has global energy optimisation as a strategic focus area. SAS has partnered closely with them, specifically on this topic.
SAS developed much of its energy cost optimisation technologies to be natively integrated with Microsoft’s Azure platform. SAS is also available on the Azure marketplace for manufacturers to purchase and deploy directly.
Wienerberger AG is the world’s largest producer of bricks, with 217 production sites in 27 countries. The company is also the market leader in clay roof tiles in Europe as well as concrete pavers in CentralEastern Europe and pipe systems in Europe.
Wienerberger was looking to optmise its energy usage, particularly in the brick kilns which require significant amounts of heat. They took the guesswork out of making improvements by combining and analysing IoT and process data from across the production process, using prebuilt analytic models to predict specific energy consumption and make sense of variable impacts – from quality of the clay to outside humidity and indoor temperatures.
By using SAS software, Wienerberger delivered mathematically optimised insights that empowered production operators to tune the process recipe setpoints, accelerating time to value and providing an average energy cost saving of 10% – hugely significant savings for that manufacturing process.
By using SAS software, Wienerberger delivered average energy cost saving of 10%
Accelerated computing company NVIDIA manufactures integrated circuits and graphics processing units, used across businesses, such as Amazon and Microsoft. The company has gone on to influence the manufacturing industry with its scientists, researchers and developers using NVIDIA technology to help businesses work together and with customers more efficiently.
NVIDIA has powered AI innovation for decades. Today, over 35,000 businesses are using NVIDIA AI technologies, and 15,000 global startups are part of the NVIDIA Inception programme. Since its founding by Jensen Huang, Chris Malachowsky and Curtis Priem in 1993, the company has continued to grow yearon-year. NVIDIA recently reported its revenue for the second quarter, US$13bn, an 101% increase from last year.
“A new computing era has begun. Companies worldwide are transitioning from general-purpose to accelerated computing and generative AI,” said Huang.
The company is based in Santa Clara, California, with more than 50 offices worldwide.
A modern network must be able to respond easily, quickly and flexibly to the growing needs of today’s digital business. Must provide visibility & control of applications, users and devices on and off the network and Intelligently direct traffic across the WAN. Be scalable and automate the process to provide new innovative services. Support IoT devices and utilize state-of-the-art technologies such as real-time analytics, ML and AI. And all these must be provided with maximum security and minimum cost.
This is the power that brings the integration of two cloud managed platforms, Cisco Meraki and Cisco Umbrella. This integration is binding together the best of breed in cloud-managed networking and Security. cisco.com
Ludwig von Reiche is the Managing Director of NVIDIA’s German companies. The German team is NVIDIA’s largest in Europe, covering a wide range of products and solutions for artificial intelligence, visual and high-performance computing, robotics and autonomous vehicles.
“Since its founding in 1993, NVIDIA has been a pioneer in accelerated computing,” explains von Reiche. “The company’s invention of the GPU in 1999 sparked the growth of the PC gaming market and redefined computer graphics. Later, it ignited the era of modern AI and is now fueling industrial digitalisation across many markets.”
“The digital twin facilitates hands-on problem-solving between numerous teams across different countries”
LUDWIG VON REICHE MANAGING DIRECTOR, NVIDIA
The metaverse is a term for the 3D evolution of the internet and NVIDIA is focused on its industrial applications.
In an address at SIGGRAPH in 2022, Huang, NVIDIA’s CEO, called the metaverse the next evolution of the internet.
“The combination of AI and computer graphics will power the metaverse,” he said.
For von Reiche, this is an exciting opportunity for manufacturing.
“The industrial applications for the 3D internet, which include digitalisation –
TITLE: MANAGING DIRECTOR
COMPANY: NVIDIA
INDUSTRY: COMPUTER HARDWARE
MANUFACTURING
LOCATION: BERLIN
Ludwig von Reiche is the Managing Director of NVIDIA’s German companies, the largest in Europe which works across AI, visual and high-performance computing, robotics and autonomous vehicles.
transforming traditionally physical processes into digitally-enabled processes – or, building virtual worlds to train the next wave of autonomous robots, vehicles and perception AIs.”
“Manufacturing businesses are using the metaverse to digitise difficult physical processes, such as designing and engineering physical products, or planning and operating physical factories and warehouses,” says von Reiche.
Many manufacturers are leveraging state-of-the-art simulation technology to create true-to-reality digital twins
on a massive scale, including 3D replicas of entire factories.
“A true-to-reality digital twin means that everything in the physical world has an exact duplicate in the virtual world, all the way down to the literal nuts and bolts. A key aspect is that users can run simulations to test possible scenarios so as to pick the most optimal option. Furthermore, data from the real world captured through sensors can be fed into the digital version to synchronise the digital twin in real time.”
NVIDIA is working with many industrial companies and manufacturers to build
digital twins of warehouses and factories to optimise their layout and logistics.
“We’re seeing customers across different industries digitising their industrial datasets, processes and systems.”
AI’s impact extends beyond industrial use cases. At the time of writing, US$235m has just been raised for an AI startup, Hugging Face. Founded in 2016, the company builds tools for AI developers to test their work. Backers included Google, Amazon, Intel, IBM and Nvidia.
“We are collaborating also with Hugging Face to simplify the creation of new and custom AI models for enterprises,” said Colette Kress, NVIDIA CFO, on the company’s latest earnings call. “Hugging Face will offer a new service for enterprises to train and tune advanced AI models powered by NVIDIA DGX Cloud.”
The evolution of the 3D internet is giving businesses various new opportunities, but there’s still a lot to learn.
“The ability to simulate and test thousands of scenarios and variations virtually, before and during physical production, saves cost and minimises waste, while increasing operational efficiency and accuracy – and in the end, a company’s competitiveness and bottom line.”
Several of the world’s leading manufacturers use NVIDIA Omniverse, a platform for developing metaverse applications and a compute engine for building and operating custom 3D pipelines, applications and virtual worlds.
“BMW has adopted a digital-first approach to its manufacturing process. In the past, reconfiguring production lines was an expensive endeavour, not least because
“In the metaverse, they can all interact with the same digital asset in real time”
LUDWIG VON REICHE MANAGING DIRECTOR, NVIDIA
NVIDIA has also gone on to make significant progress in AI, with over 35,000 businesses using NVIDIA AI technologies
of the production downtime,” explains von Reiche.
Moving valuable machinery and robotics is not a quick task, so BMW uses Omniverse to ensure decisions made in the physical world are supported by insights gathered in the virtual one.
“The digital twin facilitates hands-on problem-solving between numerous teams across different countries. In the metaverse, they can all interact with the same digital asset in real time. As a result, BMW has seen 30% more efficient planning processes, with reduced planning times and improved flexibility and precision.”
To maximise these benefits, the automaker is opening its newest electric vehicle factory in a virtual world two years before the real-world counterpart is due to be operational. BMW’s virtual factory is a physically-accurate digital replica, wherein logistics and production planners are able to virtually collaborate, visualise and decide on optimal production line design.
“This will enable BMW to reduce the risks and teething problems usually associated with new factories opening, and ensure success before committing to massive construction projects and capital expenditures.”
Manufacturers get more value from interoperable tools today because users are no longer limited to working within only one application.
“Planners, engineers and facility managers can view extremely large, complex datasets and workflows in context – seeing their massive factories, thousands of pieces of equipment and even simulated virtual workers all in one environment,” says von Reiche.
Dave
Krzeminski, Senior Additive Minds Consultant at EOS, shares how EOS’ commitment to sustainability through 3D Printing is building a greener future WRITTEN BY: HELEN ADAMSIn recent years, the results of 3D printing have amazed the worldfrom vegan steak to prosthetics, guns to human tissue, there is no stopping manufacturers as they seek to find a use for this time-saving and waste-reducing technology.
At EOS, the company offers responsible manufacturing solutions with its industrial 3D printing technology to the world’s manufacturers. EOS is the leading provider of additive manufacturing solutions, offering industry-leading metal and
Manufacturing is a lucrative target for cybercrime. As a large industry with valuable data and a growing IoT attack surface, your data is of direct value to hackers.
polymer AM Systems (3D Printers) and provides comprehensive services, materials and software to provide endto-end solutions for the industry. Formed in 1989, EOS plans to shape the future of manufacturing with its platform-driven digital value network of machines and a holistic portfolio of services, materials and processes. EOS is also deeply committed to acting responsibly for our planet.
Dave Krzeminski, Senior Additive Minds Consultant at EOS, is helping businesses reach net zero.
“EOS is committed to helping our customers tackle environmental and climate challenges, as highlighted by our responsible manufacturing corporate initiative. For example, we assist our customer YouMawo Eyewear to conduct LCA assessments which help quantify carbon emission hotspots,” he explains.
“EOS can offer customers calculations of kg/ CO2 to produce parts via EOS technology and prepare them for emerging carbon tax policies”
DAVE KRZEMINSKI SENIOR ADDITIVE MINDS CONSULTANT, EOS
Dave Krzeminski
TITLE: SENIOR ADDITIVE MINDS CONSULTANT
COMPANY: EOS
INDUSTRY: MACHINERY MANUFACTURING
LOCATION: CHICAGO
Dave Krzeminski is the Senior Additive Minds Consultant at EOS, where he supports businesses who want to reach net zero. He lives in the Greater Chicago Area.
From start-to-finish EOS provides consultation on materials, design and the printing process to meet customers’ demands for greener materials, freedom of design and reduction of carbon emissions.
“We recently developed an industry-first solution called Smart Fusion Software that can reduce material usage waste through intelligent heat management with closed loop in real-time, controlling the amount of energy being applied into a metal power bed.”
Additive manufacturing is improving the bi-product waste collection that occurs during the product process, ultimately reducing the cost-per-part and carbon footprint.
Additive manufacturing and 3D printing are different things, but they’re easily confused:
Additive Manufacturing is a broad term which covers multiple processes for creating three-dimensional objects from materials from metals to ceramics. This includes 3D printing as well as other methods, such as laser sintering.
3D Printing is a type of additive manufacturing technology, which creates physical objects from digital 3D models, printing layer by layer. It is typically plastic-based.
In a previous interview with Manufacturing Digital, EOS’ Lead Engineer of Environmental Technology in North America, Spencer Thompson, shared how the EOS team wants to make the Additive Manufacturing industry more sustainable than conventional.
“It turns out that there are many areas where we actually aren’t all that sustainable,” he said. We are learning about these through organisations like the Additive Manufacturing Green Trade Association, and coming up with a game plan to address our own sustainability hotspots.”
These range from energy generation to carbon capture and sequestration to emissions reduction to sustainable consumer goods. Thompson’s goal for 2023 has been to fully immerse himself in the sustainability space and learn the different ways companies are creating a more responsible manufacturing future.
For Krzeminski, Additive Manufacturing offers unique inherent sustainability opportunities – the biggest one being a reduction in material usage. Compared to traditional subtractive manufacturing, Additive Manufacturing has the ability to only use the material needed to create the part.
“Another advantage of Additive Manufacturing is parts consolidation, which can turn the assembly of twelve parts into one printed part,” says Krzeminski.
This method eliminates costs and the logistical problems to procure and quality control assembly parts, but it also shortens
EOS industrial 3D printing for the aerospace industry
IMAGE: ARIANE GROUP/EOS
the time to market. With supply chains in the crosshairs for major emissions reduction efforts, Additive Manufacturing can:
• Produce parts on-demand
• Prevent manufacturers from overproducing items
• Less parts will mean lower demand for items needing to be stored in a facility
“This helps to build a more robust and agile supply chain, compared to shipping parts around the globe as demand continues to fluctuate during an economic downturn,” Krzeminski describes.
EOS has developed a web-based cost-per-part calculator, available to its customers to rapidly estimate production costs.
“From this foundational product data, EOS has collected carbon emission data around
“Initiatives to be more sustainable can certainly be difficult to catalyse and knowing where to start can be overwhelming”
DAVE KRZEMINSKI SENIOR ADDITIVE MINDS CONSULTANT, EOS
IMAGE: EOS/CSI ENTWICKLUNGSTECHNIK
Additive manufactured spare parts: a core element of sustainable spare parts management IMAGE: EOS
our technology (material production, machine energy consumption, transportation emissions, etc).
With this initial carbon emission data, EOS can now offer our customers calculations of kg/CO2 to produce parts via EOS technology and prepare our customers to begin planning for emerging carbon tax policies.”
EOS can support the manufacturing supply chain through these digital manufacturing solutions.
“We also provide software that tracks machine operations live and provides data-driven decision making towards maximising overall equipment effectiveness
(OEE). In addition to direct-part manufacturing, EOS’ metal and polymer technology can also produce tooling to support other manufacturing technologies and supply chain partners.”
While there are a lot of financial and social benefits for a company seeking to become more sustainable, there are also drawbacks. The decision to change can leave manufacturers overwhelmed, confused and concerned about their future.
Ultimately, is going green worth the squeeze?
EOS is an independent company, founded in 1989“Great question! Initiatives to be more sustainable can certainly be difficult to catalyse and knowing where to start can be overwhelming,” says Krzeminski. “I think an organisation must be fully committed to going green and endure any ups and downs to get across the finish line. Getting an easy win is a big first step, compared to tackling the hardest challenge first.
I also think policies and customer demand will drive green initiatives for organisations, and being proactive will be beneficial.”
Over the next 12 months, EOS will continue to evaluate its internal processes to identify opportunities for more sustainable practices.
EOS has recently launched the Can I 3D Print This online analysis tool. Designed for both metal and polymer 3D printing, it offers users the freedom and independent inquiry to investigate the viability of Laser Powder Bed Fusion (LPBF) industrial 3D printing for production.
“We are collecting more data around our material and machine manufacturing which will feed into and bolster our Carbon Calculator,” he explains. “Equally, many exciting applications are being launched by our customers that demonstrate sustainable solutions, and EOS is working to help promote these to help spread the word to as many eyes and ears as possible.”
“EOS is committed to helping our customers tackle environmental and climate challenges, as highlighted by our responsible manufacturing corporate initiative”
DAVE KRZEMINSKI SENIOR ADDITIVE MINDS CONSULTANT, EOS
Andre Marino from Schneider Electric shares how IoT devices are impacting commercial real estate and helping buildings become more sustainable
WRITTEN BY: HELEN ADAMSIoT, AI and other machine learning technologies are helping to address some of the greatest challenges and opportunities in today’s commercial real estate industry. To provide comfortable, healthy buildings and achieve net zero, there is some complexity on the automation and optimisation side. But today’s IoT systems are much more intelligent and the knowledge needed to operate them and to oversee multiple systems is far less burdensome.
The Internet of Things constitutes the use of sensors, software and other physical information-collecting technologies in businesses. It is pervasive in the buildings industry and allows manufacturers to do more ‘light retrofits,’ which addresses a large portion of today’s real estate market and the increased demand to reduce energy and increase automation.
“By having IoT sensors and devices as part of our building systems, we can now connect straight to the Internet via wireless connection,” says Andre Marino, SVP, Digital Buildings Global LOB at Schneider Electric. “This means customers can digitise and augment their current systems or bypass older systems and go straight to the cloud, avoiding the need to replace a lot of existing infrastructure. This is a key component of retrofitting buildings, as 50% of today’s buildings will be in operation in 2050, as well as for small and mid-size buildings that need faster and simpler installation with less complexity.”
It’s also applicable for large and new buildings where IoT helps provide more processing power, flexibility and access to more valuable data to help reduce energy use and increase decarbonisation. There’s
Ensuring the agility and resilience of your business and supply chain starts with identifying the risks.
Download our report to start your resilience planning today.
Download ASCRI Report
a lot that Schneider Electric can accomplish today that was not possible some years ago.
“In comparison, in traditional manufacturing, there is a long and complex supply chain, including product development, processing, transportation and point of sale to the consumer.
However, the commonality to real estate is about flexibility: being able to leverage a lot of data with cloud-based systems; sometimes bypassing or connecting with current installations in one building or an enterprise of buildings.”
Here, Marino tells us more.
IoT in the fourth electrical revolution
As the Sr. Vice President of Digital Buildings at Schneider Electric’s global Digital Energy Division, Marino’s role is to understand market needs and share the vision for the Digital Buildings line of business. He’s also responsible for ensuring that the team allocates the right people and resources to execute and deliver on those needs and vision.
“On behalf of our division, my mission for Digital Buildings is to deliver comprehensive
“DIGITAL AND IOT BUILDING TECHNOLOGIES HELP DRAW AND RETAIN YOUNGER SKILLED WORKERS IN HIGHLY COMPETITIVE TALENT MARKETS”
ANDRE MARINO SVP, DIGITAL BUILDINGS GLOBAL LOB, SCHNEIDER ELECTRIC
building solutions that are good for people as well as the planet,” Marino explains. “This means we must ensure that all types of buildings are not only comfortable and healthy for people, but also net-zero carbon for the environment. It means providing solutions that help create Buildings of the Future: those that are Sustainable, Resilient, Efficient and People-centric.”
Before joining Schneider Electric’s Digital Energy Division, Marino worked in industrial automation, where he managed national and global operations, overseeing project services, very parallel to what Schneider Electric does in the real estate space.
“In those roles, I gained experience in navigating the industrial transformation, which has prepared me well for the fourth electrical revolution we are currently facing in the buildings segment.”
Marino believes that the convergence of electrification and digitalisation – known as Electricity 4.0 – is the fastest route to a net-zero carbon world.
“However, there are both differences and similarities. The markets are organised differently, but there is a common layer of automation and digital transformation, and a concern for climate change on both sides of the equations. Electricity enables green energy – it is the most efficient energy and the best vector for decarbonisation.”
Digitalisation allows Schneider Electric to make energy more visible, drives efficiency and helps eliminate energy waste.
IoT devices are making commercial real estate more sustainable IoT and automation are helping integrate more systems in and around the building
“WE PROVIDE SOLUTIONS THAT HELP CREATE BUILDINGS OF THE FUTURE: THOSE THAT ARE SUSTAINABLE, RESILIENT, EFFICIENT AND PEOPLE-CENTRIC”
ANDRE MARINO SVP, DIGITAL BUILDINGS GLOBAL LOB, SCHNEIDER ELECTRIC
that includes not only HVAC, power and lighting, but also workplace services, EV charging stations, microgrids and other distributed energy resources (DERs). So while these systems and the data we can capture from them are much more complex, IoT devices and AI are helping us to gather and investigate vast quantities of previously inaccessible and unstructured data. These resources make systems easier to connect, manage, automate and provide actionable insights to ensure the buildings and their systems perform optimally and efficiently.
TITLE: SVP, DIGITAL BUILDINGS GLOBAL LOB
COMPANY: SCHNEIDER ELECTRIC
INDUSTRY: ELECTRICS
LOCATION: BOSTON
Andre Marino is the Sr. Vice President of Digital Buildings at Schneider Electric’s global Digital Energy Division. He makes sure that his team allocates the right people and resources to deliver on the customer’s needs.
“Digital and IoT building technologies, for facility management as well as for tenants / occupants, help draw and retain younger skilled workers in highly competitive talent markets,” explains Marino.
The built environment contributes 37% of global greenhouse gas (GHG) emissions. Both old and new buildings must become more sustainable and achieve netzero carbon. Marino sees that there is a lot of work to be done.
“One of the biggest sustainability implementation challenges is data collection, reporting and transparency. Capturing data and automating building systems –from multiple systems from both inside and outside of the building – helps reduce energy and increase decarbonisation. Buildings are more connected and IoT facilitates the integration of once disparate systems, so they communicate and work together.
“For example, SpaceLogic™ Insight-Sensors can detect the number of occupants in a room and adjust HVAC and lighting accordingly, modifying energy use based on people in a room, and reducing energy use when spaces are unoccupied. The same sensors can open or close blinds in an office to help keep them cooler, warmer or brighter to reduce energy consumed.”
Paradoxically, while owners and managers of commercial real estate and other buildings strive for sustainability and efficient buildings, the demand for energy is going up.
37%of global greenhouse gas (GHG) emissions
BY HAVING IOT SENSORS AS PART OF OUR BUILDING SYSTEMS, WE CAN CONNECT STRAIGHT TO THE INTERNET VIA WIRELESS CONNECTION”
ANDRE MARINO
“More electric vehicles require charging and require more energy which places additional strain on the grid. Having insight and understanding of these demand spikes can help real estate managers plan and operate more efficiently based on peak demand and pricing.”
Businesses can bridge action and sustainability utilising technology and by deploying a three-step path to net-zero buildings:
• Strategise
Assess the sustainability status of the company and its buildings and develop a decarbonisation roadmap
to implement technology, identify gaps and model retrofit scenarios for net-zero action
• Digitise
Integrate the necessary digital solutions in buildings to track embodied carbon, measure energy usage and analyse energy/ carbon efficiency
• Decarbonise
Take actions like reducing the amount of carbon the business emits, electrifying business operations like transport, infrastructure and more, and installing the use of on-site renewables for direct, clean energy distribution to the building.
“I GAINED EXPERIENCE IN NAVIGATING THE INDUSTRIAL TRANSFORMATION, WHICH HAS PREPARED ME WELL FOR THE FOURTH ELECTRICAL REVOLUTION WE ARE CURRENTLY FACING IN THE BUILDINGS SEGMENT”
ANDRE MARINO SVP, DIGITAL BUILDINGS GLOBAL LOB, SCHNEIDER ELECTRIC
Many of the topics and trends discussed above are not new issues and were being addressed by Schneider Electric pre-COVID-19.
“I’d say the pandemic made them a greater reality and accelerated their priority industry-wide, such as the need for healthy, comfortable and flexible buildings, as well as for increased efficiency.”
Marino anticipates that the next 12 months at Schneider Electric will be very exciting as the company further deploys solutions and additional technologies to its customers and EcoXpert partners.
“They will help commercial real estate and building owners maximise their investments by addressing the needs of the planet and their tenants, while ensuring occupants are comfortable and productive,” says Marino. “We are leading in ESG and committed to become net-zero across our end-to-end value chain of stakeholders, suppliers and partners.”
IoT, AI and other machine learning technologies, Schneider Electric will solve the challenges present in today’s commercial real estate industry –and beyond.
DID YOU KNOW?
Schneider Electric is an Impact company, committed to bridging progress and sustainability for all. Not only is it a sustainability enabler, supporting partners and customers with digital solutions and services, Schneider Electric is also a sustainability practitioner.
6th December 2023
1,000+ Virtual Attendees
1 Day Learning and Networking Event
30+ Acclaimed Speakers
6 Interactive Panel Discussions
SPONSORSHIPS GET YOUR PASS