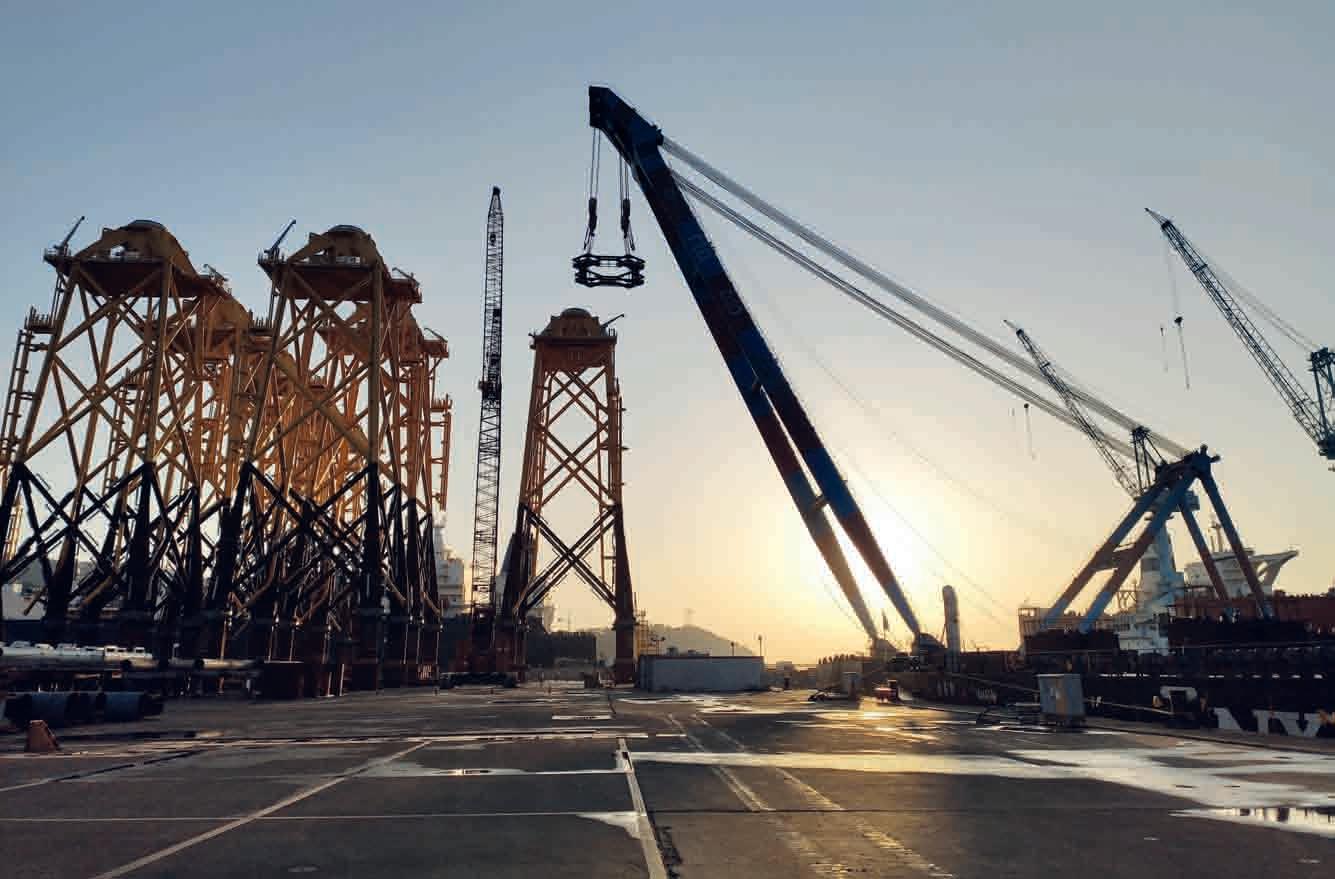
4 minute read
Demonstrating expertise
A 1,500t crane vessel has been engaged to lift the jackets onto a heavy transport vessel.
JAN DE NUL CONSTRUCTS TAIWAN OFFSHORE WINDFARMS
IN THE ASIA-PACIFIC REGION, MANY COUNTRIES ARE AIMING AT OFFSHORE WIND FOR ENERGY TRANSITION. THIS IS AN EXCELLENT OPPORTUNITY FOR EUROPEAN CONTRACTORS TO SHOW THEIR EXPERTISE IN OFFSHORE WINDFARM CONSTRUCTION. Luxembourg maritime contractor Jan De Nul Group has been active in the region for some years now and Changhua Offshore Windfarm (also known as TPC Offshore Windfarm Phase 1 Project-Demonstration) is one of the projects the company is currently involved in.
ALL PHOTOS COURTESY OF JAN DE NUL. T he Changhua Offshore Windfarm EPCI contract was awarded to the Consortium Jan De Nul-Hitachi on 30 April 2018. The project entails the manufacturing and installation of 21 5.2MW offshore wind turbines (for a total energy production of 110MW) for the Changhua Offshore Windfarm, off the coast of Fangyuan in Central Western Taiwan. The works also include manufacturing and installation of all foundations, cables, WTGs, and electrical installations, as well as operation and maintenance of the OWF for a five-year period.
Cyclonic waves and winds Jan De Nul Group is responsible for the design, fabrication, and installation of the foundations, the installation of wind turbines, the supply and
installation of the cables off and onshore, the upgrading of the substation, and for any operation and maintenance related to these works. Hitachi is in charge of manufacturing, assembly, operation and maintenance (O&M), and other works related to offshore wind turbines with downwind rotor. One specific feature of the design is that the foundations and wind turbines are designed to withstand cyclonic waves and winds, as well as earthquake loads. Manufacturing of the wind turbines was mainly planned during 2019 in order to deliver them by early 2020. Test operation of the equipment is targeted to start this Summer and completion is scheduled for the end of December.
Fangyuan For the offshore windfarm, 21 jackets of 60m high, each weighing more than 1,100t and together comprising approximately 22,000t of steel, have been manufactured at the South Korean Shipyard Company Samkang. The jackets also include the transition piece (TP) for the installation of the 5.2MW turbines. The TPs have a maximum diameter of 5.40m and a maximum height of 7m. Construction of the jackets started in the Summer of 2019. The first ones were ready for load-out to Taiwan in early May 2020. Jan De Nul Group has signed a contract with Hunghua Construction of Taiwan for this overseas transport. A 1,500t crane vessel has been engaged to lift the jackets onto a heavy transport vessel, which will then sail to the destination approximately 8km off the coast of Fangyuan in Central Western Taiwan, where Jan De Nul Group will be responsible for their installation.
Taiwan-made pin piles Each jacket will be attached to the seabed with four pin piles. The pin piles have a diameter of 3.1m, a maximum length of 82m, and a maximum weight of 310t. Eighty of them were manufactured at a South Korean fabrication yard managed by Scottish company Edgen Murray. The first load-out took place mid-April. Four pin piles have been manufactured in Taiwan by steel fabricator Ming Rong Yuan Business. These pin piles are the very first Taiwan-made foundation components for offshore windfarms in the country. The consortium hereby demonstrated its commitment to make use of the local supply chain as much as possible. Upon arrival in Taiwan, the 80 pin piles from South Korea will be custom cleared before travelling to the offshore location. Once the jackets are put in place and anchored with the pin piles, Jan De Nul can start with the installation of the Hitachi turbines.
Cable installation In August 2018, the project kicked off with the execution of onshore cable installation works to connect the 13km stretch between the existing onshore sub-station and the cable interface near shore where the land cables are connected to the subsea cable. Approximately 3.5km out of the 13km required horizontal directional drilling for installing underground pipes. The remainder of the stretch has been covered by traditional reinforced concrete duct banks and some 50 prefabricated manholes. Works were executed by Taiwanese subcontractor Star Energy Corporation and took just one and a half years. Subsequently, a total of 164km of land cable has been laid by Jan De Nul’s Subcontractor Chung-Hsin Electric & Machinery Manufacturing Corp., which was also in charge of the supply and installation of electrical equipment for the onshore substation. The connecting submarine cable will be installed in the course of 2020 by Jan De Nul’s vessels Isaac Newton and Willem de Vlamingh.
i. jandenul.com
First load-out of pin piles for the Changhua offshore windfarm took place mid-April.
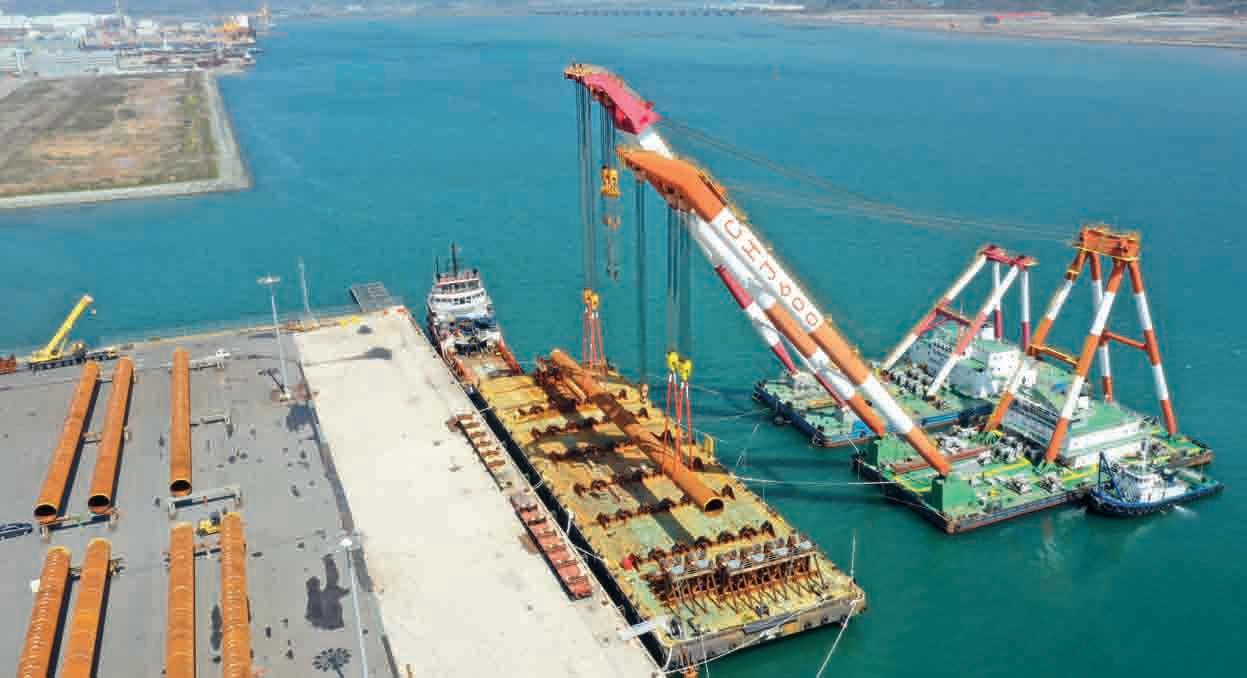