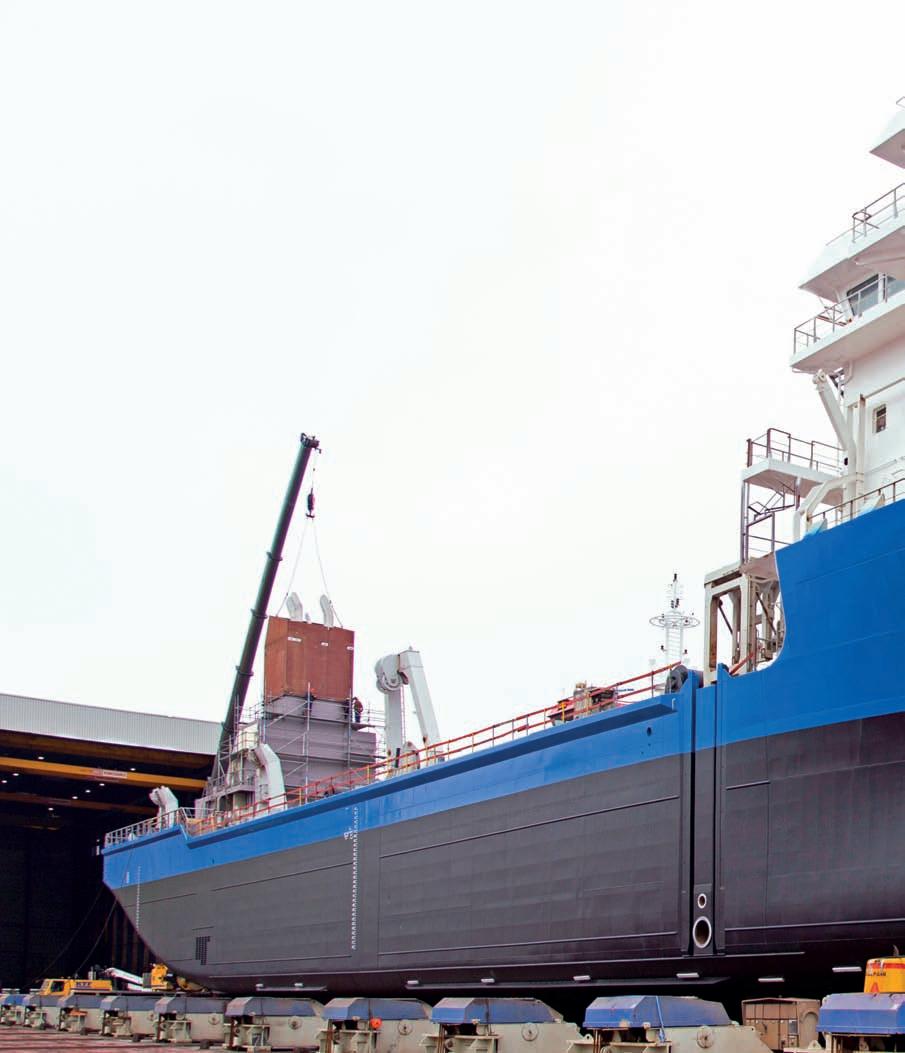
5 minute read
Vessel TSHD Anchorage: Innovative 3,000m 3
TSHD Anchorage
Barkmeijer shipyards and Thecla Bodewes shipyards Build innovaTive 3,000M 3 dredGer
Thecla Bodewes shipyards Group in Harlingen Has launcHed tHe stateof-tHe-art trailing suction Hopper dredGer anchoraGe.
TsHd anchorage very nearly did not get finished. the dredger was initially being built for a British company, but following the bankruptcy of Barkmeijer stroobos in 2018, the vessel remained unfinished. a takeover by thecla Bodewes shipyards group in 2019 blew new life into the shipyard and the project. a new client was found in building material supplier de Hoop terneuzen who was looking to expand the fleet of its sand and gravel extraction company. the half-finished trailing suction hopper dredger on Barkmeijer’s quay in stroobos fitted the plans perfectly.
All imAges courTesy of Thecla Bodewes shipyards Group.
“anchorage has been designed with state-of-the-art technology”, says thecla Bodewes, owner of the tB shipyards group. the vessel is equipped with a smart diesel-electric system, developed in close collaboration between Barkmeijer and d&a electric. “this efficiently regulates the energy supply for sailing, dredging, and unloading the ship”, explains Ms Bodewes. “as a result, energy and fuel consumption is optimised and the ship’s emissions are greatly reduced. By applying this sustainable technology to the propulsion’s system, the tsHd is ready for the future.”
Fuel Efficiency anchorage has a length of 105.9m, it is 15.85m wide, and has a draft of 6.94m, with accommodation on board for fourteen crew members. the hull was designed by, and built at, Barkmeijer in stroobos. the hull shape is optimised for both loaded and unloaded sailing by a computational fluid dynamics calculation. the hull was launched in stroobos in april 2019 and shortly after towed to tB shipyards in Harlingen, >>

Anchorage is equipped with a smart dieselelectric system, developed in close collaboration between Barkmeijer and D&A Electric.
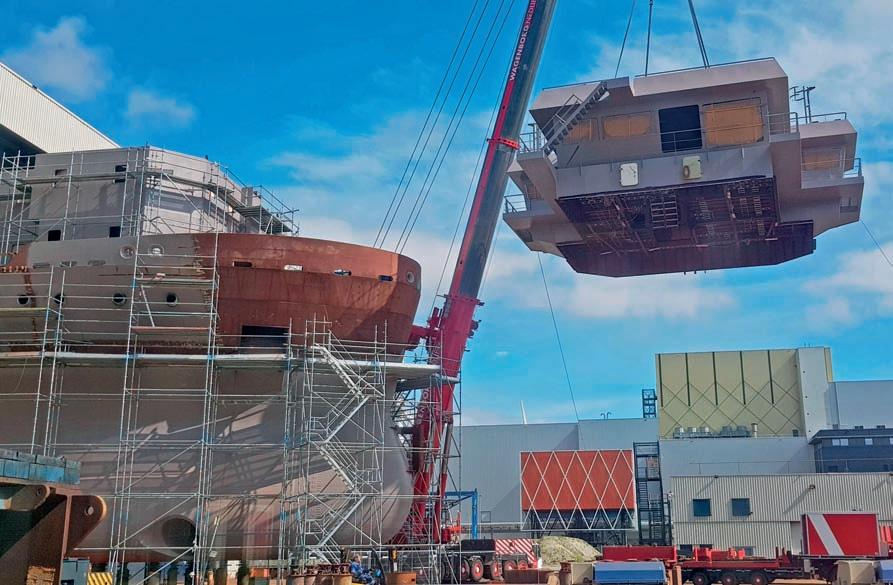
The wheelhouse is placed on board during the final outfitting at TB Shipyards in Harlingen.
The hull of TSHD Anchorage was launched at Barkmeijer in Stroobos in April 2019 and towed to TB Shipyards in Harlingen shortly after.
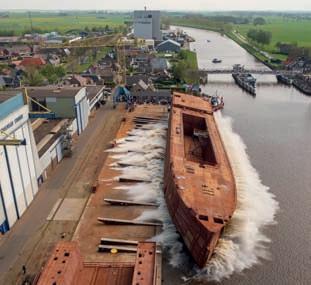
where the final outfitting, electrical works, installation of all engine room equipment, technical spaces, and pump room were carried out. “Insulation works and interior works have been done after completion of the superstructure in June 2019”, reveals Ms Bodewes. “Paintwork was carried out during the months of October, November, and December. The dredging equipment was unloaded at Barkmeijer, it was completely prefabricated here and transported to Harlingen on 23 January, just before the launch. The installation of the dredging equipment on board has started.” The TSHD is powered by three Mitsubishi medium-speed diesel generator sets. Two of 2,550eKW each, and one of 1,275eKW. The gensets are able to run all three parallel, or twin, or single, depending on the required power for each specific operation: dredging and sailing, discharging, or just sailing. The different setups of the gensets ensure a most efficient load of the gensets which results in the lowest possible fuel consumption. Fuel efficiency has further been optimised by a number of innovative features, such as the ability to use shore power for all ship systems during port stay, extensive use of waste heat recovery, variable speed pumps and ventilators, high efficiency electric motors for all applications, and LED lighting for the entire vessel.
Intelligent Automation Package The power management of the power generation, E-prop propulsion, and E-pump dredging equipment is efficiently controlled by the D&A Electric software. For controlling and monitoring all of the ship’s systems and the dredging process, Barkmeijer Shipyards collaborated with leading system specialist Alewijnse Marine. They have developed an integrated intelligent automation package. This PLC-based Alarm, Monitoring & Control System with 26in SCADA HMI workstations includes the remote control of engine room systems, ventilation, lighting, and the hydraulic equipment related to the dredging
installation. The PLC system provides the control logic, alarm logic, and interlocks in the system. A Dredge Control System module is integrated with a large number of sensors in the dredge system for monitoring the drag arm and the performance of the dredging process. The wheelhouse is equipped with multiple control positions, enabling one-man control during sailing, dredging, and unloading operations. This package provides high dredging performance and also enables dredging, sailing, and maintenance operations to be handled by a limited crew of only seven or eight members.
Dry Cargo The TSHD has been especially built for extracting sand and gravel at sea up to 60m deep. For the dredging installation, Barkmeijer co-operated with Holland Marine Technologies, who designed and supplied the efficient and maintenancefriendly equipment. An underwater pump, mounted in the suction pipe, brings the sand or gravel mixture to a sieve, which separates the sand and gravel and deposits the preferred cargo into the hopper and discharges the unwanted material back into the sea. During the trip to the port of discharge, the water is extracted from sand or gravel so that the cargo can be unloaded ‘dry’ by the ship’s onboard ship-to-shore discharge system. The dredger will be completed and commissioned in the coming months – ready to join De Hoop’s fleet before the summer of 2020. “The success of this project has been possible thanks to the close cooperation between Barkmeijer and TB Shipyards”, concludes Ms Bodewes. “Our four shipyards complement each other and as a group, we can actually build all types of ships: from simple push boats to complicated dredgers like the Anchorage. The future is looking good.”
The installation of the dredging equipment on board started in January.
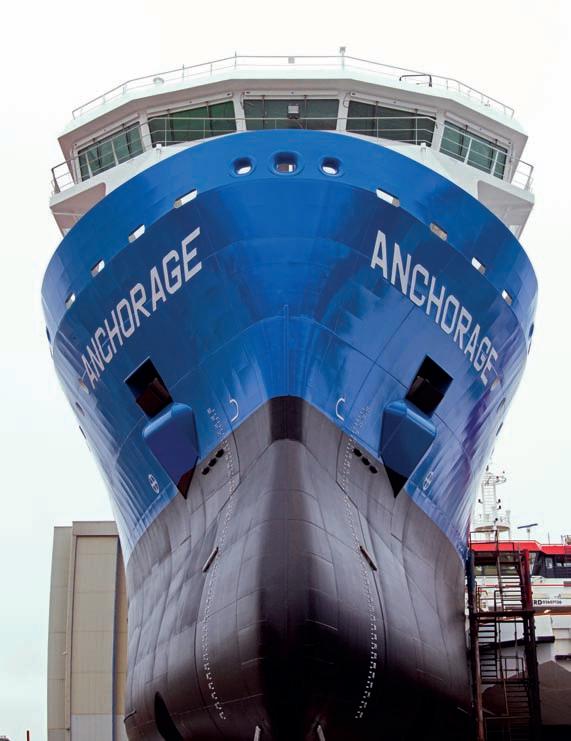
SPECS
TSHD Anchorage has been built under supervision of the Classification Society, Bureau Veritas (BV), with the following notation: I Hull Mach | Hopper Dredger | Unrestricted Navigation | AUT – UMS | Clean Ship | Green Passport
Overall length Length bpp Breadth Depth Draught summer Speed Hopper capacity Gross tonnage Air draught at 6.00 m draught Inside diameter of drag arm Maximum dredge depth 3 Main Diesel Alternator sets total installed output 1 Emergency / Harbour Diesel Alternator set output 2 Rudder propeller units driven by electric motor 1 Bow thruster driven by electric motor: 1 Submerged dredge pump driven by electric motor 1 Jet pump driven by electric motor 1 Flow acceleration pump driven by electric motor 105.9m 100.55m 15.85m 8.85m 6.94m 14 knots 3,200m 3 4343GT 22.00m 700mm 60m 6,375ekW 243ekW 2,100kW 600kW 1,350kW 500kW 260kW