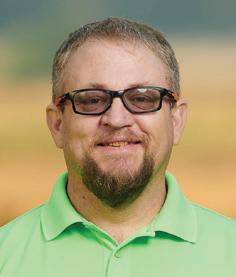
16 minute read
Plan for Concrete Slab Moisture Testing or Plan for Failure
FLOOR ED
Plan for Concrete Slab Moisture Testing or Plan for Failure
Advertisement
Excessive moisture in concrete remains a costly challenge for flooring installers. These costs are estimated to be nearly $1 billion each year in the United States alone due to moisture-related failure in commercial concrete flooring.¹ Many causes of moisture-related concrete flooring failure can be avoided or mitigated by properly testing the concrete’s moisture condition before installing the flooring.
Jason Spangler Wagner Meters’ Flooring Division Manager Jason Spangler, Wagner Meters’ Sales Manager, has more than 25 years’ experience in sales and sales management across a broad spectrum of industries. He has successfully launched a variety of products to the market, including the original Rapid RH® concrete moisture test. Jason, who received an MBA from West Texas A&M University in November 2018, has extensive industry involvement, including the National Wood Flooring Association (NWFA), the International Certified Flooring Installers Association (CFI), and is Vice Chairman of Associations for The Flooring Contractors Association (FCICA). Call Wagner Meters today at (844) 533-9100 and ask for Jason or www.wagnermeters.com.
Unfortunately, the defensive value in concrete moisture testing is often undermined due to indifferent or nonexistent test planning or poorly performed moisture testing. Poor planning or specifying can result in using a second-tier, unreliable testing method. The most scientifically validated and reliably accurate method of measuring moisture conditions in concrete is in situ relative humidity (RH) testing.
Improperly testing a slab’s moisture condition will similarly yield erroneous readings even if using an otherwise accurate test method. Consequently, RH testing must be done in compliance with ASTM F2170 (Standard Test Method for Determining Relative Humidity in Concrete Floor Slabs Using in situ Probes)² and must be done using a reliable RH testing system. The exact concrete moisture test method to be used may or may not be specified in the project documentation. Even so, failure to specify proper testing leaves everyone who

touched the concrete or the flooring vulnerable if a moisture-related flooring failure occurs. Ensuring that the ASTM F2170 testing standard and specific RH test to be used is specified in the project documentation is the most effective way to protect yourself and your team.
Concrete Slab Moisture Testing Options
● Calcium chloride (CaCl) testing ● In situ RH testing
As noted above, RH testing is the only scientifically validated method providing actionable, accurate readings that help flooring installers make informed choices about when to install flooring or take remediating steps. However, it’s instructive to review both common concrete slab moisture testing methods to understand how they work and what value they do or do not provide.
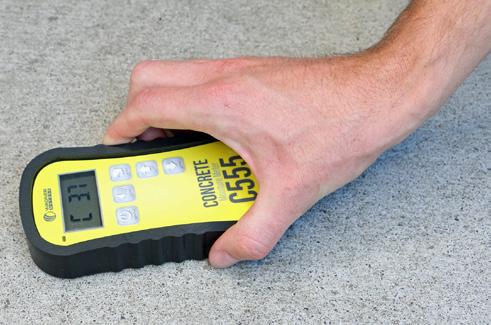
Concrete Moisture Meter and ASTM F2659
A concrete moisture meter is a useful tool to conduct an initial check of the relative moisture condition of areas on a slab. Used this way, it enhances the effectiveness of in situ RH testing, for reasons I’ll detail in the discussion on RH testing below.
However, moisture meters don’t provide quantitative moisture measurement at all. For this reason, a concrete moisture meter isn’t a tool that can assist you in making decisions about whether a slab is ready to have flooring installed upon it.
A concrete moisture meter takes a qualitative measure of a specific area on a slab relative to the slab’s overall moisture condition. It doesn’t provide a measure of the slab’s moisture condition, nor certainly, any reading that correlates to what the slab’s future moisture condition will be once sealed below the flooring.
A concrete moisture meter doesn’t provide a quantitative measure. Also, it is only reading the moisture conditions within the top one inch of the slab. Concrete’s moisture isn’t consistent throughout a slab, both because of how moisture moves through concrete and due to variations in concrete mix that could be found even within the same slab. Reading only the top layer in one spot on the slab can’t accurately measure the slab’s true moisture condition.
ASTM F2659 governs the standardized use of concrete moisture meters (Standard Guide for Preliminary Evaluation of
Comparative Moisture Condition of Concrete, Gypsum Cement and Other Floor Slabs and Screeds Using a Non-Destructive
Electronic Moisture Meter).³
The ASTM F2659 guidelines specifically state:
“This guide is not intended to provide quantitative results as a basis for acceptance of a floor for installation of moisture-sensitive flooring finishes systems. Test Methods F1869, F2170, or F2420 provide quantitative information for determining if moisture levels are within specific limits.”
ASTM F2170 refers to in situ RH testing, and ASTM F1869 pertains to calcium chloride (CaCl) testing. (ASTM F2420 governed certain uses of RH testing but was withdrawn in 2014.) I’ll go over ASTM F2170 and F1869 further down in this article. But ASTM made its point: electronic moisture meters shouldn’t be used to determine if the slab is ready for flooring installation.
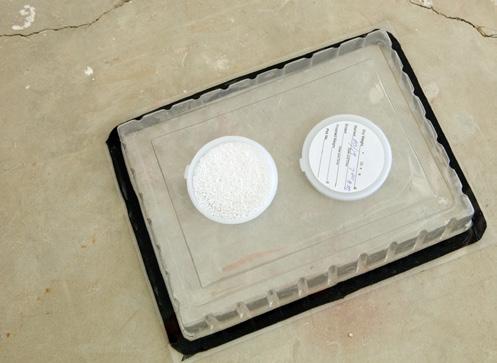
Calcium Chloride Test and ASTM F1869
The earliest documented reference we have to the calcium chloride test is from an Armstrong installation book on linoleum published in 1941. The installation book called it the “dampness test.” Flooring installers would place covered crystals on the slab and inspect them the next day to see if they looked like they’d absorbed any moisture.
In the 1960s, engineers decided to standardize how moisture measurements were determined using the CaCl test instead of relying on a visual assessment of how much moisture the crystals had absorbed. The formula devised used weight differentials in the crystals to calculate the moisture vapor evaporation rate (MVER) coming off the slab. Documentation from the 1960s often specified an MVER rate of two to three pounds, while many flooring manufacturers increased the acceptable MVER rate to five pounds by the 1990s.
The CaCl test was standardized in 1998 with the adoption of ASTM F1869 (Standard Test Method for Measuring Moisture
Vapor Emission Rate of Concrete Subfloor Using Anhydrous
Calcium Chloride).
According to ASTM F1869, the crystals need to get weighed before being placed on the slab and covered. The crystals should then be weighed 60 to 72 hours later to determine the slab’s MVER. Per F1869 guidelines, “quantity of moisture shall be expressed as the rate of moisture vapor emission, measured in pounds of moisture over a 1000 ft2 area…” Manufacturer instructions that reference ASTM F1869 specify what MVER rate range is acceptable for the flooring installation. Absent manufacturer instructions, the industry standard is three pounds. An update to ASTM F1869 prohibits the use of the CaCl test on gypsum-based or lightweight aggregate concrete.
Construction Technology Laboratories (CTL) Group conducted decade-long testing on the CaCl test to quantify how accurately the MVER standard reflected the moisture in concrete slabs. According to CTLGroup’s principal scientist, noted concrete expert Howard Kanare, the CaCl test “can be
unreliable; capable of producing both false high and low results.”
In one of the tests CTLGroup conducted, they measured four concrete slabs that had stabilized at 50% humidity for years. Following ASTM F1869 guidelines, the results of the CaCl tests returned MVER ranging between 2.5 – 4+ pounds. These results indicate that “The desiccant in the CaCl2 kit was
sucking out more moisture than was coming out of the concrete, giving a false-positive result.”
This was one of numerous tests, including laboratory and field testing, the CTLGroup conducted on the CaCl test, and the MVER measurement as a reliable indicator of moisture levels in concrete. According to Kanare, the CTLGroup outlined six reasons why MVER “suffers from serious deficiencies.”
1. No scientific basis existed for the standards when created; thus, MVER as a reliable measure of moisture has no quantitative foundation. 2. MVER kits themselves can’t be calibrated, making it impossible to determine accuracy. 3. The test only measures moisture content on the slab’s surface and provides no information about the slab’s moisture content below the surface. 4. CaCl testing doesn’t measure MVER accurately; both false positive and false negative readings are common. 5. Ambient conditions easily interfere with the results. This is one reason why CaCl testing often returns false positive or negative readings. The crystals will attract humidity out of the air, which then gets falsely attributed to moisture within the concrete.
The earliest documented reference we have to the calcium chloride test is from an Armstrong installation book on linoleum published in 1941. The installation book called it the “dampness test.” Flooring installers would place covered crystals on the slab and inspect them the next day to see if they looked like they’d absorbed any moisture.
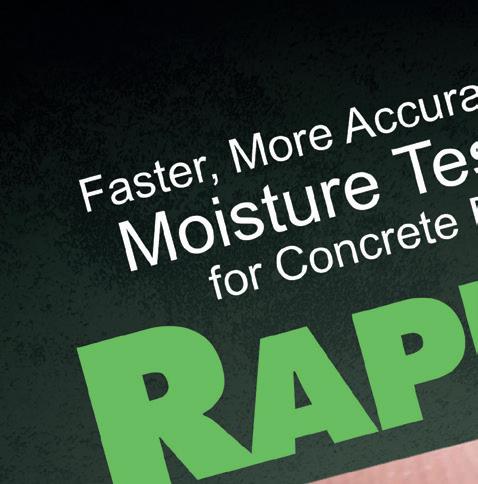




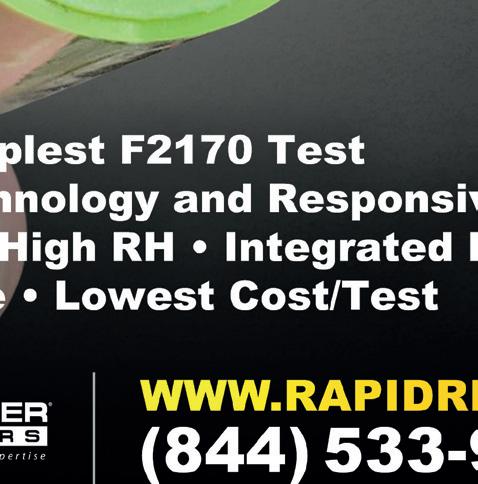
6. Certain limitations on MVER don’t account for the impact adhesives have on the flooring’s performance over the long run.
The third deficiency on this list that a CaCl test only measures surface moisture reflects that other research on moisture in concrete shows that moisture moves through concrete and doesn’t level out until the concrete slab is sealed. Consequently, measuring the moisture condition of a slab’s surface, even if done accurately, still doesn’t tell us anything useful about the moisture below the surface. And it’s any excess moisture below the surface that will move up and impact floor coverings that were installed too soon.
The other critical issue is that measuring surface moisture can have little correlation to the level of moisture that will remain in the slab after the flooring is installed over the concrete. After the flooring installation, no more moisture can evaporate. The remaining moisture will equilibrate throughout the slab. Thus, the amount of moisture left to equilibrate underneath a sealed floor has the greatest impact on whether the floor suffers moisture-related damage in the future. Any excess moisture that remains in the slab will rise without evaporating, carrying moisture vapor and chemicals that get trapped between the slab’s surface and the flooring. A reading that only reflects this at the point of time when the test was taken provides little useful predictive information about what the slab’s moisture condition will be once the floor is sealed.
The CaCl test continues to be used, despite its documented shortcomings. This may be due in part to the belief that CaCl testing is less expensive than RH testing. The cost of the CaCl test is less expensive than an RH test kit. However, CaCl testing is far more labor-intensive than RH testing. As a result, conducting CaCl testing has higher direct costs than RH testing and higher indirect costs due to its inefficient use of time and labor.
Another reason that CaCl continues to be used may also be because the CaCl has a longer field history than the RH test, which some may confuse with greater credibility. Many flooring product manufacturers continue to specify acceptable MVER rates for warranty coverage, giving the CaCl test a sheen of credibility.
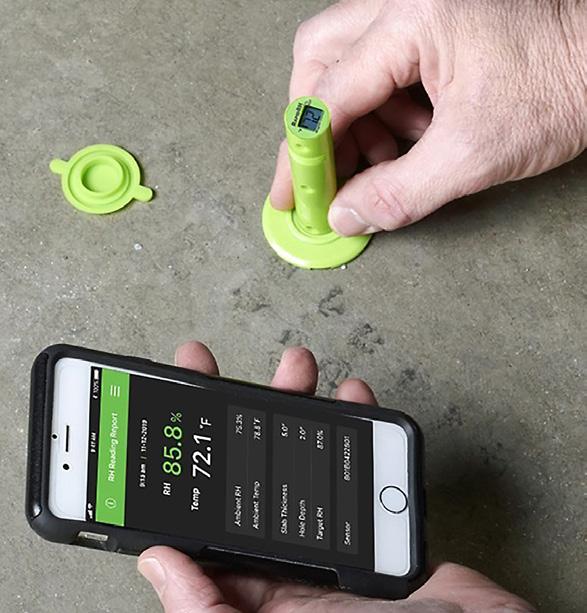
In Situ RH Test and ASTM F2170
The work from the Technical University of Lund in Sweden in the 1990s was critical in developing the in situ RH test method known today. These researchers looked at RH levels within the slab, and its relation to the slab’s EMC after the flooring is installed. They determined the precise slab depths at which an RH sensor needs to read the RH percentage reflecting the slab’s EMC once sealed. For concrete floor slabs poured on grade, the depth is 40%; for slabs drying from both sides, the proper depth for the in situ RH sensor is 20 percent. Unsur-
prisingly, the first industry associations to issue standards for in situ RH testing were in Sweden and Finland. These professional standards, colloquially called the “Nordtest,” were published in 1995. ASTM used the Nordtest as the basis for writing F2170, which was first approved in 2002.
The scope of scientific validation is a notable distinction in the contrasting histories of F1869 and F2170. The CaCl test and standardization were developed from anecdotal experience, with subsequent controlled testing revealing its weaknesses. The in situ RH was born and refined through scientific testing, and the field use standards then followed.
Continued scientific testing on the in situ RH method has improved our understanding of it, resulting in a recent update to F2170. The original F2170 standard required waiting 72 hours for the air in the concrete hole to equilibrate, and only then could an ASTM-compliant reading be taken. A precision and bias study, commissioned by ASTM and conducted by an independent laboratory in 2014, tested the efficacy of the 72-hour waiting period. The researchers took readings at multiple intervals before 72 hours to track the differential to the F2170 required 72-hour reading.
Through this process, the researchers uncovered that readings taken at the 24-hour mark were statistically equivalent to those taken at the 72-hour mark. Any occasional deviations found between the two readings were consistently and sufficiently minor to have no statistical impact. All of this is to say that the 24-hour reading was functionally identical to the 72-hour reading, making the 72-hour reading requirement moot. As a result of this research, ASTM updated the F2170 standard to allow ASTM-compliant readings to be taken 24 hours after the sensor is inserted into the hole. With the revised standard, in situ RH testing method is now the fastest concrete moisture test method available, as users of F1869 must still wait at least 60 hours before taking a standard-compliant reading.
The most significant distinction between the in situ RH and CaCl test methods is what they’re testing. As noted above, one of the most serious deficiencies of the CaCl test is that it only measures surface moisture, while it’s the moisture condition below the surface that’s most telling. Only an in situ RH sensor measures the RH and temperature within the concrete slab, making it the only test method that can accurately tell us anything about the future moisture condition of the concrete once the flooring is installed. The work from the Technical University of Lund in Sweden in the 1990s was critical in developing the in situ RH test method known today. These researchers looked at RH levels within the slab, and its relation to the slab’s EMC after the flooring is installed.
The science behind in situ RH testing also ensures that RH test kits can be calibrated according to traceable national standards. The lack of ability to calibrate the tools measuring MVER as part of a CaCl test was one of the test’s main weaknesses, as outlined by Kanare in the CTLGroup research. Without calibration, it’s impossible to verify that the testing equipment is returning an accurate reading.
In Situ RH Testing: The Most Accurate and Easiest Testing Method
It’s not always that we get the happy coincidence that the most effective and reliable option is also the easiest and fastest option. When it comes to concrete moisture testing, that is exactly the case.
First of all, it’s worth emphasizing that the newest scientific research into in situ RH testing resulted in ASTM revising the F2170 standard to require only a 24-hour waiting period. F1869 still requires a minimum of 60 hours before you can take actionable moisture readings. In addition, you can find in situ RH test kits that simplify the installation and data collection ends of in situ RH testing, speeding up the entire concrete moisture measuring timeline within a project. For example, there are easy to install in situ RH sensors, like the ones that are part of Wagner Meters’ Rapid RH® L6 concrete moisture measurement system. Unlike CaCl tests, which require a lot of set up to ensure the seal over the crystals is well-secured, in situ RH sensors install in minutes. All it requires is drilling a simple hole, cleaning it out, and inserting the RH sensor. The Rapid RH L6 system also includes various optional accessories and free mobile apps that streamline or automate the data collection and F2170 reporting processes. Enhanced data collection accelerates the schedule and provides a quantitative foundation for better understanding the drying process of a specific slab through trend analysis graphs.
F2170 stipulates a certain number of sensors be installed based on the square footage of the slab, including specifying places where some sensors must be placed. A concrete moisture meter is helpful as a targeting device that can find trouble spots within a test location to ensure they get the attention they deserve. Look for a moisture meter that gets below the surface, like Wagner Meters’ C555 pinless concrete moisture meter that reads ¾” into the slab. It returns a reading showing the spot’s comparative moisture condition, which helps identify where the slab retains the most moisture.
Ensuring Project Documentation Specifies the Right Concrete Moisture Test
While in situ RH testing is the more reliable and faster moisture test, the CaCl test still has its adherents. General contractors or flooring installers usually default to whatever test they’re most comfortable using, even if it’s not the best test to use. Nobody on a project wants to waste time after the slab has been poured arguing about which concrete moisture test to use.
The time to insist on using an F2170-compliant in situ RH test is when the project is getting specified. Doing your due diligence to validate the enhanced utility of in situ RH testing and specifying the most effective RH testing system according to your criteria for the project is a foolproof way of bringing down your stress levels — at least as it pertains to concrete moisture testing. To learn more about Wagner’s comprehensive Rapid RH L6 system, including its extensive array of data logging tools, visit wagnermeters.com or call (844) 533-9100. ❚
Resources:
1. IFTI Solutions/ Flooring Failures. (n.d.). Retrieved from Independent Floor Testing & Inspection (IFTI) https://ifti.com/solutions/flooring-failures/
2. ASTM F2170 — 19a Standard Test Method for Determining Relative Humidity in Concrete Floor Slabs Using in situ Probes https://www.astm.org/Standards/F2170.htm
3. ASTM F2659 — 10(2015) Standard Guide for Preliminary Evaluation of Comparative
Moisture Condition of Concrete, Gypsum Cement and Other Floor Slabs and Screeds
Using a Non-Destructive Electronic Moisture Meter
https://www.astm.org/Standards/F2659.htm
4. ASTM F1869 — 16a Standard Test Method for Measuring Moisture Vapor
Emission Rate of Concrete Subfloor Using Anhydrous Calcium Chloride
https://www.astm.org/Standards/F1869.htm
5. SLABS ON GRADE CONCRETE FLOOR MOISTURE TESTS https://www.concrete
construction.net/products/decorative-concrete-surfaces/concrete-floor-moisture-tests_o
6. Moisture measurement in concrete floor slabs https://www.constructionspecifier.com/mois-
ture-measurement-in-concrete-floor-slabs/2/
7. Rapid RH L6 Concrete Moisture Test https://www.wagnermeters.com/rapid-rh-l6/
While in situ RH testing is the more reliable and faster moisture test, the CaCl test still has its adherents. General contractors or flooring installers usually default to whatever test they’re most comfortable using, even if it’s not the best test to use. Nobody on a project wants to waste time after the slab has been poured arguing about which concrete moisture test to use.