

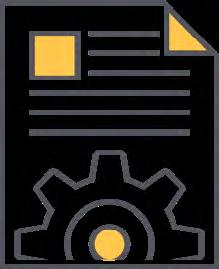
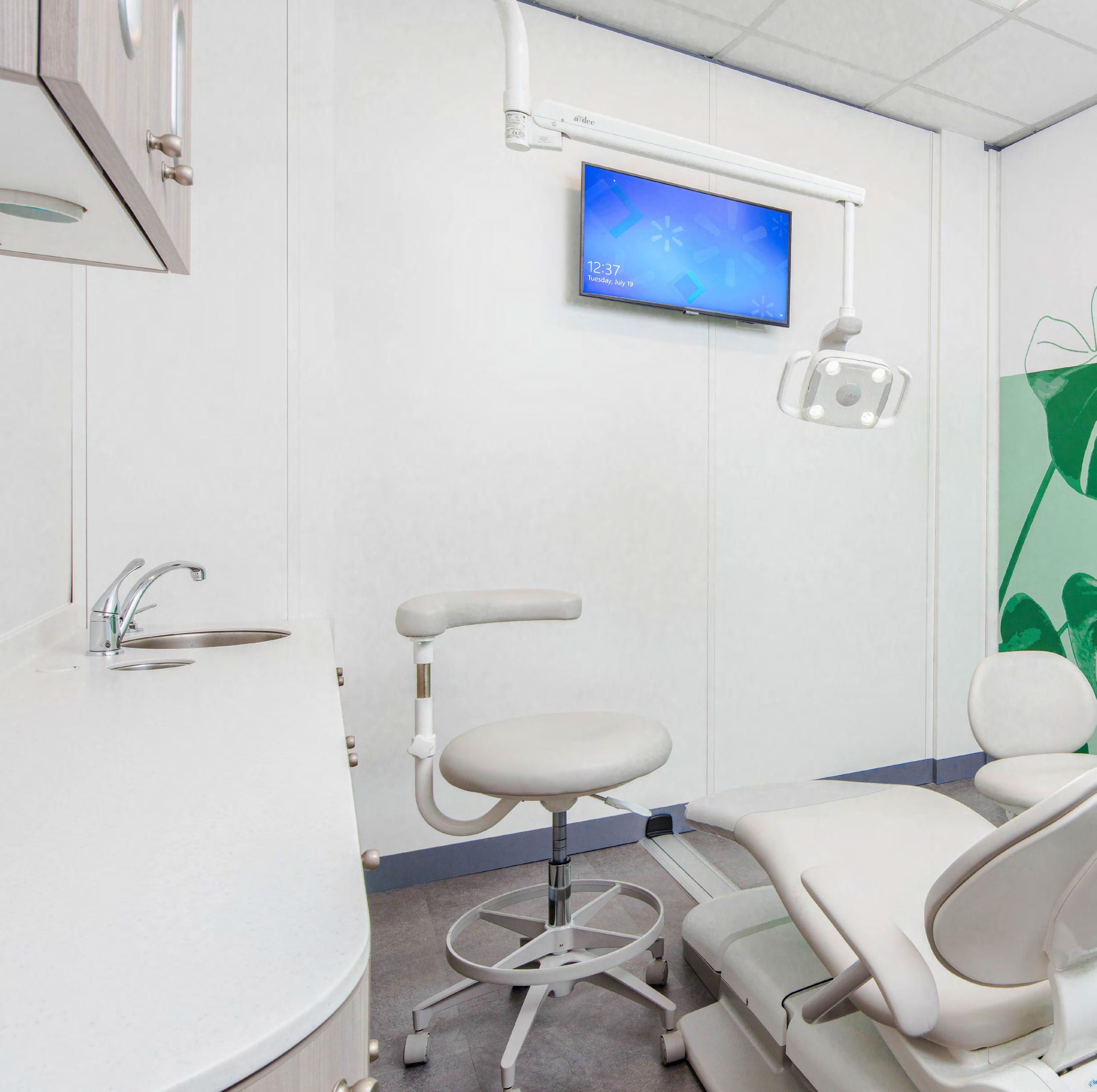
At Massa Manufacturing and Assembly (MMA), we understand that reconfiguring current space can be both costly and timeconsuming. Organizational needs, market pressures, and industry regulations, coupled with site limitations can present new and unique challenges. Space that is antiquated, ineffectively designed or under-utilized can affect key performance indicators such as quality, safety, employee engagement and customer satisfaction, which impacts an organization’s financial success. Our solution affords clients with buildings, structures, and interior desings that provide optimal solutions in the built environment with reduced capital expenditure (CAPEX) complexity and production costs.
By employing an Integrated Project Delivery system (IPD) utilizing Design for Manufacturing & Assembly (DfMA) with Modular Panels, MMA generates efficiencies throughout all phases of the design, fabrication, and construction process. Every aspect of the project from entitlements and permits, to design, manufacturing, sourcing, and assembly is skillfully managed, getting projects to market quicker.
MMA employs an Integrated Project Delivery System (IPD) utilizing Design for Manufacturing and Assembly with prefabricated, modular components including clinical walls, building systems, HVAC, lead shielding, magnet technology, vacuum plumbing systems, and any other innovation the job requires. Our streamlined approach offers measurable goals and quantifiable outcomes that address space complexity, create build consistency, and enhance speed to market.
MMA are the architects behind inbox health clinics nationwide. We are not only the designers; we are the manufacturers, assemblers, builders, and sourcing team for every component and system of the project. The prefabrication, modularization and standardization of construction processes and assets within factory-controlled environments, supported by DfMA techniques, offers a viable solution to traditional build challenges. By presenting transformative improvements across the asset lifecycle in time, cost, quality, health, and safety, off-site construction offers predictability, accuracy, and consistency.
Traditional Design Bid-Build often results in construction deliverables that lack build consistency, as various contractors manage means and methods, resulting in finish and quality inconsistencies from box to box. At a time when our industry is facing a skills shortage, taking the build off site to a factory-controlled environment reduces the levels of resources required and removes the dependency on traditional construction skills.
MMA identified this opportunity early on and devised an improved construction methodology focusing on IPD utilizing DfMA and modular panels. Design solutions “assembled” onsite rather than “constructed” on-site offers the prospect of using fewer people in a more controlled and safer environment.
IPD is a construction project delivery method that combines ideas from integrated practice and lean construction processes. It seeks efficiency and involvement from all participants (people, systems, business structures and practices) through all phases of design, fabrication, and construction. IPD reduces CAPEX complexity by simplifying key processes with a unified project execution approach, allowing the client to better manage CAPEX risk.
DfMA is used as the foundation for concurrent engineering processes to simplify and fully optimize the structure wherever possible, to reduce manufacturing and assembly costs and to quantify improvements. By facilitating greater off-site manufacturing and vastly reducing on-site construction, buildings are constructed with higher levels of speed and safety. This process delivers both resource and cost efficiencies, and does not impede creative design, inspiration, or compromise on quality.
Our IPD approach involves all key stakeholders at the early planning stages of the project, including owners, architects, contractors, suppliers, and consultants. This approach aims to optimize project outcomes holistically by emphasizing mutual goals, risk-sharing, and open communication.
Our DfMA Documentary showcases our collaborative IPD bandwidth nationwide, and highlights some of our various team members from Trane, Accorn, CED, KI, USEI, Miller Knoll, and Harrington Casework.
IPD often requires more time upfront for thorough planning and collaboration, which generates smoother execution and fewer unexpected delays during construction. Changes and adjustments can be deliberated and implemented earlier in the process, therefor minimizing disruptions as the project progresses, resulting in a well-organized, clean, safe, and more efficient work environment that produces minimal waste.
The timelapse video from a Jacksonville, Florida project displays how our crews methodically assemble a health clinic, using scissor lifts and screw guns. It is an impressive quantity of work completed in such a short amount of time.
Our most recent project is a 6500 square foot health clinic assembled in eleven weeks, allowing the client to open for business in record time. Our work included initial design, documentation, permitting, assembly, installing all FF&E, obtaining all required regulatory approvals, including physicist certifications and proper shielding for radiological diagnostics. The client’s compliance team was extremely satisfied with the outcome, as we exceeded their stringent construction compliance requirements, and they were thoroughly impressed with how clean and safe the project site was maintained …. Basically, dust free.
To view the time lapse video of this healthcare project, along with an animated process of systems installation installed in field. (DfMA Timelapse)
The IPD approach fosters teamwork and requires meticulous communication, coordination and collaboration amongst the project participants and end users. Each discipline works together to address project complexities and are accountable for their contributions to the project outcome.
Benefits of this approach include dramatically decreasing risks, ensuring projects can be delivered on time, allaying budget concerns, and improving overall quality.
Documentation of mock-ups should seriously be considered for the continued development of the program. Crossfunctional feedback from- Merchandising, Operations, Strategy, Marketing, IT, and Loss Prevention, is crucial to the success of this program.
Development of Merchandising Presentation Strategy & Program Requirements with a primary focus on Documentation of the following:
Hierarchy of product presentationincluding an outline of selection hierarchy.
Capacity analysis - Collection sizes & variables.
Documentation & assessment of current tools to determine final program requirements.
We are now designing, assembling and building pharmacies, 100,000 square foot central prescription, mail order, and specialty prescription fulfillment facilities, as well as projects in optometry, vision, and branding programs nationwide. MMA developed a premanufactured brand prototype, allowing for several hundred linear feet of branding work to be completed within one to three days at each site.
The work was done during non-operational store hours so as not to impact store operations.
MMA can refurbish existing locations and bring your new ventures to market quickly.
For example, we successfully designed and built a 35,000 square foot clinic from the ceiling grid to the floor in twelve days. This included all walls, finished floors, electrical, plumbing, casework, furnishings, and medical equipment.
Our walls are prefinished 22 gauge steel with sound attenuation and all required blocking.
Our pre-built walls are fully unitized, with all utilities (plumbing, electrical, etc.) in place.
Easy to assemble and disassemble.
95% cut to fit in the factory, only posts and trim are cut on-site, reducing mess, noise, and disruption.
Custom color matching is available to incorporate client branding.
Dedicated Installation manager/ project management. International factory-certified installation network.
Installation costs are “turnkey” and all-inclusive.
To code fire suppression integration.
Our collective team includes a furniture company and a door company.
MMA, in association with our nationallybased structural team, our ceiling manufacturer, and our wall manufacturer’s structural engineering team have collectively developed a method of utilizing a clipping system that is secured to the ceiling grid and two perimeter walls excluding the necessity to have the walls to be braced to the deck.
This method maximizes ease of construction, cost containment, and accelerates speed to market.
Our prefabricated, demountable walls offer substantial advantages over traditional construction because they are considered furniture. This classification allows for less rigorous permitting requirements and accelerated depreciation, resulting in immediate savings to an organization in both time and dollars.
The modular company we partner with is employee-owned with 2500 employees worldwide, inclusive of the facility technicians who have an average tenure of fifteen years.
The facility in Manitowoc, Wisconsin is 225,000 square feet and has the capacity to manufacture 1600 panels a week, with full fabrication, paint and assembly capabilities.
The factory uses cellular manufacturing and can easily scale up based on product demand and has an 80,000 square foot warehouse to store raw materials and finished goods.
MMA, in collaboration with our collective team members, focuses on a Manufactured Structured Scheduling System.
Our objective is:
To transform our project sites to a factory floor.
To develop a structured schedule for every vendor.
To ensure that all vendors complete their required work within our designated time frames.
To instill a “consistent pattern of behavior” mindset in our installers.
Production schedules are more important than ever before, especially considering the increased sophistication in manufacturing methods and the software necessary to manage production in a more precise manner, while also accounting for the increased complexity of global supply chains. Utilizing our well-defined production schedule that is based on accurate data inputs, our production schedules can be changed and adjusted to address temporary shifts in production requirements caused by seasonality, rapidly evolving consumer preferences, and other disruptions.
The basic components of Production Scheduling include Planning, Routing, Scheduling, Dispatching, and Execution.
Utilizes the established planning level to produce goods from components or raw materials. It is time-based and must satisfy the demand established at the planning level. These timetables can be department-specific, product specific, and process-specific. Master production schedules are used at the highest level, defining the product timeframes, while sub-schedules may be department specific for subassemblies or for mixes and blends.
In production scheduling, the role of planning is to utilize the company’s resources to maintain consistency, reduce downtime and mitigate bottlenecks to optimize production.
In discreet manufacturing, final products are made from a lengthy and complex series of sub-processes. A bill of materials may be used to dictate what items are required and in what quantity.
Routing maps out the flow of required process steps and dictates the path and sequence of performed operations. Including steps that must be done in-house and those components that may need to be sub-contracted and then returned to the production flow for final assembly.
Production scheduling must rely on proper execution to ensure that all processes are performed correctly and in the order they are intended to be produced and installed in the field. This requires that everyone knows what they are supposed to do and when they are supposed to do it. Execution involves informed management decisions, trained staff, accurate data as inputs into the production plan, a manufactured structured schedule, reliable sales figures and forecast numbers. All must be present for the organization to execute its production schedule and complete orders.
Is the process of assigning the sequence of jobs to be completed from a sub-set of jobs in the production queue. Dispatching is used to make decisions for immediate action, in comparison to planning where decisions are determined for future actions. Dispatching is used in both pull and push production systems. In a push system, production dictates how much of the product will be “pushed” to the market, while in a pull system current demand “pulls” the goods thereby determining when and how much to produce.
The Vacuum plumbing systems we utilize are simple and viable alternatives to underground piping, as noted in the latest edition of the IPC and UPC Codes. Vacuum plumbing systems use the combined energies of vacuum pressure and gravity for the collection, conveyance, and disposal of waste through a piping network that can be routed above ground.
Vacuum toilet drainage operates on the principle of having most of the plumbing system under a continuous vacuum. Vacuum drainage systems are ventless, with one or two roof penetrations and a single connection to an existing sanitary line. Many local and state plumbing codes have also accepted vacuum plumbing as an approved alternative for a variety of waste types including condensate, grey water, sanitary waste, and grease waste.
Why is Vacuum Plumbing the environmental choice? A typical vacuum system can reduce potable water consumption for toilets by 68%, with a highly efficient vacuum toilet requiring only a half-gallon per flush. Of the many benefits vacuum plumbing offers, the water and waste treatment savings are one of the most important features of this technology. The savings can be thousands of dollars and millions of gallons of water per year for larger applications. A fivehundred-person commercial office building that is serviced by a single vacuum center and half gallon per flush vacuum toilets will save over 265,000 gallons of water per year, compared to conventional low-flush toilets.
Vacuum plumbing systems can be used on virtually any project, and certain design and construction conditions make it the most cost-effective solution available. Vacuum plumbing is especially beneficial in multiple-level environments because it eliminates the need for floor penetration above and below. Vacuum plumbing avoids the need to trench concrete slabs, allowing us to keep mess and noise at a minimum, reduce overall disruption, and impact speed to market.
Magnets have been used for thousands of years by many cultures throughout the world, often for therapeutic purposes. Today magnets are incorporated in industrial machinery, consumer products, computers, and even transportation. Industrial Magnets are used in auto manufacturing and aerial manufacturing industries to hold and transport large metal components. Electromagnets are used in industrial conveyor systems, and by cranes to pick up and drop heavy loads.
We utilize magnet technology as part of our health clinic designs as magnets offer increased adaptability and flexibility to the end user. The steel surfaces of our walls allow everything a health space requires, including monitors, workstations, inter-diagnostic panels, lead apron racks, sharps containers, gloves, and paper towel holders, etc., to be mounted via magnets specifically designed to hold the corresponding weight.
When there is a need to repurpose a room or adjust equipment to meet regulatory codes, there is no need to drill into the walls. Our innovative magnet technology is strong and safe and allows for the design, branding, or function of a room to be changed easily by just adding or removing the necessary items. No mess, no holes, no hassle.
For health care projects, MMA utilizes sound attenuation materials in conjunction with our wall system’s Sound Transmission Class (STC) rating, air exchange grilles in the ceilings, and sound masking systems to address patient privacy, HIPAA compliance regulations and health facility accreditation standards.
Sound attenuation materials are used to reduce the transmission of sound between two spaces. These materials are especially useful in healthcare facilities where patient privacy is critical. There are several types of sound attenuation materials, including sound barriers, sound-absorbing materials, and sound isolation products. These materials work by absorbing, reflecting, or diffusing sound waves. To maximize patient privacy, we utilize 1-3/4 inch think ceiling tiles and lay insulation over them for additional noise absorption.
There are a variety of sounds present in clinical settings including those from individualized discussions, patient/ clinician interactions, medical equipment, rolling carts, HVAC systems and other sources. These sounds can be irritating and disruptive at times, particularly to those patients with certain medical conditions, which can be exacerbated by hearing issues, medication intake, preexisting fears and anxieties and age.
Acoustics in healthcare environments are complex and require a careful, strategic design. Specific acoustical considerations in healthcare settings include supporting patient well-being and privacy; supporting communication among staff; and meeting standards and regulations of Health Insurance Portability and Accountability Act of 1996 (HIPAA). Evidence Based Design acknowledges acoustical control as a key component in healthcare design. In this Calhoun facility, acoustical control was an essential necessity. Numerous steps were taken to control sound levels and transmission. Maintaining patient privacy was our highest concern. The following are some of the targeted mitigation measures implemented into our facility.
1. Vulcanized Composition Rubber Underlayment: Flooring is an especially important design element within the healthcare environment. Not only is it necessarily found in all spaces, but the type of flooring specified greatly influences the outcome of each space. ECO Silence Underlayment made from Vulcanized Composition Rubber (recycled tires) is an underlayment designed to exceed IIC requirements while maintaining a low profile. Our 2mm underlayment can achieve Delta IIC ratings up to 25dB and IIC ratings up to 72 dB. Rubber underlayment not only provides acoustical properties it adds additional cushion underfoot. Caregiver staff spends most of their workday on their feet and this reduces leg and back fatigue.
2. Interior solid core doors with high pressure laminate, HPL is considered to be one of the most durable decorative surface materials in the healthcare industry. All doors have acoustic sound seals to block sounds from entering or exiting the rooms.
3. The above-door transfer grille simply has two grilles located above the door between the room and common space, one on each wall, with offset baffles to limit sound transmission.
4. Rooftop HVAC units are high SEER units with lower fan speed to mitigate noise transmission
5. Sound Masking in Healthcare Clinics: It was essential to install a state-of-the-art Sound Masking System in our clinic. Our primary focus is to provide our patients’ right to speech privacy, as well as the physical and psychological effects of noise on patients and caregivers. Studies have shown that noise creates distractions in the healthcare environment that can impact safety, negatively affect health and mood, decrease staff productivity, and increase medical error rates. Sound masking is one part of a proactive approach to ensure patients have privacy and comfort, while also providing medical staff with an optimal work environment.
6. Lay-in ceiling with sound attenuation providing a CAC value of 42. Typical throughout
Air exchange grilles can also play a role in addressing HIPAA compliance. These grilles are installed in ceilings and allow for the exchange of air between rooms while preventing sound transmission. The grilles are designed to be acoustically transparent, which means that sound waves can pass through them without being amplified or distorted. This allows for the free flow of air while maintaining patient privacy.
The wall system is modular and specifically designed for healthcare environments. With an STC rating range of 44-48, it can reduce sound between rooms, making speech unintelligible to protect patient privacy. This is a significant improvement over traditional drywall, which typically has an STC rating of 35. The wall system achieves this high STC rating by using a combination of sound-absorbing materials and sound-blocking techniques.
Sound masking systems are used to help address HIPAA issues in healthcare facilities and are especially useful in open-plan healthcare environments, such as waiting rooms or shared workspaces, where conversations are more likely to be overheard. These systems use a lowlevel background sound to mask or “drown out” conversations and other ambient noise, making it more difficult to overhear Protected Health Information (PHI). Sound masking systems can be customized to suit the specific needs of a healthcare project and can be integrated with our other sound attenuation materials, such as the wall system, for maximum effectiveness.
For health clinic builds, we exclusively use Plug & Play technology, as opposed to hardwiring. The electrical wiring in our modular walls only requires a junction box in the ceiling for modular installers to easily daisy chain power to the harness in the ceiling for instant power. Each light fixture quickly connects to another with a connector, which ensures that there are no failures and maintains compliance with all applicable codes and UL ratings.
Utilizing Plug & Play technology reduces installation time and the inspections and permits required, and decreases associated labor and product costs that would be found using traditional electrical applications. Plug & Play technology saves time and money when compared to conventional lighting installations and electrical power.
We consider our products 100% reusable, truly a great environmental story. There is zero waste diverted to a landfill and there are no costs associated with disposal. In fact, if there are any recyclables to discard, MMA will give those to the client to capture the recycling refunds.
“MMA’s environmental commitment is consistent with LEED philosophy and Green Construction processes”
By applying IPD and DfMA techniques to design and build, our forward-thinking mindset supports the realization that buildings no longer need to be constructed in the traditional sense. Our firm’s innovations take shape by embracing similar manufacturing and assembly methods to those successfully utilized by the aerospace and automotive industries.
Our collective team can manufacture parts as needed and have them ready to go as projects evolve. Our method of using unitized wall systems and modular components, supported by new off-site manufacturing technology and semiautomated assembly production allows our projects to be delivered to our clients faster, ultimately lowering costs, and improving quality and sustainability.