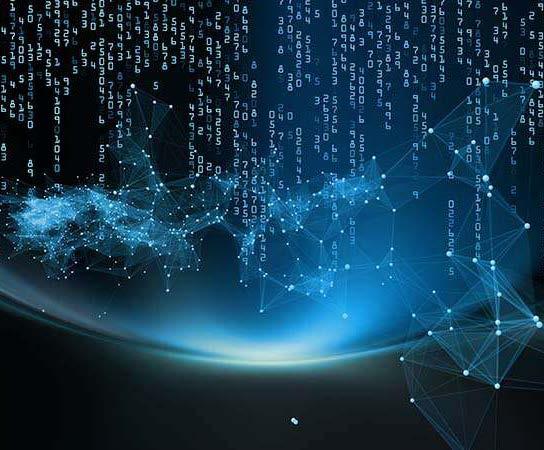
5 minute read
Why Your Material Analyser Won’t Keep You Awake at Night - But the Data Will
Source: Hitachi High-Tech Analytical Science
We’re seeing a rise in the use of material analysers as part of factory automation, whether raw material testing, in-line testing or IIOT (Industrial Internet of Things). This has been accelerated as the issue of aging global population and reduced workforce, especially as manual labour (blue collar workers), becomes a challenge for many businesses with vacancies being hard to fill. What many don’t necessarily realise is that material analysers are being developed to provide a solution to new customer demands to deliver more efficient, automated, and cleaner production and development processes. Often the data has been stored on the instruments themselves without providing wider visibility of the analysis data which can highlight issues with raw materials, product quality or processes. Today, many material analysers come with connectivity enabled already. It’s just that many aren’t taking advantage of the features available already to increase yield let alone realise what the future could look like.
Why your material analyser won’t keep you awake at night - but the data will
Automation Isn’t New
Automation has worked for years in industrial manufacturing but ensuring products meet specification, quality and throughput has until now required employee intervention. But as markets change, so does technology. 5G, multisite operations and remote/hybrid working are becoming the norm, and proactive remote interventions are becoming more accepted. Material analysers also need to adapt to changing circumstances. The idea of a fully integrated, connected, and flexible analysis equipment, that feeds smart factories with a constant stream of data is coming and is much closer than you may think. This data provides valuable information to your most precious resource, your workforce, enabling them to make the right decisions at the right time.
Why Data Matters
One of my favourite questions to ask customers when I visit them is what do you do with the data your analyser collects? We’re living in an age where we need to utilise massive amounts of data from around the world to create new value as many businesses renovate themselves with digital technologies. The analyser, whether XRF, LIBS, OES or TA, is just a means to getting a job done. But what the analyser does is it provides a constant stream of data. Valuable data. And we know data is power. You might not be aware, but we’ve had data enabled products since 2014. You can get data from the shop floor or in-field without stopping production. You can build your analysis inline or into automation. And with the data that your material analysers provide, you can reduce wastage and costs and improve production yield, throughput and crucially, your bottom line. In the near future all our instruments will be connected to ExTOPE Connect, our advanced data management solution in the cloud, with our handheld XRF and LIBS, OES and LAB-X5000 benchtop XRF analyser currently having this capability. But that’s not everything.
What is Lumada?
You may hear us talk more and more about Lumada. Coined from the words “illuminate” and “data”, the name Lumada embodies our goal of helping businesses shine a light on their data and illuminating the information it provides in such a way that we can extract new insights, thereby resolving our customers’ business issues and contributing to their growth. We’re here to help our customers in their digital transformation for a better, cleaner society. By capturing changes in the world through data,
we’re able to create new value by combining the ability to act flexibly with proven on-site knowledge to optimise manufacturing processes and storage inventory for example.
Shaping the Future Together
We’re already seeing an increased number of customers with requirements around data management and analysis. This previously was exclusive to large multinational companies, but we’re now seeing medium to small companies incorporating this into their process too. Our position is to make this capability accessible to all customers.
Ultimately, through the data our analysers are able to provide to you, we want to help to decrease failure rates, how much money is being wasted in manufacturing process, how much additional stock is sitting on shelves, and wasted energy, material and labor due to product re-work. By providing world class material analysis solutions that are digitally enabled and embedded into your business, we want to enable our customers to make fast, accurate decisions during their production process whether they be from raw material sourcing to end of life disposal and recycling. And the key to this all, is the data from your material analyser.
About Hitachi High-Tech Analytical Science
The Hitachi High-Tech range of X-ray, laser and optical emission spectrometer analysers provide superior analysis for incoming inspection, factory floor process control and NDT for final inspection to provide you with cutting-edge solutions. Their range includes: XRF (X-ray Fluorescence) is available in both benchtop and handheld formats, is ideal for measuring a wide range of elements and concentrations in many different materials, including metal alloys. XRF technology utilises an X-ray tube to induce a response from the atoms in the tested sample. This technique is ideal when you need low limits of detection for accurate grade separation. OES (Optical Emission Spectroscopy) is available in mobile and stationary formats. OES can analyse all the key elements at low limits of detection, like phosphorous, sulphur, boron – and carbon, starting with a detection limit of 30ppm. Compared to handheld XRF, the OES technique requires more sample preparation and a small but visible burn spot is left on the surface. LIBS (Laser Induced Breakdown Spectroscopy) is a fast, handheld format, ideal for the identification of different types of alloys. With a LIBS analyser, there are no X-rays as it uses a focused laser pulse to hit the sample surface, removing a very small amount of material for analysis. This means the LIBS burn mark is so small that it can often be used for finished goods.
100% Positive Material Identification
The Hitachi High-Tech range of metals analysers and technologies ensures: • Rapid, reliable material verification, even in the most demanding quality assurance and control applications • Meeting of standards, avoiding potentially devastating results for your customers, your company and even your reputation • Avoidance of costly reworks through incoming inspection of alloy material before the production phase • Avoidance of costly recalls by confirming chemical composition and material verification prior to shipment • Production lines kept running at optimum efficiency • Access to powerful data management and reporting
Read the metal. Reveal the quality.
Hitachi’s range of materials analyzers support the end-to-end metals production process from incoming inspection to final product assembly and finished goods testing to ensure product reliability, safety and regulatory compliance.
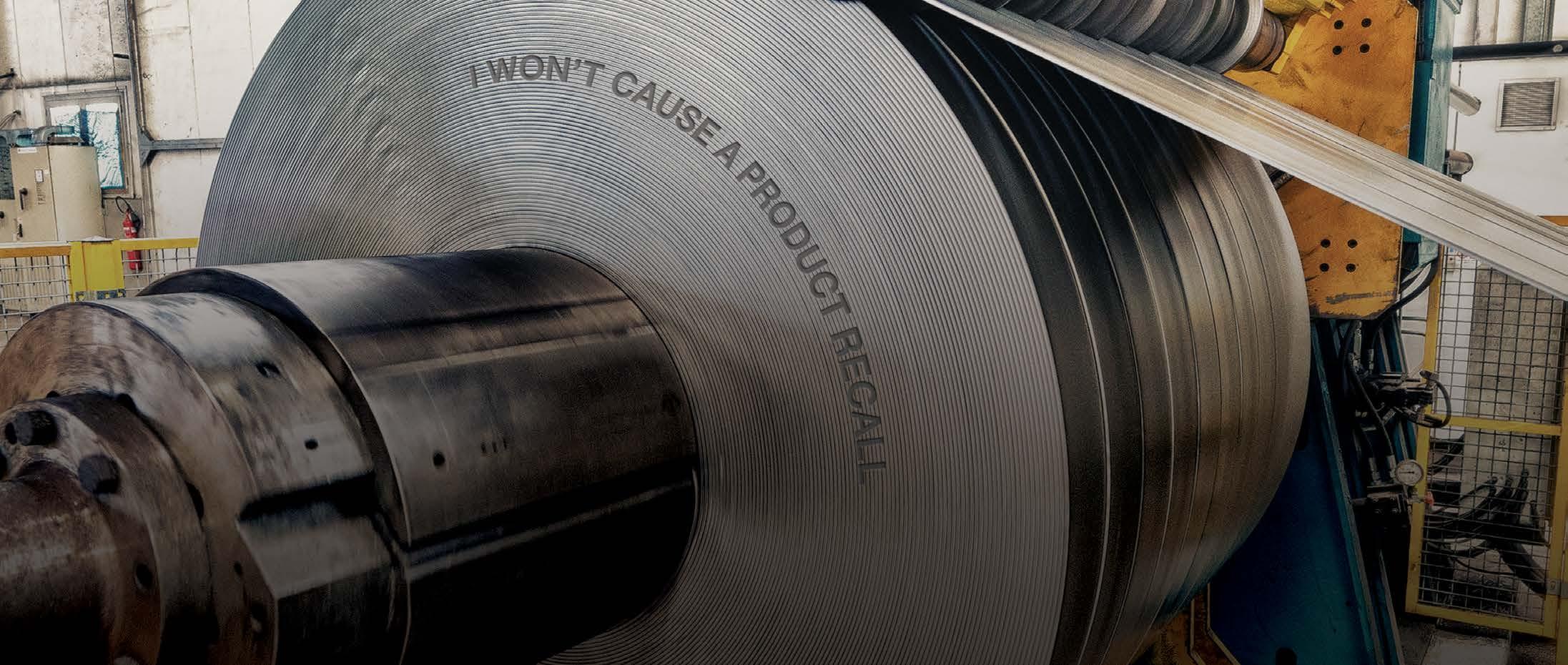
See the full range at: hhtas.net/read-the-metal
X-MET8000 - XRF VULCAN - LIBS MOBILE AND STATIONARY OES
Complete metals analysis you can count on.