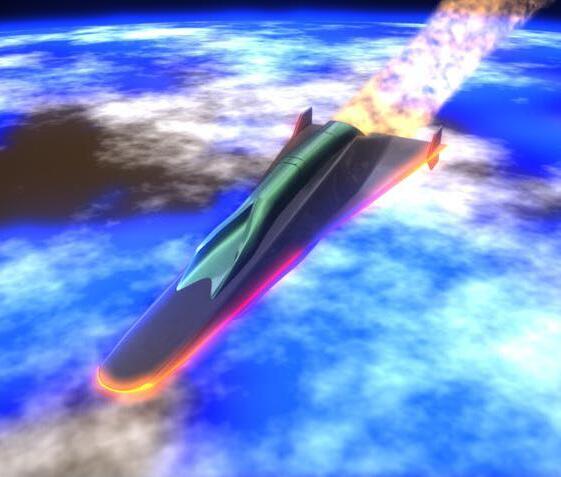
4 minute read
Queensland-Designed Rocket System Boosts Australian Space Industry
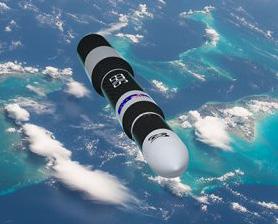
Source: Sally Wood
The University of Queensland has had hypersonic flight in its sights for over a decade.
Researchers, scientists, students and industry professionals work together to develop new technologies for the next generation of Australia’s defence sector. For example, Queensland is the home of development for a hybrid rocket, which has launched small satellites into low-Earth orbits.
Dr Ingo Jahn worked with the Gold Coast-based Gilmour Space on propellant feed systems and cycles for launch vehicles in space.
He said having researchers and industry work closely together was invaluable for Australia’s space industry.
“Rather than buying products from overseas, the rockets and components will be manufactured in Australia, and this is an essential step towards developing a space launch vehicle industry in Queensland with many expected flow-down benefits to our manufacturing industries.”
The University of Queensland team have focussed on developing and validating the fuel feed system, which must meet the stringent control and performance requirements of the launch system, while also remaining as light as possible.
“Fuel delivery systems for rockets are one of the most complex engineering challenges,” Dr Jahn said.
“They are located at the intersection of multiple systems; to stay light they have to be incredibly power dense, they must operate across wide temperature and pressure ranges and they are safety critical.”
“Finding effective and safe engineering solutions to meet all these requirements, while remaining light weight is the challenge we have to overcome,” he explained.
Meanwhile, Gilmour Space is at the forefront of development for nextgeneration hybrid rocket technologies that are safer and more cost-effective than traditional chemical-propulsion rockets.
Chief Operating Officer and company co-founder James Gilmour said the pandemic sparked a busy period for the group as it developed and tested the various rocket systems in the orbital launch vehicle.
“We’re grateful to UQ and the government for supporting our efforts to grow a space launch industry here in Queensland,” Mr Gilmour said. Similarly, Dr Jahn said the partnership is an excellent opportunity, which combines know-how and fundamental research.
“Seeing your research adopted into a product is the dream of every researcher and engineer—what could be better than seeing your research fly to the stars?”
Making Bold Strides In Space
The University of Queensland has been at the forefront of hypersonic development since 2012, when the iconic SCRAMSPACE project passed its critical design review.
SCRAMSPACE is a free-flying hypersonic scramjet, which has the capacity to reach 8600km/h.
It became the first and largest project funded by the Australian Space Research Program.
“A scramjet is an airbreathing engine for hypersonic craft that travel at many times the speed of sound, for high speed transport in Earth’s atmosphere or along trajectories to space, said Professor Russell Boyce.
"They improve the efficiency and reliability and reduce the cost of inserting satellites into orbit,” he added.
The program was supported by a $14 million international consortium of partners in five countries, and led by The University of Queensland’s Centre for Hypersonics.
Research for this project was conducted at the University of Queensland’s T4 shock tunnel, as well as the very large shock tunnels at the German Aerospace Centre in Göttingen, Germany and at the Japanese Aerospace Exploration Agency near Sendai, Japan.
“It gives us a voice in the international space arena, to be able to participate in discussions on space regulations and activity that will affect us,” Professor Boyce said.
The research team used a hypersonic wind tunnel and a X3 expansion tunnel to perform ground tests.
Materials testing took place in a plasma hypersonic wind tunnel at the Italian Aerospace Research Centre in Italy.
“We are dependent on space, yet far from self-sufficient, and the fragile space environment is congested and cluttered with debris. For both reasons, we are vulnerable.”
“We need to be able to provide leadership in the councils which regulate the space environment and space activities, in order to minimise our current vulnerabilities in space,” Professor Boyce said.
The Importance of New Materials
Researchers continue testing new materials to withstand the extreme heat experienced by hypersonic vehicles in flight to ensure they can fly for substantially longer.
For example, research teams have tested scramjets at Woomera in South Australia, where scramjet engines made of conventional materials have been tested.
When scramjets and other hypersonic materials are tested, researchers are looking at whether they encounter any problems with extreme heat including melting, and if they can be re-used.
In high-speed aircraft, air friction can cause extreme heating of the leading edge, where temperatures on the surface of an object travelling at Mach 5 can reach 1,000 °C.
These higher temperatures cannot be sustained by most materials.
Extreme heating of the leading edge was the cause of the Space Shuttle Columbia accident during re-entry in 2003. The accident was preceded by damage to protective tiles on the leading edge which occurred during take-off.
However, researchers are working to design materials that can ablate at high temperature.
Professor John Drennan is the Director of the University of Queensland’s Centre for Microscopy and Microanalysis. He is also a pioneer in ceramic composite materials, who is looking at several concepts to enable hypersonic vehicles to handle extreme heat for prolonged periods.
“The technologies we are developing will have application anywhere where performance is needed from materials in high temperature environments for long periods,” he said.
“Some potential uses for the new materials might include in power plants and for exhaust nozzles of jet engines.”
Professor Drennan said the technologies developed would benefit Australian industry by providing further capabilities in materials science.
“Australian industries will be able to build components of aircraft, rather than having to import these materials from the U.S. and Europe,” he said. Another challenging problem area is inside the scramjet engine, which must handle a corrosive mix of hot oxygen and combustion products, as well as high thermal, mechanical and acoustic loadings.
Scramjet-based launch systems promise safe, reliable and economical access to space for launches of communications satellites.
Although scramjet technology has been known since the 1950s, it has proved a hard nut for international scientists to crack.
Australia’s first professor of space engineering, Emeritus Professor Ray Stalker began studying scramjets in 1982.
His research was pivotal to the University of Queensland’s Centre for Hypersonics, which remains one of the world’s largest space engineering university groups.