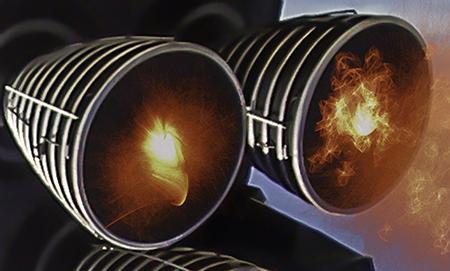
2 minute read
Extending Aircraft Life with a Bold Research Agenda
Source: Sally Wood
Fatigue and corrosion damage to structural components can be a major threat to the safety and airworthiness of civil and military aircraft.
ANSTO researchers have used nuclear techniques to evaluate a technology to repair corrosion and fatigue damage on the structural components of aircraft.
The researchers have worked with scientists and engineers from the Aerospace Division of Defence Science and Technology Group (DST Group).
Dr Wyman Zhuang, who led the research, said the team’s experiments confirmed deep surface rolling improved fatigue performance.
“Residual stresses that are found in materials and components are one of the most important factors impacting the fatigue performance of aircraft structural repairs,” he said.
The DST Group tested fatigue performance of the specimens made up of aircraft structural materials with various repair and post-repair enhancement conditions, and examined the fatigue cracking in the specimens after the fatigue testing.
This last step was conducted by using scanning electron microscopy.
“Structural integrity requirements for aircraft parts are of the highest level. The repaired components need to demonstrated that the restored component shall have a structural strength condition, equivalent or better than its original configuration, Dr Zhuang said.
ANSTO has a research agreement with the DST Group to collaborate on a number of projects, including a government radiological and nuclear spectrum database to help counter threats to Australia’s national security.
Scientific Ingenuity at Work
ANSTO provides access to a range of complementary techniques for multi-disciplinary materials to make technological advances to reduce detection of Australian Defence Force platforms and improve ballistic and shock protection.
Traditional materials characterisation methods can be enhanced by techniques that are available using ANSTO’s neutron beam instruments at the OPAL reactor, synchrotron X-ray and infrared beamlines at the Australian Synchrotron, advanced microscopy, imaging and computer modelling.
“We have had considerable success on a range of projects collaborating with the defence industry, DST and university partners,” said Di Pietro, who was pivotal to lifting these projects off the ground as the Head of Innovation and Integration at ANSTO.
“This partnership reflects a coinvestment in research and development activities that strengthen Australia’s defence priorities on ambitious but attainable projects,” he said.
In addition, ANSTO’s materials science research supports aerospace and space endeavours in Australia and internationally.
Building on experience gained in materials for advanced nuclear systems, ANSTO’s activities in this area are focussed on development, performance and in-service degradation of:
• nickel-based superalloys
• reinforced carbon-Carbon (C/C) composites
• ultra-high temperature ceramics (UHTC).
These materials are required to withstand a combination of challenging in-service environmental conditions such as high temperature, corrosion/oxidation, high-energy particle radiation and photon gamma irradiation.
ANSTO’s work has delivered innovative solutions for the production of high performance materials and systems for use in both supersonic rocket and hypersonic scram jet propulsions systems.
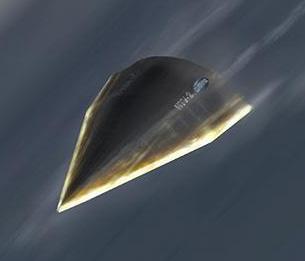
ANSTO has collaborated on the development of advanced sensors and hypersonic materials to support Australia’s defence and national security objectives.