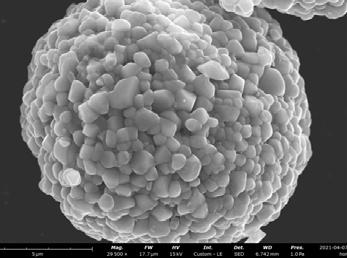
3 minute read
Phenom SEMs Provide Key Insights on Structure and Composition to Advance Battery Manufacturing
Source: ATA Scientific Pty Ltd
Global energy storage demand has driven a battery power revolution in research and development. Lithiumion batteries (LIB) have progressed in terms of power density, safety, and cycle life, however, advances in manufacturing LIBs wane behind. The required quality checks, such as the inspection of raw materials, intermediate components and final product, are central to this lag. A scanning electron microscope (SEM) is an unrivalled technique for inspecting and analysing nanoscale materials, that could benefit production processes and root cause analysis. SEM can help solve some key issues of battery manufacturing, which may eventually result in increasing battery safety and production efficiency, while lowering the cost and energy consumption.
Simple to Operate and Fast to Learn, the Phenom XL G2 SEM Allows Users to Observe:
• Size and granulometry of powders used as raw materials • Size and orientation of pores and fibres in insulating membranes • Three-dimensional structure of electrodes after production processes • Response of materials to electrical or thermal solicitations • Presence of contaminants in the battery sublayers. The Phenom XL G2 is the only SEM that can be placed within an argon-filled glovebox, allowing users to perform research on air sensitive lithium battery samples. Air reactivity of LIB materials is a key challenge in analysis, and whilst investigations in Argon can provide an inert environment, an SEM’s high acceleration voltage may cause sparking. The Phenom XL G2 employs technology dedicated to avoiding this issue, offering users a protected environment to characterise air sensitive battery samples. A glovebox is filled with Argon, and via a bypass, air is replaced with Argon to safely transport the samples in preparation for imaging. This process is fast, but importantly, the lithium samples remain protected.
Phenom SEM Reveals Detailed Sample Surface Information
An electrodes’ nano-structural shape and orientation is crucial to a battery’s longevity and efficiency. Materials used for cathodes typically look like agglomerates of smaller particles (Image 1) prompting the quest for higher resolution. Phenom SEMs can be used to inspect the morphology and surface topography of the sample with the Everhart-Thornley Secondary Electron Detector (SED). The accompanying four-quadrant backscattered electron detector (BSD) reveals areas of different compositions by varying contrast. Additionally, elemental identity of these regions can be confirmed using the fully integrated high-throughput energy-dispersive detector (EDS). This trinity of detectors render Phenom SEMs a formidable tool in the hunt for contamination. Battery insulating membranes are typically non-conductive and electron beam sensitive, promoting the value of the low voltage option (1 to 20kV) and variable vacuum levels of the Phenom Pharos, that help prevent sample damage and reduce charging effects.
Phenom SEM Detects Sources of Contamination
During the production of Li-ion powders, there are several sources of contamination. Calcination which is used to bind Li under high temperature, can introduce Al and Si contamination. Additives are used to influence the crystalline structure and improve the flexibility, increasing the number of charge cycles and voltage. Coatings are added to improve conductivity and make the powder last longer. Powder transportation and cell manufacturing processes can introduce further contaminants, which can accumulate, grow larger and larger and affect battery efficiency by lowering performance and reducing recharging cycles. Thankfully, the Phenom SEM comes to the rescue, given contaminants can pierce insulator membranes and cause short circuits, thus becoming a fire hazard.
Automated SEM Imaging Combined with EDX Analysis Using Perception Software
The Phenom ParticleX SEM advanced software analysis enables key measurements to be automated, providing more accurate results, and saving operators a great deal of time. Automated SEM plus EDS analysis can be used for monitoring different parts of the production environment. Contaminants are automatically detected and characterised, with reports showing powder purity and environmental cleanliness level complying with the latest industrial manufacturing standards. Phenom Desktop SEM can accelerate research and development to help design safer, more powerful and longer lasting batteries. Call us for a demonstration today!
Image1. Raw Powders used in the production of cathodes. SEMs are ideal tools for investigating small particles in the range of micrometres or nanometres.
Image 2: Lithium dendrite observation on cathode. Charging and discharging cycles tend to reduce capacity, and can even break due to Li dendrite formation.