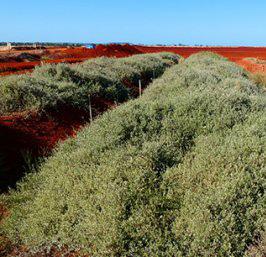
17 minute read
Breaking News
Sustainable Solution to The Mining Industry's ‘Red Mud’ Waste Enters Final Stage of Testing
Technology that could rehabilitate mine waste back to useful soil is entering full-scale trials at two Queensland refineries. Researchers at The University of Queensland’s Sustainable Minerals Institute recently developed the bio-engineering technology in partnership with Rio Tinto and Queensland Alumina Limited.
Professor Longbin Huang said the process will transform the bauxite residue, known as ‘red mud’, into a soil-like material capable of hosting plant life. “The team has secured more than $3 million in funding from Rio Tinto and QAL that will allow us to trial the technology at an operational scale at two red mud sites. This project demonstrates how transformative industry-academia partnerships can,” Professor Huang said. There are more than four billion tonnes of red mud stored in dams around the world. Australia is the second largest producer of the mineral waste by-product of alumina refining. “The salinity and alkalinity associated with the minerals in red mud means rehabilitation can be challenging,” Professor Huang said. The process eco-engineers the mineral and organic constituents into material that is more hospitable to plant life. Trent Scherer, who is the Environment and Tailings Manager at Queensland Alumina Limited, is excited to see the project moving to a full-scale trial. “After years of watching various trials unfold within our daily work environment, to now be able to see the tangible outcomes of UQ’s work has been encouraging. QAL is committed to minimising our environmental footprint through our $440 million 5-Year Environmental Strategy, and the funding and resources provided to this project are further steps in that journey,” said Scherer.
Revegetation underway at a red mud site near Gladstone. Image courtesy of the University of Queensland. RMIT University is a world leader in the development of advanced manufacturing technologies for aerospace and other industries. Image courtesy of RMIT University.
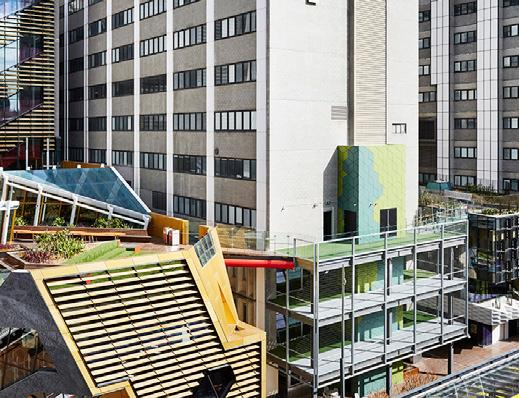
Boeing and RMIT Partner to Build Space Manufacturing Capability
Australia’s space research will take a giant leap forward at RMIT University’s world-leading advanced manufacturing hub. A recent partnership between RMIT and Boeing will focus on product design strategy, materials research and process innovation.
The collaboration will harness global networks and expertise to develop local solutions for the manufacturing of space equipment. RMIT’s Deputy Vice Chancellor for Research and Innovation, Professor Calum Drummond AO, said the research and development will be undertaken at RMIT’s Space Industry Hub.
“Our ultimate goal is to maximise opportunities for commercialisation of the products that we co-develop with Boeing,” Professor Drummond said. The hub is a launchpad that is dedicated to industrial solutions for Australia’s growing space sector. “This is a pioneering project which provides a tangible pathway for Australian businesses to upskill, innovate and export globally as manufacturers of products for space applications.” “Leveraging Boeing and RMIT’s joint expertise and facilities, we believe we can unlock boundless future opportunities for Australian industry,” Professor Drummond said. Paul Watson is the Director of Aerospace Engineering and Production at Boeing Defence Australia. He said Australia’s space sector requires the production of complex, low volume, and bespoke components that are not suited to conventional manufacturing techniques. “This partnership will develop new knowledge in advanced manufacturing technologies, which will not only stimulate the development of a local fabrication capability, but will also expose Australian industry to space export markets as part of Boeing’s global supply chain,” he said.
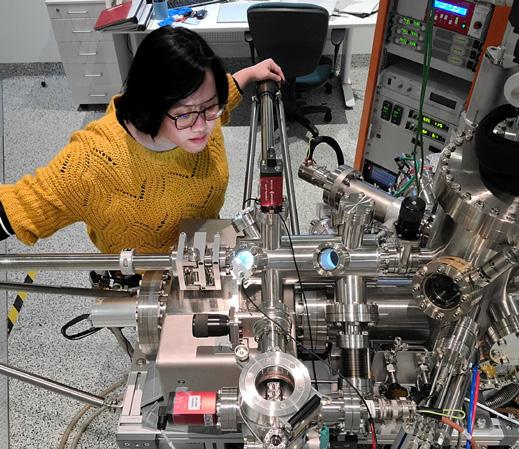
Lead author Dr Chi Xuan Trang (FLEET/Monash) is an expert in molecular beam epitaxy growth (MBE) and angle-resolved photoemission spectroscopy (ARPES) of topological materials.
Electrons On the Edge: The Story of An Intrinsic Magnetic Topological Insulator
An intrinsic magnetic topological insulator has been discovered with a large band gap. The breakthrough research makes ‘MnBi2Te4’ a promising material platform for fabricating ultra-low-energy electronics, and observing exotic topological phenomena. The material hosts both magnetism and topology, and is ultra-thin. It was found to have a large band-gap in a Quantum Anomalous Hall (QAH) insulating state. The almost-zero resistance along the 1D edges of a QAH insulator, make it promising for lossless transport applications and ultra-low energy devices. Magnetism that is introduced in topological-insulator materials breaks timereversal symmetry in the material, and leads to a gap in the surface state of the topological insulator. “Although we cannot directly observe the QAH effect using angle-resolved photoemission spectroscopy, we can use this technique to probe the size of a band-gap opening on the surface of MnBi2Te4 and how it evolves with temperature,” said Dr Trang, who is a Research Fellow at FLEET. In an intrinsic magnetic topological insulator, such as MnBi2Te4, there is a critical magnetic ordering temperature. In this process, the material is predicted to undergo a topological phase transition from QAH insulator to a paramagnetic topological insulator. FLEET PhD student Qule Li, is a co-lead author on the study, and explained the benefits of an angle resolved photoemission technique. “We could measure the band gap in MnBi2Te4, opening and closing to confirm the topological phase transition and magnetic nature of the bandgap.” Together, FLEET researchers used angle-resolved photoemission spectroscopy, and density functional theory calculations to study the electronic state and band structure of MnBi2Te4.
New Manufacturing Facility Takes Victorian Bioengineering Expertise to The World
Australia’s first facility with bioengineering expertise and technology to create medical devices for clinical trials was recently opened. The manufacturing facility, NeoBionica, marks the beginning of a new era in medical device development capability in Victoria. The Bionics Institute and the University of Melbourne are collaborating to bring the state-of-the-art laboratory to life at St Vincent’s Hospital in Melbourne. Bionics Institute CEO, Robert Klupacs, said Neo-Bionica will significantly enhance the time it takes to develop and trial a medical device, which means earlier benefits to patients of the technology. “Bionics Institute researchers have discovered that vagus nerve stimulation can be used to treat inflammatory bowel disease. However, to create a prototype device for use in future clinical trials, we had to contract a company in America, resulting in an 18-month delay.” said Klupacs. Mr Klupacs said a medical device, which was invented by Bionics Institute researchers and collaborators, stimulates the vagus nerve, and connects the brain to the gut with branches to several major organs. “Neo-Bionica has the latest cleanroom technology needed to create implants for human trials, as well as the latest engineering equipment, 3D printers and, most importantly, the combined expertise of our highly-trained engineers, scientists and clinicians,” he explained. University of Melbourne Vice-Chancellor, Professor Duncan Maskell, said he is delighted to see Neo-Bionica become a reality. “I look forward to taking Victorian bioengineering expertise to the world as we continue to build our global reputation as a powerhouse in this extremely important field.” Several devices are currently under development at the Bionics Institute, and will be prototyped in Neo-Bionica.
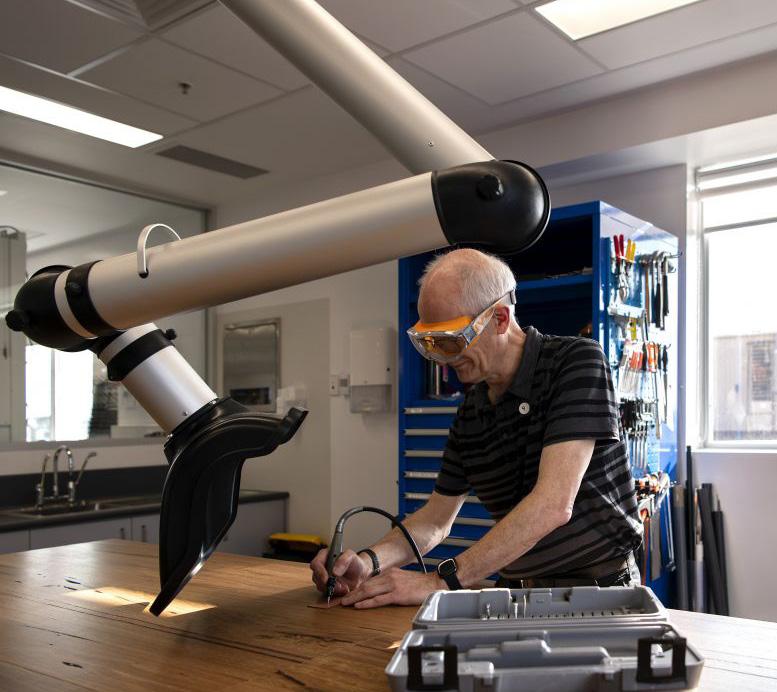
The opening of Neo-Bionica sees a new era in medical device development. Image: Alchemy Construction. Image courtesy of the University of Melbourne.
University Spin-Out Gelion to Make Next-Gen Batteries in Sydney
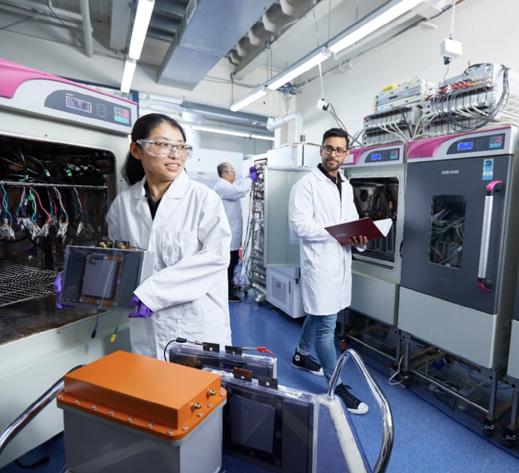
Inside the Gelion lab. Image courtesy of the University of Sydney.
Global renewable-energy storage company, Gelion, recently joined forces with Battery Energy Power Solutions to make and distribute the Gelion Endure zinc-bromide battery for the Australian market.
The batteries were invented by Professor Thomas Maschmeyer, and will be produced at Battery Energy’s Fairfield factory in Western Sydney. “There is a revolution coming in energy production and distribution worldwide,” said Professor Maschmeyer. Professor Maschmeyer has a wide range of expertise in turning foundational science into a commercial reality. He is the incumbent holder of the Australian Prime Minister’s Prize for Innovation and a member of the Sydney Nano and the School of Chemistry. The research team reimagined zincbromide chemistry to produce a revolutionary new battery, and replace a flowing electrolyte with a stable gel. “Across the globe, governments and companies are setting ambitious net-zero-carbon emission targets. To achieve these goals, renewable energy will need to be stored everywhere—and that means batteries,” said Professor Maschmeyer. “Gelion batteries are safe, robust and recyclable. For stationary energy storage, zinc-bromide batteries do away with the need for expensive cooling and maintenance systems. And they can’t catch fire,” he said. The battery operates at temperatures of up to 50 degrees and can be completely discharged of energy with no loss of function.
The battery was recently tested by heating it on a barbeque plate at about 700 degrees for half an hour. “In the coming months, we will be focused on demonstrating our next-generation battery systems in-field in Australia, commencing later this year,” said Professor Maschmeyer.
Discovery Paves Way for Improved Quantum Devices
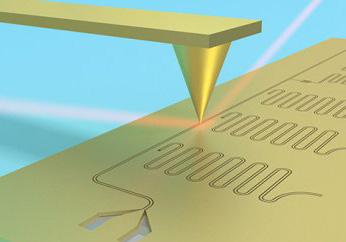
Physicists and engineers recently discovered a method to identify and address imperfections in materials for one of the most promising technologies in commercial quantum computing. Researchers at the University of Queensland developed treatments and optimised fabrication protocols for building superconducting circuits on silicon chips. Dr Peter Jacobson, who co-led the research, said the team had identified that imperfections during the fabrication process, reduced the effectiveness of the circuits. “Superconducting quantum circuits are attracting interest from industry giants such as Google and IBM, but widespread application is hindered by ‘decoherence,’ a phenomenon which causes information to be lost,” he said. “Decoherence is primarily due to interactions between the superconducting circuit and the silicon chip—a physics problem—and to material imperfections introduced during fabrication—an engineering problem. So we needed input from physicists and engineers to find a solution,” said Dr Jacobson. The team used a method called terahertz scanning near-field optical microscopy—an atomic force microscope combined with a THz light source and detector. This provided a combination of high spatial resolution—seeing down to the size of viruses—and local spectroscopic measurements. Professor Aleksandar Rakić said the technique enabled probing at the nanoscale rather than the macroscale by focusing light onto a metallic tip. “This provides new access for us to understand where imperfections are located so we can reduce decoherence and help reduce losses in superconducting quantum devices. We found that commonly used fabrication recipes unintentionally introduce imperfections into the silicon chips, which contribute to decoherence,” said Professor Rakić.
Crystal structure and initial characterisation of F5GT.
A SP-FET transistor, with F5GT flake on a solid proton conductor (SPC) – scale = 10µm. Schematic of a superconducting circuit (thin black lines) on a silicon chip (yellow base), being imaged using terahertz scanning near-field microscopy (red beam focused into yellow tip). Image courtesy of the University of Queensland.
ANU Scientists Set New Record with Bifacial Solar Cells
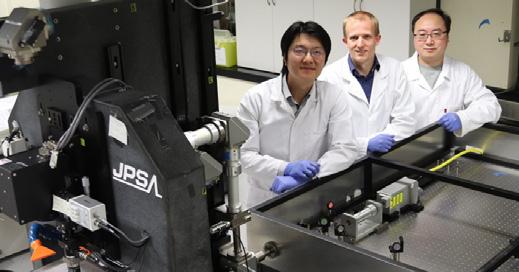
ANU researchers (L to R): Marco Ernst, Wensheng Liang and Kean Fong. Image courtesy of Eric Byler and The Australian National University.
Scientists at The Australian National University recently produced a more efficient type of solar cell that uses laser processing. The solar cells are dual sided, which means that both the front and back of the cell generate power. Dr Kean Chern Fong said the bifacial solar cells beat the performance of single sided silicon solar cells. "We have developed what I would call a true bifacial solar cell, as it has nearly symmetrical power generation capacity on both surfaces of the device.” "When deployed on a conventional solar farm, a bifacial cell absorbs direct incoming light, while also taking advantage of ground reflection, which can contribute up to an additional 30 per cent power generation,” Dr Fong said. Bifacial solar cells are a valuable tool used in solar farms. The solar cells are expected to have a market share of over 50 per cent in the next five years. "Our work demonstrates the incredible capabilities of this technology,” Dr Fong said. The research team used specific laser doping technology to fabricate the cells. This technique is a low-cost, industry-compatible process for boosting solar cell efficiency. Researchers were able to achieve a front conversion efficiency of 24.3 per cent and a rear conversion efficiency of 23.4 per cent. This performance represents an effective power output of 29 per cent, which exceeds the performance of the best single-sided silicon solar cell. This research was supported by the Australian Government through the Australian Renewable Energy Agency and Australian Centre for Advanced Photovoltaics.
Scientists at The Australian National University recently produced a more efficient type of solar cell. Image courtesy of Eric Byler and The Australian National University.
New Sulphur Chemistry Possible Key to Greener Batteries
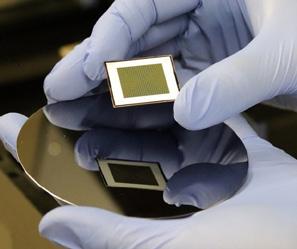
Researchers at the University of Adelaide are developing the next generation of batteries using innovative sulphur chemistry, which will reduce their environmental impact. The research team has conducted innovative work on sulphur oxidation processes. Professor Shizhang Qiao, who is the Director at the Centre for Materials in Energy and Catalysis, said the research is a breakthrough. “[It] is pushing the boundaries of the design of the next generation of batteries. Sulphur is an important electrode material in metal—sulphur batteries due to its abundance on Earth and its chemical properties, which may improve the capacity of batteries.” “Sulphur could provide the key to improving the energy capacity of commercial lithium-ion batteries,” said Professor Qiao. The research team has demonstrated the reversible electrochemical oxidation of a sulphur cathode, and has applied this new process into aluminium–sulphur batteries. “We have achieved the highest voltage output of an aluminium–sulphur battery: approximately 1.8 volts of steady power output which is significantly greater than present technology which can only achieve approximately 0.6 volts output,” said Professor Qiao. “Aluminium-sulphur batteries cost much less than current commercial lithium-ion batteries as the materials used in them are low-cost and environmentally friendly chemicals.” Advances in this type of chemical technology are reducing the environmental impact of batteries. But the demand for the chemicals that they contain, like lithium, is having a severe impact on places where it is mined. “Our research provides valuable inspiration for the design of other metal-sulphur batteries, not just ones that use aluminium-sulphur technology,” Professor Qiao concluded.
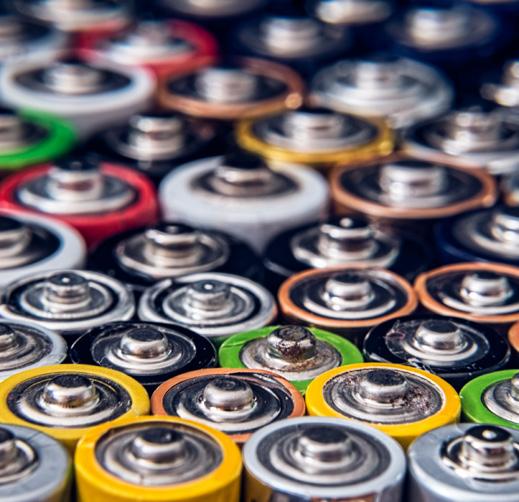
Star Attraction: Magnetism Generated In 2D Organic Material by Star-Like Arrangement of Molecules
A recent study shows the emergence of magnetism in a 2D organic material due to strong electron-electron interactions.
These interactions are the direct consequence of the material’s unique, star-like atomic-scale structure. This is the first observation of local magnetic moments emerging from interactions between electrons in an atomically thin 2D organic material. The findings have potential for applications in nextgeneration electronics based on organic nanomaterials, where tuning of interactions between electrons can lead to a vast range of electronic and magnetic phases and properties. This Monash University-led study investigated a 2D metalorganic nanomaterial composed of organic molecules arranged in a kagome geometry, which follows a ‘star-like’ pattern. The 2D metal-organic nanomaterial consists of dicyanoanthracene molecules, which are coordinated with copper atoms on a weakly-interacting metal surface. The researchers found that the 2D metal-organic structure— whose molecular and atomic building blocks are by themselves non-magnetic—hosts magnetic moments confined at specific locations. Theoretical calculations showed this emergent magnetism is a result of the strong electron-electron Coulomb repulsion given by the specific 2D kagome geometry. Associate Professor Agustin Schiffrin said this is a breakthrough development. “We think that this can be important for the development of future electronics and spintronics technologies based on organic materials, where tuning of interactions between electrons can lead to control over a wide range of electronic and magnetic properties.” This research and experiments were performed at Monash University, and supported through the Australian Research Council. RMIT University researchers have developed highly versatile catalysts that are cost-effective to make and simple to scale. The ultra-efficient 3D printed catalysts could help solve the challenge of overheating in hypersonic aircraft, and offer a revolutionary solution to thermal management across countless industries. Lab demonstrations show the 3D printed catalysts could be used to power hypersonic flight while simultaneously cooling the system. Lead researcher, Dr Selvakannan Periasamy, said the work tackles a major challenge in the development of hypersonic aircraft: controlling the incredible heat that builds up when planes fly at more than five times the speed of sound. “Our lab tests show the 3D printed catalysts we’ve developed have great promise for fuelling the future of hypersonic flight,” Dr Periasamy said. “Powerful and efficient, they offer an exciting potential solution for thermal management in aviation—and beyond.” “With further development, we hope this new generation of ultra-efficient 3D printed catalysts could be used to transform any industrial process where overheating is an ever-present challenge, Dr Periasamy explained. In theory, a hypersonic aircraft could travel from London to Sydney in four hours, but many challenges remain in the development of hypersonic air travel, like extreme heat levels.
But PhD researcher, Roxanne Hubesch, explained that using fuel as a coolant was one of the most promising experimental approaches to the overheating problem. “Fuels that can absorb heat while powering an aircraft are a key focus for scientists, but this idea relies on heat-consuming chemical reactions that need highly efficient catalysts,” Hubesch said.
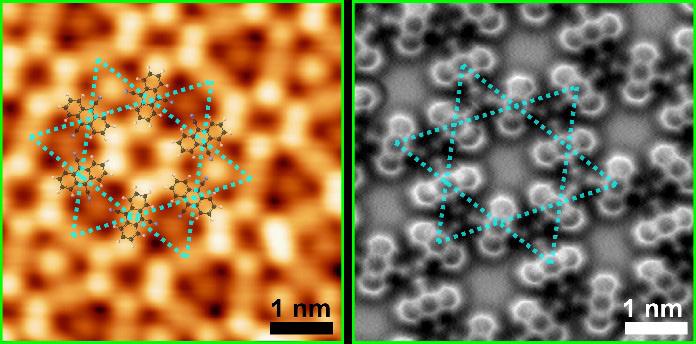
The star-like ‘kagome’ molecular structure of the 2D metal-organic material results in strong electronic interactions and non-trivial magnetic properties (left: STM image, right: non-contact AFM). Developed as part of NASA’s Hyper-X program, the X-43A hypersonic research vehicle made aviation history in 2004, reaching speeds above Mach 9.6 or over 10,000km/h. Image courtesy of NASA and RMIT University.
Next Gen 3D Printed Catalysts to Propel Hypersonic Flight
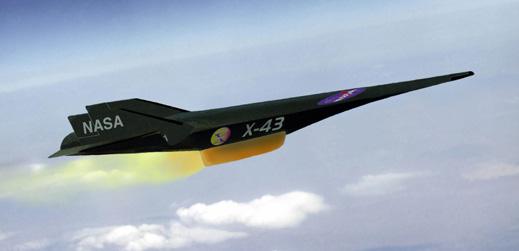
A range of experimental designs for the 3D printed catalysts. Image courtesy of RMIT University.
Australian Start-Up Additive Assurance Goes Global
Additive Assurance, an Australian start-up providing world-leading quality assurance solutions for additive manufacturing, today announced a partnership with global car manufacturer Volkswagen. Spun out of Monash University and backed by IP Group, Additive Assurance has developed an innovative technology solution, AMiRIS™, for quality assurance in metal additive manufacturing (3D Printing). Able to detect, notify and correct variations in the 3D printing build process, AMiRIS™ offers a unique solution to inconsistent production quality, a huge problem faced by the industry. Additive Assurance has signed a partnership with Volkswagen to develop a manufacturing system to suit the global car manufacturer’s production printers. Additive Manufacturing will allow Volkswagen to develop and produce car components and prototypes faster, with greater flexibility and using fewer resources. Volkswagen will use Additive Assurance’s innovative AMiRIS™ solution to verify the quality of each individual part that is printing, ensuring exact replicas are produced. Commenting on the partnership, Additive Assurance CoFounder, Marten Jurg, said: “Metal additive manufacturing is taking the world by storm, but quality is still not at the level it needs to be for important applications. We see a huge opportunity for Additive Manufacturing and are thrilled to be working with a leading company like Volkswagen to transform how they develop their products.” Oliver Pohl, who leads the Additive Manufacturing division at Volkswagen commented: “Volkswagen is actively integrating additive manufacturing in their workflow and by adopting the pioneering solution for quality assurance from Additive Assurance, we will be able to further push the boundaries towards serial production using additive manufacturing”. AMiRIS™ combines hardware that observes each layer during printing and cloud-based machine learning software to generate a real time map of defects. The solution then analyses and feeds this information directly back to the operators. Volkswagen will install the AMiRIS™ unit on their Additive Manufacturing printer at the car maker’s 3D printing facility in Wolfsburg, Germany.
CSIRO Report Reveals Potential of Synthetic Biology Ecosystem
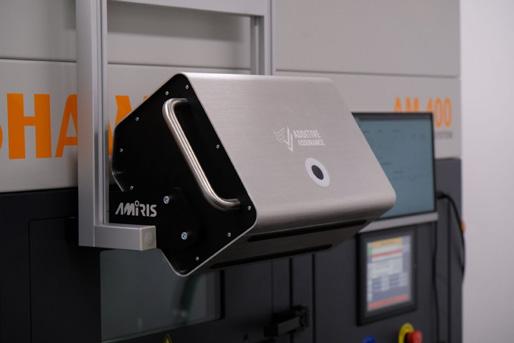
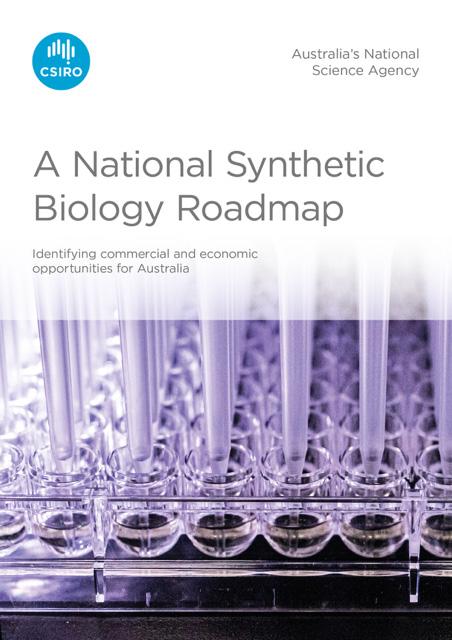
A new report from CSIRO says Australia could develop an industry worth up to $27 billion a year and create 44,000 jobs by 2040 by building its synthetic biology ecosystem. Synthetic biology is a rapidly growing field that applies engineering principles and genetic technologies to biology, drawing on biology, engineering, and computer science, as well as many other fields. According to the new report, A National Synthetic Biology Roadmap: Identifying commercial and economic opportunities for Australia, the two biggest areas to benefit from synthetic biology are the food and agriculture (up to $19 billion) and health and medicine sectors (up to $7 billion). CSIRO says it is focused on developing capacity in synthetic biology including through a new BioFoundry facility in Queensland that provides a bioengineering capability to the research and development community to rapidly design, build and test new biotechnologies. Australia has invested at least $80 million in developing synthetic biology research capabilities in recent years. Professor Claudia Vickers, synthetic biology director at CSIRO, said the scientific impact was encouraging and with sustained investment can deliver increased impact and economic benefit. “Synthetic biology can help overcome a range of global challenges, particularly in agriculture and health. It can also enable Australia to transform its economy by creating new, more sustainable industries and generating jobs,” said Professor Vickers. “Bringing technology, the research community and other stakeholders together to enable start-ups, private investment and growth of market share will be essential to achieve the vision outlined in the Roadmap.”