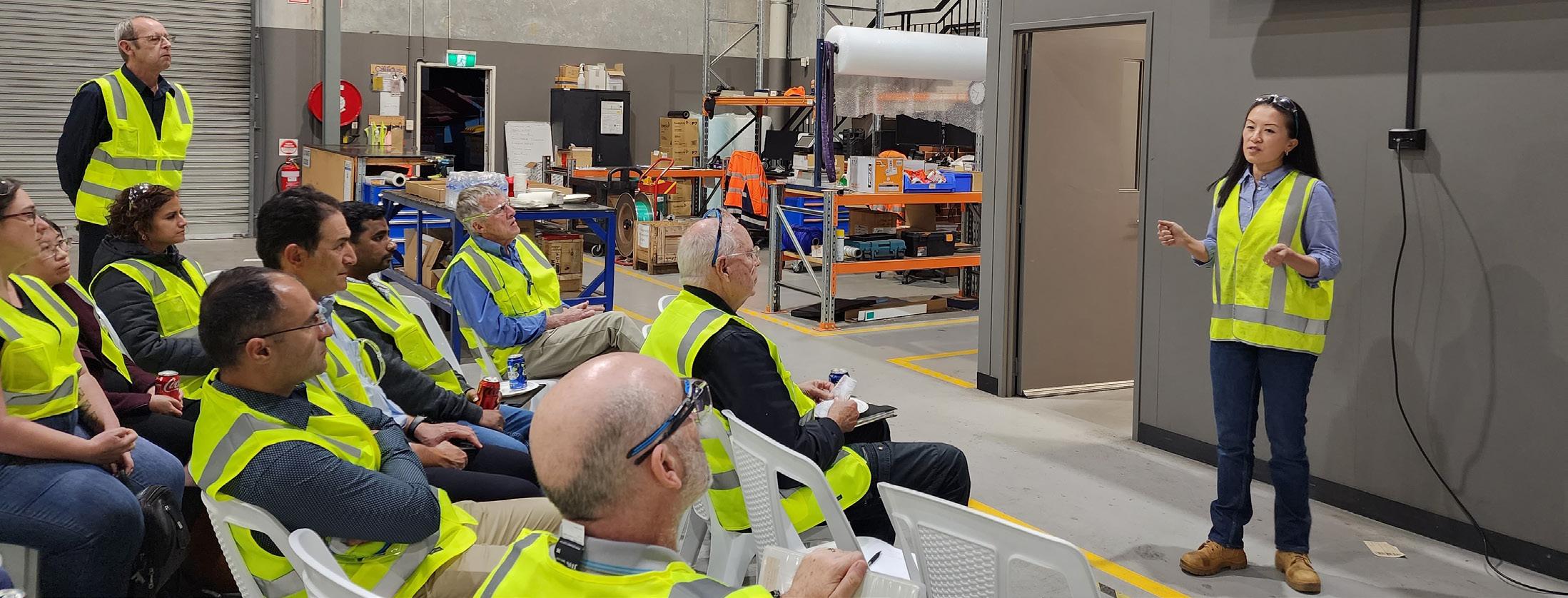
3 minute read
MATERIALS AUSTRALIA WA Branch Technical Meeting - 11 October 2023
Visit to Callidus Process Solutions
Source: Steve Algie
In early October, the Western Australia Branch facilitated a technical meeting that featured a visit to Callidus Process Solutions. Members were hosted by two key staff members from Callidus: Dominic Flaxman (General Manager of Engineering) and Dr Evelyn Ng (Materials Engineer).
The Callidus Group is a class-leading service provider to the mining and oil and gas industry, with headquarters in Balcatta and several facilities throughout the Asia Pacific region.
The Callidus Group includes Callidus Process Solutions and Callidus Welding Solutions.
The company specialises in management, maintenance, servicing and diagnostics of valves, actuators, and instrumentation. Callidus has developed in-house capability in engineering and design, fabrication and supply. These capabilities have contributed to building strong client relationships through the development and provision of engineering solutions to erosion and corrosion challenges.
Dominic Flaxman gave an overview of the firm’s history, starting with its founding in Western Australia in 1997, to service the Minara Nickel refinery. The initial focus was on valves, but capabilities extend to autoclaves, spools and piping. The severe operating conditions in high-pressure leaching led to a market for specialised testing, materials testing and development, and surface modification treatments. Capabilities now extend to field work, maintenance planning, and shutdowns and overhaul repairs and fabrication.
Callidus Process Solutions has capacity for design from scratch, though most tailored design work is for modification of OEM equipment. Other engineering services include valve selection and sizing, failure, and root cause analysis. Dominic described an example of RCA of fatigue failure in a valve body, leading to an improved design.
Evelyn Ng then proceeded with some more background about the development of the proprietary valve coating technologies that she had described in her talk to the Branch at the June meeting. Typically, these are applied to valves where nothing else works, even though they may be made from tantalum, titanium, Hastelloy, Inconel or Super Duplex alloys.
One is FM-1500, a fully dense-weld deposited coating of Titanium Nitride with additives; this survived the extreme conditions in high pressure acid leaching. Another is BM-1600 – a fused tantalum on a pure nickel welded coating, with a ceramic topcoat applied by physical vapour deposition (PVD) that can be used in oxygen at over 200°C. She explained how these had been developed as part of Callidus’ endto-end’ service offering, which she summarised as follows:
• Investigate – history and knowledge
• Solve the problem – not just diagnose it
• Provide solutions that work with existing equipment
• Do the engineering – develop compliant solutions
• Provide and implement the solution on site
To provide this service, Callidus has installed High velocity oxy-fuel (HVOF) thermal spray and atmospheric plasma spray coating equipment, and has also built its own specialised ASTM test equipment.
The talks were followed by a tour of the extensive facility. Valves up to 40 inch size, in various states of repair were shown, starting from strip-down, proceeding through coating, lapping to achieve seal, then reassembly and high-pressure testing before despatch. The materials testing laboratory and specialised ASTM testing used in quality control and new coating development were also shown.