
3 minute read
WA Branch Technical Meeting - 8 March 2021
WA Branch Technical Meeting - 8 March 2021 Overcoming Preferential Flow in Bulk Solids Handling
Source: Corin Holmes, Operations Manager, Jenike & Johanson
Corin Holmes has a Masters Degree, earned in the Wolfson Centre for Bulk Solids Handling Technology, from the University of Greenwich. Corin arrived in Australia, from Canada, in 2012 and established the Perth office of Jenike & Johanson. The company is headquartered in Boston, and has been operating for around 50 years. The company offers niche services in bulk materials storage, handling, and transport. Their approach is to determine material properties in the laboratory and apply these to design.
Corin opened his presentation by reviewing the flow characteristics of bulk solids: internal friction, compressibility, sensitivity to pressure, and ability to form piles. He then showed how these interact with geometry to produce two characteristic types of solids flow: funnel flow and mass flow, which he demonstrated with hourglass-shaped models. The desirable mass flow condition, which came from a relatively steep-sided funnel, showed uniform first-in, first-out flow behaviour, with no ratholes and minimal segregation. In contrast, funnel flow produced ratholes, dead regions (low capacity), last-in, firstout flow, and segregation. In addition, fine powders tend to fluidise internally and flood (flow like water). Funnel flow can also lead to arching, where the solids become stuck in the funnel. Corin illustrated this with photographic evidence collected from various projects. His work on these projects involved the rectification of designs for chutes and feeders. The basic principles for ensuring mass flow are to have an outlet wide enough to overcome arching, and a wall angle sufficient to overcome friction, thereby allowing the solids to slide down the wall. The company’s founder, Dr Andrew Jenike, was able to relate these parameters to measurable materials properties, thus putting chute and should be hooper design on a scientific basis. Materials testing is a key part of the company’s design approach. As a generalisation, strength is dictated by fines content (-6mm) and moisture, but properties measured include particle size distribution, shape, density, temperature, relative humidity, moisture content, time at rest, compressibility, coefficient of friction and permeability (to air). Based on these measurements, and the Jenike Shear Test, a flow function curve is developed, plotting cohesive strength against the major consolidating pressure, traversing the possible flow regimes from non-flow to free flow. At the limits of the science, it is necessary to turn to physical modelling, which is useful for tuning and calibrating design models, even though solids flow is not scalable. Corin’s presentation concluded with a highly interactive sharing of ‘war stories’ – many in the audience had personal experience of what can go wrong with hoppers, chutes and feeders. In Corin’s opinion, many of the problems originate from the way that mining and mineral processing plant design packages are put together; it is quite common for the top and bottom of a transfer chute to fall into different design packages. However, he felt that mining houses are beginning to understand that they are the ones who end up with the operational consequences of poor designs. A 45-degree hopper might require the least amount of steel to build, but it doesn’t mean that it will work. Discussion extended into feeder design, covering feeders, dischargers and conveyors; the common design objective is a reliable uninterrupted flow. Corin explained how screw and belt feeders can induce preferential flow, and then went on to describe the complex solutions that may be needed, e.g. tapered shafts and variable pitch screws, and why a screw operating in a trough doesn’t work.
Corin Holmes
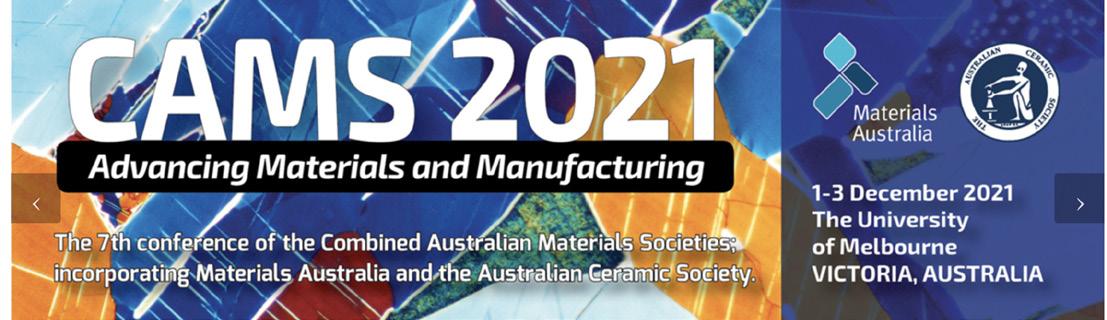