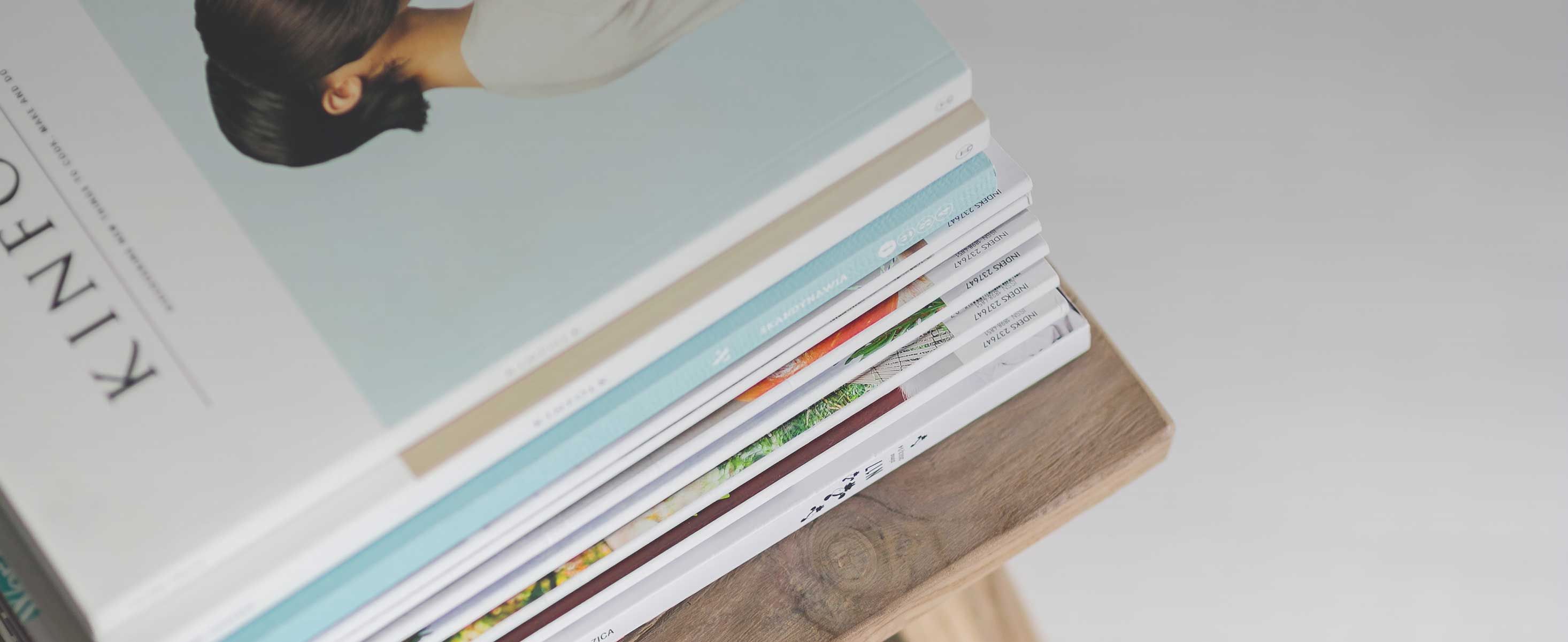
5 minute read
WA Branch Technical Meeting - 12 April 2021
WA Branch Technical Meeting - 12 April 2021 Beginners’ Guide to Cathodic Protection
Source: Ivo Kalcic, Lead Engineer – Cathodic Protection, Wood Asset Integrity Solutions
Ivo started his career in Croatia as a mechanical engineer working in the fabrication industry. His work on storage tanks revealed the need for a greater knowledge of corrosion protection, and Ivo accepted this as an opportunity, and challenge, to become an expert in cathodic protection, which led to his move to the Wood Group in Australia in 2012.
Ivo started with an explanation of the electrochemical principles of corrosion and cathodic protection (CP). Corrosion occurs when metal is oxidised to metallic ions, with the corresponding release of electrons (an anodic reaction). The flow of electrons from the corroding anodic area constitutes an electrical current (the corrosion current). For example, for a steel surface freely corroding at a rate of 1mm loss of iron per year, the corrosion current is around 50mA/m2 . For corrosion to occur it is necessary to have an anode, a cathode, joined by a Metallic path for electron flow and an Electrolyte path for the ion flow that completes the circuit (the acronym for this is ACME). Normal corrosion is driven by anodic and cathodic sites on the same metal surface, which result from, for example, differential aeration, or microstructural differences. In the case of cathodic protection, an alternative electrically connected anodic site is provided (immersed in the same electrolytic environment) to ensure that all sites on the protected surface are cathodic (consume electrons), hence the term ‘cathodic protection’ (CP). A potential difference is necessary, but not sufficient. For protection to be effective, a current flow from the protective anode must be significantly larger than the unprotected corrosion current. For steel, this means the CP current needs to be around 100 mA per square metre of surface to be protected. To avoid the need for enormous currents, the surface to be protected is normally sealed with a protective coating so that the protection is only needed where there are gaps in the coating. A perfect coating ensures that there is no electrochemical circuit. Hence, current is only drawn from the CP system when the protected surface is exposed (as when there is a coating failure). Ivo summarised the two types of CP system: sacrificial anodes and impressed current. Sacrificial anode systems, mainly used for structures immersed in sea water, connect the protected structure to a much more easily corroded metal, such as zinc, magnesium or aluminium alloy (ie, a metal with a more negative electrode potential). The lower electrode potential of the sacrificial anode makes the protected surface cathodic, and simultaneously provides the CP current by the anode’s own oxidation (hence the term sacrificial). Impressed current systems use an external voltage source to supply the potential difference required to make the protected surface cathodic. The voltage source is placed between the electrically connected protected surface and a separate electrode (usually inert) immersed in the same environment (normally soil). When an electrochemical circuit is established (as occurs when there is a break in the protective coating) the anodic reaction generates oxygen (or chlorine) gas by oxidation of the water (or soil moisture) or chloride ions in the surrounding environment, and simultaneously creates a local change in electrolyte concentration. The electrons released by the anodic reaction are collected on the anode, thus providing the CP current For CP to work, there must be a direct electrolyte path between the protected surface and the protective electrode. Ivo explained that a simple ‘rule of thumb’ for locating protective anodes is that the protective electrode should be able to ‘see’ the surface it is protecting. For example, CP is not suitable for protecting the rear surface of a structure, as the anode ‘can’t see around corners’. Design of CP systems requires knowledge of standards and expertise in understanding their limitations. Ivo referred to the main standards for CP, which lead to the usual reference to a CP potential of -850 mV (Cu/CuSO4 standard electrode). However, in practice the required potential can vary considerably, as in the Pilbara, where the iron oxide content in the soil is very high. Cathodic protection systems design needs to take into account the fact that the electrolytic path is not like a highconductivity metallic connection. The ionic current depends on a mutually dependent potential field and a diffusion-controlled ion concentration field. When a protected surface is exposed, for example by a coating failure, the ionic current starts to flow and a non-uniform field is established (this may take hours, or even days). The non-uniformity of the potential field around a cathodic site provides a means for locating gaps in protective coatings on buried pipelines, by using potential surveys. A broad-scale coating quality survey can identify local anomalies in the electric field, which indicate a local ionic current flow. Close-spaced local potential measurements, made by momentarily switching-off the protective voltage source, can then pinpoint the gap that requires remediation. Cathodic protection is an active process, with consequences that must be considered in CP system design. At the cathodically protected site the pH increases as water and oxygen in the immediate surroundings are electrochemically reduced. This can lead to carbonate precipitation and the build-up of calcareous deposits. Reduction products can lead to coating disbondment, and hydrogen gas may cause cracking of susceptible alloys. Copper used as anti-fouling becomes ineffective if it is electrically connected, as anti-fouling depends on the release of copper ions, which is not possible when the copper surface is cathodic. In general, the release of gas (hydrogen at the cathode and oxygen or chlorine at the anode) in impressed CP systems is a safety issue. Impressed current anodes must not be located inside sealed spaces. Ivo concluded his talk by dealing with some common misconceptions about CP. It is important to understand that the inside surface of a metal tank cannot be protected by an anode placed outside the tank (the external anode can’t ‘see’ the inside). With sacrificial CP, he pointed out that ‘one plus one is not always equal to two’. Each sacrificial block is only effective in providing CP current to the extent it can individually ‘see’ the protected surface; the arrangement of the blocks is an important design consideration.