
2 minute read
SA Branch Report - 5 May 2021
SA Branch Report - 5 May 2021 Surface Engineering Workshop
Source: Colin Hall
The old saying rings true: You don’t appreciate something until it is gone. The attendees of the recent in-person workshop at the University of South Australia (UniSA) certainly appreciated the opportunity to catch up in person.
UniSA hosted a joint workshop for Materials Australia, Australian Corrosion Association and Weld Australia on surface engineering. The event was proudly supported by SEAM – the Industrial Transformation Training Centre on Surface Engineering for Advanced Materials, the Future industries Institute, LaserBond and Microscopy Australia. A diverse range of industry, academia and students made up the ~40 in person participants, with a further ~25 joining via zoom. The early birds were taken on a tour of the Future Industry Institute. They had the opportunity to see the brand new Kratos XPS (Axis Supra), which is in the last steps of commissioning, and which is eagerly awaited by Microscopy Australia. The SA node of ANFF was also visited, which specialises in microfabrication supporting industry and researchers in a diverse range of fields covering medical to mineral processing. Attendees also visited the tribology facilities, which had an extensive range of wear tests on show— both standard and industry developed tests. Next on the tour was the coatings labs and the industry 4.0 test lab, which brings together software, hardware and virtual experience to showcase the capabilities of Industry 4.0. Physically, the facility can rapid prototype in both plastic and metal, and reverse engineer via laser scanning systems. The workshop consisted of three talks. LaserBond’s Dr Thomas Schlaefer gave a great introduction to thermal spray and lasercladding, covering the history of LaserBond and their large range of activities in the repair, remanufacture and supply of OEM parts. LaserBond also offers turnkey laser cladding systems, and just recently acquired United Surface Technologies (UST) in Melbourne to add to their Sydney and Adelaide facilities. AML3D was represented by Dr Paul Colegrove. Newly ASX listed, AML3D is going through a period of rapid growth. Their wire arc additive manufacturing process can efficiently produce large scale parts offering potentially shorter lead times, low material usage and overall efficiencies not achievable with conventional subtractive manufacture methods. Paul described, “if it comes in a weld wire we can probably print with it”. AML3D has a long list of qualified materials and is always open to trying new ones. They offer both fabrication and the turnkey ARCEMY system. Industry Associate Professor Colin Hall, finished off the workshop with a talk on the importance of the surface finish of additively manufactured parts. While an often overlooked or underappreciated part of AM, it is critical in achieving the final shape and required surface finish of a part. The practitioner has a wide range of surface finishing techniques on offer, including grinding, polishing, EDM, diamond point turning, vibration polishing and so on. It is a matter of selecting the right process for the right finish. A case study on freeform optical elements for space-based applications took the audience through such a selection process. A highlight of the evening was the networking. Drinks and nibbles allowed attendees to chat—just like we used to preCOVID.
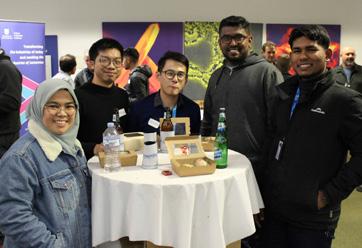

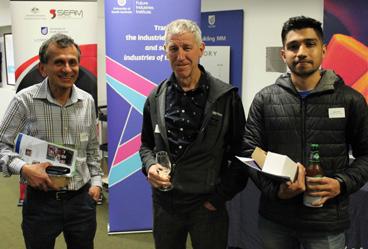
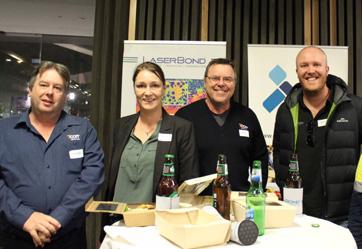
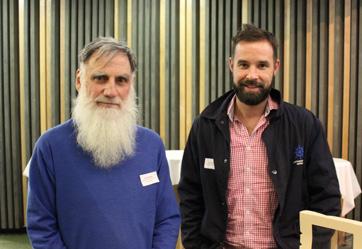