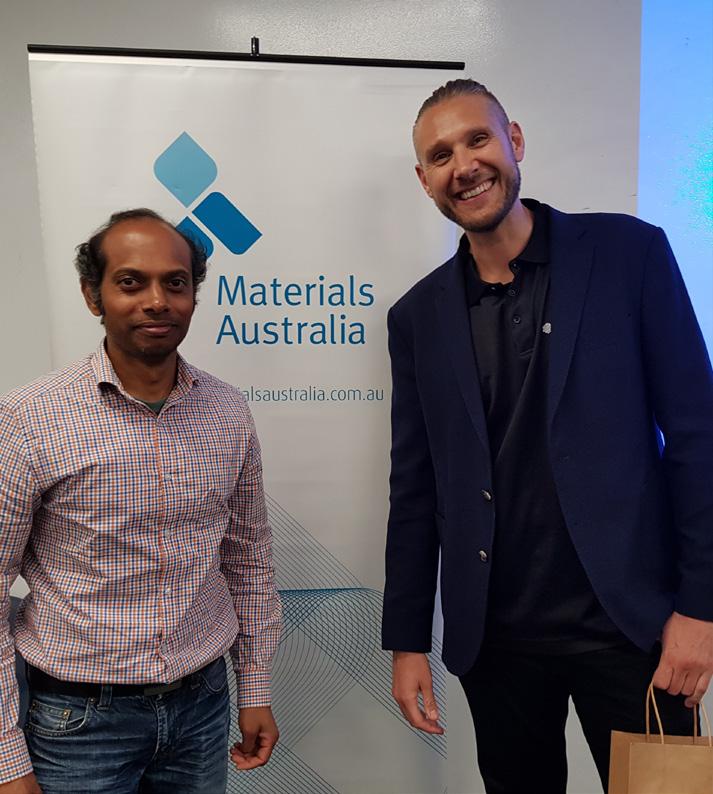
3 minute read
WA Branch Technical Meeting - 13 September 2021
WA Branch Technical Meeting - 13 September 2021 On-demand Additive Manufacturing
Source: Richard Elving, APAC Director, Markforged
The Western Australia branch recently hosted a technical evening, presented by Richard Elving (APAC Director, Markforged). Elving spoke on the topic of On-demand Additive Manufacturing. Based in Boston, Markforged was founded in 2013 on the belief that additive manufacturing can transform how entire industries operate. It describes its operating platform as ‘The Digital Forge’, based on the combination of proprietary software, materials and printers. Of these three components, it is the software that makes the company’s offering quite distinctive, networking a fleet of more than 12,000 printers in 73 countries. Elving’s career has seen him apply his background in finance to manufacturing, starting with Volvo in Sweden. He drew on this experience in outlining the strengths and limitations of traditional manufacturing and of additive manufacturing. Elving spoke about the challenges of supply chains and the volatility of skilled labour availability, and how this has led to the vision of ‘digital inventory’, with (additive) manufacture at the point of need. Elving gave an example of this approach already being applied in the case of a critical part for an industrial jack-hammer. The original part is additively manufactured, but in addition, spare parts are made (using Markforged technology) on-demand in the country where they are needed, saving inventory and shipping delays. While maybe only one per cent of parts could be made this way at present, Richard challenged the audience to consider how this might change in the next ten years. Markforged’s origins lie in the development of an innovative 3D printer that simultaneously lays a skeleton of continuous carbon fibre filament while printing a nylon matrix reinforced with chopped carbon fibre or Kevlar. The next innovation was to combine the printing technology with a software design and production platform so that parts can be designed, optimised and produced with great reliability and minimal human input. Markforged’s second technical printing innovation is a composite filament of metal powder, wax and polymer material that can be spooled, allowing safe and convenient 3D printing of metal powders. Metal components are first printed, then the wax is washed out, while a final sintering operation burns-out the polymer and consolidates the metal. Markforged sells the metallic printing material and manufactures the production system comprising the proprietary printer, automated wax wash-out unit and automated sintering unit. A significant part of the value proposition is that the printable metals (currently 17-4 stainless, Inconel, copper and tool steel) have all been developed, tested and optimised for consistent production and performance. The integrated software handles the design, including internal lattice structures and allowance for shrinkage during sintering. Elving reminded the audience that these machines are a world away from consumer-grade 3D plastic filament printers. Carbon-reinforced nylon components are equal to aluminium alloys in many applications, while additively manufactured sintered metal are commonly lighter than conventionally manufactured parts. At present, the working volume for Markforged printers is approximately a 350mm cube. The Markforged business model has parallels with other software businesses with cloud-based computing networked machines and digital transmission of design and manufacturing instructions. Feedback on machine performance and utilisation allows improvements to be made through software updates to machines and to design and production management software; increasing uptake leads to an improved knowledgebase, and in turn, to improved user productivity. The company claims “the Digital Forge lives in the cloud, powered by AI. It collaborates, scales, and gets smarter with every print.” Elving concluded his talk with a glimpse into the near future as Markforged continues the development of its blacksmith adaptive additive manufacturing software. This is based on the use of artificial intelligence techniques to monitor and analyse operating data from its printer fleet. Richard pointed out that printers are fitted with currently unused in-built laser metrology in anticipation of future software upgrades. Questions included weldability (yes, if so-designed), potential for printing precipitation-hardening metals (not yet clear) and the ratio of metal printers to sintering furnaces (printers are typically the bottleneck). To sum up, Elving emphasised the point that the key to take-up of additive manufacturing is reliability: “press the button and it just works”.