
32 minute read
Feature
Materials science delivers a suite of endless opportunities—it has the power to revolutionise virtually any product across Australia's manufacturing industry.
Materials science and engineering is a big job. The practice of sourcing existing materials, and scientifically engineering them for future use, has transformed existing societies and contemporary cities. From selecting and processing existing materials, to the development of new materials through rigorous research and design, materials science engineering brings complex technological ideas to life. For centuries, scientists have been perplexed by understanding processproperty relationships, which involve the structures and properties of materials. In addition, scientists have analysed the formability of new materials; and integrated this knowledge into process modelling for enhanced manufacturing. Today, every human-made product— from roads and bridges to schools; semi-conductor chips and medical equipment—relies on research into microstructures, modelling, and technological innovations. But without advanced science and materials engineering, the world as we know it would not exist. The practice of materials science engineering allows the quality of life to be improved through greener, costeffective, and advanced developments. In advanced economies, like Australia, manufacturing is an essential part of nation building for the future. Advanced manufacturing allows nations to remain competitive, smarter, flexible, and cleaner. As such, materials science is transforming a new generation of space exploration; new materials for the medical sector; energy storage materials; and other environmentally friendly ventures for a greener planet. Traditional thinkers may feel challenged by advances in materials science, which disrupt global supply chains and challenge existing thinking. But materials science provides a suite of endless opportunities. Together, materials science and engineering can revolutionise existing supply chains for virtually any product or service across a range of industries. Crucially, materials science requires cross-sector collaboration between researchers and local manufacturers for the future.
How Does Materials Engineering Help Manufacturers?
Materials science and engineering improves Australia’s manufacturing industry. New and improved materials require manufacturing to turn them into engineered products. The practice of materials science analyses material components, like the existing composition and microstructures. Together, scientists and engineers examine how a material’s composition and microstructure are altered when its properties are changed to create new, and more efficient materials. In fact, up to 70 per cent of the cost of new products is a result of its materials. As such, it is crucial that scientists understand the composition of materials to determine a new product’s long-term success. Materials engineering helps Australian manufacturers to get the balance right and meet specific targets and quality control measures. Together, this process ensures that all recreated or new materials are: • Durable, and do not degrade or prematurely fail • Cost-effective • Safe • Easily fabricated to create new components and joints In all, materials science is a collection of existing materials that are welded, fabricated and joined. They are designed to meet strict product performance, cost requirements and reliability targets. As such, it is pivotal to: • Select materials that satisfy a range of component and joint performance, reliability, and cost requirements • Use control measures that guarantee the properties of materials that make up components and joints to consistently meet tight specification requirements Materials science does not leave any stone unturned. It considers the shape, dimensions, weight, texture, and features of materials for enhanced mechanical construction for optimum component and joint performance. As such, materials engineers work collaboratively with Australian
manufacturers to select materials that satisfy their needs and meet the requirements of the future. Together, quality control measures ensure the properties of materials meet certain specifications for industry-wide utilisation. Controlling the variation of properties in materials requires: • A thorough analysis thorough design and process specifications with all material requirements and details— like composition, microstructure, and properties—listed. • A strict process for selecting suppliers that are capable of providing materials that meet material properties requirements. • Using advanced manufacturing and assembly protocols that minimise error and budget blowouts.
A Collaborative Approach for A Greener Future
Many countries are taking advantage of advanced materials to develop cleaner energy technologies for a more sustainable future. In fact, the Chief Executive of CSIRO, Dr Larry Marshall believes material science will be a gamechanger as Australia pivots towards a net-zero emissions future. “Australia’s future economic prosperity will depend on how well we can use our vast energy and mineral resources to play to our strengths and create new opportunities through the global transition to net zero emissions,” Dr Marshall said. “There is a wealth of opportunity in front of us that will only be fully realised by developing a Team Australia response.” CSIRO’s Critical Energy Minerals Roadmap has unlocked increased potential for Australia’s mining sector to capitalise on the opportunities posed by materials science. The roadmap turns mineral resources into high purity materials. CSIRO’s Director for Mineral Resources, Jonathan Law added that Australia could increase the value of local mineral exports, enhance local manufacturing, and strengthen global supply chains by linking materials science with manufacturers. “Australia has a real opportunity to operate all the way along the energy value chain, from extraction to processing, separating, refining and manufacturing high value materials and products,” Law said.
Closing The Loop: From Research To Project Utilisation
Australia is at the forefront of linking materials science to industry, through strong research partnerships that boast high utilisation outputs. In one project, the Advanced Manufacturing Growth Centre (AMGC) is developing a world-first geopolymer and carbon fibre solution, which offers durability like concrete. Together, AMGC is working with Austeng, a Victorianbased engineering firm to research, to design and develop a solution that offers superior thermal stability and a higher corrosion resistance. A shortfall with existing concrete is that is uses steel rebar, which rusts and breaks the concrete over time.
But Austeng’s Managing Director, Ross George, said the project delivers “a cure for concrete cancer”. Materials scientists at AMGC and Austeng have discovered that carbon fibre and geopolymer will not rust. It is also acid and salt-resistant, and can accommodate higher temperatures. George said the new material provides a suite of benefits for manufacturers. “It’s actually got better flexural strength than concrete.” “Basically, you can dump it in a tub full of acid, you can light a fire underneath it, you can put it next to salt water and it won’t degrade, it won’t rust, and it’ll still be there in 100 years or more,” he explained. George added that the new bridges will require “zero maintenance” if the new material is used. The project also meets strict budgetary requirements. It is estimated to cost $120,000. But the project is expected to provide $20 million in export revenue, as part of its early earnings forecast. In addition, it will create a domestic manufacturing capability for carbon fibre and create several jobs as part of its commercialisation venture. This project was supported by an industry contribution of $85,000; government funds of $50,000; and inkind contributions of $35,000. The project will also provide a range of qualitative benefits to the Australian manufacturing market, including: • Increased spending on research and development to validate new and complex products, specifically for the construction industry • Advanced industry expertise and knowledge by providing greater collaboration with end-user partners • Increased energy efficiency and performance, as compared to traditional products such as concrete The project has several potential research utilisation outputs for Australian manufactures and suppliers, including interest from The City of Greater Geelong, which has published a procurement for innovation tender. If this project is successful, the product will be used in three local pedestrian bridges across Geelong. The City of Greater Geelong currently owns and maintains around 160 bridges. It spends up to $200,000 in annual maintenance costs, which would be significantly reduced if the AMGC and Austeng project is successful. AMGC forms a crucial part of the Federal Government’s Industry Growth Centre Initiative, which drives industry-focussed innovation, competitiveness and productivity, across the nation’s local manufacturing industry.
Tec.Fit’s Manufacturing Expertise Provides A Point of Difference
Similarly, Tec.Fit is a manufacturing company that operates in the textile, apparel, machinery and equipment space. Tec.Fit aims to disrupt the global clothing industry by providing retailers with customised garments online. The company has developed a humanbody scanning smartphone application that converts 2D images into precise 3D digital layouts of the purchaser’s body and their measurements. In addition, a second-generation prototype 3D printer complements the Tec.Fit team by using digital layouts to produce the customised clothing. The new technology provides many benefits for Australian clothing manufacturers, who typically throw away over 25 per cent of their returns.
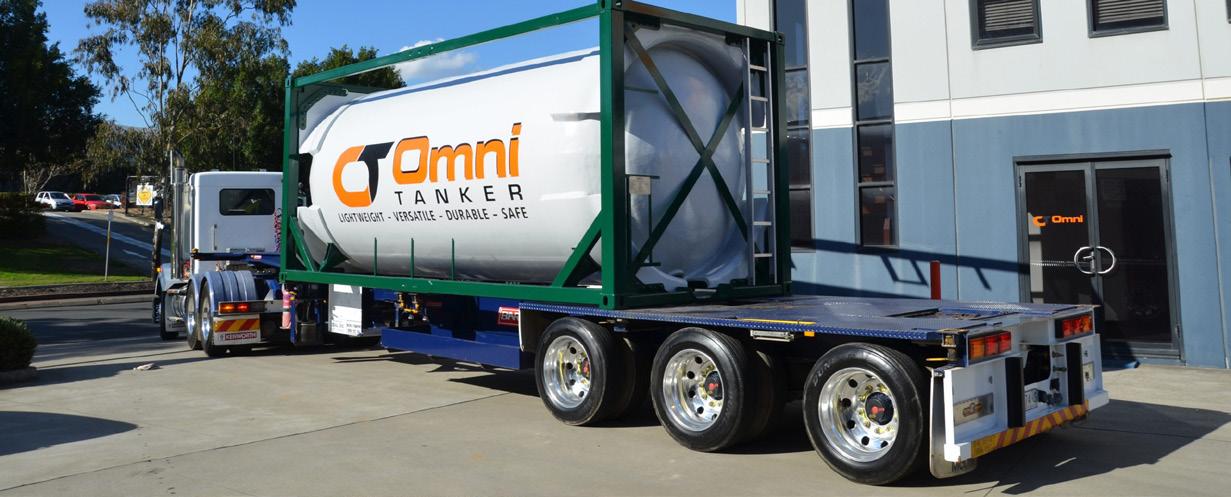
Omni Tanker is developing two types of carbon fibre reinforced polymer tanks for storing and transporting cryogenic liquid propellants.
Clothing manufacturers can use this technology to produce tailored garments like wedding dresses, wetsuits, and uniforms. Together, this innovative materials science is helping Australian manufacturing: • It reduces the return rate of online clothing purchases by 95 per cent • It reduces fabric wastage that ends up in landfill • It lowers CO2 emissions across the entire supply chain, including raw fabric production, garment manufacturing, warehousing, freight and returns logistics • It reduces working capital that is typically invested in stocks • It reduces warehouse operational demands • It reduces the overall amount of raw materials used in production In all, Tec.Fit’s technology enables retailers and clothing manufacturers to connect and provide fresh, and valuable services through a unique global platform. The company is also expecting to provide a boost to the Australian economy. In the 2023 financial year, the company has estimated revenue to be between $53 million and $139 million. Tec.Fit also estimates this project will generate more than 15 skilled labour jobs within the first two years of its completion.
Living Life in The Fast Lane with Advanced Composites
Jon Partington has spent over two decades in the automotive industry, where he has gained innovative skills and expertise on carbon fibre-based materials. “I guess carbon fibre is very engineered, it is very considered, but at the same time it is really a young technology, so there is lots of opportunity for innovation and new ideas and development,” he said. But Partington, who is also undertaking a PhD in advanced composites, has combined his expertise with his passion for cycling. “I have been a keen competitive amateur cyclist on the road, and recognised there was an opportunity within the composites space to bring these two together, particularly around lightweight wheels for pushbikes.” “Polymer composites have very different qualities to metals and they process very differently; they have different strengths and weaknesses,” he said. At Partington Advanced Engineering, a multi-material approach is using digital modelling to combine composites, metals and plastics to develop new materials and structures. The design process has produced wheels, which have been trialled by elite cyclists. The company is also seeking to commercialise high-end wheels, which boast the smart and economical use. The project team has worked with industry experts and manufacturers to turn Partington’s dreams into a commercial reality. In 2018, Partington Advanced Engineering moved into Deakin University’s ManuFutures Hub, which brings a host of new collaboration opportunities between the company and industry partners. “It has put me in touch with people within engineering enterprises which are pioneering or developing technologies or starting up,” Partington said. “It puts you in a small community of people that are having similar experiences, and that can be really useful from the very basic point of just having someone to dialogue with over similar problems, or that can extend to creating new contacts and professional relationships, which might support other business activities in the future,” he concluded.
Bolstered Tanker Capabilities
In a partnership with the University of NSW and Lockheed Martin, Omni Tanker is developing two types of carbon fibre reinforced polymer tanks for storing and transporting cryogenic liquid propellants. These tanks will offer chemical resistance; improved thermal insulation; low gas permeation; and light tank weight; with enhanced thermal insulation properties. They will provide significant benefits to space and hydrogen transport operations. In developing the tanks, the project team has characterised commercially available materials; conducted multiple tests; and analysed structural design processes. This project will ensure a higher trade intensity, and increased geographical reach for Omni Tanker. By 2026, the company is expected to reach $7 million in revenue as a result of strong research partnerships, and capitalising on the latest in the materials science space.
How FormFlow’s C90 Bend Became a World First
Source: Sally Wood
An innovative manufacturing plant in regional Victoria is using Industry 4.0-enabled manufacturing technology to transform materials science in Australia. FormFlow brings great ideas to life. Since it was established in 2016, the company has commercialised a world first metal forming technology and created a range of unique building products. The company draws on cutting edge technology and expertise to upscale its production outputs and capabilities, which has opened new pathways for commercial and residential modular buildings across Australia. FormFlow is based in Geelong, Victoria, and employs 15 staff who operate across a 1,300m2 workshop. Several students and apprentices also undertake internships at FormFlow, which builds on the company’s commitment to a stronger manufacturing sector into the future. In addition, the company works with a range of partners, including Deakin University researchers and the Innovative Manufacturing Cooperative Research Centre (IMCRC). Together, these partners have developed a new manufacturing cell to control and optimise the company’s corrugated steel-bending process for greater use. Dr Matthew Dingle is the Managing Director at FormFlow, who said the steel-bending project represents a vital step in FormFlow’s technology development and commercialisation journey. “FormFlow’s bending technology is unique. It is a secondary forming operation that relies on the theory of ‘folded developables’ to limit material deformation in incoming roll-formed strip to simple bending, while forming a complex shape, such as a 90-degree angle,” he said. FormFlow’s operations are backed by Industry 4.0 principles— focussing on the automation of traditional manufacturing with new technology—and will allow high volume manufacturing of building products to be consistent in quality and shape. The project will transform FormFlow’s processes and outputs to become a trailblazer in the materials science and engineering space. BlueScope, who markets Australia`s iconic COLORBOND® building products and technologies, has recognised the value of FormFlow products and has signed an exclusive licence to commercialise the FormFlow C90 (90-degree bend in corrugated strip) as LYSAGHT CUSTOMFLOW™ in Australia. For the process to work, the incoming corrugated strips need to conform to the surface contours of the bending tool profile. “Unfortunately, this is often not the case as different steel manufacturers use different profile shapes and material parameters.” “Thus, being able to trace the incoming profile shapes and material properties in real time and adjust the technology accordingly will enhance our bending process significantly, allowing us to respond to different customer requirements and deliver products of greater quality,” Dr Dingle explained. The company’s Industry 4.0 transformation is led by Associate Professor Matthias Weiss, who forms part of Deakin’s Institute for Frontier Materials (IFM). He said that his team was looking forward to taking FormFlow’s bending technology to the next level. “We are taking a new approach towards process monitoring and control of secondary forming operations. By linking load signatures measured throughout the bending process to changes in incoming profile shape and material parameters, we hope to develop a proactive routine for FormFlow’s shape control,” Associate Professor Weiss said. The C90 FormFlow Bend, which is a world first invention, was unanimously voted the winner of ‘Over 40 Great Innovations’ in season four of Channel 10’s ‘Australia by Design: Innovations’. This innovation enables sharp bends to be created in corrugated iron. The technology changes traditional design and construction industry practices as it ensures a smooth transition between corrugated sheet sections across a range of different angles. “It is a structural joint and it has all sorts of benefits and it looks great. Before this, if you wanted to connect bits of the roof or bits of the wall, you needed to put two flat sheets and a cover over the top. Now you can do it in one piece,” Dr Dingle explained. The C90 bend offers smoother transitions between corrugated sheet sections across a wide range of angles. It leaves clients with a distinct interlocking system that is strong, safe and reliable. Likewise, David Chuter, Managing Director and Chief Executive Officer at IMCRC, said the outcomes of this research partnership will have farreaching benefits. “By applying smart technologies, the project removes the main barrier for a much wider application of the technology.” “It opens the door for FormFlow to upscale their manufacturing capabilities and expand their business model—not just in Australia, but globally,” Mr Chuter said. FormFlow’s ‘no gaps’ solution is a winner for all clients:
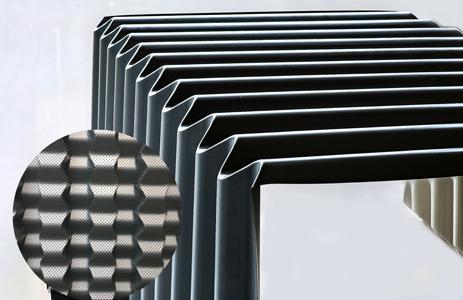

From this To this
• Provides better insulation • Lowers risk of ember attack and improves bushfire safety • Stronger than conventional corners • Clean and attractive solution • Eliminates ingress of dirt • Provides watertight and airtight finishes "The process has received praise from developers and architects, who now can produce sharp bends and ideas that are not matched by other similar technology,” Dr Dingle said. Associate Professor Weiss has been involved with sheet metal forming research at Deakin for nearly a decade. He said the “Eureka moment” occurred when the FormFlow Bend was proven. At the time, ten engineers were present, with “all of them standing there saying it couldn’t be done”. But Weiss said the innovation “came out perfect”. “We were very proud and very excited about the future,” he explained. The company has global markets in its sights, that draw on the cutting-edge technology and expertise that will upscale its production capability. FormFlow’s strong commercial interest has been sparked by the production of ‘tiny homes’ and eco-friendly construction. “It’s all about reuse and recycling, and also being able to use recycled content in our base materials.” Dr Dingle said. FormFlow has transformed the FormFlow C90 technology into a prefabricated building system, and commercialised it as FormFlow Living. FormFlow Living provides modular building systems that enable flexible, cost-effective construction of small units through to full-size family homes, at a significantly reduced cost, fostering a new approach to prefabricated modular building. “The FormFlow Bend is a world first; there’s nobody else in the world doing that. The building system may not be as revolutionary as our C90 technology, but I think we’re taking a unique approach to it,” Dr Dingle said. In collaboration with Professor James Doerfler from Deakin`s School of Architecture, FormFlow has also developed emergency shelters and isolation facilities that can be rapidly deployed for people impacted by natural hazards. These services will also be crucial for quarantine arrangements in future health crises or pandemics like COVID-19.
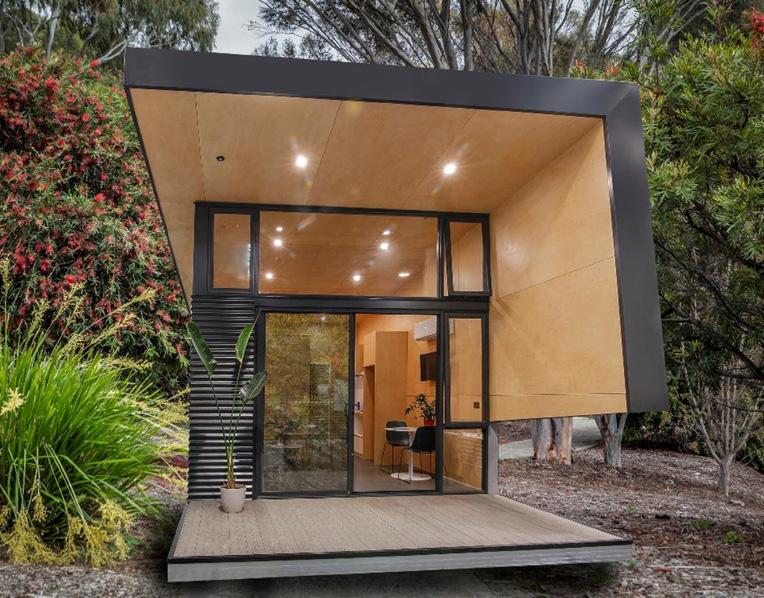
FormFlow's Work In Action
FormFlow is committed to real-world differences. For example, people who visited Melbourne’s Federation Square may have recently noticed the Future Food System—a three-storey building developed by sustainability advocates. The Future Food System demonstrated a fully self-sufficient, zero-waste dwelling. “The science behind FormFlow`s C90 core technology was developed by John Duncan, a Deakin Emeritus Professor who now lives in New Zealand,” Dr Dingle said. "He was a mentor for Matthias and I when we were doing our PhDs. It’s based on the mathematics of origami, a clever but deceptively simple process.” With the commercialisation of FormFlow`s new C60 (60-degree bend in corrugated sheet) on the way, the company is looking to expand its building technology to interconnected wall and roof cladding (gable roof) solutions and structural panel joints solutions for architectural sheds and buildings. These complex structures provide a suite of environmental benefits and have an airtight seal to deliver increased insulation. “It’s particularly good in bushfire-prone areas. It can prevent things like ember attacks, where embers make their way into the building envelope through gaps in the structure. In traditional building methods, there’s nearly always gaps in the structure. With our system you don’t get anything,” Dr Dingle explained. In collaboration with renowned bushfire architect, Ian Weir, FormFlow has extended the modular prefabrication approach to allow for BAL-FZ, full flame zone, Ratings, allowing the platform to help address the severe challenges in Australia around bushfire rebuilding and affordability.. “FormFlow`s vision is a world where everyone has a bright future and a home they love. To achieve this we innovate, refine and scale smart building solutions that benefit the environment, society and future generations” Dr Dingle said. The future of Building in Australia is here now, and it is powered by FormFlow.
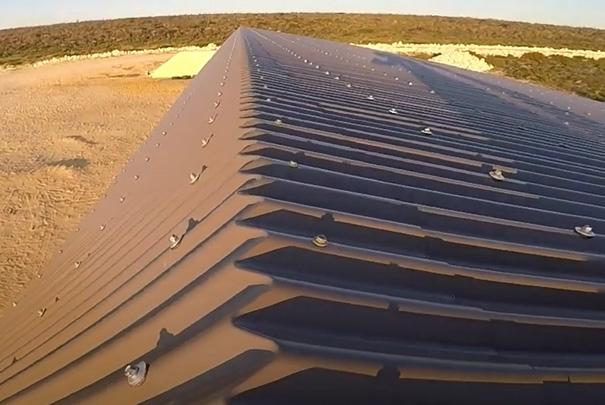
The FormFlow C60 at Earthship in Jurien Bay, Western Australia.
Quickstep’s Composite Components Lead Australia’s Defence And Aerospace Sector
Source: Sally Wood
Quickstep is Australia’s largest independent manufacturer of composite aerospace components. The company services a range of clients in the aerospace and defence industries—from small operators to the big players like Northrop Grumman, Lockheed Martin and Boeing. Quickstep seeks to bring materials science and local manufacturing to life in their state-of-the-art 16,000m2 aerospace composite manufacturing plant in Sydney, and their Research and Development centre in Geelong, which is also their Advanced Air Mobility (AAM) manufacturing Center of Excellence. Nearly 300 employees work for Quickstep, including staff based in the United States, who work closely with US-based defence and commercial aerospace clients. All employees are specialists in defence products, commercial aviation and aerospace, and advanced applications. Above all, the company is dedicated to innovation through research and development of new and exciting materials.
Taking To New Heights With Advanced Technology
Quickstep is a consistent player in the aerospace sector, where the company proudly welcomes new clients and projects. Quickstep supplies Vertical Tail Assembly components to BAE Systems for the F–35 stealth fighter aircraft. In December 2020, the company announced the production of its 10,000th component for the F–35 joint strike fighter program, representing around $250m in revenue over the last seven years. Quickstep’s Chief Executive Officer, Mark Burgess, said the company’s manufacturing abilities are a milestone. “We are extremely proud of the trust and confidence placed in us by leading global aerospace OEM, the US DoD and the Australian DoD.” “We have built a reputation for excellent delivery, quality and cost performance and look forward to securing more production opportunities on F–35 and other advanced aerospace platforms,” he said. Each F–35 Lightning II aircraft incorporates approximately $440,000 of content built at Quickstep’s manufacturing facility at the Bankstown Aerodrome in Sydney. These aircraft are poised to change the face of the Australian Defence Force. In fact, Australia has 72 F–35s on order as part of the $17 billion AIR 6000 defence program. Quickstep also supplies the global fleet of C–130 J Super Hercules military transport aircraft with flaps. Composites are a combination of two or more materials that boast unique chemical or physical properties. The defence and aerospace sector has been a trailblazer in the composite components field, as the components are lightweight, and also enhance the performance of aircraft. Damien Quinnell, Project Manager at Quickstep, said 'no two projects are alike.'
“Quickstep dedicates substantial time and effort towards driving technological change in the composites industry via our research and development team.” “We all want to do the interesting stuff and at Quickstep, we get to work on innovative composite solutions that aim to solve real world problems. And what could be better than that,” said Quinnell. The company’s ‘AeroQure’ method of production has paved the way for premium quality, lighter materials, and cost-effective production. AeroQure is a patented technology that moulds and cures large volumes of carbon fibre composite parts at high rates. AeroQure process for materials manufacturing follows a rigid process: • Low viscosity processing: which involves rapid heating of the mould and material to reduce process viscosity, improve air release and fibre wetting. • Exotherm control: a heating and cooling process to improve thermal control and heat transfer rates.
• Low pressure, low void: which assists with the removal of air and other volatiles before the gelation of the resin. This achieves void levels of less than one per cent.

“The AeroQure manufacturing process has demonstrated reduced cycle times, substantially increased automation and step-change cost performance,” Quinnell said. The AeroQure process also achieves increased performance that exceeds industry requirements in the aerospace sector. Unlike traditional autoclave practices, AeroQure offers significant advantages, including: • Reduced production time • Reduced capital investment • Reduced energy consumption • Reduced costs • Increased flexibility with design • Increased control over the cure cycle • Increased surface finishes “The project team has already worked to validate AeroQure as a viable commercial aerospace production solution, capable of meeting aerospace quality and performance requirements, as well as reduced product cost and high production rates,” Quinnell said. In addition, the AeroQure technology offers a fully automated manufacturing system for the AAM industry, helping companies productionise their prototype drones.
Research And Development In Sharp Focus
At Quickstep’s research and development facilities at Deakin University’s Geelong campus, skilled researchers, and industry experts jointly pursue a range of innovative projects in advanced laboratories. The partnerships forms a crucial part of Deakin’s ‘carbon cluster’, which bridges the gaps between research and industry. The research and development centre manages the development and innovation of Quickstep’s intellectual property and technologies. It is a enhances Quickstep’s disruptive technologies that are used in the manufacturing of carbon-fibre components. In addition, the company has harnessed the opportunities presented by Industry 4.0 to manage materials in a sustainable way. For example, Jetcam’s Crosstrack software optimises precise cutting measures and nesting that reduces the amount of material wastage across the entire company. Quickstep has also developed 3D printing capabilities that use templates and automated production to minimise wastage and error. The research and technology developed at Quickstep has secured interest from CSIRO—Australia’s leading scientific research organisation. CSIRO has analysed Quickstep’s polymer composites technology to add value and find potential users across the Australian scientific industry. The company’s advanced polymer components are strong and lightweight. The components boast ten times the strength to weight ratio, as compared to other similar materials.
Advanced Manufacturing Front And Centre During Pandemic
Like many manufacturing organisations, the COVID-19 pandemic has altered operations. But Quickstep has leveraged its supply chain, and maintained a steady pipeline of projects during the height of the pandemic. In fact, Quickstep’s sales revenue increased by 12 per cent to $82.3 million in the last financial year. Quickstep’s defence contracts have ensured the company remains globally competitive. “There are very few companies in our industry who can, like us, point to strong sales growth and even stronger profit improvement at the moment,” Burgess said. At the same time, the company’s net profit increased by 44 per cent—a promising sign that Quickstep’s strategy to grow into other aerospace sectors such as MRO and AAM is bringing success. Quickstep also has a steady stream of new orders with a range of new and emerging clients, like the rail and medical industry. The company’s Chief Executive Officer said there are vast opportunities to take advantage of during the pandemic. “In our view, there is never a more important time to invest in your business than during periods of instability.” “New technology is always exciting, but improved efficiency and enhanced margins are more exciting still,” Burgess said.
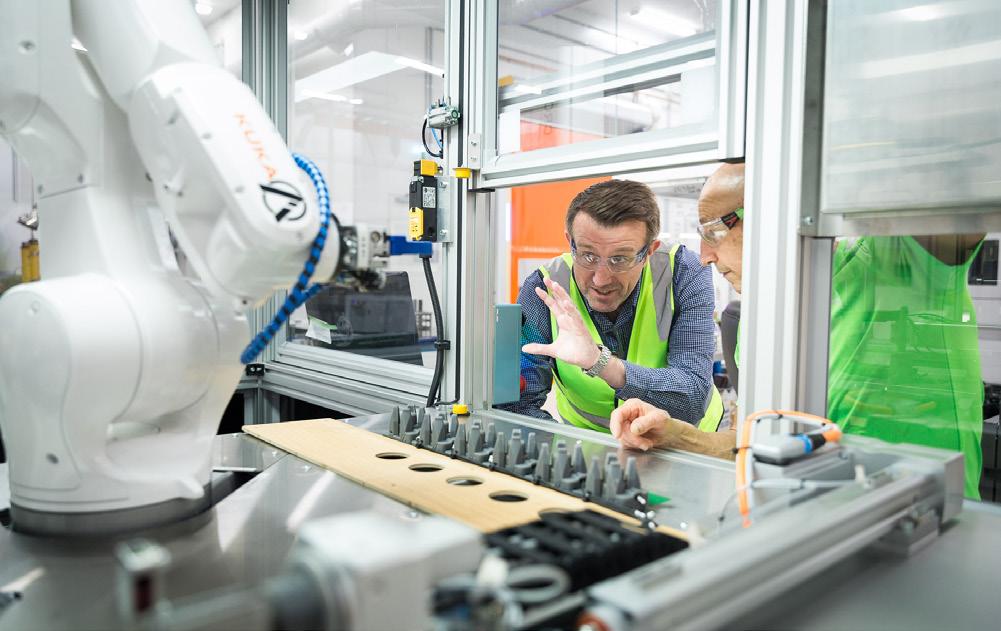
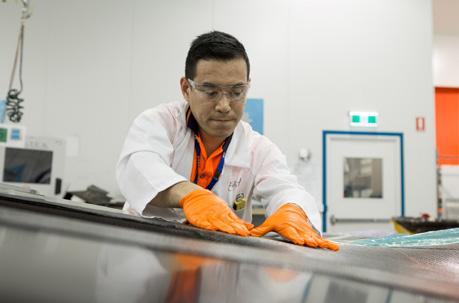

Company Profile: AML3D
Source: Sally Wood

AML3D is a globally accredited Wire Additive Manufacturing facility, manufacturing high-strength parts from a wide range of feedstock materials grades. Their innovative manufacturing technology is disrupting traditional metal manufacturing processes, providing a green, lower energy and lower waste solution. AML3D’s patented Wire Additive Manufacturing (WAM®) process includes the use of welding science, robotics automation, materials engineering and proprietary software to support smarter, leaner and greener manufacturing. The company works closely with a range of universities and scientific bodies, such as CSIRO, to find new ways of manufacturing. AML3D combines welding science with robotics, metallurgy and proprietary software. The company's process produces automated wire-fed 3D printing in a freeform environment, which can be set up anywhere and manufacture parts of any size. AML3D is the only metals diversified large-scale WAM® production facility in the Southern Hemisphere and is capable of producing finished parts and components to a certified standard under an accredited Quality Management System. The award of the Australian patent for its WAM® process has allowed AML3D to expand further. In July 2021, they launched their multi-million dollar headquarters in Adelaide. AML3D’s Managing Director, Andrew Sales, founded the company after a lifelong interest in welding and joining. Sales is a mechanical engineer and welding engineer who was inspired when studying 3D metal printing using arc welding technologies at Cranfield University in the UK. “The opening of this incredible facility has been a long-time dream of AML3D and marks yet another significant milestone for our company and our journey alongside the recent granting of our patent. Our new premises will enable AML3D to keep up with accelerating demand in 3D printing, while continuing to push boundaries in technological research and development,” Sales said.
Robot Welders Transform Metal 3D Printing
AML3D is disrupting the welding process with innovative technology. The traditional joining process of arc welding, or melting a wire with an electric circuit to form molten beads, has been revolutionised by the manufacturing of complex and high value parts with the assistance of robots.
AML3D uses ABB robotics to provide a faster and more efficient metals manufacturing process. Since introducing the ABB robot system in 2018, the industrial robots have been coordinated to act as welders within the AML3D system. “The welding head and torch are mounted on the robot, and the robot points and moves the welder, and so the robot is making the shape,” explains Sales. The use of robotics improves sustainability, using far less energy and saving the metal waste of the traditional methods of casting, forging and machining metals. Because the process melts metal wire rather than smelting large blocks of metals, it consumes “less energy by order of magnitudes,” says Sales.
Steel Products That Are Stronger Than Forged
AML3D has revolutionised steel products, providing ‘Additive Metal Layering’ 3D printing services at a commercial scale. This technology is utilised by a wide range of industry sectors, taking advantage of AML3D’s WAM® printed high strength steel. The steel products have Ultimate Tensile Strength (‘UTS’) 30 per cent higher than applicable global standards. Intertek, a group accredited by the National Association of Testing Laboratories, conducted the strength testing on behalf of AML3D. This testing involved printing of a series of geometrically shaped specimens
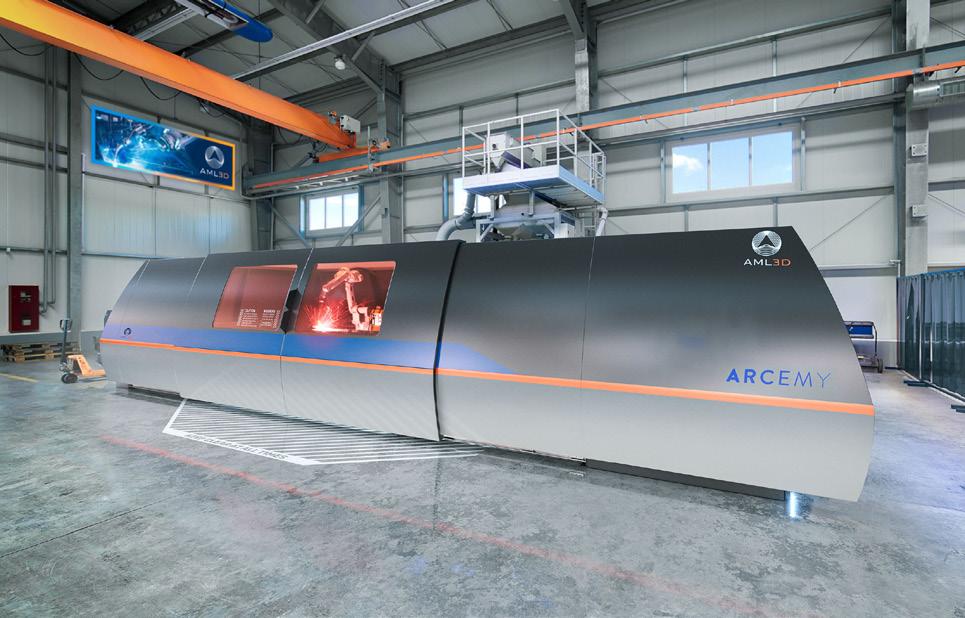
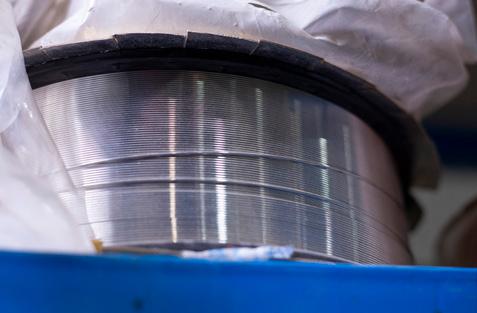

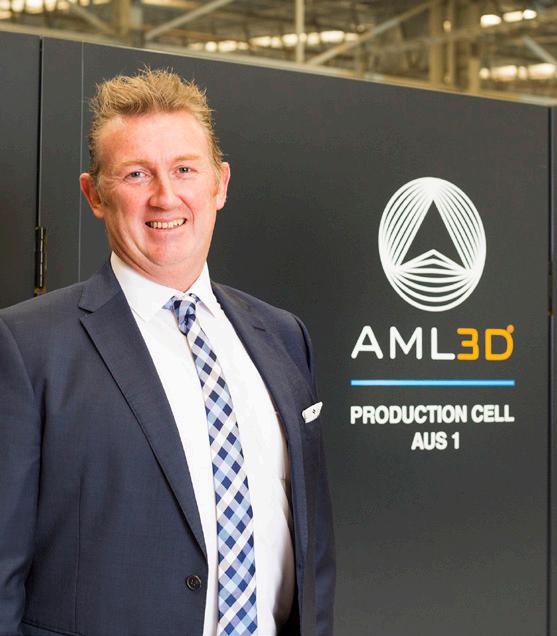

AML3D’s Managing Director, Andrew Sales. All images courtesy of AML3D.
of standardised dimensions, allowing for direct comparisons with metals produced by conventional methods. These tests have confirmed the superior strength of the WAM® printed product, demonstrating that AML3D is capable of making high strength steel components that perform better than conventionally manufactured parts. Industries including Defence, Resources and Automotive are particularly interested in the results of the Intertek testing. The WAM® process allows steel products to be produced in a way that is more cost-effective and environmentally friendly. Additionally, it highlights AML3D’s ability to disrupt conventional manufacturing within these sectors, both within Australia and globally. The results of this testing will be provided to existing and potential customers of AML3D. In a media release regarding the steel products, Sales said, “These results, which clearly demonstrate the superiority of our WAM® process compared to normal forging techniques, demonstrate what a ‘game changer’ we have to offer. The independent, third party validation testing confirmed our own data regarding how WAM® metal printing of high strength steel offers significant advantages in strength and weight reduction opportunities compared to other conventional manufacturing techniques. We look forward to near term discussions on these results with our current customers.”
Research And Development
AML3D has been working closely with industry and academia for some time, including a collaboration with Flinders University and BAE Systems Maritime Australia in large-scale metal additive manufacturing. Recently, the company announced that they are joining BAE’s and Flinders University’s ‘Factory of the Future’ to further enhance large scale additive manufacturing. This Research and Development (R&D) facility will be located at the Tonsley Innovative District in Adelaide. Sharon Wilson, Continuous Naval Shipbuilding Strategy Director at BAE Systems Maritime Australia, welcomed the addition of AML3D and their work in additive manufacturing. “The establishment of a permanent Line Zero facility will support the development of new manufacturing techniques and technologies within a factory-like environment that will ultimately be adapted to the state-of-the-art digital shipyard at Osborne, and beyond. This supports the growth of an enduring and uniquely Australian sovereign industrial capability that supports the nation’s continuous naval shipbuilding strategy for generations to come,” she said. Testing and trials of metal additive manufacturing systems will soon be underway for the potential application in naval shipbuilding. The collaboration will grant students at Flinders University the opportunity to participate in the design and delivery of metal additive manufacturing research projects. Metal additive manufacturing curriculum and training modules are being introduced, as well as work on digital shipbuilding. Flinders University will also provide access to testing and validation equipment during the project. It is expected that the partnership will attract more students and researchers to the ‘Factory of the Future’. “The additive manufacturing R&D facility is a shining example of the capacity for collaboration in advanced manufacturing at ‘The Factory of the Future’ pilot site, which will enable joint research into and enhanced uptake of technologies and processes, so we can leverage the potential benefits for shipbuilding and advanced manufacturing in Australia,” Professor John Spoehr, Flinders University’s Pro-Vice Chancellor Research Impact, said. “The opportunities for additive manufacturing are endless and our researchers and students look forward to collaborating with AML3D to explore all the potential applications.” Andrew Sales also commented on the advantages of the R&D facility. “The trials and research projects to be undertaken at the facility in conjunction with BAE Systems Maritime Australia and Flinders University will enable AML3D to further develop its large-scale metal additive manufacturing capability through added features such as in process measurement, monitoring and adjustment that will improve quality,” he said.
Research To Examine Whether 'Strong as Steel' Spider Silk Can Be Replicated for Manufacturing
Source: Sally Wood
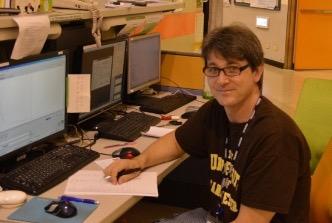
University of New South Wales (UNSW) Sydney has been awarded a grant to assess whether mimicking spider silk can be used in clothing, medical devices and prosthetics. Researchers will examine whether spider silk can be replicated for use in military and sports clothing, and medical devices and prosthetics as part of an international study funded by the PLuS Alliance. Dr Sean Blamires is from the Evolution and Ecology Research Centre at UNSW Science, he also leads the PLuS Alliance project. “Spider silk is stronger than steel and Kevlar. Tapping into its secrets could herald a revolution in manufacturing.” “Several high-performance materials could be produced such as ultra-tough ropes and cables, light-weight safety uniforms, prosthetics, binding sutures and other medicinal materials,” said Dr Blamires. Dr Blamires was selected after a call for submissions from researchers at King's College London, UNSW Sydney, and Arizona State University, which all form part of the PLuS Alliance. The PLuS Alliance seed grant will provide a much-needed opportunity to develop and assess recombinant spider inspired silk proteins, in the hope of mimicking the strong, non-toxic and antibacterial silk. Spider silk is the world’s toughest natural fibre. But unlike silkworms, harvesting silk directly from spiders is not a commercially viable option. Spiders require vast amounts of space for their webs. However, individual spiders do not produce high quantities of silk, and they tend to eat each other. Research is underway at the Spider Silk Research Laboratory, which was founded by Dr Blamires, to better understand how to produce spider silk biomimetics for a range of applications. “In this age of massive amounts of plastics pollution, the creation of spider silk materials using cutting edge genetic and spinning technologies would be of great interest to industry.” “Biotech is one of the fastest growing industries right now and this project will contribute significantly to that. There’s also the potential for new green manufacturing industries to arise in the future,” Dr Blamires said. The lab has received praise from international counterparts. It has also been visited by constituents from Australia, Germany, Taiwan, and Japan. In addition, the lab has trained PhD, honours and graduate diploma students, and produced multiple research papers. Dr Blamires said that advancing the development of high performing products using pollution-free manufacturing is a “great win for society”. The PLuS Alliance seeks to provide global solutions with impact. Together, the project boasts researchers and academic experts from three continents to address global challenges and provide world-leading education to people in need. Dr Blamires’ team includes Associate Professor Christopher Marquis, who is the Director of UNSW’s Recombinants Products Facility and Dr Aditya Rawal from UNSW’s Mark Wainwright Analytical Centre. Dr Blamires has participated in a range of publications, collaborations, writing and speaking appointments where he has shared his game-changing research to a panel of experts and likeminded peers. The researchers work across biotechnological, biochemical, biophysical and bioengineering disciplines to produce and evaluate recombinant spider silk proteins for spinning into fibres using microfluidic based techniques. PLuS Alliance seed funding is available to assist in the development of research projects that address one or more of the alliance themes: • Sustainability • global health • social justice • technology • innovation. The funds that are allocated through the project enable teams to conduct preliminary work and facilitate collaboration across the three universities. The seed-funded projects are part of an ongoing drive by the PLuS Alliance to achieve international impact through collaborative research.
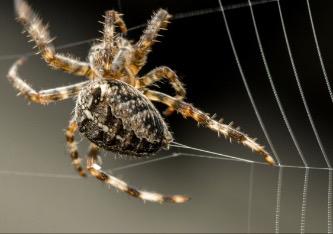
Above: Researchers say tapping into spider silk could herald a revolution in manufacturing. Image: Shutterstock.
Right: Dr Sean Blamires says the creation of spider silk materials would be of great interest to the biotech industry. Photo: UNSW.