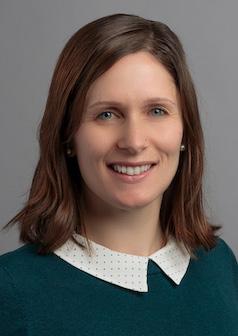
5 minute read
Women in the Industry - Alex Kingsbury
Alex Kingsbury
Alex Kingsbury is an Additive Manufacturing Industry Fellow at RMIT University, where she works to enhance links between industry and the university. These links extend across research, and teaching and learning functions at the university. Previously, Alex was the Research Group Leader for Additive Manufacturing and the Director of CSIRO’s Additive Manufacturing Innovation Centre ‘Lab22’—a metal additive manufacturing centre for industry access and research and development. In these roles, she oversaw CSIRO’s additive manufacturing research projects, both strategic and industry funded. Together with AMTIL, a manufacturing association, Alex established a national industry network called the Additive Manufacturing Hub, a body representing the interests and concerns of additive manufacturing businesses in Australia. This program of local industry engagement was the first of its kind in Australia for the additive manufacturing industry. Alex has experience in electron beam, laser, binder jetting and kinetic deposition additive technologies. She has worked more broadly in metal technologies including additive manufacturing since 2011, with a focus on powder and wire-based additive manufacturing technologies. She understands what it means to meaningfully connect industry to research and development activity. Alex’s volunteer roles include sitting as the independent expert on the Standards Australia Additive Manufacturing Technical Committee, Chair of Oceania for Women in 3D Printing, and TCT Expert Advisory board member. Alex holds a Bachelor of Engineering (1st Class Honours) with a major in metals processing from RMIT University in Melbourne and is also a Graduate of the Australian Institute of Company Directors. She is currently a PhD candidate at RMIT University. A known authority on additive manufacturing technologies, Alex is frequently called upon for expert opinion on additive technologies, the global marketplace for additive manufacturing, and forecasts for the additive manufacturing market. She has spoken at international conferences, contributed to highly respected industry publications, and worked across the media formats of television, print and radio.
Alex provided Materials Australia with some thoughts on what it’s like to be a materials engineer.
From Alex Kingsbury
I never set out to be a materials researcher, but here we are! I didn’t come from an engineering, or even a scientific family. But, an aptitude and keen interest in maths and chemistry, plus a fascination with how things worked led me to choose to study chemical engineering. After having spent some time consulting to the mining and oil and gas industries, I joined CSIRO to work as an engineer on their commercialisation projects. I was immediately thrown into the deep end of titanium metal powder research and development projects, both making it and consolidating it via a number of different processes. It was 2011, just as a process called metal additive manufacturing, also known as rapid prototyping or 3D printing, was just taking off. Little did I know, my career was just about to take off too!
Additive manufacturing, as I am sure most of you are aware, is a process where you add material layer by layer. This is as opposed to subtractive manufacturing, where an item is machined out of billet, rod or plate.
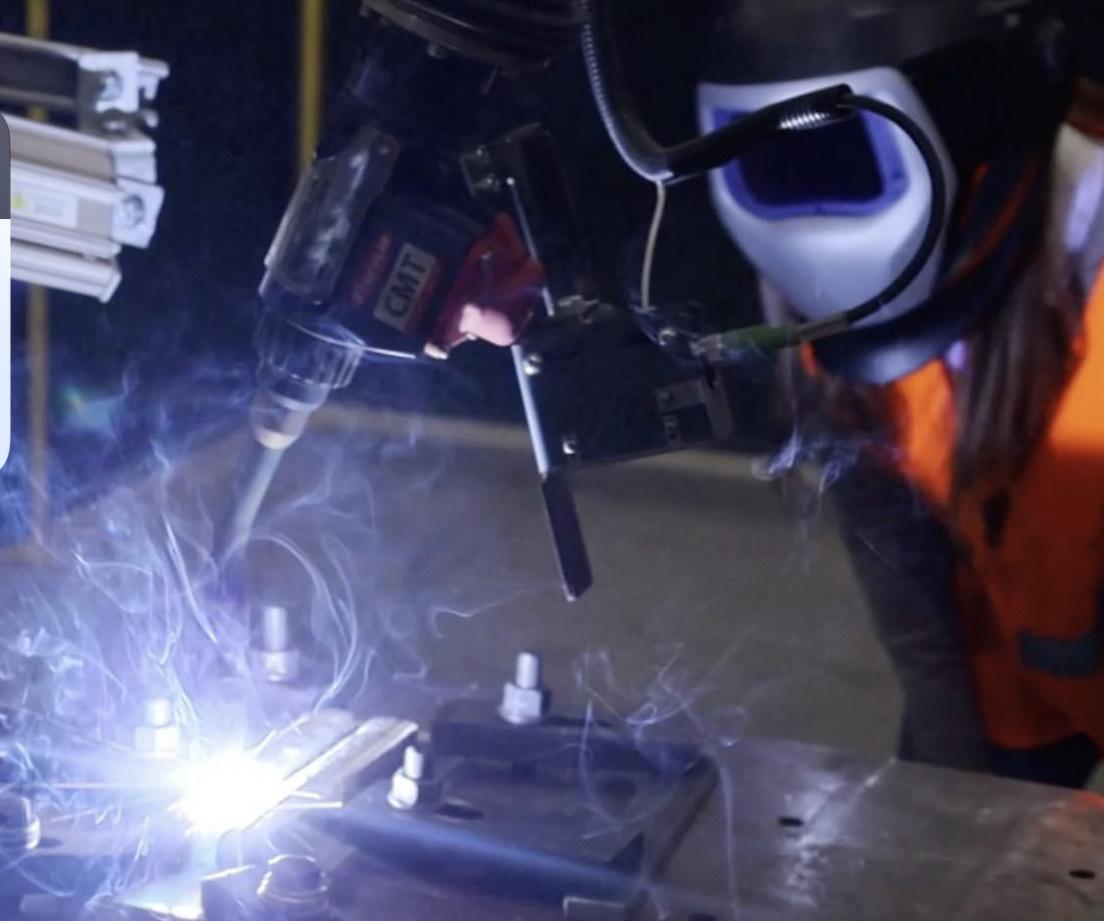
The early days of additive manufacturing started out with polymers, but advances in laser technology meant we could use lasers as a heat source to melt metal powders, layer by layer. Then it was found that different heat sources could be used, such as electron beams, and different ways of handling the powder were found, such as spraying metal powder into the path of a laser. But why use just powder? What about wire, using an electron beam or an electric arc? Do we even need a heat source? Why not spray metal powders at a substrate at supersonic speeds to consolidate them? Very quickly the additive manufacturing field found many different ways that material could be deposited in this ‘layer by layer’ fashion.
Industry 4.0 Enabling Technology
The world of additive manufacturing exposed me to the world of manufacturing, and my role at CSIRO changed rapidly as the appetite for this new Industry 4.0 enabling technology came to prominence. No longer a commercialisation engineer, I was now a research group leader and then—as my 3D printing lab grew—I became an Additive Manufacturing Innovation Centre Director.
Through those roles I spent a lot of my time engaging with the manufacturing industry, committed to understanding their needs, and assisting them to leverage the vast research capability that exists in Australia.
I did factory tours, I met founders, I presented to Boards. I came to see clearly just how important manufacturing was for our nation. We needed manufacturing, not only because to lose the ability to make things for ourselves would put us in an unacceptably vulnerable position, but also because manufacturing was a jobs multiplier in our economy. Recent pandemic related disruptions to our supply chains have brought this point into sharp relief.
Wire Arc Additive Manufacturing
But back to materials. While additive manufacturing was ‘new’, it also wasn’t. Decades of experience in metal casting, forming, welding and joining gave us the foundations upon which we could develop metal additive manufacturing technologies. The knowledge of alloys and how they melt and solidify was the basis upon which we could catapult the field of metal additive manufacturing. However, there were also some differences; building a part from a 3D model, using a layer by layer process, leads to a very different thermal history. Having the most similarities with welding, suddenly the joining process was the process. And while welding alloys are largely very suitable for additive manufacturing, particularities in the process mean that alloy chemistries, designed around this new thermal history and solidification regime, simply perform better. It is this that I am now dedicating my time and energy to, both as a PhD student and an Industry Fellow at RMIT University – designing new alloys for the wire arc additive manufacturing (WAAM) process. Maintaining a job at a university whilst also being a student is quite the balancing act; and going back to study mid-career has it’s challenges, but I have always believed that you are never too old to learn, and likewise, never too young to teach!
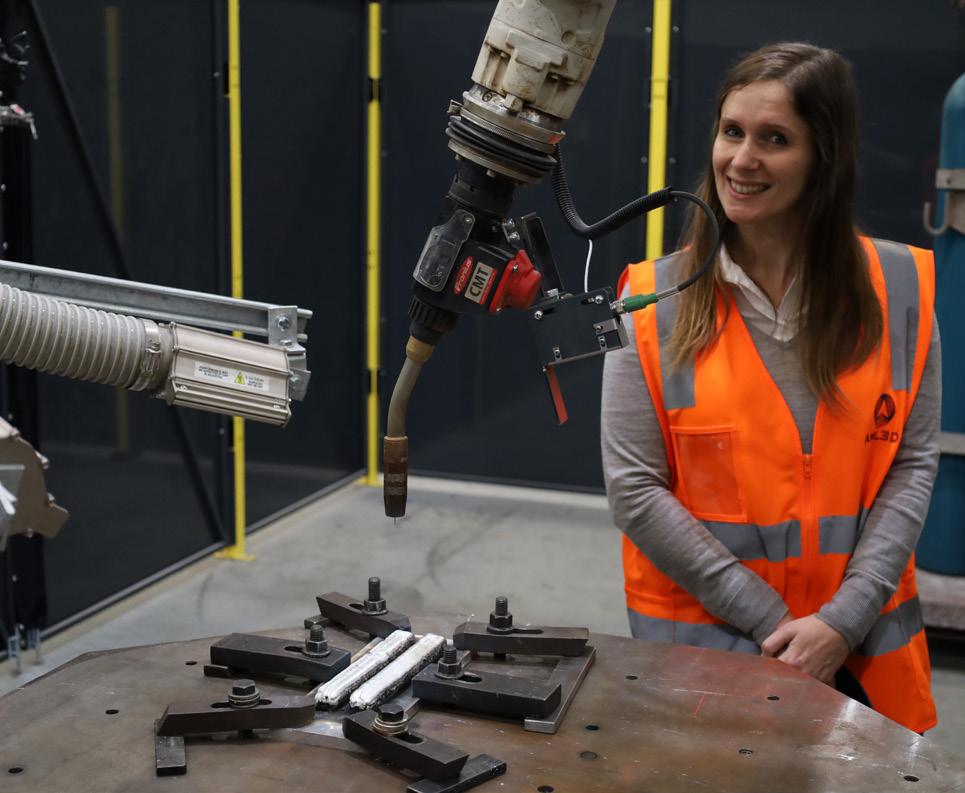
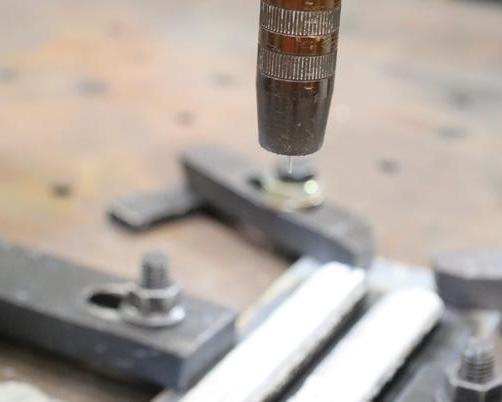
