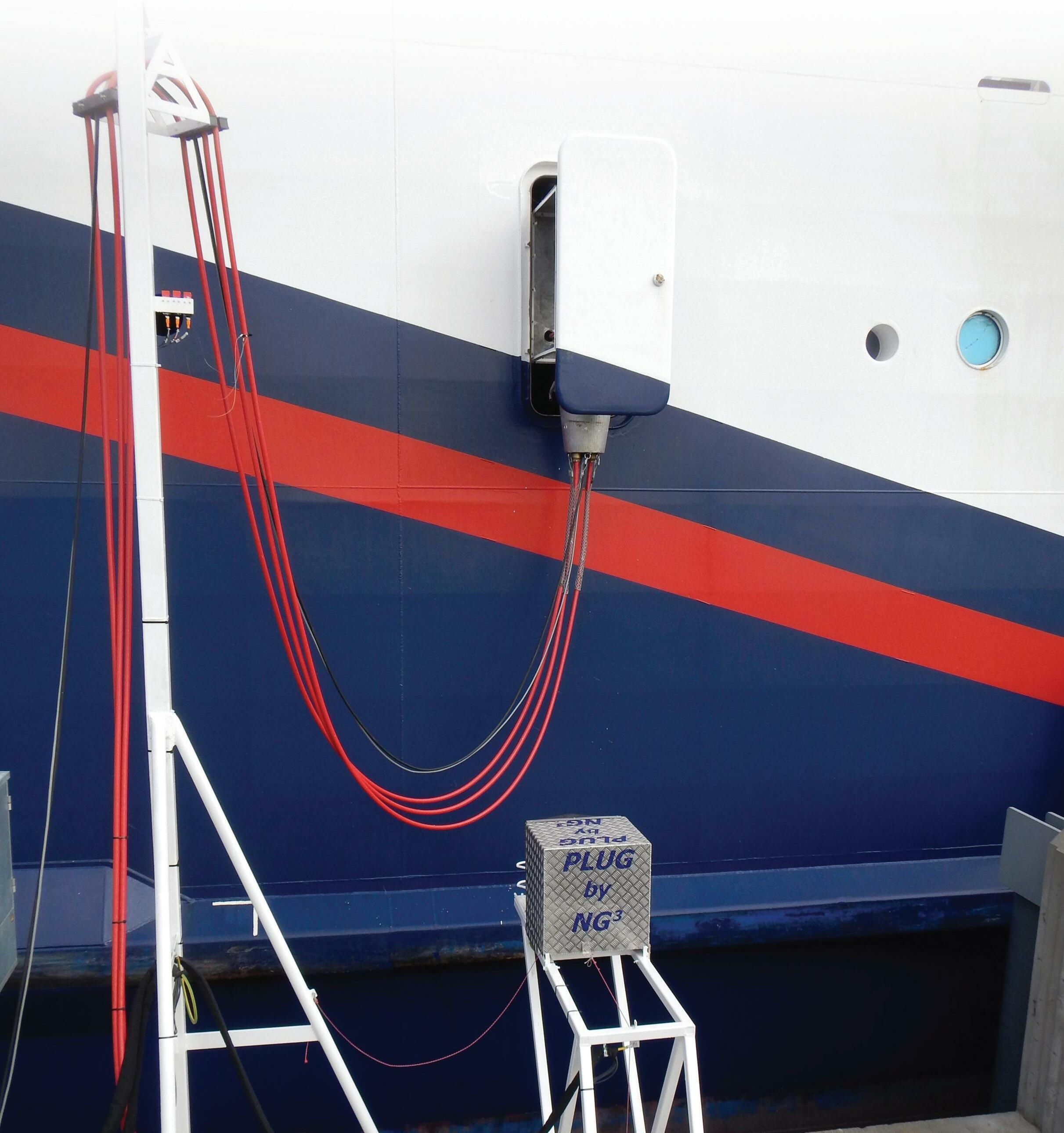
22 minute read
Shore Power
With PLUG, game changing cable management system, NG3 is making shore power even greener
ByDamienFéger,CEOatNG3
PLUG,an acronym for Power Generation during Loading and Unloading, is an innovative shore power cable management system which was introduced to the market as early as 2011, to provide a 4.5 MVA 11 kVolt shore power connection for the Color Magic ROPAX in Oslo, which was followed by the whole Color Line RoPax fleet, as well as the Hurtigruten and Havila RoPax vessels providing the Kysruten route service along the west coast of Norway.Its main design feature is that it was the world’ s first fully “hands off” connection solution of this type of vessel, providing a safe, efficient alternative to solutions based on manual connectors. As soon as the vessel is at berth, the crew has simply to slide a beam out (above the quay) to which is attached the ship side power socket, and then lower a chain toward the quay side connector. The chain is equipped with an automated hook at its end, which as soon as it is inserted and locked into the quay side connector, can hoist it, and the power cables attached to it, up towards the ship side socket.When it gets into the ship side socket, simple mechanical effects align the power exchanges contacts, so that when the chain is further hoisted up, the connection is established.With this self-mating/de-mating patented connector technology, direct handling of connector and cables is avoided, and operations can be performed by a single crew, within a few minutes. Beyond this obvious benefit in terms of safety and operational cost, in this period of resources scarcity and pressure to reduce emissions, it is worth pointing out the massive environmental gains brought by this technology.
SS2 in operation at Larvik.
One such benefit is the speed and ease of operations enabling a quick connection to shore power during shorts stops and to do so, basically, from the first to the last minute of the call.This maximises the overall environmental (and economical!) return on investment of the whole shore power infrastructure, increasing drastically its rate of use, compared to solutions based on manual connectors.As an example, for the Color Line Superspeed 1 and 2 RoPax vessels, shore power was, initially, considered only for the 7 hours long night stay, but it was found quickly that these vessels could be “PLUGGED” , as well, during the one-hour afternoon call, increasing the return on investment of the whole shore power infrastructure by 15%... while the crew were enjoying an extra hour of noise free engine room.
Secondly, compared to manual connector solutions, PLUG connector and cable weight is not a design constraint, so sizing of the power contacts and cables can be tailored to the need of the project (for example up to 2000 Ampère under 1000Volt), within a single connector and set of cables, whereas manual connectors solutions would require several units in parallel,or to raise the power exchange up to 11,000Volt to reduce the sizing of the cable and connector - generating the need for an on-board step down transformer - whose cost and implementation is a challenge for small vessels and, is anyway, an additional useless dead weight when the vessel is at sea.
Thirdly,compared to manual connector solutions, PLUG offers with a single connection, the power exchange capability required not only to cover hotel loads, but also, the massive one required to charge in a short time, the batteries of hybrid or full electric vessels. As an example, on board Color Hybrid, beyond slow charging during the night stop, a single 6,5 Mega Watt PLUG allows to boost charge the vessel’ s battery bank within half an hour, during its one hour afternoon stop, allowing this vessel to be the world’ s first to offer zero emission call capability, all operations being on battery as soon as it gets into the Sandefjord fjord.
Fourth, compared to other solutions, PLUG is characterised by an optimised use of resources: * such as steel, as by using the hull structure of the vessel itself to support the weight of the connector and cables, suppressing the need of a quay side crane; * such as copper, by avoiding the use of on-board cable reels and step-down transformer; * such as concrete, as PLUG quay side interface is lightweight and can be simply anchored on the existing quay structure; * such as electrical components such as breakers,pilot lines relays,sockets - by replacing several connections by a single one.

Fifth, by reducing drastically on-board weight, PLUG allows to reduce the deadweight to be carried by the vessel when at sea, reducing the relevant power consumption.
Sixth, by reducing drastically on-board footprint, PLUG which can be implemented within a single frame space, compared to other solutions, reduces, or even avoids, any loss of payload space on-board (for example, on Havila Capella RoPax, it was possible to implement the ship side interface between two passenger cabins, without reducing their size!), maximising, within the same environmental footprint, the vessel service capability. Seventh, PLUG solution compactness and low weight reduce its environmental impact of delivery and installation: a 13 MegaVolt Ampère ship and quay side set, enough to feed a large cruise vessel, can be delivered with just a family car and a two axles trailer, instead of a truck, and a mere forklift is needed to install the quay side interface instead of a crane.
As shore power is more and more considered as a way to reduce emissions, typically from 3% for a standard propulsion RoPax, up to 10% for a hybrid propulsion vessel and even 100% for a full electric one, it is becoming a more mature industry, which although being green by itself, cannot avoid to improve its own environmental (and economical,matching the green of emission reduction with the green of the dollars!) performance by optimising all its components.
That is what NG3 is offering, based on more than a decade of PLUG operations on board numerous RoPax vessels with its PLUG cable Management System, not only for RoPax, but as well, for other types of vessels, such as cruise ship, container carriers or tankers.
Power cables linked to shore power grid.
Greener steel solutions for port infrastructures

ByFrançoisFohl,Environmental Specialist,ArcelorMittalSheetPiling
Ports have been faced with many challenges in recent years. On the one hand, maritime traffic has steadily increased, and modern vessels keep getting bigger; on the other, our planet is struggling with greenhouse gas emissions. Ports need to expand, to build new berths, to transition their facilities to cleaner fuels and adapt their infrastructures to operate the numerous offshore wind park projects. How can they achieve these goals whilst also reducing their emissions?
Sustainable leadership
Decarbonisation is the most important aspect of ArcelorMittal’ s long-term strategy. Leading the transition of the steel industry, the group aligns with the Paris Agreement’ s goals and the European Green Deal by committing to reduce its European CO2 emissions by 35% by 2030 and to reach global carbon neutrality by 2050.
For several years already,ArcelorMittal’ s EcoSheetPile™ range of steel sheet piles have been manufactured through the Electric Arc Furnace (EAF) route from 100 % steel scrap. They are entirely recyclable and reusable up to ten times. It is a major contributor to the circular economy. Its production emits only 520 kg CO2-eq. per tonne of finished product, as certified by a specific Environmental Product declaration (EPD). For reference, the average value of the CO2 emissions for the global steel industry was around 1.85 tonnes of CO2-eq. per tonne of steel products in 2020.
To demonstrate the environmental advantages of the EcoSheetPile™ products,ArcelorMittal appointed Tractebel, an independent Belgian consulting engineering firm, to analyse this quite multifaceted topic.The engineers proposed to focus on three key indicators: technical, financial and environmental criteria. They compared three different technical solutions for the construction of a quay wall: a steel sheet pile wall, a diaphragm wall and a deck-on-piles.A realistic case study was carried out to provide a sound comparison between the three alternatives.The selected structure is a 200m long cruise ship terminal capable of accommodating the largest cruise ships. It would be built in a Belgian port, with a draught of 13m in typical soil and load conditions for a Belgian port.
Let’ s focus here on the environmental impact of the two most cost-effective solutions, and mainly on the GlobalWarming Potential (GWP), using a Life CycleAssessment (LCA).The LCA is based on the bill of quantities prepared by Tractebel and was performed byArcelorMittal’ s R&D department. It has been peer-reviewed by a panel of experts.The objective was to compare the Total Life Cycle Cost, including the burdens or benefits of the end-of-life phase, which are dismantling and recycling of the building materials. Reuse of the materials at the end-of-life was not considered in the present scenario.

Port of Egersund, Norway © Vestbetong AS
The conclusion is that the EcoSheetPile™ steel sheet pile wall has the lowest carbon footprint, with a difference of 44 % compared to the diaphragm wall (see Figure 1).A sensitivity analysis showed that modifying some of the parameters did not significantly impact the above-mentioned difference, and in no case reversed the result.This study is described in detail in the “Sustainable ports ” brochure available on https://sheetpiling.arcelormittal.com
Steel sheet piles can now be produced with even less environmental impact.ArcelorMittal’ s new brand,XCarb™ is designed to bring together all of ArcelorMittal’ s reduced, low and zerocarbon products and steelmaking activities.
Figure 1
Global Warming Potential - total impact for the quay wall
The EcoSheetPile™ Plus range,launched in 2021, is an essential part of the XCarb® recycled and renewably produced initiative. It is based on the EAF route (electric arc furnace) using 100% scrap as a raw material, and is additionally using 100% renewable electricity, from solar and wind sources connected to the same power grid as the steel mills. This allows the production of the new range with 30% lower emissions than with the usual energy mix.The gap is even higher when compared with the predominant conventional steelmaking.
Certified by a specific Environmental Product Declaration (EPD), the production of the EcoSheetPile™ Plus range emits as low as 370kg CO2-eq./t of steel produced. It comes also with a ‘Guarantee of Origin ’ certifying the renewable sources for the electricity, audited by an external third party.The lowemissions EcoSheetPile™ Plus range has already been selected for tens of projects in Europe. Three prime examples are the works on quay walls in the port of Egersund in Norway, the port of Aalborg in Denmark, and the new Canal Seine-Nord Europe in France.
A new fishing terminal in Egersund, Norway
A major fishing port expansion programme in Egersund, Norway will be built using 2,200 tonnes of ArcelorMittal’ s unique straight web steel sheet piles, in a circular cell structure. Pelagia AS is a leading producer of pelagic fish products for human consumption, and an important supplier of essential ingredients in all kinds of fish and animal feed. Located in one of Norway ’ s largest and most important fishing harbours, Pelagia Egersund Seafood has been a pioneer fish processing factory since 1993.
A new fishing terminal is being built to expand their operation in Egersund, based on circular cell structure that will be filled up with sands dredged out from the seabed. The main contractor for this project is Vestbetong AS, while Fundamentering AS is the sheet piles driving contractor.
The circular cell structure made from ArcelorMittal AS 500® straight web steel sheet piles was considered the most appropriate in this case, as it will collect the sand dredged from the seabed to cope with the increased traffic and larger vessels. It will store the dredged materials safely and prevent any pollution of the sea water. A key differentiator that convinced the client to choose an ArcelorMittal steel solution for this expansion project is the availability of the low carbon footprint EcoSheetPile™ Plus range, made from 100% scrap and with 100% renewable electricity from wind and solar sources.The new range will reduce the total carbon footprint of the project.
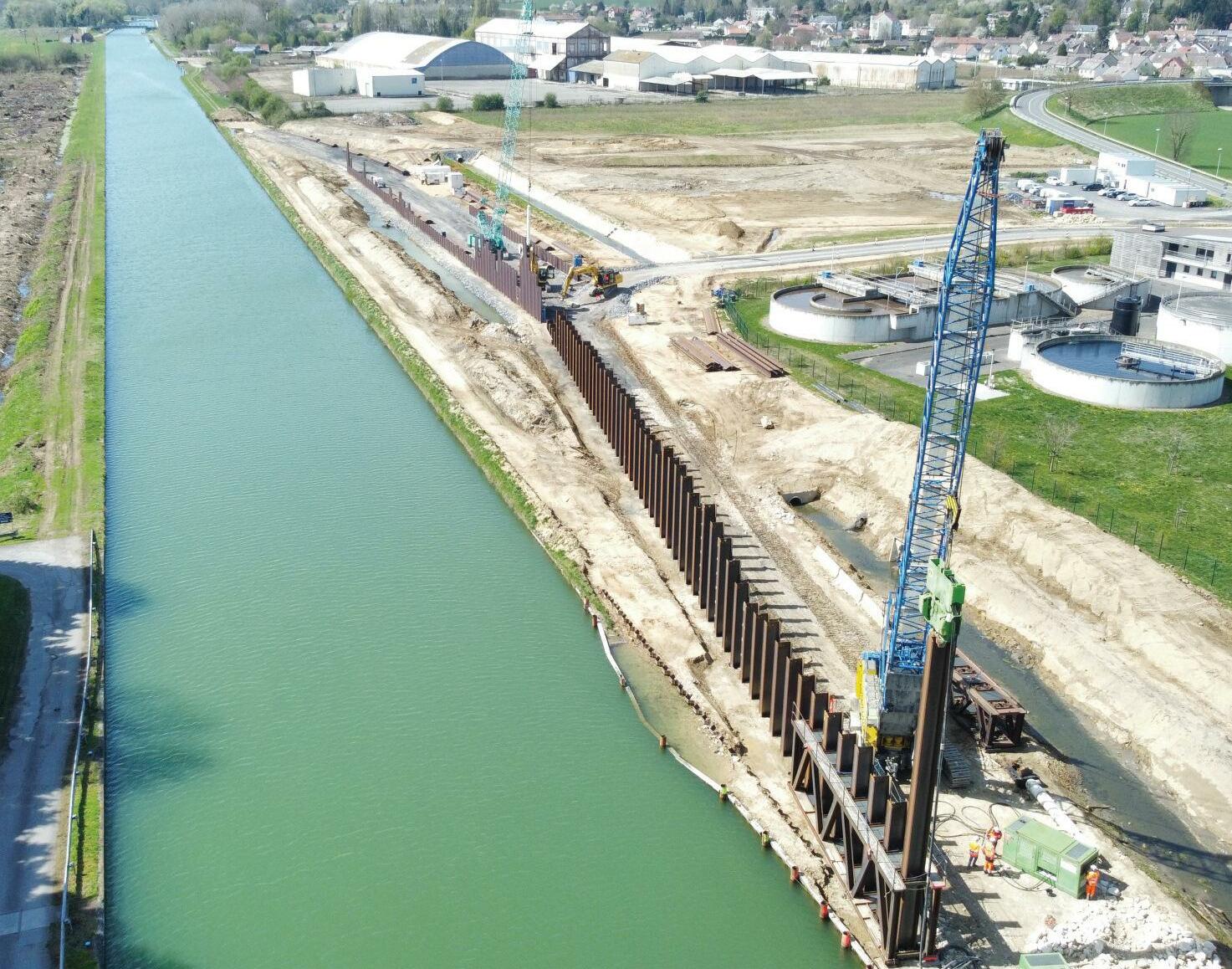
Quay wall extension at the port of Aalborg, Denmark
Located in the North of Denmark, the port of Aalborg is a vital multimodal logistics hub, offering transport via sea,road and rail.The inland port is Denmark’ s fifth largest port in terms of total volume of cargo and is fully owned by the Municipality of Aalborg.The rapidly increasing demand for storage capacity near the quay and the prospective growth in cargo compel the port authority to expand its quay capacity for the first time in more than 30 years. The 100m quay extension will be built using 303t of ArcelorMittal’ s AZ 28-700 sheet piles, establishing an additional terminal area of 27,800 sqm.
As sustainability is one of the most important pillars of the Port of Aalborg, efforts have been made to reduce, as much as possible, the carbon footprint of the project with existing technologies.Therefore, the choice of the right building material is crucial to reach the most environmentally-friendly solution for the quay extension.The port of Aalborg and their partners (Per Aarsleff and COWI) chose a steel sheet piling solution using the new EcoSheetPile™ Plus range from ArcelorMittal, manufactured from 100% recycled steel and with 100% renewable electricity from solar and wind sources. Together with additional measures to reduce the carbon footprint, it is possible to reduce the CO2 emissions of the project by approximately 30%, while increasing the carrying capacity of the port by over 50%.
A new 200m quay wall on the “Seine-Nord Europe” canal in France
Located in the north of France, the “Seine-Nord Europe ” canal will link the French waterways with the Northern Europe network. It will allow the development of water transport in France as an ecological alternative to road transport. Some barges can carry as much cargo as 220 trucks!
The new 200m quay at Ribécourt is one of the first essential stages in the whole project. Once completed, it will allow the supply of the building materials for the construction of the canal by barge.Works on the new quay wall have already started, using ArcelorMittal’ s unique HZ®-M/AZ® combined wall system. All together 910t of HZ 880M A-12 king piles and AZ 13-770 intermediary sheet piles are used. To reduce the total carbon footprint of the project,the structure is being assembled using ArcelorMittal’ s new EcoSheetPile™ Plus range, made from 100% recycled steel and with 100% renewable electricity.
Quay wall in Ribécourt, France © NGE Fondations
Bigger, better, faster...
ClaireInstonedeliversWPD’sregularport constructionround-up…
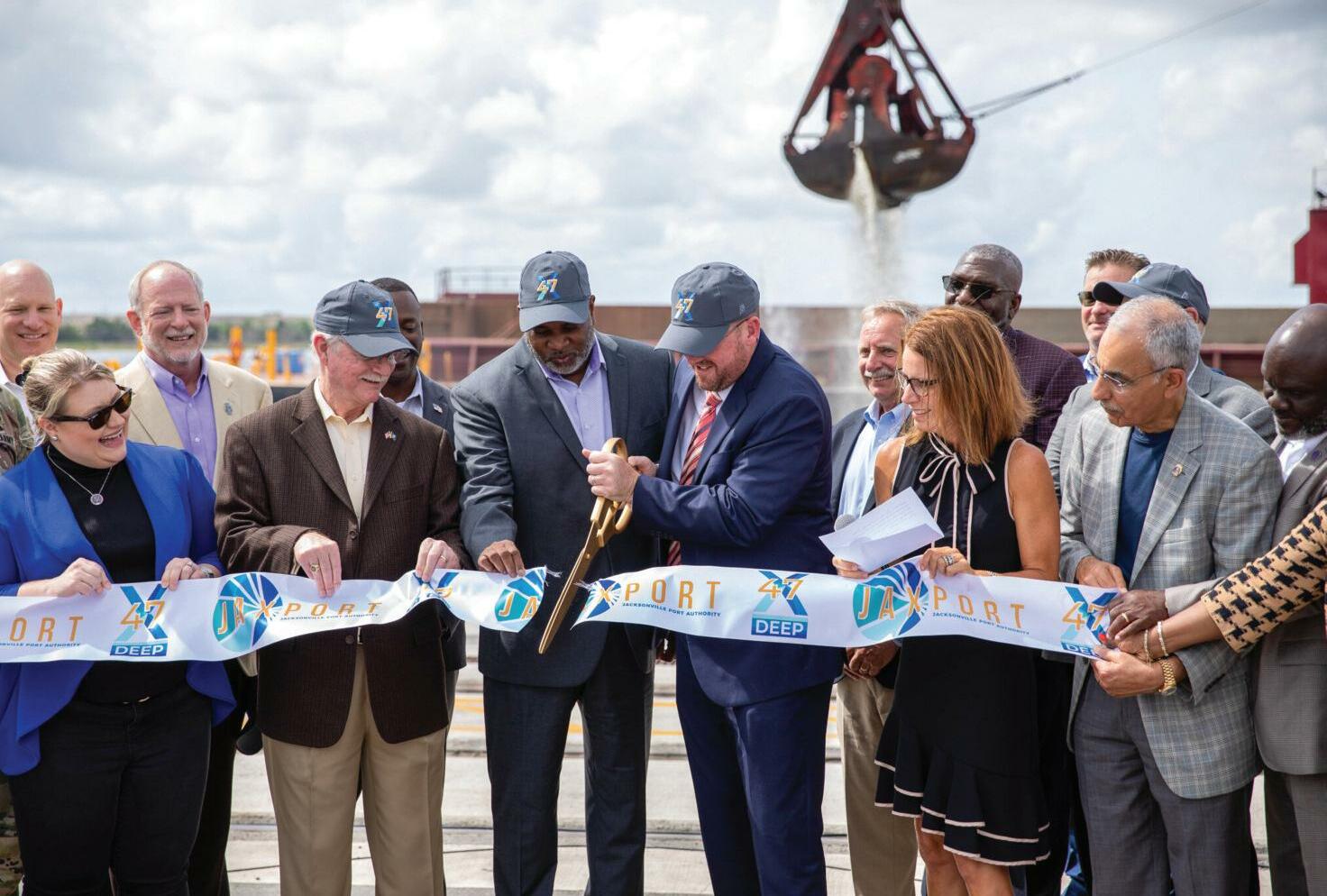
Supply chain, logistics and shipping leaders are looking to expand their routing options in 2022 and beyond. Herein, I take a look at how ports and terminals are working to offer more flexibility, capacity and speed in order to serve demand. Numerous projects are being considered, assessed, or are already underway and hitting milestones - all of which promise to deliver higher productivity, more space and more inland connectivity.
Weighing up the options
* South Carolina Ports in the US has commissioned Hamburg Port Consulting (HPC) to assess the capacity expansion of the Inland Port Greer, one of its intermodal rail terminals located in the Northern part of the state.The assessment was used to validate HPC’ s original capacity and review options for expanding total capacity, ensuring the rail-served inland port can handle growing cargo volumes for customers. Extending the range of the seaport' s economic influence has been a driving factor for the development and construction of SC Ports ’ inland port in Greer. In light of the growing container volumes handled at the facility, SC Ports commissioned HPC to develop a capacity improvement plan for the terminal with the aim of evaluating the potential for expansion as a timely response to future volume developments. After providing a development plan for the facility a few years ago, HPC has now prepared an update, taking into consideration the impacts of ongoing supply chain disruptions in North America and the need for more capacity to handle customers ’ growing supply chain needs.Amongst others,the layout concept and equipment procurement plan for long-term expansion have been generally validated within the framework of a sensitivity analysis. HPC has analysed the influencing factors under different dwell time scenarios to map the supply chain resilience.As a result,some adjustment measures have been suggested, making the facility capable of handling up to 300,000 rail units.
* FSX (developer of the Freight Shuttle System) and Port Houston in North America have entered into an agreement to explore the steps required for deployment of Freight Shuttle ’ s Seaport System at the port’ s growing container facilities.The Freight Shuttle is an elevated, zero emission system for moving shipping containers to and from the port’ s busy terminals, making best use of available space and addressing the need to improve air quality in the region. “Considering the tsunami of freight on the horizon, solutions like the Freight Shuttle are needed now more than ever, ” says Steve Roop, Founder and CEO of FSX. With immense commercial growth at Port Houston, creative solutions are needed as demand for port services continues to grow. Recent and ongoing global supply chain disfunction has highlighted this necessity. The System is a force multiplier for cargo space by accelerating the rate at which containers are moved from the port, transporting them via autonomous vehicles safely and efficiently to a facility closer to customer hubs and away from critical high-traffic choke points. The proposed system will promise to keep pace with commercial growth at the port while reducing emissions and reducing truck miles on roadways shared by passenger vehicles. ” Implementation of the System is one way that Port Houston is planning to stay in front of the shipping needs of the Houston region.
Celebrations at JAXPORT.
Making headway
* The Contrecœur land reserve was acquired over 30 years ago by Montreal Port Authority (MPA) and been the focus of careful collaborative planning to support the development of the supply chain in Quebec and Eastern Canada. With the support of Canada Infrastructure Bank and the Government of Quebec, the Port of Montreal and its partners plan to develop a new state-of-the-art container terminal able to handle up to 1.15 million containers (TEUs). The MPA recently announced that a new phase is underway to complete the major expansion project in Contrecœur, as three bid respondents qualified.The selected bid files were from Axium Infrastructure Canada and Pomerleau Capital,PortsAmerica Holdings, andTerminal Investment Limited.The international Request for Qualifications (RFQ) was issued in November 2021, using the Design-BuildFinance-Operate-Maintain (DBFOM) model. Five compliant bid packages were evaluated. The three qualified finalists will be invited to submit bids in the Request for Proposals (RFP) phase, which is underway and will last around 12 months.Announcement of the private partner is slated for the second quarter of 2023, with financial and commercial closing in the third quarter of 2023, for a start of construction within the year.The terminal is expected to be commissioned by the end of 2026.At a time when Montreal' s facilities will soon reach maximum capacity, this expansion will result in increased efficiency and competitiveness for the businesses served by Montreal' s port facilities.The investment is estimated at between $750 and $950 million.
* In the US, federal, state, and local leaders joined JAXPORT and the US Army Corps of Engineers (USACE) Jacksonville District to celebrate completion of the Jacksonville Harbour Deepening Project through JAXPORT’ s Blount Island Marine Terminal. The project deepened 11 miles of the federal shipping channel - from the sea buoy to Blount Island - to a depth of 47 feet from its previous depth of 40 feet. The 47-foot harbour provides the channel depth needed for larger ships to call Blount Island to and from destinations worldwide and allows existing
ships calling Jacksonville to carry more cargo on board.In addition,the project includes a new turning basin allowing larger vessels to turn around at Blount Island berths. In coordination with deepening, JAXPORT completed more than USD100 million in berth enhancements in the last few months to enable the SSA Jacksonville Container Terminal (JCT) at Blount Island to simultaneously accommodate two post-Panamax container ships. In early 2023, terminal operator SSA Atlantic will welcome three new eco-friendly 100-gauge container cranes, bringing the JCT’ s total to six.
* Lagos State government in southwestern Nigeria recently confirmed that plans to begin construction of Badagry Seaport have reached the advanced stage.The new facility – to be located in the Badagry area of the state of Lagos – is cited to reduce congestion at Apapa Seaport. It has been reported that the state government has secured land for the project but was waiting for the approval of the Federal Executive Council (FEC).The container terminal at Gangavaram Port, for which work has already started, will be ready for commissioning by the second quarter of the 2023 financial year.The new facility is expected to provide growth for the cargo business in the hinterland of Andhra Pradesh and surrounding industrial hubs.The terminal is also set to help increase efficiency, reduce turnaround time and logistics costs, and improve the supply chain for industries in the hinterland which include metal and minerals, agriculture products, chemical, and more.
Digging deep
* Head of the Suez Canal Authority (SCA) recently announced that the SCA’ s dredger Tariq bin Ziyad has joined the fleet already operating in the canal expansion project. He confirmed the project to develop the southern sector of the canal is proceeding according to the set timetable.The initiative is of great importance as it aims at increasing navigational safety at the southern entrance by 28% and enable the canal to receive an average of six additional ships. Egypt started work to expand the southern entrance of the Suez Canal back in May 2021, a few weeks after the Ever Given ship incident.
* India is set to increase draught depth at Cochin Port in order to boost trans-shipment operations as the Sri Lankan crisis continues. It was reported in May that the 300-crore dredging project will be done under the Sagarmala programme and hopefully be completed in a year or so.Anticipating an increase in trans-shipment operations at Cochin, following the economic and political turmoil in Sri Lanka and reports of congestion at Colombo port, the Shipping, Ports and Waterways Ministry will take up the dredging works in order to increase the port’ s draught depth to 18 meters to allow bigger vessels to visit.
* The Nigerian Ports Authority (NPA) has re-enforced its commitment to revamping ports in the Delta State by embarking on the dredging of channels and rivers in the State. Work has already begun and is about halfway done.When complete, it will enable ports in Delta State to have a better draught, receive bigger vessels and record less incidences of vessels running aground. “We all know that the breakwaters collapsed about ten years ago, and there has been high siltation resulting in reduction of the draught from seven meters to three meters in some places, ” confirmed a representative for the port. In addition to this work the Nigerian Ports Authority has also started the mapping and charting of the Escravos channel, starting from the fairway buoy down to Koko Port, which has not been done for well over a decade.
All systems go!
* Chinese state-owned conglomerate COSCO Shipping Holdings is moving forward with its own solution to sorting the congestion problem at ports in the Americas by building a USD3 billion deep-water port linked to an industrial and logistics park. Located in Chancay, 55km north along Peru ’ s Pacific coast from the capital Lima, development of the only new port in the Americas is underway. COSCO runs operations at around 35 ports globally, but Chancay will be the conglomerate ’ s first outpost in South America. “COSCO Shipping will jointly cooperate with Peru to develop Port of Chancay into an important hub port in Latin America, ” Chairman Xu Lirong said back in 2019 when the company orginally closed the deal to buy 60% of the project from Glencore ’ s Volcan unit.Working with COSCO on the initiative is China Railway Group and China Communications Construction, especially its China Harbour Engineering unit.According to COSCO’ s plan, the new port will be able to handle the world’ s largest container ships and process up to 1 million standard shipping containers a year, with the first piers due to open in a year ’ s time. * Construction has commenced on a new 42-acre industrial development in Ellesmere Port in the UK. Developer, Firethorn Trust, broke ground at Link Logistics Park - a former brownfield site which is set to be transformed into more than 760,000 sq. ft. of industrial space within which will stand a 655,000 sq. ft. warehouse.The site is to be delivered with net-zero carbon construction with help from partner Winvic. Immediately adjacent to Junction 7 of the M53 and within a 45-minute drive of Liverpool and Manchester airports,the multi-modal industrial development lies in close proximity to the Manchester shipping canal, just 22 miles from the Port of Liverpool, offering exceptional transport links to the UK logistics network.
* The Cambodian Ministry of Public Works and Transport has held a ground-breaking ceremony to mark the start of construction at the new International Multi-Purpose Logistics and Port Centre in the southwestern province of Kampot.The seaport will have a total handling capacity of 300,000TEUs in 2025 and up to 600,000 TEUs by 2030.The project - estimated at USD1.5 billion - includes a container terminal, special economic zone, free trade area, logistics hub, oil refinery, and a terminal for tourist vessels. Built on a total area of 600 hectares with a depth of 15 meters, the Centre aims to improve efficiency for traders and investors in exporting agricultural, industrial, and fishing products in local and global markets - and boost Cambodia ’ s economic growth in the process.The project will be implemented in three phases, the first of which is set to begin operations in 2025.
* Over in the US,APM Terminals Mobile has signed an agreement with the Alabama State Port Authority to add 32 acres to the current 134-acre container terminal yard to keep up with future demand, creating one million TEU throughput capacity.This move represents the third expansion in the last six years.The USD104 million expansion will begin later this year.The first 19 acres are due to be completed next year, with the remaining 13 acres by early 2025.As part of the project,APM will purchase two super post-Panamax ship-to-shore gantry cranes and related support equipment for crane operations.The brand new additions will complement the four existing gantry cranes. Moreover, the US Army Corps of Engineers is currently dredging the Mobile Harbour channel in order to reach 50 feet by the end of 2024.

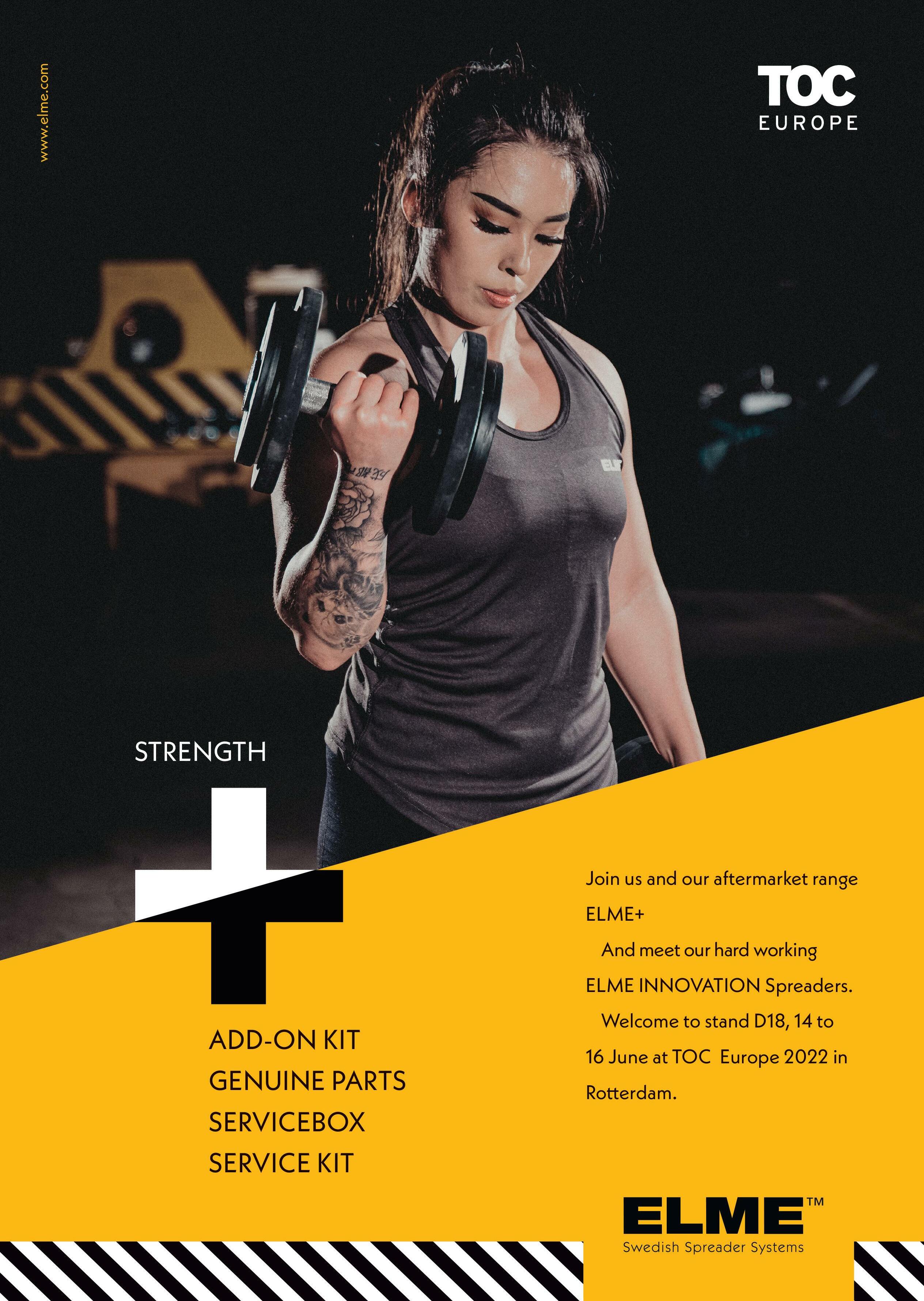