
5 minute read
Diversification Innovation
winning combo for bulk solutions provider
Bedeschisharesitsviewonthecurrentstacker/reclaimermarket,highlightingitsachievementsinthebulksectorwithcasestudiesof tworecentbucketwheelprojects.WorldPortDevelopmentreports...
The supply at Taman Coal Terminal includes four combined bucket wheel stacker-reclaimers, some 16 kilometers of belt conveyors with relevant ancillaries equipment, and four shiploaders.
Over the years, Bedeschi has been hard at work reinforcing its position across the globe in the bulk handling industry, offering a wide variety of tailor made solutions to transport and store any type of bulk material including coal, iron ore, limestone, fertiliser, clinker and many others, covering any capacity from 100 to 10.000 tph. Besides delivering traditional stackers and reclaimers designed for sticky and difficult materials as well as the most complete range of equipment for power, cement chemical and mining plants, Bedeschi has also recently supplied over ten new bucket wheel stacker/ reclaimers, operating on coal and iron ore in Europe,Asia and South East Asia.
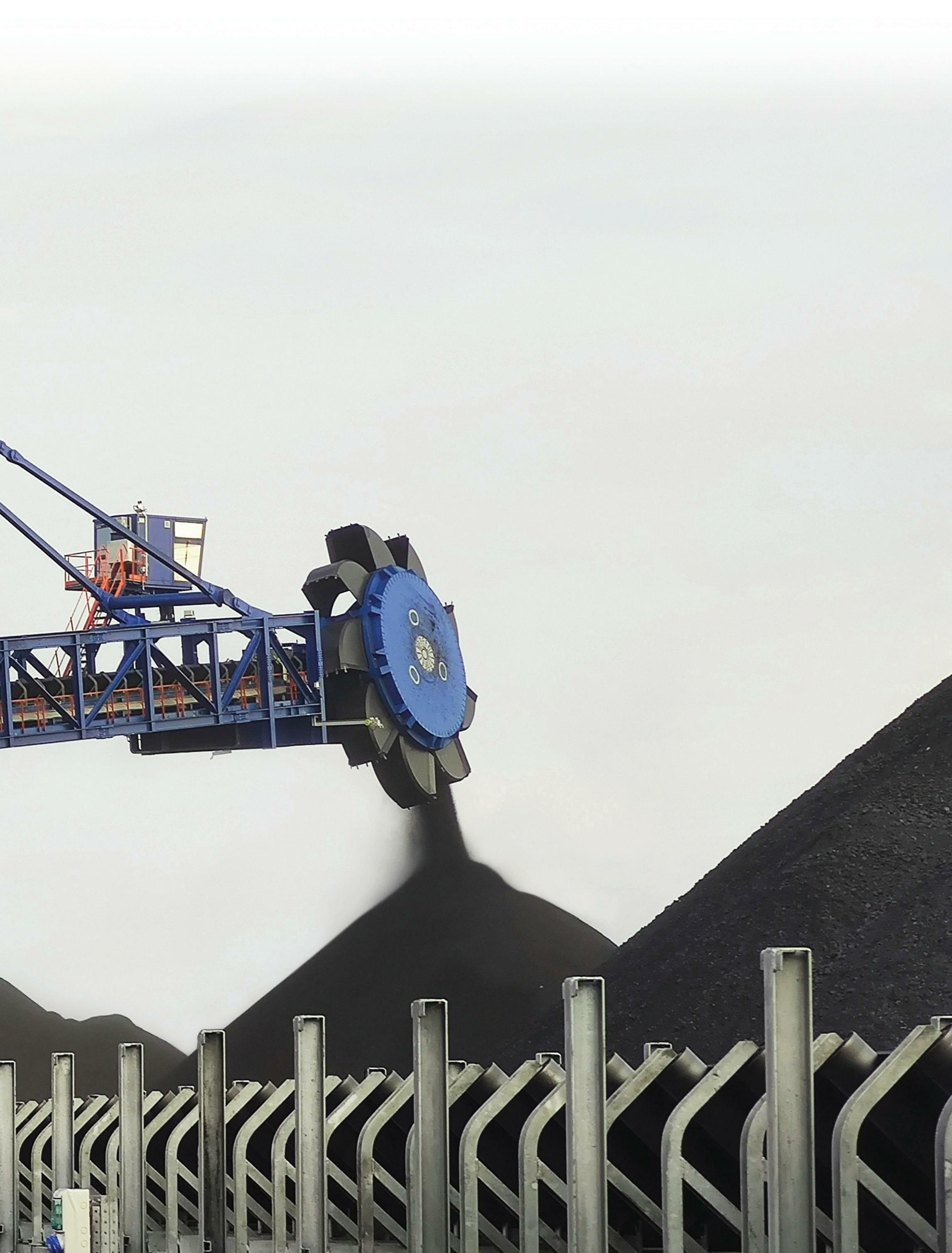
“Diversification is our major asset which we nourish with a continuous innovative attitude in products and service to tailor fit customer needs. Operating in different industries and with different materials we are able to think ‘ out of the box ’ , using technically consolidated concepts, but in different contexts, for a totally customised solution capitalising on synergies and cross competence, ” states a representative for the manufacturer which was established in 1908 and is one of the oldest European companies specialising in turn-key solutions for bulk handling, container logistics and bricks. When asked for an example of their innovation, the Italian-headquartered firm explained: “We are using the most classic machine for cement factories (the belc system) to create a self-unloading vessel totally different from any other conventional self-unloading vessel presently on the market.We are also working to integrate data acquisition systems for remote monitoring and control and preventive/predictive maintenance into all our machines - in particular on stackers and reclaimers. Of course, in the R&D Department we are also focusing on environmental protection, energy efficiency and pollution prevention - issues that will become even more important in these industries.This is where Bedeschi is pushing the upcoming technology development efforts. ”
Commenting on the company ’ s outlook for the stacker/reclaimer market across 2022 the solutions provider highlighted trends in the cement, coal and food industries stating: “Following the trends of 2021, the cement industry is showing promising improvements worldwide for the coming year. Moreover, the aftermath of the situation in Ukraine will probably change the declining forecasts for coal power plants, at least in the short term, to cope with the exceptional price fluctuation relevant to energy production.In addition, the food handling business will also be influenced by the war:the forced change of cereals and oilseed supply routes will favour the refurbishment and construction of new terminals in alternative areas. ” For more than a century Bedeschi has been providing effective and reliable solutions, taking care of each step of the project - from execution and engineering to assembly, installation and start up. Herein, the company presents two case studies from recent projects.
Taman Coal Terminal, Taman, Russia
The first project highlighted is the supply of a fully automated coal export terminal atTaman with a total aggregated capacity of more than 48.000 tph on 6 loading lines.The facility will reduce handling time of Capesize ships at the port by half, from 48 to 24 hours.
The terminal in Taman in Russia is the most efficient coal loading line in the country thanks to its ability to reduce ship handling times and ensure stable operations all year round. For the customer, that means reduction of seaborne freight expenses.The peak export capacity of the terminal, when fully operational, will be 55000 tph (including existing machines). Moreover, with the introduction of advanced and green technological solutions it will meet the highest environmental standards.
The supply at Taman Coal Terminal includes four combined bucket wheel stacker-reclaimers, some 16 kilometers of belt conveyors with relevant ancillaries equipment, and four shiploaders, delivered fully erected to the terminal jetty. Overall, four combined stacker + reclaimer machines have been supplied.Their rated capacity is 8000 tph, both in stacking and reclaiming mode.With a total installed power of 1500 kW, fed through a medium voltage cable reel, each machine has a service weight of about 1700 tonnes.The length of the stockpiles the machines can build is over 1100m with a pile base of 56m.With all the stacker-reclaimers operational, the potential storage capacity reaches up to 3.9 million tonnes.
All the machines are equipped with a bypass system to direct the material to the export lines, if needed, without being stockpiled first. The automatic reclaiming mode takes the machines to their best efficiency, thanks to the continuous control loop which involves the reading of speeds, power and instant flowrate on the boom conveyor.The target is to have the highest possible output rate, regardless of the conditions of the stockpile, without overloading the downstream conveyors.
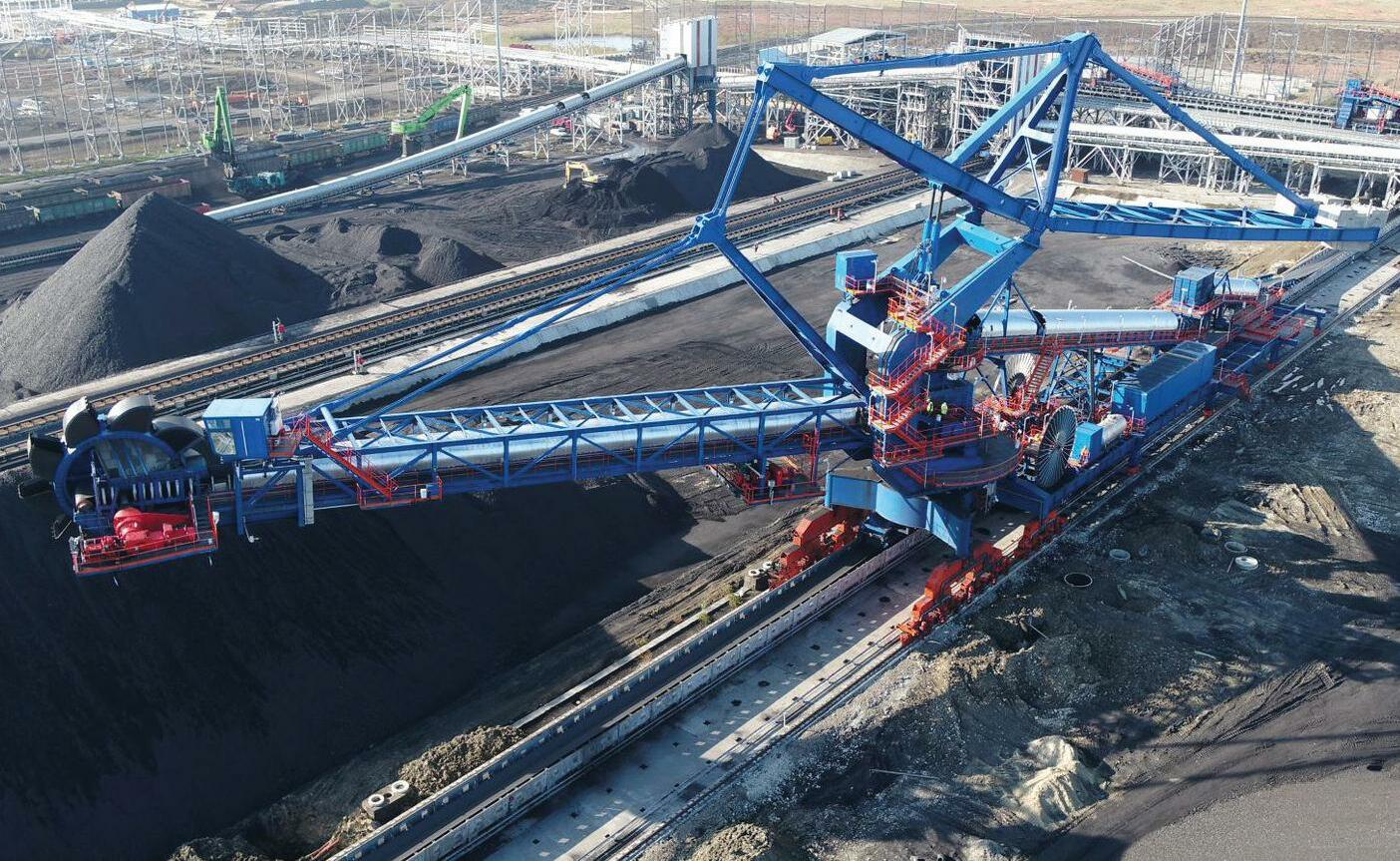
The erection took place in the stockyard but, to minimise structural welds done on site, a partial assembly of the machines was performed at the manufacturing area.The pre-assembled sections were then shipped by sea directly to the service dock of the terminal.
ILVA Steel Plant, Taranto, Italy
The ILVATaranto steel plant, which is currently owned by the Italian government but leased by ArcelorMittal, is aiming to be one of the most advanced and environmentally-friendly facilities in Europe.The steel plant is, according to the European Commission, the largest in Italy and the EU. It has a capacity to produce 10 million tonnes of steel annually, which corresponds to 40% of Italian steel production. As part of the environmental renovation work to be carried out at the facility, Italian company Cimolai was awarded the design, manufacture and assembly of the Mineral and Fossil Parks Safe Confinement.This is a double steel structure, 80m high, 254m wide, and 476m long.As part of the project, Bedeschi was awarded the supply of the stacking and reclaiming system inside the primary park (fossil).
Bedeschi supplied three bucket wheel stacker/reclaimers, all of which were identical except for their tripper/trailer. Each have a stacking capacity of 6.500 t/h and a reclaiming capacity of 1.600 t/h.The erection was done at site outside of the dome, then each machine was put in its final work position without interrupting activities.
The supply of the new machines will have a key role in reducing dust spillage towards the city, plus enable energy savings and improved efficiency in both the production and reliability of the plant.Thanks to Bedeschi’ s commitment to producing eco-friendly equipment, the machines were equipped with systems to limit dust production via controlled flow spouts, filters and dry fog that uses microdrops of nebulised water to keep the surrounding environment clean.
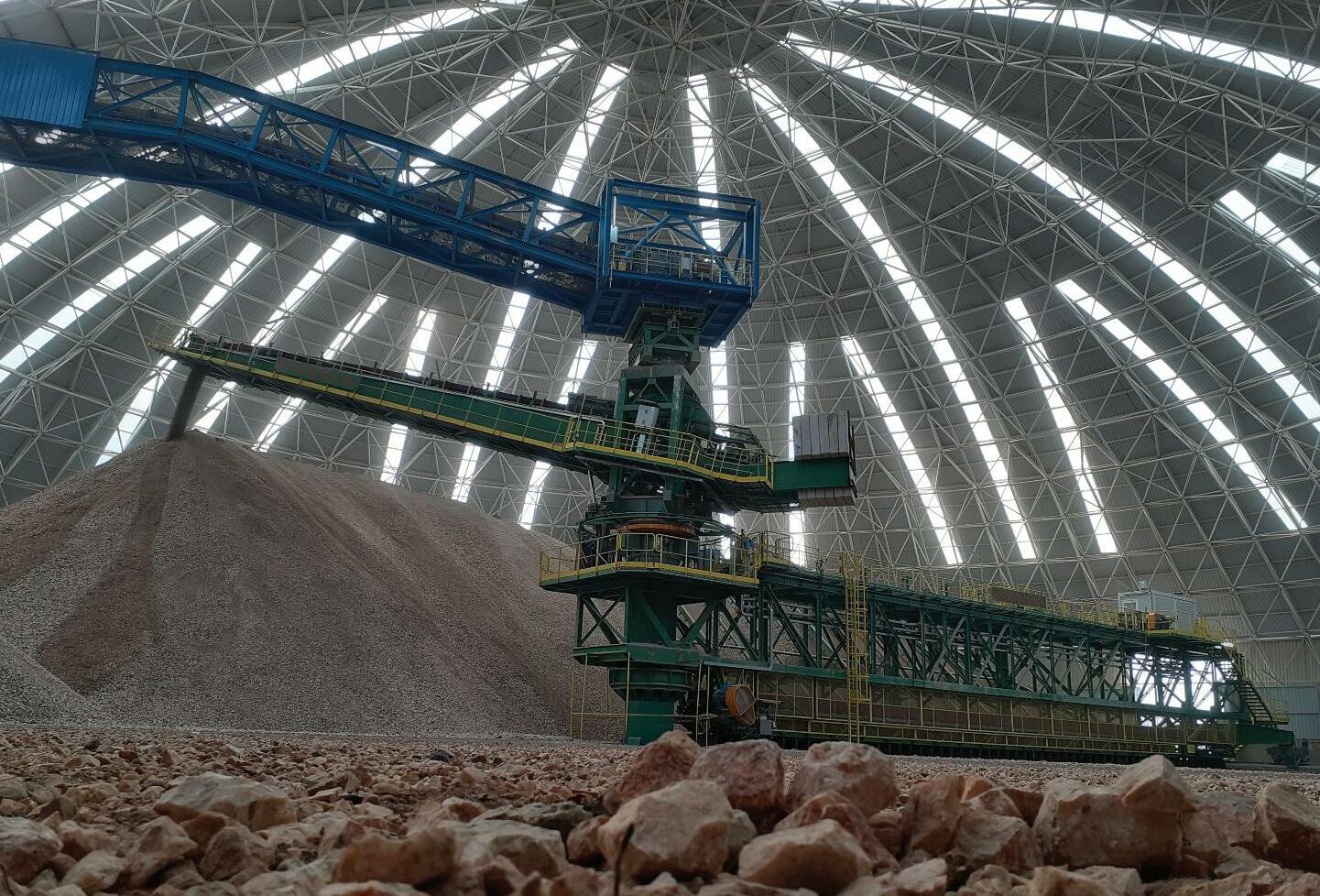
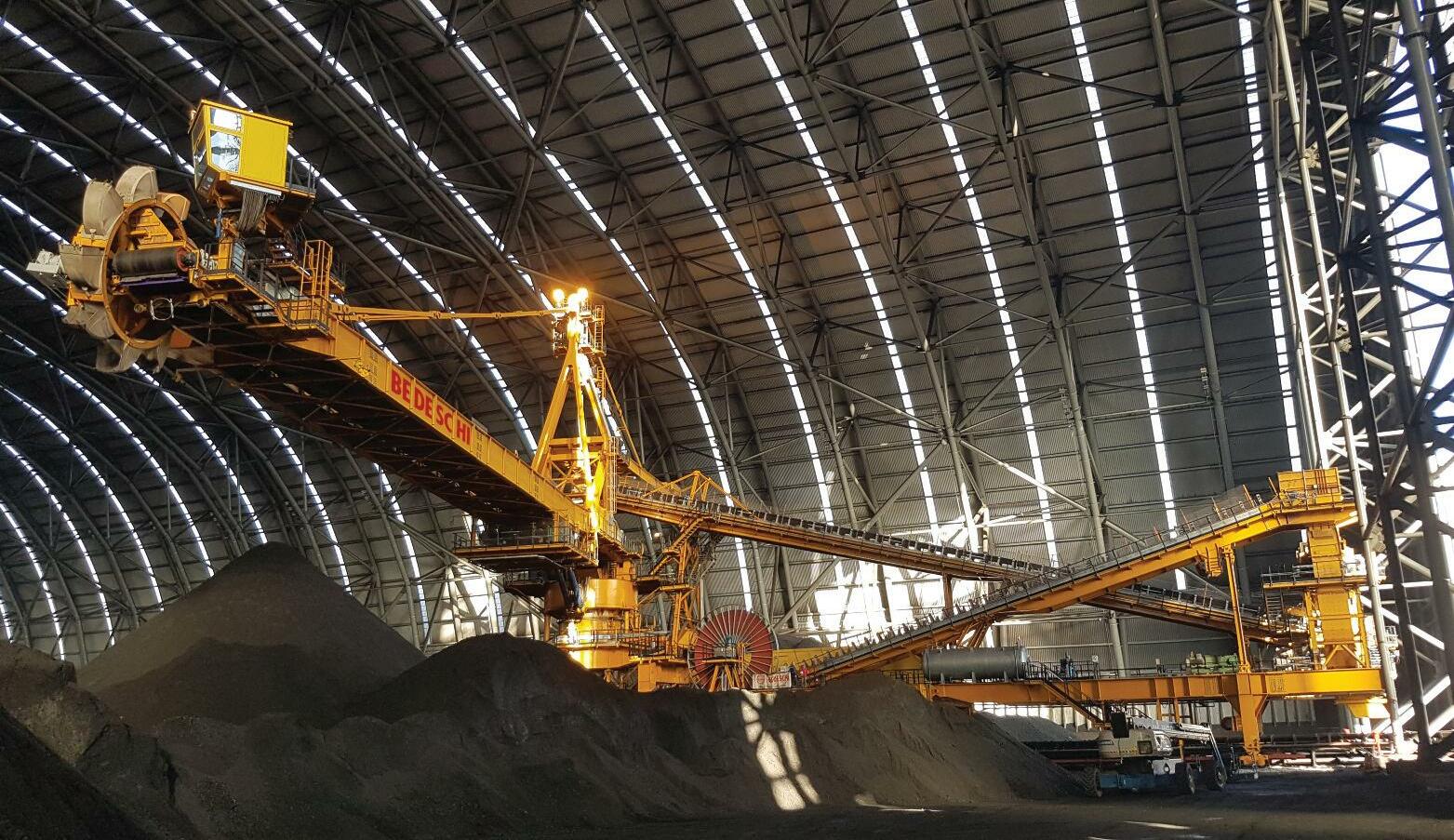
The terminal in Taman in Russia is the most efficient coal loading line in the country.
Bedeschi’ s circular storage solution.
Bedeschi supplied three bucket wheel stacker/reclaimers for the plant in Taranto.