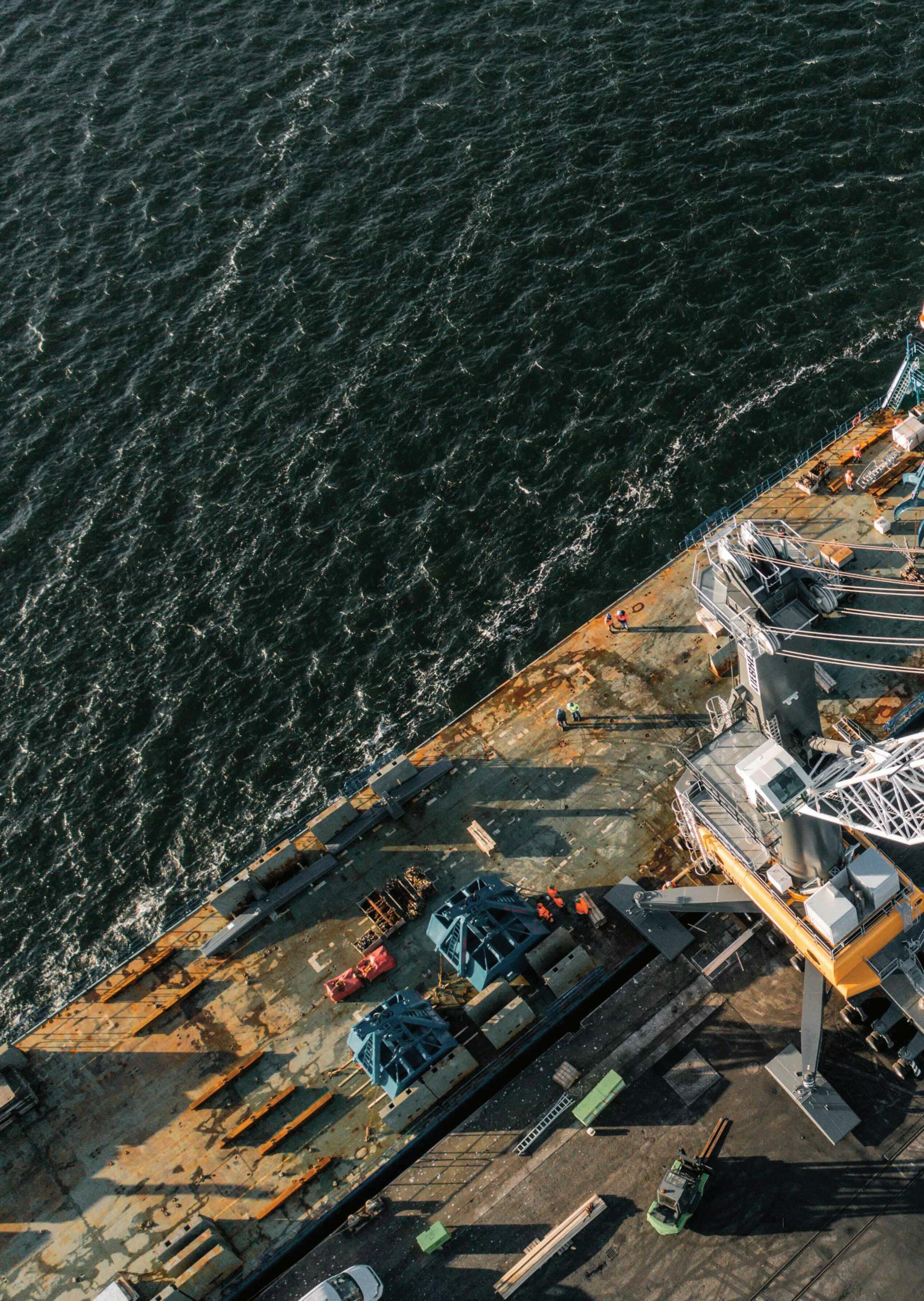
19 minute read
Downturn? What downturn?
IfyouthoughtthemarketforMobile HarbourCranessloweddownforthelast coupleofyearsjustreadtheannualreport publishedinApril2022byAustria-based LiebherrGroup.ThomasFrancisreports...
G
oing through the annual report of Liebherr Group the company achieved a turnover of EUR 11.6 billion in 2021 - an increase of 12.6% (almost EUR 1.3 billion) compared to 2020.As a result, the Liebherr Group was almost able to match its previous record year in 2019 in terms of annual turnover.
In the product segments, including maritime cranes,aerospace and transportation systems, gear technology and automation systems, refrigerators and freezers,as well as components and hotels (yes, they also own several hotels), Liebherr achieved total revenues of EUR 3.63 billion - up 3.9 % compared to 2020.
What is interesting is that the order intake for Mobile Harbour Cranes (MHC) in 2021 was higher than ever before. In total, more than 80 new units and also various used units were sold to customers worldwide. Liebherr mobile harbour cranes were ordered from 31 different countries with all continents being represented. There was strong growth in the Middle East and West Africa regions and stable core markets in Europe as well as North and South America.As in previous years, the LHM 550 is the most popular crane, closely followed by the LHM 420.A strong increase in sales of the LHM 800 was recorded, which more than tripled compared to 2020.
However, just like other MHC manufacturers there are still uncertainties with regard to pandemic-related restrictions, the effects of steep price increases for many goods and services, shortages of certain raw materials and the lack of skilled workers, as well as bottlenecks across different supply chains. But the company reported to have started 2022 with a very good order book, although the negative effects on the activities of the Liebherr Group due to the war in Ukraine can already be seen. Liebherr is monitoring and assessing the situation in Ukraine and Russia on a daily basis and is currently in the process of adjusting its Russian activities to the extensive sanctions imposed on the country. In March 2022, one of the leading port operators in Poland, Port Gda sk Eksploatacja SA, took delivery of a new Liebherr LHM 550 mobile harbour crane - the 300th order of this crane type.
A Liebherr LHM 550.
As the most popular crane type in the Liebherr mobile harbour crane portfolio, the LHM 550 has contributed significantly to Liebherr ’ s market leadership in the MHC market, according to the company. Since its market launch, with the delivery of the first LHM 550 to Kuwait in 2010, a double-digit number of this crane type alone has been delivered worldwide every year. In terms of sales per country, India leads the ranking with 23 units sold, closely followed by Italy and the USA. In 2021 alone, 26 LHM 550s were sold worldwide.The crane supplied to Port Gdansk Eksploatacja SA has a boom length of 48m and a lifting capacity of up to 104 tonnes, and will primarily be used for bulk handling of coke, coal and scrap metal. Statistics provided by Liebherr shows that a large number of their customers use the LHM 550 for several applications including container handling and even heavy-duty lifts of up to 154 tonnes. In addition to a hybrid drive concept consisting of diesel and electric motors, the cranes can also be used exclusively in electric only operation, thus making an important contribution to emission-free cargo handling. Over 30% of the LHM 550s sold in 2021 were equipped with an electric main drive.

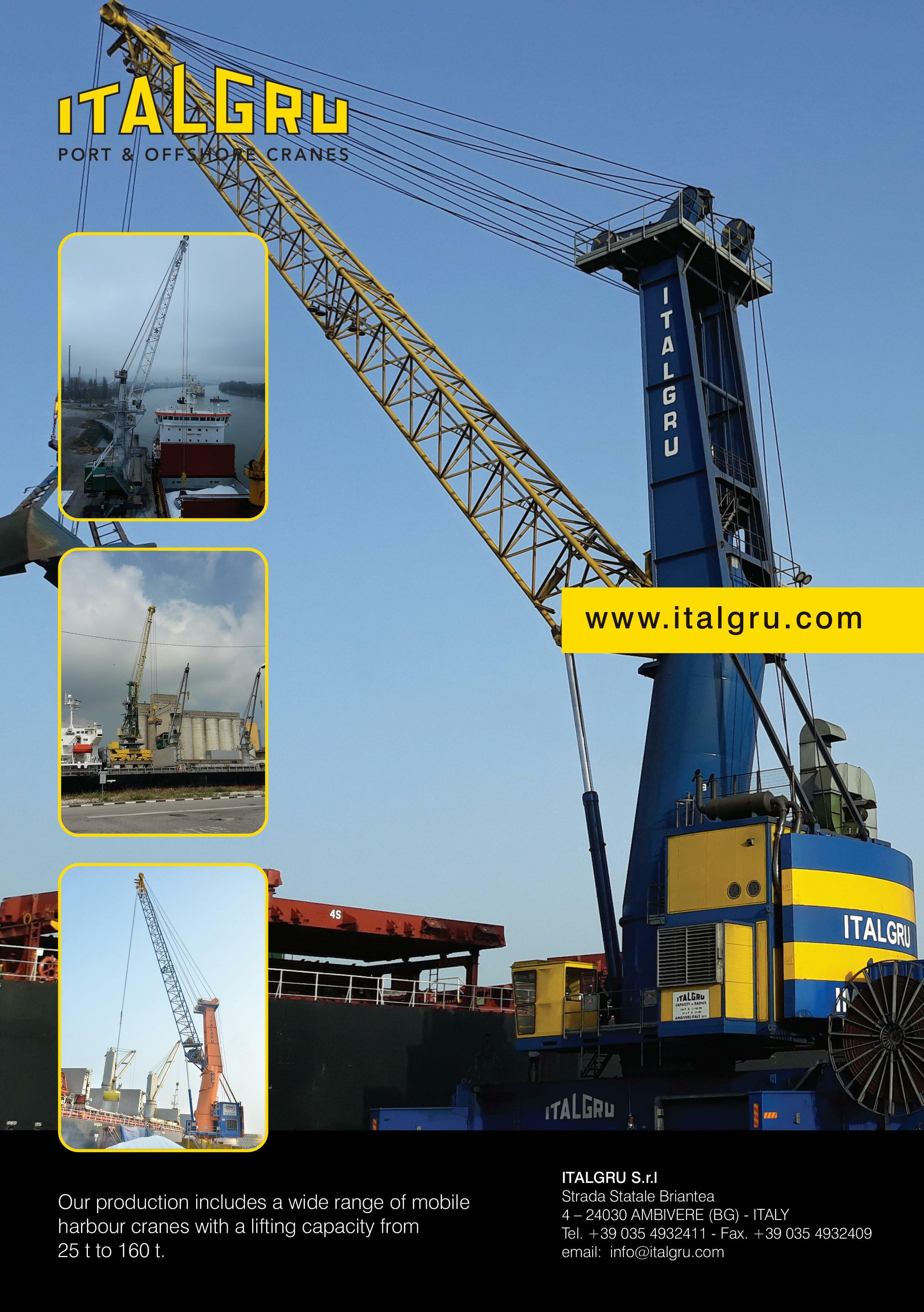
Italgru is reporting to operate at full capacity and an impressive order book.
Italgru
Similar stories are coming from Italy-based Italgru when it comes down to the effects of steep price increases, shortages of certain raw materials and bottlenecks in different supply chains. But despite all these issues, Italgru is reporting to operate at full capacity and an impressive order book.
The company does report that it has seen more and more customers opt for environmental machinery. Hence it decided to offer both diesel-hydraulic and diesel-electric cranes in order to meet customer expectations. In addition, Italgru has opted for sub-vendors that can supply low-emission engine motors and eco-friendly components, in order to offer energy saving features on their MHCs, such as an accumulator that stores energy during the lowering phase to be redistributed to other movements available.
Such accumulators can be installed on the diesel-hydraulic configuration of an MHC, whilst on the diesel-electric configuration, a series of regenerative inverters can be installed, which are able to redistribute the energy stored during the lowering phase to the electrical grid of the berth.The principle (of the accumulator and hydrostatic drive) is based on a main drive that supplies power to pumps and a hydraulic transfer gearbox. The main drive can be a diesel engine or an electric motor.All energy-consuming movements are connected to a closed hydraulic circuit and are fed by it when required. Closed hydraulic loops are used for all main functions such as hoisting,slewing and luffing.The benefits of all this are extremely precise control, a minimum number and size of components and reduced fuel consumption thanks to the standard use of reverse power. Such innovative drive systems generally saves diesel or energy during crane operation and enables sustainable and efficient operation.
According to Mauro Cacciatore at the Commercial Department at Italgru, by introducing a new design for all models, with electric drives on both hoisting and slewing movements, the company is dedicated to those customers focusing on eco-friendly solutions.
Last year, Italgru delivered one diesel-electric IMHC 2120 E to Volos Port in Greece. The MHC is a single winch with a maximum capacity of 125 tonnes and is equipped with a cable reel in order to plug-in to the electricity supply on the berth.A total of six MHCs were heading towards India - four of these were diesel-hydraulic and electric IMHC 2120 with a maximum of 100 tonnes capacity under hook. Just like the unit for Volos Port they were equipped with a cable reel to draw electricity from berth. In addition, two MHCs had a maximum capacity of 140 tonnes under hook. Currently, Italgru are working on a diesel-hydraulic IHMC 1580 (maximum 80 tonnes capacity) for Azov port in Russia and one diesel-hydraulic IMHC 2120 (125 tonnes capacity) for Barletta port in Italy.
Italgru is also completing work on three diesel-hydraulic IMHC 1580 units (with a maximum capacity of 63 tonnes) for the ports of Ravenna and Oristano with expectations that they will be handed over to the customers in August 2022.
In early 2022 the company also started commissioning one IMHC 2120 for Durres port in Albania and one IMHC 1580 (with a maximum capacity of 63 tonnes) to the port of Rijeka in Croatia. It is anticipated that both MHCs will be handed over to their respective customers in both June and August respectively.
The lastest order came from Sicily for one IMHC 2120 E with an electric drive and equipped with a cable reel to draw electricity from berth.
Perhaps one positive thing that has come out of the global pandemic is the use of the internet for remote maintenance as well as for collaboration with local technicians. Now standard practice for all manufacturers this can be a new norm as cranes can be monitored through tele-maintenance.
“This is an effective tool that allowed us to oversee operations from our HQ, ” said Cacciatore. “The crane is connected, through the internet, to our offices in Italy or a local maintenance station, for a real time monitoring and troubleshooting of the crane. ”
Cacciatore also told us that remote support has always been a tool used by Italgru to help their customers. “The global pandemic and the restriction imposed to travelling has certainly increased the number of requests to operate directly from our headquarters. ”
Apart from keeping an eye on the crane in operations it also serves as an excellent tool to keep in contact with existing customers and with potential ones, providing the opportunity to connect from your home or office thus avoiding a slowdown in negotiations or project management.
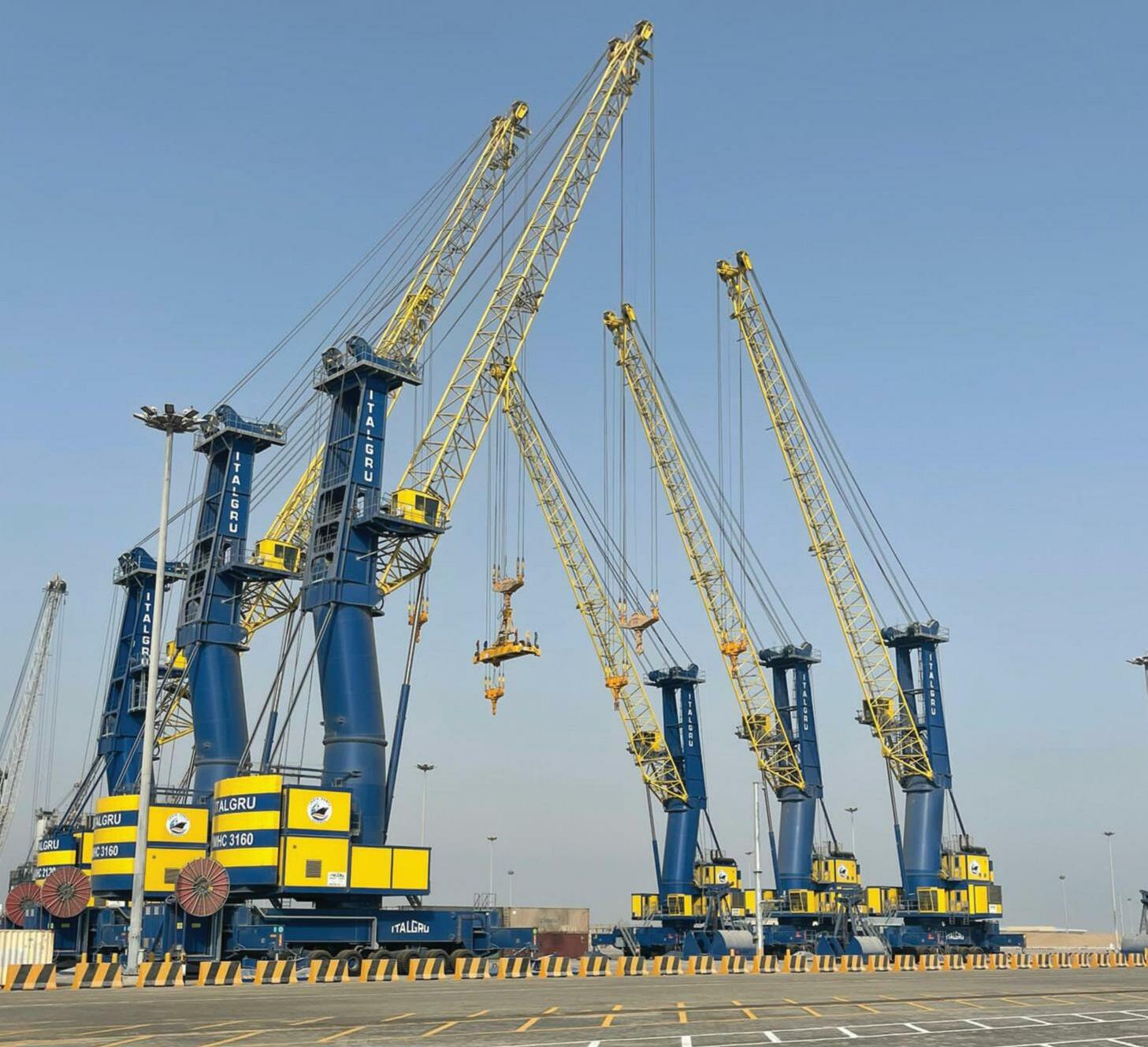
Konecranes
In April 2022, Konecranes put out a press release about Russia ’ s aggression towards Ukraine and decided already in the early days of the invasion to not take any new business from Russia. Konecranes operates a crane and component factory in Zaporizhzhia, in the south-eastern part of Ukraine.The factory is one of the Industrial Equipment supply factories for crane components and a crane manufacturing unit for Eastern Europe deliveries.
It also offers extra capacity for Konecranes ’ western crane deliveries specialised in large steel structures. In addition, Konecranes has employees working in crane service, port service, spare parts and industrial crane sales operations mainly in Odesa, Mariupol and Zaporizhzhia.
The production at the Ukrainian factory was stopped after the war started with planned production redirected to other Konecranes manufacturing sites.The company also started downscaling their Russian business although in 2021, Konecranes ’ sales to Russia totalled EUR 55 million.As a result of this decision, in the first quarter 2022, Konecranes has written off EUR 79 million of orders from Russia and cancelled EUR 32 million of sales to Russia.
Despite all this, Konecranes has been busy with their Mobile Harbour Crane offerings.
At the end of 2021, long-standing customer Tincan Island Container Terminal Limited (TICT) ordered two eco-efficient Konecranes Gottwald ESP.8 MHCs for their container operations in Lagos, Nigeria.The cranes will be operated by TICT alongside a large fleet of Model 4,Model 6 and Model 7 Konecranes Gottwald MHCs already on site.TICT is a a consortium made up of Bolloré Ports and a Chinese partnership formed by China Merchants Holding International (CMHI) and China Africa Development Fund (CADF).
The cranes on order have a working radius of 54m and a capacity of 150 tonnes. Compared to the Generation 5 cranes already on-site, they feature strong lifting capacity curves for improved performance and a higher classification, which doubles their service life in container handling operations. The cranes have a customised propping base adapted to local conditions, as well as a tower extension to reach higher container stacks and a better view of the vessel for improved precision and safety.Built-in readiness for an external power supply will make conversion to electric operation easy when resources allow.The cranes are scheduled to be delivered in June 2022.
In November 2021,Turkish terminal operator Celebi Bandirma Uluslararasi Limani Isletmeciligi AS (Celebi Port of Bandırma) ordered two eco-efficient Generation 6 Konecranes Gottwald MHCs for their terminal on the coast of the Sea of Marmara,Turkey.The two new MHCs will serve the port’ s upcoming expansion plans, helping the port to increase their bulk handling and improve their management of general cargo and containers.
They will have a working radius of up to 51m and a lifting capacity of 125 tonnes.They feature a high tower cab for an excellent view over the working environment and strong lifting capacity curves for high handling performance. Both cranes are equipped with a fuel-optimised diesel engine and an external power supply. The cranes will be handed over in July 2022.
In January 2022, the Port of San Diego ordered two eco-efficient Generation 6 Konecranes Gottwald MHCs for their Tenth Avenue Marine Terminal (TAMT) in Southern California, USA to help reach their ambitious clean air goals.These MHCs are equipped with an external power supply.Thanks to their electrical design concept, efficiency increases when they are connected to the harbour mains. Instead of onboard diesel engines, the cranes are equipped with battery packs.They allow extensive travelling time when unplugged from the harbour mains.
In addition, short-term load handling is possible with the battery drive in case of an emergency, such as an unexpected power loss.The battery takes its charge from the mains but also collects energy from braking and lowering movements for later use.
The two new all-electric cranes will have a working radius of up to 59m each and a lifting capacity of 200 tonnes.The cranes can be used together,doubling capacity to 400 tonnes thanks to the innovative Tandem Lift Assistant, a Smart Feature which helps synchronise the cranes during dual lifting controlled by just one operator, making the most of the full capacity of both cranes. The cranes are anticipated to be in operation in mid-2023. In April 2022, Konecranes delivered an eco-efficient Generation 6 Konecranes Gottwald MHC to Mexican terminal operator Grupo CICE (Corporación Integral de Comercio Exterior SA de CV). CICE provides port and logistics services since 1991 at several locations in Mexico from their head office inVeracruz.
The Port ofVeracruz is the oldest and largest port in the country and includes CICE’ s largest facility.With a continuing expansion of terminal capacity, CICE was looking to upgrade its equipment with a high-capacity crane that can handle both containers and general and project cargo.
The new MHC will have a working radius of up to 61m and a lifting capacity of 125 tonnes. It features a tower extension for reaching higher container stacks on deck and a better view of the vessels and working environment. It provides a strong lifting capacity curve for high handling performance and an A7 classification in container handling for a long service life.
It is obvious that the MHC market is undeterred by pandemic-related restrictions, steep price increases, shortages of certain raw materials and the lack of skilled workers, or even bottlenecks in different supply chains. There might be one negative effect that could affect the market as a whole.As the war in Ukraine continues, and MHC manufacturers start pulling out of Russia and cancelling orders from Russian customers, their actions will affect their turnover for 2022.
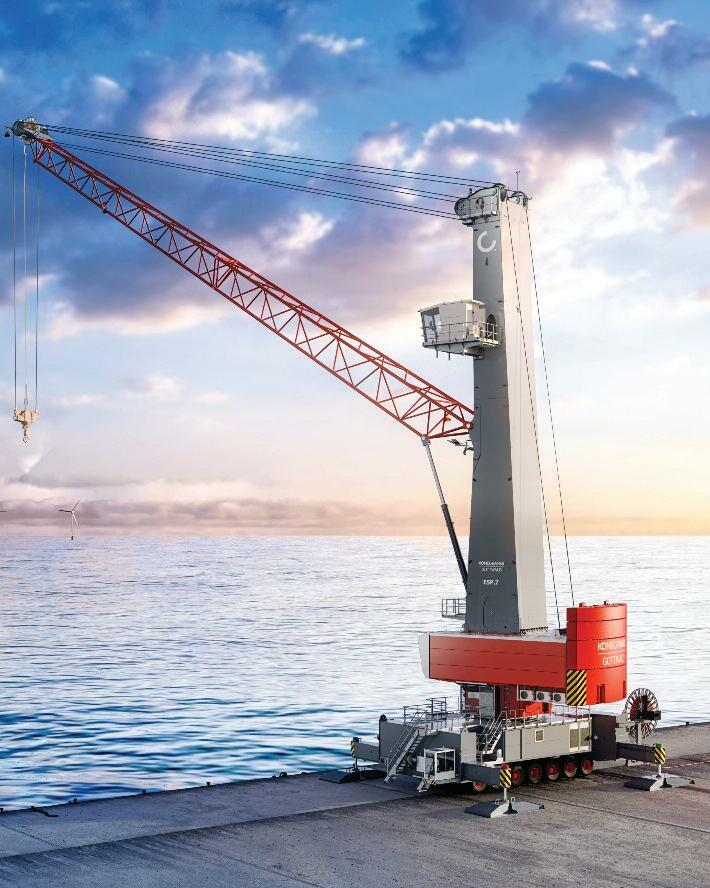
Konecranes has been busy with their Mobile Harbour Crane offerings.
Total loss - numerous luxury German cars including electric vehicles were on board MV Felicity Ace when a fire broke out.
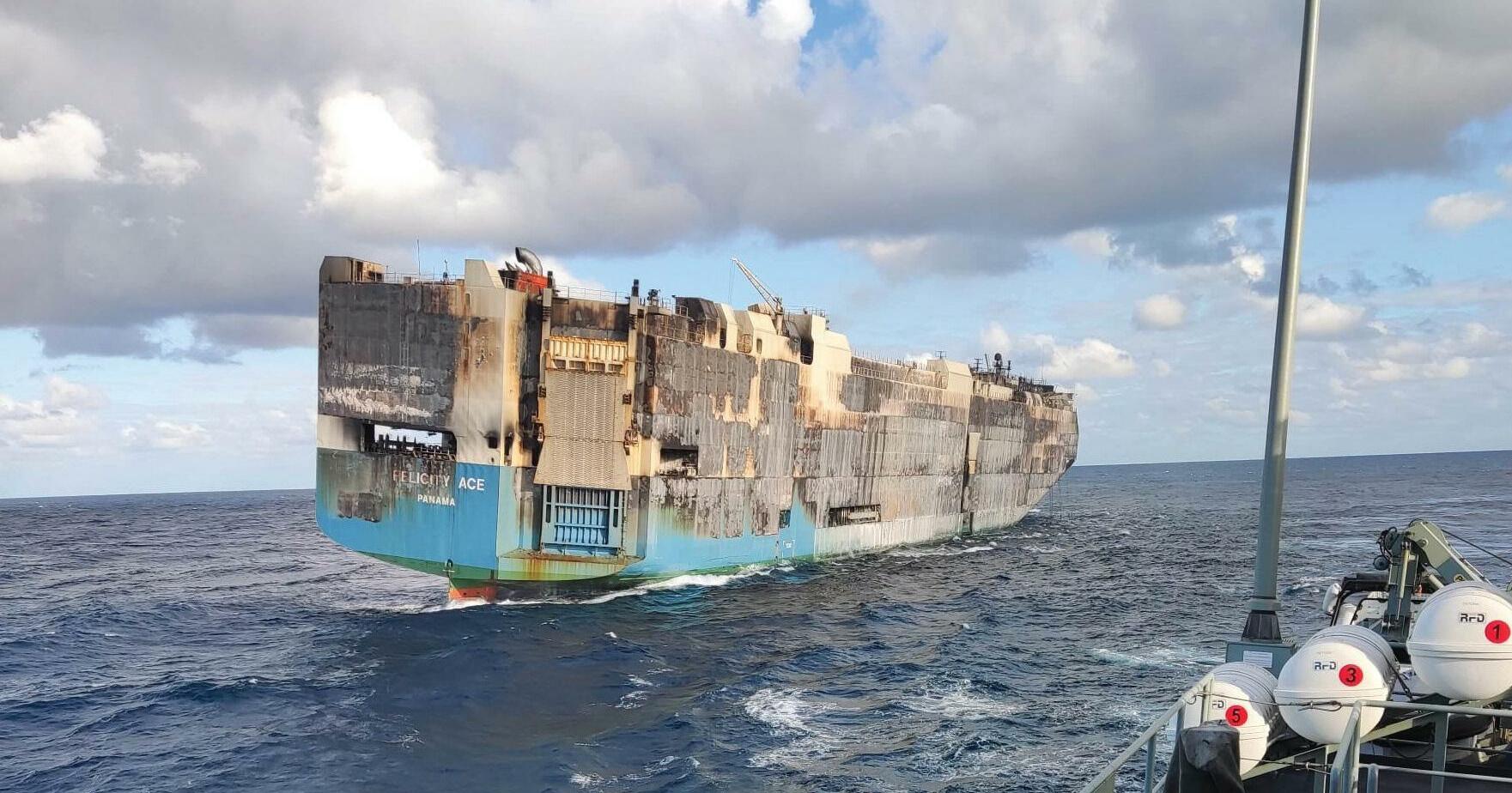
TheThe pitfallspitfalls ofof goinggoing electric...electric...
Ourarticleonelectricreachstackersin ourlastissuegeneratedsomeinteresting feedbackfromourreaders.Inthisarticle welookatrecentdevelopmentsintheuse andpossiblepitfallsoflithiumbatteries. ThomasFrancisreports…
The market for electric equipment is exponentially increasing through demand from terminal operators around the world, but whilst equipment manufacturers put such machinery in their offering, there are rumours of pitfalls ahead.
Elon Musk once made a prediction that every form of transport (with the exception of space-faring rockets) will become electric. This prediction is starting to materialise as markets for electric cars, trucks, buses, boats, two-wheelers and air taxis reached new heights in 2021.
As we have seen in our previous issue, such a statement, undoubtly, is also applicable for electric container and bulk handling equipment. Over the years, numerous manufacturers have taken the huge step of putting their R&D departments to some good use by developing electric machinery.
One of these companies is BigTruck container handling manufacturer Hyster, based in Nijmegen, the Netherlands. Here, innovative applications of lithium-ion batteries and hydrogen fuel cells are enabling the company to develop zero emission container handlers and reachstackers for the first time. Plus, StageV engines that comply with EU emission regulations are introduced for Hyster BigTrucks, with capacities of 8 tonnes or more, helping businesses comply with emissions legislation, while also heightening productivity,and reducing the cost of ownership for the customer.
“As well as implementing sustainable manufacturing processes, we are also evolving the complete range of Hyster products towards low or zero emissions with key advances in technology and truck design, ” explains Conal McNally, Environmental Engineer for Hyster Europe. “From Big Trucks used in ports and terminals, right down to low-capacity lift trucks in busy logistics operations. ”
To further support the reduction in its carbon footprint, Hyster also employs low emission methods to deliver finished trucks to customers,wherever possible.Reachstackers, constructed in Nijmegen, can be transported by barge from their facility to the main port of Zeebrugge in Belgium, thus reducing the number of trucks on the road, and saving on fuel consumption.
“A big part of our green approach is supporting customers across multiple industry sectors in their own sustainability objectives with the right products,and the right aftermarket solutions, such as carbon-neutral lubricants, ” said McNally. “Some Hyster Big Trucks for the European market are prefilled with Shell’ s carbon neutral engine oil. ” At the beginning of May 2022, Hyster announced it had signed a non-binding Memorandum of Understanding with Hamburger Hafen und Logistik AG (HHLA) for two electric container handling vehicles, including the first-ever empty container handler powered by fuel cell technology in a real-world application.
In addition, the company would also supply the first Hyster terminal tractor in Europe. Both units will be powered by Nuvera fuel cells and run on hydrogen fuel produced locally at the HHLA Hamburg Green Hydrogen Hub.
The hydrogen fuel cell-powered empty container handler will be powered by a single, 60-kilowatt Nuvera fuel cell, while the terminal tractor will be powered by a 45-kilowatt Nuvera fuel cell. Both trucks will share many of the same components such as drive motor, battery modules, converters, hydrogen tanks and controls.
The equipment will be deployed at the HHLA Container Terminal Tollerort (CTT) in Hamburg, Germany. It is planned to equip CTT with a refuelling infrastructure and connect the terminal to the future Hamburg hydrogen grid.The delivery of the terminal tractor is planned for late 2022, with the empty container handler to follow in early 2023. There is no doubt that lift trucks are a vital part of cargo handling operations, and expectations are that the ports industry will
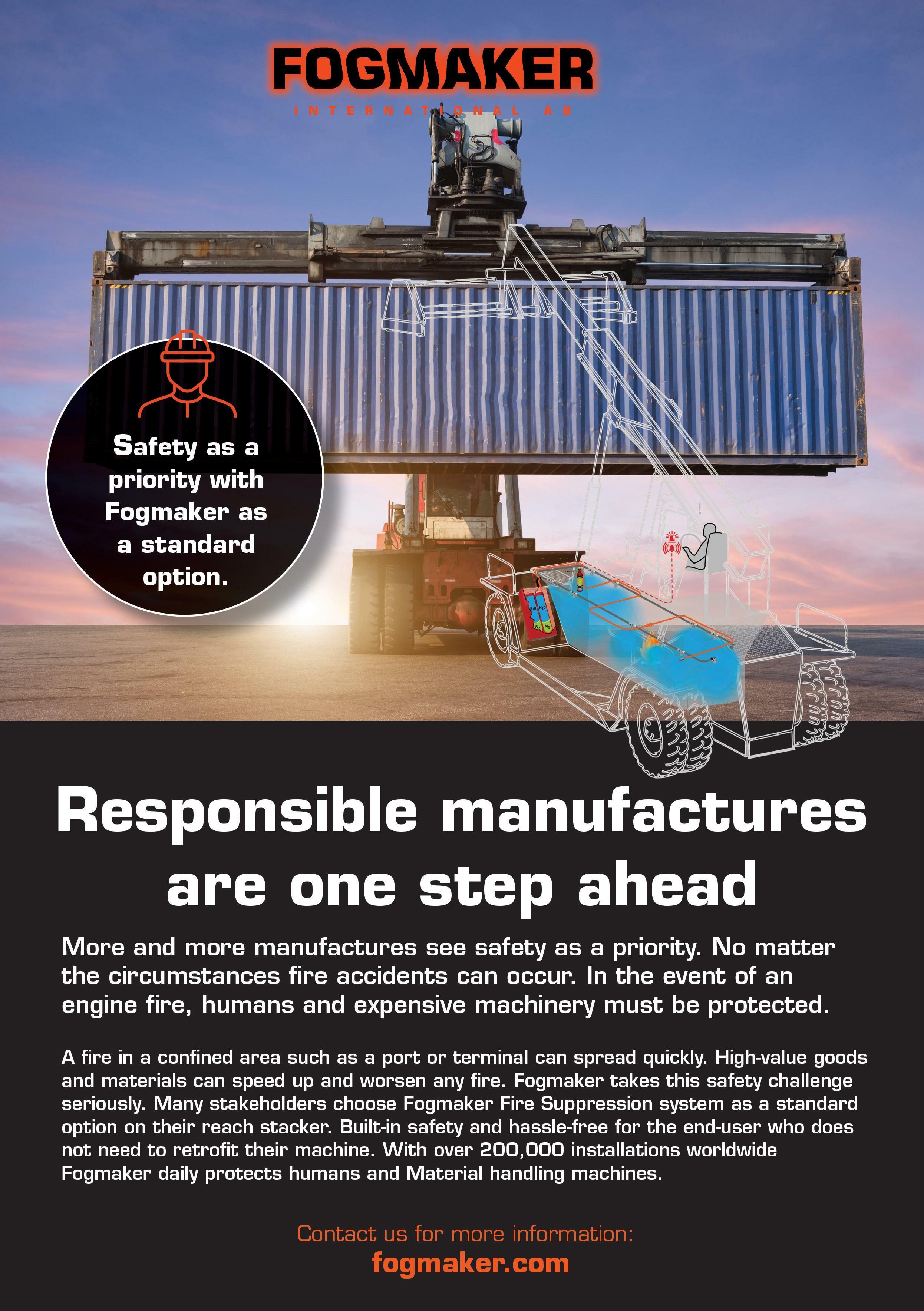
provide a fantastic place for many to begin the transition to clean power, as there is a growing interest from ports and terminals alike to electrify operations and ‘ go green ’ .
Pitfalls
Despite record growth in the sector of alternative fuel including electric cargo handling equipment, the tragic war in Ukraine is creating new challenges for manufacturers on top of two highly challenging and unpredictable years caused by the global COVID pandemic.
As economies have opened up after the COVID-19 restrictions, and sanctions against Russia have constrained oil and gas supply, electricity prices and fuel prices have climbed. This brings electric vehicle markets to the forefront, but at a time when equipment manufacturers grapple with a lingering chip shortage, new COVID lockdowns in China, increased raw material prices, and shortages of parts produced in Ukraine.
As a result, it is to be expected that many equipment manufacturers will be forced to react, increase prices or delay and limit production. Expect that these price increases will not be trivial.When comparing port equipment manufacturers with car manufacturers for example, and looking at the electric car - the Tesla ’ s base Model 3 - we can see a staggering 20% increase from around USD39,990 in 2020 to USD46,990 in 2022.
In addition, some car manufacturers have limited their production with the latest news coming from automotive giant Volkswagen (VW) announcing earlier this year that it has effectively sold out of electric vehicles in the US and Europe for 2022.
When we turn to electric container handling equipment there is just one main component of concern - the battery.The battery remains the largest cost component of the equipment, and climbing costs of battery raw materials, particularly lithium and nickel, are a factor behind the huge increases.
This is driven by shortages and new lockdowns in China as well as the Russia-Ukraine war with China processing most of the world’ s lithium, whilst Russia accounts for around a fifth of global class 1 nickel supplies.As shortages continue, this will have a huge impact on non-automotive sectors including cargo handling equipment which use similar technologies. With more and more terminal operators opting for ‘ greener ’ cargo handling machinery the use of lithium-ion batteries, used to power the equipment, has seen a sharp rise. These lithium batteries are required to be certified to an international standard involving a rigorous series of tests performed by an approved independent testing laboratory, to ensure they can both withstand everyday use through their expected lifetime and the rigours of transport.
Unfortunately, the huge demand has been accompanied by supply of cheaper, poorer quality and untested batteries, including refurbished and even homemade power banks. “E-commerce platforms have facilitated a global trade in potentially lethal products, often circumventing global standards and regulations, ” said Peregrine Storrs-Fox, Risk Management Director at TT Club - a market-leading independent provider of mutual insurance and related risk management services to the international transport and logistics industry.
Revised regulatory restrictions regarding the carriage by air of lithium batteries, may result in greater volumes being transported by surface modes. Recently recorded incidents of container fires caused by, or suspected to involve lithium batteries,as well as conflagrations of significant proportions on car carriers and ro-pax ships mean that safety concerns rightly continue to grow amongst the maritime community.
Fires caused by lithium-ion batteries are ferocious and extremely difficult to control. Terminal personnel and ships ’ crew can face serious injury or worse when these batteries overheat (thermal runway) and ignite. Another problem is that often people don ’t know how to quell the flames.
In the shipping sector we have seen quite a few blazes on ships in recent years caused by vehicle batteries.And with more and more electric driven equipment on container yards, fire caused by electric vehicle batteries will become commonplace.
“Make sure the fire never reaches the lithium-ion batteries and in case it does make sure the deployment time of your fire suppression system gives you enough time to evacuate, ” warns Fredrik Rönnqvist, Key Account Manager at Sweden-based Fogmaker. Fogmaker focuses on fire initiators, which are external to the battery, to prevent a fire from spreading to a battery, as well as delaying the spread of fire from a battery to adjacent materials. “There are several fire initiators in an electric vehicle such as heaters,A/C-compressors, hydraulic fluids, 12/24 volt systems, flammable materials and interior textiles etc., ” explains Rönnqvist.
By installing Fogmaker ’ s high performance water mist system it will protect these common fire initiators, for example by thermal shielding and cooling the exterior of a battery in an (electric) vehicle.
Although some terminal operators might be reluctant to use water on ’ electric ’ fires, reports and research have shown water mist as the premier choice of fire suppression and cooling for vehicles, Lithium-ion batteries and hot surfaces.The reason for this is that water mist cannot conduct electricity in the range of voltage found in automotive applications.This is assured by the micro-sized water mist droplets - water and insulating air in between those droplets. “Fogmaker ’ s water mist will not penetrate IP classification IP66 or higher either, ” says Rönnqvist.
“Understanding the risks is crucial, ” comments Storrs-Fox. “The majority of shippers will take all practicable steps to ensure that their lithium batteries achieve certification and are classified, packaged, packed, labelled and also declared correctly. A small - frankly criminal - minority are motivated to avoid compliance, entering cargo into the supply chain that presents great risk to all, ” said Storrs-Fox.
“Once lithium batteries are placed into the intermodal supply chain, there is little opportunity for the cargo to be checked, visually or otherwise to verify compliance. For all who are contracted to transport, handle or store lithium batteries therefore, developing a thorough understanding of this particular cargo is a prudent step. Moreover, due diligence into the origin of manufacture and integrity of the shipper instigating the move of these potentially lethal power sources is critical. ”
It is clear that with these last remarks from Storrs-Fox the shipping industry needs to look much closer at how to procure lithium batterires and consider safety before price.