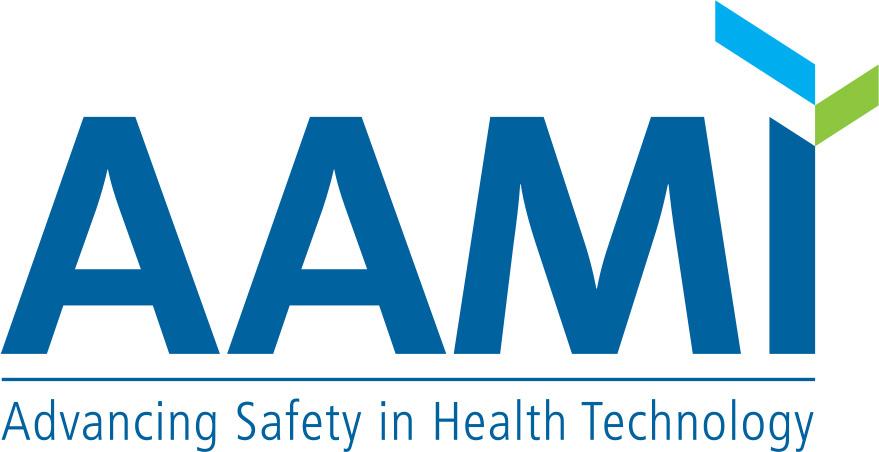
3 minute read
AAMI Update
Medical Device Work Order Types Standardized by CMMS Collaborative
Following an early first success with the standardization of healthcare technology management (HTM) failure codes, a new white paper from the AAMI-sponsored CMMS Collaborative project has been published to create a standard categorization for all work activities carried out by HTM personnel.
Up until now, there has not been a standard approach for using the “work order type” field that is found in most computerized maintenance management system (CMMS) software.
“The HTM community has been rather inconsistent in how they configure them, what data they associate with them, and what is done with the data,” the white paper reads. “It was agreed that the types and data associated with them could not readily drive management decision-making because of these inconsistencies.”
The team was initially hesitant to invest time and resources into standardizing something as seemingly straightforward as labeling different types of work orders for HTM departments, according to Matt Baretich of Baretich Engineering and Vancouver Coastal Health, co-facilitator of the new white paper. However, as the CMMS Collaborative team worked to consolidate key data from the HTM community, they kept running into issues concerning how departments categorized their work.
“It’s not quite as easy as defining planned maintenance (PM) and repair. Of course, we do lots more and we need to capture that somehow,” Baretich said. “For example, there’s the cybersecurity and networking work that we do. That’s not really PM; it’s not really repair, but it’s very important.”
On a high level, the new white paper outlines best practices for differentiating between maintenance and non-maintenance activities in most CMMS databases. This can help managers optimize their maintenance schedules or craft Alternative Equipment Maintenance (AEM) programs as needed.
“What makes this effort different is that we’ve got the suppliers who build the tools that use these codes agreeing to this standardization,” said Baretich. “Their customers are looking for best practice for using these deeply customizable management systems, and now there is one.”
Standardizing the data that HTM departments collect “also opens the door for CMMS data to be of value to the larger organization as well,” added Carol Davis-Smith, vice chair of clinical engineering of the AAMI Board of Directors and principal of Carol Davis-Smith & Associates.
Davis-Smith, who worked with Baretich to make this second white paper a reality, explained that consistent data from HTM departments will enable the setting of benchmarks for comparing program success between health system locations and service providers. Additionally, a long-term goal for the project team is better informed policy. With robust data, the HTM community and CMMS suppliers can work with regulators in a more proactive manner than is currently possible.
But first, HTM departments must adapt the failure code and new work order type standards. To facilitate a speedy adoption, the CMMS Collaborative members have already committed to working with
their existing clients to transition from current platform configurations to ones that leverage the team’s evolving standards.
“When we started this project, we were worried that CMMS suppliers wouldn’t want to collaborate with their competitors,” Baretich said. “However, that worry was really off base. By standardizing things that are common to all CMMS packages, suppliers can remain very competitive on how they implement it and the extra features they offer, even while enabling clear applications of data, and ultimately, better ways to ensure patient safety.”
The new white paper Optimizing the CMMS Work Order Type Field was sponsored by the Association for the Advancement of Medical Instrumentation (AAMI) and represents the insights of a CMMS Collaborative made up of experts from Accruent, EQ2, MediMizer, Nuvolo, Phoenix Data Systems, and TMA Systems. It can be downloaded at aami.org
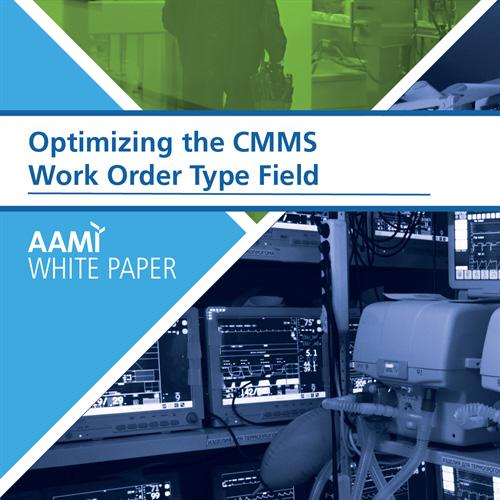
QUALITY FOCUSED. DATA DRIVEN. CUSTOMER MINDED.

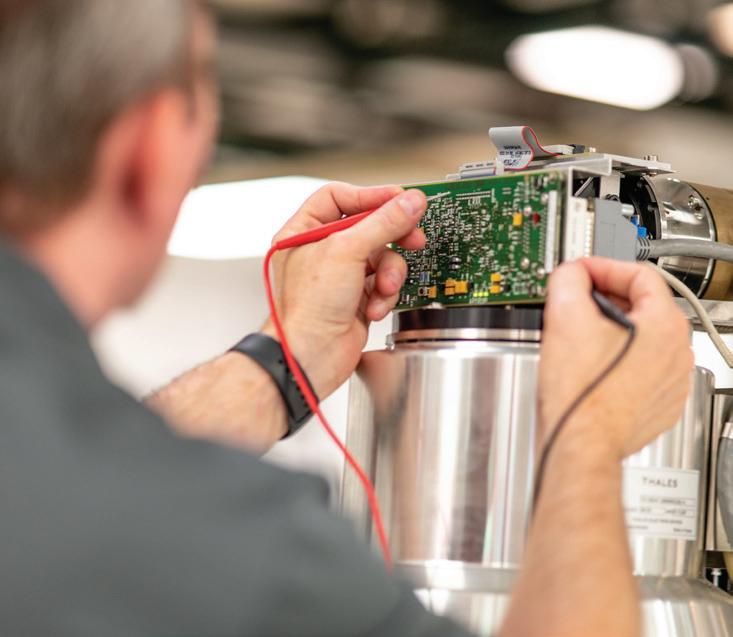
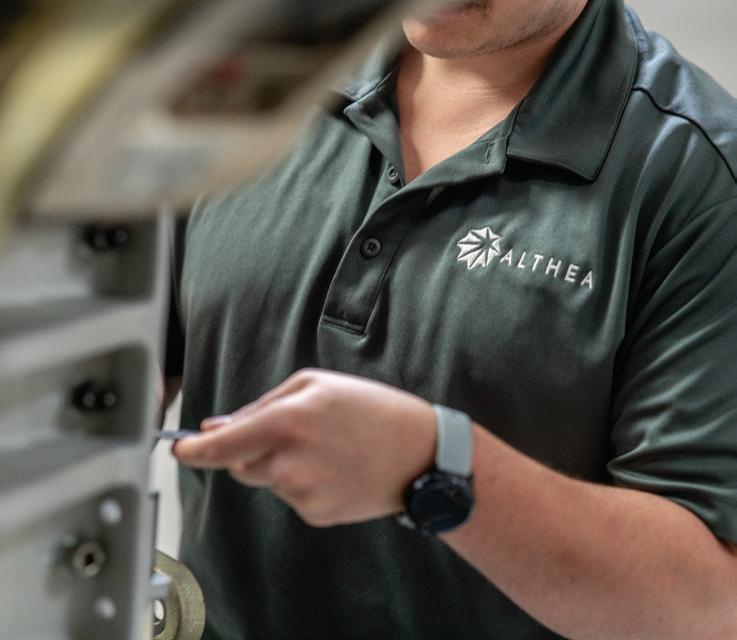
Our Core:
MRI CT Injectors XRAY Mammography Our Service Offerings:
Parts
Depot Repair
Training Service and Support Equipment Sales and De-install/Installation
Contact us at (888)652-5974
or us.sales@althea-group.com Ask us about our parts plus program!
Scan the QR code below and follow us on LinkedIn.