
6 minute read
REFRIGERATION Phil J. Boudreau A detailed review of the various methods of oil cooling
OIL COOLING FOR SCREW COMPRESSORS − PART II
In Part I in the November/December 2020 issue (available online at www.mechanicalbusiness.com), the need for oil cooling in screw compressors at higher compression ratios was discussed. In this article, we review the various methods of oil cooling in more detail; the function of thermostatic mixing valves in oil cooling applications; and points that cover the sequence of operation.
As mentioned, liquid refrigerant injection oil cooling is very limited. The amount of injection cooling must not exceed a certain percentage of the total cooling capacity. When cooling the compression process using this method, the liquid injection may be fed into the economizer port or dedicated liquid injection port as recommended by the compressor manufacturer. Note the liquid is not fed into the suction port of the compressor as it can result in lubrication problems for the compressor.
Water-cooled, refrigerant (DX) and air-cooled are the main methods used for oil cooling. The DX cooler simply uses a DX system to extract the heat while the water-cooled method uses an oil-to-water or aqueous solution type of heat exchanger with one or more valves to control the fluid flow. In situations where the oil cooler temperature drops below 20°C (68°F) during the off cycle and/or the volume of oil in the oil cooler and associated piping exceeds 25 litres or 6.6 U.S. gallons, the circuit must be designed so that the oil leaving the oil separator bypasses the oil cooler. This can be accomplished by using a mixing valve which, in addition to regulating flow through the oil cooler, allows the oil to warm up quickly.
In situations where the oil cooler is subject to cold ambient temperatures, it may be also necessary to add heat and insulation to the oil injection piping. In this type of application, it is also important to ensure that the oil separator is kept sufficiently warm during the off cycle and the oil separator is heated and insulated to minimize heat loss.
The mixing valve is typically installed so that the hot oil from the oil separator is connected to port B and the cooled oil from oil cooler is connected to port C on the valve. These ports are both used as inlets in this case. Mixing valve port A is then connected to the oil injection line feeding the compressor.
An alternate way to connect this valve is in a diverting type of arrangement, where the hot oil from the oil separator is connected to valve port A, the oil cooler inlet is connected to valve port C, and the compressor’s oil injection line is connected to port B. In this case, the valve is used in such as way that results
FIGURE 1 WATER-COOLED OIL COOLER

Phil Boudreau Phil is the Ontario sales manager for Bitzer Canada Inc. and provides training and technical support for Bitzer’s clientele. He can be contacted at: pboudreau@bitzer.ca.
in one of the ports being an inlet and the remaining ports being outlets. However, in both configurations, the valve modulates to maintain the desired oil temperature for the compressor so the results are the same. Always refer to the compressor manufacturer’s instructions to ensure correct application of the three-way oil valve.
In Figure 2, which illustrates the air-cooled oil cooler with a three-way valve, the valve is used in a mixing configuration which maintains the desired oil injection temperature. When the valve is piped in a diverting mode, the oil temperature leaving the oil separator is maintained because the internal thermostatic element modulates flow according to the temperature at port A.
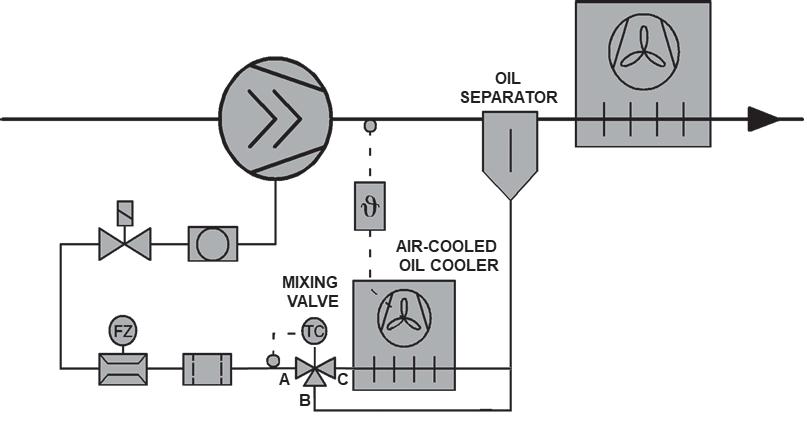
An alternative arrangement is to use a type of valve that modulates oil flow through the oil cooler based on the discharge line temperature. In this case, a three-way valve with remote temperature sensor will be required. When this approach is used, it is possible to maintain a very consistent discharge temperature. When using a valve that modulates oil flow through the oil cooler based on oil injection temperature, a constant oil injection temperature will be maintained.
However, with ammonia applications, it is generally recommended, and perhaps even required in some cases, to modulate oil flow through the oil cooler based on the temperature of the oil entering the compressor.
LIKE YOU, THE SuperEvac™ PLUS II IS ALWAYS READY.


The integral DC motor means power on demand… less wear and tear over time. Lightweight puts less strain on you. The SuperEvac™ PLUS II gets the job done.
WORKS IN LOW VOLTAGE CONDITIONS HANDLES EXTREME TEMPS 20% LIGHTER WEIGHT THAN AC PUMPS A2L SYSTEM COMPATIBLE
MADE IN THE USA To learn more, connect at yellowjacket.com
A
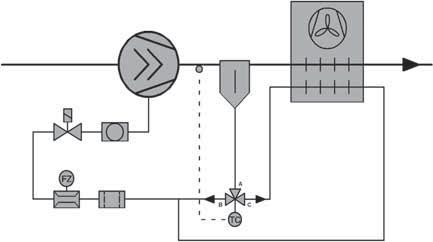
B C
It is possible to integrate the oil cooling circuit into the air-cooled condenser. However, in this case, the fan-cycling control strategy must also ensure proper oil cooling during all operating conditions. This can be a challenge in some cases because oil cooling load may increase as the load decreases. The condenser fans are typically cycled based on ambient temperature or condensing pressure and not compressor discharge or oil temperature. Integrating the oil cooling into the condenser should not be considered for situations where the condenser is not close coupled to the oil separator. The oil cooler must be located as close to the compressor as possible. Additionally, it should be installed at an elevation that is lower than the oil injection port of the compressor to prevent the possibility of It is possible to size the condenser to carry both the total compressor heat of rejection and the oil cooling load. This can be accomplished using a thermosyphon oil cooler approach. With this approach, a thermosyphon receiver is placed below the air-cooled condenser, but above the oil cooler. The thermosyphon receiver takes what it needs before transferring the remaining liquid to the system’s main receiver. This ensures that there will always be adequate liquid refrigerant for oil cooling. Liquid from heat exchanger used to cool the oil. Therefore, this is a refrigerant-cooled oil cooler. A brazed plate heat exchanger or shell and tube heat exchanger can be used for this purpose, but direct expansion heat exchangers used in this application must be selected and installed in piping lengths must be also calculated and arranged in such a way to allow the thermosyphon arrangement to that the pressure gained in the liquid drop leg from the thermosyphon receiver must be high enough to overcome the pressure needed to return the superheated vapour to the thermosyphon receiver. This same approach must be used to ensure that the heat-laden vapour that accumulates in the thermosyphon receiver will naturally transfer back to the air-cooled condenser as needed.
Imagine a Refrigeration System that…
• Uses 100% “plug & play”controls over secure connection • Less than half the refrigerant charge of conventional platforms • Incorporates Vapour Drive™ … oil free, magnetic drive, 0-100% modulation, semi hermetic scroll compressor • VFD driven modulating compressors
No need to imagine. Meet the Oxford LPP.

