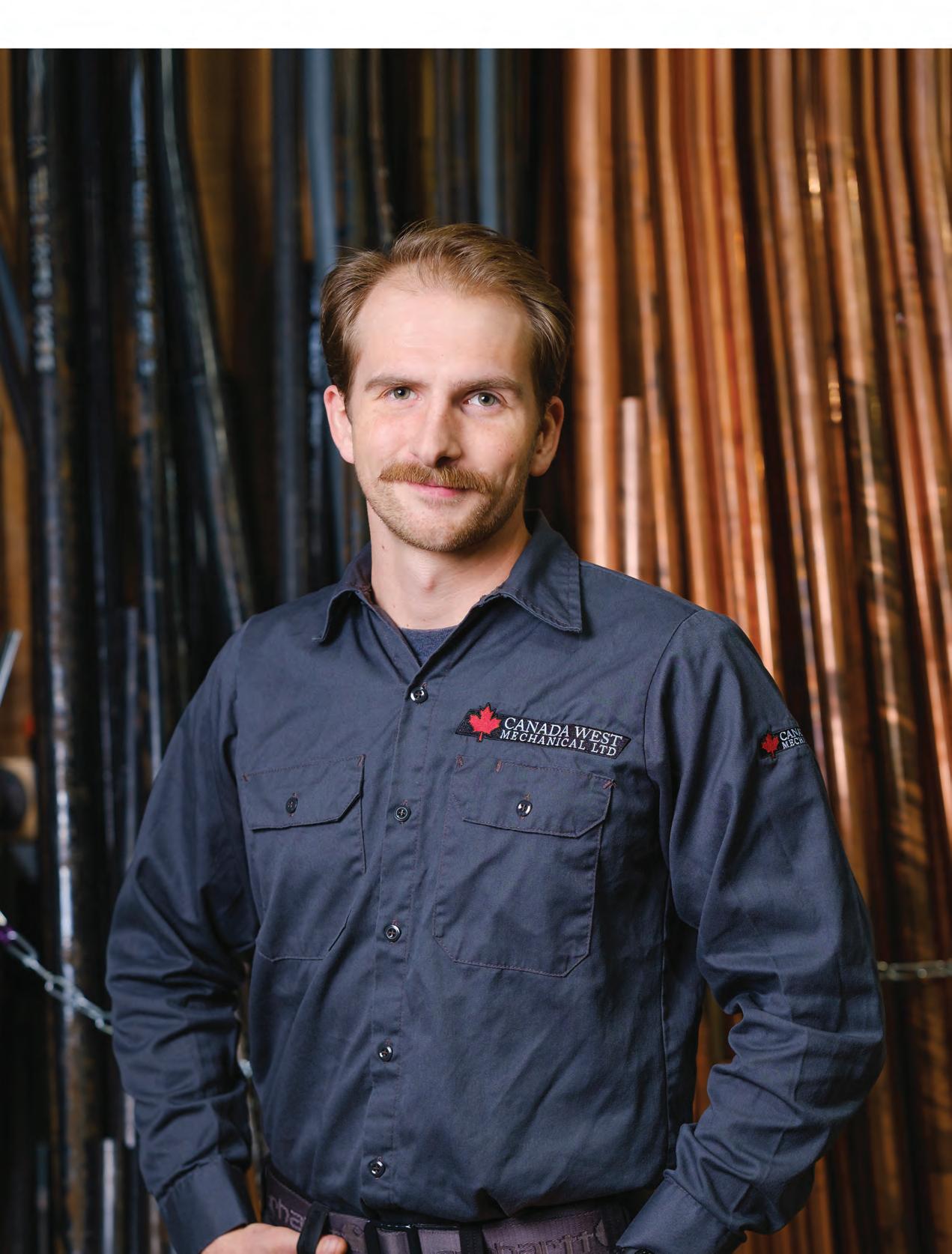
DISTRIBUTION SYSTEM TROUBLESHOOTING MASTERING EFFECTIVE HYDRAULIC SEPARATION
COMBUSTION: HOW TO ENSURE A SAFE AND EFFICIENT FLAME BOILER INSTALLATION DOS AND DON’TS PRODUCT SHOWCASE
DISTRIBUTION SYSTEM TROUBLESHOOTING MASTERING EFFECTIVE HYDRAULIC SEPARATION
COMBUSTION: HOW TO ENSURE A SAFE AND EFFICIENT FLAME BOILER INSTALLATION DOS AND DON’TS PRODUCT SHOWCASE
One of the most innovative commercial boilers on the market, CREST® boilers with Hellcat™ Combustion Technology features a ground-breaking O₂ sensor system, designed for condensing hydronic boilers. Combined with Lochinvar’s highly-advanced SMART TOUCH™ control system, this unit can intuitively adapt to the environment it’s installed in, without any manual adjustments - making it a truly intelligent boiler.
Learn more about CREST boilers with Hellcat Combustion Technology at lochinvar.com
Content Media Group Inc. 2 Campbell Dr., Suite 807 Uxbridge, ON L9P 0A3
Tel: 905.465.2919 www.mechanicalbusiness.com
January/February 2025 Issue Published 2 times per year.
For All Subscription Inquiries
Shila Naik Circulation Director 905-272-4175 shila.naik@mechanicalbusiness.com
Editor: Kerry Turner, C 416-435-1193 kerry.turner@mechanicalbusiness.com
National Sales Manager: Kyle Badder, C 416-735-1375 kyle.badder@mechanicalbusiness.com
Operations Manager: Caroline Bexfield, C 647-217-2076 caroline.bexfield@mechanicalbusiness.com
Contributing Editor: Carolyn Cooper editorial@mechanicalbusiness.com
Art Direction: Fourteen Orange Graphic Design Inc. davem@fourteenorange.com
Controller: Liz Mills liz.mills@mechanicalbusiness.com
Publisher: Bruce Meacock, C 416-457-9563 bruce.meacock@mechanicalbusiness.com
System
Bob “Hot Rod” Rohr
Installation dos and don’ts Chad Edmondson
When it comes to boilers, we tend to spend a lot of time discussing which piping method is best and/or which zoning method rules. What we don’t spend enough time on is the combustion side of things.
Matthew Reid
Dustin Wright, a Red Seal plumber and gasfitter at Calgary, AB’s Canada West Mechanical Ltd., enjoys the changing nature of hydronics.
Carolyn Cooper
A
Match the correct definition or meaning to the terminology you hear in the field and enter for your chance to win a $150
Hydraulic separation is key to maintaining balance in hydronic systems, ensuring smooth and efficient water flow in a closed-loop hydronic system.
Todd Wiggins
When it comes to boilers, we tend to spend a lot of time discussing which piping method is best and/or which zoning method rules. What we don’t spend too much time on is the combustion side of things.
The combustion of a gas fired appliance such as a boiler falls into three major parts. The combustion air, the actual flame, and the flue exhaust. Those three components are going to be responsible for ensuring a safe and efficient flame.
I want to stress that the two best places to get information for all these components are the manufacturer’s installation manual, and the gas code such as CSA B149. It is also important to note there will be overlap between residential and commercial but there are also going to be some differences depending on the set up.
Negative pressure or an undersized combustion intake pipe will cause you intermittent headaches on some jobs.
There are two options for combustion air. Either direct pipe (bringing in combustion air directly to the appliance) or room air. There are proponents for both. For appliances under the 400 MBTU/hr limit, there are some good arguments for the direct pipe approach. It is relatively simple, provided you have the room, and it takes the room pressure out of the equation. Manufacturers will usually provide guidelines as to which size pipe to use depending on the length of the run.
With larger and much larger appliances, I have seen snow and ice buildup inside the appliance because they draw a tremendous amount of air for the combustion cycle and in the middle of a snowstorm you will be pulling a lot of air and atmospheric conditions will apply.
For the room air option, you will need to provide a room opening according
to the manufacturer’s manual which may or may not comply with the gas code. CSA B149 states there must be a permanent air supply opening having a total crosssectional area of not less than 1 sq. in. for each 30 MBTU/ hr (30,000 BTU/hr) when using the room for combustion air. However, some manufacturer manuals state there must be an opening of not less than 1 sq. in. for each 4,000 BTU/hr. That is quite the difference. The main goal of the manufacturer’s installation manual is to ensure the room never goes into a negative pressure.
Manufacturers will usually provide guidelines as to which size pipe to use depending on the length of the run.
Matthew Reid is technical director – heating division at Enviroair’s Richmond Hill, ON office. He can be reached at mreid@enviroair.ca
The actual combustion of the fuel is going to be dependent on a few things, including gas and gas pressure. Gas pressure is going to be a result of the regulator, pipe sizing and pipe length. All of these items must work in unison to provide the appropriate gas pressure to the appliance. Starting with the regulator, it is important to get a regulator that can adequately support the appliance you are installing. In some residential cases you won’t need to worry about this if the regulator from the gas supplier can adequately handle the total building load.
In commercial applications it may be necessary to use multiple regulators in a building with a specific one just handling the boiler load. In cases where an additional regulator must be used, be sure to give some pipe length between the regulator and the boiler. If they are too close you will not have enough pressure built up in the lines to adequately handle the fluctuations in pressure during light off and modulation.
We’ll come back to modulation when we discuss exhaust but this plays a very large role in overall combustion efficiency. Pipe sizing plays a role as well. Undersized piping usually happens because we didn’t factor in the equivalant length of the fittings.
Gas pressure, pipe sizing and pipe length must work in unison to provide the appropriate gas pressure to the appliance.
By Matthew Reid
Next on the combustion list is “dialing in the boiler” or tuning. The primary byproducts of combustion are CO₂ and H₂O. Some access O₂ is necessary for clean, safe and reliable combustion. Too little and you do not have a clean burn. Too much and you lose efficiency. You usually dial in combustion levels (primarily O₂ and CO₂) when tuning a boiler. As O₂ goes up, CO₂ goes down and vice versa. You usually dial in at high fire and at low fire but some boilers have multiple points of combustion that need to be set.
How often a boiler should be tuned depends on a number of variables.
There are also CO limitations to be aware of. High levels of CO can be caused by a number of things, but the main culprits are either a cracked HX or the unit needs tuning.
I get asked a lot as to how often a boiler should be tuned. That’s a hard question to answer as there are a number of variables such as the time of year, air quality, gas quality, and boiler operations, but I will tell you that it’s very difficult to do it too often. On the flipside, it’s very easy to not do it often enough.
The primary byproducts of combustion are CO₂ and H₂O.
Light off refers to when the appliance, such as a boiler, ignites. It is the stage of the sequence of operations when you have ignition. The fuel and air mixture flows past either a HSI (hot surface ignitor) or spark generator and that mixture combusts. The first few moments of that combustion are called light off. After light off, the flame sensor will prove flame and then the ignitor or spark generator will stop and the burner will usually modulate either up or down depending on the delta T between the demand temperature and the incoming water temp.
Finally, on to exhaust. Again, there are some overlaps between residential and commercial but the larger the application the more complex exhaust venting becomes. For smaller residential applications the manufacturer will provide a chart that states how long you can vent with a certain size pipe. This is referred to as equivalent length.
For commercial it’s more about the draft pressure. There is a reason for this. The equivalent length method is not a substitute for good engineering practice to determine acceptability of a vent system. This is due to varying burner modulation rates, ambient air temperatures, and flue gas temperatures, among other factors.
The key word to take note of here is the modulation rate. This is where things can get complicated for commercial installs. If you have a 1,000 MBTU/hr boiler with a 10:1 turndown, you have a maximum firing rate of 1,000 MBTU/hr and a minimum of 100 MBTU/hr. The burner modulates its fan speed, and the gas valves either allow or pull a certain amount of gas in, to meet the target combustion to satisfy the load.
So, the air we pull for combustion can change, the gas can change but our exhaust pipe cannot change. It is a fixed pipe size and length. This problem becomes more complex when we are talking about multiple boilers. If you have a vent pipe sized for two or three 1,000 MBTU/hr boilers but it’s the beginning of fall and the load can be maintained by one boiler at low fire, the flue vent may have a hard time maintaining draft pressure. A few things can help with this, including a modulating flue damper which effectively changes the “size” of the draft as far as the boiler is concerned.
The other item that I would highly recommend for a multiple boiler system is a draft fan. These fans can modulate to maintain whatever draft pressure the boiler requires regardless of how many boilers are firing and at what rate. Truly this is the right answer when it comes to venting large boilers with a high turndown rate and multiple boiler applications.
Acommonservice call for a hydronic system usually revolves around the mechanical components in the mechanical room. As the troubleshooter, you may start your diagnosis by cranking up the thermostats to check individual zones for operation. Next, you’ll ensure the pumps and/or zone valves operate and you have adequate flow. What is often overlooked is the distribution system, specifically the heat emitter. Perhaps the one I see most compromised is the common fin tube. First, ensure that the fins are in the correct direction. Cool floor temperature air comes into the bottom of the enclosure and convects upward. They do not work very well if the fin openings are from front to back − don’t laugh.
The heat emitter assessment and cleaning will take time, maybe hours or a day.
By Bob “Hot Rod” Rohr
Bob Rohr is a trainer with Caleffi, and was the recipient of the 2020-2022 CarlsonHolohan Industry Award of Excellence. He has 40+ years of experience as a plumbing, radiant heat and renewable energy contractor.
If there are underperforming areas of the home, check that there is adequate fin tube to cover the load. Use the manufacturer’s rating chart for expected output. Fin tube output is based on the average water temperature (AWT) through the loop. Measure incoming temperature after the system has been running, and the temperature at the end of the loop. Add these values together and divide by 2. For example, 180°F supply water temperature (SWT) and 160°F return water temperature (RWT) averages to 170°F. Use that number for output.
The next step is to make sure there is an air space below the front enclosure of the fin tube. If flooring was added or carpet installed over a previous wood floor, this can cut down on the air space, and lower convection and output. Dampers need to be fully opened. Pet hair can also restrict air flow considerably. Check and vacuum as needed. However, be careful with the vacuum. Fins damaged from aggressive vacuum cleaner operation will reduce output. Front enclosures need to be in place and custom wood covers need to have adequate air slots on top and air space below for convection currents to flow across the fins.
Manual bleeders are often found on baseboard ells. If you hear water flowing, you may need to do some bleeding at the individual runs.
The system needs to run and get to thermal equilibrium to get accurate heat output assessments. Hydraulic equilibrium is reached when the SWT and RWT are staying stable. This tells you the heat emitters are putting their full output into the space. At this point take your SWT and RWT measurements. Some fin tube ratings have a “pick up factor” added. If you are dealing with a new or tightly-insulated home, divide by 1.15 to get a more realistic output number. Even today, the rating tables published by baseboard manufacturers list heat outputs at water temperatures up to 220°F, and in some cases up to 230°F. An example of such a rating table is shown in Figure 1.
A footnote that often accompanies a fin tube rating table states the ratings include a 15 per cent “heat effect factor.” When conceived decades ago, this factor was meant to boost the tested heat output by 15 per cent to account for the baseboard being installed at floor level, where surrounding air temperatures were often significantly cooler than air temperatures higher in the room.
Figure 1 Rating Table
Today’s homes do not have such drastic room air temperature stratification, and as such, the heating effect factor is not appropriate. Conservative design practice is to divide any heat output ratings that include the heating effect factor by 1.15 to remove it and use the corrected value when sizing the baseboard.
Based on typical rating tables similar to Figure 1 (see pg. 46), one might assume that a fin tube baseboard cannot operate at water temperatures under 150°F. This is not the case. Any heat emitter will release heat as long as the fluid inside it is warmer − even slightly − than the surrounding air temperature.
Air handlers (AH), fan coil units (FCU), hydro-coils, and kick space heaters are examples of forced convection heat emitters. A fan forces air across the fins to increase the output. These are also prone to plugged fins as the higher airflow tends to pick up and pack in dirt, pet hair, etc. Again, a portable vacuum cleaner with a soft brush end is your friend for servicing any coil or fin tube. Fin combs can help straighten out damaged or crunched fins.
Suspended tube systems need proper insulation. Rim joists should always be rigid foam sealed with spray foam, in my mind. There can be a huge infiltration loss around that exterior framing. A few cans of expanding spray foam can save plenty of heat loss. It is a gift that keeps on giving.
Constipation in radiant systems usually comes from deterioration on the inside of the tube. Take a sample of the system fluid, water or glycol. Look at it, smell it, and let it settle overnight. Most system fluid will take on a brown or gray tint from the metals in the system. That is normal. Fluid should not be black, dark brown, gritty, or smell like an old locker room.
Non-barrier radiant tubing should always be suspect. O2 ingress corrodes ferrous metals, pumps, expansion tanks, and steel nipples. This can form a sludge that coats, or even plugs, the tube. Systems that constantly take on fill water can also scale from the mineral precipitation.
Damaged and plugged fin tube baseboard.
Cast iron or panel radiators should be inspected, also. Some panel radiators have fins inside. They have coarser spacing, but may still be plugged up. There are some convection currents involved with radiators. So, make sure they are not blocked by custom enclosures, or a box across the top. Sometimes radiators have valves on them for adjusting flow or isolating the radiator. Of course, these need to be wide open for maximum performance.
Inspecting radiant tube systems gets more complicated. If you can gain access, be sure it was installed to manufacturer’s requirements. Of course, you won’t be able to inspect the work that has been buried in concrete. Transfer plates need to be tight against the floor. Loop length can sometimes be calculated at the manifold as the foot markers are printed on most tube loops.
Example of clogged radiant tube.
Several types of hydronic cleaners can be used to bring these dirty systems back to better operating conditions. Some cleaners are strong detergents. These work well on systems with oily, or greasy, fluid, and old glycol systems. If the system shows a lot of white scaling from hard water deposits, an acid-based product may be a better option.
Boiler and pump manufacturers have a water quality specification in their manuals. A few inexpensive testers can provide a picture of the fill water compatibility. A pH tester, hardness test kit, and a TDS meter are good to have on hand. These tools can save you so much time and energy. Or you can send a sample to outside companies for a deep analysis. Local wholesalers and reps can steer you to a test option. Add a hydronic system conditioner and get the manufacturer’s test kit and check it every year or two.
Promote the heat emitter assessment and cleaning as a service you offer to get or keep systems working efficiently and saving your customer fuel dollars. Equipment warranty could hinge on proof of required service. So, when the mechanical room looks sound, take your troubleshooting skills off to emitter land.
Water quality on the job should always be tested.
5000 & 6000 MBH
The Avenger® Series II is an advanced two-pass, counter-flow firetube commercial boiler, providing efficient hot water for demanding commercial needs.
» Industry-leading 40:1 turndown
» Thermal efficiencies of up to 96%
» Designed for today’s higher turndown variable primary and low pressure systems
» 3 to 4 week lead-time with stock units available for quick ship
www.camus-hydronics.com/HigherTurndownHydronics
Spirotherm has updated the Spirovent Quad hydraulic separator with powerful magnets for improved efficiency. Available from Ontor, it delivers the same air separation efficiency and adds fast and effective separation of ferrous and non-ferrous debris, while providing the critical interconnection between hydronic loops. Magnets located on the exterior of the housing surround the flow-path of the system water to efficiently capture ferrous material. By sliding the magnet jacket down, the collected debris can be flushed from the unit without having to isolate or open it. The separator is available in 1-, 1 1/4and 1 1/2-in. sizes with threaded, sweat and press fit connections.
www.
ontor.com
Webstone large-diameter Pro-Connect Press XLC fittings include largediameter adapters, couplings, tees, elbows, flanges, and caps in sizes 2 1/2 in. to 4 in. The lead-free fittings are compatible with Press XLC tools, and are available in a range of reducing sizes, and threaded or street end connections in copper or forged dezincification-resistant brass. The fittings feature a single O-ring design, a 300 PSI maximum cold working pressure, 250°F maximum temperature, and are certified to NSF/ANSI 61 & 372 - PS117. www. nibco.com
Weil-McLain Canada’s Simplicity residential stainless steel firetube boiler offers heat-only or both space heating and domestic hot water in a single, compact unit. With high-efficiency performance up to 95 per cent AFUE and a 10:1 turndown, the boiler comes in three sizes (110, 150 and 199 MBH) and features userfriendly interface with Bluetooth connectivity. It is wall-mountable or can be placed on an optional floor stand and is designed for ease of serviceability. www.
weil-mclain.ca
CB Supplies offers IVAR stainless steel radiant manifolds, which are precision manufactured in Italy. Each manifold arrives complete in one box, making installation straightforward. They feature manual shutoff valves and optional actuators (electrothermal heads) for precise circuit control via a controller or space thermostat. Choose from two header sizes (1 in. and 1 1/4 in.) and configurations of two to 12 loops. www. cbsupplies.ca
Rinnai’s RCB-Series RCB1000AN floorstanding commercial boiler is 98 per cent thermal efficient and rated at 999 MBH. Rinnai’s Integrated Cascade Logic allows users to connect up to eight units, each interchangeable as the lead. With builtin levelling caster wheels, they easily roll onto the site and fit through standard doorways. Every RCB-Series boiler features a 10:1 turndown ratio, allowing precise adjustments. They are built with a 316-L stainless steel water tube heat exchanger. www. rinnai.ca
Taco's LOFlo injection pumping system works to reduce the flow of water in hydronic heating and cooling systems such as radiant panel and chilled beam applications. The technology reduces pump flows and pipe sizes, lowering energy consumption and costs, while providing precise control of supply water to the terminal and precise control of room temperatures. The system is designed for a maximum working pressure of 200 psi and maximum fluid temperature of 110°C, in four connection sizes: 3/4, 1, 1 1/4, and 1 1/2 in. www.
tacocomfort.com
Conforto ENERGY STAR certified, high-efficiency condensing gas boilers offer advanced performance with up to 95 per cent AFUE. Designed for wall-mounted or floor-standing installations, they feature gas adaptive technology, integrated advanced intelligence for optimal efficiency, and a compact design. Combi models provide both space heating and domestic hot water, eliminating the need for a separate water heater, with flow rates of up to five gallons per minute.
www.
confortohvac.com
The tekmar Smart Steam Control 289 simplifies steam boiler management with real-time remote access across multiple properties via the Watts OnSite app, enabling adjustments from a phone or desktop. The unit can be retrofitted to any boiler, and offers energy savings of up to 20 per cent through outdoor reset, indoor temperature feedback, and warm weather shut down technology. Key features include system alerts, a 5-in. colour touchscreen with setup wizard, and compatibility with all boiler brands.
www. watts.ca
Viessmann’s air-to-air ductless heat pump systems are suitable for residential and light commercial applications, and offer quiet operation. The heat pumps use inverter technology and offer low ambient heating and cooling down to -22°F (-30°C) and as high as 122°F (50°C). The new Vitocal 100-S single zone heat pump is a high-efficiency unit with ratings up to 28.1 SEER2 and 13.6 HSPF2. Models are available in sizes from 6,000 to 58,000 BTU, with a choice of indoor units. Units come with a total piping length of 213 ft. for flexible installation. www.
viessmann.ca
The HeatLink magnetic dirt separator removes suspended solids from the system fluid, which can otherwise cause increased wear and tear, and decreased system efficiency. The separator uses a candle-shaped magnet in the upper part of the body, plus three more in the lower part to capture ferromagnetic particles. A stainless steel mesh blocks additional residual impurities from passing back into the system. The swivel connection allows for mounting in any orientation on the return or supply side, and a manual air vent allows for the release of entrained air. The GHT drain valve allows for easy draining and cleaning.
www.
heatlink.com
Benchmark E from Aerco is a zeroemissions electric boiler featuring Peak Load Management and Hybrid Plant capability. Up to 16 boilers can be sequenced, including hybrid configurations with gas-fired units. Pair it with AERCO’s SmartPlate EV for a fully electric, vent-free heating and hot water plant. Available in five sizes (216 to 684 kW), the boiler supports up to 350 GPM.
www.
aerco.com
SEP4 four-in-one hydraulic separators (Union) from Caleffi offer a combination of hydraulic, air, dirt and magnetic separation in one unit. The units come complete with a drain valve, thermowell tap (1/2 in. straight female), and mounting bracket. The separators are made of steel, with a maximum operating pressure of 150 psi and a fluid temperature range of 32°F to 212°F.
www.
caleffi.com
Pressure independent balancing control valves (PIBCVs) from Viega automatically adjust to fluctuations in system pressure to ensure a consistent flow rate. Features include full-stroke modulation, built-in PT ports, and EPDM sealing elements. Models are available with and without an actuator. Temperature range is 14°F to 250°F and maximum pressure differential is 116 psid. The latest Viega MegaPress and ProPress PIBCVs offer press technology for ease of installation.
www.
viega.us
Axiom Industries’ Axi-THERM Express canisters offer solutions for residential and light-commercial hydronic system cleaning and inhibitor introduction. Designed for fast, efficient dosing, they deliver precise amounts of cleaning agents, or inhibitors, directly into hydronic systems. The 3/4-in. garden hose swivel adapter and fastaction formula minimize application time. www. axiomind.com
Aquatherm Blue is a long-lasting option for mechanical heating and cooling, and industrial piping systems. The PP-R and PP-RCT piping systems are made from high-quality polypropylene for longevity. The pipe also features a multilayer faser composite, a technology that blends glass fibres with PP-R and PP-RCT to minimize the linear thermal expansion that typically occurs when plastic pipes are exposed to heat. It is installed using heat fusion to create a permanent, leak-free connection. www.
aquatherm.com
Ionic floor standing boilers and volume water heaters from Triangle Tube offer reliability and easy installation and maintenance for commercial applications. The compact units are Low NOx certified, and feature a full-text interactive colour display, and stainless steel heat exchanger. Models range from 1,250 to 4,000 MBH, with modulation of up to 8:51, and thermal efficiency of between 97 and 99.9 per cent. www.
triangletube.com
A. O. Smith/AO Smith
Protects pumps, valves, boilers and heat exchangers from air, dirt and debris
SPIROVENT QUAD
Connections and coalescing medium are engineered to allow for the ultimate in hydraulic balance
Eliminates 100% of the free air, 100% of the entrained air, and up to 99.6% of the dissolved air in the system
Separates dirt particles down to 5 micron and ferrous material using powerful magnets within the flowpath
Combines the advantages of the Spirovent and Spirocombi with the functionality of a hydraulic separator
For information and availability: www.spirotherm.com
Dustin Wright
Name: Dustin Wright
Nickname: Dusty
Company: Canada West Mechanical Ltd.
Job Title: Hydronics specialist – estimator
Born in: Calgary, AB
Lives in: Foothills, AB
Age: 24
Girlfriend: Simone
Pet: A Yorkie called Coffee Bean
“When I started at Canada West, that’s where I got more into the service end, as well as still being able to manage a smaller construction project. I started doing a lot of boiler retrofits, doing some intermittent chiller system installs, as well as service on high efficiency and condensing boilers. That’s where I grew this passion for hydronics,” says Dustin Wright, a Red Seal plumber and gasfitter at Calgary, AB’s Canada West Mechanical Ltd. “It’s something that’s always changing, always updating.”
Growing up Wright says he was always interested in the trades, and originally wanted to be a pipe fitter. After having trouble finding a job in that field, he instead began a plumbing and gas fitting apprenticeship with Calgary’s Botting & Associates, working on large-scale commercial projects. From there he joined Canada West Mechanical, where he is currently the company’s hydronics specialist – estimator. The company provides HVAC/R and hydronic services to the industrial, commercial and resource sectors.
Wright says approximately 60 per cent of his work is servicing, while 40 per cent involves construction projects. “I estimate a lot of our boiler retrofits and intermittent chiller system installs, and am servicing mostly high-efficient condensing boilers. So, fire tubes, water tubes, we do a bunch of mid-efficient boilers as well. And we have some natural draft at some of our sites. We do have chillers on a lot of our sites too, that we maintain through our maintenance contracts.”
Wright says he enjoys the challenge of designing a hydronics system, as well as learning about and working with new technology. “There are lots of projects I’ve been trying to get into.
I mean, you’re seeing a lot more starting to include heat reclamation, heat exchangers to extract even more heat from the flue gasses, and the associated equipment. There are also the CHP (combined heat and power) systems that are coming over from Europe. Every unit is different in its own way. So, when it comes to troubleshooting a system and trying to figure
out where the problem lies, it can be a bit more of a challenge, depending on what you’re working on.”
The variety of projects Canada West undertakes is also a highlight for Wright. One memorable project involved a chiller retrofit in Banff that required equipment to be flown in and out by helicopter. Another involved constructing an intermittent chiller system for an IT company for computer ECMs and applied large environmental test chambers. Wright says the entire system was built on a truck that the IT company could move from facility to facility. “That one took about five months, but it was good. It was a lot of extra planning, but it was definitely a cool one.”
Wright is currently completing his apprenticeship in refrigeration and air conditioning, as well as a hydronics design and installation program. “I think education is your best tool to have in the trade, so my main goal is just to stay focused on school. I know it’s hard to take two months every year to go to school, but I keep doing it and keep growing myself professionally. And the owners here are extremely supportive of everyone’s education and any special courses. They encourage us to advance ourselves as far as we can.”
By Carolyn Cooper
Favourite part of the job: The sense of accomplishment after completing a challenging troubleshoot, repair, or project
Your favourite tool in your toolbox: Combustion analyzer
Tool that you wish you had: Thermal imaging
The most useful tool in your toolbox: Multi-meter
If you were granted one wish: To eliminate disease and chronic illness from the world
Favourite band/performer: Warren Zeiders
Best concert you ever attended: Country Thunder Music Festival
Favourite book: Harry Potter
Favourite movie: Hacksaw Ridge
Favourite TV show: Criminal Minds
Favourite sport: Hockey
Favourite vehicle of all time: 2006 Chevrolet Silverado 2500HD LBZ Duramax
In the mechanical industry since: 2018
Schools and programs: Foothills Composite High School, June 2018; SAIT, Red Seal Plumber & Red Seal Gasfitter May 2023, and Refrigeration & Air Conditioning Mechanic, in progress; NAIT, Hydronics Design and Installation Technician, in progress
Favourite teacher: Fred Bretzke
Favourite class: Heating theory
Best advice you’ve ever received: Mistakes happen. It’s how you learn from those mistakes that determines success
Advice for young people considering entering the trades: Connect with people in the fields you’re interested in. You’d be surprised at how many are willing to offer help and share valuable insights
The current work ride: 2021 GMC Savana
Service area: Calgary and Southern Alberta
Favourite season: Fall
Favourite restaurant or local lunch hang out: Yume Sushi
Favourite food: Prime rib
Favourite snack: Corn nuts
Favourite outdoor activity: Hunting
Favourite place to be: Kananaskis Country
Hobbies: Camping, ATVs, hunting, fishing
Favourite website: Reddit
Biggest pet peeves: Micromanaging
One word or phrase that describes you: Motivated
By Todd Wiggins HYDRAULIC
Water flows all around us − through pipes, heating and cooling systems, and even in the air we breathe. Yet it also follows a complex balance of pressure that controls its movement. Hydraulic separation is key to maintain this balance in hydronic systems, ensuring smooth and efficient water flow in a closed-loop hydronic system to ensure optimal performance and comfort.
To start, we require a basic understanding of how a hydronic system works. A hydronic system is a heating or cooling system that uses circulation of a fluid, typically water, to transfer thermal energy. Hydraulic separation plays an important role, because it balances the flow between different pipes.
Todd Wiggins works in outside sales business solutions − hydronics with The Master Group in Calgary, AB. Wiggins is residential radiant hydronics design (RRHD) certified. He can be reached at twiggins@master.ca.
Primary piping refers to the loop that manages everything on the boiler side. Secondary piping, or distribution piping, handles the system side, including system circulators or zoning devices such as zone valves. By separating the primary and secondary piping, hydraulic separation is achieved. This separation allows the system to operate efficiently with no interference between the primary and secondary circuits.
With a basic understanding of hydraulic separation. let’s discuss why it’s important for retrofit applications. Both the closely spaced tees and hydraulic separator methods are suitable to decouple the primary/secondary circuits. The optimal choice would vary depending on certain job requirements.
Older systems were typically designed with a single pump to manage the system’s full load, and the flow required through the boiler. New condensing boilers have specific flow requirements recommended by the manufacturer, and so changes to the existing pump may need to be made. Hydraulic separation is especially crucial for a retrofit project so that the new primary circuit can operate with no interference from the existing secondary circuit.
Effective hydraulic separation is crucial for hydronic heating system retrofits.
Closely spaced tees are a standard method used in residential hydronic heating systems. When using this method, it’s important to ensure the tees are spaced four pipe diameters apart. For example, if you’re using a pipe with a one-inch diameter, the centre-to-centre spacing between the tees should be four inches. If you space them further apart than the recommended four inches, you’ll encounter
Hydraulic separator with coalescing mesh helps eliminate air and debris from the system piping.
Models Range From 299 to 500 MBH
Models Range From 1,250 to 4,000 MBH
Whatever your needs may be, you can trust that you’re installing a product that is produced to the highest standards. Both models offer our Peace of Mind Warranty Program. Choose Triangle Tube for efficient and reliable solutions for your heating and hot water needs.
SCAN TO LEARN MORE
issues with what is commonly known as “ghost flow.” The result of this excess spacing is unwanted flow in the secondary loop.
If done properly this method of hydraulic separation ensures proper design flow in the primary loop. If the system is installed correctly, the pressure drop across the tees is negligible, which prevents water from entering the secondary loop until needed.
Another method of achieving hydraulic separation is also the one that I consider most effective. This method utilizes a hydraulic separator, a device designed to keep hydronic heating systems running smoothly. The beauty of hydraulic separators lies in their simplicity; they are easy to install, with supply flow entering at the top and return flow exiting at the bottom.
From an installation perspective, hydraulic separators are often the preferred method since they drastically reduce time and labour. Simple installation also eliminates the risk of installation errors you might experience when using closely spaced tees.
Further understanding of hydraulic separators requires a more technical deep dive. Positioned in a specific spot within the system, the hydraulic separator serves as a low-pressure zone with a nearly zero pressure drop, effectively decoupling the primary and secondary circuits. This design allows each loop and circulator to operate independently without interference.
In many systems, the secondary piping will have multiple circulators. Using a hydraulic separator ensures that each system circulator performs at its designed duty point.
A misconception about sizing a hydraulic separator is that it should be sized based on the pipe size it connects to. But the truth is it should be sized based on flow. For example, when reviewing product submittals, you’ll notice that a two-inch union connection will have a different flow rate than a twoinch flanged connection. This is something to be mindful of when selecting a hydraulic separator.
Hydraulic separator with coalescing mesh helps eliminate air and debris from the system piping.
Figure 1 The difference in gallons per minute between each separator, specifically the two-inch models
Hydraulic separators not only ensure proper flow but also provide efficient air and dirt separation. A coalescing mesh helps remove unwanted air and dirt from the system inside the separator’s body. Many manufacturers now offer hydraulic separators with magnetic dirt separators to capture metallic debris in the return piping. It’s a common recommendation to use magnetic separators for retrofit applications. This provides critical protection for your boiler’s heat exchanger and the rotors in ECM pumps, which will help with the overall system efficiency.
To continue learning and deepen your understanding of hydraulic separation, there are some excellent resources available. For example, I frequently rely on webinars such as Taco Tuesday by Taco and Coffee with Caleffi by Caleffi, which are great tools to enhance knowledge.
» Dual fuel capable with a compact design
» Offers up to 99% ef ciency, exceeding minimum energy performance standards
» TurboFer® retube technology for optimal heat transfer
» Standard less than 20 ppm NOx, sub 7 ppm NOx available
» Available in 11 models from 500 to 6,000 MBH
ClearFire®-CE: Up to 99% Efficient, 100% Condensing Hydronic Boiler
» Enhances heat pump performance during extreme temperatures
» Reduces downtime during power shortages
» Provides fuel exibility during peak fuel demands
By Chad Edmondson BOILERS
The following installation “dos and don’ts” will impact the longevity of a boiler system.
DO use the onboard control system that most manufacturers now include with their boilers. No one, not even the controls contractor, understands how to stage, modulate or optimize boilers as well as the manufacturer. These days, onboard boiler controls can control On/Off operation, modulation and sequencing, primary boiler pump speed, and even outdoor temperature reset.
Remember, boiler control can still be integrated into the Building Management System (BMS) for remote monitoring and communicating alarms, however operational control conforms to manufacturer protocol for both condensing and non-condensing boilers and primary pumps.
Residential gas boiler installation
DON’T power the primary boiler pump(s) through the boiler(s) if the required pump motor amperage exceeds the amperage rating of the associated boiler pump motor relay. This will cause you to blow a fuse in the boiler and the pump will lose power. The best way to avoid this common scenario is to add an external contact to provide electricity to the pump.
Emergency stop is usually placed inside the boiler room.
breaker will immediately shut off the fuel or energy supply. Make sure to consult local codes to see if they have additional requirements.
DON’T use venting material that was installed for existing non-condensing boilers for newly installed condensing boilers. Condensing boilers require either Category II or IV vent, depending on whether the draft is natural or pressurized. The sizing of the vent may also be different for a condensing boiler.
DO consult local jurisdiction requirements for emergency stop wiring to determine how many and where emergency stop devices should be installed. Many jurisdictions require ASME CSD-1 controls and safety devices for automatically fired boilers, in particular, an emergency boiler “STOP” switch at every entrance to the boiler room. This emergency stop is
usually placed inside the boiler room so that in the event of any emergency you can hit it on your way out of the room, thus disabling the equipment. Activation of the remote shutdown switch or circuit
DO consult with a venting expert to specify an engineered vent system for gas-fired boilers.
DON’T expose boiler pumps to magnetite (the sludge that leaches from piping and equipment) when using pumps with electrically commutated motors (ECM), which use a magnet to make the impeller spin instead of the shaft. The magnet attracts this metallic material, causing it to build up inside the pump leading to premature failure.
DO pipe condensate to a neutralization kit to raise the pH before it is discharged into a drain. The condensate should be able to drain by gravity from the boiler through the condensate trap and finally the neutralization kit before going down the drain. Make sure the boiler is installed at a higher elevation to permit this drainage, otherwise, you will need to install a small condensate pump to facilitate drainage.
Always install a neutralizer kit to prevent boiler condensate from damaging drainage piping.
DO install a magnetic filter to protect ECM pumps that use a magnet to attach the impeller.
DON’T overlook local codes or assume one jurisdiction has the same requirements as the last project you designed. Local jurisdictions vary in terms of required boiler clearances, gas venting, safety measures, and more.
DON’T discharge condensate from a condensing boiler directly into a drain. This condensate is highly corrosive to pipes and equipment due to its low pH and must be neutralized before disposal.
A magnetic filter should be used to avoid magnetite build-up.
DO remember that it is much easier to meet code requirements during installation, rather than “fixing” code violations after the installation is complete.
Chad Edmondson is vice president of business development at JMP Equipment Company (jmpcoblog.com/series). He can be reached by email at ChadE@jmpco.com.
10) Heating curve H) Another name for a reset line
A) Industry standard mounting rail for relays and other modular controls
B) Measures the pressure difference between two points in a piping system
C) Describes the IBR net output rating of a boiler
D) Used to coat PEX tubing to reduce oxygen diffusion through tubing walls
E) Designed for component isolation purposes
F) Control algorithm in which the length of the on-cycle varies based on the error between the target value and the measured value of the controlled variable
G) Has an inlet connection perpendicular to the plane of its impeller
H) Another name for a reset line
I) The pressure differential at which differential bypass valves begin to open
J) Tapered threads on the outside diameter of pipes or fittings
Match the terminology you hear in the field to the correct definition or function by March 14, 2025 and enter for your chance to win a $150 Visa gift card. This contest is open to Mechanical Business subscribers in Canada. Send your answers to kerry.turner@mechanicalbusiness.com or enter online at mechanicalbusiness.com. Thank you for participating!
K) Undesirable operating condition in which a circulator is running, but flow through it is blocked