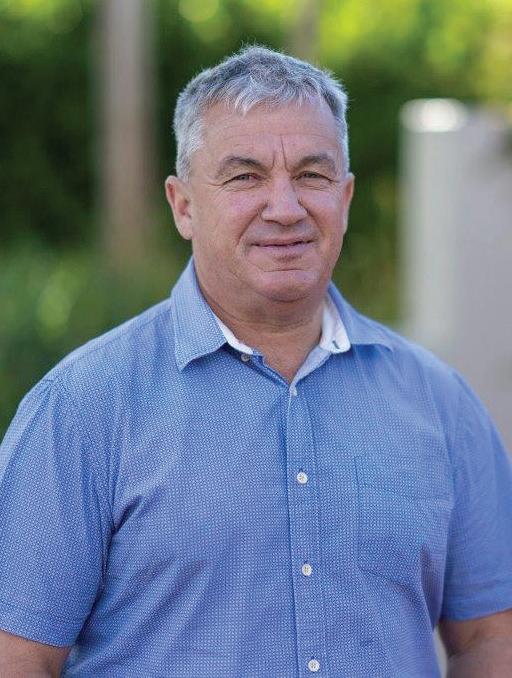
7 minute read
Regulated stewardship coming soon for synthetic refrigerant industry
By Jason Richards – National Programme Manager -
Synthetic greenhouse gases, such as synthetic refrigerants (sometimes called F-gases), are used in everything from vehicle air conditioning to heat pumps, supermarket and corner store fridges, and industrial-scale cooling and freezing.
Advertisement
While they only account for 2% of New Zealand’s emissions their potency means, globally, properly managing them is one of the most effective ways to tackle climate change.
In July 2020 Government declared synthetic refrigerant gases, and the equipment that contains them, from consumer equipment like heat pumps and car air conditioning units to retail and industrial refrigeration systems, as a priority product. This means a regulated product stewardship scheme will have to be established, encompassing all of industry to manage the gases.
Product stewardship manages the collection of products at the end of life so they can be reused, recycled or properly disposed of. In the case of synthetic refrigerants, proper disposal through high-heat incineration is currently the best pathway.
SF6 is included
Also included in the stewardship will be SF6 (sulphur hexafluoride) gas, which is found in equipment used to distribute electricity. It is the most potent greenhouse gas known to man, being over 20,000 time more effective than carbon dioxide at trapping heat.
What is the current situation?
New Zealand has had a voluntary stewardship scheme for synthetic refrigerants since 1993 operated by The Trust for the Destruction of Synthetic Refrigerants (RECOVERY). Between then and October 2022 it has prevented 1,236,000 tonnes of CO2eq greenhouse gas emissions, in addition to 36,000 tonnes of avoided ozone depletion to our atmosphere.
Following a scheme design phase, which was facilitated by 3R Group, the Trust has applied to Government to be the product stewardship organisation (PSO) for a regulated stewardship scheme.
RECOVERY, now known as Cool-Safe continues to be managed by the Trust and operates the country’s only voluntary scheme for synthetic refrigerants. It works with industry to collect and properly destroy the gases, as well as works with industry to promote installation, maintenance and decommissioning aligned to industry best practice to avoid leaks.
The Trust and Cool-Safe’s Chief Executive Janine Brinsdon says they’re on a mission to inspire, support and reward the refrigerants industry for protecting the atmosphere from the harm of released refrigerants:
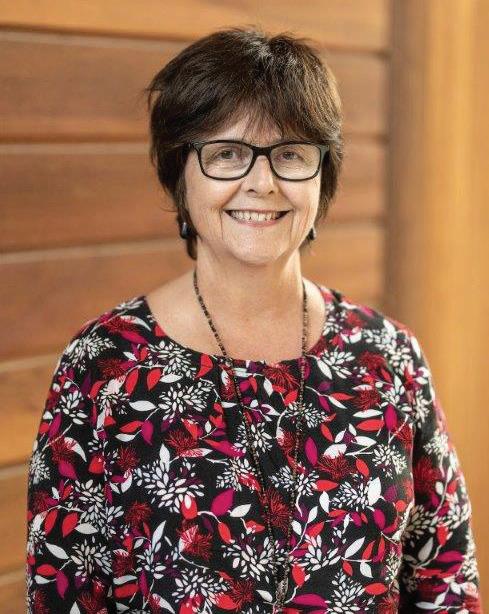
“Refrigerants play a really important role in our day-to-day lives, along with making a huge contribution to our economy both directly and indirectly.
Our first priority is to make sure we are all doing all we can to protect the environment from the synthetic refrigerant harm, while also recognising the innovation and new technology industry has already adopted with the switch to lower GWP refrigerant, and rewarding those organisations and technicians who are doing the right thing.
It’s a win-win for both the environment and the valuable role refrigerants play in our communities.”
In October 2022 Cool-Safe launched a Buy-Back Programme for synthetic refrigerants and is developing and streamlining the recovery process for technicians across our network of collection sites. The Trust is also in the process of leading the development of a multi-million-dollar, state-of-art destruction facility in the Bay of Plenty, so the gases can be dealt with onshore. This facility will use plasma arc technology to break the gases down on a molecular level. Any toxins are neutralised and the resulting by-product can be safely disposed of in landfill.
The facility, which should be operational by 2024, is key to creating an onshore solution and will mean collected gases don’t need to be shipped overseas to be destroyed – lowering the scheme’s operating emissions.
Why regulated stewardship?
While voluntary product stewardship has been effective at keeping some synthetic refrigerants from the atmosphere it’s limited by data, resources and free riders who don’t contribute but whose products are still stewarded.
Regulated stewardship creates a level playing field, the scheme is better resourced, and data is greatly improved. Well designed and run regulated schemes are almost always more effective.
Will this affect me?
If your business or organisation uses refrigeration, imports the gases, or imports or manufactures the equipment they go in, then you will be affected. Regulated stewardship requires everyone from importers to retailers to be part of the scheme and contribute to the collection and safe destruction of the synthetic refrigerants.
Users of the gases and equipment will need to make sure they are dealing with registered scheme participants or certified technicians. The scheme will also be heavily focused on ensuring industry best practice is followed when installing, maintaining, and decommissioning machinery which uses synthetic refrigerants.
Cool-Safe will award accreditation to those handling synthetic refrigerants who can demonstrate they are compliant with best practice.
Refrigerant technicians will also be able to apply for Cool-Safe certification after completing industry-recognised training and quality-control assessments. The overall aim is to create a consistent and high standard which will keep refrigerants from leaking and adding to climate change.
When will this happen?
According to Cool-Safe it expects that by 2024 the recovery and disposal of synthetic refrigerants will be controlled, with a government-accredited, regulated scheme in place. This regulated scheme will be run by a PSO for the priority product, which the Trust for the Destruction of Synthetic Refrigerants is currently working to become.
If you are in doubt about how you fit into this picture, I encourage you to visit the Cool-Safe website and make contact. www.coolsafe.org.nz
3R accelerate the circular economy through the design, implementation and management of product stewardship schemes and other sustainability services. They facilitated the design of the scheme for synthetic refrigerants and supported RECOVERY in their accreditation application. Find out more at www.3r.co.nz
Article: Part one
Circular economy: so much more than recycling!
Dr Barbara Nebel, CEO thinkstep-anz
The circle has been an important symbol since early times. To many ancient Eastern and Western civilisations, it represented unity, balance and stability. Fast forward to 2023 and the circle is the most talked about shape in sustainability. Why? Because it’s time to get serious about the circular economy and the business, environmental and social benefits it offers.
What is ‘circular economy’?
Circular economy (CE) is an economic system that can help your manufacturing business reduce risks and costs, become more resilient and build your brand. It can also help you identify new income streams.
CE decouples using resources from economic growth. It recognises that the ‘linear’ economic system we use to produce and consume goods and services –‘take-make-dispose’ – cannot go on forever.
As manufacturers, you know that the resources you use are finite (‘take’). You may be facing shortages or skyrocketing prices, particularly with critical materials like lithium. Many of you will be looking for a more sustainable way to manufacture your product (‘make’). You may be concerned about what happens when consumers dispose of your product (‘dispose’). Are you contributing to landfilled waste?
Could you be liable?
Enter circular economy and solutions to these problems.
Circular economy is based on three principles
Principle 1: keep products and materials in use
Circulating products and materials means keeping them in use at their highest value. It avoids the costs of extracting and creating materials, and of disposing of waste.

A circular product is one that consumers can use for as long as possible (e.g. it is easy to repair). When the product wears out, its parts can be reused, or the product remanufactured (remade). At the end of the product’s life, its raw materials can be fully recycled.
Principle 2: design out waste and pollution
CE sees waste as a design flaw that causes us to use more resources than we need. Overusing resources results in volatile prices, shortages, and ecological damage. By designing out waste, CE lets businesses create value without using up finite resources.
Principle 3: regenerate natural systems
A circular economy supports natural processes and lets nature flourish. CE encourages regenerative systems as well as economic gains. Positive side effects include regenerating soil, well-managed water resources and thriving biodiversity.
Circular manufacturing processes (and why recycling is the last resort)
There are several circular manufacturing processes. They involve making products from material that is safe, renewable, and already in use, and designing them to be shared, repaired, reused, and recycled. Every circular manufacturing process achieves one or more of the three principles above. However, some are more circular than others.
Highly circular: sharing products, ‘building to last’, reusing products
• Sharing. The ‘sharing economy’ (one product, many users) is ‘gold star’ CE. It moves economies from ‘owning’ products to ‘accessing’ the services those products provide. For a business, sharing achieves the same economic outcomes with fewer resources and generates many streams of income. Examples include car-sharing schemes.
• Building to last and repairing. Blunt™ Umbrellas designs its product to withstand extreme weather. The company offers replacement parts for simple fixes plus repair centres across New Zealand. This strategy helps Blunt build a premium product and continue to engage with its customers over time.
• Reusing. Medsalv collects medical devices that health providers would otherwise discard after one use. It cleans, inspects, and repackages them and sells them back to hospitals. This strategy helps Medsalv reduce the cost of its materials and keeps high-value materials in use. (In practice, reuse involves some ‘losses’ from the circular system. For example, some medical devices will be damaged before Medsalv can reuse them. This makes ‘reusing’ a little less circular than ‘building to last’.)
Moderately circular: remanufacturing products and materials
• Remanufacturing. AB Industries remanufactures, repairs, and maintains mechanical equipment like diesel engines and compressors. This strategy helps the company keep high-value components in use without incurring the full costs of manufacturing.
Slightly circular: recycling products and materials
Yes, recycling features low on the list. This is because a recycled product is much less valuable than the original product. The value of intangible assets like a product’s branding and warranties is often far greater than the value recovered from recycling materials. (Think of the effort that goes into building your product’s brand!) Remanufacture your product and you retain much of this value.
Recycling begins at a product’s end-of-life. CE focuses on the beginning of life: it prevents waste from being created in the first place. About 80% of the environmental impact of a product is locked in when it is designed. Creating circular products involves changing the way we choose materials and design, produce, and distribute products.
Recycling still matters: it lets us reuse materials. Product stewardship goes further: it makes manufacturers, importers, and retailers responsible for what happens with products, rather than the products’ users. Tyrewise is New Zealand’s first regulated product stewardship scheme for recycling tyres. It will keep used tyres away from landfill and reduce stockpiling and illegal dumping. In next month’s issue, we’ll look more closely at the business benefits of CE and show you how to get started.
www.thinkstep-anz.com