
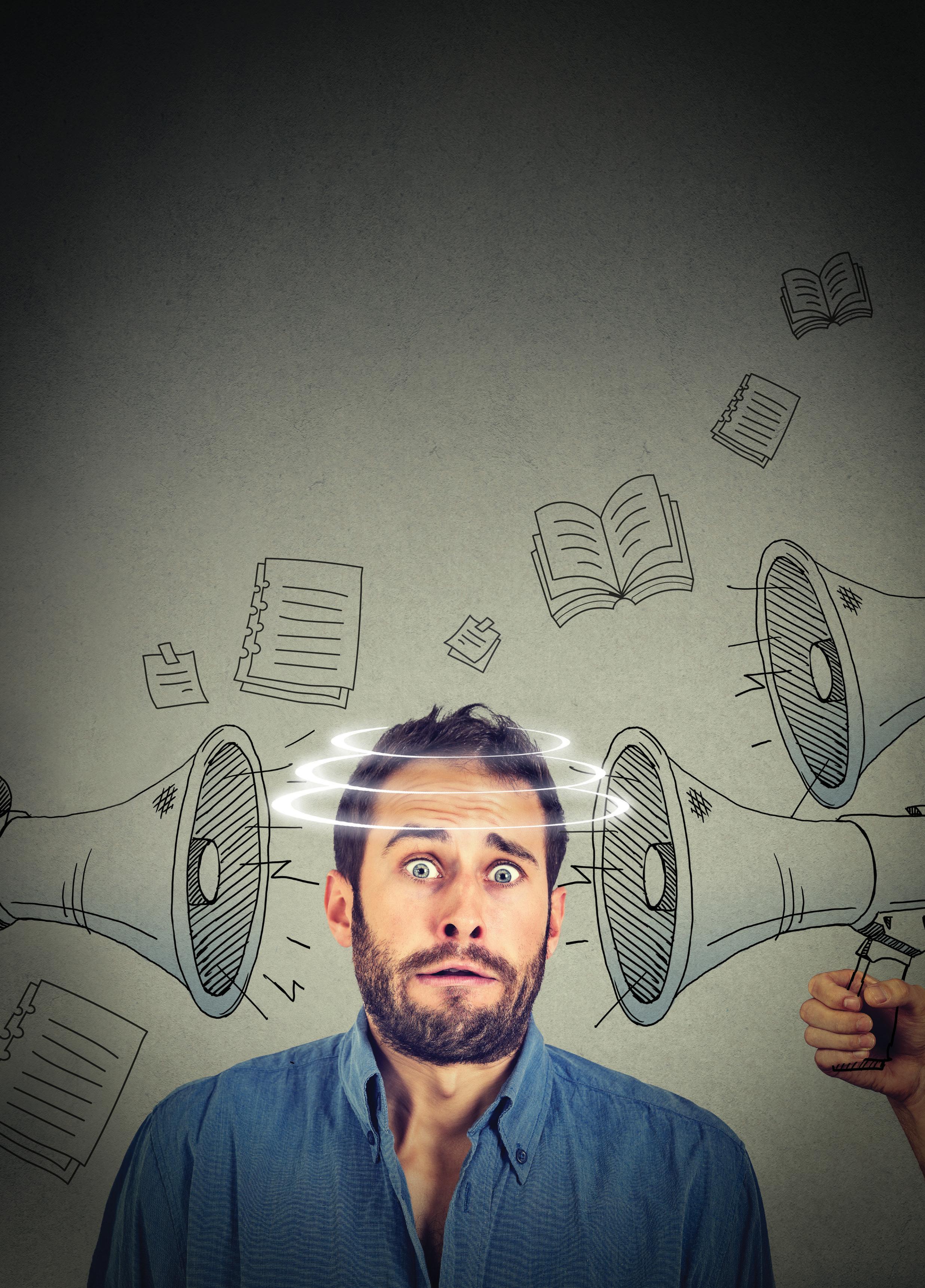
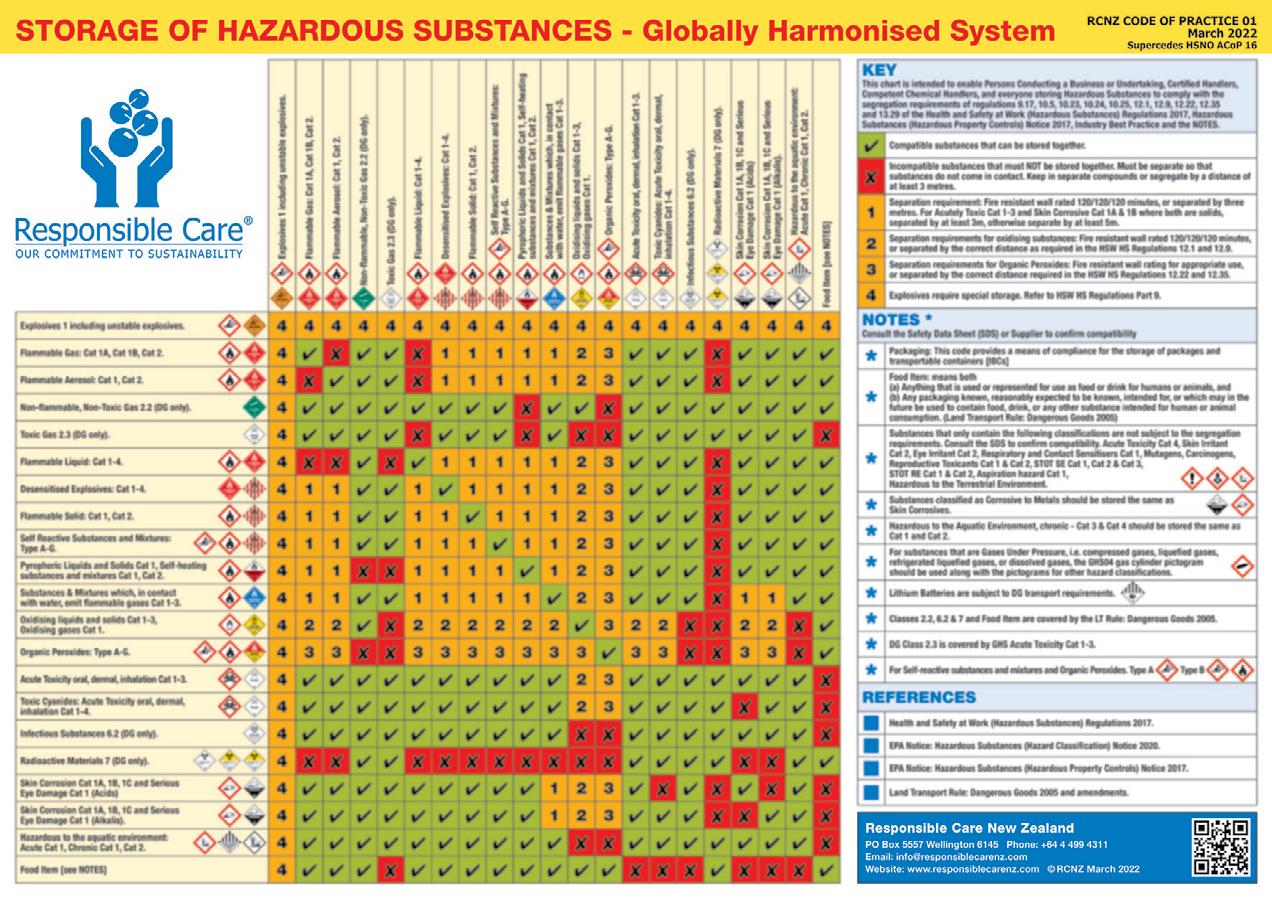
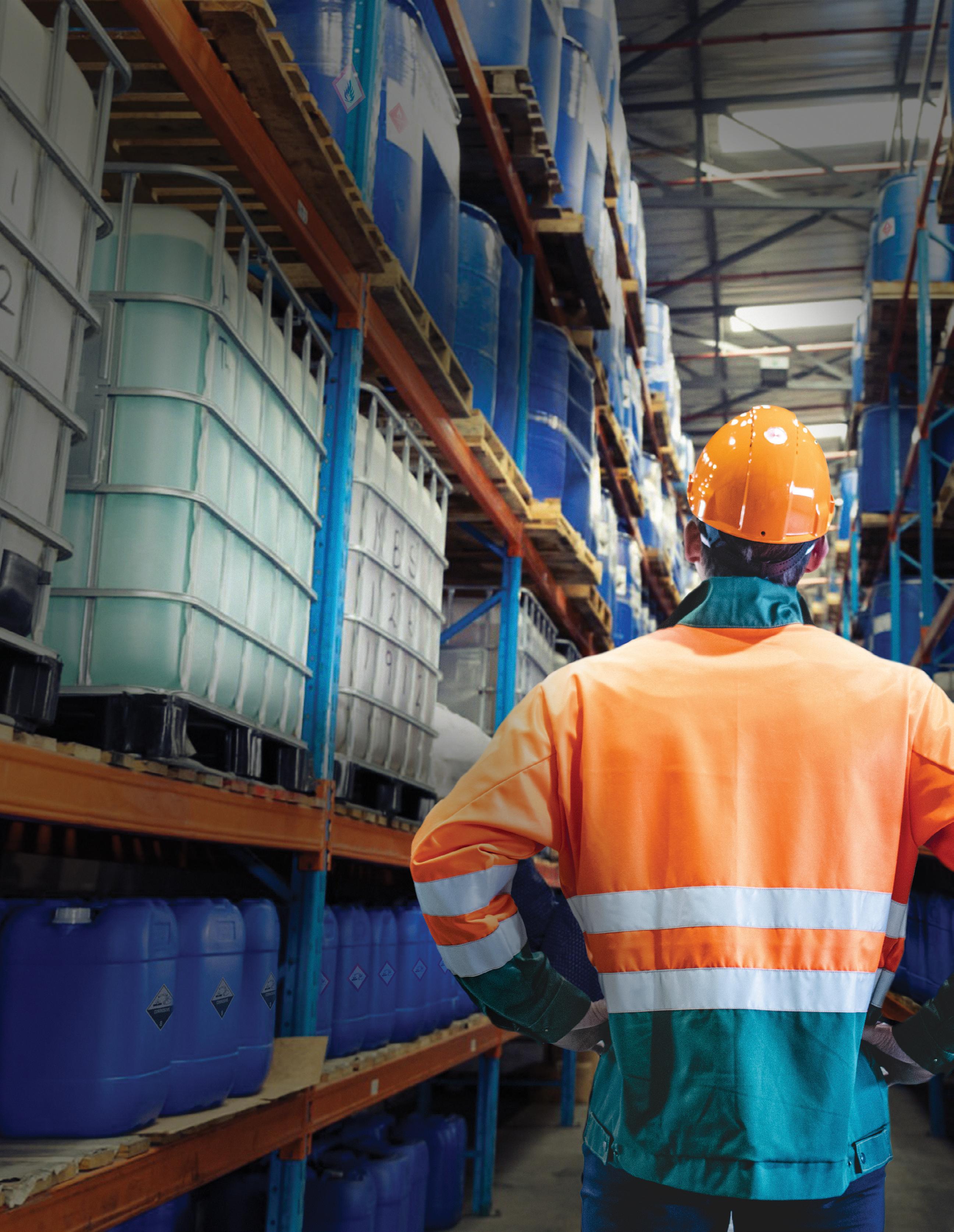


New Zealand’s former chemical management regime included a popular key resource which enabled business operators to readily demonstrate compliance, without unnecessary cost and inconvenience.
Developed by the NZ Chemical Association using the same robust process for ISO Standards, Approved HSNO Codes of Practice:
• Identified the performance requirement;
• Explained the preferred solution;
• Standardised training, compliance assessments and enforcement, transcending Government ‘silos’;
• Provided accurate, low-cost best industry practice advice;
• Surpassed mere compliance by enabling superior, allencompassing best practice.
Simplifying prescriptive, complex and inflexible regulations, industry codes are pragmatic,
user-friendly, inexpensive and most importantly, easily updated to enable desired outcomes. They deliver accurate advice – first time, every time.
HSNO Codes were abandoned without discussion in favour of diluted and often confusing ‘guidance’ material, often requiring expensive consultants and relying on selfappointed advisors replacing former knowledgeable workplace inspectors.
For example, the widely used RCNZ
GHS Segregation Code provides ‘at a glance’ answers, replacing hundreds of pages of regulatory material.
Restoring Government approved industry codes eases pressure on risk-averse regulators and their resource-poor target audiences by explaining standardised best industry practice in ‘plain language’ guidance material, thereby sharing responsibility for safely managing chemicals throughout the product life cycle.
University of Auckland researchers say New Zealand’s Emissions Trading Scheme (ETS) is being let down by five critical sectors.
The scheme, which is designed to cut emissions and encourage economic growth, could have a much greater impact on the country’s emissions reduction goals, say the researchers.
Their study shows that five key sectors—agriculture, transport, energy, petroleum and diesel, and waste—are underperforming.
While the ETS effectively reduces emissions on a broad scale, the researchers: Dr Le Wen, Associate Professor Stephen Poletti, Dr Selena Sheng and Simon Tao, say it’s failing to spur economic expansion and curtail emissions simultaneously.
In their paper, Enhancing New Zealand’s emissions trading scheme: A comprehensive sector-level assessment for a stronger regulatory framework , the authors explored the emission reduction potential of the ETS by sector.
Compared to emission trading schemes utilised in China and the EU, which have received extensive academic attention, the researchers say relevant analyses regarding the NZ ETS is scant.
“We wanted to understand where the scheme’s effectiveness comes from and where it’s lacking,” says lead researcher, Business School PhD candidate Simon Tao.
“We show that the ETS could better stimulate the economy and reduce greenhouse gas emissions if the planning authorities focus on those five key sectors.”
The study points out that
The impact of New Zealand’s main tool to reduce emissions could be improved if five sectors were better regulated, according to a new study
the energy, waste and agriculture sectors are key to New Zealand’s economy and major sources of emissions.
Because cutting investments in these areas to reduce emissions could slow economic growth, Tao says the Government should look at ways to lower emissions while encouraging growth through investing in innovation and energy alternatives like hydrogen.
Meanwhile, the authors say the agricultural sector’s greenhouse gas emissions rank first among all in-
dustries’ emissions. At the same time, they say practical, impactful solutions to curtail emissions from this sector haven’t been available.
“There’s an assumption that market participants will comply with their emission reduction commitments, but that’s a hard task when no substantial initiatives are available,” says senior research fellow Dr Selena Sheng.
“One option may be to instate a fixed carbon price ceiling. We also argue that regulators can impose tax
on those sectors in the agricultural industry where emissions exceed the average.”
The researchers say the Government could also focus on creating a dedicated agriculture-focused technology hub. This, says Sheng, could help promote the adoption of innovative mitigation technologies and practices among farmers, fostering progressive and sustainable changes.
No-one was more excited at the prospect than the Chemical industry. Relieving New Zealanders of expensive and complex regulations (causing widespread frustration over the absence of any tangible benefit from highly prescriptive regulations) would indeed be welcome.
Regulation Minister David Seymour notes New Zealand is overregulated and has too many departments making regulations of poor quality. The fledgling Ministry for Regulation (MFR) was established with $16m and almost 90 staff, inherited from the disestablished Productivity Commission.
Critics were quick to highlight a generous budget, an expensive communications team and speculate about the Ministry’s ability to analyse and improve complex regulatory performance standards, often involving multiple government agencies.
A Regulatory Standards Bill requiring a comprehensive cost benefit analysis of new regulations will wend its laborious way through the legislative process.
Meanwhile, there are many opportunities to accelerate achieving the desired efficiencies in productivity without jeopardising workers’ health and safety or incurring additional expense.
No more fixing something that isn’t broken
The first priority for the chemical industry would be a return to approved industry codes of practice (ACoP).
A robust development process reflecting A/NZ
A highlight for business operators scrutinising the otherwise largely bare cupboard of the May budget was the intention to reduce red tape while improving the quality of outcomes.
Standards requirements and the New Zealand chemical industry association’s user-friendly HSNO Approved Codes provided the optimum solution. It encapsulated international best practice, delivered through credible training, enabling compliance and simplifying enforcement.
There was no explanation
as to why industry codes did not survive the creation of WorkSafe NZ. The incomplete transition from HSNO legislation to the HSWA Act and the complex, often irrational HSW (Hazardous Substances) Regulations frustrate compliance. Abandoning the sensible but inconsistently delivered HSNO Approved Handler requirements
qualification while retaining a few exceptions for niche chemical handling roles, has deprived more than half a million SMEs of a useful, in-house chemical safety adviser.
Our association has consistently opposed the present approach to regulating industry, namely: • Decide without consultation there is a problem;
• Issue a ‘consultation’ document remarkedly like a draft regulation reflecting the
resources to enable implementation; and
• Include industry in developing user-
present mix of unyielding, prescriptive compliance requirements, variable interpretation and too often
associations helps establish and confirm safe workplace practices, enabling regulators to effectively
The first priority for the chemical industry would be a return to approved industry codes of practice .
their value in sustaining and
inexplicable loss of industry Approved Codes of Practice and the Approved Handler concept.
immediate relief.
Effective options to rapidly enhance workplace and consumer chemical health
There was no explanation as to why industry codes did not survive the creation of WorkSafe NZ.
Industry covers the bases while regulators have other priorities
Fortunately, the chemical industry’s customised Competent Chemical Handler courses not only ensure workers can safely use workplace chemicals, but also provide employers with in-house, basic workplace chemical safety advice.
Whilst regulators grapple with many pressing concerns, chemical safety is not a priority for WorkSafe NZ - all the more reason for key regulatory agencies to harness the expertise and support available by collaborating with the
and safety include taking advantage of industry expertise and recognising the value of proven and inexpensive industry developed ‘compliance tools’. Reinstating enforceable, low-cost industry approved codes to enable and support training, compliance and enforcement costs Government nothing.
The absence of workplace chemical safety in the new WorkSafe NZ priorities for the next two years is an unintended boost for easy solutions provided by industry codes.
A rapid return to robust, approved industry
Dismantling the silo approach by working collaboratively with proactive industry associations
chemical association in joint endeavours. The common aim is to protect people and our environment from the mis-use and mismanagement of chemicals. Responding to business lobby groups, the Government is opting for the massive task of reviewing the Health and Safety at Work Act 2015. Meanwhile, simply dismantling the traditional Government agency ‘silo approach’ by working collaboratively with proactive industry associations provides
solutions.
When it comes to audience appeal, “Slashing red tape” will always guarantee media attention, however solutions are harder to find.
Stakeholders will all
benefit from proven industry expertise, resources and support –bringing rapid relief to the backbone of New Zealand – the 545,000 small and medium enterprises.
Barry Dyer Chief Executive Responsible Care NZ
compliance tools implemented by competent workers will quickly overcome concerns about inadequate performance, ease pressure on resources of risk-averse government agencies and increase respect for proactive participants and their achievements.
The good news? We need not wait for chemical safety to feature on legislative priority lists, avoid the new regulation queue, or bleat about diminishing resources. Benefit from proven industry compliance
Care is a global voluntary chemical industry initiative developed autonomously by the chemical industry for the chemical industry.
Chemical suppliers continue to help customers achieve workplace chemical safety aspirations through product stewardship initiatives.
To help solve the in-house chemical compliance dilemma in New Zealand, Responsible Care NZ delivers specialist and cost-effective Certified Handler standard training, complete with a certificate.
Responsible Care NZ site compliance assessments are non-threatening, effectively capturing and assessing chemical safety performance in a variety of workplaces.
+64 4 499 4311
info@responsiblecarenz.com www.responsiblecarenz.com
This indispensable selection includes a handy compliance checklist poster together with the Safe Storage Code displaying the essential user-friendly information you, your
Together with our customised Approved Handler Training this valuable set of international pictograms and labels plus a useful checklist enables you and your team to comply with workplace chemical safety responsibilities.
Brett Murray
Site Safe is offering up to 24 scholarships to the health and safety leaders of tomorrow. Their Health and Safety in Construction programme has been growing year on year and is for anyone keen to achieve their goals of higher-level learning.
Successful participants will be awarded with an NZQArecognised New Zealand Certificate in Workplace Health and Safety Practice (Level 3).
Site Safe Chief Executive, Brett Murray, says the scholarships are a great opportunity for aspiring health and safety leaders to gain valuable skills and qualifications.
“We are proud to support the next generation of health and safety champions who want to make a positive difference in their workplaces and communities. The scholarships are a way of recognising the diversity and talent within the construction sector and encouraging more people to pursue a career in health and safety."
Site Safe’s scholarships are open to anyone who works in the construction industry, regardless of their role, experience, or background and aim to support diversity in the industry. Applicants can apply for one of six categories: Māori, Pasifika, Under 25, Women in Construction, Accessibility,
This
initiative is part of Site Safe’s dedication to supporting the construction industry’s next generation of aspiring health and safety leaders.
and Open (to anyone).
Each recipient receives regular, ongoing support
providing continued guidance throughout their learning journeys. Over the
from Site Safe as they go through the programme. A dedicated team of experts assists students each step of the way, planning their course pathways and
years, Site Safe has seen successful graduates of the Health and Safety in Construction programme and go on to become industry leaders in health
and safety.
Graduates frequently tell Site Safe that the programme boosts their confidence and helps them apply new safety skills on site. Feedback also shows that learning in the classroom with peers from the construction industry allows for valuable discussions.
To acknowledge their achievements, successful scholarship recipients are invited to Site Safe’s flagship event, the Evening of Celebration in Auckland in March 2025 to receive their scholarship award and connect with those already established in the health and safety industry.
Scholarship applications now open
Scholarship Categories
• Māori
• Pasifika
• Under 25
• Women in Construction
• Accessibility (any age, gender or ethnicity)
• Open (any age, gender or ethnicity)
For more information on the Health and Safety in Construction programme, or to enrol, contact us on 0800 SITE SAFE, email programme@sitesafe.org.nz or visit our website sitesafe.org.nz.
We have learned a lot from Cyclone Gabrielle, and developed good policies and guidelines as a result, but some aspects of the Building Act still need to change to put them into practice, says University of
Auckland Associate Professor Martin Brook
One year on from the devastating Auckland Anniversary storm and Cyclone Gabrielle, many stories of misery and financial disasters have emerged. It’s important to reflect on the impact of those events on individuals and communities, but also on what knowledge has emerged over the last year, what we have learned from recent history, and what scientific advances have
been made.
It has been reported that the early 2023 storm events caused more than 140,000 landslides, and possibly as many as 800,000 landslides, and though a large portion of these landslides were in unpopulated hill country, many landslides were in populated suburbs in cities and townships. In addition, flooding from the storms inundated areas of Auckland and parts of the eastern North Island.
If there is a silver lining to those devastating events, we have learned a lot and there have been several important responses to these storms over the last year.
First, while immensely damaging to people, communities and the economy, the massive amount of landslides across such large areas has provided an unprecedented opportunity to analyse landslides, from several
standpoints, including: the mechanisms of how the slope failed; locational factors such as slope angle; and the amount and rates of local rainfall and the soil or rock properties of where the landslides occurred. This research has been undertaken by the universities and crown research institutes, such as GNS Science. This is using new satellite data and laser scans of the land surface, which can determine
volumes of displaced material, from comparing “before” and “after” digital elevation models. In some areas of the eastern North Island, such as Esk Valley, more than 150 landslides per square kilometre have been identified. That is an extremely high density of landsliding, which led to substantial soil erosion. In theory, all of this landslide and erosion research conducted over the last year should be used to improve hazard zoning and setback distances in future.
Second, central government passed into law the Severe Weather Emergency Legislation Act on March 20, 2023 and the Severe Weather Emergency Recovery Legislation Act on April 12. These changes modified the existing Resource Management Act and provided more flexibility for councils to assist affected communities to recover.
Third, local government, via subcontracting teams of experienced geotechnical engineers and engineering geologists, have been busy undertaking the land categorisation (1, 2A, 2P, 2C, 3). Category 3 is a buyout, 2P allows some funding of mitigation for individual properties, and 2C provided for community-based mitigation schemes (a flood embankment, for example).
Fourth, a new 84-page Landslide Planning Guidance document, Reducing Landslide Risk through Land-use Planning was published in January 2024 – a joint project by GNS, MBIE, EQC and industry specialists from the New Zealand Geotechnical Society. The 12 key messages listed inside the front cover should be salient messages to anyone involved in land
development. Notwithstanding the policy responses and science that has emerged over the last 12 months, the major challenge in New
that:
Zealand continues: the best, world-leading science can have minimal if any real-world impact here, because of the law.
My colleague Associate Professor Murray Ford identified 15m of coastal erosion caused by Cyclone Gabrielle at Whangamatā.
Murray said that “Development along the coast must be cognisant of the hazards which might impact the coast, both now and in the future”.
I agree, but though being cognisant of hazards may seem to be obvious when building and developing land, a seemingly intractable problem in New Zealand is the Building Act 2004.
Within the act, hazards are not necessarily something to be too concerned about. Indeed, Section 72 of the Building Act (2004) requires a building consent authority that is also a territorial authority to grant a consent provided the building consent authority considers
• the building work will not accelerate, worsen, or result in a natural hazard on the land or on any other property; and
• the land is subject or is likely to be subject to one or more natural hazards; and
• it is reasonable to grant a waiver or modification of the building code in respect of the natural hazard concerned. Thus, Section 72 accepts that an existing risk of natural hazard (for example coastal erosion/land sliding) should not prevent building work going ahead, as long as the work will not make the situation worse. The clear implication is that Section 72 allows land developers and lawyers, who will push the law to its limits in court if necessary, to build a house on land subject to natural hazards, and sell it, often to unsuspecting buyers. The law really can be an ass, and if we are to learn from the tragic events of 2023, some of it, particularly pertaining to building consents, needs to change.
Of course Gabrielle revealed the hazards that emergency personnel were exposed to during responses to the storms, which was highlighted in July 2023 when Fire and Emergency New Zealand released an independent report into the deaths of two firefighters on February 13 in Muriwai, Auckland, during Cyclone Gabrielle.
The report found that “FENZ’s risk management systems did not identify landslides as a hazard that could harm its firefighters, which resulted in a lack of landslide related procedures and training for firefighters. The Muriwai firefighters knew about Muriwai’s general susceptibility to landslides but did not recognise the warning signs that indicated an imminent landslide threat”.
This raises the question that improved training may be needed for FENZ personnel in future, given New Zealand’s hilly terrain, and susceptibility to a wide range of landslide types.Some countries, for example Sweden, have long recognised the risk of landslides to emergency crews, and in 2013 Sweden published a Response Guideline for Landslides for rescue personnel.
Developing something similar may be useful in New Zealand, and indeed the FENZ report does state that on May 5, 2023 they issued a national safety notice on “Safety around landslips and land subsidence” to all operational personnel. The contents of this are unknown, but I would hope this will be an extremely valuable safety notice for responses to similar events to those in early 2023.
Many of the results and conclusions drawn from those surveyed in Australia in the Design and Make report will be equally important and offer meaningful directions to New Zealand operators in this category says Autodesk
Much like Australia, business resilience is as critical as ever given New Zealand’s economic landscape, and in the same vein, the country’s AECO companies face challenges with cost control and talent says Andy Cunningham, Autodesk’s Senior Regional Director for Australia and New Zealand.
“Naturally, the exact figures would show slight variation when surveyed but there are distinct
similarities with what I am seeing across New Zealand,” he says.
“We are seeing an increasing number of progressive and digitallytransformed organisations in New Zealand – both those with local offices such as Aurecon and Unispace, as well as home-grown success stories such as Warren &Mahoney (WM).
“WM is an especially interesting case study. The company is heavily
using digital capabilities to access material data from its building design portfolio at scale and speed,” says Cunningham.
“This has enabled it to pursue game-changing projects across its daily operations right through to instances of machine learning. Crucially, WM uses data generated through its technology investments to drive fast and easy material design decisions to minimise impact on the
Autodesk’s State of Design & Make report studied 5400 business leaders worldwide –including 451 in Australia –in industries that comprise the Design and Make category. These sectors include architecture, engineering, construction and operations (AECO), product design and manufacturing (D&M), and media and entertainment (M&E).
environment and reduce embodied carbon of construction projects.
“If we look broadly, sustainability is high on the New Zealand government agenda, which is helping position the nation at the forefront of global and cross-region initiatives to become more sustainable in terms of the built environment.
“It is important to note, though, while the government is critical in influencing sustainability goals, this needs to be matched by corporations and investors to allow sustainability to both prove short- and longterm value to business health and contribute to a more sustainable world for generations to come, Cunningham says. The study of the 451 Australian Design &Make companies revealed greater confident from AECO and D&M sectors, with digitalisation and sustainability strategies progressing amid ongoing operational challenges
According to the report, 78 percent of Australian leaders and experts say their companies are prepared to handle unforeseen economic or geopolitical challenges –ahead of the global average of 73 percent, and up from 63 percent in 2023.
The report also found respondents are confident in their companies’ market position: 94 percent feel they are keeping up with the rate of change in their industry, and 86 percent say their companies outperformed expectations in the previous year.
Although these figures reflect that the sense of uncertainty brought about by the global pandemic, geopolitical turmoil and economic instability is
easing, 63 percent believe the global landscape feels more uncertain now than three years ago.
While Australian companies are improving their positions and operations – with many planning new offerings, entering new markets, increasing agility, and diversifying supply chains – the scope of challenges they face has shifted.
Artificial intelligence is steadily making its way into Design and Make sectors. Two thirds (67 percent) of Australian respondents say
“These are fundamental factors that will steer the industry forward as we approach a wave of next generation manufacturing,” he says.
Digital advantage Digitalisation continues to be a centrepiece to driving new outcomes and broadening opportunities for Design and Make organisations across Australia. A third of Australian companies strongly increased investments in technology to deliver improved project outcomes, and 15 percent strongly increased overall investments.
The predominant
Australia’s manufacturing industry hasn’t gone through any drastic changes in the last 10-20 years, and as it stands, many are still focused on the issues of today –predominately, how to reduce the number of times they can do something. The attention needs to shift to improving performance.
they are approaching or have already achieved their goal of incorporating AI into their companies.
Additionally, 79 percent trust AI technologies for their industry, 77 percent agree AI will enhance their industry and make it more creative, and 67 percent agree AI will be essential across the board in two to three years.
The industry must double down on upskilling and reskilling the workforce to thrive in a digital and AI-led economy says Matthew McKnight, Autodesk’s Director for Design &Manufacturing in Australia and New Zealand.
“It needs to identify where AI can take over repetitive processes to free employees to focus on different types of thinking and high-value work, and adapting generative design to drive greater sustainability.
companies across Design and Make sectors have faced multi-faceted volatility, and in many cases, complete turmoil,” says Cunningham “While we are still far from calm waters, architects, engineers, builders, designers and manufacturers have made notable strides in creating foundations for recovery.
As the report flags, Australia is ahead of the global average in preparedness, moving faster to leverage advanced technologies like AI, and hold much stronger views on the short- and long-term benefits of sustainability on business.
results from these digital investments include: improved profitability (seen by 35 percent), better reputation (30 percent), improved productivity (29 percent) and improved data exchange (29 percent).
There were, however, barriers to digital transformation; 30 percent identified cost as one of them, and 37 percent felt the time needed to invest in new tools and ways of working was holding them back.
The report identified that cost control is currently the top challenge (32 percent), followed by attracting, training and retaining talent (30 percent), and environmental sustainability (29 percent). Interestingly, 18 percent noted unreliable supply chain as a challenge.
“For several years,
“This is the result of a concerted transition from reactive to proactive positions, and is creating both resilience and certainty for the years ahead, and with it, uncovering new avenues for growth. Crucially, it’s leading to strong competitive advantage for Australian and New Zealand industries at a global scale, and stands to help in bringing international talent to our shores.”
Attracting and retaining talent continues to plague Design and Make companies. Leaders want to train and upskill their workforces – 71 percent agree this is important –but not everyone knows how, and 46 percent of organisations lack the expertise needed to design effective internal training programs. On a positive note, 71 percent are implementing continuous learning, and 73 percent are investing in digital skills training programs.
Andy Cunningham, Autodesk’s Senior Regional Director for Australia and New Zealand.
Over the next three years, the technical and digital skills organisations expect to prioritise are: advanced skills working with building information management (BIM), modelling or 3D design (39 percent) and software development and programming (36 percent). This is followed by knowledge of data safety and security (35 percent), data analytics, mining and insights (35 percent) and digital skills design (35 percent).
The emphasis on ramping up digital skills comes down to the fact 71 percent of companies believe digital maturity helps attract talent.
The last year has seen a
substantial shift in attitudes towards sustainability and reducing negative impact on the environment.
In 2023, 53 percent of leaders and experts said sustainability is good for short-term business – in this year’s report, that figure is 82 percent.
Meanwhile, 77 percent wish their company prioritises sustainability as much as profits, and 82 percent believe their company’s sustainability initiatives are a key part of business growth strategy for the next three years. As organisations take more sustainability-centred actions, report respondents note significant changes in how they feel about their companies’ efforts: today, 81 percent are proud of their organisation’s sustainability efforts, compared to 47
percent in 2023.
This article was authored by Autodesk, the staff of which surveyed and interviewed nearly 5400 industry leaders, futurists, and experts in the architecture, engineering, construction, and operations; design and manufacturing; and media and entertainment industries from countries around the globe for the Design &Make report.
Autodesk says its software is changing how the world is designed and made. Its technology spans architecture, engineering, construction, product design, manufacturing, media and entertainment, empowering innovators everywhere to solve challenges from greener
buildings to smarter products
For more information, visit autodesk.com.au or follow @autodesk. #MakeAnything ##
Over the next three years, the technical and digital skills organisations expect to prioritise are: advanced skills working with building information management (BIM), modelling or 3D design (39 percent) and software development and programming (36 percent). This is followed by knowledge of data safety and security (35 percent), data analytics, mining and insights (35 percent) and digital skills design (35 percent).
E v e r y p e r s o n , e v e r y c a n c e r
895,115 Kms driven to get people to appointments
46,600 Bed nights for people receiving treatment 5,742 People attending supportive care programmes
0 8 0 0 C A N C E R ( 2 2 6 2 3 7 )
The success of Rapid Facility Services is driven by a team that combines experience, commitment and a professional skillset that covers every aspect of facilities management with personal service
The team was forged by three friends working in the industry who realised that the key thing stressed building managers, business owners and landlords needed was to make a single call and get a reliable and qualified support team that would cover any aspect of facilities management.
The Rapid trio set down a business philosophy that “we will do what others can’t or won’t do “ and set about assembling a highly trained, efficient and safety-conscious team of professionals who get the job done right, the first time.
Today that service stretches from food manufacturers’ audit cleaning, all aspects of industrial cleaning, painting, building and floor safety management to anti-microbial and moss
Having worked in the industry for many years, three friends, Paul Schoch, Robyn Schoch and Andrew Chan realised that by combining their skills, they could create a company unlike any other
and mould treatments to prevent surface
to roofs, ceilings, walls, floors and specialised equipment.
Nearly a third of Australian companies are already trialing or using AI to help solve major issues facing the industry, including reducing the cost of construction . Another third plan to use it in the future.
This is likely also to play out in New Zealand, which is facing similar issues. The construction sector is facing significant challenges and disruptions, including a shortage of labour, skyrocketing construction costs, and weather-related incidents impacting infrastructure projects and buildings.
The new report by Autodesk and Deloitte, the State of Digital Adoption in the Construction Industry 2024 report , has found the construction industry across AsiaPacific is facing
similar challenges, and is exploring AI and other technologies to help solve these problems.
“What we’re seeing in New Zealand is similar to construction challenges that are being faced in Australia and across AsiaPacific,” says Sumit Oberoi, Senior Manager, Construction Strategy & Partnerships, AsiaPacific at Autodesk.
“Construction is a much needed and growing industry in New Zealand, but it has seen some challenges – particularly over the past few years. The sector has
continued to be impacted by supply chain disruptions, rising construction costs and labour shortages.
“This has been followed by a double-dip recession, with rapid interest rate rises to curb inflation and the damage from extreme weather damaging roads and impacting many of New Zealand’s fruit and vegetable-growing regions,” says Oberoi.
“With the challenges facing the construction industry, as well as increased productivity required to address the issues the
industry and economy is facing and to deliver the infrastructure pipeline, digital transformation is understandably one of the key emerging trends we’re seeing in New Zealand’s construction sector,” says Oberoi.
The report is the second edition of the annual survey, with insights from 933 construction firms across six markets including Australia, Singapore, Japan, India, Malaysia and Hong Kong.
The report finds 30 percent of Australian companies surveyed are currently
trialing or using Artificial Intelligence (AI) software to increase efficiencies and help to solve major issues facing the industry, including increased labour shortages, higher material costs, and global supply chain disruptions.
Additionally, 61 percent of Australian construction companies surveyed say AI will help them to reduce costs amidst more construction companies entering external administration than any other industry in the financial year to date.
“Disruptive new technologies combined with a challenging business outlook means that construction and engineering leaders in Australia and across AsiaPacific are hav-
ing to seriously rethink their tools, workforce skill needs and how they interact with clients and contractors.
“Generative AI has ex-
a new project proposal doesn’t need to start from scratch, instead leveraging material and pricing based on projects with similar
Generative AI means that a new project proposal doesn’t need to start from scratch, instead leveraging material and pricing based on projects with similar specifications
ploded onto the agenda for senior leaders with the rapid adoption of tools like ChatCPT, Midjourney and Github Copilot. No industry is immune from the transformative potential of this technology,” says Oberoi.
“Generative AI means that
specifications completed by the company.”
A further 33 percent of Australian construction companies plan to use AI in future, making it the most common technology they are looking to integrate into their operations.
“If all companies with plans to adopt AI do so, AI will have a similar level of prevalence in the construction industry as data analytics or mobile apps,” reckons David Rumbens, Partner at Deloitte Access Economics Integrating technologies like these into business operations will be no small feat. New Zealand’s building and construction sector is a significant contributor to the economy, contributing 6.7 percent of real GDP to March 2022 and was the third largest employer in the year to June 2022. Building consent numbers reached record-level highs and the workforce pipeline has continued to grow.
“Priority areas for construction businesses to
improve digital adoption include starting small by piloting projects, selecting a digital champion, tracking a range of success measures, building a digital ecosystem, and asking whether your business is AI ready,” says Oberoi.
“Put simply, construction companies need to get their ducks in a row now so they can implement AI in future years. The first step to successfully implementing AI is data standardisation and having an operational common data environment for teams.”
This article was authored by Autodesk and Deloitte, the staff of which surveyed and interviewed 933 construction firms in Australia, Singapore, Japan, India, Malaysia and Hong Kong.
Autodesk's Design and
• Across APAC, 30 percent of construction companies are trialing or currently use AI in their operations, with a further 38 percent in the article percent planning to use the technology in the future
• Nearly 80% percent of businesses believed they received strong business returns or a positive return on investment from implementing AI and other technologies including data analytics, mobile apps, robotics, prefab and modular construction, and construction management software
• The critical role of technology in supporting business growth is increasingly being recognised. There was an increase in both businesses seeing new technology as assisting with new project work (up from 38 percent to 45 percent) and technology in improving internal processes (up from 37 percent to 43 percent).
• Foundational technologies are the most commonly used, with data analytics (47 percent), construction management software (43 percent) and mobile apps (40 percent) providing the backbone of construction operations
• Generative AI is expected to become as pervasive in the construction and engineering industry as these foundational technologies, with 94 percent of businesses now having plans to integrate AI and machine learning into their businesses
Make Platform unlocks the power of data to accelerate insights and automate processes, empowering
customers with the technology to create the world around us and deliver better outcomes for their business
and the planet. Visit autodesk.com or follow @autodesk . #MakeAnything
Civil Contractors New Zealand Technical Manager Michelle Farrell observes a real-life scenario of temporary traffic management and how it aims to reduce risk, but in some ways achieves the opposite
The activity is footpath construction on two corners of a no exit street, off a side street, off a very busy Auckland urban road. The Code of Practice for Temporary Traffic Management (CoPTTM) dictates a
30km/hr temporary speed limit, shoulder closures, pedestrian detour and up to 100m taper in each direction. The TTM workers did a nice job of setting out the cones and signs and were pleasant to deal with while the road needed
stop/go on the first day. They worked long hours in the fierce sun and were first onsite and last to leave, as you’d expect.
Several days later, during a long weekend, I was passing by and noticed several hazards had
occurred, so I took the opportunity to look at the picture with a wider lens. Some might say I did a quick risk assessment. I noticed the following risks. Several signs had blown over in the strong winds we had, with two blocking
the footpath (a busy access road to a popular beach) – now hazards for pedestrians and children on bikes. An elderly man was seen struggling to move a sign blocking his driveway. The pedestrian detour signs had blown over, making the setup unclear.
With approximately 300m of residential road affected by the CoPTTM-prescribed cone layout, the workers supposedly had to knock on doors (time consuming) to get residents to move vehicles off the street for several days (it’s usually packed with parked cars) –potentially congesting other narrow local roads. Some vehicles owners apparently couldn’t be contacted, and several vehicles remained parked in the coned off areas throughout the works.
Cars drove through the area at speed – by removing parked cars
either side of the road, the usable carriageway width is significantly wider, meaning vehicles are travelling faster with the TTM in place than they would on a normal day. Later during the long weekend when the weather cleared, all the cones delineating the no parking taper along the whole road had been moved aside and cars lined both sides, as public blatantly ignored what was perceived as unnecessary TTM to access the popular beach.
To summarise some risks that were observed during a three minute walkover (i.e. what can I see here that could potentially become a hazard?): high winds knocking over signs, therefore lack of signs making the directions to road users and pedestrians unclear; signs and cones being hazards in themselves;
vehicle drivers ignoring the temporary speed limit and in fact travelling faster than usual due to increased carriageway width; public moving cones to park cars in zones that were supposed to be blocked off. It occurred to me, that the TTM in place (in accordance with CoPTTM) may have been achieving the opposite of its intention, due to the particular situation. What is the purpose of the long taper of cones? Would removing these cones increase risk to anyone? Or would it in fact decrease the risk of road users ignoring temporary speed limits, moving TTM out of the way and potentially becoming more desensitised and disrespectful. In turn potentially leading to abuse of the TTM staff. Could the work be planned differently (timing,
staging, construction methods) to avoid TTM being in place for longer than needed? Is a shoulder closure necessary, or would a bulky physical barrier (eg a small truck) parked in front of the works actually provide better protection for the workers? Is the unattended site’s TTM working as intended, is it necessary or is there a better way of doing it?
It seems to me the required CoPTTM setup is potentially creating more risks in this scenario than the works themselves. And if an incident occurred due to this set-up, who would be held responsible?
If we treated traffic management in the same way we treat other high risk activities in a public urban residential area, we might see someone coming to site to view what the street usually looks like (parked
cars on both sides, traffic forced to slow down due to this narrowing effect and a busy beach access, including for children on bikes); they might consider the proposed timing of the works (the day before a four day summer weekend beside a popular Auckland beach) and wonder whether the works could be staged on either side of the weekend; they might consider bulky physical barriers to protect the works and to force road users to both slow down and go around the works; they might even realise that letting the cars stay parked along the ‘taperzone’ where works were not actually happening could help calm traffic, rather than hinder the works.
Often this information isn’t available during the planning stage and when
the contractors turn up to site to start the works they might notice other risks, such as the high winds or the increased carriageway width or realise that delays have occurred to the works starting and now the works will straddle a 4-day weekend.
A pre-start or quick toolbox meeting held in the morning, including the physical works contractor, the STMS, and perhaps a client representative could identify these new risks together and collectively make a decision of how best to minimise them. The decision would then be appropriately recorded and communicated to anyone affected by the changes, perhaps with a note for the STMS to keep an eye on one of the controls (how are pedestrians acting for
example, is the layout working as intended?) and to give the contractor project manager a ring if they’re concerned. Actually, it reminds me a bit of the three C’s: “consultation, cooperation and coordination” as well as Worksafe advice that a risk-based approach can help parties “reach a common understanding and establish clear roles, responsibilities and actions”. Some food for thought, as we try to understand how the risk-based approach can be applied to temporary traffic management. Who needs to be involved in these decisions and at what stage? What processes are in place, or need to be added for success? How do we make it easier for people to make smarter decisions based on the specific environment and
activity they’re working in and not just lay out cones according to a book and a traffic management plan they’ve been handed for the first time that morning.
And remember, both the contractor and the TTM provider in this case have followed their longpractised approach of applying stock-standard thinking and done everything just as they should under CoPTTM, this is in no way a poor reflection on them. This is why it’s time for a change.
Pssst – what do they mean by a risk based approach for temporary traffic management? | Civil Contractors NZ
STAY IN THE HEART OF CHRISTCHURCH
Our brand-new Quest on Cambridge is opening this November. Enjoy introductory rates from $135 per night for stays from 15th November 2023 to 14th January 2024*.
SUSTAINABILITY IS HERE TO STAY
We’ve replaced almost all single-use plastic shampoo, conditioner and bodywash bottles with dispensers - removing 3.68 tonnes of plastic out of circulation. We’re also recycling old soap bars into new ones together with Soap Aid. Find out more at soapaid.org