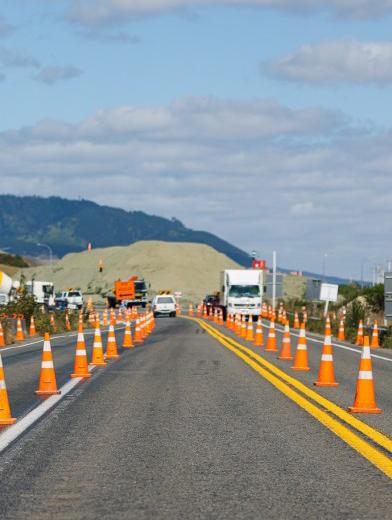
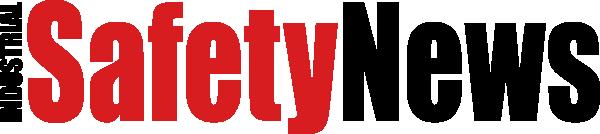
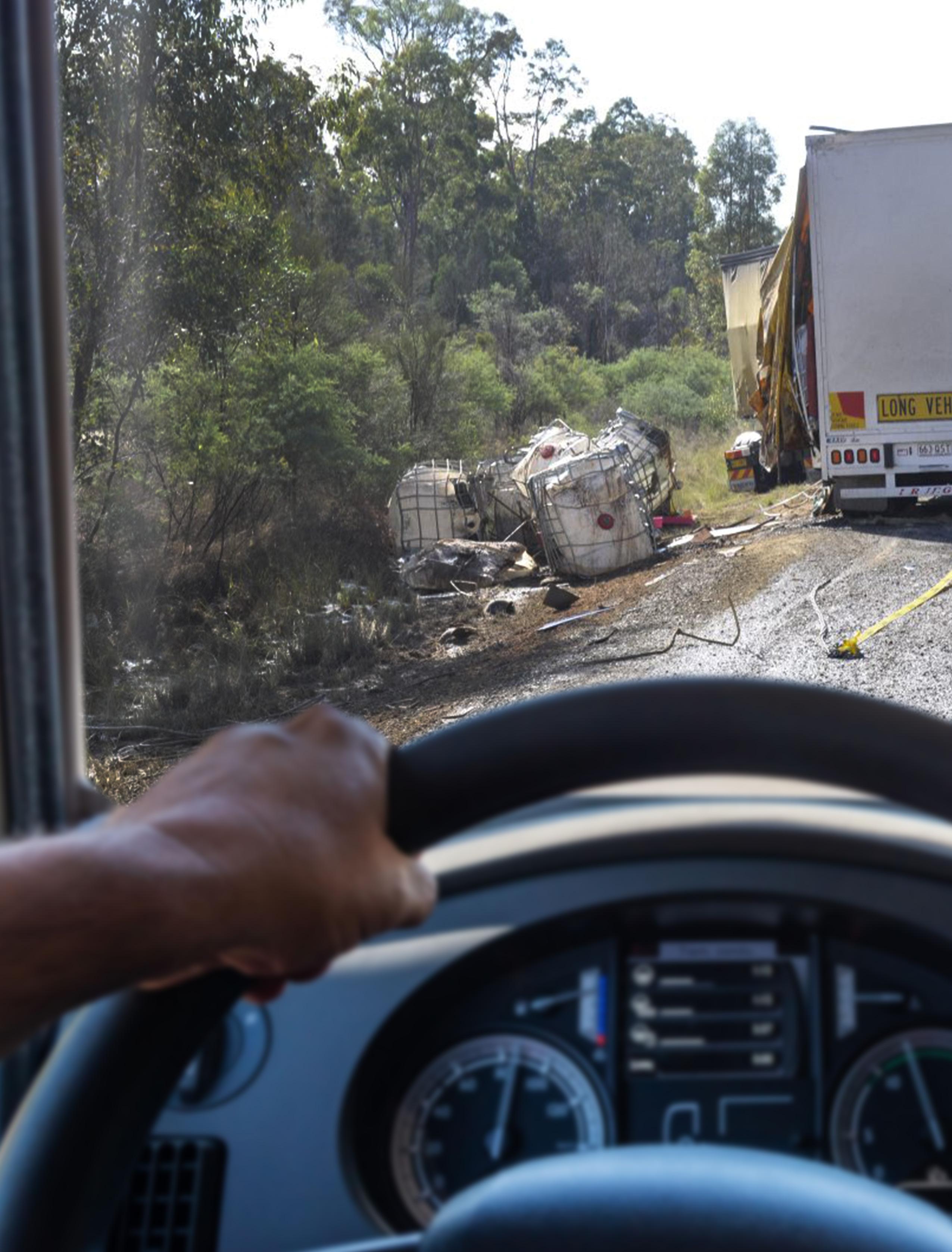
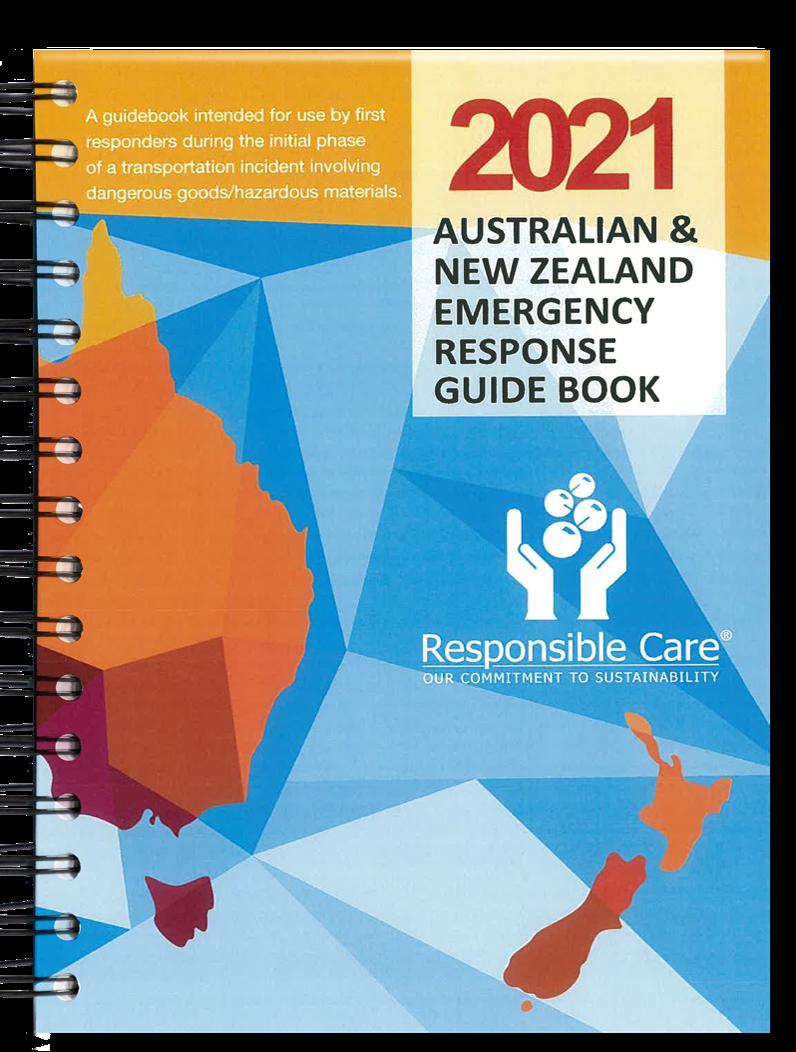
Now is the time to schedule your customised Responsible Care NZ Competent Chemical Handler course, conveniently delivered on your own site
Changes to our Global Harmonisation System (GHS) chemical regime applying from 30 April 2021 require accurate and timely advice - non-compliance could prove costly.
Competent staff avoid expensive and sometimes confusing compliance advice, while enabling an effective response to chemical incidents, often without requiring emergency services.
Inspectors and certifiers with years of expertise warn of a declining national workplace chemical safety performance.
A crucial factor is the continuing loss of onsite chemical safety advice, primarily due to replacing flawed but effective mandatory Approved Handlers with whatever employers now deem sufficient.
A second major chemical incident in the same public facility is a timely reminder that safe chemical management is not receiving the attention it deserves. Competent staff are essential.
Onsite Responsible Care NZ (RCNZ) Competent Chemical Handler Certification courses are tailored to reflect your chemical inventory and enable compliance.
Upskill the last of your HSNO Approved Handlers, update Certified
Handler requirements and successfully implement the updated Global Harmonisation System (GHS).
For struggling, noncompliant business operators who are attracting attention from enforcement agencies, practical onsite advice from Competent Chemical Handlers helps lessen the load on a diminishing number of Compliance Certifiers. It helps to ensure site chemical safety measures remain effective.
RCNZ Competent Chemical Handlers (CCH) are increasingly in demand, resulting from our popular ‘Walk and Talk’ site visit to assess actual chemical management performance, identifying the need for specialist training, throughout the product life cycle.
Chemical incidents now guarantee media attention, often sensationalising the incident by highlighting persons adversely affected by unwanted exposure to chemicals.
This can irretrievably damage reputations to both customers and suppliers, particularly if employers have not taken all practicable steps to safely manage their chemical inventory throughout their operations.
When chemicals do cause problems, employees, customers, WorkSafe
Ensuring staff are competent to safely manage the harmful chemicals essential to your business includes your effective response to a chemical incident.
To enable a smooth, cost-effective transition to and beyond compliance, you need compliance tools: - the updated RCNZ industry Codes of Practice reflecting our revised GHS chemical management system
- your 24/7 CHEMCALL® emergency response subscription; and the all-important ‘how to’ advice arising from our popular site ‘walk and talk’ assessments - replacing your Approved Handler with our Competent Chemical Handler certification
These are all cost-effective measures which add value to your business.
Talk to us today about compliance tools, which confirm you are a good employer, committed to safeguarding employees and our environment by safely managing your chemical inventory.
Responsible Care NZ 04 499 4311 www.responsiblecarenz.com
inspectors, local authorities, health protection officers and emergency response organisations all benefit from the expertise and product safety information available 24/7 from 0800 CHEMCALL®, our industry’s unique, subscription based chemical emergency advisory service.
Supported by thousands of compliant Safety Data
Sheets (SDS) combined with their collective industry expertise and local knowledge, CHEMCALL® responders provide callers with comprehensive advice about how to safely manage the incident, safeguarding people and often avoiding business disruption.
The judgment comes around two-anda-half years after Wiles and then University of Auckland employee Professor Shaun Hendy initially filed their claim with the Employment Relations Authority in January 2022.
Dr Wiles alleged the university failed to protect her from a “tsunami of threats” she received for her public commentary on the Covid-19 pandemic. She said she had raised concerns to the university about her safety since April 2020, shortly after the pandemic began.
The university has denied unjustifiably disadvantaging Wiles, breaching their agreement or its statutory obligations. It said it had also acted in good faith towards her. However, the Employment Court’s judgment does not agree.
“This case is important for organisations where staff have public profiles or are engaging with traditional or social media,” says employment law expert, Dr Dawn Duncan.
The University of Otago law lecturer says the judgment confrims that employers have a legal duty to take all reasonable steps to protect their employees from harm, including mental and physical harm posed by third parties.
“Where employees are required to be in the public eye or have an online presence, they can face very real risks to their mental health and physical safety. Risks can include online abuse and harassment, disclosing personal information, stalking and threats of violence to themselves or their loved ones.
“Employers need to ensure they have the right policies and processes in place, that
The Employment Court has ruled that Associate Professor Siouxsie Wiles’ employer breached its contractual obligations to protect her health and safety in the wake of harassment she experienced as a result of her work
they are proactive in getting the right advice and taking appropriate action, that they listen to and work with their staff to get the right solutions, and that they tailor their health and safety responses to an employee’s individual risk profile.
“What the law requires of an employer will vary
depending on the situation and the nature of the risks but could include a range of online or physical security measures, practical changes to working practices, specific training, additional workload support, help in working with Police or other agencies, or providing
access to counselling.
“This case highlights the growing problem of online abuse and harassment faced by people working in the public eye. Responding to the risks posed by this behaviour is an essential part of an employer’s health and safety obligations.”
The Expos will showcase the most comprehensive range of innovative products, services, solutions and the entire supply chain under one roof by local and international participants to trade visitors, potential buyers, policy makers, government officials, C-Level executives, business leaders, leading industry experts, top-tier public visitors and key decision makers from the region and beyond, making it a definitive power packed networking platform, where new projects and partnerships are initiated and visionary objectives are implemented.
Architecture and Urban Planning Expo - Oman’s first and only dedicated event focusing on Architecture and urban planning will showcase the latest technologies, products and services.
Architecture Section is an exclusive event where architects, designers, specifiers and property developers from the Sultanate of Oman and the Middle East region explore carefully selected innovative and inspiring products, materials and services for their projects. Some of the most revolutionary solutions will be presented in the Expo which will generate high interest among the architects and designers’ community.
The Urban Planning section will provide an unmatched platform for the urban and landscape design industry to secure new business in the Sultanate of Oman and the region. Key decision makers will meet local and international suppliers to explore business opportunities, and to source the latest landscaping,
Exhibitors and visitors are invited to participate in the Home and Building Expo, co-located with the Architecture and Urban Planning Expo, which is the Sultanate of Oman’s premier bespoke B2B and B2C event to be held from 07 - 09 October 2024 at the Oman
Convention and Exhibition Centre, Muscat.
infrastructure & urban development solutions and technological advancements.
There are diverse and cost-effective ackages to
ensure participation with assured ROI and exhibition booths to create a strong impact and presence at the event.
The event organiser also offers customised packages best suited to your organisation’s requirements and budget.
Event website: http://omanhome-building.com/ For more information, please contact: Ms. Ulrika Varela Email: ulrika@muscat-expo.com Mobile: +968 9396 1624
Industry leaders are calling recent commentary on temporary traffic management uninformed and unhelpful, as they work to transition from a ‘one size fits all’ model to a more risk-based approach
Temporary Traffic Management
Industry Steering Group (TTM ISG) Chair Dave Tilton says the industry is already making progress in ensuring temporary
traffic management is fit for purpose through the transition from the compliance-based Code of practice for temporary traffic management (CoPTTM) to the more riskbased approach described
in the New Zealand guide to temporary traffic management (NZGTTM).
Tilton says this work has been underway for the past few years.
“The controls we are using, such as cones and
temporary speed limits, and the way we are using them, often do not align with the risks of a specific site or job. This can make it difficult for the public to see the correlation between the temporary traffic
management in place and the risks to themselves, other road users and our frontline people.
“There’s an obvious difference in risk in conducting the same work on a busy fourlane, 100km/h motorway compared to a rural road or quiet urban cul-de-sac.
“CoPTTM is prescriptive and can sometimes be implemented as a ‘one size fits all’ approach, which has its challenges, particularly across such a diverse roading network.
“The move to a more risk-based approach enables temporary traffic management that is as safe as possible for the specific risks at a particular site. It will allow the industry to apply more targeted temporary traffic management solutions and will result in a reduction of unnecessary temporary traffic management,” Tilton says.
However, he explains that the industry is focused on success over speed when it comes to the transition.
As highlighted in the Ernst & Young Global Limited (EY) report commissioned by Auckland Mayor Wayne Brown into the temporary traffic management system in Auckland:
‘The current TTM situation did not get this way overnight. It cannot be fixed overnight either … Real progress requires – and demands – a coordinated response with central government providing local government the tools they need to create the right incentives within the TTM system.’
Tilton says it’s a big change to the way the industry has planned and delivered temporary traffic management for more than 20 years.
“It is a big learning curve for everyone involved and important we get it right.”
Civil Contractors New Zealand Chief Executive Alan Pollard says a collaborative approach is needed.
He says while contractors are an easy target
– to keep road users and workers safe during highrisk works.”
He acknowledges that there is always room for improvement, and echoes Tilton’s point that the industry has been moving toward riskbased temporary traffic
for criticism, a more collaborative approach including clients, designers and subcontractors is needed to reach better outcomes, as industry works within health and safety legislation, enforced by WorkSafe as the regulator, with project standards and traffic management plans set by designers and clients.
“Suggesting traffic management is deployed to maximise profit is nonsense,” Pollard adds.
“It’s there for one reason
Pollard says.
Tilton adds that everyone has a role in improving safety for people who are working at or travelling through road works and, while he acknowledges people’s frustrations, he cautions against the current, unhelpful rhetoric around temporary traffic management.
“How road users respond to temporary traffic management is a critical factor in how safe these environments are for everyone, including themselves.
“The stronger the ‘war on road cones’ narrative, the greater the public disregard for temporary traffic management, the more unsafe our worksites will be – and the more traffic controls, like cones, we need to keep people safe.
“This kind of rhetoric is not only unhelpful, it’s reckless and it actually serves to exacerbate the problem.”
He says road cones and temporary speed limits are a symptom of the problem, not the problem itself.
management for some years. However, Pollard says while this would lead to better safety outcomes and appropriate on-site controls, it would not necessarily lower traffic management costs.
“The way sites are set up is a function of the client requirements and what is needed to meet contractor obligations under health and safety legislation. We will not and cannot compromise people’s safety. It’s something everyone needs to improve on,”
“They are a highly visible symbol of ineffective systems and planning. Ensuring the right balance between costeffectiveness and the safety of everyone who works on or travels through road works will require integrating temporary traffic management earlier in the planning of work activities, rather than treating it as an afterthought at the end.
“Temporary traffic management is used to keep people safe while the work gets done.
Effective temporary traffic management should be no more – and no less – than what is required to keep everyone safe.”
“Businesses must manage their risks to keep workers safe. In each of these cases there was a failure to follow basic machine safety standards. WorkSafe investigated and prosecuted the cases as part of our role to hold businesses to account when they fall short on health and safety,” says WorkSafe principal inspector Mark Donaghue.
“All three cases are from the manufacturing sector – which has a persistent problem with machine safeguarding and is one of the country’s high-risk industries.”
One worker had two fingers amputated and a third degloved in a punch and shear machine, when the regular machine was out of order at Thompson Engineering in Timaru in January 2022. The business was recently fined $247,500 and ordered to pay reparations of $35,000.
Another worker had three fingers partially amputated while using a punch and forming press at Auckland’s Anglo Engineering in March 2022. In sentencing, Judge Lisa Tremewan referred to “an unintended complacency” and that “it is critical that robust practices are employed by those within the relevant industries”. A fine of $200,000 was imposed, and reparations of $35,337 were ordered.
And a third worker was cleaning a machine when it amputated two fingers and degloved a third at Flexicon Plastics in Auckland in August 2022. The machine’s on/off switch had been knocked into operation because the interlock wasn’t functioning. A fine of $74,392 was imposed, and reparations of $33,000 ordered.
Courts have imposed more than half a million dollars in penalties since mid-March, in cases where workers have lost fingers on machinery that wasn’t kept safe by businesses
“If you are unsure whether your safeguarding is up to scratch, engage a qualified expert as soon as possible,” says WorkSafe’s Mark Donaghue.
“These sorts of incidents are avoidable. Workers should not be suffering harm like this in 2024, and businesses have no excuse. WorkSafe is notified of
machine guarding incidents from across the country every week, and is regularly prohibiting dangerous machinery as part of its proactive and targeted assessments. WorkSafe has a role to influence business to make sure they keep people healthy and safe –that’s why we’re speaking out on this issue.”
Workplaces have been required to safeguard machinery since the Machinery Act 1950 took effect. But more than 70 years later, workplaces still aren’t getting it right, with too many workers in Aotearoa being injured and killed from unsafe machinery.
A tragic start to this year’s lambing and calving season has prompted WorkSafe to issue a warning to rural workers to refocus on the risks around quad bikes
WorkSafe is investigating all four fatalities, the first of which occurred on 18 July in Wairarapa. It was followed by another on 22 July in Canterbury, one on 26 July in Southland, and most recently in Northland on 30 July. All four incidents coincided with the start of lambing and calving season.
“Our sympathy is with every family and community mourning these sudden deaths. Although our investigations are in their early stages, the trend is worrying enough for us to sound the alarm already,” says WorkSafe principal inspector Graham Bates.
“Doing a risk assessment of your terrain and tasks
must be the top priority before getting on a quad bike. This is a time of year when we are experiencing variable weather and growth, and variable ground conditions. Sloped surfaces and steep terrain can be especially problematic and have sadly been a factor in some of the recent cases.”
Farm vehicle incidents are one of the top two causes of workplace deaths in New Zealand, which is why agriculture is a priority sector under WorkSafe’s new strategy.
WorkSafe is targeting the biggest risks and working with the sector to improve health and safety in agriculture.
“Farming consists of a never-ending list
of tasks and constant reprioritisation. However, we cannot let those challenges contribute to loss of life or injury. The people with the most power to influence this are those on the ground each day doing the work,” says Bates.
WorkSafe’s recommendations for reducing the risks of harm on farm include:
• Consider installing a crush protection or rollover protection device on your quad bike.
• Choose the right vehicle for the job and ensure that the driver is competent.
• Always use your
seatbelt and helmet.
• Consider undergoing quad bike training.
• Prioritise maintenance. That should cover attachments, good tyres and brakes.
• Remember tired people make mistakes.
• Ensure that the vehicle is safely stopped and brakes are fully engaged before getting off.
• Don’t be afraid to seek assistance when you need to –neighbouring farmers are always more than willing to lend a hand.
Read WorkSafe’s guidelines on safe use of quad bikes
Creating a healthy workplace starts with a solid foundation for wellbeing – the overall physical, mental, emotional, spiritual, and social health of people. A positive culture, increased productivity, higher staff retention, and better health and safety outcomes are just some of the benefits that come from making wellbeing a key focus of an organisation.
Leading health and safety organisation Site Safe New Zealand is on a journey to work with the construction industry to shift the approach to wellbeing in the workplace and set people up for success with the tools and resources they need to support wellbeing.
Since the release of a 2019 research report conducted by Site Safe into suicide in New Zealand’s construction industry, there has been acknowledgement from industry that mentally healthy and well workplaces have benefits for both health and safety and business success.
“We know how important it is to destigmatise the idea of looking after ourselves, especially in our industries who have typically had more of a ‘toughen up’ attitude when it comes to our wellbeing,” says Brett Murray, Site Safe New Zealand Chief Executive.
“We already work with key partners like MATES in Construction and Hato Hone St John to provide resources and training courses focusing on mental health in the industry, but we knew there was more we could do to support our industry and members, and in particular
small organisations who don’t have the financial resources to invest in this area.”
This year, Site Safe has partnered with Ignite Aotearoa to give Site Safe members free access to their
are evidence-based, easy to access, flexible and affordable, with a focus on partnering with workplaces to enhance employee wellbeing.
Site Safe are also investing in the wellbeing of the industry by sponsoring a
online platform and a large range of mental health and wellbeing resources, information, and workshops.
Ignite Aotearoa is a social wellbeing enterprise backed by Emerge Aotearoa – one of New Zealand’s largest independent mental health and social service organisations. Ignite Aotearoa’s mental health and wellbeing offerings
number of one-on-one support sessions so members can try out one of the services offered by the platform. Ignite Aotearoa hosts over 100 different providers, including financial advisors, human resource consultants, occupational therapists, dietitians, social workers, counsellors, psychologists, and more.
“80% of our members are
small businesses who may not have ready access to tools and resources that support workplace wellbeing,” explains Murray. “We want to support our members to create a solid foundation for wellbeing by giving them access to a wide range of information and support that suits their needs.”
“Both our organisations have strongly aligned values,” says Murray. “Like us, Ignite Aotearoa believe New Zealanders should be able to access mental health and wellbeing support whenever they need it.”
By being proactive and getting support, employers can set a positive example for workers. Being open, honest, and free of judgement is a sure way to ensure people feel comfortable speaking up and ask for help when they need it.
To learn more, visit https://www.sitesafe.org. nz/news--events/news/ new-member-benefit-igniteaotearoa/
Access to exclusive guides & resources
Show your commitment
Discounts on Site Safe
Invitation to member only events
Discounts from well-known suppliers (Member App)
KiwiRail needs to fix problems with its systems and training for responding to foul weather and stay up to date with how well third parties maintain their waterways in the rail corridor, the Transport Accident Investigation Commission (TAIC) says
Anew report on a train derailment in stormy weather near Te Puke, Bay of Plenty, in January 2023, identifies systemic safety issues.
A KiwiRail freight train was travelling from Kawerau to Tauranga on the East Coast Main Trunk line with 39 wagons in the early hours of 29 January after heavy rain with flooding. The train drove at about 60km/h along a section of track with floodwater crossing it, the emergency brake activated automatically and the locomotive stopped. Only five wagons were behind the locomotive, of which four were uncoupled, and the remaining 34 wagons were 100 metres back down the track. Eleven wagons had derailed and lay strewn, some overturned, with disgorged freight in a chaotic pile across fields on either side of the track.
Chief Investigator of Accidents, Naveen Kozhuppakalam, says the accident happened because heavy rain and consequent volume of floodwater overwhelmed the drainage system around and under the rail corridor.
“At the accident site, water levels rose about 3.5 metres and washed out the stone and gravel support for the tracks. The fully laden train passed over the unsupported tracks, pushed the rails
out of shape, wagon wheels lost contact with rails, and the wagons derailed.
“The train was cleared to travel on this section of track, but it shouldn’t have been. The previous day, the same train crew told Train Control that they saw high water at what became the accident site, but they did so unclearly and the track inspector inspected the wrong location.
“To avoid similar accidents in future across New Zealand, a lot of elements need to come together. KiwiRail should have Triggered Action Response Plans in place. And staff should be adequately trained to identify when and where parts of the rail corridor are vulnerable – like this one, which was flood prone and there was reported high water after forecast rainfall.
“If the right plan is in place and staff are trained and correctly equipped, then proactive rather than reactive track inspections or closures are more likely.”
“KiwiRail should have good awareness about how well third parties –
landowners, councils and the like – are maintaining waterways that they own in the rail corridor. There’s more risk of flooding if third parties don’t adequately maintain their streams and culverts. So KiwiRail needs to satisfy itself that all those waterways, have effective and up-to-date maintenance programmes.
The Transport Accident Investigation Commission opens an inquiry when it believes the circumstances of an accident or incident have – or are likely to have – significant implications for transport safety, or when the inquiry may allow the Commission to make findings or recommendations to improve transport safety.
The Commission’s purpose is to improve transport safety by avoiding repeat accidents, rather than by ascribing blame.
Three nationwide safety issues and recommendations for KiwiRail to reduce the risks of serious accidents:
1. Foul weather responsiveness: KiwiRail’s
current response to adverse weather conditions is not fit for purpose and is not consistent throughout New Zealand’s rail network. Recommendation that KiwiRail review its adverse weather response system and processes.
2. Foul weather training: KiwiRail’s training for rail personnel on the procedures for reporting and receiving unusual weather condition information was inadequate. This meant procedures to ensure safety of trains were not initiated in accordance with KiwiRail’s own rules. Recommendation that KiwiRail put more emphasis on training rail personnel in reporting unusual weather conditions.
3. Knowledge management about waterway maintenance: KiwiRail lacked adequate awareness of maintenance by third-parties of the waterways those parties owned in the rail corridor. Insufficient maintenance increases risk that they won’t function as designed. Recommendation that KiwiRail address this
Historically safety documents and certificates have been hard copy paperwork that sparkies need to lug from one premise to the next, which really isn’t practical when safety assessments need to be logged right away on every job, says Fergus founder Dan Pollard
Digital safety certificates have helped tradies move from easy-to-lose, paper documentation to a simpler, more efficient digital format. For instance, these certificates mean sparkies can complete necessary safety checklists electronically, ensuring that all safety measures are reviewed and met before starting a job. This way electricians can go through each item on the safety checklist systematically. By assessing the risks
methodically, electricians can make more informed decisions that prioritise their safety and that of their mates onsite.
Job management software also plays a role in safety, going hand-in-hand with digital safety certificates. This type of software means that sparkies have easy access to previous safety certificates if needed, as well as track their safety checklist completion and monitor the safety status of ongoing projects.
Communication is
crucial to a safe working environment, and by using digital certificates, or even better job management software, this can be streamlined between workers. Tradies can share safety-related information and updates in real time to ensure that everyone on the team is aware of any potential hazards as well as any precautions needed to mitigate these risks.
Many sparkies find admin overwhelming, time consuming, and, let’s face it, boring. Fortunately, smart
digital job management tools can automate many of the admin tasks associated with safety compliance, like scheduling safety training sessions and reminding sparkies to complete their safety checklists, so they don’t have to worry about it. In short, automation takes away the admin burden for sparkies so they can focus more on their core tasks—like working with live electricity—while still ensuring compliance with safety regulations.
OFSEC EVENT 2024 is designed to meet the needs of the local, regional and international markets by linking practitioners, suppliers, distributors and manufacturers from the fire, safety, HSE and security industry, with key decision makers from the government and private sectors, making it a definitive networking platform, where new projects and partnerships are initiated and visionary objectives are implemented. This event also aims to create synergy and strengthen the collaboration between the authorities and the industries.
The 2-day Exhibition & Summit will attract participation from a large number of exhibitors and representation from over 30 countries, with a slew of product and service launches, to the trade visitors and potential buyers from the region and beyond. The Summit will feature an expansive lineup of stellar speakers, case studies, panel discussions, unique presentations providing access to a wealth of industry leading knowledge, sharing best practices and experiences, spotlighting trends, information exchange,
insights and outlooks with actionable takeaways. OFSEC has collaborated with government bodies, leading industry associations, research partners and specialists to establish the exhibition that caters to the entire fire, safety and security sectors, making it an imperative convergence point. The expo is aligned with the demand and supply of the
market across the board of industries to share best practices, tackle challenges, and explore breakthrough methods for the integration of safety and security technologies.
Event Website: https:// www.ofsecevent.com/
For more information on Sponsorship and Exhibiting Enquiries, please contact:
Navneeth K. | Project Director
Mobile: +968 9123 7892
Email: nk@muscat-expo. com
Muscat Expo LLC | P O Box 1406 PC 133 | Al Khuwair, Sultanate of Oman
After a worker in the kiwifruit industry was traumatically injured, WorkSafe has accepted a commitment from his employer to an enforceable undertaking centered around using Artificial Intelligence (AI)
AI technology to sense pedestrians around forklifts is the centrepiece of a new safety commitment WorkSafe has accepted from a major player in the kiwifruit industry.
The commitment, known as an enforceable undertaking, was put forward by Trevelyan’s Pack and Cool Limited in Te Puke, where a worker was traumatically injured in April 2022. Trevelyan’s is New
Zealand’s largest singlesite kiwifruit and avocado packhouse.
The man was struck while walking behind a reversing forklift, and had his left leg and foot run over. When the driver moved the forklift forward, he ran over the victim’s foot a second time. Ultimately, the victim’s lower left leg could not be saved, and it was amputated below the knee.
WorkSafe’s role is to influence businesses to
meet their responsibilities to keep people healthy and safe. Our investigation found Trevelyan’s traffic management plan for the site was deficient, with forklifts and workers clearly not kept separate.
“Forklifts are essential to the kiwifruit industry and we expect businesses to manage their risks. Where they don’t, we will take action. Harvest season brings heightened risks from more product
movement, less space to work, and more people in close quarters,” says WorkSafe’s regulatory support manager, Catalijne Pille.
In response to the incident, Trevelyan’s has committed to delivering a series of safety initiatives worth half a million dollars, including:
• An AI pedestrian detection system fitted to 40 forklifts to improve safety and
reduce risks.
• Collaborating with the kiwifruit industry to spread the uptake of this technology and enhance safety.
• Investing in training to improve health and safety competency across the business.
• Reparation to the victim.
• Funding for the Amputee Society of Waikato, Bay of Plenty and Districts.
• Funding scholarships for the Health and Safety Association of New Zealand.
“Artificial intelligence brings significant possibilities for health and safety innovation. In this case, it’s about using algorithms and sensors to detect nearby pedestrians to reduce the risk of accidents and enhance workplace safety. We hope to see the benefits extend beyond the kiwifruit industry,” says WorkSafe’s Catalijne Pille.
As a result of the undertaking, WorkSafe’s charges against Trevelyan’s were discontinued.
WorkSafe will regularly monitor progress on the agreed initiatives and can resume prosecution if necessary.
“Trevelyan’s investment to improve safety in their workplace is the preferred solution in this case. It demonstrates a substantial commitment to health and safety which may not have been achieved by prosecution.”
Read the decision document
Read more about worksite traffic management
Statement from the forklift incident victim
My life changed in one second on 25 April 2022. Since then, everyday tasks like dressing, showering, and walking have become challenging. My mental health has been up and down, it is physically difficult for me to play with my grandchildren, and
not want anybody else to go through my experience.
Statement from Trevelyan’s Pack and Cool Limited managing director James
Trevelyan
Trevelyan’s Pack and Cool Limited acknowledges the importance of learning from the accident and is committed to ensuring that such incidents do not reoccur.
Trevelyan’s Pack and Cool Limited is not only committed to investing in the health and safety of our workforce and the broader industry, but also in actively supporting the injured person and his family. We are dedicated to building robust capability in the New Zealand workforce, with a specific focus on the prevention of forklift accidents.
An example of implementing improvements includes installing artificial intelligence (AI) equipment in our forklifts. While this AI system is in use in other industries across New Zealand, Trevelyan’s is the first within the kiwifruit industry to have trialled and fitted the equipment to its fleet. As part of our EU commitment, we have also funded another 60 pieces of equipment for other postharvest facilities across the remainder of the industry.
sometimes even lying in bed is painful. My injury had a very bad effect on my retirement savings, as I’d planned to work for another five or ten years, but I’ve not been able to. I didn’t want to tell my story in court, but I’m pleased to see Trevelyan’s invest in making its site safer as I do
Trevelyan’s Pack & Cool Limited places the highest priority on the health and well-being of all Trevelyan’s staff, growers, suppliers, and community. This commitment not only reflects our obligations under the Health & Safety at Work Act 2015 but is also a testament to our genuine concern for each individual associated with us.
PCBU means a
A PCBU must, so far as is reasonably practicable, provide and maintain a work environment that is without health and safety risks. The work environment includes:
• the physical work environment, including lighting, ventilation, dust, heat and noise
• the psychological work environment, including overcrowding, deadlines, work arrangements (eg the effects of shift-work and overtime arrangements) and impairments that affect a person’s behaviour, such as work-related stress and fatigue, and drugs and alcohol.
PCBUs are responsible for providing and maintaining
a
Most New Zealand businesses, whether large corporates, sole traders, or self-employed, are classed as PCBUs.
safe plant and structures. This includes machinery, vehicles, vessels, aircraft, equipment (including personal protective equipment), appliances, containers, implements, tools, buildings, masts, towers, frameworks, pipelines, quarries, bridges, underground works (including shafts and tunnels) and any component of one of these items or anything fitted or connected to one of these items. PCBUs must also ensure the safe use, handling and storage of plant, structures and substances.
Providing safe systems of work is also a PCBU’s responsibility, as is providing any information, training, instruction or supervision that is necessary to protect
all persons from risks to their health and safety which may arise from the work of the business.
It is also a PCBU’s job to monitor the health of workers and the conditions of the workplace.
Another responsibility of a PCBU is to provide adequate facilities for the welfare of workers when doing work for the business, including ensuring access to those facilities. This also applies to providing healthy and safe worker accommodation when appropriate.
Click here for more information.
PCBUs that fail to meet their health and safety obligations are putting people at risk and can face prosecution. The following are recent examples of health and safety failures by PCBUs and the resulting consequences.
Fine: $350,000 | Reparation: $141,502.12 | Max Fine: $1.5m
Trade Depot has been ordered to pay out almost $500,000 after it was found no plan was in place to keep pedestrians and moving vehicles separate
The customer was waiting to collect whiteware from the customer collections area outside Trade Depot in Onehunga, when she was struck by a forklift in August 2022. The 68-year-old was rushed to hospital with injuries so severe her left leg had to be amputated below the knee.
WorkSafe charged Trade Depot after finding it had no effective traffic management plan to ensure moving vehicles and pedestrians were kept separate.
In addition, WorkSafe investigators found that the lights on the forklift were not functioning at the time of
incident.
“It is only by sheer luck that a serious injury or death was not caused before this incident. Forklifts were moving in and around pedestrians, delivering goods on a daily basis, but the site lacked any adequate systems to manage the risk of interaction between forklifts and pedestrians in the customer collections area,” says WorkSafe’s area investigation manager, Paul West.
“One-way systems, barriers, designated crossing points, and speed bumps or signage are among the measures that could have
avoided this unfortunate injury. All businesses whose work requires traffic management should take notice of this case to ensure they aren’t falling short.”
In response to this incident, WorkSafe immediately issued two improvement notices to ensure a barrier was put between the pedestrian pathway and vehicles at the Onehunga site, and to ensure procedures were in place for forklifts operating near pedestrians. Both notices were complied with.
“Forklifts are a known risk – many people have died or been injured by forklift
incidents, yet it’s clear the risks are not being appropriately managed in many workplaces. Risk assessment should consider anybody who could be harmed – which includes both workers and customers, and businesses must not lose sight of that,” says Paul West.
Read WorkSafe’s guidelines on managing work site traffic
Read about a 2016 WorkSafe prosecution of Trade Depot
Fine: $180,000 | Reparation: $110,000 | Max Fine: $1.5m
When there is no obvious safe way to work, it’s best to stop, reassess, and involve experts to develop a new approach – rather than attempting to adapt things on the fly, says WorkSafe’s area investigation manager, Danielle Henry
The death of a 21-year-old in the construction sector shows how easily stopgap measures can endanger workers.
Aidan Paszczuk was removing steel beams when one fell and killed him at a Newmarket construction site in October 2021.
A WorkSafe investigation found that workers devised an ad-hoc way to get the job done when their original method could no longer be used. Unfortunately, they did not have access to safetycritical information about the security of the 500-kilogram beam. When Mr Paszczuk stood on a stack of five
wooden forklift pallets to use an angle grinder, the beam fell on him.
The employer Grouting Services Limited (GSL) should have carried out an effective risk assessment to protect workers, and has now been sentenced for its health and safety failures. Not stopping for a short amount of time to come up with an alternative safer method cost a family their loved one, and affected productivity on a major construction worksite for days and weeks afterwards. Getting workers home healthy and safe must always be the top priority,
especially on fast-moving and dynamic construction sites.
A separate WorkSafe prosecution against CLL Service and Solutions Limited involved a crane toppling at the same busy Newmarket construction site a year prior to the death of Aidan Paszczuk. Sadly, the crane incident was not heeded as the site safety warning that it could have been. The risk of serious harm and death in the construction sector is well known, and WorkSafe is committed to ensuring businesses uphold their responsibilities for worker
health and safety.
Read more from WorkSafe on construction safety
‘Not the place for childcare’: forklift hits five-year-old
Fine: $7,000 | Reparation: $25,000 | Max Fine: $1.5m
A workplace has been fined $7,000 after allowing an underage driver to get behind the wheel of an unsafe forklift whilst a young boy was left unsupervised
When childcare fell through, the boy was taken to the orchard in January 2022 by his grandparents who worked there. He was told to stay inside the packhouse on a couch. Unfortunately, he wandered from that spot and into the path of a reversing forklift being driven by a 14-year-old worker.
The victim survived but suffered significant complex fractures to his hip bones and was hospitalised for a month. The orchard owner has now been sentenced for health and safety failures. A WorkSafe investigation found the victim was under limited supervision as
the caregivers were busy working. The forklift was poorly maintained with no basic safety features like reversing lights, mirrors, flashing lights, or a horn.
The driver was underage, and the site had no written traffic management plan for forklift use.
“Naturally children want to explore, try new things, and push boundaries. As we head into the holiday season, this case is a reminder that children are always at risk on worksites and should not have been present,” says WorkSafe’s area investigation manager, Paul Budd. It was common for the
young driver to be behind the wheel, and the owner had not done enough to establish his age.
Businesses must remember that workers under 15 are not allowed to drive vehicles on worksites.
Risk management by the business was verbal and informal because of language barriers.
“It’s not good enough to say that your risk management is verbal because employees cannot always read English. Translating your safety information for workers, if necessary, goes a long way to keeping them safe.”
“Better traffic management would also have made a
big difference to safety. This could have included exclusion zones to separate vehicles from people, the use of barriers when operating the forklift, clear signage, and separate entry and exit points for people and vehicles,” says Paul Budd.
Children are now prohibited from the orchard during operating hours, and the victim has made a full recovery.
Read more about young people in the workplace
Fine: Inspire Building: $30k | Thorne Group: $210k
WorkSafe New Zealand is calling on the construction sector to “up its game” after a teenager was killed just four months into his apprenticeship
Ethan Perham-Turner was killed when timber framing weighing 350 kilograms fell on him at a residential building site in Ōmokoroa in March 2022. The 19-year-old was just four months into an apprenticeship with Inspire Building Limited at the time. A WorkSafe investigation found the risk was heightened by the framing being manually installed around the site, and a temporary support brace being removed just prior to the fatal incident. When one frame knocked another, it fell on the teenage apprentice.
Inspire was providing building labour for the main contractor, Thorne Group. Both were charged for health and safety failures in relation to the death. The businesses should have consulted each other on the framing installation plan, and ensured a mechanical aid (such as a Hiab crane truck) was used.
“The death of a worker so young is an indictment on the construction sector. Ethan was new to the job, and new to the task of manoeuvring framing. He should have been provided with what he needed to be
safe,” says WorkSafe’s area investigation manager, Paul West.
“The safest way would have been to mechanically lift the framing into place, given its weight. This can come at little to no extra cost. In this case, the supplier delivering the framing had a Hiab and could have lifted it into place if asked.
“The high number of deaths and injuries tell us construction is a very dangerous industry.
WorkSafe has seen other similar incidents where workers handling large or heavy frames
have been paralysed or killed. It is unacceptable that companies are not identifying the risks and providing workers with a safe workplace. We can only hope the death of a very young apprentice might motivate the step change required to improve the sector’s health and safety performance,” says Paul West.
Read safety alert on installing frames
Expanding government-industry partnerships to help business operators should be a no brainer. Inviting enquirers to read the regulations falls well short of educational expectations
Barry Dyer Chief Executive Responsible Care NZ
Today, chemical suppliers and their customers continue to adjust to the Covid operational environment.
They struggle with supply chain delays, the loss of experienced staff, frustration with unanswered queries to risk-averse authorities, inflexible and prescriptive regulations, rising compliance costs, diminishing resources and increasing public chemical safety expectations.
While 130,000 businesses are reportedly captured by the Hazardous Substances and Major Hazard Facilities regulations, the official mantra of “600-900 persons seriously harmed each year by unwanted exposure to chemicals in their workplace” presumably applies to all of the country’s 530,000 workplaces.
Increasing community concerns about vulnerability to unwanted chemical exposure and damage to our fragile environment places additional pressure on both suppliers and users of the chemicals.
We all need to sustain and improve our quality of life and these products must be safely managed throughout their life cycle.
Downgrading the flawed but effective HSNO Certified Handler requirement has inadvertently undermined an invaluable capability.
The action deprived businesses, particularly SMEs, of an immediate and recognisable source of workplace chemical safety and compliance advice -- a safe chemical handling capability and emergency response knowledge – critical when a chemical incident occurs.
PCBUs and SMEs must now devise their own solutions to ensure employees are competent to safely handle the chemicals with which they work.
Chemical industry leaders are moving away from relying on lagging indicators of safety performance in favour of identifying safer work practices and work-
places, by responding to workers’ suggestions about improvements.
Conscientious business operators can add value by sourcing accurate, cost-effective workplace chemical safety advice and compliance tools from their suppliers, industry partners and Responsible Care NZ.
A proven strategy is government agencies collaborating with proactive industry associations to best achieve workplace safety aspirations. The problem is that SMEs rarely join associations.
However, they all obtain their chemical requirements from suppliers and can benefit from product stewardship advice and cost-effective industry compliance initiatives.
Responsible Care NZ extols less regulation in favour of enabling business operators to be increasingly self-sufficient, using cost-effective products and services such as site compliance assessments and specialist training.
The focus is keeping people safe around the chemicals we encounter every day by adding value to businesses.
Responsible Care is a global voluntary chemical industry initiative developed autonomously by the chemical industry for the chemical industry.
Chemical suppliers continue to help customers achieve workplace chemical safety aspirations through product stewardship initiatives.
To help solve the in-house chemical compliance dilemma in New Zealand, Responsible Care NZ delivers specialist and cost-effective Certified Handler standard training, complete with a certificate.
Responsible Care NZ site compliance assessments are non-threatening, effectively capturing and assessing chemical safety performance in a variety of workplaces.
+64 4 499 4311 info@responsiblecarenz.com www.responsiblecarenz.com
The success of Rapid Facility Services is driven by a team that combines experience, commitment and a professional skillset that covers every aspect of facilities management with personal service
The team was forged by three friends working in the industry who realised that the key thing stressed building managers, business owners and landlords needed was to make a single call and get a reliable and qualified support team that would cover any aspect of facilities management.
The Rapid trio set down a business philosophy that “we will do what others can’t or won’t do “ and set about assembling a highly trained, efficient and safety-conscious team of professionals who get the job done right, the first time.
Today that service stretches from food manufacturers’ audit cleaning, all aspects of industrial cleaning, painting, building and floor safety management to anti-microbial and moss
Having worked in the industry for many years, three friends, Paul Schoch, Robyn Schoch and Andrew Chan realised that by combining their skills, they could create a company unlike any other
and mould treatments to prevent surface damage to roofs, ceilings, walls, floors and specialised equipment.
From 1 November this year, new Building Code rules come into effect around smoke alarms – both builders and homeowners need to be thinking ahead and, in some cases, starting to address the changes, says Jared Dinneen, NZ Country Leader, Home & Distribution Schneider Electric New Zealand
Mid-winter is peak house fire season. It only takes three minutes for a house fire to claim lives, and good working smoke alarms are essential. More so as New Zealand’s housing density and population grows, and extreme weather events roll in.
From November 1, it will
be mandatory for all new homes to have a Type 1 Smoke Alarm System. This system consists of interconnected smoke alarms strategically placed in all bedrooms, living spaces, hallways, and landings on every level of the home, providing early fire alerts to occupants. If one smoke alarm in a
room detects a fire, all the smoke alarms in that house will activate and sound an alarm – helping occupants escape. Requiring these alarms in all new builds will go a long way towards protecting families from potential fire hazards. Previous versions of acceptable solutions and verification methods will
no longer be deemed to comply with the Building Code. For new buildings, a hard-wired interconnected smoke alarm system can be installed during construction while the house is being wired. For those who wish to upgrade to the new Building Code requirements while renovating an
existing building, there is a battery-operated, wireless interconnected smoke alarm system which enables safety improvement and compliance without rewiring the home. Note that the wireless interconnected system is also a compliant option for new buildings.
Builders need to incorporate the new Building Code regulations as soon as possible. Moving forward, builders and homeowners alike need to stay on top of the new requirements, install compliant smoke alarms, and perhaps be mindful of 5 myths.
Smoke alarms tend to be obtrusive.
These days, good smoke alarms are designed to blend in seamlessly. They have sleek, low-profile and modern designs that merge stylishly into the ceiling to complement existing interior décor, and they can be the same size as most LED lights.
Myth 2
Smoke alarms are all about sound.
Ongoing innovation means that smoke alarms have become more effective in saving lives. Some models combine an alarm with smart home functions.
Features can include lights turning on when smoke is detected (an extra safety measure for very young or elderly occupants, or those who may not be able to hear an alarm), and push notifications to smart devices. Through an app, test reminders (like the emergency alarm alerts sent to your phone) can be sent at regular intervals to prompt alarm system tests.
Along with ensuring regulatory compliance, smoke alarms need to be installed properly, tested, and maintained. Electricians can benefit from purchasing smoke alarms with features that make installation easier. For example, ample wiring space and large terminals make for easy installation and maintenance.
With some wireless lithium battery powered products, installation is as easy as using a few screws. They can be installed by a registered electrician or by the homeowner or occupant – and with the lithium battery backup options, homeowners won’t need to remember to replace the battery, providing added peace of mind.
Dust or insects in the sensing chamber of a smoke alarm can lead to false alarms and failure. With new builds, it’s critical to leave the dust covers on until after construction and cleaning. Many smoke alarms returned by customers have no faults, but they are full of “Gib“ dust.
All smoke alarms have a limited-service life of 10 years. After that period, the entire smoke alarm unit must be replaced with a new one. If homeowners aren’t sure, they should contact a registered Master Electrician to provide guidance.
Quest Apartment Hotels has opened its fourth Christchurch property as it continues to grow its portfolio in New Zealand and Fiji
Located at 93 Kilmore Street, Christchurch, Quest on Kilmore is opposite the Christchurch Town Hall. A quick walk to the restaurant strip of Oxford Terrace, Quest on Kilmore offers its guest’s a central location. As well as the 42 rooms, Quest on Kilmore has a meeting room that can easily cater to 20 people.
With Quest on Kilmore being its 43rd property in its New Zealand and Fiji portfolio, Quest Apartment Hotels (NZ) continues to defy economic challenges, Chief Operating Officer Adrian Turner says. This growth has been
planned for a while and there will be more to come, he says.
“The opening of Quest on Kilmore in Christchurch is the last of the four properties we have planned for Christchurch. It will support Quest Cathedral Junction, Quest on Manchester and Quest on Cambridge and provide much needed inventory for the Christchurch market especially since the opening of Te Pae, Christchurch’s new convention centre.
“We are already seeing many advance bookings from both our existing corporate clients as well
as our new clients to experience the Quest boutique apartment hotels.”
Operated by Aaron and Lucie Carpenter, Aaron was the Commercial Manager at Quest Corporate Office who had been with Quest for nearly 11 years and the couple are really looking forward to opening this new property.
“I have been with Quest since 2013. I was the Commercial Manager at Quest Corporate Office and when an opportunity came up of the possibility to take on a brand-new property, we knew we wanted to do that, and the rest is history,” says Aaron.
“I am trying to get my head around being on the other side of the business now and we have lots to learn but we are very excited for what is to come. We look forward to strengthening the Quest network in Christchurch and nationwide and working closely with the other Quest properties in Christchurch.
“We are currently in the process of getting set up and plan to provide a great stay with exceptional customer service to guests. We will be ready to welcome you very soon” says Aaron Carpenter.
E v e r y p e r s o n , e v e r y c a n c e r
895,115 Kms driven to get people to appointments
46,600 Bed nights for people receiving treatment 5,742 People attending supportive care programmes
0 8 0 0 C A N C E R ( 2 2 6 2 3 7 )