
13 minute read
Posadzki żywiczne – trwałe i estetyczne wykończenie podłogi
70 mgr inż. Maciej Rokiel Pod pojęciem podłogi należy rozumieć wykończenie poziomej przegrody konstrukcji nadające jej wymagane właściwości użytkowe. Są to zatem warstwy hydroizolacyjne, paroizolacja, izolacje termiczne i akustyczne, warstwy ochronne, nośne (betony, jastrychy), dobrane dla konkretnego przypadku w sposób zależny od obciążeń, rodzaju pomieszczenia i związanych z tym wymagań użytkowych. Posadzka natomiast to wierzchnia warstwa podłogi przenosząca na warstwy konstrukcji obciążenia użytkowe i/lub zabezpieczająca przed zniszczeniem.
Rozwiązanie konstrukcyjne będzie różne w zależności od obciążeń i miejsca wbudowania (warunków eksploatacyjnych). Rodzaj zastosowanych materiałów zależy przede wszystkim od rodzaju pomieszczenia i obiektu, sposobu obciążenia, obecności i rodzaju agresywnych związków, sposobu użytkowania pomieszczenia, dodatkowych wymagań sanitarnych itp. (rys. 1).
Advertisement
1 8
6
4
2
Rys. 1. Ogólny układ warstw podłogi na gruncie: 1 –warstwa przerywająca podciąganie kapilarne – żwir płukany 8–16 mm, 2 –folia PE lub membrana kubełkowa, 3 –konstrukcyjny beton podkładowy, 4 –hydroizolacja, 5 –termoizolacja, 6 –warstwa ochronna – chemoodporna membrana zgrzewana lub sklejana na zakładach, 7 –beton nośny, 8 –posadzka żywiczna Rys. autor
Podstawowym warunkiem długotrwałej, bezproblemowej eksploatacji posadzki jest przyjęcie technicznie poprawnego rozwiązania materiałowego związanego nie tylko z samą posadzką, lecz także z warstwami konstrukcji podłogi. Chodzi tu nie tylko o zdolność do przeniesienia obciążeń użytkowych (mechanicznych – od nacisku kół, sił powstałych przy hamowaniu, dynamicznych, od uderzeń, termicznych, np. w chłodniach czy na parkingach otwartych, chemicznych itp.), lecz także o bezpieczeństwo użytkowania, zabezpieczenie wód gruntowych przed przedostaniem się do nich agresywnych substancji (jeżeli występują), odpowiednią izolacyjność termiczną oraz akustyczną, odporność na starzenie czy wreszcie łatwość w utrzymaniu w czystości. Z tym wiąże się także konieczność wykonania tzw. trudnych i krytycznych miejsc, takich jak dylatacje czy wpusty, jak również uwzględnienie zjawisk związanych z ruchem wilgoci przez przegrodę, których zaniedbanie także może prowadzić do powstania uszkodzeń.
Rodzaje posadzek żywicznych, właściwości i zastosowanie
Rozwiązań materiałowo-konstrukcyjnych samych posadzek jest wiele, jednak najczęściej wykonuje się posadzki betonowe oraz żywiczne, jak również z płytek ceramicznych. Posadzki żywiczne najczęściej są wykonywane na bazie syntetycznych spoiw: » epoksydowych, » poliuretanowych, » polimocznikowych, » epoksydowo-poliuretanowych. Poprawne wykonanie posadzki przemysłowej wynika z dobrania odpowiedniego rodzaju zabezpieczenia (impregnacja, posadzka cienkowarstwowa/grubowarstwowa itp.) do występujących obciążeń. Chodzi tu przede wszystkim o obciążenia mechaniczne, chemiczne, termiczne, promieniowanie UV itp. To z kolei wymaga znajomości właściwości, którymi cechują się możliwe do zastosowa
nia w tych warunkach żywice syntetyczne. W zależności od bazy (epoksyd, poliuretan, akryl itp.), parametry i cechy stwardniałych powłok będą różne, zależne także od grubości powłoki [1–5].
Cechą żywic epoksydowych jest wysoka odporność mechaniczna (wytrzymałość na ściskanie rzędu 40–90 N/mm 2 , na zginanie rzędu 20–40 N/mm 2 , na rozciąganie rzędu 12–20 N/mm 2 ), twardość i odporność na ścieranie, uderzenia czy zarysowania. Z tym wiąże się jednak sztywność powłoki. Sam proces sieciowania i twardnienia, zwłaszcza przy stosowaniu kruszywa kwarcowego jako wypełniacza, przebiega z minimalnym skurczem. Są mniej wrażliwe na wilgotność resztkową podłoża i wysoką wilgotność powietrza podczas aplikacji i twardnienia niż żywice poliuretanowe.
Zaletą żywic epoksydowych jest odporność na agresywne media – zarówno kwaśne, jak i alkaliczne. Są odporne na roztwory kwasów nieorganicznych i organicznych (z wyjątkiem fluorowodorowego i octowego), roztwory soli nieorganicznych i wodorotlenków oraz na materiały pędne i smary. Ograniczoną odporność wykazują na substancje utleniające (chlor, kwas azotowy), alkohole (np. metanol), estry (np. octany butylu), ketony czy węglowodory. Poza tym epoksydy są odporne na wpływy atmosferyczne, a jedynym ich mankamentem jest skłonność do żółknięcia i kredowania pod wpływem promieniowania UV. Nie wpływa to jednak negatywnie na parametry użytkowe powłoki [1].
Dwuskładnikowe żywice poliuretanowe, podobnie jak epoksydowe, wiążą z minimalnym skurczem. W przeciwieństwie do epoksydowych są jednak elastyczne, mają zdolność mostkowania rys podłoża oraz są bardziej odporne na uderzenia i to w niskich temperaturach. Są także odporne na promieniowanie UV oraz na starzenie. Ich parametry wytrzymałościowe są jednak niższe niż epoksydów, dotyczy to zwłaszcza odporności na ścieranie (wytrzymałość na rozciąganie rzędu 2,2–3,5 N/mm 2 , wydłużenie względne przy rozciąganiu do 160%).
Jeśli chodzi o odporność chemiczną, są odporne na paliwa (materiały pędne), sma
ry, rozcieńczone kwasy i zasady, jak również na oleje, tłuszcze, aromatyczne węglowodory i estry. Są mniej odporne na stężone zasady, zwłaszcza w podwyższonych temperaturach, oraz na ketony [1].
Jednoskładnikowe żywice poliuretanowe są generalnie odporne na paliwa (materiały pędne), smary, rozcieńczone kwasy i zasady. Są niewrażliwe na wpływy atmosferyczne. Właściwością przypisaną wszystkim poliuretanom jest ich wrażliwość na wilgoć w podłożu, jak również wysoką wilgotność względną powietrza. Dotyczy to zarówno momentu aplikacji, jak i procesu sieciowania. Wymaga to szczególnej ochrony (do momentu stwardnienia) przed oddziaływaniem wilgoci.
Spotyka się także żywice będące swoistymi hybrydami, np. epoksydowo-poliuretanowe. Wykazują one cechy właściwe zarówno epoksydom, jak i poliuretanom, np. elastyczność w połączeniu z odpornością na ścieranie.
Żywice polimocznikowe z kolei cechują się wysoką odpornością mechaniczną przy znacznej elastyczności i zdolności przekrywania rys (wydłużenie przy zerwaniu może dochodzić do 400%, a wytrzymałość na rozciąganie do 20 MPa), odpornością termiczną w suchym środowisku do temperatury 120–180°C, a w wilgotnym do 80°C i wysoką odpornością chemiczną (roztwory kwasów organicznych o stężeniu rzędu 10%, roztwory kwasów nieorganicznych o stężeniu do 20% oraz ich sole w roztworze o wartości pH < 6, zasady nieorganiczne i ich sole o pH > 8 oraz roztwory soli nieutleniających się pochodzenia nieorganicznego o pH rzędu 6–8). Posadzkowe żywice epoksydowe są najczęściej dwuskładnikowymi kompozycjami składającymi się z ciekłej żywicy epoksydowej, modyfikatorów i wypełniaczy mineralnych oraz ewentualnie rozcieńczalników (składnik A), a także z utwardzacza (aminy alifatyczne, aromatyczne, cykloaminy itp.). Jednoskładnikowe żywice poliuretanowe składają się z poliuretanowej żywicy z dodatkiem modyfikatorów, mineralnych wypełniaczy i pigmentów, ewentualnie organicznych rozcieńczalników. Kompozycje dwuskładnikowe składają się z poliuretanowego spoiwa, mineralnych wypełniaczy i pigmentów z dodatkiem modyfikatorów, ewentualnie rozcieńczalników organicznych (składnik A). Utwardzaczem (składnikiem B) jest związek poliizocyjaninowy. Podstawą kompozycji poliuretanowo-epoksydowych są żywica epoksydowa modyfikowana poliuretanami, mineralne wypełniacze i pigmenty, plastyfikatory i inne modyfikatory (składnik A). Utwardza
czem (składnikiem B) jest modyfikowany związek aminowy.
Kompozycje żywic poliuretanowych i/lub epoksydowych służą do wykonywania posadzek typu: » powłokowego – grubość kompozycji żywicznej rzędu 0,5–1 mm, » wylewanego – grubość kompozycji żywicznej rzędu 1,5–4 mm, » szpachlowego – grubość kompozycji żywicznej rzędu 3–25 mm (m.in. ze względu na cenę stosowane są najrzadziej). Inne kryterium podziału to: posadzki cienkowarstwowe, posadzki grubowarstwowe czy wręcz powłoki lakiernicze.
Posadzki powłokowe wykonuje się w pomieszczeniach nienarażonych na intensywne obciążenia ruchem kołowym i przy słabym lub ograniczonym oddziaływaniu agresywnych mediów. W praktyce są to obiekty budownictwa ogólnego (lub użyteczności publicznej), w ograniczonym stopniu tego typu posadzki wykonuje się w budownictwie przemysłowym. Posadzki wylewane epoksydowe stosuje się w budownictwie przemysłowym, użyteczności publicznej i budownictwa ogólnego, dla wysokich obciążeń mechanicznych i przy obecności agresywnych mediów. Żywice poliuretanowe w tego typu posadzkach stosuje się tam, gdzie jest konieczność użycia materiału elastycznego, należy jednak pamiętać, że odporność poliuretanów na oddziaływanie agresywnych substancji chemicznych jest mniejsza niż odporność epoksydów. Z drugiej strony żywice epoksydowe są w znacznie mniejszym stopniu odporne na UV, nie tracą wprawdzie swych właściwości, jednak w wielu sytuacjach ważny jest aspekt estetyczny.
Spotyka się także żywice poliuretanowo epoksydowe, cechujące się większą odpornością mechaniczną i chemiczną niż posadzka poliuretanowa przy pewnej elastyczności, czego z kolei pozbawiona jest posadzka epoksydowa.
Posadzki szpachlowe stosuje się przy bardzo ciężkich warunkach eksploatacyjnych i przy oddziaływaniu bardzo agresywnego środowiska.
Parametry i właściwości użytkowe dostępnych na rynku żywic syntetycznych pozwalają nie tylko uzyskać warstwę użytkową odporną na ekstremalne obciążenia mechaniczne i chemiczne, ale umożliwiają też wykonanie posadzki przy braku przeciwwilgociowej izolacji konstrukcji posadzki oraz na podłożach mokrych i zaolejonych, bez obaw o niebezpieczeństwo późniejszego odspaja
nia się żywicznej warstwy użytkowej. Jest to bardzo istotne przy remontach i naprawach uszkodzonych posadzek przemysłowych.
Systemy posadzek cienko-/grubowarstwowych składają się z: » gruntownika, » warstwy pośredniej, » warstwy zamykającej (lakierowania), przy czym wykonanie warstwy zamykającej może być opcjonalne, zatem warstwa pośrednia jest warstwą użytkową. Możliwa jest jednak sytuacja, że warstwy użytkowe są bardziej rozbudowane.
Na świeżej warstwie żywicy gruntującej wykonuje się posypkę ze specjalnego piasku kwarcowego przeznaczonego do żywic. Jego uziarnienie wynosi zazwyczaj 0,2–0,7 mm, a po związaniu gruntownika nadmiar piasku usuwa się. Na tak przygotowaną warstwę gruntującą nakłada się, warstwą o określonej grubości, materiał będący właściwą powłoką ochronną. Jeżeli nie jest wymagana antypoślizgowość czy nadanie specyficznego wyglądu (matowego, z połyskiem), wykonanie posadzki można uznać za zakończone. W przeciwnym wypadku konieczne jest przelakierowanie specjalnymi żywicami (zazwyczaj poliuretanowymi, jednoskładnikowymi lakierami). Dla wersji antypoślizgowej świeżo nałożoną żywicę trzeba posypać piaskiem kwarcowym lub korundem, o określonym uziarnieniu, zależnym od wymaganej klasy antypoślizgowości i przestrzeni wypełnienia, a po usunięciu niezwiązanego piasku, wykonać lakierowanie zamykające.
Epoksydowe żywice do wykonywania powłok grubowarstwowych mogą być mieszane z piaskiem do żywic (takim samym jak do wykonywania posypki). Zwiększa to odporność związanej żywicy na obciążenia mechaniczne (oraz zmniejsza koszt materiału), może jednak wpływać negatywnie na odporność chemiczną. Proporcje mieszania podaje zawsze producent systemu (wagowo mogą się one wahać od 0,5 do nawet 2 części piasku na 1 część żywicy). Im większa ilość dodawanego piasku, tym gorsza rozlewność masy. Występują tu także ograniczenia polegające na konieczności wykonania warstwy o podanej przez producenta minimalnej grubości.
Żywice poliuretanowe często stosuje się jako posadzki na parkingach, wykończenie powierzchni balkonów oraz wszędzie tam, gdzie konieczne jest zastosowanie elastycznej, mostkującej rysy powłoki.
Do żywic poliuretanowych piasku z reguły się nie dodaje. Co prawda niektórzy produ-
cenci w kartach technicznych dopuszczają taką możliwość, jednak należy do tego podchodzić bardzo ostrożnie. Dodatek piasku do żywic poliuretanowych znacznie pogarsza bowiem ich elastyczność. Dlatego jego ilość nie przekracza zazwyczaj 0,4–0,5 części wagowych.
Uwaga! Powłoka z żywicy poliuretanowej zachowuje elastyczność, gdy jej grubość wynosi przynajmniej 1,5 mm.
Zróżnicowanie systemów posadzek z żywic łatwo przedstawić na przykładzie nawierzchni parkingów. Spotyka się rozwiązania z zastosowaniem żywic poliuretanowych, poliuretanowo-epoksydowych oraz epoksydowych. Wybór materiału zależy od miejsca jego wbudowania (umiejscowienia posadzki – parking odkryty na dachu, parking w ogrzewanej hali, stropy pośrednie itp.).
Najbardziej narażone na oddziaływania mechaniczne oraz warunki atmosferyczne są parkingi na dachach. Oprócz obciążeń dynamicznych dochodzą tu także znaczne obciążenia termiczne (gradient temperaturowy lato–zima dochodzący do 100°C), promieniowanie UV, oddziaływanie środków odladzających oraz paliwa, olejów i płynów eksploatacyjnych. Zastosowany materiał musi cechować się przede wszystkim elastycznością i odpornością na promieniowanie UV, dlatego stosuje się tu żywice poliuretanowe. Grubość warstw użytkowych wynosi zazwyczaj 3–5 mm, najczęściej spotyka się dwa warianty takiej posadzki: pierwszy – na gruntowniku układana jest warstwa elastycznej żywicy poliuretanowej grubości 1,5–2 mm, a na niej druga warstwa (3–4 mm) także elastycznego poliuretanu, lecz o większej odporności na ścieranie oraz drugi wariant – na gruntowniku układa się warstwę elastycznej, lecz odpornej na ścieranie żywicy poliuretanowej (ewentualnie poliuretanowo-epoksydowej) grubości 2–4 mm. W obu przypadkach powierzchnia posadzki musi być szorstka, dlatego świeżą warstwę żywicy należy posypać kruszywem (piaskiem kwarcowym, korundem) o odpowiednim uziarnieniu i przelakierować odpornym na promieniowanie UV lakierem, np. poliuretanowym.
W przypadku parkingów podziemnych lub zakrytych, gdzie nie ma obciążenia zmianami temperatury zamiast żywicy poliuretanowej stosuje się żywicę epoksydową, często z dodatkiem piasku kwarcowego, co zwiększa jej odporność mechaniczną. Warstwa zamykająca (można tu stosować zarówno żywice epoksydowe, jak i poliuretanowe) wykonywana jest także na posypce nadają
cej antypoślizgowość. Konstrukcja ta nie ma możliwości mostkowania rys.
Płyty stropów pośrednich w parkingach otwartych także są narażone na oddziaływania termiczne, jednak nie aż tak duże. Dlatego oprócz żywic poliuretanowych można tu stosować także elastyczne żywice poliuretanowo-epoksydowe. Grubość warstwy nośnej wynosi zazwyczaj 3–4 mm. Konieczne jest również wykonanie lakierowania zamykającego nadającego antypoślizgowość.
Podane grubości warstw są wartościami przeciętnymi, w zależności od obciążeń (samochody ciężarowe, osobowe) mogą być one zwiększone lub zmniejszone, jednak nie bezkrytycznie. Żywice poliuretanowe cechują się zdolnością mostkowania rys, gdy są ułożone w warstwie min. 1,5–2 mm.
Przykładowe warstwy systemów posadzek cienko- lub grubowarstwowych przedstawiają się następująco: » posadzka gładka (rys. 2), składająca się z: –kompozycji gruntującej,
–posypki z piasku kwarcowego (opcjonalnie), –kompozycji podstawowej (czysta żywica lub zmieszana z wypełniaczem – piaskiem kwarcowym), –kompozycji wykańczającej/zamykającej – lakierowania (opcjonalnie); » posadzka antypoślizgowa (rys. 3), składająca się z: –kompozycji gruntującej, –posypki z piasku kwarcowego (opcjonalnie), –kompozycji podstawowej (czysta żywica lub zmieszana z wypełniaczem – piaskiem kwarcowym), –posypki z piasku kwarcowego lub kruszywa korundowego o odpowiedniej frakcji – zależy od wymaganej klasy antypoślizgowości i przestrzeni wypełnienia, –kompozycji wykańczającej – lakierowania zamykającego, Możliwa jest jednak sytuacja, że warstwy konstrukcji są bardziej rozbudowane (rys. 4).
Rys. 2. Posadzka gładka: 1 –podłoże, 2 –gruntowanie, 3 –szpachlowanie w celu wyrównania ewentualnych nierówności podłoża (mieszanina żywicy z piaskiem) lub posypka z piasku kwarcowego, 4 –warstwa użytkowa (czysta żywica), 5 –lakierowanie (opcjonalnie) Rys. KLB Koetztal

Rys. 3. Posadzka antypoślizgowa: 1 –podłoże, 2 –gruntowanie lub gruntowanie i szpachlowanie w celu wyrównania ewentualnych nierówności podłoża (mieszanina żywicy z piaskiem) + posypka z piasku kwarcowego, 3 –warstwa użytkowa (czysta żywica lub zmieszana z wypełniaczem – piaskiem kwarcowym), 4 –posypka z piasku kwarcowego nadająca antypoślizgowość, 5 –warstwa zamykająca Rys. KLB Koetztal Rys. 4a. Dekoracyjna, szczelna dla cieczy posadzka dekoracyjno-przemysłowa: 1 –podłoże, 2 –gruntowanie, 3 –szpachlowanie w celu wyrównania ewentualnych nierówności podłoża (mieszanina żywicy z piaskiem) lub posypka z piasku kwarcowego, 4 –warstwa uszczelniająca (czysta żywica), 5 –warstwa uszczelniająca (czysta żywica – druga warstwa – posypana piaskiem kwarcowym), 6 –warstwa użytkowo-dekoracyjna (czysta żywica posypana kolorowym piaskiem kwarcowym), 7 –warstwa ochronna (bezbarwna żywica), 8 –warstwa zamykająca (np. bezbarwna żywica matująca) Rys. KLB Koetztal
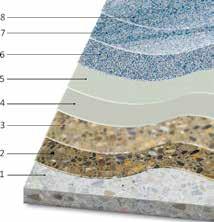
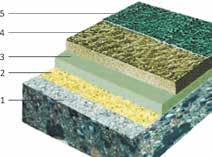
Rys. 4b. Dekoracyjna, elastyczna posadzka przemysłowa na parkingu odkrytym: 1 –grunt, 2 –przepona, 3 –warstwa zasadnicza, 4 –posypka z piasku kwarcowego, 5 –warstwa uszczelniająca Rys. Sika
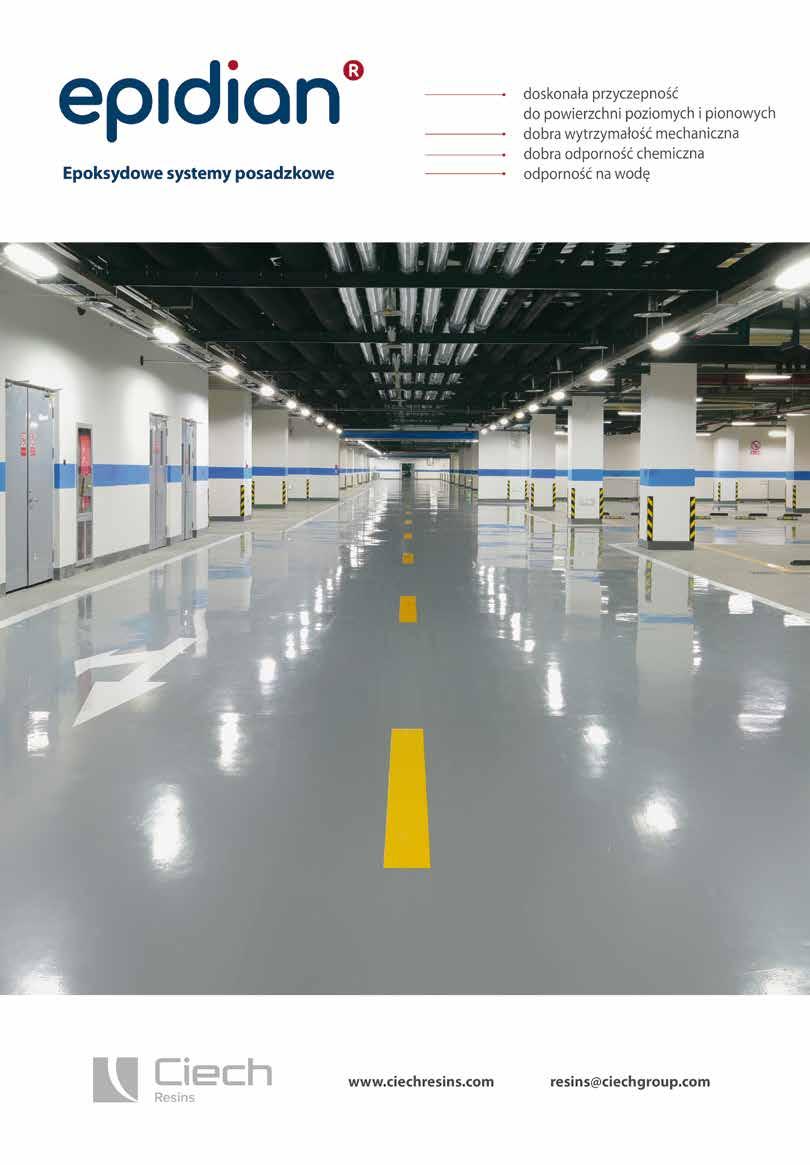
W każdym przypadku trzeba zwrócić uwagę na dyfuzję pary wodnej w przegrodzie i, jeżeli jest to wymagane, odpowiednio zapobiegać negatywnym skutkom (np. przez wykonanie odpowiednich warstw paroszczelnych, wymalowania o dużym oporze dyfuzyjnym, specjalne gruntowniki epoksydowe będące warstwą paroszczelną, stosowanie żywic cechujących się zdolnością do dyfuzji pary wodnej).
Zdolnością odprowadzania ładunków cechują się posadzki antyelektrostatyczne. Taki system może występować w wariancie gładkim lub szorstkim (antypoślizgowym). Podstawą systemu są warstwy przewodzące (taśma, lakier, żywica).
Powierzchniowym zabezpieczeniem posadzki jest również jej impregnacja. Stosuje się tu zazwyczaj epoksydowe impregnaty
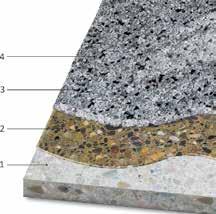
Rys. 5. Posadzka dekoracyjna: 1 –podłoże, 2 –grun towanie, 3 –warstwa dekoracyjna – mieszanina żywicy z barwnym kruszywem, 4 –bezbarwne lakierowanie zamykające Rys. KLB Koetztal Fot. Sika
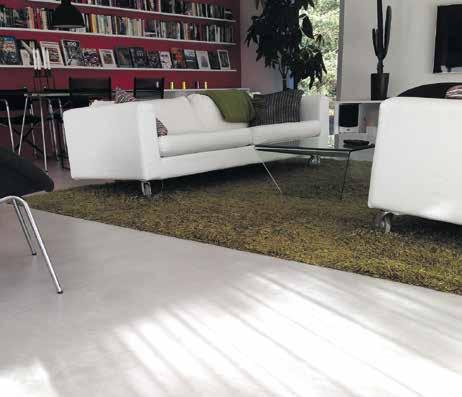
na bazie rozpuszczalników (w porównaniu z preparatami dyspersyjnymi cechują się one większą zdolnością do penetracji w podłoże), choć spotyka się także preparaty bezrozpuszczalnikowe. Efektem jest zwiększenie wytrzymałości na ściskanie i zginanie, zmniejszenie nasiąkliwości, zwiększenie odporności chemicznej oraz poprawa estetyki posadzki. Nie tworzą jednak ciągłej, szczelnej powłoki. Impregnaty mogą być (i często są) stosowane na posypkach utwardzających oraz posadzkach polimerowo-cementowych. Mogą one wówczas pełnić funkcję zarówno ochronną (zapobiegającą zbyt szybkiemu wysychaniu), jak i typowego impregnatu.
Posadzki dekoracyjne Innym rodzajem posadzek są posadzki dekoracyjne (rys. 5). Możliwość aranżacji ich wyglądu jest bardzo szeroka. Począwszy od jednorodnego, błyszczącego lub matowego wykończenia, poprzez zastosowanie barwionego kruszywa czy tzw. chipsów, a skończywszy na efekcie zwanym 3D. Bazą takich posadzek jest zwykle spoiwo epoksydowe i/lub poliuretanowe, spotyka się jednak także posadzki na bazie żywic metakrylowych. Wykonuje się je zazwyczaj jako wielowarstwowe (zależy to od oczekiwanego efektu).
O poprawności rozwiązania technologiczno-materiałowego decyduje nie tylko dobór odpowiednich materiałów do wykonania posadzki, lecz także konstrukcja podłogi. Oznacza to, że na etapie projektowania należy przyjąć poprawny układ warstw całej konstrukcji, jednoznacznie definiując rodzaj zastosowanych materiałów i ich parametry. Począwszy od poprawnego rozpoznania warunków gruntowo-wodnych i określenia niezbędnych parametrów warstwy nośnej (w przypadku podłóg na gruncie), a skończywszy bezpośrednio na warstwie użytkowej (posadzce).
Warstwa betonu nośnego musi umożliwić przejęcie przede wszystkim obciążeń mechanicznych oddziałujących na podłogę. Grubość płyty betonowej i klasa betonu zależą od przewidywanych obciążeń powierzchni (dlatego zawsze podaje je dokumentacja projektowa). Dla obciążenia lekkim ruchem pieszym za minimalną klasę betonu można przyjąć C16/20, przy intensywnym obciążeniu ruchem pieszym lub obciążeniu wózkami na kołach ogumionych będzie to beton klasy C20/25, przy ruchu wózków na kołach stalowych – C25/30, jeżeli do tego dochodzą jeszcze obciążenia udarowe lub ujemnymi temperaturami/szokowe za minimalną klasę betonu można przyjąć beton C30/37.
Literatura 1. BEB Arbeitsblatt KH-0/S Stoffe, 2002. 2. BEB Arbeitsblatt KH-1 KH-1 Imprägnierung, 2009. 3. BEB Arbeitsblatt KH-3 Beschichtung/Belag, 2007. 4. BEB Arbeitsblatt KH-2 Versiegelung, 2004. 5. BEB Arbeitsblatt KH-5 Estrich, 2008. 6. Fussböden In Arbeitsraumen und Arbeitsbereichen mit erhöhter Rutschgefahr, ZH 1/571, IV 1989. 7. PN-EN 1504-2:2006, „Wyroby i systemy do ochrony i napraw konstrukcji betonowych. Definicje, wymagania, sterowanie jakością i ocena zgodności. Część 2: Systemy ochrony powierzchniowej betonu”. 8. ZUAT-15A/III.09/2003, „Zestawy wyrobów do wykonywania posadzek żywicznych”, ITB, 2003. 9. ZURT-15/VIII.24/2008, „Zestawy wyrobów do wykonywania posadzek żywicznych”. 10. PN-EN 13529:2005, „Wyroby i systemy do ochrony i napraw konstrukcji betonowych. Metody badań. Odporność na silną agresję chemiczną”. 11. DIN 51130 2004-06, „Prüfung von Bodenbelägen; Bestimmung der rutschhemmenden Eigenschaft; Arbeitsräume und Arbeitsbereiche mit erhöhter Rutschgefahr; Begehungsverfahren; Schiefe Ebene”. 12. E. Neufert, „Podręcznik projektowania architektoniczno-budowlanego”, Arkady, Warszawa 1995. 13. L. Czarnecki, P.H. Emmons, „Naprawa i ochrona konstrukcji betonowych”, Polski Cement, Kraków 2002. 14. J. Banera, M. Maj, A. Ubysz, „Powłoki polimocznikowe w budownictwie”, Grupa MD, 2017. 15. „Warunki techniczne wykonania i odbioru robót budowlanych. Część B: Roboty wykończeniowe. Zeszyt 3: Posadzki mineralne i żywiczne”, ITB, 2018. 16. „Specyfikacje techniczne wykonania i odbioru robót budowlanych. Posadzki z żywic epoksydowych i poliuretanowych”, Promocja, 2017. 17. M. Rokiel, „Hydroizolacje w budownictwie”, wyd. III, Grupa MEDIUM, Warszawa 2019.
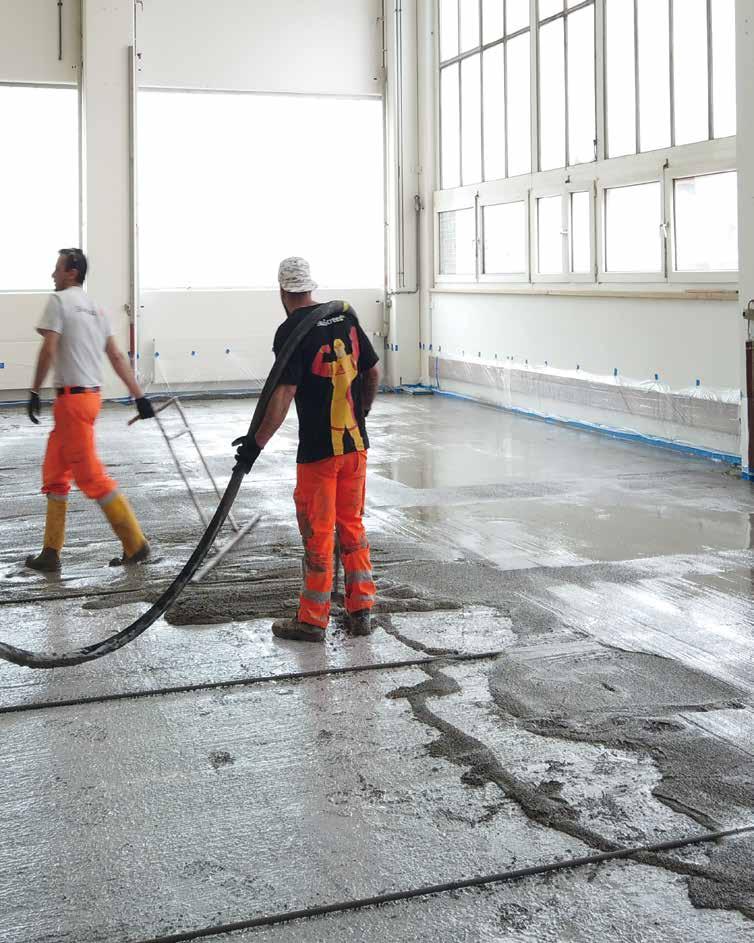
