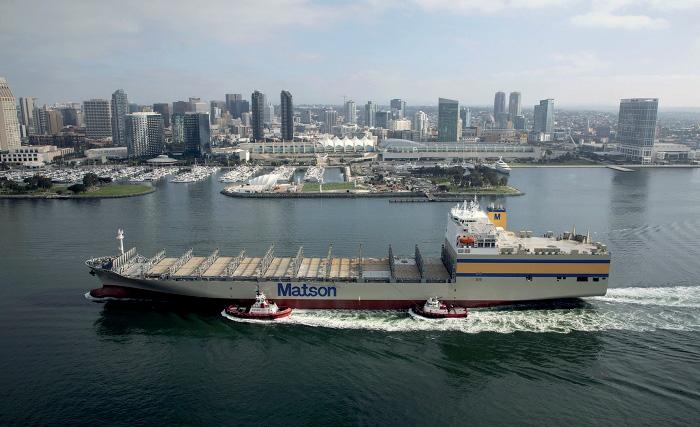
7 minute read
MAN extends 10.6 platform
General Dynamics’ NASSCO yard at San Diego, California, has been central to the past decade’s Jones Act trading fleet revitalisation, but the December 2020 delivery of the second of two 3,500TEU con-ros for Matson Navigation signified the completion of the commercial vessel workload. The production focus has now switched to the contract for six US Navy fleet replenishment tankers, the first of which was launched in January this year.
A new chapter in US shipbuilding is starting through the implementation of a project for the first-ever Jones Act wind farm service operation vessel (WSOV). The newbuild scheme is the outcome of a long-term charter agreement between diversified US company Edison Chouest Offshore (ECO), Danish group Orsted, and US energy firm Eversource, relating to the provision of an SOV for planned wind farms off the north eastern seaboard. The 80m vessel, accommodating up to 70 technicians and other personnel, will be utilised for operation and maintenance activities.
ECO has been in the vanguard of initiatives in the deepwater Gulf of Mexico and Brazilian offshore markets and has grown its shipbuilding network in the USA and beyond. The SOV will therefore not only be run within the ECO fleet but also constructed by the group, utilising the combined resources of yards in Florida, Louisiana and Mississippi. The newbuild will have a diesel-electric installation meeting EPA Tier 4 emission standards and will feature the proprietary ECO variable frequency drive system.
Another milestone was signified by the laying of the keel of a wind turbine installation vessel (WTIV) for Dominion Energy at the Brownsville, Texas, yard of Keppel AmFELS during December. The 144m jack-up type newbuild, the first Jones Act-compliant WTIV in the USA, will carry a 2,200t liftcapacity crane.
Having finally responded to the fleet enhancements effected and planned by potential adversaries, the US acted on its icebreaker renewal strategy by entrusting a US$746 million contract for a 140m polar security cutter to VT Halter Marine. If options on second and third ships are exercised, the cumulative value of the deal would reach US$1.94 billion.
The technological intensity of the project surpasses that of most mercantile vessel projects, and will provide benefits across homeland industry. To be handed over to the US Coast Guard by 2024, the lead polar cutter has been specified with a diesel-electric power and propulsion plant of some 33,700kW, the capability to navigate through ice of 1.8-2.4m, 90 days’ endurance, and accommodation for up to 186 persons.
In addition to design consultancy Technology Associates Inc (TAI), VT Halter has partnered in the project with ABB/ Trident Marine for the adoption of an Azipod propulsion system, Caterpillar for the main engines, Raytheon for command and control system integration, Bronswerk for the heating, ventilation and air conditioning (HVAC), and Jamestown Metal Marine for the joinery package.
The American icebreaker fleet is in a parlous state, with only two polar vessels operational. More than 10 years ago, the High Latitude Mission Analysis Report had identified the need for six new polar icebreakers to cover year-round missions in the Arctic and support the US Antarctic Program.
In April 2020, VT Halter attracted a US$1.7 million grant for a press brake at its Pascagoula yard in Mississippi. The machine will be brought to bear on the polar icebreaker contract, in the plate shaping phases. Recently completed investments have included robotic welding plant and a PythonX plasma cutter. Furthermore, by July 2021, the shipbuilder aims to complete upgrades to the launchway area on which the polar cutter will be laid down.
The paucity of commercial vessel work for the larger yards tends to overshadow the industrial and economic contribution made by, and the challenges facing, the country’s extensive network of enterprises catering to the small-ship end of the market. However, MARAD demonstrated its commitment to continuing a line of support to that sector in January this year through a new tranche of Federal funding under the Small Shipyard Grant Program. Awards under the further US$19.6 million available for yard improvement schemes are to be made by the end of April.
First introduced in 2008, the grants cover capital expenditure and equipment upgrades related to vessel construction, repair and reconfiguration, and to training in technical skills leading to improved efficiency and productivity. Allocations are limited to 75% of estimated costs, and to yards with fewer than 1,200 production employees.
The industry sustains a vigorous and targeted, collaborative R&D agenda through the National Shipbuilding Research Program (NSRP). The cooperation provides a framework to manage, develop and share R&D initiatives and leverage best practices in shipbuilding and shiprepair, through projects typically of 12-month duration. The NSRP schemes are co-funded by 11 yards owned by the eight shipbuilding groups involved together with the US Navy, as the undertaking’s ultimate mission is to reduce total ownership costs and raise the performance of both US-flag commercial ships and US government vessels.
The awards approved by the NSRP’s executive award towards the end of last year spanned 17 projects valued at approximately US$2.5 million, to be undertaken by research consortia encompassing partners from the wider industry as well as NSRP members. The financial allocations by NSRP in each case are relatively modest, in the order of $150,000 per project in the latest schemes.
The broad swathe of practical topics addressed under the latest round included the use of single-pass, buried arc welding to reduce time and costs associated with welding single-sided joints, utilisation of 3D ship model data for corrosion control and coatings, and development of a visual guide for non-ferrous and stainless steel surface preparation. Other research assignments concern automated label plate generation from 3D design models, the evaluation of fusion spliced fibre optic connectors in ship construction, additive manufacturing of seawater heat exchangers, double electrode processes for precision fillet welding, and digital tooling for cable routing and installation.
While heavy reliance on naval construction will remain the industry’s bedrock business, yards are acting on opportunities for specialised civilian projects and emergent sectors within the captive US market.
8 Con-ro Matsonia,
built by General Dynamics NASSCO in San Diego, and one of the few Jones Act mercantile completions in 2020
WINGD’S GALKE CAUTIOUSLY OPTIMISTIC ON 2021 MARKET
Switzerland-based engine designer WinGD is continuing to develop its portfolio, as it positions for a modest recovery in the market in 2021, Volkmar Galke, Global Sales Director, WinGD, told The Motorship during a recent interview
In common with other suppliers to the maritime industry, WinGD had seen the newbuilding market aff ected by global events. However, WinGD fi nished the year strongly, benefi ting from a number of new orders at the end of what was a “roller-coaster” year.
“We ended the year with a 36% share of the global twostroke market, measured by engine capacity - you could say it was a good year at a low level”.
The company benefited from a strong order book for its low-pressure, dual-fuel two-stroke X-DF engines, helped as expanding LNG production capacity translated into newbuild LNG carrier orders.
“We have continued our success in the dual-fuel segment and ended the year with a 59% share of the dual-fuel market.”
The company's low-pressure dual-fuel X-DF engine remains the preferred choice for large gas carriers, which helped WinGD consolidate its strong position with shipowners. “We achieved a 100% share of the market for LNG carriers in 2020,” Galke said.
While the company has continued to increase its sales of X-DF engines, deliveries of the engine are increasing steadily.

Image courtesy of WinGD
The company has now delivered 90 X-DF engines, and its engines have recorded over 850,000 operating hours.
The company had achieved a number of firsts during 2020, including the first deliveries of X-DF engines for two H-Line dual-fuel Newcastlemaxes, as well as the first voyage by CMA-CGM's dual-fuel Jacques Saade now recognised by the Guinness Book of Records as possessing the world's most powerful dual-fuel engine.
“The vessel's engineers have told us that the systems have been running very well. The vessel has made the round trip back to Asia, passing through tropical conditions, and the engines are running fantastically well.”
X-DF 2.0
Galke also noted that the company had received the first order for an engine, an X62DF2.0, featuring WinGD's iCER (intelligent control by exhaust recycling) after the launch of the X-DF 2.0 platform. The solution will reduce methane slip from the engine by more than 40%.
The main driver for continuing innovation was to meet market demand to minimise methane slip from marine
8 WinGD's dual-fuel