
35 minute read
Emissions reduction potential
For NOx emissions, the benefit of the insulated turbocharger turbine is the increase in temperature, especially during warm-up, for the selective catalytic reduction (SCR) catalyst. In the hybrid vehicle system analysed, the electrically heated catalyst uses energy from the battery that could otherwise have been used to propel the vehicle. Using it to heat the catalyst to control emissions could be seen as a parasitic loss, but the insulated turbocharger turbine reduced the amount of heat required for this.
A reduction in fuel consumption could also be achieved during particulate filter regeneration which would therefore require less fuel to raise the temperature of the exhaust. “There will be a further benefit because the NOx aftertreatment can be more effective due to the increase in temperature, so some of the NOx mitigation measures such as late fuel injection and high exhaust gas recirculation rates that usually penalise fuel consumption and increase particulate emissions can be relaxed,” says Burke.
The turbocharger is a primary source of heat loss in the exhaust system, as it is cooled to protect the bearings. This means there is a significant heat loss inherent to the turbocharger that needs to be considered at a system level, says Burke. “Is there a chance that we are creating too much cooling to protect the bearings which is compromising the exhaust emissions? There could be some interesting thermal designs to consider here that try to block heat conduction into the bearing housing.”
He says the research results on the 48V hybrid system open up the potential for new electrical technologies that could reduce emissions including electrically-assisted boosting systems, electrically heated catalysts and electric thermal management systems. It also offers the potential for collecting energy via regenerative braking.
Burke’s research team is focussed on improving the modelling further such that the thermal insulation effects can be characterised accurately from minimal or no test work using higher order models. “This is essential as hardware decisions will be increasingly made based on simulations in the future. It is essential that we can generate suitable models that truly reflect the behaviour of the technology.”
8 Dr Richard Burke,
head of the research team at the Institute for Advanced Automotive Propulsion Systems at the University of Bath




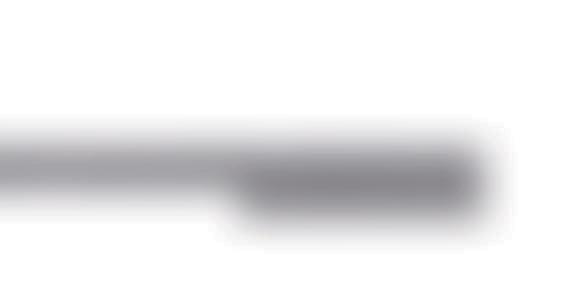
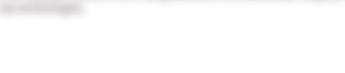




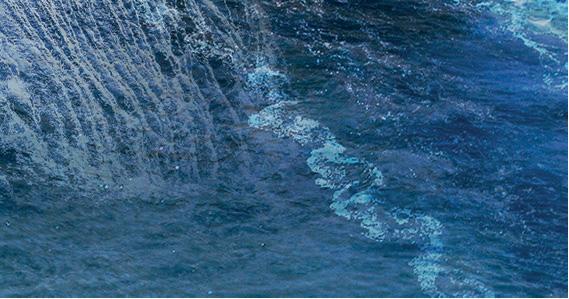




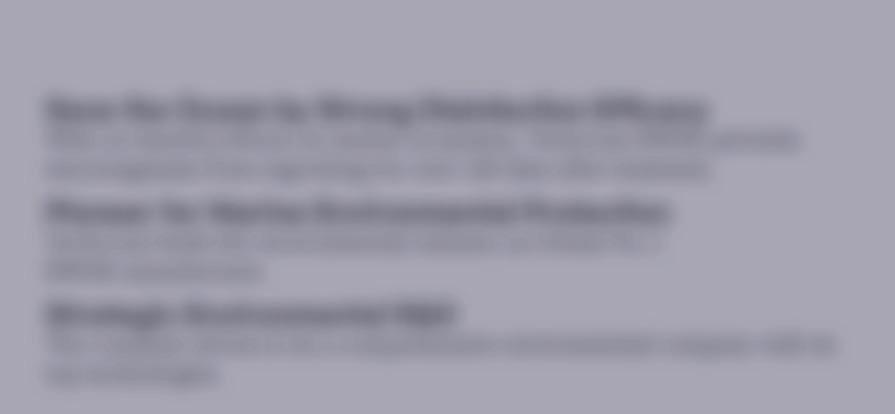
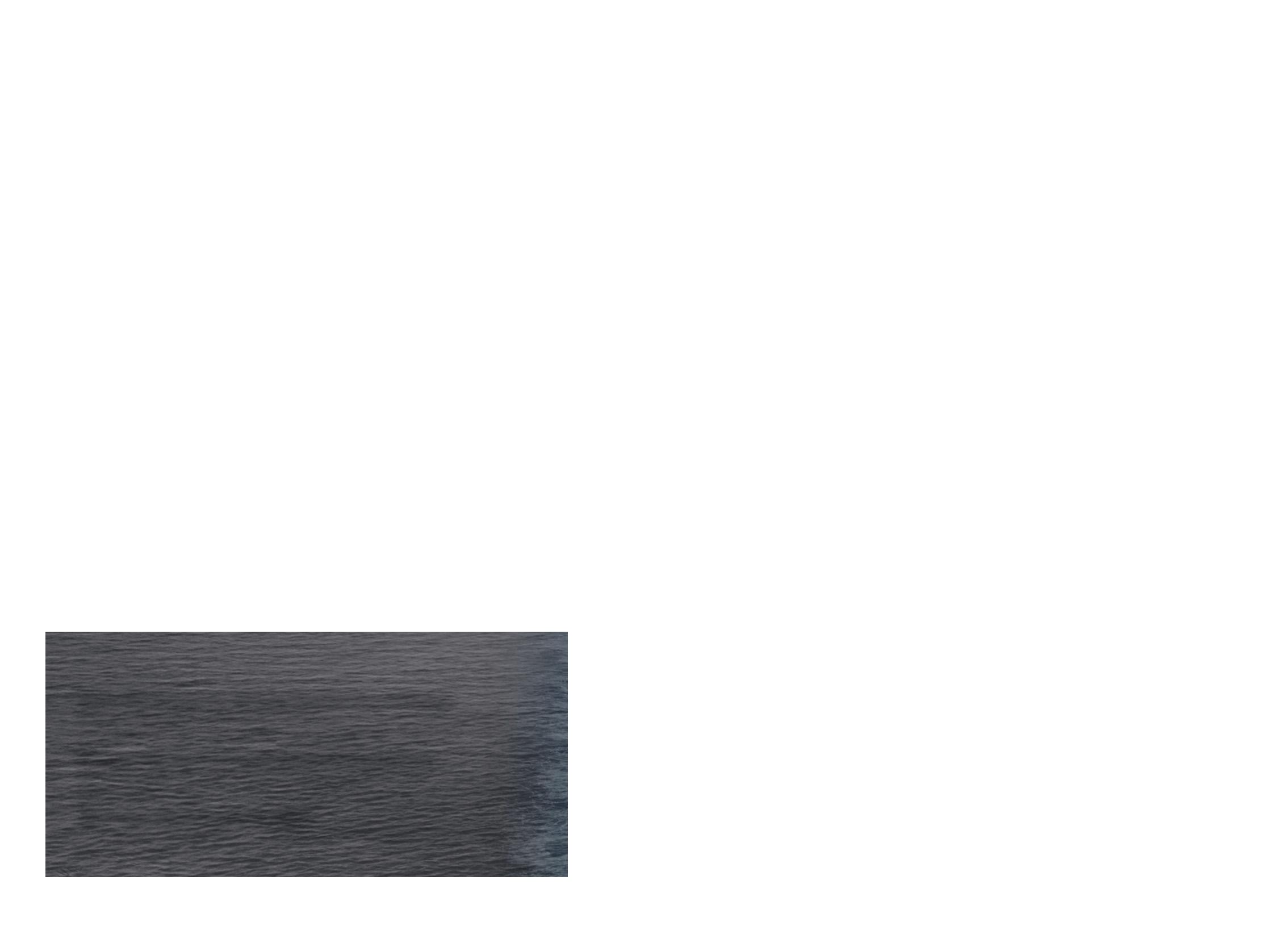



CII’s IMPACT ON ENGINES REMAINS UNCLEAR
The IMO’s proposed Carbon Intensity Indicator (CII) may be an operational measure but could have an impact on machinery, Paul Gunton reports
Uncertainty about the impact of IMO’s proposed Carbon Intensity Indicator (CII) on ship operations was voiced in The Motorship in December by Lars Robert Pedersen, deputy secretary general of the international shipowners organisation BIMCO. Now, engine builders and a leading organisation representing machinery manufacturers have added their voices to concerns about a lack of information about the new measure.
In his commentary, Mr Pedersen described the amendment to Marpol Annex VI that will bring in CII as “a novel piece of regulation” for which his members “are certainly not prepared”. CII, he said, “[has] not been clearly defined.”
Now a leading figure in the ship machinery sector, Peter Müller-Baum, secretary general of CIMAC, has told The Motorship that, with no details about how the CII will be calculated, “we do not yet know ... what adjustments might be made to the engine.” He said that to make any comments on CII’s impact on ship’s machinery would be “like looking into a crystal ball” and it was impossible “to say if, or to what extent, existing engines will have to be modified.”
He pointed out that since CII is an operational index, it is more of a measure of how machinery is used, rather than the hardware itself and its “first targets will probably not involve machinery conversion,” although “mid- to long-term targets will likely require ... onboard machinery modifications” in relation to fuel supply changes.

Image: MAN Energy Solutions
Zero-carbon fuels will certainly be necessary alongside “other technical and operational efficiency measures,” he explained, if shipping is to achieve the greenhouse gas (GHG) emission reductions in line with IMO’s GHG strategy and the Paris Agreement.
Dr Gunnar Stiesch, senior vice president and head of engineering engines at MAN Energy Solutions, also stressed the significance of new fuels on calculating CII, which he said “incorporates in its numerator fuel-related specifics” that are “influenced by the engine design and the fuel used on board.”
MAN Energy Solutions has a “standing development target” to lower OPEX while reducing CO2 emissions, he said, stressing that its own engines and systems can operate on a variety of fuels to “pave the way for a use of low and zero carbon fuels.”
But implementing an operational measure such as CII “has to go hand in hand with a further development of designrelated measures [EEDI and EEXI] to foster improvement of ship design and engine technology development,” he added. And he acknowledged that there are “pros and cons to several methodologies being considered for CII” and that “practicable implementation of CII is important to ship owners and operators.”
Nonetheless, he welcomed IMO’s decision to introduce CII, describing it as “an important step to assess operational performance of ships” and echoed Mr Müller-Baum by saying that this will help meet the goals of IMO’s Initial GHG Strategy.
8 Implementing
CII must be linked to design-related measures, says Dr Gunnar Stiesch
WORKING GROUP TO REPORT TO MEPC 76
Behind the scenes, a correspondence group set up by the delayed Marine Environment Protection Committee’s 75th meeting (MEPC 75) in November is working on a number of CII-related tasks, including drafting guidelines on operational carbon intensity indicators and their calculation methods, and will submit its report first to the next Intercessional Working Group on Greenhouse Gasses (ISWG-GHG 8), which is due to meet in May, before it goes to the delayed MEPC 76 in June.
The correspondence group’s full terms of reference can be found in IMO’s document management system, IMODOCS, where MEPC’s outcomes can be found in document MEPC 75/18. However, a separate addendum to that document, MEPC 75/18/Add.1, suggests that when the various proposals for CII reach MEPC 76, they may not simply be rubber-stamped for adoption.
That document includes some statements that delegations asked to be minuted, including one from the US delegation. This says that “the United States continues to have concerns over the rush to approve operational carbon intensity requirements before developing core aspects of the measure, including the basic metric to be used for measuring carbon intensity.”
It goes on to warn that, when the proposals reach MEPC 76, “our final view on the measure will depend upon these elements being developed to ... reassure ourselves that they do not disproportionally impact ships in the US fleet.”
Assuming they are adopted in June, the amendments could come into force 16 months later, in October 2022. They include a review date of 1 January 2026 “at the latest” by when IMO must review “the effectiveness of the implementation of the CII and EEXI requirements ... and, if necessary, develop and adopt further amendments,” an IMO summary of MEPC 75 notes.

8 It is impossible to say whether CII will require engine modifi cations, says Peter Müller-Baum
SUBSCRIBE NOW
to receive your three month free trial

•Instant access to industry news ws •Expert opinion •Monthly features •Weekly eNewsletter Maritime Journal is relied upon by marine zone and short sea commercial maritime businesses.

Informing over
maritime professionals across Europe
TO SIGN UP FOR YOUR THREE MONTH FREE TRIAL
visit maritimejournal.com email subscriptions@maritimejournal.com or call +44 1329 825 335
maritimejournal.com
PRACTICAL BWMS INSTALLATION AND REGULATORY INSIGHTS
Installation, operation and maintenance issues continue to be a challenge, but experience gained is helping operators make progress towards BWM compliance, writes William Burroughs, Senior Principal Engineer, ABS

Credit: ABS
The COVID-19 pandemic has not spared vessel owners from compliance requirements with national and international ballast water management regulations. The pandemic has exacerbated the delays previously observed with retrofi ts. For new vessels delivered with systems fi tted and for those vessels already retrofi tted, offi cers and crew must make special eff orts to understand operations, maintenance and repair - and what to do when things go wrong, or Port State Control comes onboard.
The US Coast Guard is providing ”COVID-19” extensions for vessels with no BWMS installed and some vessels with Alternate Management System-accepted BWMS at or nearing the end of the vessel's five-year AMS periods. The USCG's Marine Safety Information Bulletin (MSIB) 14-20 provides 12-month extensions for vessels with compliance dates (either original or extended) between 1 April 2020 and 1 April 2021, though for some vessels with substantiation, longer extensions might be granted depending on the persistence of the pandemic.
Extensions of the AMS periods granted by the USCG could help thousands of vessels continue operating in US waters until the pandemic subsides. These ships, with their AMS accepted BWMS and 2008 G8 Type Approvals, are compliant with the BWM Convention and with the short-duration AMS extensions, could operate in US waters and internationally until the BWMS can be upgraded.
Many BWMS vendors have 2016 G8/BWMS Code Type Approvals necessary to complete the USCG and BWMS Code approved reconfigurations. However, some BWMS vendors continue struggling to complete either their USCG approval or BWMS Code Type Approval due to the pandemic. The USCG's COVID-19 extensions provide an important compliance strategy until the pandemic subsides.
The bigger challenge is that some shipyards, required to observe social distancing, are being forced to limit the scope work that can be accomplished until the pandemic is over. This could prevent some vessels from completing their BWMS retrofits leading to challenges when the vessel's IOPP Renewal Survey is completed.
Some accommodations should be provided by Flag Administrations to support vessels struggling to get a BWMS installed on the ship or not completed due to limited vendor technical assistance because of restrictions on international travel.
While the USCG's extension policy provides extensions for vessels affected by the pandemic, the IMO BWM Convention does not and missing a retrofit deadline creates a noncompliance problem. There is limited guidance from IMO to date on how vessels that cannot retrofit BWMS will be treated though it is possible that IOPP Renewal Survey dates could be delayed for three months to allow some breathing space.
8 The USCG
expects contingency measures to be included in the BWM Plan to cover cases where the system is nonoperational or fails
BEST MANAGEMENT PRACTICES
For shipowners operating installed systems, ABS held a series of workshops providing practical guidance and advice for Best Management Practices (BMP) with BWMS under IMO and USCG regulations. The feedback received from owners demonstrated that operation of BWMS continued to be challenging. In addition to installation issues, training, commissioning, operations and maintenance, planning for inspections, outages and the development of contingency measures continue to be key topics.
The most recent update to the BMP included a survey of owners' experience in practice. It found that between 2017 and 2019 - with more systems in service - the number of inoperable units fell by more than half, though the number of owners who found operations problematic doubled. A minority of systems were not subject to monitoring or testing and a quarter were regularly operated and subject to monitoring and testing.
Installation of a BWMS requires a well-planned timeline and a focus on training of the crew, ideally from before the system is installed. Crew rotation means that sophisticated understanding can simply walk off the ship so Proper training records should include video of the installation and commissioning if possible.
In operation, the burden is shared between the senior officers, the crew and even shore staff. Likely pressure from the owner to return the vessel to service puts pressure on the engineering crew to understand not just the facets of BWMS operation but its maintenance and breakdown procedures.
After installation and commissioning, technical support may disappear which means the vessel must rely on its approved BWM Plan which itself must be updated regularly; crew must also understand how to produce data records, especially in US ports.
Sooner or later, an inspector will want to come onboard and sample the output of the BWMS. Guidelines (G2) to the BMW Convention provide design and installation guidance for the sampling facility but there remains limited training and know-how for keeping the G2 facility clean and how to obtain a sample to avoid cross-contamination that could falsely indicate non-compliance. This requires additional training for the crew.
It is advised that the crew practice for Port State Control inspections to better understand requirements they will sooner or later have to meet. Even when the BWMS is not targeted in an inspection, they will need to understand how to prove that they can they produce compliant ballast water including sampling procedures to avoid potential false results.
It is important to recognise that different administrations could have different requirements thus there needs to be communication with shipmanagers on sailing routes and the applicable rules in different locations should be understood by port engineers and communicated to the vessel's crews.
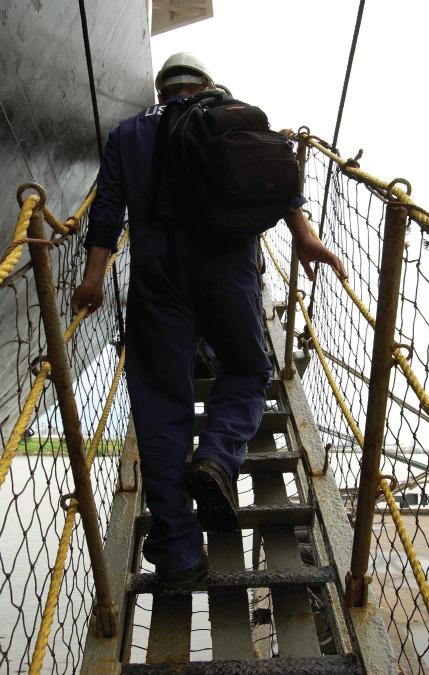
PLANNING FOR SUCCESS
Despite the rise in the number of systems in operation, it is important to understand what happens if the system fails and the fastest way to restore it to normal operations. In the case of failure, the water onboard might not be considered properly treated and it may be necessary to stop cargo operations.
Interpreting alarms and alerts is critical as well as understanding the system design limitations (SDL). When the ballasting port's ambient water is outside the water quality suitable for treatment, the crew must be trained to know what to do next. Ballasting rates can vary by the design of each system's computer-based controls and cargo operations may need to be repeatedly started and stopped if BWMS repairs and resets are required.
Maintenance intervals should be planned based on other equipment maintenance schedules and spare parts acquired in the most cost-effective ways to maintain the system in operation. The Type Approval certificate granted to the system will be valid for the lifecycle of vessel, but the use of unverified spares or mis-repairs can invalidate the warranties. This can be exacerbated by the likelihood that some parts will become obsolete through the vessel lifecycle.
Another issue for vessel operators is the preparation of contingency measures in case of system is non-operational or fails. Though initially optional for the BWM Convention, the USCG expects measures to be included in the BWM Plan for when something goes wrong. These contingency measures should be practical and feasible to provide protection to the port.
The IMO's MEPC and USCG have published high level guidelines covering equipment redundancy and crew training but in reality, vessels may need to use ballast water exchange (BWE) if they have non-compliant water onboard.
Owners using the BWMS bypass need to be aware that regaining compliance for all ballast water on the ship may become more complicated. The use of potable water is still only allowed for US compliance.
Numerous other complicated operations including transitions between light and heavy weather ballast conditions and the potential impact on vessel air draft should also be considered. Testing the vessel's ability to produce compliant ballast water discharges during commissioning following installation may be the most important pre-operational validation of the readiness of the crew and vessel to meet both USCG and BWM Convention compliance. The crew should be thoroughly trained and compliance tested often enough to reduce chances of failing a PSC testing challenge.
Credit: ABS 8 The US Coast
Guard is providing "COVID-19" extensions for vessels with no BWMS installed
PETER SAHLÉN SEES DEMAND FOR MORE BWTS TRANSPARENCY
Peter Sahlén, Head of Alfa Laval PureBallast, takes the temperature of the ballast water treatment system market and sees the advantages of transparency.
Speaking on the fi rst day of the Chinese New Year, Peter Sahlén, Head of Alfa Laval PureBallast, was keen to share his perspective on the outlook for 2021.
In common with other suppliers, Alfa Laval expects to see a surge in new orders over the course of 2021, as ship owners book in ballast water management system installations to meet compliance dates falling due in 2022, Sahlén said, citing DNV and ClassNK analyses.
“One of the unusual characteristics of the peak is the proportion of ship owners of smaller sized fleets who will be booking in installations,” Sahlén said.
Alfa Laval has been preparing to meet this expected surge in orders from an operational perspective. Sahlén noted that the company had been building up inventories at its main production facility in Aalborg, Denmark in order to meet expected demand.
The company has a fast track solution for a limited number of the most popular PureBallast 3 model sizes.
“We know that some of the ship owners are likely to delay ordering until the last minute and we are prepared to meet requests for short lead times.”
Alfa Laval has been operating with higher inventory levels at Aalborg following the introduction of production changes in 2020 during an earlier stage of the Covid-19 pandemic.
“The changes, such as segregated shift patterns, have helped us to maintain production over the course of 2020. In fact, we set a new production record in 2020, delivering over 1,000 units, and we have started 2021 in similar fashion.”
NEED FOR TRANSPARENCY
Sahlén also noted that owners were likely to be looking for a reliable source of information regarding different systems, as well as the specific operational requirements of their own vessels. Back in August 2020, Alfa Laval set up an online portal, Compliance Navigator, to bring together the certification of different BWMS producers. The data source also allows ship owners to compare the operational requirements of their fleet, by comparing their vessels' route planning with the characteristics of the waters they are passing through.
“This allows ship owners to compare any hold time, salinity, temperature or UVT limitations based on their operational profiles,” Sahlén said.
Compliance Navigator offers transparency around system design limitations or system performance for customers. “Even if a ballast water treatment system is certified, it may not get your vessel where it needs to go,” Sahlén said.
He cited the example of a number of large LNG carriers, which had opted for Alfa Laval's UV-based system rather than competing EC-based solutions on the basis of the system's performance in cold, low salinity waters at higher latitudes, as an example of the advantages of transparency for Alfa Laval itself.
Turning to specific vessel solutions, Sahlén noted that Alfa Laval's Bulker Fit solution was attracting significant interest from ship owners and operators in Europe and Asia.
The solution was tailored to the specific requirements of bulker vessels, where the variation between ballasting and deballasting requirements can significantly affect BWMS system requirements.
“We recently signed a major fleet agreement with a Greecebased premium bulk carrier,” Sahlén said, “and have also signed orders from smaller operators in Asia and China.” The asymmetric capacities offers operating capacity advantages.
In the tanker market, where Alfa Laval offers a tailored Tanker Fit solution. The Alfa Laval PureBallast 3 Ex deckhouse solution offers a practical solution for tankers equipped with submersible cargo pumps. “It also offers a convenient onestop solution for ship owners, rather than having to manage the logistics of ordering and managing various components themselves.”
The solution has attracted strong interest, particularly from the MR tanker segment, where Alfa Laval has a long standing reputation for flexibility.
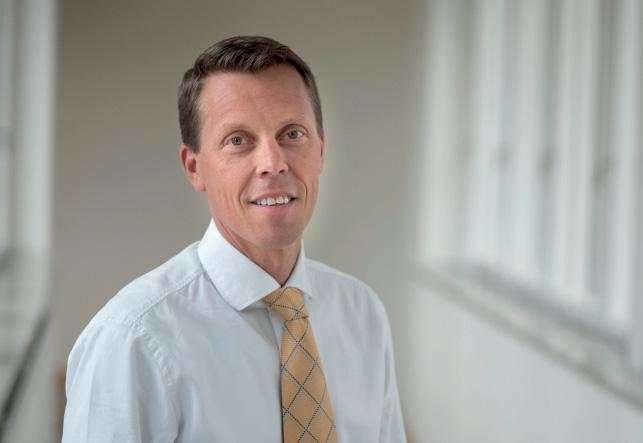
SERVICE NETWORK
Sahlén concluded by briefly looking back at Alfa Laval's experiences in 2020. While the pandemic had accelerated a trend towards remote services, and Alfa Laval had seen demand increase for its services, such as Compliance Service and PureBallast Connect, there was no alternative to physical attendance for some services.
Alfa Laval's global network of 160 service engineers had allowed services to continue, avoiding the impact of global travel restrictions on centralised pools of engineers.
“This meant that we were able to conduct service calls on our systems. We are always available for our customers through our 24/7 with our global service network.” The advantages also extended to the installation and commissioning processes, many of which Alfa Laval was able to manage itself, Sahlén concluded.
8 Peter Sahlén
noted Alfa Laval's PureBallast UV-based system had received orders from LNG carriers on the basis of the system's performance in cold, low salinity waters at higher latitudes
UECC’s HYBRID PCTC TO USE BATTERY FOR BOW THRUSTER
European ship operator United European Car Carriers (UECC) has successfully operated a pair of LNG-fuelled short-sea PCTCs since 2016. The company is now building a series of three further vessels that will be the fi rst LNG battery hybrid PCTCs in the world

Credit: UECC
The vessels are being built by China Ship Building Trading and Jiangnan Shipyard Group, with the design work done in conjunction with DNV and ship Designer Shanghai Merchant Ship Design & Research Institute (SDARI). The fi rst vessel is scheduled for delivery later this year, with the other two following next year.
The energy storage system (ESS) system will be charged by a permanent magnet, directly driven shaft generator or dual fuel generators. The ESS won’t normally need charging in port, as the energy management system will automatically interface to AIS and voyage routing systems to ensure it is charged and ready for use when it is needed to power the bow thruster for harbour manoeuvring or supplying the ships’ general power demand.
As part of the total power system, which includes a WinGD 6RT-Flex50DF dual-fuel engine, a controllable pitch propeller, a bulb rudder, two dual-fuel gensets and a dual-fuel boiler, the ESS will provide power to the main switchboard, peak shaving capabilities for the main engine and auxiliaries and offer black-out prevention. The vessels will only require two auxiliaries, as the ESS and the shaft generator eliminate the need for one more that would otherwise have been required. The highly-efficient design means that ESS is expected to have a payback time of five years.
The vessels will achieve DNV’s Battery Safety notation. WE Tech of Finland is providing its WE Drive direct drive permanent magnet shaft generator, the DC-link power distribution system and the ESS, with Corvus Energy providing the battery package. Kongsberg Maritime is providing the energy management system which acts as a supervisory and control system for the overall production and consumption of energy onboard the vessels, ensuring flexibility and optimal operations at sea, in port and during manoeuvring.
The capacity of the battery is based on the design of the hybrid solution for operation of these short sea vessels, says UECC Head of Ship Management, Jan Thore Foss. The battery capacity has been sized to optimise utilisation, based on detailed modelling of the vessels’ expected operational
8 UECC ceo
Glenn Edvardsen noted that the newbuildings qualifi ed for green fi nancing from Svenska SkeppsHypotek
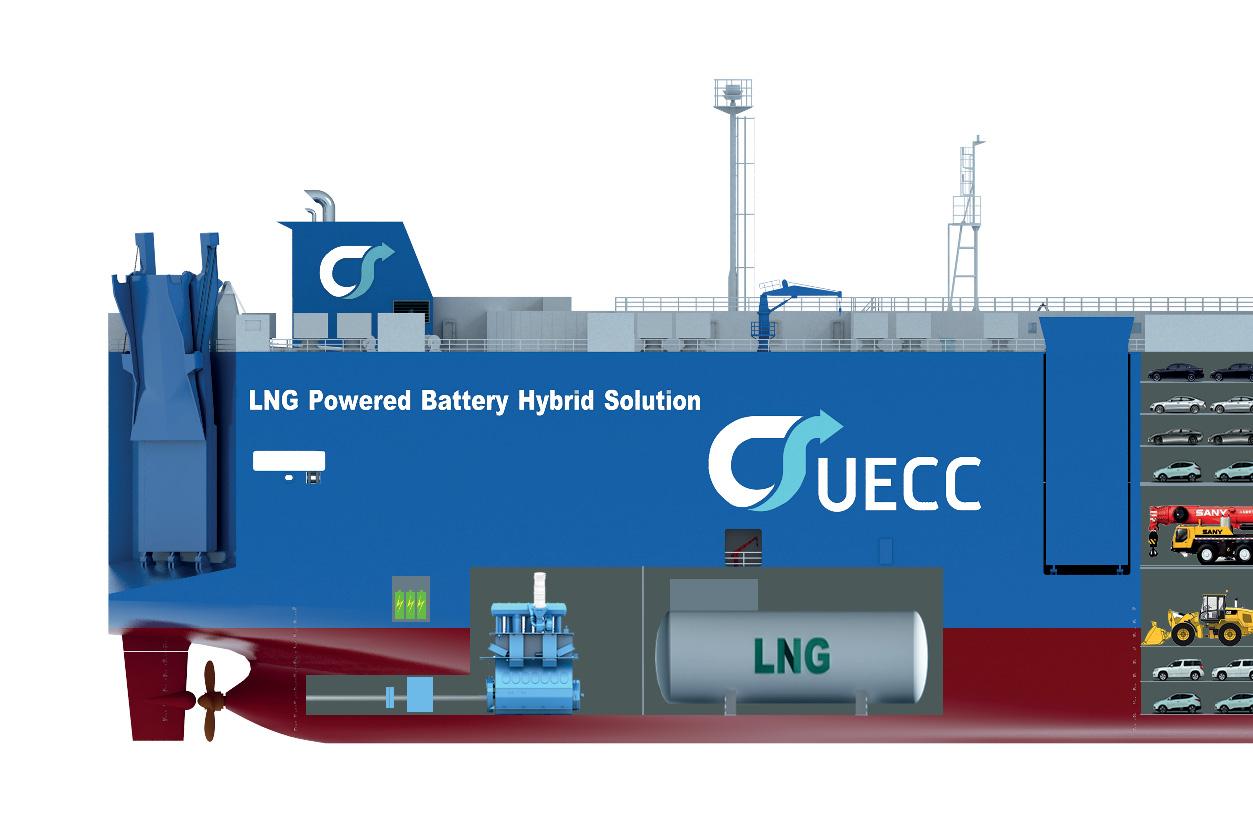
profile, to maximise the economics of the installation. Furthermore, the vessels will be shore-power ready. Availability of the service is expected to grow and will provide power whilst the vessels are alongside in port to reduce SOx and NOx emissions and PM.
MARKET EDGE
UECC, jointly owned by NYK and Wallenius Lines, is a leading short-sea operator and logistics provider for the transportation of cars, vans and high and heavy cargo in Europe and currently has operates a fleet of 18 purpose-built vessels. The new vessels are part of a fleet renewal program designed to boost environmental performance. They will sail predominately in the UECC Atlantic trade and will meet the Tier 3 IMO NOx emission limitations coming into force for the Baltic and the North Sea for newbuildings with keel laid on or after 1 January 2021.
UECC ceo Glenn Edvardsen is proud of the vessels’ pioneering design, which is an integral part of the improved efficiency. “We have done extensive model testing to achieve the very best hull performance, so we believe it’s an improved design compared to other PCTCs today,” says Edvardsen. The vessels won’t have conventional bulbous bow as a sharper waterline at various drafts is better suited to the sea conditions. Their pioneering design will take UECC beyond the IMO target of 40% reduction in carbon intensity by 2030 through the combination of optimal hull design and the LNG battery hybrid solution.
“Added to that, LNG is currently the most environmentally friendly marine fuel there is. It has been for some years already. And, of course the battery installation will further reduce the emissions, he says.
“In our market, in our region, UECC is currently the only shipping company that is actually investing in environmentally friendly and sustainable newbuilds. So, we have big hopes that they will bring a lot to the marketplace by providing help to the customers to lower their emissions. Everybody is interested in lowering emissions in their logistic chains, and we are there for them.”
At a time when many financial institutions are paying considerable attention to the environmental credentials of newbuilding projects, the highly efficient PCTC newbuildings secured green financing from Svenska SkeppsHypotek. As the project met green criteria, the loans were offered at a reduced cost.
CARGO FLEXIBILITY
The new vessels will have a length overall of 169 metres and a width of 28 metres. They will have a car carrying capacity of 3,600 units on 10 cargo decks, two of them hoistable using electric hoists from TTS/MacGregor. The vessels will have a quarter ramp of 160 metric tons safe working load and a side ramp of 20 metric tons safe working load and can accommodate cargo units up to 5.2 meters high. This will make the vessels extremely flexible, enabling them to accommodate a multitude of high and heavy, breakbulk and mobile loading platform (mafi) cargoes, which are cargo segments, in addition to cars, that UECC has built a significant portfolio for over the years since its establishment in 1990.
THE LNG ADVANTAGE
UECC’s two existing LNG-fuelled vessels Auto Eco and Auto Energy are the biggest 1A super Finnish/Swedish ice classed PCTCs and the first PCTCs in the world capable of operating on LNG. They are capable of sailing a 14-day round trip in the Baltic solely on LNG, storing approximately 800cbm in a cylindrical Type C tank, and were the first clients of the world’s first seagoing LNG bunkering vessel, ENGIE Zeebrugge, which is home ported at Zeebrugge.
Edvardsen is confident of on-going ready access to LNG bunkering services in Europe, and he anticipates that LNG will remain competitive in price. “We have seen that LNG fuel has become very competitive in terms of pricing,” he says. “As we’re moving ahead, we will really improve environmental performance, so we’re very excited.”
“We are very keen to move on with dual fuel engine technology, not only because of LNG,” says Foss. “In the future we will be in a good position because we can also run on biogas and low emission fuels. As we speak, we are testing alternative fuels. Last year, for example, UECC trialled GoodFuels’ biofuel oil on the AutoSky. The fuel was bunkered at Rotterdam and tested successfully on the vessel’s normal route between Zeebrugge and the Spanish port of Santander.
UECC is waiting for the right time to switch over to nonfossil fuels, seeing LNG as part of a roadmap that will lead to zero emissions. “We are continuing on that journey, blending in biogas, which reduces the CO2 even further than what we will be achieving with the LNG battery hybrid solution,” says Edvardsen. “That’s the beauty with the dual-fuel setup. We are able to burn many other alternative fuels as they become available and are sustainable. We’re not stuck with LNG. LNG is what we are using today, because it is the most environmentally friendly marine fuel available on the market.”
Foss adds: “We have to keep our eyes open for new future technologies. Our mission is always to be a leading provider of sustainable short sea transportation in Europe, and to achieve that mission, we have to operate a sophisticated fleet.” Asked if he anticipated challenges with the newbuildings, Foss says: “It’s not new technology as such, it’s just the combining of everything which make it very special and efficient. But of course, to be at the front and to be pioneering, there are sometimes things you don’t expect. We’re willing to take on that risk. The experience we have from the existing vessels is that dual-fuel operation really pays off. So, we are ready to take the challenges if they come.”

Credit: UECC 8 Integrating an
ESS and shaft generator into the hybrid dual-fuel PCTC design allows the vessel to reduce the number of auxiliaries to two
NEWCASTLEMAX TRANSITION TO LNG FUEL
A seminal event in the move towards the use of LNG fuel in the deep-sea bulk trade lanes is signalled by the handover of two Korean-owned and -built vessels, writes David Tinsley

Credit: POSCO
South Korea’s shipping and shipbuilding sectors have opened a new chapter in deep-sea bulk carrier design and trading through the completion of a pair of LNG-fuelled newbuilds of 180,000dwt. The Newcastlemax-class HL Eco and HL Green are the largest bulkers commissioned to date with the capability to use LNG as the primary fuel.
Powered by dual-fuel machinery throughout, covering both propulsion and auxiliary systems, each 292m bulker is expected to make about 10 round-voyages per annum between Australia and South Korea. The prospective impact in terms of emission reduction is substantial, as operation in gas mode with the type of engines installed promises the virtual elimination of SOx and particulate matter (PM), and up to 85% less NOx and a 30% curtailment of CO2 compared to existing mainstays of the trade.
Constructed by Hyundai Samho Heavy Industries (HSHI) to the order of Seoul-based H-Line, the HL Eco and HL Green reportedly commanded a per-ship price of around US$62 million, reflecting the significant premium entailed with a dual-fuel specification relative to conventional powering arrangements. Indicative of the cost gap, brokers currently put the representative newbuild price for ‘standard’ Newcastlemax bulkers at about US$48 million, down somewhat from the US$50 million or so that pertained when the H-Line tonnage was ordered in October 2018.
Acknowledging the extra cost burden associated with building gas-fuelled ships, the Korean government has proved supportive to the marine industries by incentivising domestic investment in such tonnage from home yards.
H-Line’s initiative in committing to LNG power for large bulkers has been followed by a succession of LNG-fuelled newbuild projects in the Newcastlemax sector by owners worldwide, for raw material flows into the east Asian industrial powerhouses of South Korea, Japan and China. A particularly important development came last September when Australian miner BHP awarded Eastern Pacific Shipping a five-year timecharter contract covering five LNG-fuelled, 209,000dwt Newcastlemax newbuild bulkers to carry iron ore from Western Australia to China.
The H-Line ships made their debut on the Australian coast during January. On her maiden voyage, HL Green put in to Port Hedland, Western Australia, to take on iron ore, while HL Eco shipped a cargo of Hunter Valley coal via Port Waratah’s facilities in Newcastle, New South Wales. In both cases, the destination on the Korean peninsula was Gwangyang, the site of one of POSCO’s steelmaking complexes.
South Korea had put down a marker for the industry in 2018 when Hyundai Mipo Dockyard (HMD) delivered the 50,000dwt LNG dual-fuelled bulker Ilshin Green Iris into the coastwise traffic carrying limestone under POSCO charter.
Ilshin Green Iris had been built to dual Korean Register of Shipping (KR)/Lloyd’s Register (LR) class, HSHI parent Hyundai Heavy Industries signed a joint development agreement with LR in 2017 for the design of LNG-fuelled bulkers in the 180,000dwt category. HL Eco and HL Green have come into being under dual class assignment, although in this case with DNV notations alongside those of KR.
Each of the new vessels is equipped with two Korean-
8 At point of
handover, HL Eco and HL Green

Credit: Pilbara Ports Authority
manufactured, 1,600m3 Type C LNG fuel tanks, among the most capacious at sea to date. The tanks were fabricated using POSCO’s 9% nickel steel, ensuring the requisite containment temperature of minus 163degC.
POSCO has provided the industry with another option by developing a high-manganese steel that can be used in the production of LNG fuel tanks. The company’s austenitic manganese tank technology had its initial application in the Ilshin Green Iris. The high manganese-content (26%) steel offers benefits in weldability and cost-efficiency relative to nickel, while affording comparable quality. The extended product range is salient to POSCO’s preparations for an expected surge in demand for LNG tank material during the next few years as more and more shipowners and operators turn to LNG-fuelled vessels.
POSCO’s involvement in the H-Line bulker newbuilds otherwise entailed the supply of 42,000 tonnes of steel plate for hull construction.
Whereas Korea’s milestone LNG-fuelled bulker Ilshin Green Iris had provided a showcase for MAN’s ME-GI high-pressure DF propulsion engine technology, H-Line’s Newcastlemax duo employs low-pressure DF two-stroke machinery from the Winterthur Gas & Diesel (WinGD) stable. Each vessel’s sixcylinder X72DF engine achieves Tier III compliance in gas mode without extra measures, and is rated for a maximum continuous output of 16,180kW at 72.5rpm. The engines were produced at the Ulsan works of licensee HHI.
The auxiliary outfit comprises three aggregates based on dual-fuel prime movers from HHI’s in-house HiMSEN fourstroke range. The engines are of the H22CDF type in five-cylinder layout, driving 1,262kVA gensets. Both the oil/ gas-fuelled main boiler and the economiser are of Alfa Laval (Aalborg) design.
H-Line awarded HSHI a repeat contract in July 2019, such that third and fourth examples of the HL Eco type are to be handed over by the end of March 2022. Two newbuild membrane-type LNG carriers are also on the books at the Yeongam-Samho yard to H-Line account, and are scheduled to enter service during the early part of 2022.
The H-Line fleet comprises over 40 bulkers and seven LNG tankers. Most of the bulk carriers are engaged in the transportation of raw materials for long-term clients POSCO and Korea Electric Power Corporation (KEPCO). The highestcapacity units are the very large ore carriers (VLOCs) HL Tubarao and HL Brazil.
Split off from bankrupt Hanjin Shipping in 2014, H-Line had been Hanjin’s bulk cargo division and was acquired by South Korean private equity firm Hahn & Co. As the controlling shareholder, Hahn & Co subsequently augmented H-Line’s interests and scope through the purchase and assimilation in 2016 of Hyundai Merchant Marine’s dry bulker operations. The LNG carriers deployed by H-Line serve traffic flows from Indonesia, Oman and Qatar under long-term KOGAS contracts.
PRINCIPAL PARTICULARS - HL Eco/HL Green
Length overall 291.9m Length bp 287.0m Breadth, moulded 45.0m Depth 24.8m Draught 18.0m Gross tonnage 97,000gt Deadweight 179,650t Cargo holds 9 Propulsion + auxiliary engines LNG dual-fuel Main engine power 16,180kW Speed 14.5kts Main gensets 3 x 1,262kVA Class (dual) KRS/DNV Flag Panama
8 HL Green at Port
Hedland, to take on her fi rst cargo
DECLINING SHIPBUILDING AND VLCCs
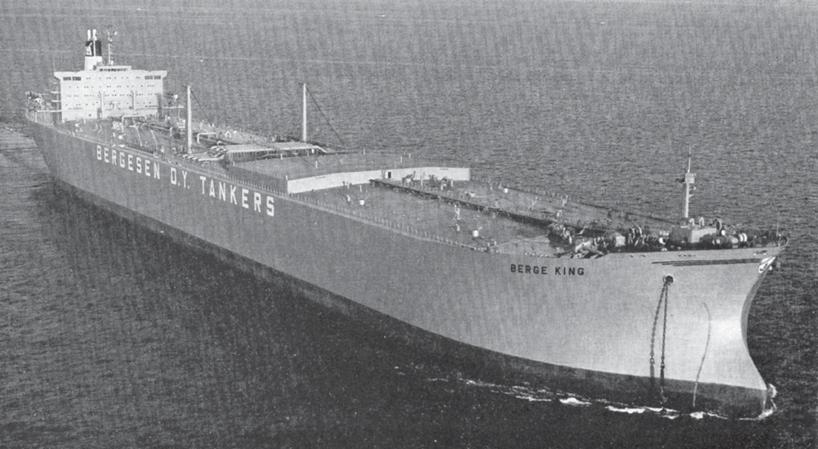
8 Bedplate for a 10-cylinder Fiat 1060s engine, seen at
the new GMT plant in Trieste
The February 1971 issue of The Motor Ship reminded us that this title’s ethos was not only to provide news of the marine engineering world, but to fl y the fl ag for British Shipbuilding.
That was brought home by an editorial opinion piece, in which the writers highlighted the removal of investment grants by the government of the day - in other nations as well as Britain. But it was noted that with the exception of one or two yards, and despite a high level of completed tonnage, the British industry was facing rapidly rising material and labour costs in the face of a backlog of unprofitable fixed-price contracts, signed with official backing in a relatively recent, economically happier, climate. “However can any government, especially of a large maritime nation, be disinterested in the future of its own shipyards?” asked the article. As we now know, it didn’t take long for the effects of this disinterest to become apparent. Indeed, another editorial mentioned that Britain had just fallen behind Spain in terms of orders.
Elsewhere, the industry had cause to celebrate, with the delivery of the latest contender for the ‘world’s largest motor ship’ title. This was the 280,420 dwt VLCC Berge King, for the Norwegian owner Bergesen, which had been built at the new Chiba yard of Mitsui in Japan. Like most of the company’s fleet, the 342.9m long Berge King was powered by a B&W diesel plant, in this case a 9K98FF main engine rated at 35,300 bhp. The design was largely conventional, though the piping and pump system serving a total of 18 cargo tanks was arranged so that loading and ballasting could be carried out
8 The 280,420 dwt VLCC ‘Berge King’ -1971’s largest
motor ship
simultaneously, meaning that as soon as the cargo was loaded, the ship was ready to sail. In line with current practice, all main systems were arranged for automated operation, with the engine controlled directly from either the bridge or a dedicate soundproofed control room. Nevertheless, a crew of 47 was needed to keep this giant afloat.
Other main features included a review of propulsion engines from 1970, noting the growth in bore dimensions of the still-dominant two-stroke power plant, as well as the trend towards multipleengine installations, of both low speed and medium speed types, with the growing container sector providing most of the references for the former. Demand for compact engine rooms, optimising cargo space, was fuelling the high-power mediumspeed market, while the potential of gas turbines for merchant vessel propulsion - not to mention nuclear power - was still being regarded seriously.
One major engine development was the new diesel engine factory - which, being able to turn out 1 million hp annually, was described as the world’s largest and most efficient of its type - for Grandi Motori Trieste, a joint venture between the Fiat group and the Italian state.
An interesting experiment reported on in February 1971 was Europe’s first ocean-going integrated tug and barge system. The Swedish Neptun company was hoping to put into practice what was (and still is) common practice on the North American waterways, with two 5,600bhp tugs and a pair of 10,000dwt self-unloading barges. The barges were built at HDW in Kiel, and the tugs at Ulstein in Norway and Asiverken in Sweden. The tugs - believed to be the first such vessels to be fitted with bow thrusters and stabilisers - would operate with a crew of 12, considered low for the volume of cargo carried. Initial contracts were for pulpwood and coal in the Baltic, though Neptun envisaged various cargoes, including liquids, throughout NW Europe, using further barges that were on order or being designed.

MOTORSHIPTHE
INSIGHT FOR MARINE TECHNOLOGY PROFESSIONALS
The international magazine for senior marine engineers
EDITORIAL & CONTENT
Editor: Nick Edstrom editor@mercatormedia.com
News Reporter: Rebecca Jeff rey rjeff rey@mercatormedia.com
Correspondents
Please contact our correspondents at editor@motorship.com Bill Thomson, David Tinsley, Tom Todd, Stevie Knight, Wendy Laursen
Production
Ian Swain, David Blake, Gary Betteridge production@mercatormedia.com
SALES & MARKETING t +44 1329 825335 f +44 1329 550192
Brand manager: Toni-Rhiannon Sibley tsibley @mercatormedia.com
Marketing marketing@mercatormedia.com
EXECUTIVE
Chief Executive: Andrew Webster awebster@mercatormedia.com
TMS magazine is published monthly by Mercator Media Limited Spinnaker House, Waterside Gardens, Fareham, Hampshire PO16 8SD, UK
t +44 1329 825335 f +44 1329 550192
info@mercatormedia.com www.mercatormedia.com
Subscriptions
Subscriptions@motorship.com or subscribe online at www.motorship.com Also, sign up to the weekly TMS E-Newsletter 1 year’s magazine subscription Digital Edition: £GBP173.00
© Mercator Media Limited 2021. ISSN 2633-4488 (online). Established 1920. The Motorship is a trade mark of Mercator Media Ltd. All rights reserved. No part of this magazine can be reproduced without the written consent of Mercator Media Ltd. Registered in England Company Number 2427909. Registered offi ce: Spinnaker House, Waterside Gardens, Fareham, Hampshire PO16 8SD, UK