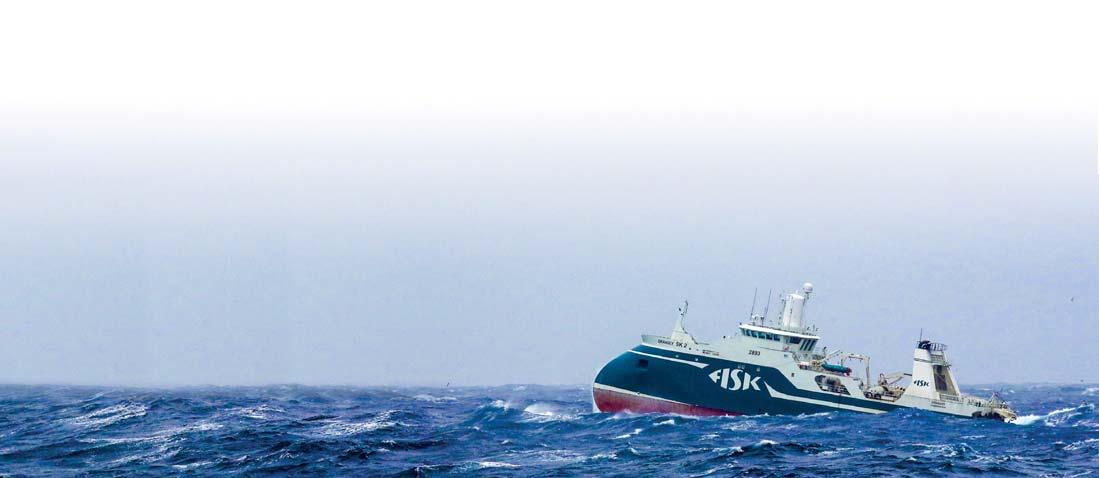
2 minute read
TWO-STROKE ENGINES NEW OPTION IN METHANOL POWER
Methanol-capable two-stroke propulsion options have been extended into a lower power range by MAN Energy Solutions in response to heightened interest in the fuel as a means of reducing shipping’s carbon footprint, writes David Tinsley.
The latest development involves a methanol dual-fuel variant of the 450mm-bore G45ME-C engine, under the G45ME-LGIM designation, widening the market reach of the technology among smaller ocean-going vessels.
The G45ME-C family is characterised by an exceptionally high stroke-to-bore ratio of 5:1, entailing a piston travel distance of 2,250mm. The heavy fuel oil engine, updated nearly two years ago as the C9.7 version, spans a nominal, maximum continuous output band from 6,950 to 11,120kW at the L1(111rpm) rating, and 4,000-5,600kW at the L4(85rpm) setting, while a broadly similar power profile applies to the LNG dual-fuel, G45ME-C9.5-GI gas-injected variant.
Shipowners, operators and builders now have the choice of eight MAN low-speed engine series, at six bore sizes, able to run on methanol. The addition of the G45ME-LGIM means that the portfolio starts from 4,000kW, stretching to just over 82,000kW in
8 MAN ES has confirmed plans to extend the range of LGIM engines to include a 450mm-bore engine in addition to its existing options installations using the largest methanolcapable engine in the range, the G95ME-LGIM.
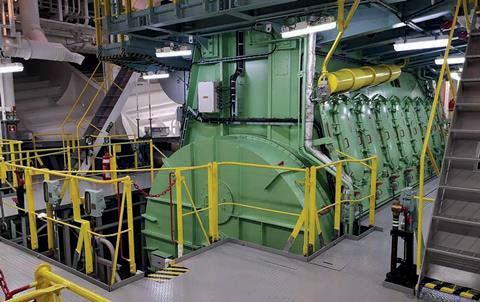
LGIM dual-fuel technology was initially introduced at the 500mm-bore size, and was first ordered for a programme of chemical/ product newbuilds intended for worldwide trade with methanol cargoes. Subsequently, 2021 saw the release of LGIM versions at 950mm- and 800mm-bore, augmented last year by 600mm- and 700mm-bore models, bringing all main types of large and mediumsized merchant vessel within the compass of the technology.
Design delivery schedules for the new
Source:
G45ME-LGIM type are expected from the end of March 2025 onwards.
As concerns the clutch of 600mm- and 700mm-bore LGIM models announced in early 2022, MAN is tentatively scheduling opening design deliveries of the S60ME-LGIM towards the end of 2023, and is looking to mid 2024 in the case of the G60ME-LGIM and G70ME-LGIM types.
By November 2022, 19 engines of the 500mm-bore LGIM series had been taken into service at sea, and the forward orderbook totalled 78 units across the different bore sizes, including 24 of the G95 variants at the top end of the range. The 950mm-bore methanol dual-fuel engine figures prominently in Maersk’s newbuild programme, as in series of 16,000TEU and 17,000TEU boxships contracted from Hyundai Heavy Industries.
Increasing selection and consideration of the LGIM offering reflects methanol’s cleaner-burning, low-carbon properties, and its potential as a zero-carbon fuel if supplied as ‘green’ methanol. It also offers practical advantages in terms of storage and bunkering at ambient temperatures and available supply infrastructure.
Organised by: Media Partner:
Japan’s largest shipbuilder is taking a stake in the country’s two-stroke engine production sector, writes David Tinsley. A draft agreement has been signed for Imabari Shipbuilding’s intended 35% equity participation in a company to be created through the spin-off of Hitachi Zosen’s marine engine business.
Hitachi would retain a 65% holding in the new entity, which has the interim title ‘HITZ Marine Engine Preparatory Corporation’. A trade name will be adopted with effect from the completion of the transaction and planned business start on 1 April 2023.
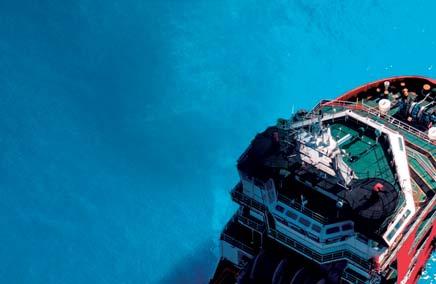
Imabari is a dynamic force in the industry, consistently investing in existing facilities and acquisitions and now controlling 10 domestic yards and other interests.
The group’s rationale for the latest tie-up is to ensure the stable supply and procurement of engines for its newbuild workload from the Hitachi works, with an eye to next-generation machinery on the path to zero-emission ships, while Hitachi is looking to expanded sales, improved profitability and increased focus on new-technology engine development.
Both shipbuilding and marine engine manufacturing in Japan face a tougher business environment and intensified competition, accentuated by volatile steel and material prices. Furthermore, technological