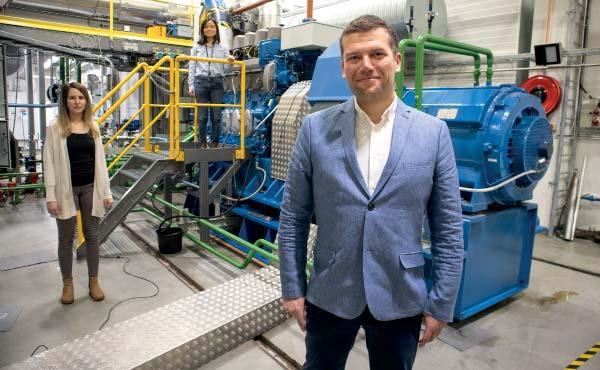
3 minute read
RCCI PROJECT EMBEDS MODELBASED COMBUSTION CONTROL
Finland’s Clean Propulsion Technologies project is developing a medium-speed marine engine based on Reactivity Controlled Compression Ignition (RCCI) technology which is designed to take advantage of model-predictive control to optimise combustion in real time
The project is in its final year, with the engine almost built, and Project leader, Maciej Mikulski, Professor in Combustion Engine Technology at Finland’s University of Vaasa, says the self-learning functionality is derived from the same predictive models that are used to develop the engine calibration. It will optimise key operating parameters relating to the in-cylinder fuel blending and advanced variable valve actuation. The functionality will further help detect anomalies to support condition-based maintenance and fault detection.
RCCI is a variant of Low-Temperature Combustion technology that uses in-cylinder fuel blending by first injecting a low-reactivity fuel such as natural gas, methanol or hydrogen combined with air and recirculated exhaust gases followed by injection of a high reactivity fuel such as biodiesel directly into the combustion chamber.
The demonstration dual-fuel LNG, RCCI engine developed by the Clean Propulsion Technologies project is expected to increase engine efficiency by 2 percentage points compared to current dual-fuel engines, reduce GHG emissions by 20%, reduce methane slip by 90%, and result in ultra-low NOX and PM emissions. Further progress towards near zero emissions will be achieved through advanced after-treatment and hybridization technologies also being developed.
The project has showcased a paradigm shift in engine development methodology, with the predictive simulation models that enable calibrating the engine with only limited physical testing. This approach was needed to fast-track the complexity associated with optimising 15 independent engine control parameters. (State-of-the-art gasoline engines in cars have about five independent control variables.)
“It’s a new engine concept, and we need to put it into the laboratory and start testing where the optimum is. With 15 independent control parameters, this ends up involving 10 to the power of 17 calibration points at full factorial. This translates to around two trillion years of laboratory work if we were able to work 24/7. Clearly, we had to find a more efficient way.”
Simulations based on widely-used reactive models would take several weeks for a single combustion cycle - something Mikulski’s team can now do in three minutes.
“Instead of a 3D framework predicting how the vortex moves, we have simplified the thermal and reactivity stratification being created across the cylinder. The 13 zones still reflect the mixing but allow for much faster simulation.” The simplification still matches the experimental results within 5% in all combustion indicators.
For the whole factorial optimization, assuming dedicated time on a supercomputer cluster, a model run takes around three weeks. The new in-house combustion model has now been coupled with the commercially available GT-Suite system to facilitate full propulsion train modelling.
To ensure robust operation of the ultra-sensitive RCCI engine, parts of the modelling framework need to be able to calculate combustion in real-time, to support the engine control functions. For this, a simplified but still physics-based model of the combustion chamber has been developed. The real-time surrogate is built by direct linearization of the detailed multi-zone chemical-kinetic solution and matches it in accuracy but only around a certain range of operating conditions.
“Previously simulations have been used to help develop individual components of the engine, but we are creating a complete rapid prototyping package to support the engine and powertrain control-development framework. The development of the whole system is based on a fully predictive optimization model, including embedded solutions for integration with a controller in real-time. Aside from enabling our ambitious goals in RCCI engine performance, our project will be the world’s first demonstration of the model-based workflow on such a scale.”
Mikulski says the main engine model, named the University of Vaasa Advanced Thermo-Kinetic Multi-Zone Model (UVATZ), enables superior insight, fast predictive optimisation and control development, and is the fastest RCCI modelbased development toolchain for the level of fidelity/ predictivity it achieves. “It will be validated in real use cases when the experimental platform fires up.” That will happen in the next few months, and Mikulski is confident the testing will be completed the end of 2023.
A smaller high-speed engine for non-road mobile machinery is being developed in parallel as part of the project, and it will ultimately be designed to use hydrogen as fuel. This could pave the way for marine applications later on.
The current project is funded by Business Finland and includes 15 partners including University of Vaasa, Tampere University, Aalto University, Åbo Akademi University, VTT Technical Research Centre of Finland and LappeenrantaLahti University of Technology LUT, Wärtsilä Finland, AGCO Power, Dinex Finland, Proventia, Bosch Rexroth, Geyser Batteries, APUGenius, Napa and Meyer Turku.