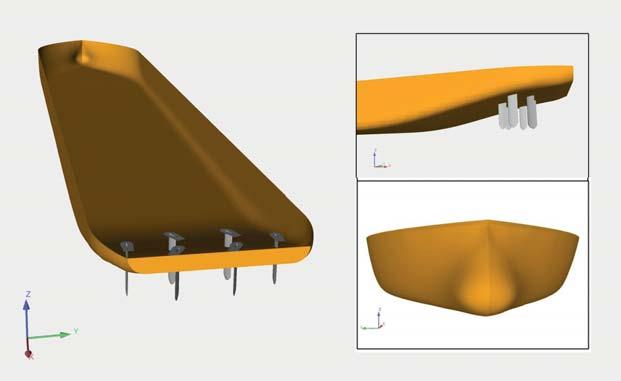
3 minute read
COUNTER-FLAPPING FOILS TO BOOST PROPULSIVE AREA
Researchers from VTT have developed a concept for counter-
Gains in hydrodynamic efficiency will result in reductions of harmful environmental emissions, irrespective of the energy source, and this has been the driving force for a team of researchers at the VTT Technical Research Centre of Finland.
Solutions for emission reductions will need to combine a variety of technologies, operational practices, energy sources and efficiency measures, says Dr Antonio SánchezCaja, but ship emissions seem shifted around rather than eliminated by some clean technologies. “For example, the use of scrubbers often transfers harmful gas emissions from air to water with uncertain ecological consequences. Other example is the use of fully electric propulsion in regions where electricity is generated by burning fossil fuels. Even in fuel cell propulsion the problem persists since the cells generate electricity from hydrogen. The hydrogen has been usually made by steam reformation of natural gas, generating CO2 as a waste product.”
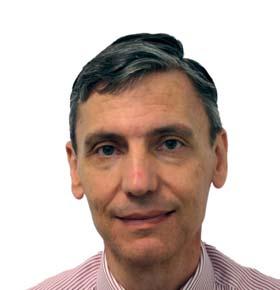
On the other hand, from a hydrodynamic standpoint, conventional marine propellers are known to be low in efficiency, he says. As an indicative example, a large number of propellers installed on cargo vessels waste about 40% of the energy in the form of rotational losses in the wake, vortex generation, noise, cavitation, etc. Design constraints, such as the maximum propeller diameter, result in a reduced propulsive area and thus a high blade loading, which penalizes efficiency.
“The development of highly-efficient innovative propulsors with efficiencies far above current levels would be desirable. Hence, an effective strategy for cutting ship emissions is focusing on hydrodynamics.”
His team’s propulsor concept focuses on reducing both emissions and operational costs. The design consists of thrust-producing counter-flapping foils cyclically oscillating along a closed trajectory. The arrangement of lifting surfaces allows for optimum generation of a steady and uniform overall thrust over the propulsor swept area, says Sánchez-Caja, and no rudders are needed for directional motion control.
“The huge reductions in hydrodynamic losses from the new propulsor concept result from: i) Large propulsive area: hydrodynamic efficiency grows as propeller loading (thrust per square meter) decreases, ii) Recovering of lateral losses in counter-flapping foil arrangements (similar to energy-loss recovering in contra-rotating propellers), propulsive efficiency than conventional propellers ls easily iii) Uniform distribution of blade loading along the propulsive area, and of propeller induced velocities, iv) No need of rudders (no rudder drag) for manoeuvrability: the propulsor can act as a rudder by controlling the foil angles in the fore and aft- rows, v) Self-adjusting blade pitch for off-design operation with optimum incidence angle along the span, contrary to controllable pitch propellers with portions of blade sections working at wrong incidence angle.”
Previously, other attempts to reduce propeller loading for a given thrust have been made by increasing the surface area of the propeller. However, increasing propeller diameter is limited by ship draught. Twin or multi-screw configurations take advantage of more of a ship’s breadth, but unconventional, propulsors with a rectangular propulsive area have also been proposed – including oscillating foils and cycloidal propellers.
In the VTT concept, an endless-chain/belt mechanism controls for foil motions so unsteady phenomena are limited to a small portion of the trajectory. The foils are motor-driven and arranged in two parallel rows travelling in opposite directions. They move perpendicular to the direction of the inflow of water. The foils in the downstream row benefit from the velocities induced by the foils in the front row, recovering lateral losses in the direction perpendicular to the vessel motion. Losses due to unsteadiness are reduced as they are only produced only at the edges of each row. This results in uniform flow over most of the trajectory.
In a study published in Ocean Engineering, the VTT team highlight that: “In principle, the new propulsor is conceived to operate in off-design conditions by adapting the foil pitch angle to achieve the required force in magnitude and direction. Contrary to controllable pitch propellers, the effective inflow at the sections along the blade span will not present strong variations in angle of attack.”
The team claims that the use of large area propulsors combined with counter-flapping foils easily increases the levels of attainable hydrodynamic e above 15% compared to conventional propellers for both design and off-design operations. “The challenge is to mechanical solution for the propulsor and to build the first prototype,” says SánchezCaja. “Here at VTT we are working on possible mechanical solutions, and we are looking for partners interested in developing the concept.”
15
TO JUNE 202 Southampton United Kingdom
Marine Civils is open for business all year
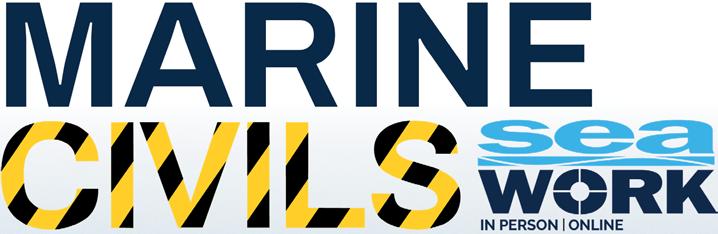
Marine Civils is Europe’s leading event dedicated to showcasing the latest equipment and solutions for marine, coastal and other challenging civil engineering projects with unique landscape features.
Reach a larger audience than ever before
Marine Civils is held in association with Seawork, Europe’s leading commercial marine and workboat exhibition.
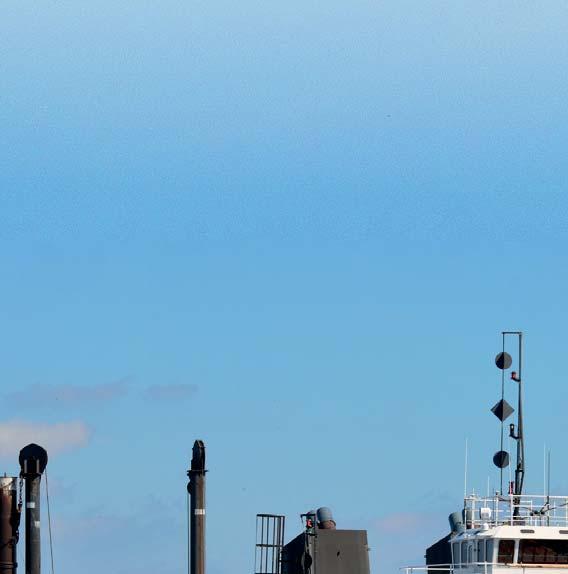
Marine Civils gives exhibitors the opportunity to showcase the latest innovations in equipment and solutions for marine, coastal and other challenging civil engineering projects.
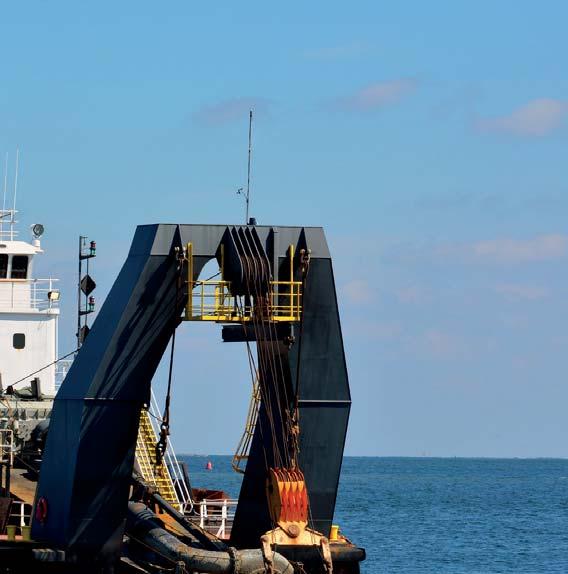
Reserve now for 2023 and make the most of marketing support from Marine Civils, Seawork and our leading commercial marine magazines, in print, online, eNews and via social media.
For more information visit: marinecivils.com contact: +44 1329 825335 or email: info@marinecivils.com
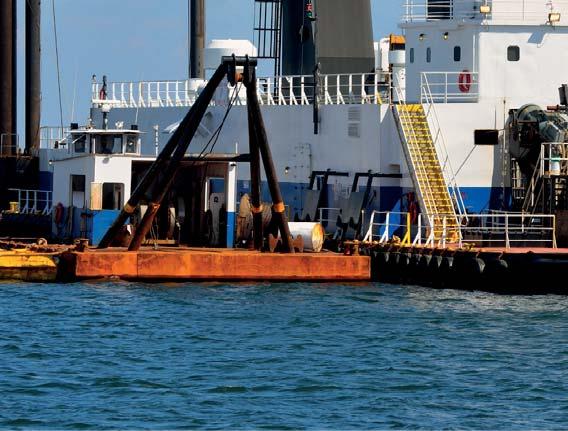
#MarineCivils2023
Organised by:
Media partners: MARITIMEJOURNAL
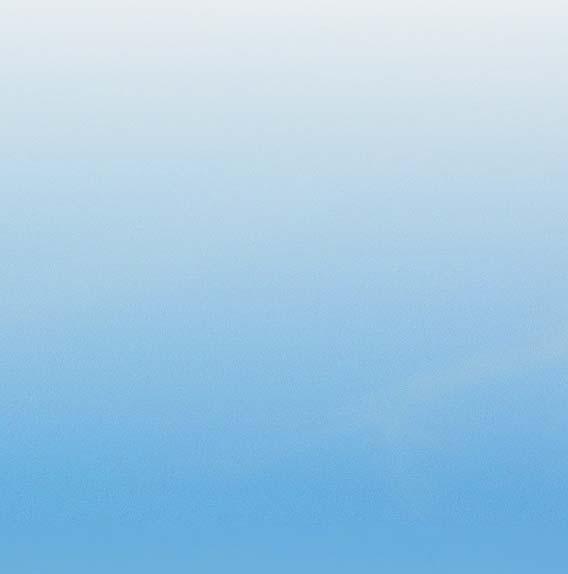
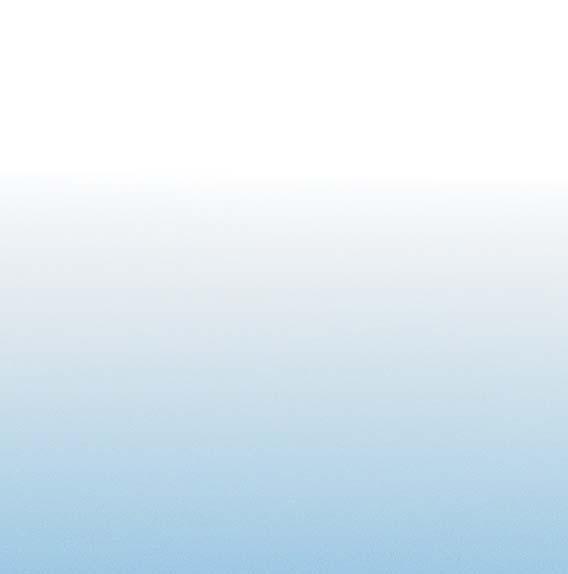