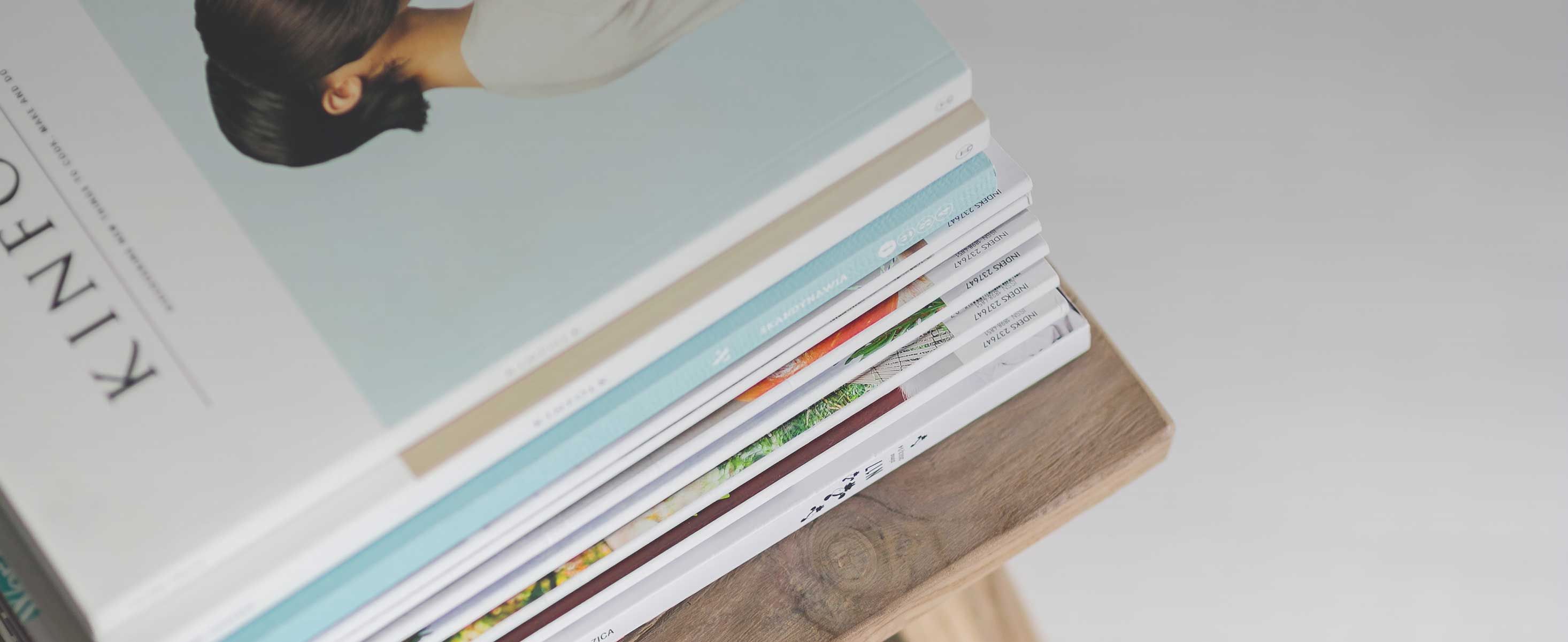
2 minute read
PREVENTING TANKER EXPLOSIONS
The March 1973 issue of The Motor Ship included no fewer than four special supplements: Marine Automation, Worldwide Fishing, Prevention of Tanker Explosions, and a look at three Austin & Pickersgill designs for standardised cargo ships.
It was the subject of tanker safety that was exercising our editorial predecessors at the time. Following the 1969 explosions on the VLCC Mactra and two other similar vessels, the Court of Inquiry was recommending the fitting of inert gas systems to all tankers with cargo compartments exceeding 10,000m3. This echoed a recommendation by the International Chamber of Shipping (ICS) and Intergovernmental Maritime Consultative Organization (IMCO) for installation of inert gas and deck-froth systems for new crude carriers exceeding 50,000 dwt. A leading article noted that if the ICS/IMCO recommendation became mandatory, over 1000 tankers would need to be equipped, at a cost of some GBP 300,000 each – even at 1973 prices. With only 20 or so companies worldwide making such systems, the supply and demand equation would prove highly problematic, albeit profitable. In fact, a similar situation to that which arose around ballast water treatment systems many years later. The Court of Inquiry recognised this, saying that retrofits should be carried out “subject to the capacity of the shipbuilding and repairing industry.” Nevertheless, the topic was considered well worth a comprehensive survey of the economics, problems and methods of explosion prevention by inert gas and other methods.
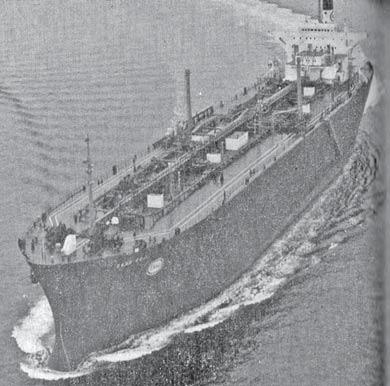
Three engines recently demonstrated by Burmeister and Wain were examined in some detail, being considered suitable for “modern demands” of the industry. The K90GF, forerunner of a range of five new low-speed engine size, had already secured a large number of orders through licensees worldwide, mostly for large tankers. It was designed for a high power output from the size and weight of the engine, as well as long service intervals, well in advance of competing engines. The K90GF was seen as having the potential to compete with steam turbines for the new generation of ULCC and container ships beginning to enter service.
The other new engines were the U50HU medium speed engine, similarly attracting pre-production interest and expected soon to be followed by the 1500bhp/cylinder 60P, while another four-stroke, the high speed U28L was well advanced in its initial testing.
As far as the actual ships were concerned, one notable vessel reported on in March 1973 was the Esso Fuji, said to be the largest LPG carrier to enter service. Built in Japan by Hitachi Zosen, the 100,000m3 234m long ship carried liquefied butane and propane gases at atmospheric pressure and low temperature in insulated prismatic tanks. Cargo handling relied primarily on shore equipment to handle vaporisation during loading and unloading, though a reliquefaction plant was installed onboard to provide partial vapour requirements when shore systems were not available. Machinery comprised a Hitachi-B&W 8K84EF main engine rated 20,000 bhp at 114 rpm driving a four-blade fixed pitch propeller, proving a service speed of 17.6 knots. Four HitachiB&W 826MTBH40 auxiliary diesels provided the high levels of electrical power needed for the cargo and other systems.
Another Hitachi yard, that at Sakai, was building a series of economical 260,000 dwt standard oil tankers, notable for the attention paid to prevention of corrosion, with epoxy-type paints employed for the hull, topsides and cargo tanks with chlorinated rubber protection on the decks. Main and auxiliary machinery was all steam-powered, with a Hitachi UA-360 two cylinder impulse cross compound turbine of 35,000 hp coupled to a five-blade propeller, plus two Fuji Electric 1320kW alternators driven by single-cylinder back-pressure steam turbines.
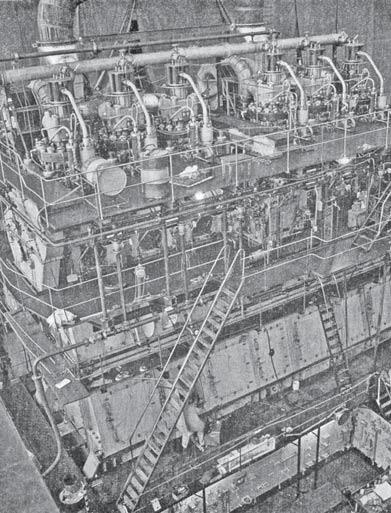
The international magazine for senior marine engineers
EDITORIAL & CONTENT
Editor: Nick Edstrom editor@mercatormedia.com
Correspondents
Please contact our correspondents at editor@motorship.com
Bill Thomson, David Tinsley, Wendy Laursen
SALES & MARKETING
Brand manager: Sue Stevens sstevens@mercatormedia.com Tel: +44 1329 825335
Production David Blake, Paul Dunnington production@mercatormedia.com
EXECUTIVE
Chief Executive: Andrew Webster awebster@mercatormedia.com
TMS magazine is published monthly by Mercator Media Limited Spinnaker House, Waterside Gardens, Fareham, Hampshire PO16 8SD, UK t +44 1329 825335 f +44 1329 550192 info@mercatormedia.com www.mercatormedia.com
Subscriptions
Subscriptions@mercatormedia.com Register and subscribe at www.motorship.com
1 year’s digital subscription with online access £222.00
For Memberships and Corporate/multi-user subscriptions: corporatesubs@mercatormedia.com
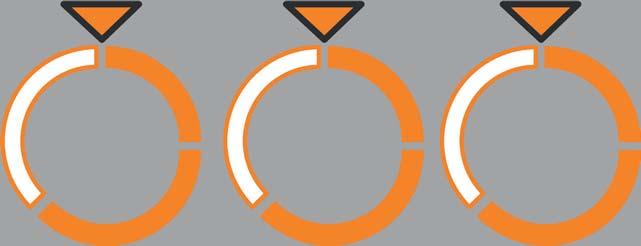