

Clear route ahead
Two-stroke solutions for the future of shipping
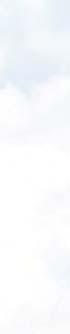
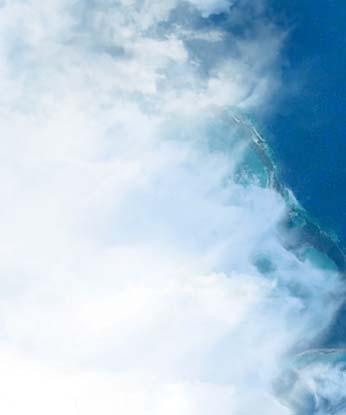

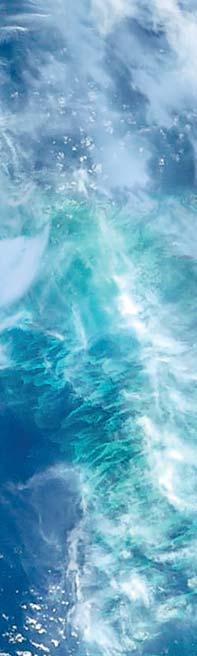


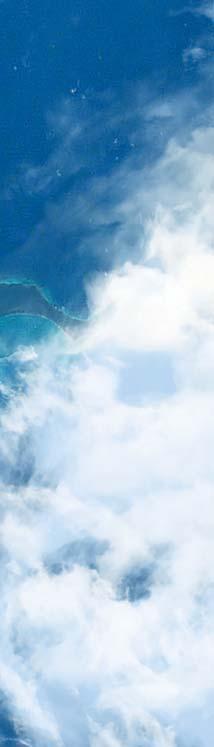
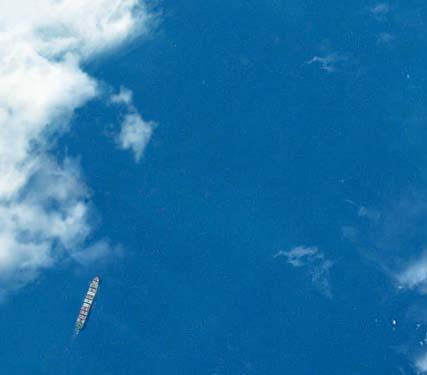
Navigating new regulations, decarbonization, and complex fuel economics is easy with us as a partner. Our two-stroke

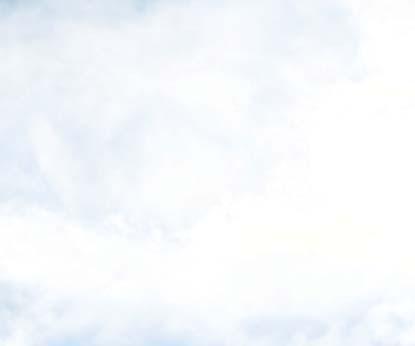
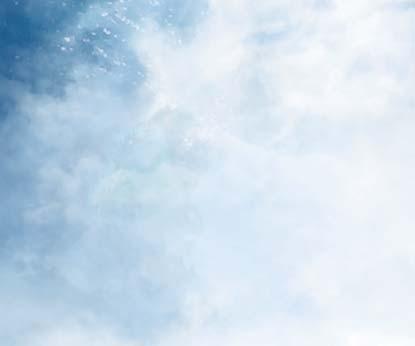

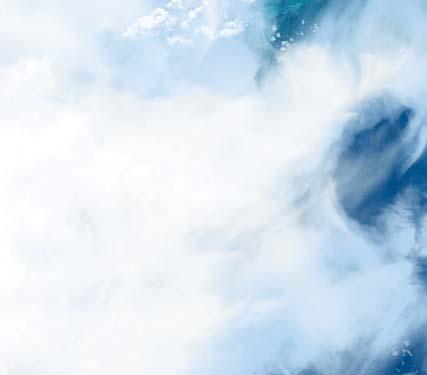
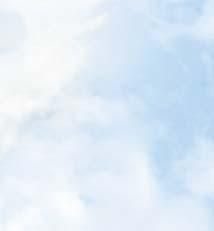
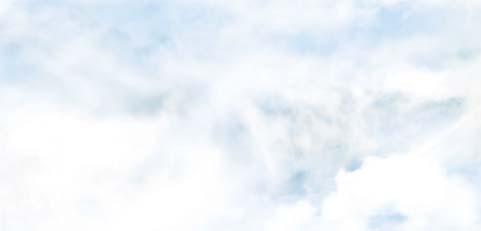

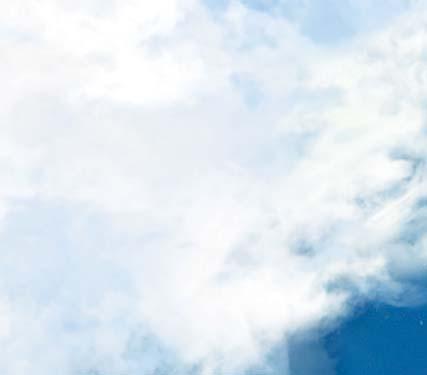

of millions of running hours and assistance that goes beyond installation and commissioning: Complete life-cycle support from our dedicated staff and the worldwide MAN PrimeServ after-sales network.
Clear route ahead – with MAN B&W two-stroke solutions.
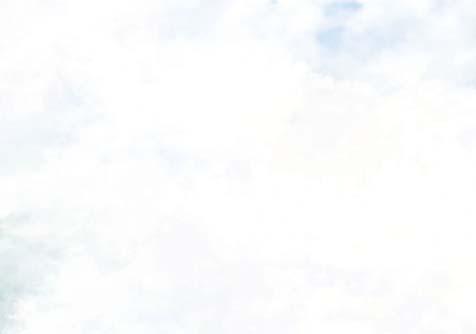
HHI-EMD’s new H32DF-LM
been
landmark
China Classification Society (CCS) and Dalian COSCO Shipping Heavy Industry held an ignition ceremony for COSCO’s first ammonia powered duel-fuel test engine.
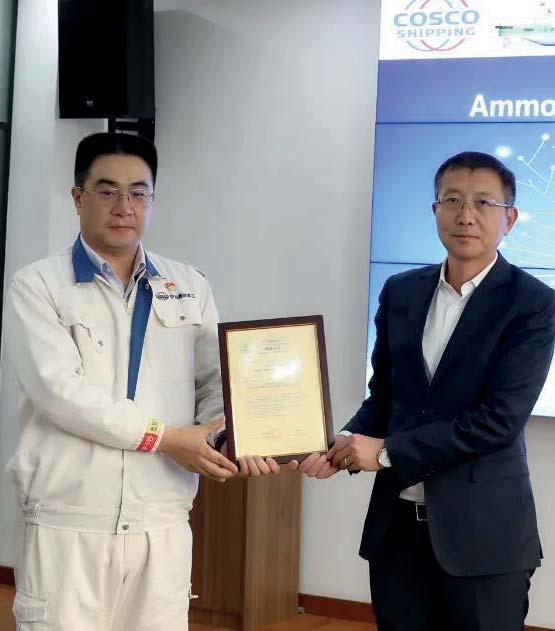
Onboard CCS trial
Sinotech CCS Co. Ltd., a Shanghai-based developer of carbon capture solutions, plans to install its first CCS unit onboard an Asian owned vessel by November 2022.
REGULARS
8
Regional Focus
While German maritime technology and shipping retains global influence, the country’s shipbuilding industry is at a crossroads, facing new uncertainties, writes David Tinsley.
14 Immutable laws
The laws of thermodynamics will limit battery-hybrid and fuel cell applications in deep-sea shipping, Duncan Duffy, Global Head of Technology, Electro Technical Systems, at LR tells The Motorship.
22 Hybrid propulsion concepts
MAN ES and ABB have teamed up to develop a dual-fuel, electric+ (DFE+) propulsion concept for LNG carriers.
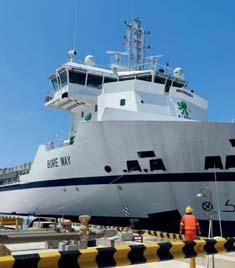
28 One step beyond
Studies are pointing to the viability of onboard carbon capture and storage (CCS) technology for some ship types, but even in the best cases, CAPEX and OPEX are expected to be high.
Leader Briefing Georgios Plevrakis, ABS Vice President, Global Sustainability discusses carbon pricing and its effect on the maritime sector in an exclusive interview with The Motorship.
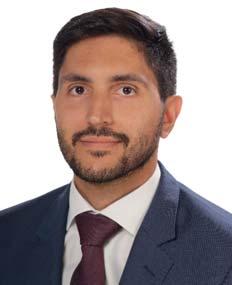
Ship Description
A new class of Chinesebuilt ships for the Baltic forestry products industry combine cargo carrying flexibility with a reduced carbon footprint, writes David Tinsley.
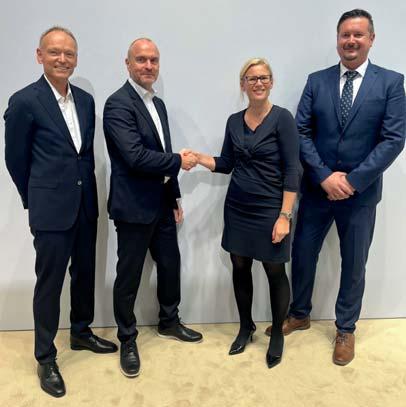
32 Boundary conditions
The IMO is considering how it can incorporate a well-to-wake (WtW) approach into the assessment of future fuels.
38 Hammer time
Ulstein has designed a ship built to house a thorium MSR reactor, Catherine Kristiseter Marti, Ulstein Group CEO tells The Motorship.
The Motorship’s Propulsion and Future Fuels Conference will take place this year in Hamburg, Germany. Stay in touch at propulsionconference.com
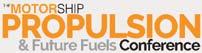
PROPELLER BLADE UPGRADE CUTS FUEL CONSUMPTION
VIEWPOINT
NICK EDSTROM | Editor nedstrom@motorship.comA hat tip
Writing ahead of our upcoming Propulsion and Future Fuels conference, which will be held in Hamburg in late November, I wanted to reflect on the alternative fuels space, as methanol and soon ammonia engines appear ready to change the face of the market.
It is worth reiterating how fortunate the shipping industry has been to have been so well served by forward thinking class societies, engine designers and of course ship owners over the last few years. Just because they have succeeded in making the remarkable appear routine should not blind us to the scale of the industry’s achievements in recent years.
No less remarkable is the ongoing expansion of the fuel mix to encompass methanol, and soon ammonia. These are significant achievements for an industry that has sometimes been unfairly characterised as resistant to change.
The Propulsion and Future Fuels event has been a long-term proponent of ammonia and methanol as alternative fuels, just as it championed LNG during the earliest stages of its commercialisation in the early 2000s.
The sheer range of fuel combustion solutions that are being developed is astonishing. In this issue alone, we cover the launch of Dalian COSCO Shipping Heavy Industry’s four-stroke dual-fuel ammonia-powered test engine in October; Hyundai Heavy Industries-Engine & Machinery Division’s successful test of an LNG and hydrogen fuel mix; and Volvo Penta’s decision to commercialise a hydrogen-injection solution on a small scale.
Early stage research into alternative fuel combustion is continuing, including a UK pure-hydrogen recuperated split cycle engine-based project involving Dolphin N2, Brighton University and Hiflux.
The fate of some of these solutions is likely to depend on the scope of regulations that are being discussed at the moment. We cover the argument about well-to-wake emissions, as well as the economics of carbon markets again this month.
The energy politics of different fuels, such as methanol, is another fascinating area. China’s position here is interesting: Sinopec has played a leading role in the development of domestic carbon capture use and storage (CCUS) schemes since China confirmed plans to introduce a domestic Emissions Trading Scheme (ETS), which came into force in July 2021.
Sinopec is also expressing an interest in recycling liquefied carbon dioxide from onboard CCS units, according to an interview with Sinotech CCS, featured in this month’s magazine.
Returning to the technological arena, delegates at this month’s PFF event should expect to see interesting technical developments in a range of areas. Just to pick one OEM, the steady expansion of FuelSave’s combustion optimisation solution across various 4-stroke engine solutions remains an example of a technological solution that we have followed closely since the late 2010s.
We have covered the development of battery-hybrid dual-fuel solutions for deep-sea commercial vessels previously. This issue sees the introduction of a new project: ABB is bringing its experience with DC grids to bear in a new collaboration with MAN Energy Solutions on a dual-fuel, electric+ (DFE+) propulsion concept for LNG carriers.
Berg Propulsion has secured a substantial reduction in fuel consumption and vibration for a long-serving Baltic ferry, after a propeller blade replacement.

Stena Danica entered service in 1983 and was fully renewed in 2005. It sails between Sweden and Denmark, connecting the ports of Gothenburg and Frederikshavn in just three hours and 30 minutes.
Last year, Stena Line asked Berg Propulsion to revise the 154.9m length ship’s twin propeller blades, with the aim of eliminating a persistent cavitation issue and enhancing fuel efficiency in a single project. In an additional technical challenge, Berg’s solution needed to be reverse engineered to fit with the existing propeller hub originally manufactured by another company.
“Stena continuously reviews the performance of its ships to evaluate whether machinery and systems on board are optimal for their actual operations,” said Per Wimby, Senior Naval Architect, STENA TEKNIK. “This is actually the third propeller blade replacement undertaken on Stena Danica over the years but this one is especially timely, given that it anticipates new regulatory requirements for all ships to demonstrate their energy efficiency.”
Stena Danica’s twin control pitch propellers are served by two Sulzer 12ZV40 medium speed engines per shaft. After several months of commercial operations in multiple sea states, Wimby confirmed that using the new propeller blades has reduced
average fuel consumption while neutralising a longstanding issue with vibrations. “It is a balance between efficiency and comfort onboard,” he said.
Victor Abrahamsson, After Market Business Development, Berg Propulsion, said that blade design had been optimized to reflect a planned reduction in operating speeds, in a compromise between one engine per shaft line running at full power or two engines running per shaft, without ‘overpitching’.
“Blade geometry has moved on quickly in recent years, based on more accurate calculations, 3D scanning and better modelling tools. Today, we make better use of materials so that the same or enhanced efficiencies are achieved using slimmer profiles and blades which cover less area. It’s also much easier to evaluate and predict the relative performance of different blade types.”
Magnus Thorén, Energy & Efficiency Account Manager, Berg Propulsion, said: “With fuel consumption so high on the agenda, we are putting all available tools at the disposal of our owner clients to secure the efficiencies they need. That means delivering tailor-made solutions for specific ship operating profiles, but this project also demonstrates what’s possible using the existing propeller hub: our designers and shipyard project teams could do this for any hub.”
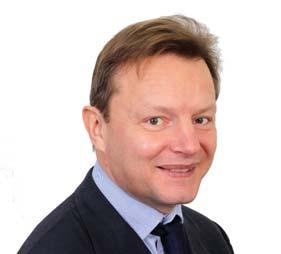
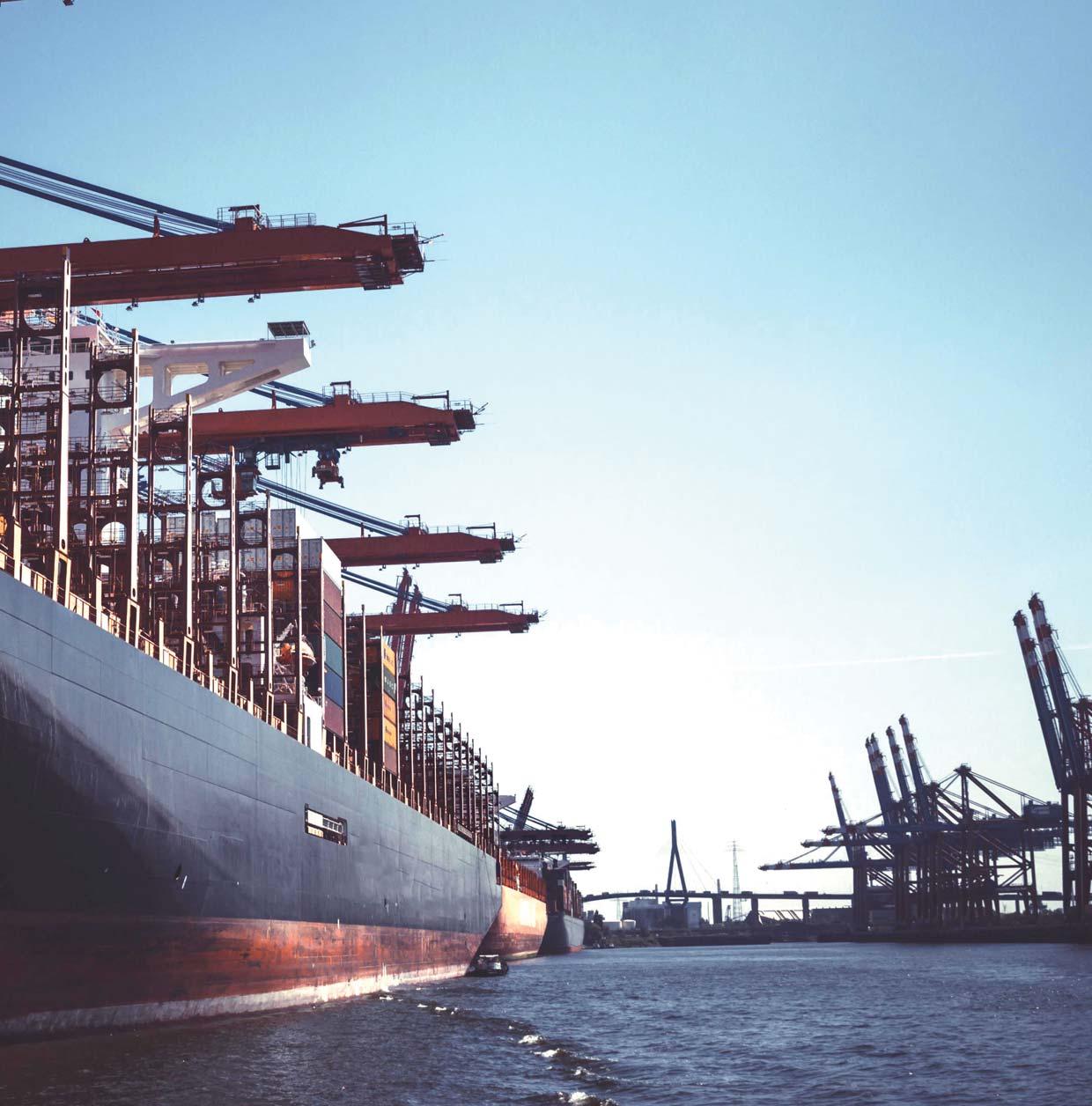
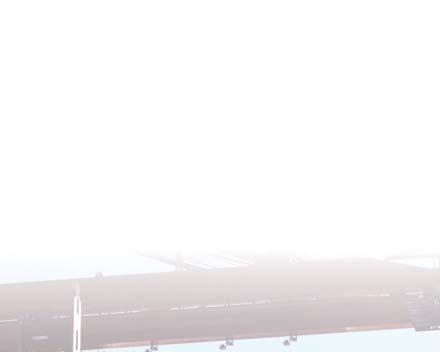
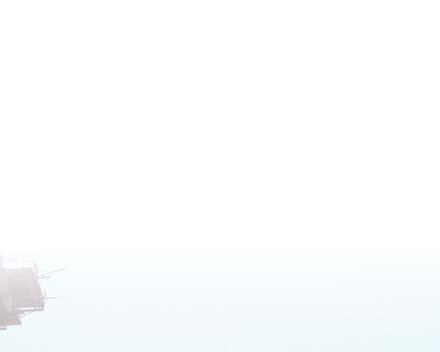
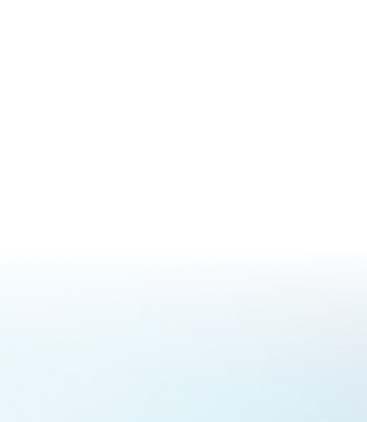
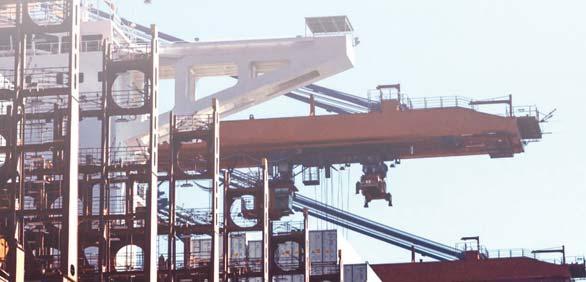
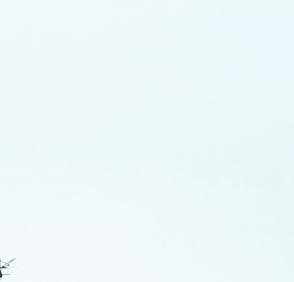
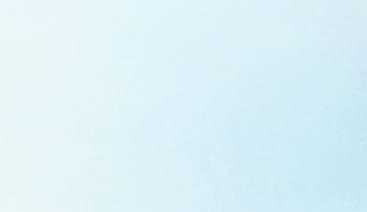

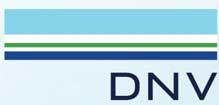
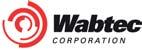


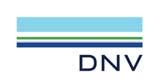




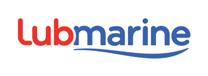
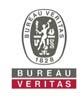
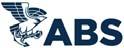
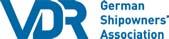

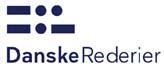


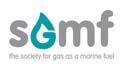
Hyundai Heavy IndustriesEngine & Machinery Division’s new methanol dual fuel HiMSEN engine has completed type approval testing with seven class societies including KR, ABS and DNV.
The H32DF-LM, 4,000~6,000bhp was tested at the company’s Techno centre in Ulsan, South Korea.
The diesel/methanol genset significantly reduces GHG emissions, SOx and NOx. In addition, it prevents corrosion by using special materials and achieves stable high-power production by applying diesel cycle combustion and electronically controlled fuel injection (Common Rail) technology.
The first methanol HiMSEN engine will be delivered to the
HHI-EMD METHANOL ENGINE GAINS TYPE APPROVAL
2,100TEU container vessel that is built by Hyundai Mipo Dockyard in December. So far, 50 engines (13 vessels) have been ordered. HHI-EMD expects demand to increase.
Hyundai Heavy Industries has announced that its new engine factory can now produce 100 sets of HiMSEN engines per year.
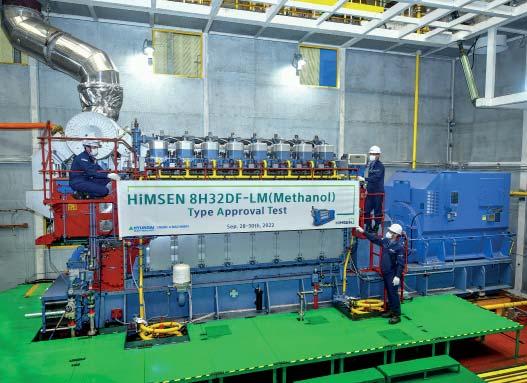
Hyundai Engine Company has a plan to supply the dual-fuel engines to the domestic and foreign major shipbuilder such as Hyundai Samho Heavy Industries.
Ammonia development project
Svanehøj’s deepwell fuel pump has been chosen for a development project which aims to develop ammonia-fuelled vessels with 4-stroke auxiliary engines.
The company said that among the partners in this project is one of the world’s largest shipyards and one of the leading manufacturers of marine engines.
“A development project such as this is a great opportunity for us to show that Svanehøj is part of the solution to the climate challenge of shipping,” said Markus Tauriainen, sales director, fuel, Svanehøj.
a fuel pump solution for this project, we will contribute further to the ongoing fuel transition.”
Fully compatible According to leading companies in the shipbuilding industry, the most likely initial newbuild targets for ships utilising ammonia fuel will be container vessels and very large crude carriers. These vessels operate with 2-stroke main engines and 4-stroke auxiliary engines and Svanehøj has a strong ambition to become the preferred supplier of pump systems for these ships.
BRIEFS
SOFC trial on LNGC
Shell has signed a deal to power an LNG carrier with a HyAxiom-developed solid oxide fuel cell (SOFC). Under the agreement, Shell International Trading and Shipping Company, KSOE, DNV and Doosan Fuel Cell, agreed to launch a vessel powered by a SOFC in 2025. Doosan Fuel Cell says the low temperature SOFC it is currently developing has up to 65% efficiency, reduces noise and vibration and lowers maintenance costs.
”At Svanehøj, we have been working to develop solutions for future fuels for years. By supplying
BV AiP for GTT
Bureau Veritas has awarded an Approval in Principle to GTT for a new LNG carrier design based on a three cargo tanks arrangement. The new 174,000cbm design replaces a 4-tank configuration with a 3-tank design. The innovative new design is expected to reduce the boil-off gas (BOG) below 0.085% while reducing the operational costs for the gas carrier. The concept is designed to fit either with Mark III or NO96 technologies, developed by GTT.
Svanehøj’s fuel pump is a long-shafted cryogenic deepwell, multistage centrifugal pump, launched in 2016. It is
WinGD Qatar order
WinGD has received 25 orders for its dual-fuel X72DF-2.1 engine featuring its new onengine iCER , the company announced. The orders for 50 engines have been placed by multiple shipyards and shipowners in connection with QatarEnergy’s NFE project. The order includes a pair of LNGCs at Daewoo Shipbuilding & Marine Engineering (DSME), the first ships to be built by DSME featuring WinGD’s on-engine iCER.
described as a smaller version of Svanehøj’s well-proven deepwell cargo pump for gas, which has been installed on more than 1,100 gas carriers since the 1960s.
All the benefits of the larger cargo gas pump have been retained in the deepwell fuel pump, ensuring stability, optimised performance, high reliability and long service intervals.
The Svanehøj deepwell pump enables a ship to comply with both current and future requirements as the pump is fully compatible with all types of liquid gas fuels, including LNG, LPG, ammonia, methanol and hydrogen.
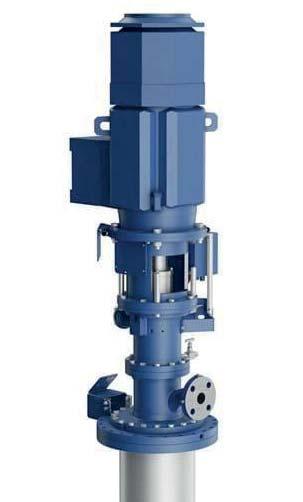
Damen eyes OPS
Mc Energy and Damen Services have signed a collaboration agreement to bring a shore power solution to market. Damen B-Shore can supply multiple voltages and switch between 50Hz and 60Hz networks. This means that every on-board network can be linked to a local network. B-Shore also absorbs any instability of the local grid and provides a safe separation between shore and ship, thus avoiding galvanic corrosion.
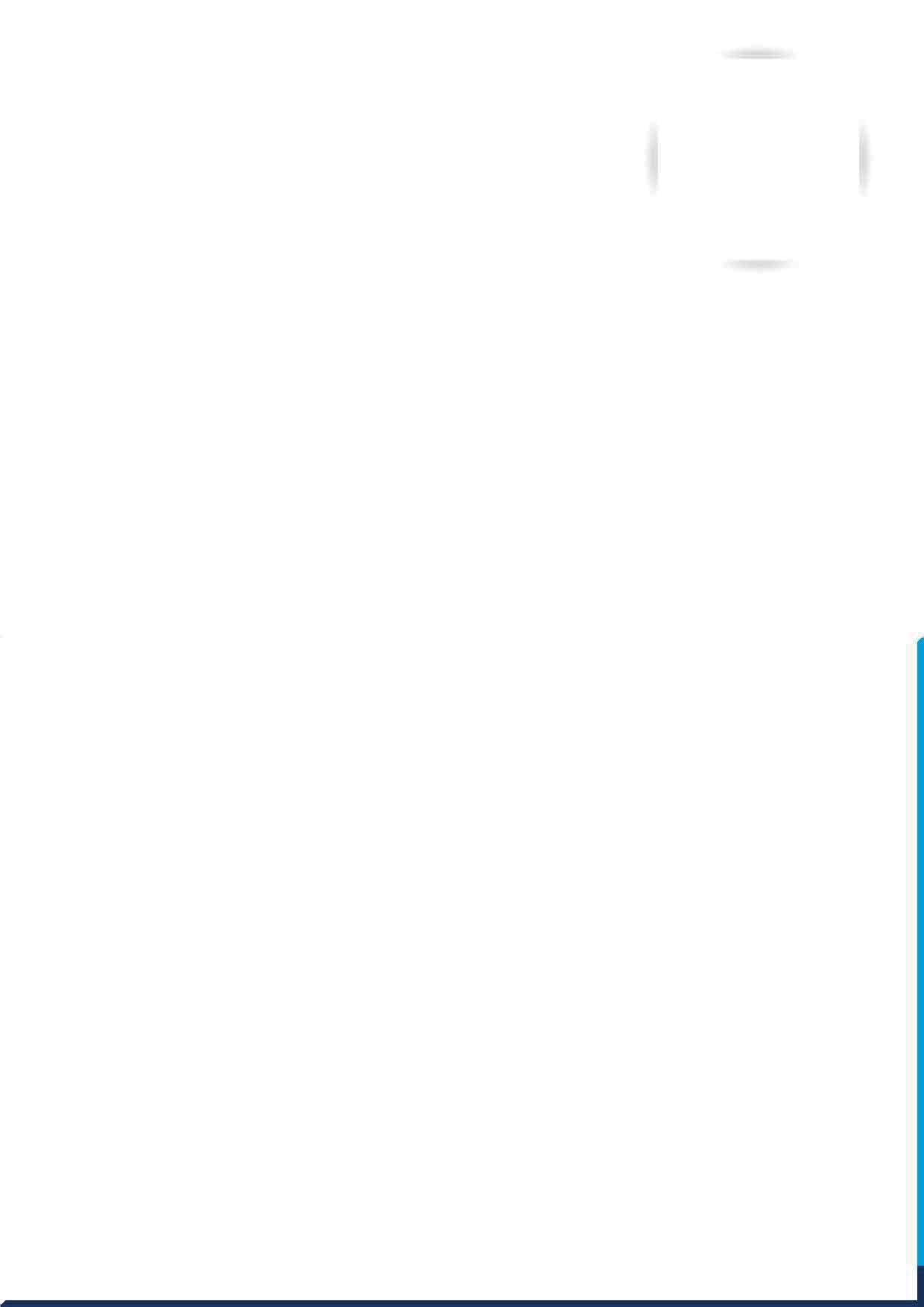

GERMAN YARDS ADJUST TO NEW REALITY
Bearing the scars of the Covid-19 onslaught, yards have maintained production continuity, albeit at lower levels than earlier, and delineated new business strategies aimed at conferring greater resilience and competitiveness in the years to come. But a large swathe of the sector, through the failure of Genting-owned MV Werften, has been taken out of the immediate reckoning as regards large-ship construction and export earnings. At the same time, recent changes in shipyard ownership together with fresh collaborative ventures, acting on new or unfolding opportunities, promise to re-energise some shipbuilding communities.
At a presentation held earlier this year, the Association of German Shipbuilders & Maritime Technology Suppliers(VSM) sounded a stark warning as to the future of the shipbuilding industry in Germany, and in Europe as a whole. Although global demand for newbuilds is robust, Asian yards not only attract the preponderance of contracts for all main categories of merchant shipping, with an increasing adeptness in newgeneration ‘green’ tonnage, but are also securing a growing proportion of the orders for more specialised vessels. Moreover, China’s domination now of the market for ro-ro and ro-pax tonnage is accompanied by its emergence as a cruiseship builder, a move that is in fact being technologically assisted by European organisations.
The VSM contends that China and South Korea are posing ‘unfair’ competition, engendered through both overt and covert support and financial mechanisms on the part of their
respective governments. The industry body suggested that shipbuilders in Europe could disappear altogether in just 10 years’ time if the European Commission and individual EU countries do not address the situation.
While EU action is still absent in response to the industry’s travails and its calls for a ‘level playing field’, the German Federal Government has displayed some acknowledgement of concerns through the announcement in August 2022 of a new package of financial support. This entails increased funding towards ‘green’ shipping, encompassing the development of environmentally-friendly maritime technology and construction of zero-emission ships. An additional EUR 30m ($29.2m) per year will be made available for such initiatives through to 2025.
Backing for investment by the shipbuilding industry in digital technology was contemporaneously expressed by clearance for a EUR 1.3m ($1.27m) state grant towards an ambitious research project to enhance shipbuilding production technology. The goal of the initiative, entitled “Digitisation of cold-plastic forming through continuous quality control”, is to provide a means of inspecting the surface of the sheet metal with the aid of sensors and to digitally record the forming process in 3D format so that manual intervention can be reduced. Downtime on pressing machines could be reduced by approximately 35%.
The Meyer Group, whose Papenburg fully-enclosed ‘ship factory’ is the jewel in the crown of the country’s commercial
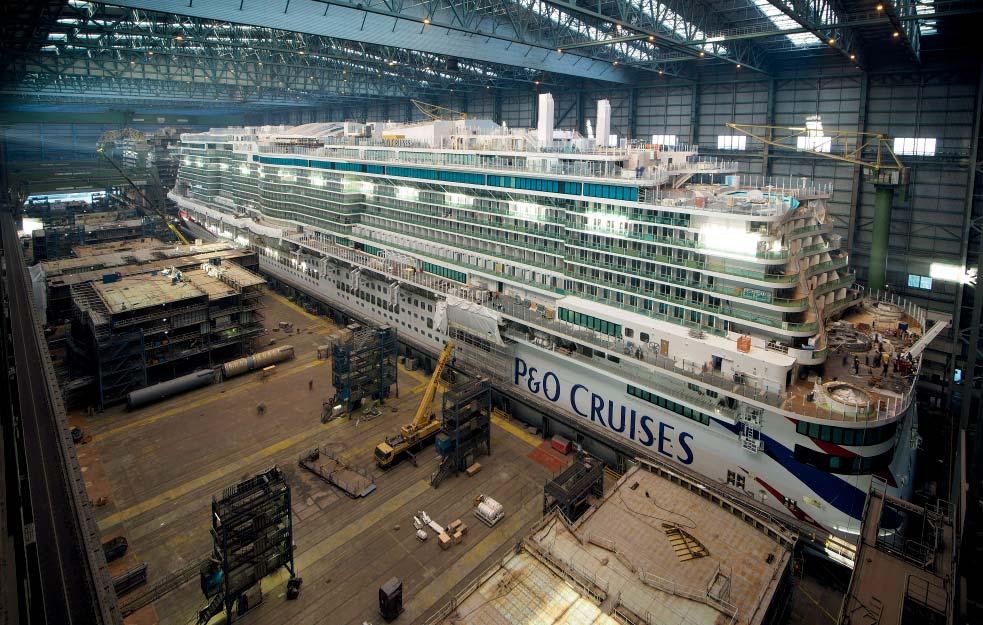
While German maritime technology and shipping influence continues to show its mettle on the world stage, the country’s shipbuilding industry is at something of a crossroads, facing new uncertainties, writes David TinsleyCredit: Meyer Werft
shipbuilding sector, was in the process of implementing a plan to expand annual throughput and deliveries at all three of its yards in Germany and Finland prior to Covid-19. Moreover, a EUR260m ($253.2m) investment programme at the Finnish subsidiary, Meyer Turku, had been completed just before the outbreak of the pandemic. The expenditure at Turku has come to represent a cost burden on the group against the backcloth of the subsequent fall-off in orders.
While the pre-pandemic cruiseship newbuild workload at both Papenburg and Turku was retained, through renegotiations with clients leading to ‘stretched’ delivery times, this has been at the expense of a reduction in annual production volume and earnings.
Meyer Werft distinguished itself yet again last year by attracting two of the handful of contracts awarded worldwide for cruiseship tonnage, winning a medium-sized, 229m newbuild for Japan and a 289m apartment vessel for Norwegian-American interests. Nonetheless, the work inflow at Papenburg has not been enough to sustain pre-Covid utilisation rates, and shipyard utilisation will remain at a restrained level unless more orders can be attracted.
Since the minimum time from contract signing to delivery of a high-capacity cruise ship is approximately three to three and a half years, Meyer Werft needs to secure fresh contracts by early 2023 at the latest.
Although cruise ship construction will remain the core business of Meyer Werft and the Meyer Group as a whole, the family-controlled group has taken steps to expand and diversify its offering. As well as providing for more ‘one-off’ cruise vessels and also smaller sizes of ship, the revised strategy targets government vessels(such as research ships and naval auxiliaries) and mega yachts at the uppermost end of the scale. A dedicated division, Meyer Yachts, has been created to focus on newbuilds of more than 120 metres in length. Meyer has also entered into a joint venture addressing what is viewed as an emerging market for the production of floating real estate. The new entity, Meyer Floating Solutions, is headquartered in Turku.
Meyer and compatriot shipbuilder Fassmer strengthened their cooperation this year through the joint acquisition of Neptun Ship Design, previously part of MV Werften. The takeover signifies a strengthened focus by Meyer and Fassmer on the development of highly complex, specialised ships, which represent a key target market for both shipbuilders.
Cooperation between Meyer and Fassmer is already expressed in the contract for the new research ship Meteor IV, ordered by the Federal Ministry of Education and Research at the beginning of 2022. Due for handover by 2026, the newbuild is of some 10,000gt and has a length of approximately 125m, and will accommodate 35 scientists plus 36 crew.
To draw added value from its core business in the construction of cruise ships, the Meyer Group has created a new company, Meyer Re, which will offer service packages to maintain, refurbish and technologically update Meyer-built vessels throughout their operational life.
Both Genting Hong Kong and its German shipbuilding subsidiary MV Werften, with shipyards at Wismar, Stralsund and Rostock-Warnemuende, filed for bankruptcy in January 2022, leading to insolvency proceedings under an administrator appointed on March 1. The financial hiatus, compounded by the Covid pandemic, also hit the parent group’s cruise ship companies, and this had further impact on the German shipbuilding orderbook as various Genting entities and brands were the only customers of MV Werften.
However, the industrial fabric in Germany may to a large extent be saved through re-purposing of former MV Werften yards, with the accent on the naval market and on German
intent to raise defence spending in the light of Russia’s invasion of the Ukraine and aggressive stance towards the West. The purchase of the former MV Werften-owned Wismar shipyard by thyssenkrupp Marine Systems in June 2022 was quickly followed by the Federal Government’s acquisition – effectively nationalisation – of the Rostock-Warnemuende facilities.
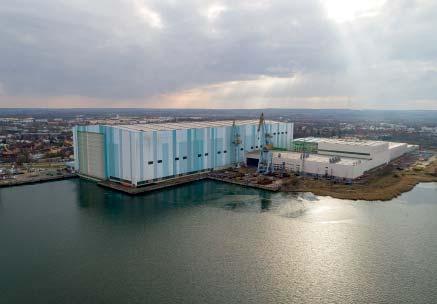
Defence contractor thyssenkrupp Marine Systems considers that business opportunities in its key target sectors offer a long-term future for shipbuilding at Wismar, and holds out the prospect of submarine construction being implemented at the site in 2024. Meanwhile, revival of the Rostock yard under state control is expected to involve its transformation into a naval arsenal, with the possibility that portions of the yard may be leased out or dedicated to commercial and offshore-related activities.
Genting’s troubles also had an impact elsewhere in Germany. Shortly after MV Werften filed for bankruptcy, Lloyd Werft Bremerhaven – controlled by the Genting Group since 2015 – took the same step. Within the space of two months, new buyers were found, and the yard was reinstated as Lloyd Werft Yachts, with a primary role in mega-yacht newbuilding, refit and conversion. The purchasers are two German companies, the Heinrich Ronner Group and the Zech Group.
In the meantime, commercial shipbuilding has been revived in the northwest German town of Flensburg. The launching of a 4,000 lane-metre ro-ro freight vessel from Flensburger Schiffbau-Gesellschaft (FSG) in June this year was the first since the yard’s re-start, following its purchase out of insolvency by the Lars Windhorst-headed company Tennor Holding in 2020.
FSG is chasing the long-discussed plan for a large, new German icebreaking research ship, and sees benefit in the proposed creation of a shipyard consortium to attract the complex newbuild project. In line with the company’s plan to enter the luxury super-yacht sector and naval market, Tennor/ FSG purchased the insolvent Werft Nobiskrug during 2020.
The Nobiskrug yard at Rendsburg has now been brought under the management of FSG at Flensburg, to streamline operations and resources at the two yards.
A new project was announced in August 2022 with Canadian transport company Oceanex. This combined FSG’s expertise in ro-ro equipped vessels with another strand of the shipyard’s re-defined strategy, whereby newbuilds will incorporate comprehensive life-cycle analysis and planning. The agreement with Oceanex calls for the joint development of an innovative design of ice-classed, container/ro-ro(con-ro) vessel for eastern Canadian trade. This is designed to be ultra-efficient and “climate-neutral”.
The Flensburg yard delivered a tailor-made vessel to Oceanex in 2013, in the shape of the 210-metre, 19,460 dwt con-ro Oceanex Connaigra, which carries containers, trailers and motor vehicles between Montreal and Newfoundland.
ALLOW THE MARKET TO SUPPORT THE DECARB JOURNEY
8 Carbon economics at work: Sinopec completed the construction of China’s first large-scale carbon capture, utilization and storage (CCUS) project at Shengli Oilfield in January 2022, six months after China introduced a national Emissions Trading System (ETS) in July 2021
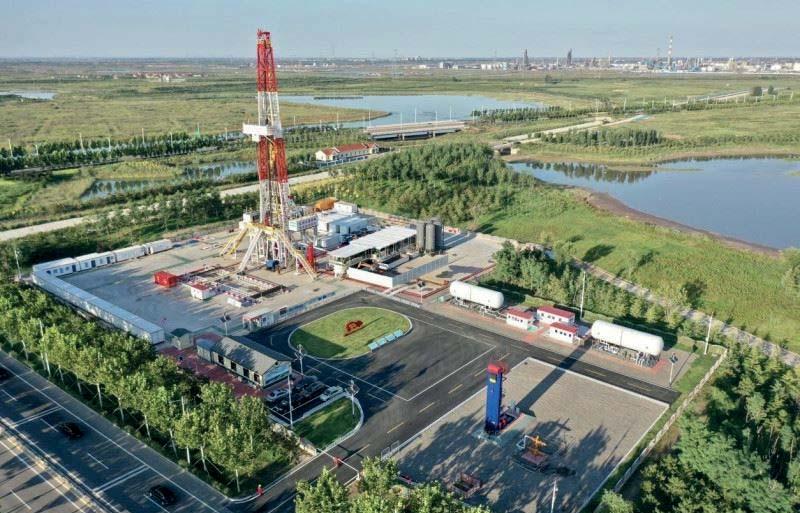
Georgios Plevrakis was keen to discuss the practicalities of carbon pricing when he was interviewed by The Motorship at SMM. Although many of the specific decisions around the scope of regional and international schemes, such as the EU’s Emissions Trading System (ETS) extension and the FuelEU Maritime proposal have not yet been finalised, Plevrakis noted that many of the specific issues had been identified and discussed.
“We’ve been discussing these issues for over two years,” he said, referring to specific issues that carbon pricing had to confront from a maritime perspective, including identifying where the ultimate responsibility for carbon emissions sits from a producer-pays perspective, as well as where the decision-making responsibility for operational decisions lies.
As editor of ABS’ latest publication in its Setting the Course to Low Carbon Shipping series, Plevrakis also noted carbon pricing would play an important role in creating the conditions for the emergence of hydrogen and carbon value chains.
Plevrakis looked beyond some of the short-term discussions to look at how the potential introduction of carbon pricing will affect the operation of shipping markets.
The appeal of carbon pricing for the industry is that it actually creates opportunities for ‘first movers’, and directly benefits operators who champion efficiency and adopt solutions earlier, Plevrakis noted. This will accelerate the adoption of clean technology solutions in the industry.
Plevrakis noted that the rules need to be predictable,
transparent and applicable, in order to encourage adoption by the maritime industry as well as the wider industrial complexes upon which the maritime sector will need to coordinate with it.
The success of the introduction of carbon capture use and storage (CCUS) supply chains will depend upon other hardto-abate sectors, such as cement manufacturing, steel making and other non-ferrous metallurgical sectors, adopting CCUS technology.
Clarity around these issues is vital in order to stimulate the development of technological solutions. “We need a standardised approach towards the sustainability aspects of [these] different areas.”
Taking a broader perspective, such schemes are expected to help to raise funds for both the development of solutions that are at pre-commercial stages of development, and help to support the cost of developing supply-side infrastructure.
Any assistance would be welcomed by the industry in the current economic environment. The annual cost of investing in the infrastructure required for the energy transition was likely to be between USD30 billion and USD60 billion over the next 30 years.
Returning to the issue of regulation, and taking the EU’s regulatory efforts as an example, Plevrakis cited the FuelEU Maritime scheme and the extension of the Emissions Trading System (ETS) to shipping as areas where a carbon price would be defined.
Georgios Plevrakis, ABS Vice President, Global Sustainability discusses carbon pricing and its effect on the maritime sector in an exclusive interview with The Motorship at SMM in September 2022
“The ETS creates a delta that can be traded, while the FuelEU Maritime scheme introduces a financial penalty, but both should help to support the transition,” Plevrakis noted.
The Motorship notes that the establishment of financial liabilities and an international pricing mechanism is also likely to accelerate the development of hedging tools to allow larger operators to manage their financial exposure to carbon prices, although the different bases of the ETS and FuelEU Maritime schemes will complicate basis risk calculations.
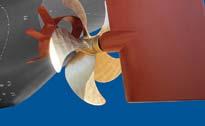
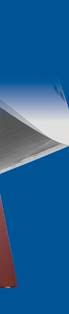

While the ETS and FuelEU Maritime schemes will help to establish financial liabilities for a carbon price for ship owners and operators in the EU, they will not be sufficient to offset the cost differential between alternative fuels and existing conventional fuels.

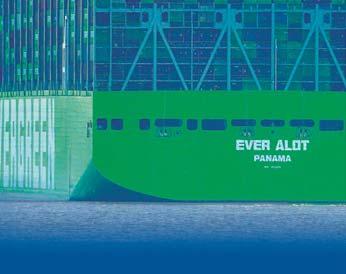
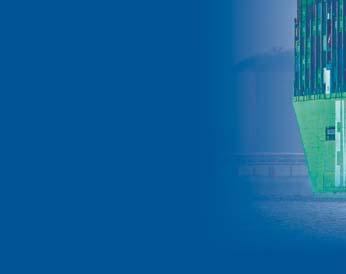
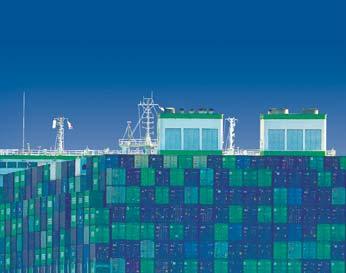

Taking into account the differences in energy density between alternative fuels such as methanol and ammonia and conventional fuels, and the higher production cost of producing alternative fuels, “the carbon neutral fuels that we will be producing will still be less cost efficient than the fossil fuels that we are using today,” he added.
Plevrakis concluded by calling for a carbon-based levy to be introduced on to fuels, in order to narrow the price differential between carbon-neutral fuels and conventional fuels.
Depending upon how the rules are framed, The Motorship notes that the effects of such a carbon levy alter the carbon economics of different fuels significantly. Scandinavian methanol suppliers believe that carbon-neutral methanol produced from renewable energy sources with the addition of recycled carbon dioxide from CCUS schemes could be carbon-positive.
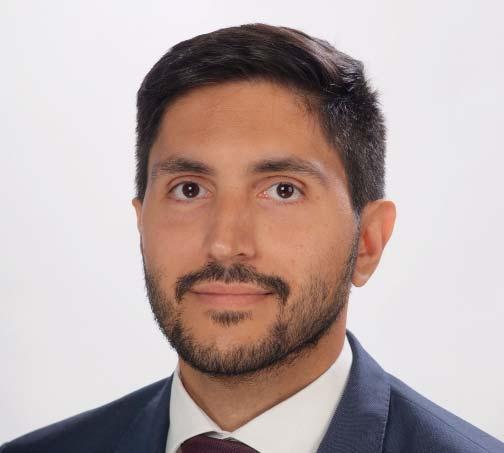
METHANOL RETROFIT COSTS ADD UP FOR CONTAINER SHIPS
Back in August 2021, Maersk announced an order for eight new 16,000 TEU container ships powered by methanol, a move that brought the potential of the fuel to wide attention. Orders for another 10 are expected, and new projects are emerging across the sector, including retrofits
At SMM in September 2022, DNV signed on to a project to study the conversion of a container vessel into a methanol dual fuel vessel along with CSSC, MSC Mediterranean Shipping Company, WinGD – Winterthur Gas & Diesel, and Marine Design and Research Institute of China (MARIC). The project is still in its infancy, but DNV has previously studied the potential of methanol in the sector, noting that the additional CAPEX for installing a methanol system on board a vessel is roughly one third that of the additional costs associated with LNG systems. OPEX for methanol systems is expected to be comparable with that for oil-fuelled vessels without scrubber technology, but experience is limited.

According to DNV, methanol reduces GHG emissions by 8-9 % compared to MGO from a tank-to-wake perspective. It contains no sulphur, and some engine concepts could meet Tier III NOx requirements without after-treatment. Methanol can improve EEDI, EEXI and CII up to 8–9% compared to fuel oil, but in practice the improvement may be less if dwt is decreased or if auxiliary engines are not running on methanol.
Due to its density and lower heating value, methanol fuel tanks need to be approximately 2.5 times larger than oil tanks for the same energy content and 1.3 times larger than LNG tanks. An advantage over LNG, however, is that there’s no need for special materials to handle cryogenic temperatures, and methanol’s low corrosivity means that tanks can be stainless steel or coated carbon-manganese steels.
Risks
Øyvind Skåra, Principal Engineer, Piping Systems & Alternative Fuels, Maritime, at DNV, notes some risks associated with methanol including its low flashpoint which means it generates an explosive atmosphere in air at temperatures above 11oC. “Methanol flames are particularly hazardous, as they burn at low temperatures with a flame that is nearly invisible in daylight, with no smoke,” he said. “A methanol flame often goes undetected until it has spread to adjacent materials that burn in a wider range of light.”
A methanol-water mixture of at least 25% methanol is capable of burning, so fire extinguishing practices include the use of alcohol-resistant foams. A fixed fire detection and fire alarm system complying with Fire Safety System Code should be provided for all compartments containing a methanol fuel system. Additionally, the means to detection methanol fires in machinery spaces, such as portable heatdetection devices, should be installed.
Safety
While the IGF Code is mandatory under SOLAS, the IMO Interim Guidelines for the Safety of Ships Using Methyl/Ethyl Alcohol as Fuel (MSC.1/Circ. 1621), a supplement to the IGF Code, is non-mandatory and its use must be agreed with the vessel’s Flag Administration on a case-by-case basis. Skåra says that before signing a contract shipowners should seek confirmation from the Flag Administration that the Interim
Guidelines can be used in lieu of the IGF Code Alternative Design Approach or at least as a basis for approval.
According to the Interim Guidelines, cofferdams must have vapour and liquid leakage detection systems and the potential for water filling or inert gas purging upon detection of leakage. Water filling must be done via a system without permanent connections to water systems in non-hazardous areas. Emptying must be done with a separate system, and bilge ejectors serving hazardous spaces must not be permanently connected to the water system.
Nitrogen is needed for keeping an inert atmosphere in the fuel tanks at all times, and for purging bunkering lines and fuel lines. According to the Interim Guidelines, inert gas should be available permanently on board in order to achieve at least one trip from port to port considering maximum consumption of fuel expected and maximum length of trip expected and to keep tanks inerted during two weeks in harbour with minimum port consumption. The nitrogen required to gas-free tanks is in addition to these requirements.
Fuel tanks must not be located within machinery spaces of category A, accommodation spaces or spaces which are not defined and arranged as hazardous zone 1. The forepeak and afterpeak tanks cannot be used as fuel tanks either. Additional safety barriers required for both tank and ship are specified in the Interim Guidelines.
The fuel tank vent outlets are to be arranged at a distance of at least 15 metres from the nearest air intake or opening to accommodation and service spaces. The vapour discharge must be directed upwards in the form of unimpeded jets. Fuel tank vent outlets must be situated not less than three
8 MSC, WinGD, naval architects Marine Design and Research Institute of China (MARIC) and CSSC agreed to conduct a study project to examine the possibility of converting the main engine of a container vessel to a methanol-fuelled dual-fuel engine during SMM on 7 Septembermetres above the deck or gangway if located within four metres from such gangways. The vent system shall be sized, allowing for flame arrestors, if fitted, to permit filling at 125% of the design rate without over-pressurizing the tank.
Economics
A study just released by the Mærsk Mc-Kinney Møller Center for Zero Carbon Shipping examined the design of a methanolfuelled dual fuel 15,000 TEU vessel, estimating that methanol newbuilds would cost approximately 11% more than a standard newbuild and a conversion 10-16% more, depending on the level of preparation at newbuild.
The Mærsk Mc-Kinney Møller Center for Zero Carbon Shipping’s report: Preparing Container Vessels for Conversion to Green Fuels was a collaboration between the Center and ABS, Maersk, MAN Energy Solutions, Mitsui, MHI, NYK Line, TotalEnergies, and Seaspan. It found that converting to methanol is less expensive than converting to ammonia partly because fuel tanks can be sized for methanol, installed at newbuilding, and then used for fuel oil before conversion. However, this is not possible for ammonia tanks, which are also more expensive than methanol tanks.
Tank volumes of 16,000 m3 were used for methanol, double the volume required for fuel oil, in the report’s analysis of a 15,000 TEU vessel converted to achieve equivalent range. This reduced cargo space by 240-610, with conversion of unprepared ships sacrificing most space. The vent mast is located at the front of the vessel, 10 metres away from the accommodation, service spaces, the funnel, air intakes, and ignition sources to meet the requirements of the Interim Guidelines.
An open or semi-enclosed bunker station is arranged on the port and starboard sides, so that the parallel body line is sufficiently contacted with a bunker barge. Finding space is challenging due to the limited space between side of the ship and the hatch cover. The space between the hatch covers may be used, but width is limited. As a result, it is recommended that bunker stations are prepared for at newbuild stage.
For unprepared vessels, the conversion only made financial sense after eight to 10 years of operation when the increased earning potential from using the full cargo space balanced out the increased cost and cargo loss of conversion.
These losses can be reduced if range is reduced. A tank capacity of 10,000 m3 led to the loss of around 400 TEU. In this case, the smaller methanol tank system only occupies a single cargo bay located close to the engine room and fuel preparation room. It is assumed that the auxiliary engines and boiler are not converted to methanol use. Conversion
CAPEX reduced to 9-12% of a standard newbuild cost, making it attractive after four years.
For conversion, the fuel tank would need to be cleaned and transfer pumps replaced. The tank coating may also need repair. A dedicated fuel supply system is needed for each fuel and must meet the requirements specified by the engine designer, typically supplying methanol at 13 bar. Fuel pipes outside the fuel preparation room in enclosed spaces must be double walled and will need to be routed in the existing ship structure and machinery space, a complicated undertaking.
The report states that conversion of the 2-stroke main engine requires new cylinder covers, installation of methanol injectors and a new, additional injection system with valve blocks and chain pipes. Other engine parts such as liners and exhaust valves may also need to be replaced, depending on the engine.
The report proposes installation of methanol tanks under the accommodation to reduce cargo losses and a combined fuel oil/methanol tank system that allows for initial use of fossil fuels. Additional tanks could be built between cargo holds according to the desired fuel oil range. “If a vessel is unprepared for conversion and the fuel tanks are not prepared for methanol, for a full range conversion we propose locating the additional tank next to the engine room. It is assumed that the tank will be built as a self-supporting double walled tank, that will be fixed in the cargo hold, and not fully integrated in the hull structure.”

Converting unprepared vessels only makes economic sense on longer timelines or where reduced range options reduce cargo loses, states the report. However, the different preparation levels analysed only had a small impact on newbuild and total costs and very little impact on the total lifetime cost. The desired range after conversion, on the other hand, had a much larger influence on conversion CAPEX and therefore the total lifetime cost.
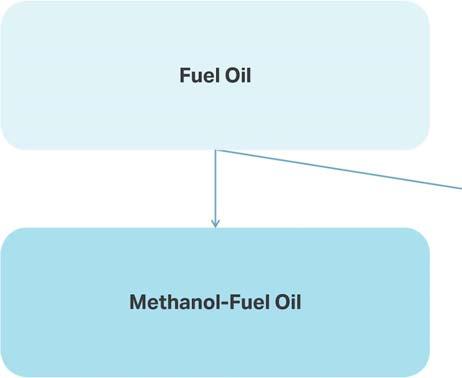
Methanol flames are particularly hazardous, as they burn at low temperatures with a flame that is nearly invisible in daylight, with no smoke. A methanol flame often goes undetected until it has spread to adjacent materials that burn in a wider range of light
THERMODYNAMIC LAWS TO LIMIT
PURE-ELECTRIC APPLICATIONS
Duncan Duffy, Global Head of Technology, Electro Technical Systems, at Lloyd’s Register (LR) sees greater opportunity for battery-hybrid and fuel cell applications in deep-sea shipping
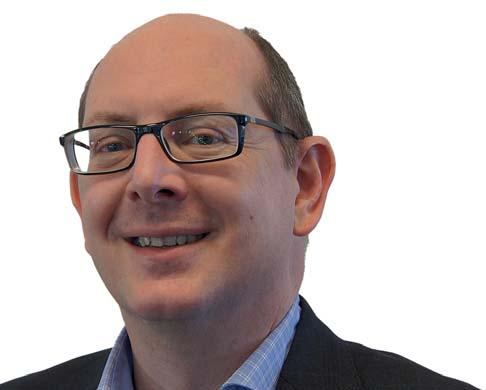
Duncan Duffy expects market economics to help pureelectric solutions to find a place among a range of options for ship owners operating in short-sea trades.
Leaving aside the potential impact of regulatory changes, it is a simple matter of thermodynamics. “Charging a batterypowered vessel directly with renewable electricity might result in conversion losses of 15% over the entire supply chain,” Duffy notes. This compares with the 63% efficiency of passing renewable electricity through an electrolyser to generate green hydrogen, and then converting it again to methanol.
This is before you even consider the efficiency of combustion engines, which are approaching their theoretical limits at 55% efficiencies. “For every penny you spend on renewable energy, you end up with significantly less value in terms of propulsion, when it gets to the propeller.”
But Duffy is clear that the technical challenges of scaling up pure-electric solutions to larger displacement vessels cannot be overcome by incentives. He cites the example of a pure-electric cruise vessel to illustrate his point.
“A passenger cruise vessel, operating a 14-hour route between overnight stays with a 10-hour recharging period, would require around 700 MWh,” Duffy noted.
Simply installing sufficient energy storage capacity onboard a vessel to store 700MMWh would introduce its own challenges from an energy storage system sizing perspective. “You would be looking at an ESS equivalent to around 140 teus, or 4,500 cubic metres”.
Duffy also noted that stepping up the electricity from 10kV to 54-55kV DC is likely to push the outer limits of what is technologically possible on vessels. “Bear in mind that the standards that are coming in from the IEC are increasing AC voltages to 36kV AC.”
For Duffy, the most convincing argument against building fully-electric larger displacement vessels is the scale of the renewable energy required to recharge them.
“You would need around 66MWh to recharge such a vessel. Or to put it another way, you’d be dedicating 5% of the output of Dogger Bank A simply to recharge a single vessel.”
LR projects
services is one of the outcomes we expect to get from that work.”
Nuclear power
Duffy noted that the sheer volume of renewable electricity required to produce hydrogen and then on to other hydrogenbased carriers, such as ammonia or methanol, was encouraging market participants to re-evaluate the potential for nuclearpowered propulsion to be used in the civilian market.
Interestingly, some of the work going into certifying swappable battery systems was likely to be applicable for nuclear designs. Potential suppliers of nuclear propulsion technology were also interested in supplying reactors on an Energy as a Service type (EaaS) contract.
“So as long as you have designed and built the ship to accommodate your specific reactor type, what you are effectively delivering is a plugin unit that comes with its own certification.” This would allow LR to leave avoid the challenge of becoming a nuclear regulator, and would also avoid leaving commercial ship operators with the challenge of disposing of nuclear waste at the end of life stage.
Fuel cells
In terms of other technologies, Duffy noted that LR had been involved in research involving fuel cell installations. “We've done studies looking at some fuel cell installations up to the 10MWh level in order to understand how that would integrate with other systems.”
While the technology offers advantages from an emissions perspective, there was little prospect of them replacing pure combustion engines as main movers for larger vessels in the short term.
“It is unlikely you would consider a fuel cell installation on its own without a supporting battery installation or another technology to store and release energy for those short-term transients.”
Battery chemistry
Duffy explained how LR is involved in Current Direct, an EU funded project to examine the potential for developing containerised swappable battery energy storage with a particular focus on the inland waterway market.
“We are using that research to understand the challenges of that technology, both from a security but also from a certi perspective... One of the challenges swappable equipment poses is that the equipment on the ship will change constantly. How we can accept that onto a classified ship as part of the essential
ber projects e n Current mine the inerised with a terway erstand th from tification wappable ent on the can accept he essential
Lloyd’s Register is active in a number of projects involving the electrification of maritime transport.
Duffy noted that lithium ion (Li-ion) was likely to remain the dominant chemistry for batteries for the maritime market for the remainder of the current decade. While other chemistries were under development, all had their own challenges: flow batteries have energy density constraints which are likely to limit their applicability in marine applications, for instance.
dominant for batteries fo cu other chemistries were un had their own challenge energy constr to limit their app applications, for inst
Advances in manufacturing were likely to lead to a doubling in Li-ion battery capacities from 2-3MWh in a teu to 5-6MWh/teu “over the medium to long term”, with university research suggesting that 15MWh/teu might be achievable. But y cautioned that real life operating experience suggested that batteries would rarely be fully charged.
Advances in man to lead to a doub from 2 “over term”, with migh Duffy cautioned that sugge
8 Duncan Duffy, Global Head of Technology, Electro Technical Systems, at Lloyd’s Register (LR)
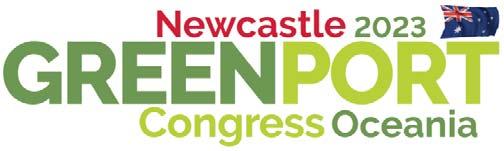
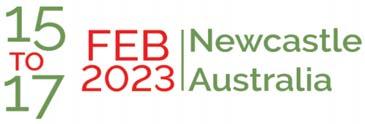
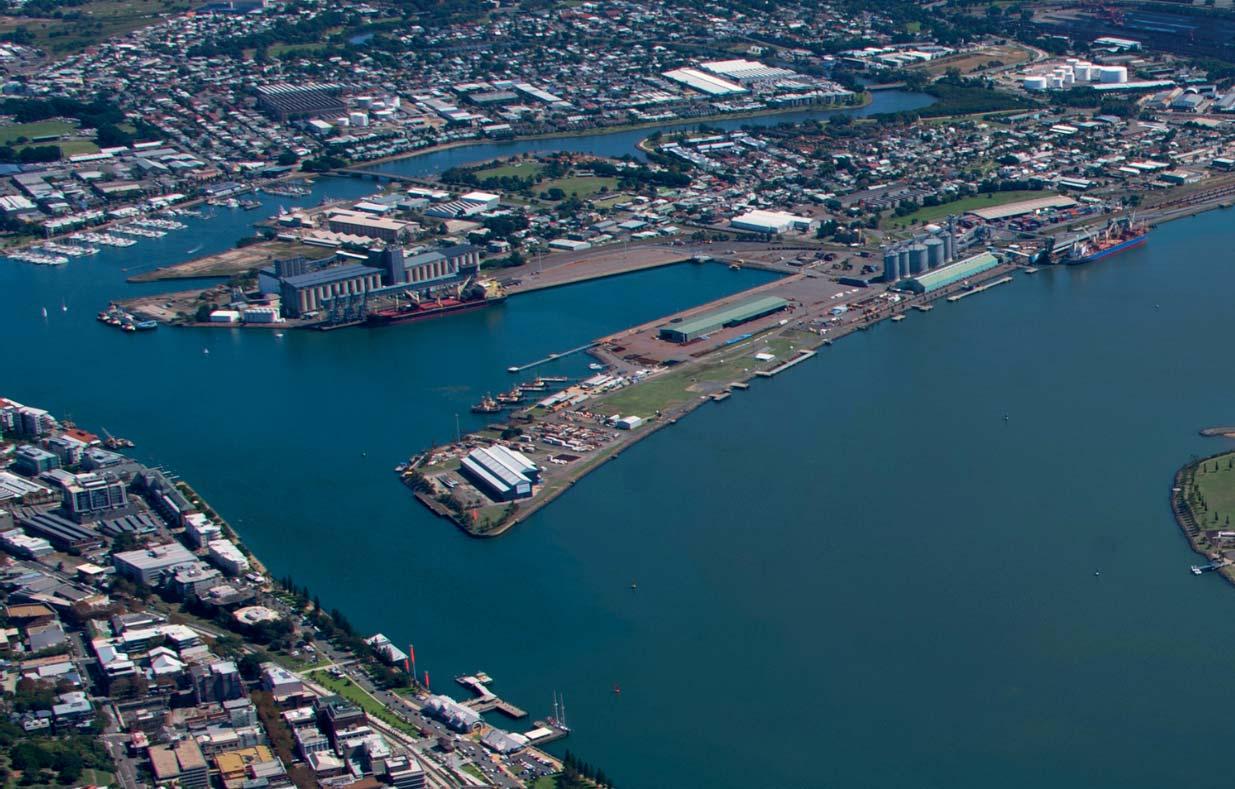
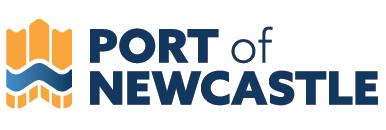





STOPFORD: SHIP RETROFITS POSE HUGE DECARB CHALLENGE
The shipping industry faces a significant challenge in meeting the IMO’s decarbonisation targets and the task becomes the more difficult the better the economic climate and the stronger the growth of global trade, said Dr. Martin Stopford, the shipping economist
Dr Stopford notes that demand the World Bank forecasts the world’s population will grow by 24% by 2050 from 8 billion in 2021, which means a growing carbon emission burden. It is also likely to lead to growing demand for the services of the shipping industry.
Rather than forecasting the growth in global trade over the coming 30 years, Stopford presented four scenarios for global trade growth. In the first, trade would grow by 3.5% per year and emissions from shipping would reach 28.4 billion tonnes. This, however, he described as unlikely. At a 2.0% annual trade growth, emissions would reach 21.4 billion tonnes and if global trade only grew by 0.8%, the emissions would still amount to 15 billion tonnes in 2050. With lacklustre growth at first and gentle, sustained decline after that the emissions would amount to 11.3 billion tonnes in 2050, a slight reduction from 2021.
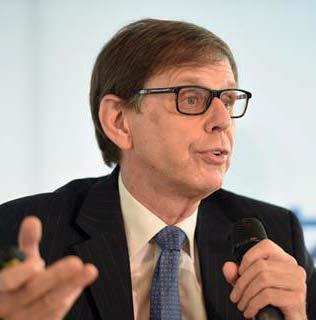
Retrofitting existing ships with fuel saving technologies will be one of the challenges that the industry will meet when it works its way towards decarbonisation. There are about 24,000 ship owning companies in the world at the moment and some 13,000 of them only have one vessel. Given the fact that freight markets are quite volatile, a major question is whether these owners will have the resources to make the necessary investments, Stopford noted in a presentation at Marintec in Shanghai in September.
Assuming that global trade will grow by 0.8% per year up to 2050, some ships built before the year 2020 would remain in service up to 2045. The propulsion system on these is based on diesel technology as is that one the first wave of vessels completed after 2020 that Stopford forecasts to trade up to the second half of the 2040s.
From the middle of this decade, wave 2 intermediate technology vessels will start entering service followed by zero carbon wave 3 vessels that will start to emerge soon after the second wave.
The fact that ships based on diesel technology are expected to remain in service for more than two decades from now highlights the need to upgrade existing vessels with energy saving technologies. However, the highly cyclical nature of shipping freight markets means that the main focus of ship owners lies in riding these cycles – it does not lie in technology or innovation.
This focus is quite distinct from the technological changes required to meet the IMO’s decarbonisation objectives. “You need entrepreneurs, people who make things work, young engineers who can work at home and at the office and who understand digital,” Stopford said. Although there is a lot of discussion about unmanned ships that may operate on the oceans in the future, the most crucial challenge that the shipping industry faces is not technology, but people.
While the industry needs entrepreneurial people, they should also be prepared to meet obstacles. “[When] Alfred Holt decided to use the type of boiler used in locomotives that worked at a pressure of 100 pounds per square inch on
his ships, rather than [the] ones working at 10 pounds that was the norm in shipping… the government tried to stop him,” Stopford said, referring to a British shipowner in the 1860s.
Shipowners should also be aware that there is likely to be a significant “green energy gap” as the production of green fuels is unlikely to keep up with demand growth from the second half of this decade onwards. As the demand for green energy is likely to outstrip supply in the near future and ultimately the production of fossil fuels will peak, nuclear power could be an option that the shipping industry needs to consider, Stopford concluded.
Investment needed in skilled staff and technology Stopford also notes that digital skills will be increasingly important in future, as ship owner seek to optimise the performance of systems onboard. Digital capabilities will be required to monitor the development of emissions from its ships and to reduce them. “Many owners do not have the staff to do this, they do not have the technical support anymore,” he told The Motorship.
Consequently, ship owners may well need to invest in hiring people with the right skills, at the same time as investing in energy saving technologies, to ensure that the investment in hardware produces the desired results.
8 Stopford: Digital technology and skilled employees will be required to achieve decarbonisation objectives
PARTNERS READY FOR DUAL-FUEL HYDROGEN ENGINE PROJECTS
The companies have worked together in pilot projects since 2017, successfully adapting Volvo Penta engines to run as a dual-fuel hydrogen and diesel solution via a conversion kit provided by CMB.TECH. Now, says Jakob Ursby, Director of Business Development at Volvo Penta, they are ready to start the dialogue with the market related to this increased cooperation on a project-to-project basis, with the aim of moving into small-scale industrialisation.
The aim is to establish dual-fuel hydrogen technology as a low-carbon interim solution before suitable zero-emissions alternatives become viable. It is an important step in Volvo Penta’s and CMB.TECH’s joint ambition to help accelerate their customers’ transition to net-zero emissions.
“From the initial dual-fuel technology projects we have seen reductions of CO2 emissions of up to 80%,” says Roy Campe, Chief Technology Officer at CMB.TECH. “It is clear that the energy transition is a major challenge in many types of applications. With the dual-fuel technology we have been developing over the last few years, we can provide a costeffective and robust solution for a variety of applications. We think there is huge potential in this solution for customers, both on land and at sea.”
The solution is expected to appeal to many shipowners due to its ease of installation, maintenance, and use. For the marine portfolio, the partners aim to start with pilots within the Volvo Penta commercial marine engine range. “Our dual fuel technology can be implemented on any diesel engine. The modification is minor and entails mainly the installation of a hydrogen injection manifold onto the air inlet collector. Also, the engine controller needs to be flashed with new software which allows for a switch over to the dual fuel mode,” says Campe.
large commercial sea going vessels. It uses two dual fuel combustion engines (H2ICED) with a total capacity of 441kW.
“The simplicity of the dual fuel technology allows a quick introduction into many applications. The potential to decarbonise with green hydrogen is huge, but many applications require a fallback scenario of traditional fuel to maintain a viable business. With the dual fuel technology, your asset is future proof, even without a full coverage of a reliable hydrogen infrastructure today,” says Campe.
He says: “The dual fuel technology is ideally suited to solve the chicken and egg story which is applicable if one wants to introduce a new fuel. It is a cost-effective and robust solution for emission reduction without compromising the operational performance. The transition can start today, even without a full coverage of a reliable hydrogen infrastructure. Using dual fuel engines, today's production capacity, experience and the widely spread service network can be applied to support energy transition, while getting acquainted with hydrogen as an alternative fuel.”
8 The design and testing of CMB. TECH’s hydrogeninjection system takes place at its Technology and Development Centre in Brentwood, in Essex, England
The co-combustion process involves hydrogen being injected and aspirated in the cylinder during the intake stroke. It mixes further to create a homogeneous mixture during the compression stroke, then a small amount of pilot diesel is injected into the chamber before top dead centre. The diesel auto-ignites due to the high temperature and pressure and co-combusts with the hydrogen, forcing the piston down during the power stroke. The cylinder is cleaned during the exhaust stroke with lower NOx and CO2 emissions in the exhaust gas.
CMB.TECH has its own passenger vessel, the Hydroville (in operation as from 2017), working on the dual-fuel technology implemented on the Volvo Penta engine. The 14-metre catamaran is a pilot project to test hydrogen technology for
Ursby says that a range of vessels across the commercial marine market are suitable for the dual-fuel solution. “Applications will go hand-in-hand with infrastructure development. For example, with the development of the ecosystem of vessels in the harbors, then we can imagine tugs and pilot boats as key targets. Another great potential is the crew transfer vessel market serving the offshore windfarms.
“This is a way to bridge over the gap to fully greenhouse gas free solutions which are under way. The dual-fuel solution will heavily reduce the emissions of greenhouse gases while at the same time provide a robust and reliable solution and thereby high productivity.”
Volvo Penta is investing heavily in exploring a wide range of sustainable and bridging technologies – such as hybridisation, electric drivelines, fuel cells and alternative fuels for combustion engines – giving customers the opportunity to find the technology that works best for their application.

Volvo Penta and CMB.TECH have agreed to accelerate the development of dual-fuel hydrogen-powered solutions
The dual fuel technology is ideally suited to solve the chicken and egg story which is applicable if one wants to introduce a new fuel
‘‘Credit: CMB.TECH
COSCO NH3 TEST ENGINE AMONG CHINESE AMMONIA LANDMARKS
China Classification Society (CCS) and Dalian COSCO Shipping Heavy Industry have held an ignition ceremony for COSCO’ first ammonia powered duel fuel test engine and an Approval in Principle (AiP) release ceremony for the design of ammonia-powered ships and ammonia supply system design
8 China Classi
cation Society (CCS) and Dalian COSCO Shipping Heavy Industry have held an ignition ceremony for COSCO’s
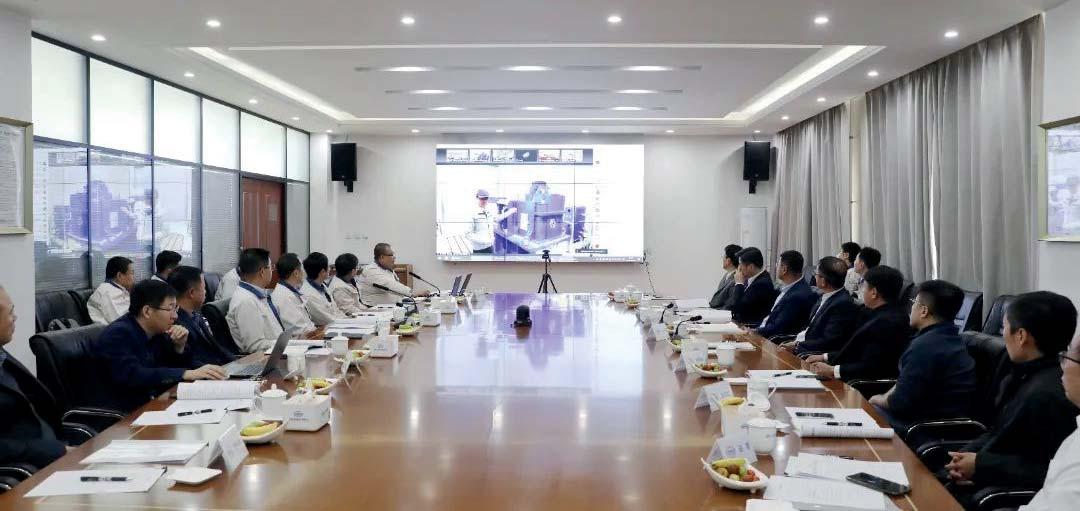
rst ammonia powered duel fuel test engine
The project is based on the 5000HP engine built by Dalian COSCO Shipping Heavy Industry and includes the design and manufacture of ammonia storage and gas supply systems, exhaust gas treatment, and the overall design and construction of ships.
CCS has set up a team of experts to participate in the R&D of the related sub-projects and the construction and inspection of the actual ship.
At the AIP release ceremony, Zhang Hui, general manager of CCS’s Dalian Branch, issued the world's first AiP certificate for an ammonia-fuelled tug design based on a construction project underway at Dalian COSCO Shipping Heavy Industry.
Ni Zhiyong, Director of the Product Division of CCS’s Shanghai Branch, issued an AiP certificate for the first domestic ammonia fuel supply system for marine four-stroke engines to Weihai Heavy Industry Technology.
HHI-EMD tests hydrogen blend on HiMSEN engine
Hyundai Heavy Industries Engine & Machinery Division (HHI-EMD) has tested an LNG and hydrogen fuel mix in a 1.5MW HiMSEN engine.
This engine performed with excellent performance and stability during the test, says HHI-EMD, which was conducted at HHI-EMD’s R&D centre. The mixing ratio of 25% hydrogen led to a 30% reduction in CO2 emissions compared to a diesel engine.
This LNG-hydrogen HiMSEN engine can be used for stationary power plants, or as a genset or propulsion engine on ships. The hydrogen evaporation gas (BOG) can be reused as fuel for the engine.
HHI-EMD has been developing the eco-friendly engine for LNG, methanol and ammonia, and additionally has a plan to develop the pure hydrogen combustion engine by 2025.
8 Weihai Heavy Industry Technology was awarded an AiP for an ammonia fuel supply system for marine four-stroke engines
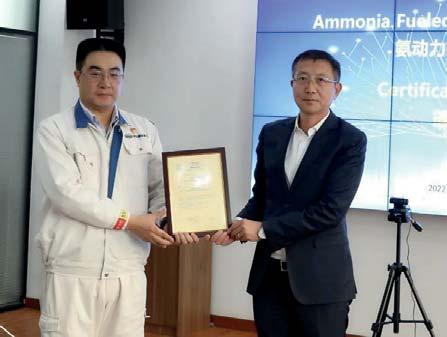
8 HHI-EMD has successfully tested an LNG and hydrogen fuel mix in a 1.5MW HiMSEN engine at HHI-EMD’s R&D centre
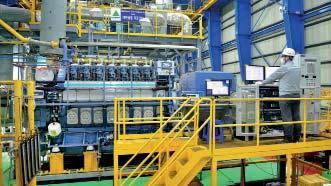
ON THE CHARGE: VARD EXPECTS ELECTRIC SHIFT IN SOV MARKET
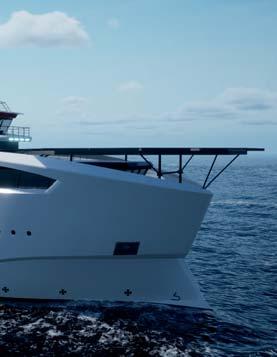
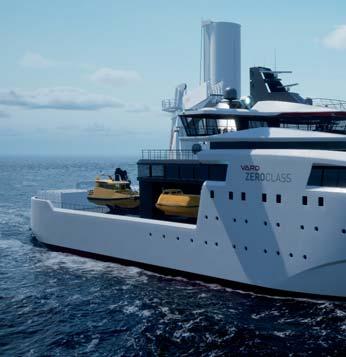
Busy with plans for new windfarm support vessels (SOVs), ship designers from around Norway’s west coast offshore cluster, and their corresponding yards, are proceeding on the understanding that windfarm operations will soon be powered entirely by battery-electric systems

A world-leader in shore power, and deriving over 95% of its energy needs from renewable hydropower, Norwegian companies are uniquely placed to consider how ship operations could become fully-electric with assistance from batteries. Already, Norway operates several allelectric vessels operating using large battery banks, including ferry Bastø Electric (4.3MWh) and the famous container feeder Yara Birkeland (6.7MWh).
Olympic Subsea, based in Fosnavåg, has subsea and offshore oil and gas vessels converted to work as SOVs. The company is also preparing its vessels to be able to plug in to wind turbines to charge. “We are a preparing a mooring system in the stern, which we can take on board a charger cable. It’s uncertain what standards are going to be in the industry, but we are preparing the vessel to have the route of the cables, the foundation for a mooring system. We have a battery pack on board, and we have dedicated additional rooms on deck, to facilitate up to four times the battery capacity.”
Designer Vard boasts that 87% of the vessels in its orderbook will either be delivered with batteries installed or be battery “ready”. Asked for clarification on what “ready” meant in this context, Henrik Burvang, Vard Design Manager, Research and Innovation explained: “Yes, to a large extent this boils down to providing that space. [But] if you actually have the intention of installing [batteries]… you need to be confident that it is manageable, and especially in regard of safety, and the approval process. So how much ventilation is needed, what kind of hazard do storms create on the ship.
“The more you prepare in the design phase, the more studies we are able to do, the easier the retrofit will eventually be.”
To this end, Vard is combining iterative computing with computational fluid dynamics, in a toolset it calls ‘parametric optimisation,’ to devise by machine-learning the best hull shape to allow its ship to move most efficiently through the waves, while also providing the optimum hull geometry to house large banks of batteries. “…we can do studies all night, on hundreds of different hull shapes,” Burvang said.
A design for a green SOV is part of Vard’s “Zero Class” line up which also includes a fishing vessel and a platform supply vessel (PSV). But Vard wants to take the concept of plugging ships into turbines even further, though, with its Plugin Electric PSV Project (PIEZO), which, confusingly, has nothing to do with piezoelectric minerals. It proposes to decarbonise offshore oil and gas, by capitalising on recent branching-out of some oil majors like project stakeholder Equinor, into renewable energy.
Norwind Offshore has only one vessel currently in its stable, Norwind Breeze, a former Vard PSV, now converted into an SOV. But the fledgling offshore company, which was formed by Volstad, Farstad and Kleven during the pandemic, has four more SOVs on order, of the Vard 4 19 design with hybrid diesel-electric propulsion. Each will have space underneath the working deck which can accommodate a large bank of batteries. “From our point of view, the
technology is there, it is just about scaling up,” said Roy Ove Standal, Norwind COO. “With a 25MW battery package, we can operate on electricity about 15 hours per day.”
But the batteries are not being fitted at the yard, and there is a tacit understanding that the spaces might be used for something else, like methanol tanks.
“In the US, Equinor tells us, they are obliged to offer a charging facility offshore,” explained Norwind Offshore CEO Svein Leon Aure, “So that will come, and we will deliver the vessel with the battery and a charger.”
He suggested the same might not pan out so neatly in Europe, without support from the right quarters. The vessels may instead be forced to bunker methanol or ammonia, from an offshore production facility powered by windfarm energy.
He acknowledged that charging onboard batteries with electricity would be cheaper and more efficient, “from our [an SOV operator] point of view.” However, he said: “I think there is a lot of politics involved. The energy the windmills are producing is very often sold already… so we cannot just tap from the production, which is one challenge.
“And, certain areas are requiring that all additional energy produced should be converted to hydrogen. So there is no defined way as to how this will develop.”
8 Vard SOVMONO FUEL HYDROGEN ENGINE PROJECT WINS UK FUNDING
The Department allocated over £14m to 31 projects supported by 121 organisations from across the UK to deliver feasibility studies and collaborative R&D projects in clean maritime solutions.
HydroMAR-E, a collaboration between Dolphin N2, Brighton University and Hiflux, supported by BMT, is developing a mono-fuel hydrogen version of the recuperated split cycle engine can be used in a range of heavy-duty applications for land and sea. It offers very high efficiency (competitive with a PEM fuel cell) very low emissions, and moderate capital cost increases compared to existing internal combustion engine manufacture.
Uniquely, and unlike a standard internal combustion engine, the new engine has demonstrated ability to use diesel, methane and hydrogen in the same core engine (and has potential for the same with ammonia or methanol) with the same high efficiency and low emissions, enabling a rapid transition as future fuels become more widely available.

The engine concept is covered by eight international patent families. A single cylinder proof of concept engine has been running at Brighton University since 2017.
Dolphin N2 says the recuperated split cycle is an internal combustion engine, with all that implies in terms of low cost and ease of manufacture, that aims to compete with zero emission drivetrains. It targets long haul trucks, 0.5-50MW distributed power generation, mixed-mode rail and marine applications. It can potentially do this with the efficiency of the largest power stations, and air quality somewhere between the toughest Californian passenger vehicle standard, and zero-impact (meaning emissions can’t be detected or are cleaner than the surrounding air).
There are two versions of the technology: ThermoPower® is a simplified system offering most of the air quality benefits and efficiency advantage versus advanced diesel engines and CryoPower® which delivers ultimate efficiency and air quality by the addition of liquid nitrogen or air to its internal processes.
“Split-cycle engines are known technology, and recuperation is commonplace in industrial gas turbines. It is the specific combination of these, plus the use of water or liquid nitrogen, that is innovative,” says Dolphin N2 on explaining the technology:
The distinctive feature of the engine is that the “cold” and “hot” parts of the traditional internal combustion engine are separated. A first set of cylinders draw in air and compress it – in the CryoPower® version, Liquid Nitrogen is injected to keep this process cool for maximum efficiency; the simpler ThermoPower® injects water. Then the compressed air passes through a recuperator, where the engine’s exhaust heats it up – saving fuel which normally has to do this. The air now passes to the second, hot cylinder set, which are thoroughly insulated – something that is not feasible in a normal internal combustion engine where the same cylinder handles hot and cold processes. These cylinders host the combustion and expansion events, which produce power;
they are bigger than the compressor cylinders (again impossible in a standard engine) because that is most efficient. The hot air passing into these combustion cylinders does so at the speed of sound, leading to extraordinary mixing with the fuel, and a unique “cool combustion” regime. The very low level of emissions, especially NOx and particulates, can be reduced using urea-based selective catalytic reduction after-treatment.
The cost for the ThermoPower® engine is estimated at around +20% compared to conventional diesel, with a fuel saving of 10-18% giving payback within a year. For CryoPower®, capital cost is estimated at around +50% of the cost of a commercial diesel engine, with fuel cost savings of up to 2025% per year giving a rapid payback on the extra cost.
HydroMAR-E will use a laboratory single cylinder engine, which has already demonstrated starting and running, to develop this spark-guided system to TRL4, then a multicylinder prototype to demonstrate TRL5 in readiness for future application demonstration in marine environments. Supporting work will develop an improved recuperator system, and review marinisation, installation, vessel systems and regulatory aspects.
Commenting on the award of the grant, Jake Rigby, Research and Development Lead at BMT said: “The UK is one of the global leaders in clean shipping, and, in an industry that is strongly focused on sustainability and zero emissions, it makes sense that the supply chain is also as decarbonised as practically possible, with retrofit and newbuild power generating solutions being considered for maritime applications. We look forward to moving this project forward, using the best in innovative green technology, complex engineering, and a partnership mindset to contribute to a more diversified and resilient energy economy.”
8 HydroMAR-E, a collaboration between Dolphin N2, Brighton University and Hiflux, is developing a mono-fuel hydrogen version of the recuperated split cycle engine, which can be used in a range of heavyduty applications for land and sea
project has been selected to develop is mono fuel hydrogen engine as part of the UK Department for Transport’s Clean Maritime Demonstration

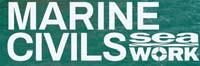



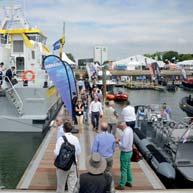
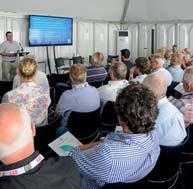
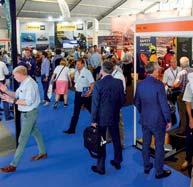
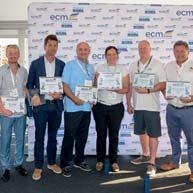
ABB’S DAC SYSTEM UNDERPINS MAN HYBRID DF LNGC DESIGN
The DFE+ concept features the MAN 49/60DF engine and ABB’s Dynamic AC (DAC) technology which aims to cut fuel consumption and reduce CO2 and methane emissions compared to conventional dual-fuel diesel electric (DFDE) propulsion systems. It also provides operational flexibility for different trades or retrofit from an LNG carrier to an FSU or FSRU.
A conventional DFDE concept is characterised by gensets operating at constant speed over the entire engine load, optimised for high load, typically 85%. At lower loads, the engines operate less efficiently, leading to higher fuel consumption and more methane slip.
In contrast, the new MAN/ABB DFE+ concept implements variable-speed operation, leading to better efficiency with significant reduction of methane slip over the entire engine load.
Variable speed power
Rune Lysebo, Head of Global Sales, ABB Marine & Ports, says the electric system can be optimised regardless of what fuel is used, and as a result, the concept is future-proof. “The same level of efficiency cannot be reached with fixed speed dual-fuel engines as the basis.”
The system also allows the use of future energy sources, such as fuel cells. “Shipowners who equip their vessels with an electric backbone and DAC will benefit from a fuelagnostic and 2050-ready ship.”
LNG carriers have two main operational modes: oceangoing and loading/ off-loading mode. Ocean-going mode represents the majority of the operational time, says Lysebo. DAC enables varying the frequency of the main power distribution system to match the vessel's power needs, providing significant energy savings. Loading / offloading mode is done with engines operating at nominal speed, hence standard cargo pumps can be used.
“This concept can be applied to Azipod® units, single and twin screws, as well as permanent magnet, synchronous or induction motors and gearboxes,” says Lysebo. “Based on the typical operational profile and sailing speed of LNG carriers, we see that the efficiency can be significantly improved from the current dominating propulsion concept used on LNG carriers. The new concept will give greater freedom in designing power and propulsion trains on LNG carriers. We expect to see more space available for payload or reduced length of the vessel, which again will contribute positively to lower fuel consumption and lower emissions.”
Energy storage is an optional extra benefit for the system. It can help to achieve more optimal load points for the engines, provide enhanced dynamic support of the distribution system and act as spinning reserve without causing additional emissions.”
Lysebo says that while variable-speed applications are well established for power distribution systems up to 10MWe, torque requirements and the low efficiency of first-generation dual-fuel engines – including limitations in the e-systems
design for diesel-electric propulsion systems over 10 MWe – made variable speed for propulsion systems over 10Me10MWe unworkable. The DAC technology overcomes this and is suited to a range of vessel types.
With DAC, the ship’s main power system is engineered for variable frequency, including component design and system integration. Power distribution for auxiliary loads is provided by frequency converters or directly from the variable frequency system. There are numerous small consumers in a vessel that are supplied by the engine room switchboards. This low voltage distribution is normally 400 – 690V with constant frequency, 50 or 60Hz. The DAC concept handles low voltage distribution and can be customised into different configurations to suit owners’ requirements.
The basic solution uses centralised frequency converters (island converters) to feed constant frequency at desired value to low voltage switchboards and distribution panels. and other loads requiring constant frequency. This is quite straightforward approach and allows the downstream distribution network to remain unchanged.
To achieve higher levels of integration, it is possible to combine the island converters with motor drives in multidrive configuration. This solution would reduce the size of island converters even more and in some cases make separate converters for single motors unnecessary.
8 Pictured at SMM, Stig Leira, Transformation Program Manager, ABB Marine & Ports; Rune Lysebo, Head of Global Sales, ABB Marine & Ports; Marita Krems, Vice President and Head of Four-Stroke Marine & License, MAN Energy Solutions; and Elvis Ettenhofer, Head of Marine FourStroke – Region Asia Pacific, MAN Energy Solutions

and
have teamed up on the
for LNG
Dual-fuel flexibility
With DFE+ shipowners will face less challenges in meeting the IMO’s Carbon Intensity Indicator (CII) requirements than would with existing LNG carrier propulsion technologies, says Elvis Ettenhofer, Head of Marine Four-Stroke – Region Asia Pacific, MAN Energy Solutions.
“In the last 15 years the shipping industry has made a continuous change for most of the ship applications from liquid fuels like MGO, MDO or HFO to cleaner and more environmentally friendly fuels like LNG. New emission regulations and geopolitical developments are accelerating the request for carbon neutral fuels like methanol, ammonia, hydrogen or synthetic fuels. Compared to LNG where the industry had a clearer picture and more time, today nobody can predict 100% when and what fuel will make the race. This creates uncertainty in respect of investment decisions to our customers and therefore the biggest value we can provide to our customers is flexibility.”
The newly launched MAN 49/60DF is available as an in-line engine with 6, 7, 8, 9 or 10 cylinders or as a V-type engine with 12 or 14 cylinders. Its output ranges from 7,800 to 18,200 kW, and it can run on LNG, diesel, biofuel blends and synthetic natural gas to provide fuel flexibility on the path to decarbonisation. “MAN 49/60 is our new 4-stroke flagship, and the engine platform is ready for all main alternative carbon neutral fuels. We still consider LNG as the main transition fuel and have therefore released the LNG version first. Next year the pure liquid version will follow for example diesel or synthetic fuel, and this version will be methanol ready.”
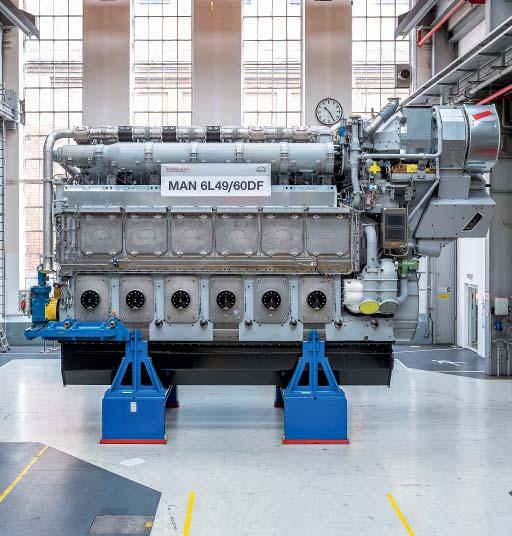
The 49/60DF features MAN’s latest technologies, including two-stage turbocharging, second-generation common-rail fuel injection, SaCoS5000 automation system and MAN’s next generation Adaptive Combustion Control ACC 2.0 that automatically sets combustion to optimum levels depending on ambient conditions, fuel quality and engine wear. The engine also retains existing MAN technologies such as the gas-injection system, pilot-fuel-oil system and MAN Selective Catalytic Reduction (SCR) system.
The 49/60DF can start in gas mode where it complies with IMO Tier III without secondary measures. In diesel mode, it complies with Tier III when combined with MAN’s SCR system. Soot emissions are halved in diesel mode due to MAN’s new common rail system 2.2, while the 49/60DF’s methane emissions are also drastically reduced in gas mode.
“One big benefit of a DFE+ System is that you can use the engines for the propulsion but also during LNG loading and unloading at the terminal,” says Ettenhofer. “This means you can reduce installed power to a minimum and still have enough redundancy in case of a technical issue or planned maintenance during regular ship operation. The exact number of engines or cylinder variants installed are very much dependant on the customers’ requirements for redundancy and ship speed. But considering as an example a required propulsion power of 22MW at design speed, 3 x 10L 49/60DF (1,300kW per cylinder) with a total installed power of 39MW, would be sufficient to have 2 x 10L 49/60DF online and one 10L 49/60DF standby for the operational load point with the highest power demand. Our customers benefit from the reduced numbers of installed engines and cylinders when it comes to maintenance costs and higher pay-load due to weight.”
Combined benefits
Regarding anticipated fuel savings, Ettenhofer says: “MAN and ABB are running simulations, and we will double-check our results with shipyards. This is a complex process and will take some time, but we see already now significant potential
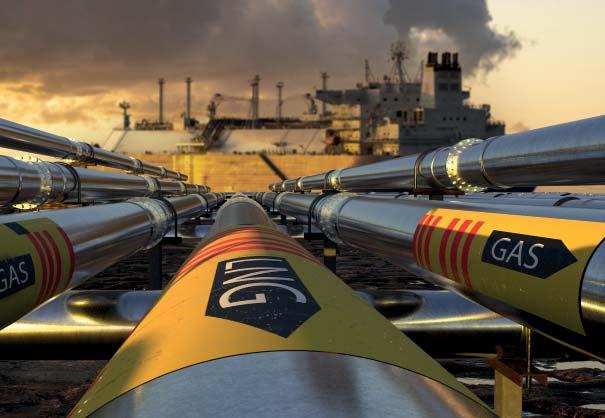
in reduction of fuel costs and methane emissions. From a 49/60DF engine perspective only, we have around 4% in fuel savings compared to MAN’s first generation 51/60DF engine and around 40% in methane emissions reduction, with constant speed.”
“These improvements result from MAN’s two-stage turbocharging and improved combustion process based on MANs ACC2.0 (adaptive combustion control), smart sensors and enhanced pilot fuel injection that give us the possibility to perfectly control every individual cylinder and combustion cycle and reduce the methane emission and lift the efficiency of the engine to another level. Together with the integrated MAN/ABB DFE+ concept, additional savings in fuel and methane emissions will be generated.”
The DFE+ concept is able to be integrated with MAN’s ALSi (Air Lubrication System interface). Typically, conventional air lubrication systems use compressors to provide the air, and this means a lot of energy is required, says Ettenhofer. “MAN’s 49/60DF provides a smart interface that means no compressors are needed, and this improves vessel efficiency.”
MAN and ABB presented the DFE+ solution at the SMM trade show and have received a lot of positive feedback. The companies are expecting to announce their first customer soon.
8 The DFE+ concept aims to cut fuel consumption and reduce CO2 and methane emissions compared to conventional dualfuel diesel electric (DFDE) propulsion systems for LNG carriers
8 MAN 6L49/60DF engine
MODULARITY KEY TO DECATRIP BIO-LNG CORRIDOR PROJECT
A project called Decatrip aims to introduce carbon neutral ferry travel between Finland and Sweden in five years’ time but it also has a wider aim: to present modular architecture on which similar projects could be implemented elsewhere in Europe, which again could benefit a wide range of industries
In early September, Business Finland granted almost EUR1.6 million to a project called Decatrip set up by the shipbuilder Rauma Marine Constructions (RMC), Åbo Akademi University, charging solutions supplier Kempower and the ferry company Viking Line to set up a green corridor on the roughly 10 hour ferry crossing between Turku in South Western Finland and the Swedish capital Stockholm. Each ferry makes two crossings per day.
“The solutions developed in the project will enable fully carbon-neutral freight and passenger travel between Turku and Stockholm, but the project will also be scalable for other routes. This is important since all EU countries, Finland included, have signed on to build green maritime transport corridors,” said Mika Laurilehto, interim CEO of RMC in a statement.
Dr. Magnus Gustafsson, Research Director in Industrial Management at Åbo Akademi University, told The Motor Ship that the project’s roots go back to 2020 and discussions with RMC concerning the prospects for shipping in the region to use locally produced renewable fuels. It was clear from the start that these would be much more expensive than the ones that shipping uses today.
Håkan Enlund, SVP sales and marketing at RMC, had pointed out how the situation in shipping was akin to that with cars in the US before the oil crises of the 1970s. “Cars were fuel hungry, because fuel was cheap and fuel was cheap, because cars were fuel hungry,” Gustafsson cited Enlund’s words.
Given the much higher price of a green, renewable, locally produced fuel, it was necessary to bring stakeholders in the ferry service in question around a table to discuss the practical implications of such a move.
Commitment of all stakeholders prerequisite Freight owners accepted that Viking Line would have to charge more for each lorry that it would carry in the future, but because ferry freight comprises finished products, industrial components and e.g. foodstuffs, the increase would have a marginal effect on the cost of the products carried. “iPhones cost an awful lot per kilo so the additional freight cost from renewable fuels is minimal,” Gustafsson pointed out.
Setting up a facility to produce a green, renewable fuel would require an investment rising to hundreds of millions of euro. Such a commitment would only become possible if there was a customer committed to the long time use of the fuel, such as Viking Line. It could only make a commitment to such a fuel if freight owners accepted a higher cost base. On the other hand, all partners could expect a significant PR gain by being able to say that they do not emit CO2 on the sea crossing.
Electric lorries are likely to emerge in the next few years as a viable option for haulers and for this reason, Kempower was included in the project because charging of the lorries during the sea crossing is an important part of the project. “It is about sustainable transport, rather than sustainable
8 Viking Line is participating in a Finnish project that seeks to promote the development of renewable biomethane solutions, among other decarbonisation strategies
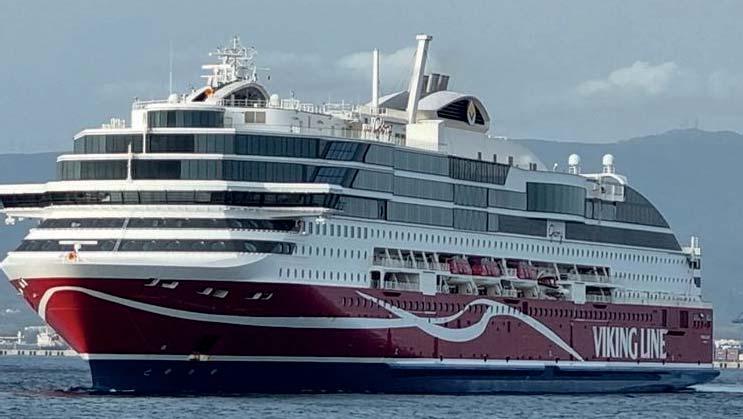
crossing,” Gustafsson said, adding that it was important to look at the whole transport corridor.
“The ships sail at rather slow speeds through the archipelagoes of Turku and Stockholm. Battery packs could be used to store electricity generated during these times and cars and lorries onboard could use the power stored in them to charge their own batteries,” Gustafsson said. The battery packs could also be used to power the vessels themselves for part of the crossing.
The Decatrip project is based on the use of synthetic methane as the renewable, clean and locally produced fuel of the future. The CO2 that would ne needed in the process to produce it could be sourced from e.g. wood-fired districtheating plants. The use of synthetic methane would require little work on the two Viking Line ships as they are already capable of using LNG, Gustafsson pointed out.
Modular approach should allow others to use same architecture
– all the time. Decatrip project partner RMC delivered last year the 21,400 gross ton Aurora Botnia to Wasaline, another ferry company that operates between Finland and Sweden. It also uses Wartsila 31DF engines and LNG as fuel, but the ship has been designed to switch to liquid bio gas in the future.
Competition on services between south-western Finland and Sweden is poised to intensify next year, when the Grimaldi owned Finnlines will introduce two new 64,600 gross ton ropax ferries between Naantali and Kapellskar. With a capacity of 5,500 lane metres and 1,100 passengers they will be more freight focused than the cruise ferries of Viking Line.
Grimaldi has fitted battery packs on its Eco class freight ferry newbuildings and these will be a feature on the new ropax vessels as well, which will be known as Finnsirius and Finncanopus. Tallink Grupp operates two large, conventional cruise ferries between Turku and Stockholm as well, but one has been chartered out as an accommodation vessel for the winter 2022-23.
winter
The project’s wider aim is to provide a platform for ferry companies elsewhere is Europe to introduce green corridors as well. In order to do that, a system approach is required. All relevant stakeholders – ferry company, freight owners and energy company – need to commit themselves to a long term use of a green, locally produced fuel.
It is important that this transition, which means signi investment and higher costs, will be commercially viable for all participants. Gustafsson said that a CO2 free transport corridor would offer a competitive edge for the companies involved in such a project as consumers are becoming increasingly concerned about the state of the environment. “European industries have largely removed CO2 emissions from their own production, but sea transport still has got some way to address these issues,” he noted.
Another key element of the project is to come up modular solutions that would make them adaptable to use in various parts of Europe. The most suitable fuel, for example, could be methanol in some cases. While the investment on the two ships of Viking Line that involved in Decatrip is not expected to be significant, this may not be the case in some other cases.
Ferries are a good platform to test new technologies and concepts, because they usually operate on relatively short crossings and call at the same ports – often just two or three
r ridors ed. All rs and a ificant ble for nsport panies oming ment. ssions as odular arious uld be e ected cases. es and short three
Magnus Gustafsson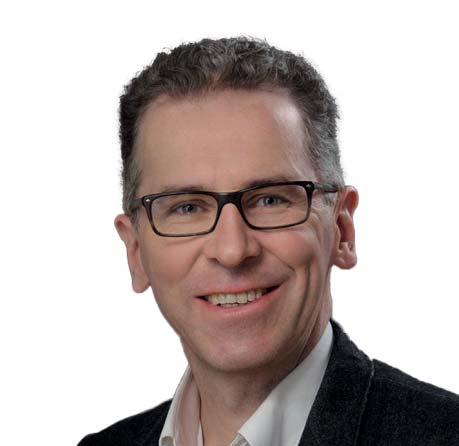
Two large LNG dual fuel engine cruise ferries as platforms
Viking Line has two large cruise ferries on the Turku-Åland Islands-Stockholm service that both are involved in the Decatrip project.
The first on to be completed was Viking Glory that entered service early in 2013 and was built by what is now the Meyer Turku shipyard. The 57,655 gross ton ship is powered by four Wartsila 8L50DF dual fuel engines that develop a total of 30,400kW and it has two 200 cubic metre LNG tanks on an open deck in the stern. The engines drive generators and two electric motors, each connected to a fixed blade propeller.
Viking Glory was delivered by the Xiamen shipyard in China late last year and it entered service in the spring of 2022. At 65,211 gross tons, it was the largest
passenger vessel built in the country until the completion of the 69,500 gross ton ropax ferry Moby Fantasy this year.
Viking Glory was the first ship to be fitted by Wärtsilä 31DF engines and the six units onboard develop a total of 33,000kW. Unlike its older running mate, Viking Glory is fitted with Azipods.
Dr. Magnus Gustafsson, Research Director in Industrial Management at Åbo Akademi University, said that Viking Line was a natural partner in the project, because of their proven track record in environmental matters. Viking Grace was one of the first large ferries in the world to have dual fuel engines capable of running on LNG. Rotor sails made by Norsepower were also tested on Viking Grace, but they were
removed after it had become clear that the Turku-Stockholm route with the archipelagoes and subsequent need to change course often was not ideal for them.
Meanwhile, Viking Line said the Wärtsilä 31DF engines offer a 10% reduction in fuel consumption compared to those on the earlier ship. As they require slightly higher pressure in the gas system onboard, an LNGpac system is used on the new ship.
Gas pressure levels would be maintained by pumps rather than the more conventional heat exchangers. Azipods will reduce emissions by about 10,000 tons per year and steam turbines that are driven by Climeon Heat Power system cut CO2 emissions by a further 4,000 tons each year.
Conference Programme


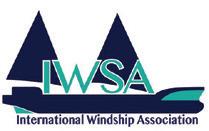
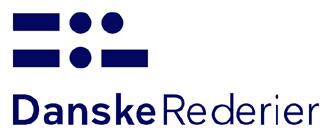

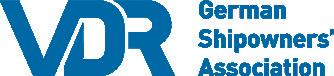
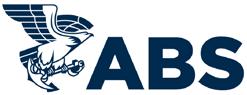
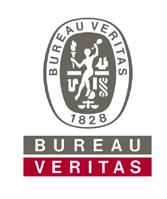

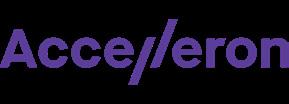




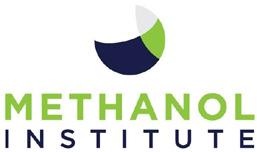
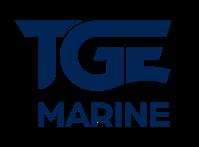
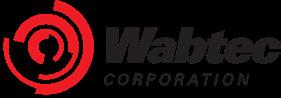
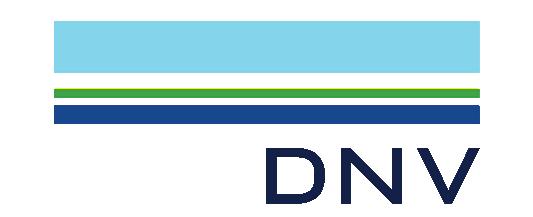
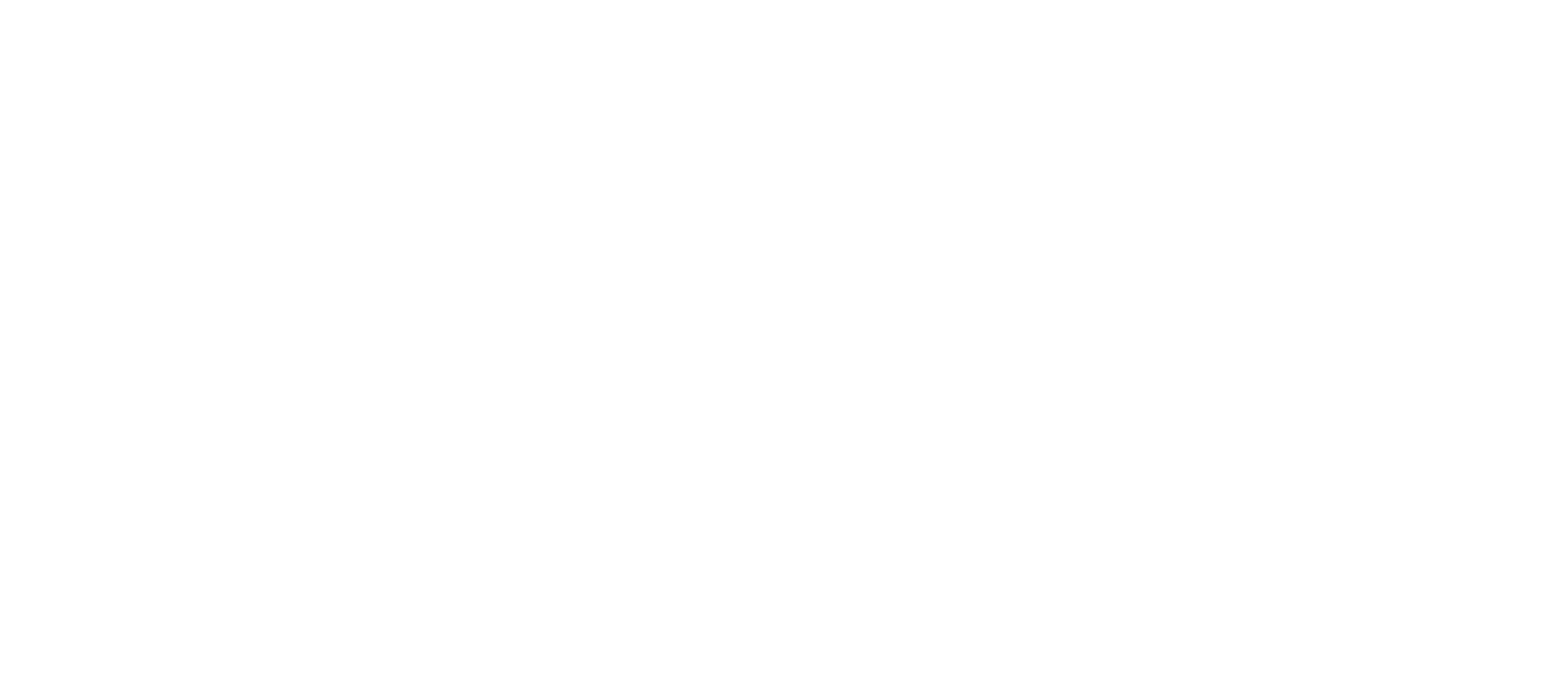
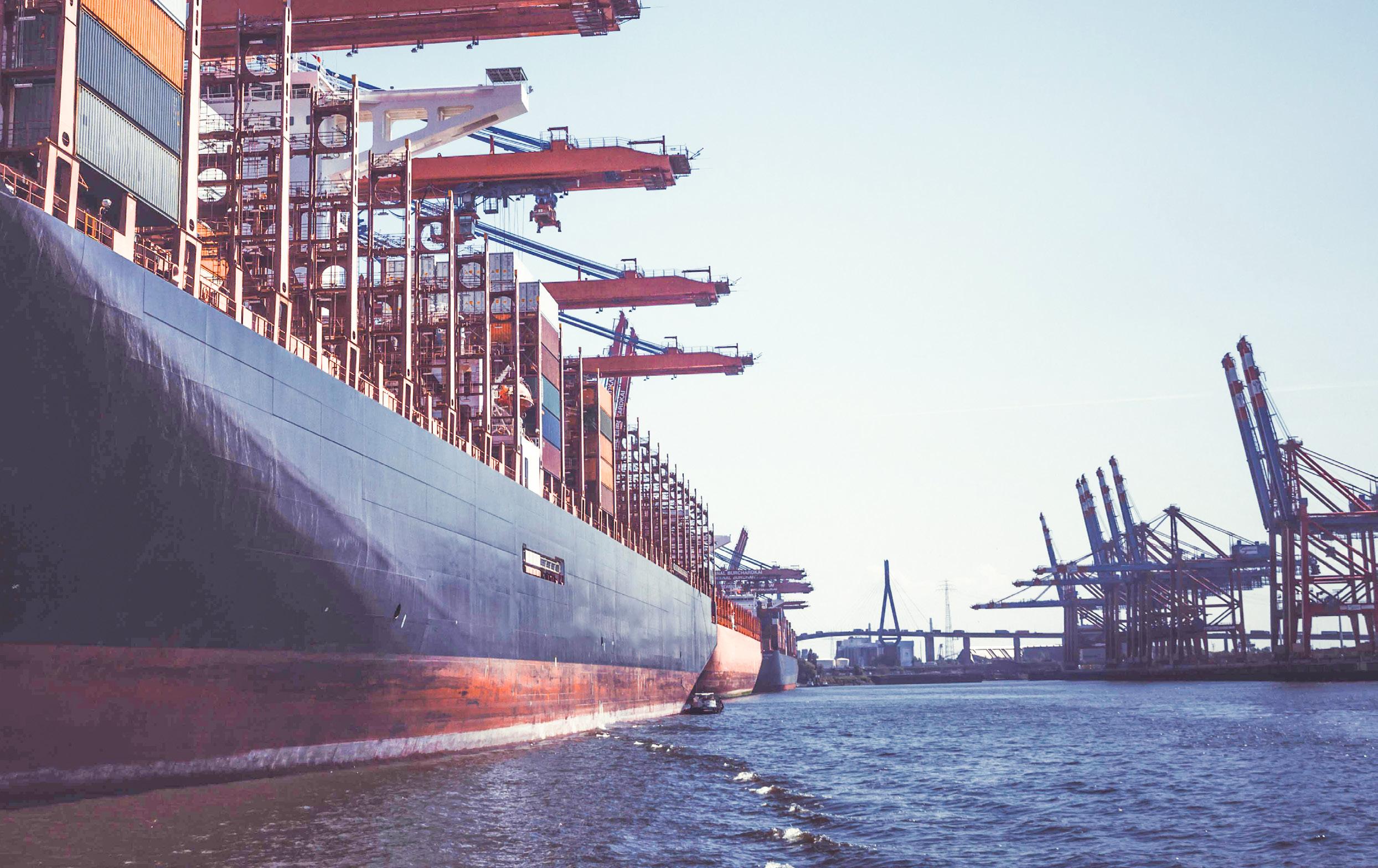
DAY ONE - TUESDAY 22 NOVEMBER 2022
08:00 Coffee
09:00
09:15-09:25
welcome
Lars Robert Pedersen, Deputy Secretary General, BIMCO Reinhard Lüken, Managing Director, VSM German Shipbuilding And Ocean Industries Association
Gold Sponsor Welcome DNV
Rasmus Stute, Vice President - Area Manager, DNV
KEYNOTE PANEL: THE JOURNEY TO 2030 WITH SHOREPOWER
Moderator: Lars Robert Pedersen, Deputy Secretary General, BIMCO Under the Fitfor55 legislative package shore-side electricity has been given particular attention. Requirements for shore-power infrastructure development under the Alternative Fuels Infrastructure Regulation (AFIR), and for zero-emissions from ships at berth under FuelEU Maritime, will give shape to a new ecosystem in Europe aimed at improving the air quality in EU ports and supporting the Energy Transition/ decarbonisation in shipping.
Ricardo Batista, Policy Officer, Directorate-General for Mobility and Transport European Commission
Isabelle Ryckbost, Secretary, General, ESPO
Martin Kröger, Chief Executive Officer, VDR German Shipowners’ Association
Kai-Dieter Classen, Deputy Director External Affairs, Hamburg Port Authority
Wolfram Guntermann, Director Regulatory Affairs Fleet, Hapag-Lloyd AG
Torsten Schramm, President Maritime, DNV
10:30-10:50 Coffee break
SESSION 1 ELECTRIFICATION FOR BIG SHIPS
Moderator: Reinhard Lüken, Managing Director, VSM German Shipbuilding And Ocean Industries Association
10:50
Charging for the future: The rise of hybrid propulsion systems
Dr. Torsten Büssow, Managing Director, Electrical & Power Systems Business, Wärtsilä
The marine market is in a move. The decarbonization targets are changing the way we look at a ship propulsion system, that have been like this for decades now. What is the future operational profile? What is the future power source? Will there be more than one? What fuels do we burn? All or these uncertainties you can address already today with a alternative propulsion systems, which will in most cases be hybrid. The presentation explains several hybrid systems we are building at the moment and summarizes our experience of 70 hybrid vessels from Wartsila.
11:05 Enhancing energy efficiency of merchant ships through system-wide control
Stefan Goranov, General Manager, Sustainability Solutions, WinGD The presentation discusses the importance of integrating all the components of the hybrid ship’s energy system on control level, so it functions as a coordinated whole. Particular attention is dawn on the two-stroke engine integration as a crucial factor for maximising the energy efficiency onboard.
11:20
Turbocharging solutions to support the decarbonization journey Simone Bernasconi, Head of Global Product Line Upgrades, Accelleron To support shipping’s journey towards decarbonization, easy-to-implement turbocharger technology can play an important role in reducing the CO2 footprint of existing installations. But to achieve any significant impact, wide market adoption is key. Combining greater efficiency with a sound business case will be vital to maintaining a competitive edge in a low carbon world.
energy efficiency including electrical production for LNG fueled vessels. Natalia Zubenko, Business Development Manager, GTT
SESSION 2: DIGITALIZATION, DIGITAL EFFICIENCY AND THE FUTURE TECHNOLOGY OF THE MARITIME SECTOR
Moderator: Reinhard Lüken, Managing Director, VSM German Shipbuilding and Ocean Industries Association
13:40
Shipping decarbonization and digital thread
Mia Elg, R&D Manager, Deltamarin
This presentation focuses on showcasing a realistic pathway to decarbonized shipping with practical examples from our ongoing projects. We discuss about the related digital modelling and optimization methods and about their application and validation.
13:55
The Digital Wave
Gregory Puckett, Head of Group Digital, MAN Energy Solutions
In his presentation, Mr. Puckett describes the “digital wave” within MAN-ES. From connectivity, to cloud, from data to artificial intelligence. The digital wave is continuous, it is variable, it can be calm one moment, and stormy the next. Most interesting it will never not turn back.
14:10 Digital tool to ensure engine efficiency
Matthias Winkler, Managing Director, CM Technologies
Digitalisation for engine performance measurement including automated data transfer between ships and ashore. Important is the possibility to have all data at one place allowing access from everywhere at any time for anyone. Useful assistance for ship and shore personnel.
14:25 The significance of data in achieving sustainable performance
Pascal Reolon, Head of Digital Product Management, Digital Customer Solutions, Accelleron
A closer look at the analytics layer sitting on top of the electronic logbook and continuous operational data. How enhanced data provides deeper insights into key performance indicators and supports proactive decision making for managing decarbonization.
14:40-15:00 Q&A
15:00-15:30 Coffee break
SESSION 3: THE MOTORSHIP AWARD
Moderator: Lars Robert Pedersen, Deputy Secretary General, BIMCO
15:30 With Orca; Norwegian zero-emission bulk carrier project
Michael North, Sales & Marketing Manager for Norway & Iceland, Lloyd’s register
Earlier this year, Lloyd’s Register awarded Approval in Principle to Norwegian ship owner Egil Ulvan Rederi AS for its zero-emission self-discharging hydrogen-fuelled bulk carrier, With Orca. The innovative vessel will be fitted with two large rotor sails and is planned to enter into a long-term transport contract with cargo owners Felleskjøpet Agri SA and HeidelbergCement. It was designed by Norwegian Ship Design.
15:45 The Aurora Class - the future of deep sea shipping
Henrik Andersson, Head of Sustainability, Hoegh Designed to carry up to 9100 cars, the multi-fuel and zero carbon ready Aurora Class vessels will be the first in the PCTC segment to be able to operate on zero carbon ammonia, signifying a breakthrough in reaching Höegh Autoliners’ ambitious net zero emissions target by 2040.
16:00 Solutions for groundbreaking carbon-transport-and-storage project
Kristian Mogensen, Promotion Manager, MAN-ES
16:15
Two-Stroke
Stam Achillas, Head of Business Development & Sales, 2-Stroke Fuel Conversions, Wärtsilä
+44 1329
DAY
A retrofit-optimised solution to convert existing 2-stroke electronicallycontrolled engines to
either LNG, methanol or ammonia.
The ground-breaking technology will be applied on a 13’000 TEU
MSC containership to convert it first (2023) to LNG and later (2024) to ammonia.
Stefan Goranov, General Manager, Sustainability Solutions,
Four NYK Line vessels will meet IMO’s 2030 target when they enter service
WinGD integrating
technology, energy management and LNG-fuelled engines. Such configurations will reduce the cost of using alternative fuels
Gröninger Privatbrauerei Hamburg, Willy-Brandt-Straße 47, 20457 Hamburg, Germany
Announcement of the Motorship Award winner, Presented by Nick Edström, Editor, The Motorship
- Wednesday 23 November 2022
08:30 Coffee & Registration
09:15-09:30 Recap of day 1 by Chairmen
Lars Robert Pedersen, Deputy Secretary General, BIMCO
SESSION 4 MARKET BASED MEASURES
Moderator: Lars Robert Pedersen, Deputy Secretary General, BIMCO
09:15
09:30
The Future of Bunker Fuels for world’s Shipping Fleet
Jon Buckingham, Chief Mechanical Engineer, BMT
Exploring the carbon pricing mechanism
Sebastian Ebbing, Technical Advisor, Climate, Marine fuels, Innovation, Funding, German Shipowners’ Association (VDR)
09:45
Development of IMO’s Market Based Measure
Chris Waddington, Technical Director, International Chamber of Shipping With the coming into effect of the CII and EEXI requirements in January 2023, the first phase of IMO’s workplan for GHG reduction will be in place. Within the second phase, IMO is now considering a Market Based Measure (MBM). This presentation will outline the various MBM proposals under consideration, and will summarise the remaining processes for finalisation of this measure.
10:00
– Why Carbon Needs a Price
Merten Stein, Head of Shipping Advisory Hamburg & Dubai, DNV MBM focusing on maritime carbon emissions will come into play in EU by and are considered by IMO. But how will they impact shipping cost and what are the consequences for future fuels and technologies? Selected considerations and case studies will address key aspects to spark further thinking.
10:15-10:35
10:35-10:55 Coffee
+44 1329
SESSION
SESSION
Moderator: Lars Robert Pedersen, Deputy Secretary General, BIMCO
10.55 Power-to-X - Decarbonisation with Future Maritime Fuels
Daniel Chatterjee, Director Technology Management & Regulatory Affairs Head of the Green-and High-Tech and NetZero @ PowerSystems Program, Rolls-Royce
11.10
On the Way to Zero Emissions: Considerations for the Design and Operation of Fuel Treatment Systems
Franciska Kjellström, Global Application Manager, Marine Fuels, Alfa Laval
There is currently a high interest in biofuels including FAME and HVO as well as methanol. Ships can already bunker these fuels and engine combustion technology is available. We will discuss the impact of various new fuel types on the ship’s fuel cleaning and fuel supply systems.
11.25 Avoiding stranded assets
Lex Nijsen, Senior Vice President and Head of Sales, 4-Stroke engines, Man ES
The various fuels in gaseous or liquid forms have impacts on fulfilling rules and regulations. In the presentation pathways to decarbonization are highlighted and the value of having options to adapt vessels to fuel supply developments.
11:40 Moving biofuels into the mainstream Monique Vermeire, Fuels Technologist, Chevron Biofuels can offer a carbon-free alternative to other non-fossil fuels, if considered on a lifecycle basis. Monique Vermeire will also discuss the impact of biofuels on NOx emissions and consider their operational and technical implications alongside the regulatory approach to their use.
SESSION
THE FUTURE
Moderator: Sebastian Ebbing, Technical Advisor,, Climate, Marine fuels, Innovation, Funding, German Shipowners’ Association (VDR)
10.55 Carbon Levy Why Advanced Coatings will be Essential to Success in the Age of the Carbon Levy
Philip Chaabane, CEO of I-Tech
11.10 Who can improve energy efficiency in ship operations and bring down emissions?
Rene Taudal Poulsen, PhD, programme director for BSc Program in international shipping and trade, Copenhagen Business School, Denmark We study how a large network of decisionsmakers, including cargo-owners, commercial managers, ship operators, port stakeholders and public actors influence voyage planning and execution. We find that they often pusue commercial objectives, which undermine energy efficiency in ship operations.
11:25 Wärtsilä 2-Stroke Radical Derating Stam Achillas, Head of Business Development & Sales, 2-Stroke Fuel Conversions, Wärtsilä A solution to significantly reduce an existing 2-stroke engine’s emissions by modernising its combustion while preparing it for future fuels.
11:40 Hydrocat - the world’s first dual-fuel CTV Benjamin Weinacht, Managing Director, Compagnie Maritime Belge (CMB) Hydrocat is the first crew transfer vessel operating based on dual fuel, i.e., diesel and hydrogen generating up to 50% of emissions.
Hydrocat is operated by Windcat Workboats which is part of the CMB Group.
11:55-12:15 Q&A
Moderator: Lars Robert Pedersen, Deputy Secretary General, BIMCO
13.45
Technological considerations of ammonia as a marine fuel
Peter Morsbach is Vice President Sales Operations at Høglund Marine Solutions
This presentation will examine the technological considerations that must be overcome on board a ship before widespread adoption of green ammonia as a marine fuel can begin, looking at the technical, operational, commercial, regulatory and environmental aspects such as health and safety (toxicity), materials elections (corrosiveness), engine requirements (combustibility), and emission prevention (engines and fuel system).
14.00 Ammonia as a Marine Fuel is Coming Closer to Materialization René Sejer Laursen, Director, Fuels &Technology, Global Sustainability Center Copenhagen, ABS Ammonia (NH3 ) is identified as a zero-carbon fuel that can enter the global market relatively quickly and help meet the GHG reduction target for 2050 set by the IMO. Ammonia offers ship owners and operators a zero-carbon tank-to-wake emissions profile, regardless of the source of the fuel.
During this presentation you will hear more on the consideration of ammonia as a marine fuel option in both the near-term and long-term.
14.15 Development cycles towards ammoniafuelled two-stroke engines
Dr Andreas Schmid, General Manager Technology Development, WinGD Industry interest in carbon-free fuels has reanimated development towards ammonia-fuelled ship engines. In this presentation, Andreas Schmid will explore the many areas that engine designers and builders are working on to bring safe, reliable and efficient ammonia-fuelled engines to market.
14.30 Engineering the ammonia engine of the future
Kristian Mogensen, Promotion Manager, MAN-ES The development of MAN Energy Solutions’ first two-stroke ammonia engine is well underway. We share our learnings from designing and commissioning an ammonia fuel supply for our test engine facility, along with experiences from initial testing.
14:45-15.05 Q&A
Moderator: Sebastian Ebbing, Technical Advisor, Climate, Marine fuels, Innovation, Funding, German Shipowners’ Association (VDR)
13.45 Methanol: A Future Proof Marine Fuel Matthias Ólafsson, Chief EU Representative, Methanol Institute
14.00 Development of worlds 1st methanol engine for very large container ships
Dr Gwang-Hyeon Yu, Senior Researcher Green Oiwer & engine Systems research, Hyundai Heavy Industries
14:15 Methanol’s Role in the Race to Decarbonization
Daniel Barcarolo, Senior Sustainability Engineer, Global Sustainability Center Copenhagen, ABS Methanol is one of the many fuel options being considered in achieving decarbonization because it offers several advantages including carbon neutral potential, existing infrastructure, and IMO Interim Guidelines. Due to its potential to reduce the CO2 output from marine fuels, applications of methanol are drawing a wider interest from owners of oceangoing vessels, short sea shippers, ferries, cruises, and inland waterway vessels. During this presentation you will hear more on the consideration of methanol as a marine fuel option.
14:45-15.05 Q&A
SESSION 7.1 MULTIFUEL ENGINES
Moderator: Lars Robert Pedersen, Deputy Secretary General, BIMCO
15.35 Will “multi-fuel” propulsion engines be the solution to solve the “future fuel” uncertainty?
Rolf Stiefel, Regional Chief Executive, Bureau Veritas Marine & Offshore
The advent of multi-fuel systems is a key step towards 2030 and 2050 decarbonisation targets, yet a number of challenges must be addressed – from the safety and control of fuels with different properties, to storage, bunkering, infrastructure and regulatory considerations.
15:50 The Multi fuel engine, the main corner stone of a successful fuel transition Maikel Arts, General Manager Market Innovation, Wärtsilä
The Multi-fuel engine technology enables the transition from fossil to renewable fuels through its built in technical feasibilities and economic viability.
Infrastructure and availability of green fuels need time to mature while Multi-fuel engine technology enables shipowners a safe transition journey starting already today.
16.05 Alternative Fuels – Preparing for the impact on marine lubricants
Harriet Brice, Technology Manager Marine Engine Oils, Lubrizol
This presentation will discuss approaches to formulating effective marine cylinder lubricants for use with new alternative fuels. This requires gaining the best possible understanding of new engine designs, fuel and combustion characteristics and the challenges they may present.
16.20 What will a multi-fuel, low carbon future look like?
Eddie Fish, Market Development Advisor, ExxonMobil Marine & Aviation Fuels The IMO’s ambition to reduce international shipping’s carbon footprint creates new challenges for the entire maritime ecosystem.
To overcome them and lead the energy transition, advanced solutions will be needed to meet society’s needs.
Lars
SESSION 7.2 RETROFIT SOLUTIONS
Moderator: Sebastian Ebbing, Technical Advisor, Climate, Marine fuels, Innovation, Funding, German Shipowners’ Association (VDR)
15.35 Combining efficiency technologies with wind to deliver results beyond compliance Tuomas Riski, CEO, Norsepower Norsepower’s Rotor Sails improve environmental performance and reduce fuel consumption, especially alongside other clean technology solutions such as hydrodynamic hull optimisation or hybrid electric propulsion systems Regulation, including EU ETS, is driving shipowners to choose proven solutions, demonstrated by Scandlines’ M/V Copenhagen.
15.50 The role of retrofitting in the Clean Fuel Transition Jan P. Brugger - Co-Founder& COO, FuelSave The use of hydrogen & methanol retrofit echnology can help shipowners to meet IMO Tier III standards. An alternative to urea or ammonia, these solutions achieve substantial emission reductions and cost savings, whilst curbing OPEX.
16.05 Retrofitting to Methanol DF operation an Owners experience Claes Tretow, Project Manager Newbuildings, Stena RoRo AB
16:20 Economic and Ecological Considerations for Wind-Assisted Ship Propulsion Systems Karsten Hochkirch, Head of Ship Performance Center, DNV Wind propulsion is well known and has propelled ships for millennia. However, with the advent of fossil-fuel powered ships, wind energy lost its importance for cargo transport almost 100 years ago. Rising fuel prices and a society being more aware of the consequences of CO2 emissions fuels the revitalization this energy source and a variety of wind assisted propulsion systems are on the market today. Key factors for success of wind assisted propulsion are discussed and a case study for a multipurpose vessel is used as illustration.
SOx STORY DOESN’T END WITH
CAP
8 Value Maritime has developed a modular system that can reduce CO2, particulate matter (99% PM10 and >90% PM2.5) and SOx emissions from conventionallyfuelled ships

These emissions have been linked to asthma, pulmonary, cardio-vascular and respiratory diseases, and a recently published NASA study reports significant reduction in ship track clouds, the polluted marine clouds that trail oceancrossing vessels, since 1 January 2020.
After that date, the IMO's global regulation changed the chemical and physical composition of ship exhaust. Ship track clouds are formed by water vapor coalescing around small particles of pollution (aerosols) in ship exhaust. The highly concentrated droplets scatter more light and therefore appear brighter than non-polluted marine clouds, which are seeded by larger particles such as sea salt. Less sulphur emissions mean there are fewer of the aerosol particles released and less ship tracks.
According to the researchers, similar but regionally defined sulphur regulations – such as an IMO Emission Control Area in effect since 2015 off the west coast of the U.S. and Canada – did not had the desired effect, because operators altered their routes and charted longer courses to avoid designated zones.
The good news on atmospheric pollution doesn’t tell the whole story.
The Exhaust Gas Cleaning Systems Association (EGCSA) might have thought that the independent ecotoxicity study undertaken in accordance with the IMO GESAMP guidelines would end discussion about the potential harmful effects of the wash water discharged from open loop scrubbers. The study indicated that both in a standard OECD port and in a highly trafficked seaway the operation of open loop scrubbers did not create an unwarranted risk.
Don Gregory, Director of the EGCSA, said last year that “the results of the study were not unexpected. The study puts to bed the myth and unsubstantiated claims of some NGOs
who are simply seeking to ban the use of residual fuel oil. They have used rhetoric, sensationalism and unsubstantiated claims or pseudo studies to attempt to discredit scrubbers.”
Still, a recently published study from the Chalmers University of Technology, Sweden, showed that wash water is responsible for up to 9% of certain cancer-causing polycyclic aromatic hydrocarbons (PAHs) into the Baltic Sea. This has led the Swedish Transport Agency and the Swedish Agency for Marine and Water Management to propose a ban on the discharge of so-called scrubber water into the internal waters of the Baltic Sea. Similar bans exist in some European ports.
The study's data was collected in 2018, and at that time there were approximately 180 ships with scrubbers in the Baltic Sea. In 2021, there were almost 600.
According to September 2022 Clarksons Research data, over 4,838 ships now have scrubbers (including pending retrofit), equivalent to 24.9% of the global fleet’s total gross tonnage. While scrubber retrofitting activity has slowed, newbuild uptake grew slightly in 2021.
Equipment manufacturers have continued to innovate. Alfa Laval, for example, announced an upgrade to the water cleaning system of its PureSOx system. Installed on Evergreen’s Ever Ace, the system incorporates three highspeed separators, flocculator modules and a feed pump. Though it serves two PureSOx scrubbers with a combined exhaust gas cleaning capacity of almost 200 t/h, the water cleaning system has a minimal footprint in relation to its high efficiency, says Alfa Laval.
SodaFlexx has developed the concept to treat exhaust gas emissions with sodium bicarbonate powder (baking soda) without the need for sea water intake or discharge. The concept was adapted from proven land-based technology, where sodium bicarbonate (NaHCO3) powder is injected
sulphur
which led to the wide use of low sulphur fuels or the installation of scrubbers, was forecast to lead to a
drop in overall sulphur oxide emissions from ships –a reduction equivalent to 8.5 million metric tonnes of SOxCredit: Samskip
directly into the exhaust gas stream to neutralise SOx. A chemical reaction occurs converting SOx to a highly stable and non-toxic salt – sodium sulphate (Na2SO4). This salt is released safely into the atmosphere or can be captured by SodaFlexx’s bespoke cyclone Particulate Capture System and recycled ashore.
After three years of trials, the latest SodaFlexx dry exhaust gas cleaning system has been installed on the 96,772 dwt Yeoman Bridge owned by BONTRUP. The application is currently in the process of obtaining a US patent, and SodaFlexx was recently contracted for another installation of their EGCS on another BONTRUP vessel Bontrup Amsterdam.
SodaFlexx is trialling technology adapting their proven powder delivery systems to treat and handle CO2 from marine engines. Scale tests have shown promising results, and a shipboard installation is planned for Q1 2023.
With renewed focus on the atmospheric emissions of new fuels, stack technology is now taking another turn. SailPlan is offering a system that directly measures CO2, SOx, NOx, methane, particulate matter, black carbon and around 20 other types of emissions in engine exhausts. The company says that the industry standard, estimating these emissions from fuel consumption, takes a lot of time, can be imprecise, and doesn’t give insights into where improvements can be made.
SailPlan’s monitors are installed on the exhaust stack, and pollutants are identified by continuous emissions monitoring systems (CEMS). The technology platform also includes engine, fuel, speed, and stability data and advanced weather, mapping, and vessel traffic data. SailPlan’s unique micro-stations and Application Programming Interfaces (APIs) collect high-resolution, real-time air quality, observed weather, and vessel traffic data along with live video/audio streams. This data is then uploaded to SailPlan’s cloud and made available securely on the web dashboard, mobile apps, and API.
Harvey Gulf has used SailPlan’s emission measurement technology to directly measure the outputs during different load scenarios on one of its vessels. Before SailPlan, Harvey Gulf could have used fuel consumption to calculate emissions, but fuel input does not take into account the operation of engines and assumes that fuel was combusted fully. SailPlan found that at low speed, methane emissions were relatively high, but load optimisation was able to elimate them.CO2 emissions were only slightly reduced, and SailPlan suggests that this casts doubt on the value of slow steaming as a method for measurable reductions in CO2 emissions.
Langh Tech has conducted several preliminary tests of capturing CO2 emitted by a vessel’s main engine by the means of using an existing Langh Tech closed loop SOx scrubber system. In the tests, additional alkali was added to the scrubber closed loop process water in order to provoke a reaction between the alkali and CO2, effectively capturing the CO2 from the exhaust gas into the process water.
The setup of tests was limited by the capacity of the existing alkali pump, but positive results were observed even with only a slight increase in the alkali dosing. At a main engine load of approximately 85%, a 5% increase in alkali dosing (over normal level) was able to reduce the measured CO2 emission by 3.3%. At 40% main engine load, a CO2 emission reduction of nearly 7% was observed.
During the tests, the alkali consumption remained at a reasonable level, and effect of this to the operating expenses of the vessel would remain feasible. The CO2 capture feature could be applied to any Langh Tech closed loop or hybrid

scrubber systems with relatively low cost impact, with only minor changes to the existing scrubber system. The process could be performed with readily available alkali products such as NaOH and MgOH2, which are both already being used in many SOx scrubber processes.
Langh Tech is also researching methods of extracting the captured CO2 from the process water and looking for ways to store and/or utilise the captured CO2 efficiently both onboard vessels and upon possible discharge to shore.

Samskip is making carbon capture a key part of its integrated plan for decarbonisation by choosing the Value Maritime’s Filtree gas cleaning solution for the container ships Samskip Innovator and Samskip Endeavour. Due for commissioning in early 2023, each Samskip installation will feature a gas cleaning unit behind the ship funnel, with recovered CO2 pumped to a 10MW CO2 battery set housed in ISO tank containers and carried on deck. Charged during the voyage, these batteries are unloaded in port, with Value Maritime trucking them to CO2 consumers such as greenhouses for discharge, then returning them empty for the next voyage.
“We work closely with freight owners who prioritise sustainability and whose end consumers hold them to account,” said Erik Hofmeester, Head of Vessel Management, Samskip. “Samskip Innovator and Samskip Endeavour, for example, run between the UK and the Netherlands on biofuels, which already cut CO2 by 90%. Using the Filtree system in addition will allow us to offer our first carbon neutral shortsea services.”
Value Maritime sees a growing market for the system in the short and long term. The system can reduce CO2, particulate matter (99% PM10 and >90% PM2.5) and SOx emissions in the short term from the 60,000 oil-powered ships. In the long term, the same system can be used to capture CO2 from, for example, green methanol emissions and return it to green methanol plants to make green methanol again. “We encourage the shipping industry to start now with solutions that exist today, make savings, and future-proof your business by staying flexible for the next 2-3 years.”
8 Preliminary results from an installation of SailPlan’s emission measurement technology on a Harvey Gulf vessel suggest slow steaming may not achieve measurable reductions in CO2 emissions
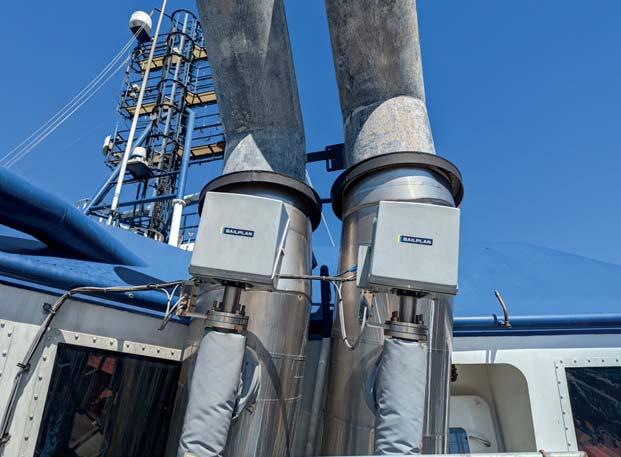
ONBOARD CARBON CAPTURE
INTERMEDIATE STEP
8 Stena Bulk is participating in a two-year project with Alfa Laval, ABS and Deltamarin that aims to be the world's first to demonstrate endto-end shipboard carbon capture at large scale and across the full value chain
That hasn’t squashed enthusiasm. In September, US-based Carbon Ridge secured $6 million in funding to develop its onboard carbon capture system ready for an onboard pilot in 2023, with some of the money coming from shipowners Crowley and Berge Bulk.
“We believe in the potential of onboard carbon capture and storage as one of the effective solutions to enable Berge Bulk’s commitment towards zero emissions,” says James Marshall, CEO of Berge Bulk.
Chase Dwyer, Founder and CEO of Carbon Ridge, is obviously upbeat: “We believe onboard carbon capture and storage will be the lowest cost and most efficient pathway to achieve near-term decarbonisation in the maritime industry.”
Among his competition is Daewoo Shipbuilding & Marine Engineering (DSME) which has now completed the verification process for CCS technology onboard an in-service LNG carrier. The system was jointly developed with Hi Air Korea, a domestic shipbuilding equipment company, and involves the use of an aqueous sodium hydroxide (NaOH) solution for absorption. The system converts the captured CO2 into a mineral that can be unloaded in port or potentially discharged to the ocean, depending on the results of the marine environmental impact assessment currently being carried out. DSME says the system consumes very little energy compared to other CCS technologies and is relatively small.
DSME is also partnering in a project with ABS and Gaslog for the installation of systems on four newbuilding LNG carriers that are expected to be delivered to Gaslog in 2024 and 2025.
And under the terms of an MoU signed in September, HMM and PANASIA have agreed to undertake a feasibility study, economic analysis and risk assessment for a CCS system that HMM is then expected to install on its vessels.
Stena Bulk has also entered the space. In October, the company announced the launch of a two-year project aimed at demonstrating shipboard CCS, partnering with the Global Centre for Maritime Decarbonisation (GCMD), the Oil and Gas
Project REMARCCABLE (Realising Maritime Carbon Capture to demonstrate the Ability to Lower Emissions) will result in one of Stena Bulk’s medium range IMOIIMAXX tankers having a system installed that will target at least a 30% absolute CO2 capture rate (approximately 1,000 kg/hr) during normal vessel operations and on deep-sea voyages. The project aims to be the world's first to demonstrate endto-end shipboard carbon capture at large scale and across the full value chain.
“Since the production of zero-carbon fuels to scale will take some time, we see carbon capture coupled with low carbon fuels as one of the potential pathways to help the shipping industry navigate to a net zero future,” says Sameer Kalra, President of the Marine Division at Alfa Laval.
An MR tanker was chosen for the project as vessels of similar size are estimated to emit 17% of shipping’s total CO2 emissions. The initial demonstration will involve over 500 hours of capture of the exhaust from burning high sulphur fuel oil (HFO) or very-low sulphur fuel oil (VLSFO) and will include offloading of the captured and liquefied CO2 at ports along the route of a 10-day deep-sea voyage. Stena Bulk aims to retain the system onboard and continue using it after the pilot test.
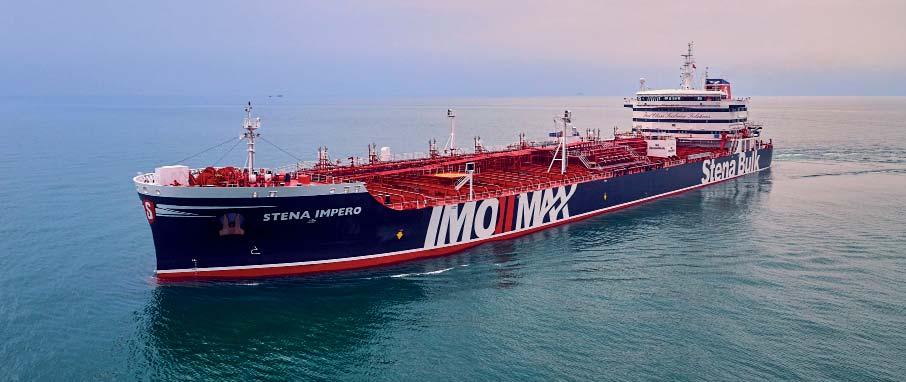
The project will use non-proprietary equipment and processes, so results can be shared broadly and publicly to maximise learning and encourage further development. It also aims to establish a pathway to reduce the cost of onboard CO2 capture to €150 per tonne of CO2 or lower, to allow the technology to be commercially deployed in the near future.
The partners say that although a lot of effort is going into the development of low and zero-carbon fuels, that development alone may not be fast enough to allow international shipping to meet IMO’s greenhouse gas emissions reduction targets. Projections indicate that 85% of the fuel mix for two-stroke engines will remain fossil-fuel based by 2030 and 34% by 2050.
Climate Initiative (OGCI), Alfa Laval, ABS, Deltamarin and TNO.Shipboard carbon capture can help reduce GHG emissions of current vessels, with the possibility of recycling captured CO2 to produce alternative fuels.
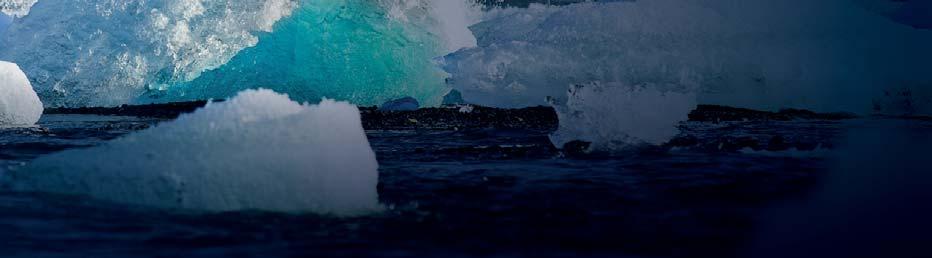
Georgios Plevrakis, VP Sustainability at ABS, says CCS may require significant additional capital and operating expenditure, especially where regulations and technologies are still developing, and the economic feasibility of the technology is still not fully understood. “Onboard carbon capture is only one part of a multi-step process for atmospheric carbon reduction involving land-based and offshore carbon capture technology, temporary storage, offloading and discharging infrastructure, transportation by pipeline or vessel and utilization or geological sequestration. For onboard carbon capture to be considered viable, an economic feasibility case must be built.”
Typically, carbon capture systems may not effectively capture all carbon from the exhaust stream, he says. While it is possible to capture higher percentages of carbon from the exhaust, more input energy and/or additional equipment may be disproportionately required. The effectiveness of carbon capture systems to purify exhaust gas varies widely, depending on the type of capture system, rate of absorption, capture system size, fuel type, fuel consumption rate and the amount of CO2 concentration in the exhaust gas.
Operators must therefore decide the quantity of carbon intended to be captured based on emission reduction goals in relation to operational profile and the feasibility of additional equipment, storage space supporting systems for onboard capture systems as well as discharge locations.
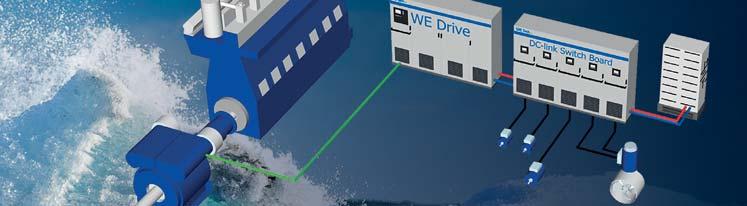
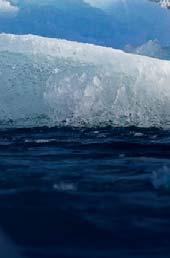
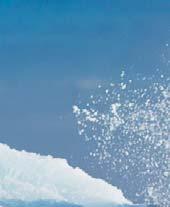
ABS released Insights into Onboard Carbon Capture in





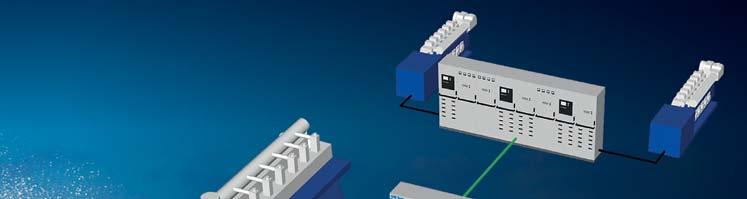
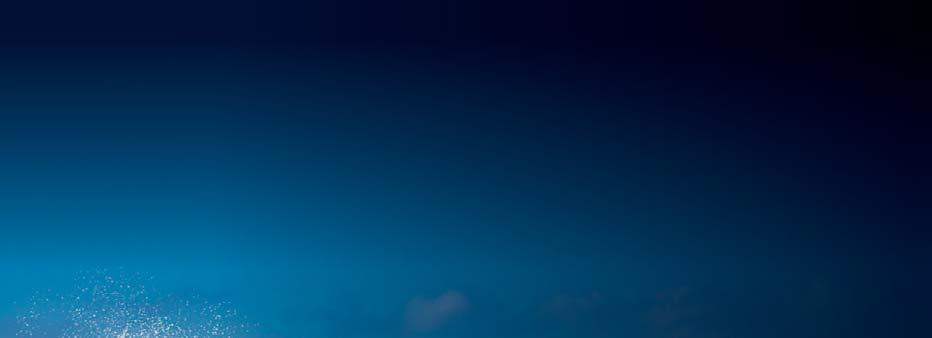

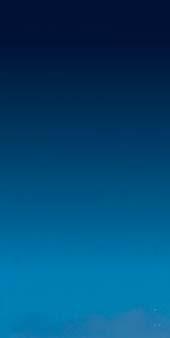
September 2022 to help inform the industry of the issues. The report discusses energy requirements onboard, noting that they vary depending on the type and size of the system, the flow rate of exhaust gas into the system and the target efficiency for carbon removal.
“The energy requirements for carbon capture can increase immensely as the target capture rate rises,” it states. The energy is required for equipment such as heat exchangers, chemical regeneration activities, steam generation, pumps, compressors, condensers, evaporators, reactors and
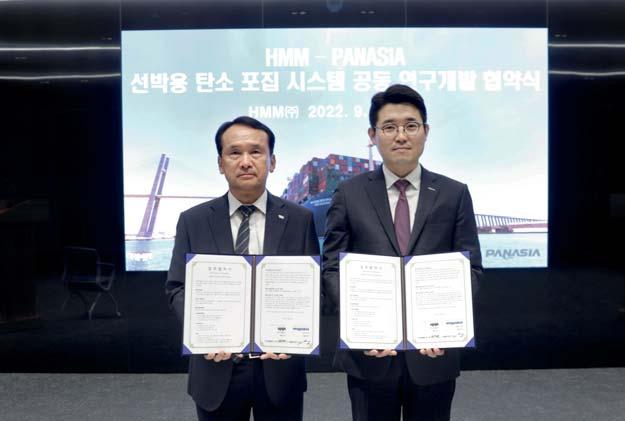
liquefaction systems. And the energy requirements come in addition to the usual vessel loads, so more power may be required from onboard engines and auxiliary generators. This in turn increases the amount of CO2 emissions.

The CO2 liquefaction equipment in particular can significantly increase the required energy supply. Yet, if liquefaction is not performed, the space required for onboard storage of gaseous CO2 would likely increase prohibitively.
The storage of CO2 onboard raises management concerns including its potential corrosiveness due to its moisture content and contaminants. Sufficient power is required to maintain the pressure and temperature of the compressed or liquified CO2 within set limits. There will need to be foundational support for added equipment, and vessel strength and stability needs will need to be met. There will also need to be equipment for measuring and verifying the amount of CO2 captured, stored and offloaded.
The ship design will need to consider the potential for CO2 leakage or release of CO2: it is a dense gas that does not readily disperse. CO2 detection and alarm systems will be required, and non-welded connections will need to be minimised for leak protection. There will need to be emergency procedures in place and crew training on storing CO2 and incident response.
ABS participated in a study released by the Mærsk McKinney Møller Center for Zero Carbon Shipping in September 2022. The report examined the role of onboard CCS and concluded that the technology was not readily suited to some vessel types. It considered a series of case studies and analysed the impacts of full or partial application of CCS on container, bulk and tanker vessels using carbon-based fuels, as part of a newbuild or retrofit.
Installation of a system on to bulk carriers could be challenging due to the space and system integration required. For an 82,000dwt bulk carrier, for example, one cargo hold would probably be needed to house CO2 storage tanks. While on average it costs around 40% of the newbuild price to install a system, it can be as high as 70% for smaller bulk carriers, states the report.
For the case of a 15,000 TEU container vessel, a RotterdamSingapore single trip (8,300 nautical miles) was used as the reference route with CO2 receiving facilities located in both Rotterdam and Singapore. A round trip case was also investigated but proved difficult due to a large increase in hull girder shear force (+20%) and stability problems caused by increased CO2 storage requirements.
The VLCC evaluated was least impacted by installation of a CCS system, because two CO2 storage tanks could be fitted on the forward part of the deck. This would, however, necessitate raising the height of the navigation bridge by 4-5 metres. The tanks also increase maximum longitudinal bending moment of a vessel by 5-10%, so depending on strength margin of the original design, hull reinforcement or operational limitation may be necessary. There is no cargo volume loss, but the vessel’s lightweight increase leads to a deadweight decrease of 3-4% (2,800-3,600 tons).
For a VLCC newbuild, the best business case studied, CO2 abatement cost ranges from $220-290/ton CO2 with a tankto-wake effective CO2 emission reduction of 74-78%. The VLCC’s endurance was based on a Persian Gulf -Japan round trip (13,400 nautical miles over 41 days) at a speed of 14.5 knots. For LSFO, the CCS system increases CO2 emissions by 42% due to the additional energy demand. For maximum carbon capture, about 55% of the additional energy is required for electricity (for circulation pump, liquefaction, etc.) and another 45% for steam (for separation of CO2).
The CAPEX to install a system on a VLCC ranged from 26% of
the newbuild price for an LNG-fuelled ship to 42% for a LSFOfuelled ship. Additional OPEX ranged from $2.3 million for the LNG-fuelled ship to $5.2 million for the LSFO-fuelled ship.
The major driver of additional OPEX for the ship types evaluated was the fuel consumption of the CCS system, which can be more than 70% of the total additional OPEX. Excluding fuel cost, OPEX is estimated to be around $0.5-2 million per year depending on vessel type and size.
Based on the case studies completed, the report predicted that CCS with chemical absorption is technically feasible and expected to reach commercial availability by 2030. Additional CCS energy requirements lead to higher total fuel consumption (up to a 45% increase), so the potential application of CCS shows the most promise for newbuilds. Retrofits are costly and can require major modifications.
While onboard CO2 capture rates can be high, they do not directly translate to the expected well-to-wake (WtW) emission reductions of between 55-60%. This is less than some new fuels but could still make a significant contribution to reducing the emissions of existing fuel oil vessels, especially where the build-out of renewable energy or sectoral competition is too high for shipping to get access to near-term low carbon alternative fuels.
The researchers conclude that CCS can be applied to all carbon-containing fossil, electro, and biofuel power solutions and, as a result, could play a mid- to long-term role in maritime decarbonisation. However, this would depend on several factors including CCS technology development, commercial viability, alternative fuel prices and availability, and future emission-related regulatory requirements.
Shipowners Maersk, Seaspan and NYK participated in the study, demonstrating once again that industry interest is increasing. Seaspan’s decarbonisation strategy includes CCS as the company believes the path to zero carbon includes several potential trajectories: For LNG or light gas fitted vessels, the company anticipates a longer-term decarbonisation pathway through synthetic or bio-methane. Additionally, bio/synthetic liquid drop in fuels will be used. Longer term, the company expects other GHG mitigating technologies to develop to maturity, such as solid oxide fuel cells, onboard carbon capture, and alternative fuels.
Although CCS systems are still being piloted, investment is expected to increase over the course of the next decade, and technology development is ongoing, within and beyond the shipping industry. As Dr David T. Kearns, Principal – CCS Technologies at the Global CCS Institute, says: “The CCS sector has been growing at an unprecedented rate in recent years, and that growth is only accelerating. The increased dependence of global plans for net-zero on CCS means that the economic performance of CCS is becoming increasingly ficant
years, and that is accelerating The incre dependence for net-zero on CCS means economic of increas important. Technology development will be a signi driver of improved economics for CCS.”
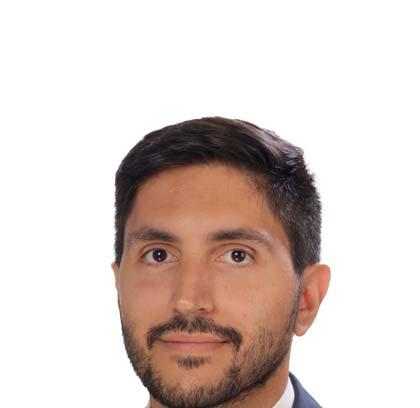
8 Georgios Plevrakis, ABS Vice President, Global Sustainability
SOLVENT CHOICES WILL AWAIT ON BOARD CCS TRIALS: WÄRTSILÄ
Wärtsilä is marinizing a solvent-based carbon capture system, which has been successfully deployed in stationary applications for many years.
However, one of the key differences between stationary and maritime installations is the need to minimise space requirements in marine systems, as this impacts the economics of carbon capture and storage systems.
The regeneration capability of the final solvent is likely to impact the volume of consumables required for the operation of the system. “We are assessing different solvents to find the right balance between efficiency and optimisation,” Javaid told The Motorship, although the final decision between the shortlisted solvents is likely to be made after the onboard trial.
The onboard storage options for the captured CO2 is another area where Wärtsilä is examining different options. Initially, it appears likely that Wärtsilä will liquefy the CO2 to store the gas on board the vessel, although “the temperature and pressure is still being discussed”.
Modular EGCS approach
Kashif added that Wärtsilä’s engineers were already looking at potential product level solutions to allow a CCS option to be added to existing Wärtsilä scrubber systems.
“We expect the unit to be attached as an additional unit… [which is consistent with] our modular approach which allows us to add on additional technologies to tackle pollutants in exhaust gases.” Javaid noted that there were also likely to be different challenges for different ship types, with container vessel installations likely to have some impact on container capacity, while the installation configuration was likely to be a greater challenge for bulker and tanker vessels.

Promising results from Moss trial Kashif Javaid told The Motorship that Wärtsilä had agreed to trial a carbon capture and storage system onboard a Solvang vessel, the 21,000cbm ethylene carrier Clipper Eos, with the installation provisionally expected to take place by Q4 2023.
Wärtsilä’s engineers have been conducting tests at the Moss test facility since December 2021. The initial results of trials of the stationary installation at Wärtsilä’s Moss test facility in Norway had produced encouraging carbon capture rates of “60-70%”.
Sinotech targets Q4 for onboard CCS trial
Sinotech CCS Co. Ltd., a Shanghai-based developer of carbon capture solutions, plans to install its first CCS unit aboard an Asian owned vessel by November 2022.
The developers signed a worldwide distribution agreement with Ecochlor in August 2022. Depending upon the results of the first trial, which should be completed within “8 to 10 months”, the company intends to bring the CCS solution to market by Q3 or Q4 2023.
In common with several other developers, Sinotech is marinizing a mature aminebased absorption-based technology that has been successfully installed within China’s coal-fired power generation sector.
The company has received Approvals in Principle from a number of classification
societies, including Bureau Veritas, Lloyd’s Register and ClassNK.
The solution stores liquefied CO2 within an onboard deck mounted Type C CO2 storage tank at around 20 bar. The solution uses a compression and separation system to remove impurities from the waste gases. The process incorporates a drying step before compression to eliminate moisture to minimise the risk of dry ice formation.
The solution requires around 1kg of amine to capture 1 tonne of CO2. The comparatively low price of amine (USD3,000/tonne at current market prices in late August) means that the cost of consumables was unlikely to be significant.
However, the solution was also expected
to be sensitive to desired carbon capture rates, opening up the opportunity of “flexing” rates away from the 25% CO2 capture rate. This might be particularly interesting for deep-sea vessels on longer routes, where the storage of captured carbon dioxide might become significant.
Another interesting aspect of Sinotech CCS’ development plans relates to its plans for processing the CO2. Sinotech plans to discharge the CCS from the onboard CO2 storage tanks while in port.
The company already has an agreement with China’s largest oil company, Sinopec, to supply the captured CO2. Sinopec uses CO2 within its upstream operations for enhanced oil recovery.
8 Wärtsilä Exhaust Treatment expect to install the new carbon capture unit on Solvang’s Clipper Eos, sister ship of the Clipper Enyo (pictured) by Q4 2023Kashif Javaid, Director of Sales at Wartsila Exhaust Treatment, discusses the progress of Wärtsilä’s CCS solutionCredit: Solvang
APPROACH POSSIBLE, BUT COMPLEX
A Ricardo Energy & Environment report submitted to the IMO’s Intersessional meeting of the Working Group on reduction of GHG emissions from ships (ISWG-GHG 11) in March 2022 mapped existing standards, regulations and methods for calculating WtW emissions for new fuels and concluded it would be possible to apply lifecycle principles to a fuel GHG intensity factor covering WtW emissions.
However, the report notes that because of variations in feedstock, production methods, and distribution practices, the upstream element of the GHG intensity needs to be calculated for each fuel pathway and potentially each process or batch of fuel. Examination of exhaust emissions may require engine or vessel certification to reflect the powertrain technology and any exhaust catalysts. Even then, exhaust emissions may depend on the engine operational profile.
Tore Longva, DNV Principal Consultant, believes the IMO’s Lifecycle Assessment (LCA) will need to consider individual production lines, but this would entail giving the same certification for many batches. He notes that this sort of certification has already been achieved in the EU as part of the Renewable Energy Directive, and for sustainable aviation fuels, so he believes it is achievable.
“If you study the same fuel with different assumptions, different methods, you get quite different results,” he says. This means the IMO is going to have to make some decisions on, for example, how electricity used to produce hydrogen will be accounted for. There is a variety of different sources including coal, hydropower and nuclear power, so countries such as France, Norway and Poland would have different upstream emissions.
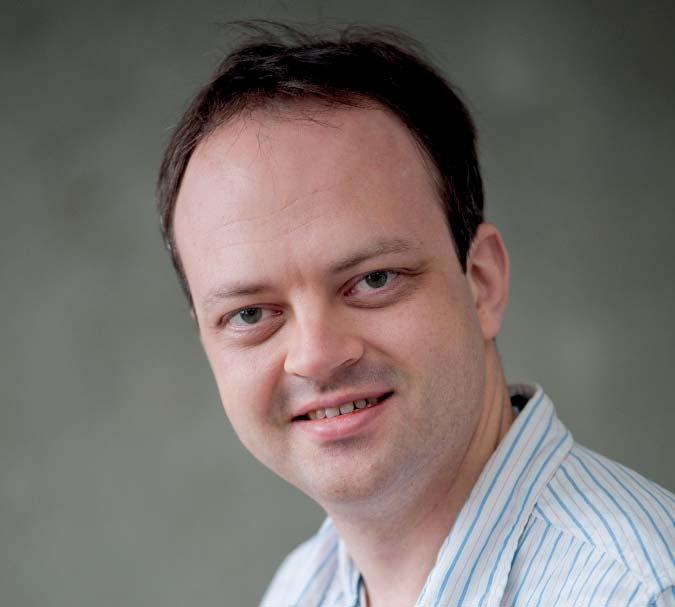
The IMO is currently considering about 100 upstream pathways, covering all types of fossil fuels, biofuels and hydrogen-based fuels, as part of its LCA work. Biofuels are expected to be a popular choice for improving Carbon Intensity Indicator (CII) performance in the short-term and this needs urgent attention, says Longva, but the IMO is expected to tackle other new, hydrogen-based fuels over time.
When the first version as adopted in July next year, the LCA will be a standalone guideline, so it doesn't automatically apply to specific IMO regulations. The work to achieve that also needs to be done, but Longva notes that there are already proposals under consideration to allow biofuels to boost CII calculations.
Simon Bennett, ICS Deputy Secretary General, says: shipping requires global rules for GHG reduction. “Otherwise we have chaos.” As well as the technical complexity, he says there is also political complexity. “This does not mean it can’t be done. It’s just that in the current stage of the IMO negotiations there are lots of moving parts.
“The focus of the current IMO GHG reduction regime for the existing fleet is tank-to-wake (TtW) emissions only. As ICS explains in an important new publication Reducing GHG Emissions: A Guide to IMO Regulatory Compliance this includes the approach adopted for the new carbon intensity framework with which ships will have to comply when the
latest amendments to MARPOL Annex VI enter into force globally on 1 November 2022. But in the current negotiations at IMO on how shipping can decarbonise completely (and ICS advocates for net zero emissions by 2050) addressing upstream emissions are on the agenda.
“Many governments, like China, argue that IMO has no mandate to regulate upstream emissions caused by ships or to impose costs on these via an economic measure, which they insist must be addressed by the commitments they have made for their national economies under the Paris Agreement. But this is not to say that these governments don’t care about the upstream emissions created by the new fuels which the shipping sector may decide to use.
“Hopefully the situation will become clearer when IMO has finalised guidelines on carbon life-cycle assessment. These might allow the sector to ‘reduce’ the carbon factor of certain fuels like biofuels or green methanol, even if they are still calculated, nominally, on a tank-to-wake basis. For example, IMO could agree that some of these emissions ‘don’t count’ because they are taken out elsewhere in the carbon life cycle and are therefore not part of the IMO inventory (which is permitted by UNFCCC accounting).”
Whether what the IMO decides on will be consistent with regional regulations such as the EU’s FuelEU Maritime proposal is uncertain, but disputes have already arisen in the absence of any industry-agreed methodology. A recently released International Council on Clean Transportation (ICCT) report, Comparing the Future Demand for, Supply of, and LifeCycle Emissions from Bio, Synthetic, and Fossil LNG, predicts
8 Tore Longva DNV Principal Consultantapproach into the
that the industry
that using renewable LNG could cut well-to-wake (WtW) CO2e emissions by 38% based on 100-year global warming potentials (GWP) but raise emissions 6% based on 20-year GWP because of methane’s strong near-term warming effects.
It cites methane slip from marine engines as a key consideration, but in rebuffing the results, industry body SEALNG said the figures are based on historic vessel fleet data that is dominated by older, obsolete 4-stroke low pressure dual fuel diesel electric engine technologies which have relatively high levels of methane slip. A recent study commissioned by SEA-LNG concluded that bio-LNG can make a major contribution to maritime decarbonisation.
Steve Esau, SEA-LNG COO, notes that all alternative fuels, be they LNG, methanol or ammonia share the same decarbonisation pathway, starting with fossil and ending with synthetic hydrogen-based fuels. “LNG provides immediate GHG reductions of up to 23% on a well-to-wake basis and an incremental pathway to full decarbonisation via bioLNG and synthetic (e-) LNG. Fuels such as methanol and ammonia start from a worse and more expensive place - fossil-derived methanol has 14% higher emissions than VLSFO on a full lifecycle basis, whereas the figure for ammonia is 47%. This means that these alternative fuels cannot replace VLSFO until enough renewable energy capacity has been built to produce them at scale.”
Upstream projects are advancing. e-methanol producer Liquid Wind recently undertook a lifecycle assessment which concluded that the product produced from its a commercial-scale renewable facility, FlagshipONE, will have carbon equivalence up to 94% lower than fossil fuels.
Paul Delouche, Strategy Director at Bureau Veritas, says: “Achieving decarbonisation in WtW terms will require unprecedented collaboration and transparency with upstream and production chains, including a broad range of stakeholders from energy and chemical suppliers to authorities and financiers.”

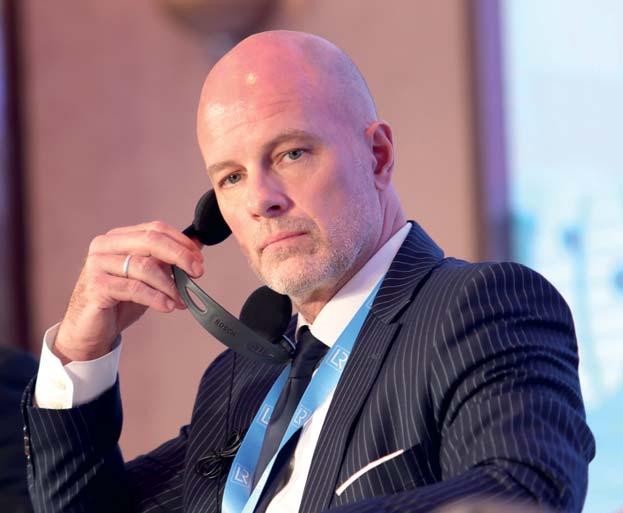
Chris Chatterton, Chief Operating Officer, The Methanol Institute, highlights four important implications of WtW analysis for shipping. “First, it would provide an investment signal and foster innovation in renewable power generation and avoid transferring the reallocation of GHG emissions to upstream fuel production processes.
“Second, the burden of decarbonization would belong to the entire maritime sector rather than to shipowners alone.
“Third, it will enable the industry to respond to fastapproaching regulatory targets and adopt sustainable fuels without delay, and finally, it would foster policy that incorporates incentives as well as presenting investment signals.”
er stment

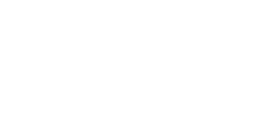
plant. Prins agrees with SEA-LNG’s belief that full lifecycle analysis for all alternative fuels is central to the effective decarbonisation of shipping and other hard to abate sectors. However, he notes that bio-LNG, comes with its own set of challenges when measuring its environmental impact on a full life cycle basis. “For example, transparency on the bioLNG feedstock and traceability of the supply chain is key. This poses an international regulatory challenge. However, the EU does already have standards in place. Namely the revised Renewable Energy Directive (EU) 2018/2001 (RED II). Certification schemes like the International Sustainability and Carbon Certification EU (ISCC EU) are compliant to this standard and are recognised by the European Commission. These certification schemes ensure that bio-LNG can be traced back to a sustainable source.”
Dylan Prins, Renewable Fuels Business Development, Titan, says the company is focused on bio-LNG at the moment although it is committed to delivering all fuels that will decarbonise shipping and industry. It has recently announced the creation of the world’s largest biomethane liqui

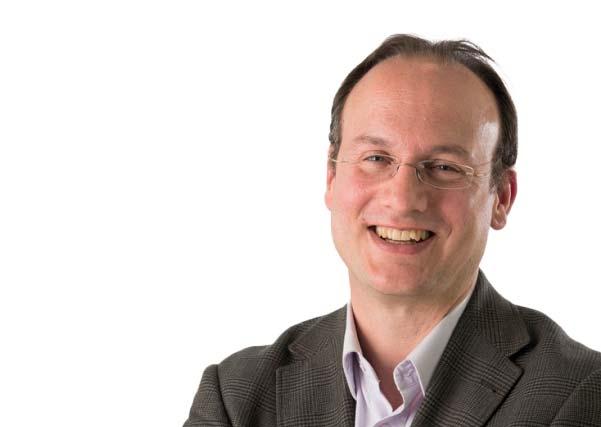
n bio-LNG at the moment vering all fuels that will t has announced biomethane fication
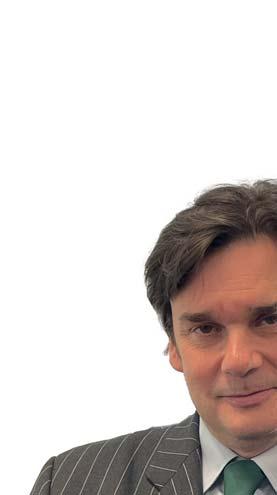
otherwise be vented into the res in a reproce
These are the must is achievablpyy
Titan is ISCC EU certified and only buys from, and partners with, organisations that are certified by a European Commission recognised scheme such as ISCC EU. This is important, says Prins, because different feedstocks and production methods will result in different lifecycle emissions reductions. When produced from domestic and agricultural waste, bio-LNG production can capture methane that would otherwise be vented into the atmosphere, resulting in a fuel that is not just net zero in GHG emissions, but also potentially net negative. “By assisting with the reprocessing of waste materials, bio-LNG can support the circular economy and help with yet another global concern: waste management. These are the type of variables that must be factored in but comprehensive lifecycle analysis is achievable.”
8 Chris Chatterton, Chief Operating Officer, The Methanol Institute
8 Left to right: Dylan Prins, Simon Bennett Steve Esau
KEEPING STEADY IN ROUGH
8 The newly converted SOV, Norwind Breeze, has been equipped with an Uptime walk to work rental system
The dangers of moving cargo and personnel has always been a key issue for the maritime and offshore industry. Legislation around safety regulations is being highlighted more as new products come on to the market.
The latest developments that are happening in the offshore market also focus on the safety aspect and also standards of operation.
Palfinger has recently launched its latest design of PF crane that will meet with the latest safety requirements for the offshore wind segment.
The new range has been designed in accordance with the latest technical requirements of the European standard EN13852-3 for light offshore cranes and plays an important role in lifting spare parts and equipment in the daily offshore wind industry supply chain.
The European standard EN13852-3 covers requirements for all significant hazards, hazardous situations and events relevant to light offshore cranes for lifting of goods and lifting of persons, when used as intended and under conditions foreseen by a risk assessment.
“Because access to offshore wind farms is limited and every working hour must be efficiently used, we’ve made the new PF cranes highly resistant to the harsh environmental conditions. Furthermore, we reduced the maintenance effort to lower the life-cycle-costs for the wind park owner. The new crane range was designed based on more than fifteen years of installed base experience and feedback from service teams and our clients. It is therefore well positioned for the future requirements of the global offshore wind industry”, says Franz Schnöll, Head of Global Marine Product Management.
The crane has a modular design and standardized reach
from 3 to 7 meters, the redesigned crane can lift materials and tools from the crew transfer vessel (CTV) onto the transition piece (TP) platform of the wind turbines. Furthermore, it will be used during routine inspection and service work throughout the turbines' entire operational life.
Beyond its compact design, each crane undergoes thorough function and load tests at the assembly plant before being delivered. This procedure ensures ‘plug and play delivery’ with the highest safety standard and minimised installation time.
The company highlights that more than 250 of the fixed boom cranes have been ordered and are scheduled to be delivered to the UK, Taiwan, USA, and Japan between Q4/2022 and Q2/2024. They will be installed on jacket and monopile bottom fixed structures as well as substations and used for servicing offshore wind turbines and other equipment installed on substations.
Further in the offshore market Seaonics has received an order by Norwind Offshore to supply its all-electric gangway.
“With these new contracts, SEAONICS further reinforces its position as a supplier of specialised lifting and handling technology in the offshore wind market,” says Managing Director Håkon Fauske. The company signed the contract with the shipbuilding group VARD for installation aboard two of Norwind Offshore’s new vessels.
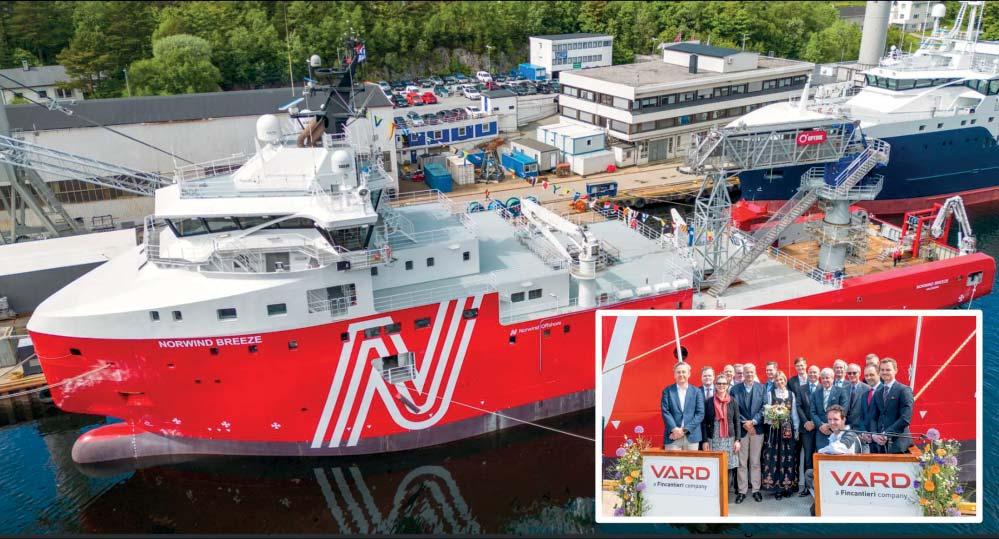
According to Ståle Fure, Head of Sales, SEAONICS is delighted to have been selected for these projects. “The deliverable comprises a ‘Walk to Work’ gangway from our newly developed SOV concept, whose primary focus is effective cargo and personnel handling,” he continues.
Whilst the ‘Walk-to-Work’ concept may not be something totally revolutionary for the industry. It is often highlighted
and can also been seen these days on social media, the dangers of crew and cargo transfer, especially in rough conditions at sea.
The Seaonics ECMC Gangway is the latest generation of ‘Walk to Work’ gangways that features improvements in technology. With growing demand for autonomous operations and functions, the company has developed an auto-landing system based on imaging and sensor technology to minimise the risk of human error during critical operations.
The fully electric gangway compensates for the vessel’s movements on three axes to keep the tip still and land it safely on bottom-fixed installations, such as offshore wind turbines and sub-stations. The technology utilised by the system will provide better operations, while helping to minimise their impact on the marine environment, the company claims.
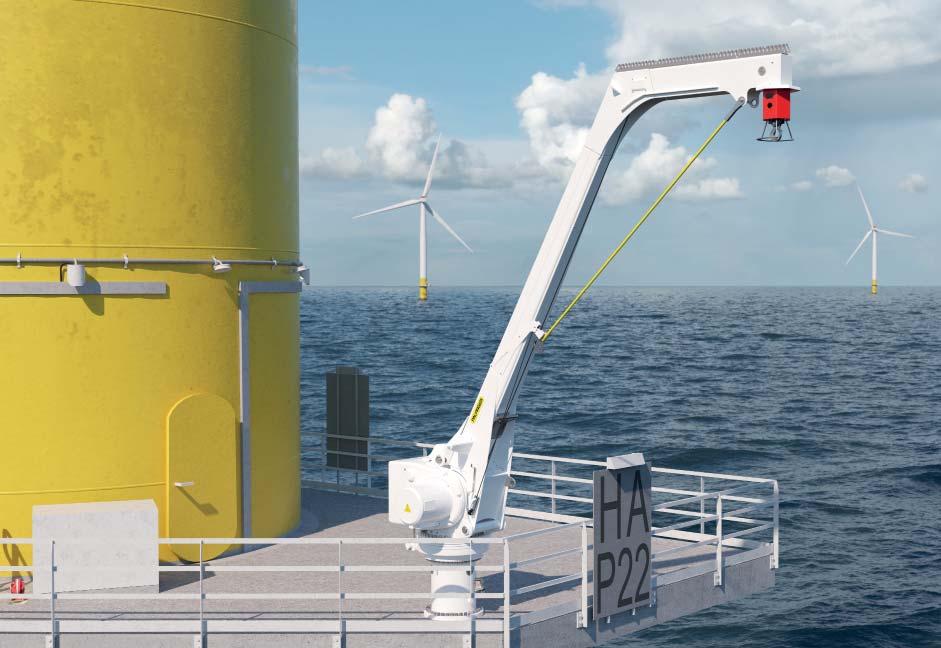
Earlier this year Amplemann supplied US offshore company Otto Candies with its walk-to-work system. An E1000 motion compensated system will be supplied to the marine transportation and towing company to facilitate operations during the construction of Southfork-, Revolutionand Sunrise wind farm - three commercial scale wind farms in the north-east US Atlantic. The company notes that this is a significant step for this type of technology in the American renewable energy sector.
The E1000 will be fitted onto the Inspection, Maintenance and Repair Vessel (IMR), Paul Candies, in Q3 2023, to support the hook-up and commissioning of turbines. The system compensates for all six degrees of freedom in relation to the vessel and turbine, it will enable safe, consistent, and reliable offshore access in sea states up to 4,5m Hs during its yearlong operation.
Along with providing safe access for personnel, the system will also be used to hoist cargo, equipment, and tools up to a 1,000kg and the gangway’s fuel transfer capabilities will allow for the testing of the generators and turbines. By converting the Paul Candies into a W2W vessel, the E1000
will enable the servicing of multiple turbines at once, greatly increasing the speed and efficiency of operations.
Norwegian offshore equipment manufacturer Uptime also saw another order for its system from Norwegian offshore company. Norwind Offshore order the system for its latest vessel to join its fleet, Norwind Breeze, a former PSV that has been converted to a SOV by Vard Brattvaag. The vessel is equipped with an Uptime walk to work rental system as a frontrunner, while the ordered Uptime 30m autonomous system is being finalized.
The Norwind Breeze is the first vessel of the newbuild program for the offshore wind company, Norwind Offshore, of a total of five vessels. The vessel is of VARD 4 01 design, developed by Vard Design in Ålesund in close cooperation with Norwind Offshore. The renewables company Ørsted has contracted the Norwind Breeze in their project for developing the world’s largest offshore wind farm, Hornsea 2 on the British continental shelf.
Although, the offshore market took a turn for the worse with the financial crisis, there are slow but sure signs that this market is coming back. With the focus now being more on safety and looking after crew the need to have the right type of equipment onboard to keep them safe has exponentially grown. How, the developments in digitalisation will see this equipment develop in future will also be an important factor as vessels become more ‘connected’.
8 Palfinger latest PF crane has been designed in accordance with the latest technical requirements of the European standard EN13852-3 for light offshore cranes
With these new contracts, SEAONICS further reinforces its position as a supplier of specialised lifting and handling technology in the offshore wind market
‘‘
LOWER BALLAST DESIGNS OFFER OPEX AND CAPEX ADVANTAGES
While the sloping of the design below and above the waterline is novel for LNG bunker vessels, it is a regular feature of icebreakers and has also it was introduced by Flensburg Shipyard to increase the main deck width, for a given waterline width to carry increased containers or trailers on deck.
The author should declare an interest, having proposed the design in Engineering for Ship Production, as a way to simplify ship construction and thus increase shipyard productivity and lower building costs.
Although the study was instigated for an LNG bunker vessel it is applicable to any type of ship. The ballast draft and trim are stipulated in the Classification Society Rules, but the study used 70% of the design displacement. Any difference could affect the results requiring more or less ballast water thus changing the limits in the charts, but the concept is sound. Although the Ballast Free approach only appears to be applicable for small ships, the Reduced Ballast concept still has benefit for ships of all sizes.
In the original article, reproduced below, one of the stated disadvantages was that the Sloped Hull Form would probably have an increased building cost. This was only because it is different and so the builders of the new design will play safe. In fact, it is believed that the design will actually have a reduced building cost resulting from a reduction in structural manhours and possibly reduced propulsion power.
When the author originally proposed the concept to a potential customer in 2018, the approach was not accepted as there was no need for a bunker vessel operating in the same area if not the same port to prevent the introduction of indigent species. However, the remaining advantages still applied. Not only the reduction in required ballast space but reduction in size of the ballast treatment plant.
GTT is to be commended for presenting this concept in the design of an LNG Bunker Vessel and performing tank testing that showed that the Sloped Hull Form has no negative propulsion or manoeuvring problems.
Ballast Free/Reduced Ballast Ship Design
There have been several attempts at designing/building ballast free ships. The impetus for this is the transfer of indigenous sea creatures from one part of the world to another where they can adversely affect the eco system.
IMO has issued Laws for ballast transfer which in turn brought about renewed interest in ways to solve this problem. Most ships have used ballast water treatment system. It should be remembered that even so-called ballast free designs may still need some water ballast, usually in the peak tanks, to be able to control trim and propeller immersion on ballast voyages.
Ballast Free Concepts are only possible for ship types with low Deadweight to Displacement ratios and usually small ships. However, sometimes ballast is required for stability reasons even for these ships.
So, for a ship to be ballast free (defined by requiring no
water ballast for normal operations), it must be able to be at an operating draft of about .5 to .7 (smaller ships require higher value) of the design draft on return/empty voyages.
To examine the potential for ballast free/reduced ballast (BF/RB) designs for LNG Carriers a study was performed for a 7,500 CBM LNG Bunker vessel and 80,000 CBM and 174,300 CBM LNG Carriers and the results will be presented, but first the concept and advantages and disadvantages will be examined.
Ballast Free/Reduced Ballast Design Concept
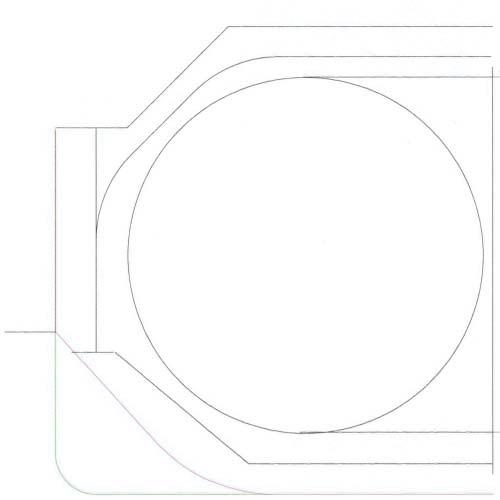
The traditional hull form design approach for commercial ships is to maximize the Midship Section Coefficient with as tight a bilge radius as practical. This gives a relatively direct draft to displacement curve, so if the ballast draft was to be 70% of the design draft, approximately 70% of the displacement would be required. The BF/RB approach is to change the displacement curve shape so that at the lower drafts there is less than traditional hull form thus requiring deeper draft for same displacement. This can be accomplished by sloping the hull sides below the design waterline and using a large bilge radius as shown in Figure 1.
Study Results
The draft displacement curves for Traditional and BF/RB hull forms were derived for a 7.5 K CBM LNG Bunker Vessel, an 80 K CBM LNG Carrier and a 173.4 K LNG Carrier. The curves are shown in Figures 2 to 4 respectively.
It can be seen that the 7,500 CBM Bunker Vessel can achieve complete Ballast Free operation whereas the two larger ships cannot. They can, however, achieve significant reduction in the amount of ballast carried, namely 46.7% and 37.8%. This could result in a smaller ballast treatment plant. There is a building cost (probably increased) associated with the BF/RB hull form and the reduced size of ballast water treatment plant. To decide if this approach is economically
8 Figure 1. Traditional and BF/ RB Design Concepts
Thomas Lamb offers a personal perspective on the potential advantages of ballast free ship designs, and their potential applications for LNG bunker vessels and carriers
beneficial a cost analysis of the various options would be required.
LNG Bunker Vessels
For the low-end of the scale, like bunker vessels, these will be restricted to a port or small coastal area, so they would not be bringing different species from one part of world to another, so they will not require to have ballast treatment equipment. However, if it is still desirable from any other consideration, there are advantages and disadvantages.
Advantages for LNG Bunker Vessels
5 Deadweight/displacement ratio will be about 0.5 to 0.7, which means the empty ship will have more than 50% of the loaded draft but will require careful arrangement design so that the empty ship will have correct trim for propeller immersion.
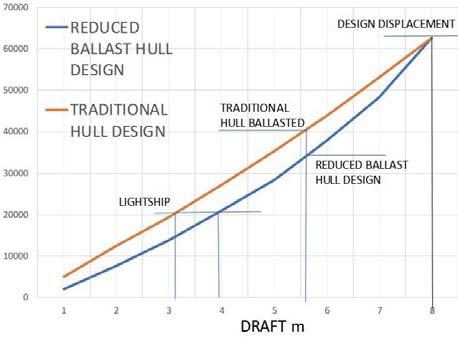
5 Existing CDTS designs already have used larger than normal bilge radius, to extend the length of the parallel body, and for ballast free approach, non-vertical sides below the design waterline would be used
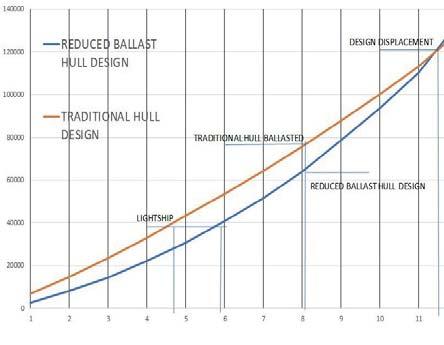
5 Also, the relatively low Deadweight to Displacement ratio for LNG carriers, especially smaller ships, makes it easier to achieve ballast free designs if required
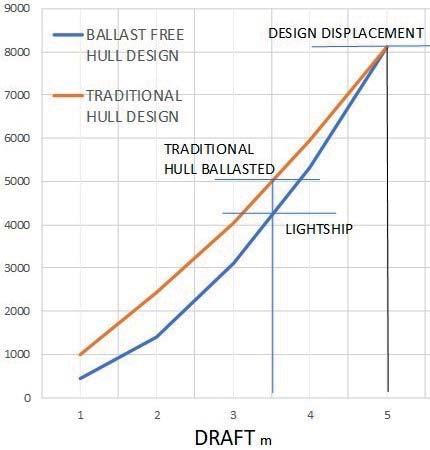
5 Significantly smaller Midship Section Coefficient increases Prismatic Coefficient for same Block Coefficient and MAY reduce powering.
5 Increased Prismatic Coefficient will increase length parallel body thus benefitting installation of LNG Tanks
Disadvantages for LNG Bunker Vessels
5 Forward deckhouse will make it more difficult to get this balance
5 If water does get into double bottom or side tanks, there is no adequate drainage system to empty them
5 It removes any draft/trim control from the operation of the ship, for example, to get propeller immersion for empty ship there will be significant difference between drafts aft and forward, and forward draft may not meet Classification requirements, and
5 then if there is a need to get empty ship with LEVEL draft for getting into very shallow ports or drydocking, they will not be able to do so.
5 The double bottoms and side tanks will become void spaces/cofferdams which can have equally or worse maintenance problems than ballast tanks
5 There may be resistance and powering penalties associated with this type of hull form, so it will require extensive model towing tank tests
Some of these could apply to the Reduced Ballast cases but the main would be the reduction in ballast space on the ships.
ULSTEIN’S THOR AWAITS JUDGEMENT
Navies around the world already operate onboard reactors, but this belies their cost and impracticality. Each reactor is accompanied by dozens of highly-trained technicians – an approach at odds with maritime’s drive toward lean-manning and de-skilling. Costs, meanwhile, are a military matter.
However, there are some few examples of a nuclearpowered ship being used to carry cargo. Beginning in 2018, Sevmorput, a Russian icebreaker, was used to transport frozen fish east to west along the Northern Sea Route (NSR), from Petropavlovsk-Kamchatsky to St. Petersburg, twice as fast as would be possible on the Trans-Siberian railway. But the second of these voyages was cancelled, because despite having a power source on board which would not need to bunker fuel, the voyage economics could not be justified.
Even amid atomic age naivete, the story was scarcely different. Savannah¸ a nuclear-powered liner intended to carry passengers and cargo, suffered no reactor trouble, but seemingly every other kind of mishap, including strikes among the irreplaceable nuclear-trained crew. The onset of low-cost air travel promptly put paid to the passenger side of the business, and containerisation ruined the business case for the breakbulk cargo shipments as well. On top of this, many ports decided they wanted nothing to do with the ship, citing safety concerns.
Savannah’s bad luck ended when was taken out of service a year before the Arab Oil Embargo, an inflection point which might have seen nuclear shipping become the norm, had it remained extant.
In 2021, Korea Atomic Energy Research Institute (KAERI) and Samsung HI embarked on a plan to develop molten salt reactors (MSRs) for marine propulsion and floating nuclear power plants. Lee Dong-hyung, head of the KAERI's innovation strategy department, said that "the use cycle of nuclear fuel for MSR is more than 20 years, which is the same as the vessel's own life cycle, so there is no need [for the reactor] to be replaced, once installed.
“Furthermore, MSR is so small that it can be fitted on a vessel,” he added.
Raising the hammer
Now, Ulstein shipyard believes it has uncovered a business case for a civilian nuclear-powered vessel: Thor, short for
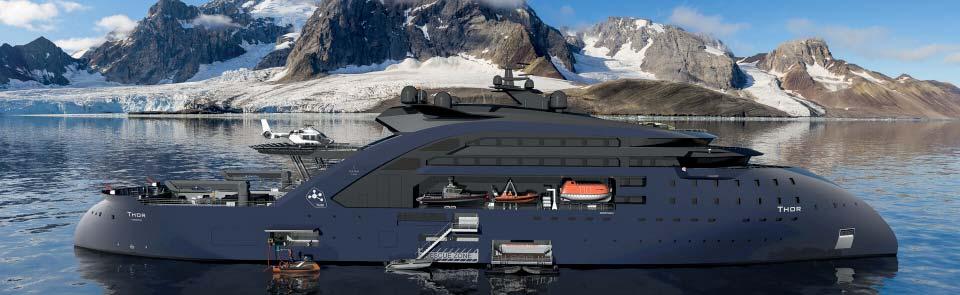
thorium, a nuclear material in abundant supply in Norway. It would be used as a kind of nuclear FPSO for bunkering battery-powered expedition cruise vessels, and remote workboats.
Thorium has a number of advantages. It is estimated that there is enough to last for thousands of years; it has a radioactive half-life of 500 years compared with uranium’s 10,000. Proponents say that a molten salt reactor (MSR) using thorium would prevent itself from melting down a la Chernobyl or Fukushima, since the further the reactor goes above the 600°C operating temperature, the more rate of fission decreases.
But the main case for allowing thorium reactors to pass into civilian hands – that it is ‘proliferation resistant’ -- is a matter of debate. Proponents argue the fuel cannot be used to make bombs, as it is not fissile. But uranium-233, which is created when thorium is bombarded with neutrons, certainly can. A U-233 warhead generated a blast of 22 kilotons when tested by the US in 1955.
As Catherine Kristiseter Marti, Ulstein Group CEO, explained to The Motorship, Ulstein is not a designer of nuclear reactors, and the Thor design is one of a ship built to house one, rather than a nuclear-powered ship design per se. This will be a comfort to nuclear energy’s detractors. “What is extra, or special about our design… is [its capabilities] in remote areas. The X-Bow, the X-Stern, gives it better operability further offshore, and makes it perfect for those areas.”
Kristiseter Marti also said that Thor represents a nailing of Ulstein’s colours to the mast, on one side of the nuclear debate: the company, she says, wants nothing to do with uranium. “Internally, when we get asked these questions, it’s a no [to uranium] because it can be weaponised. We feel that it would ruin the purpose of Thor.”
Though there is no entity currently weighed down with working thorium MSRs and in search of a ship to put them in, Kristiseter Marti told The Motorship that her yard must get ahead of such eventualities. “We launched the X-Stern in 2015-16 and it got no attention whatsoever,” she said. It was only after the X-Stern was installed on the first windfarm vessel, that it became “a big hit.”
“You need to keep trying,” she added. “It’s the only way to stay ahead.”
8 A design developed before a propulsion solution: Ulstein’s Thor design is an example of a thorium MSR ready design
decarbonisation technology so uncertain, the possibility of running ships on nuclear energy is once again under quiet discussion

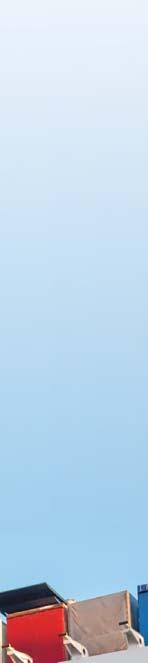

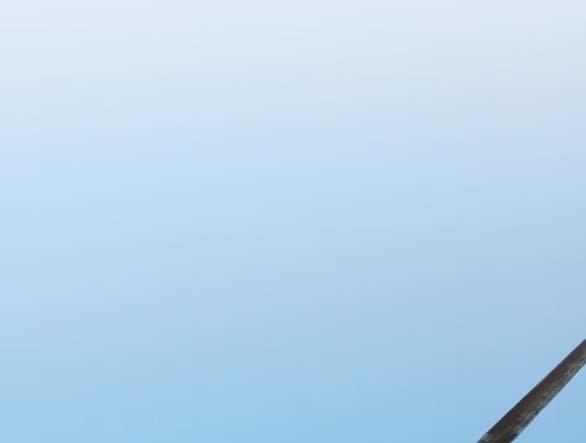
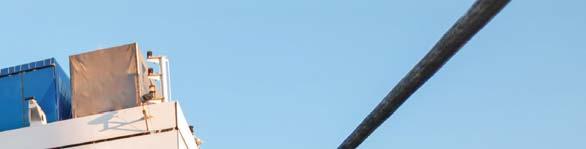
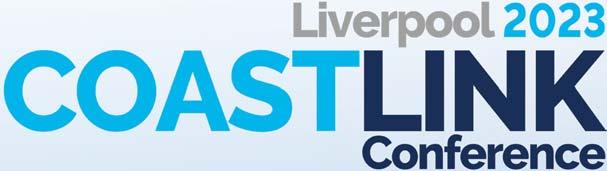
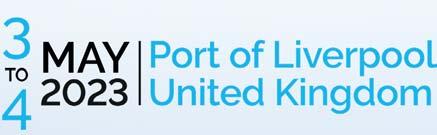

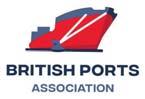

FINNISH PAPER MAKER SHAPES RO-LO SERIES
Leading a new class of three Chinese-built ships tailored to the stringent requirements of the Baltic forestry products industry, the 122m Bore Way combines cargo carrying flexibility with a reduced carbon
The commissioning of the 6,770dwt Bore Way is the latest stage in the unfolding of a programme launched in August 2019, when UPM entered into long-term charter agreements with Helsinki-based Bore and Delfzijl-domiciled Wijnne Barends, both affiliates of the Dutch group Spliethoff.
Under the pact, the operators undertook to provide seven newbuilds in total, comprising three ro-ro/lo-lo(ro-lo) vessels on Bore’s part, primarily to handle UPM paper products, and four lo-lo multipurpose cargo ships from Wijnne Barends, to carry exports of pulp and other forestry goods and return loads of raw materials.
Common features stipulated for the two distinct vessel series were ice class and LNG propulsion. Structural reinforcement to sustain the high cargo densities associated with the paper trade has been another facet of the Bore Way type. DNV provided key expertise for the project, and the society’s application of a ‘rolling approval process’ facilitated the technical work and collaboration with owner, charterer, and designer.
Employing designs developed by Conoship International of Groningen, construction of all seven ships was entrusted to Wuhu Shipyard in China, located on the Yangtse upstream of Nanjing.
Deliveries of the 5,900dwt quartet for Wijnne Barends began in January 2022 with the handover of the 115m Lady Marie Christine, while the first of Bore ships was completed towards the end of April. Build schedules as a whole have suffered from the havoc wrought by the Covid-19 pandemic,
affecting not only the yard but the supplier network in China, with completion of the Bore Way having originally been expected in the autumn of 2021. However, future consorts Bore Wave and Bore Wind are now due in quick succession.
The ro-lo’s superstructure is located far forward, with all ro-ro and sto-ro cargo handling effected over the 14.5m-wide stern ramp direct to and from the single, box-shaped hold. Paper and other products are stowed using clamp trucks, with transfers and also direct shipments made using rolltrailers or cassettes.
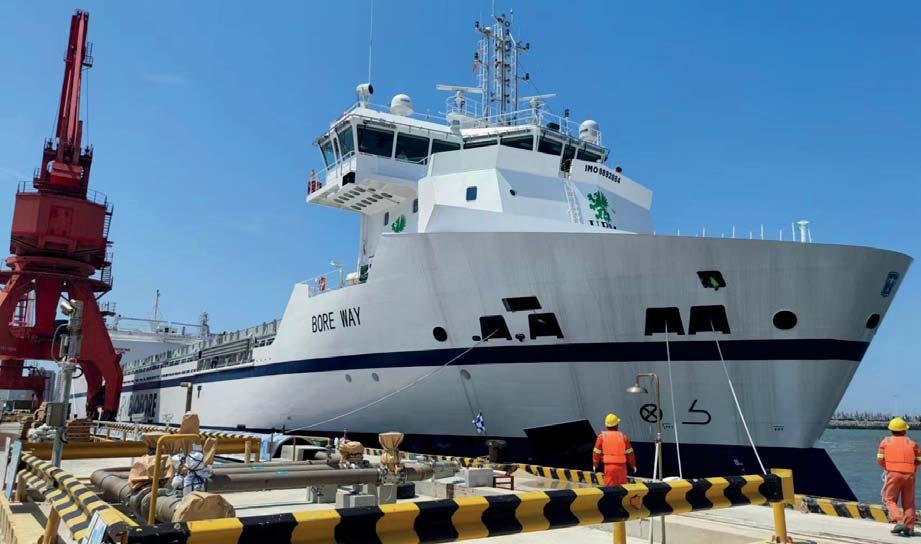
The ro-ro intake equates to 435 linear metres in lanes of 2.9m width. The vessel’s arrangement also facilitates the lolo mode, whereby freight is worked to and from the hold by means of shoreside cranes. Moreover, the lift-off hatch covers can bear containers. A two-high stack on deck plus a two-high load in the hold renders a potential box capacity of 264TEU. Crew accommodation is located in the bow section, in keeping with the design focus on maximisation of the hull length for cargo space, leading to the placement of all machinery below the large, obstruction-free cargo hold.
“While the Bore ships will carry a wide variety of forestry products, whether in break-bulk form, on trailers or in containers, the transport of paper reels involves the most stringent requirements,” explained Jaap Nieuwenhuis, manager of the design department at Conoship International. Calculations were accordingly based on paper reels as the reference cargo. The result is a vessel providing exceptional structural strength and rigidity to avoid elastic deformation in
8 Bore Way will give year-round service to UPM’s Finnish paper millswrites David TinsleyCredit: Bore
rough seas or while loading and unloading heavy rolls of paper.
Paper is especially sensitive to handling procedures and to temperature and air moisture conditions, and considerations from a design standpoint also took due account of the ambient changes entailed in trade between the Baltic and more equable and warmer climes to the south. To protect cargo from quality-damaging environmental influences, particular importance was attached to ensuring that the hatch covers and the stern ramp form tight seals when closed, and to the system of climate control in the hold.
Dehumidification of the cargo spaces required an extensive system of air ducts that needed to be integrated into the walls of the hold. “Finding a way to route these ducts and gutters to drain moisture without compromising the structure of the ship, all the while meeting the required damage stability, was quite a challenge,” explained Conoship naval architect Roel Blom. The ducts ensure a continuous, horizontal air flow throughout the entire cargo space without leaving any dead spots.
The design configuration also favours overall ship productivity, in that cargo capacity can be utilised for return, northbound shipments of raw materials for UPM’s paper production mills in Finland.
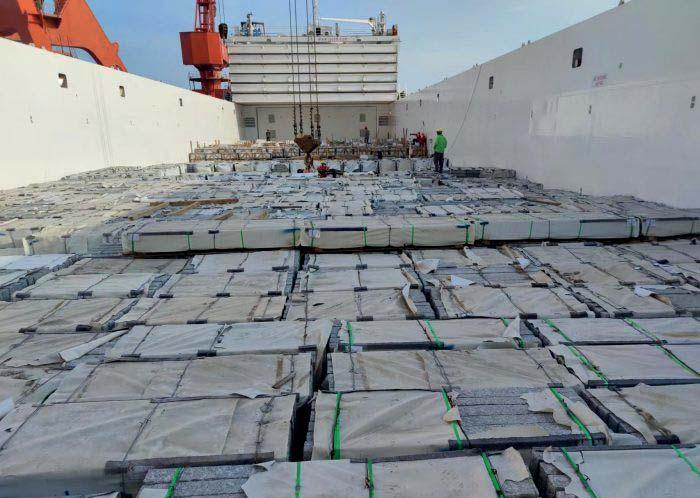
The space availability, or confinement, below the ro-ro deck, where all the machinery is located, had to be reconciled with the need to accommodate the most suitable engineering and propulsion equipment and systems.
Wartsila’s compact, well-proven 34DF design of mediumspeed, dual-fuel engine, chosen in its eight-cylinder model, delivers propulsive power via reduction gearbox to the controllable pitch propeller. The 340mm-bore, four-stroke engine offers 500kW per cylinder at maximum continuous output, making for a 4,000kW nominal power concentration.
Allowing for a 15% sea margin, the installation gives an open-water service speed of 13.5 knots, and a maximum 15 knots on ballast draught, and confers the requisite ice-going capability for harsh Baltic winter conditions. The 34DF can operate with equanimity on either MGO or LNG, the latter fuel being fed from a type C tank of 250m3 capacity sized for a round-trip, and located below the ro-ro deck and forward of the engine room.
The energy-saving strategy saw the inclusion of WE Tech’s Solution One system, consisting of a WE Drive and a variablespeed shaft generator, interposed on the transmission.
The WE Drive renders significant benefit by allowing the shaft generator to be operated at variable speed, which in turn enables the propulsion machinery to be run at the most efficient point. In PTO mode, the ship’s electrical power will be wholly supplied at sea from the shaft generator, obviating any need for auxiliary sets to be fired-up. Moreover, the bow thruster motor incorporates a variable-frequency drive, further reducing power consumption.
Electrical energy is otherwise obtained from two 250kW gensets, each based on a Volvo Penta D13 diesel.
Beyond the economic foundation for a technical approach which scrutinises every aspect of energy usage, the provision for primary operation on LNG aligns with UPM’s environmental agenda. Besides the fuel’s beneficial properties in largely eliminating SOx and soot particles and in cutting NOx by 85%, running on LNG is expected to cut CO2 emissions by 20-25% relative to operation on MGO.
“UPM has committed to reducing the greenhouse gas emissions of its supply chain by 30% by 2030,” said Lauri Rikala, director of UPM’s Global Break Bulk Shipping, adding that “As part of our efforts to meet that target, it was crucial for us to invest in a modern fleet to meet the most stringent
environmental requirements. And through these investments, we will also help deliver a lower carbon footprint to our customers’ value chains.” UPM claims that the charter arrangements for the Bore ships and the other Spliethoff Group newbuilds signifies its pioneering of a new path in the forestry industry, upgrading its transportation network with environmentally ‘smart’ vessels.
The use of LNG as the main fuel was clear from the beginning, according to Bore’s marine management vicepresident Joergen Mansnerus: “It significantly reduces carbon output and almost eliminates all other emissions, and the market is growing. Furthermore, we believe that LNG is more than a transitional fuel. For our fleet, we consider that fossil LNG can eventually be replaced by biofuel as a drop-in. Biofuel can be produced from the by-products from paper and pulp manufacturing and other organic waste; a biofuel plant recently opened in Finland, and more will follow. Some other Scandinavian shipowners are already using biofuels.”
The project is testament both to the integrated approach adopted by industry and the shipping community in the Nordic region, and to the ever-rising international profile of Chinese shipbuilding in bespoke fields of vessel production.
PRINCIPAL PARTICULARS - Ro-ro/lo-lo Bore Way
Length overall 121.89m
Length bp 113.61m
Breadth 21.00m
Depth 12.40m
Draught 6.75m
Ro-ro capacity 435 lane-m
Lo-lo capacity 264TEU
tonnage 9,133t
Deadweight 6,770t
Main engine power 4,000kW
Fuel LNG/MGO/MDO
Speed, maximum 15kts
service 13.5kts
Main generators 2 x 250kW
thruster 500kW
Class DNV
Class notations
1A General dry cargo ship, RO/RO Container, BIS, BWM(T), Container DBC, DG(B, P), E0, Gas-fuelled, Ice(1A), LCS, NAUT(NAV), Recyclable, TMON(oil lubricated)
Flag Finland
8 High stowage factors in all modes are afforded by Bore Way’s single hold
POWER AND DESIGN TO ATTRACT THE YOUNG
Purpose-designed for students of maritime courses related to inland shipping, the 67m futuristic-looking Ab Initio is equipped as a learning and operating platform, and technology demonstrator, in keeping with the rapid pace of change taking place in the sector. ‘Sustainability’ is to the fore in the newbuild, which incorporates a hybrid dieselelectric propulsion system with battery pack, a 200m2 solar panel array, and hydrogen fuel cell.
The project was initiated in 2018 by the Rotterdam-based training specialist STC Group, backed by a grant from the De Verre Bergen Foundation (SDVB) and with subsequent sponsorship from a wide range of organisations, including marine equipment companies and Rotterdam’s port and municipality.
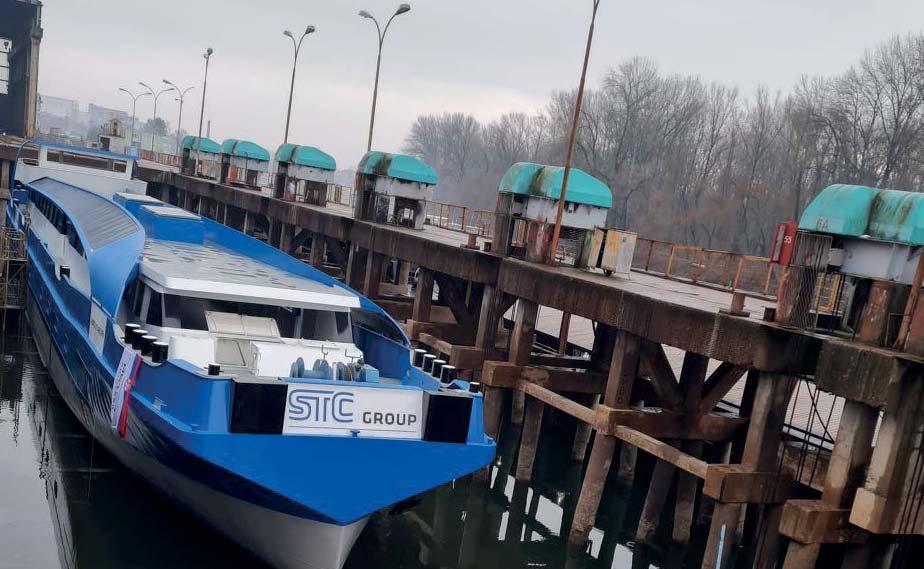
The focus from the outset was on achieving a state-ofthe-art training ship, drawing on the latest insights and developments from the Dutch maritime sector, and raising the appeal of careers in the industry for young people. The newbuild award to Concordia Damen was announced in April 2020, whereupon hull construction was assigned to a yard in Serbia, with outfitting to be undertaken at the main contractor’s Werkendam premises on the Nieuwe Merwede waterway in the southern Netherlands.
Ab Initio (Latin for “from the beginning”) will replace two STC training ships dating from the 1960s, both of which were bought by Concordia Damen in conjunction with the newbuild deal.
There are 39 berths aboard, providing for up to 30 students plus crew and training staff
Besides the primary role in developing and instructing future masters, deckhands and technical personnel, the vessel will double as a field laboratory in which companies can trial new equipment and technology, in collaboration with HBO-level students. The socio-economic dimension to the project, as reflected in SDVB funding plus local authority and government support, is to contribute to Rotterdam’s future maritime standing to the benefit of the community.
Dutch consultancy C-Job Naval Architects provided the design, which draws only 1.8m and has been conceived to allow flexibility and facilitate through-life updating as regards powering. While a hybrid configuration was foreseen from the outset, the decision to also install a fuel cell module was only made by STC during construction, which necessitated a substantial increase to the original budget, achieved through subsidy applications and sponsorships by members of the maritime cluster.
STC’s rationale for the addition to the technical specification was the expectation of a growing role for hydrogen in the shipping industry. Zepp Solutions was accordingly nominated to produce and supply an integrated 45kW fuel cell system and 35kg-capacity hydrogen storage. The fuel cell will serve as a range extender, charging the vessel’s battery system. The compact nature of the module is a key characteristic, and the minimisation of critical interfaces and incorporation of all sub-systems reduces integration
complexity and cost and makes for a ‘drop-in’ solution.
The adoption of fuel cell technology has meant that sailing duration in emission-free mode has been very substantially increased, potentially doubled, from the four hours initially envisaged on the 400kWh battery installation alone. Bunkering hydrogen, which will take place in Rotterdam, and working with the proton exchange membrane (PEM)-type fuel cell will form part of the students’ learning process.
The possibility of retrofitting larger fuel cells or alternative, zero-emission energy systems to replace one of the two generators in the future has been taken into account in the layout and construction of the vessel. The drive train is modular, and the Stage V-certified generators can be accessed or lifted from above through hatchways. One of the aggregates is a 600kW KEES generator from Koedood, which uses Mitsubishi high-speed engines, and the other is a 280kW set from Volvo Penta.
The propeller is driven by an Oswald permanent magnet propulsion motor, and De Waal supplied the complete, oillubricated shaft installation and seals, low-resistance Easyflow rudders and steering gear.
A dedicated training room provides a view through soundproof window to the engine room in the stern section, so that instruction to students can be carried out without disturbing operations. Furthermore, the vessel has been modelled on STC simulators, and is to be equipped with sensors to facilitate remote monitoring of operational data and consumption and for maintenance purposes.
One facet of ‘hands-on’ training is the vessel’s push bow and coupling winches, so that students can learn how to handle barge coupling and uncoupling procedures.
The hull was built at the Apatia yard in Serbia, with support from Gebr de Jonge Shipbuilding Services. The ‘casco’ was then transferred by push tugs, via the Danube, Rhine, Waal and Merwede, to Concordia Damen at Werkendam, where outfitting and completion work was carried out in cooperation with local subcontractor CCM3.
8 Hull of Ab Initio in transit from Serbia for completion in the NetherlandsPractical, long-term thinking as regards the next generation of maritime personnel is expressed in a newly-completed, innovative Dutch training vessel, writes David TinsleyCredit: STC Group
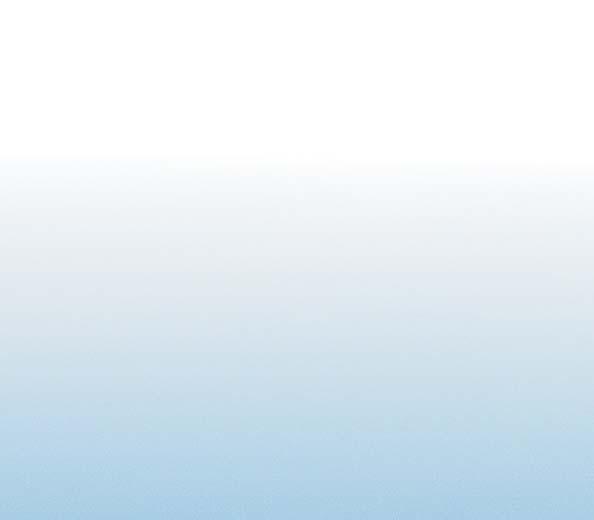

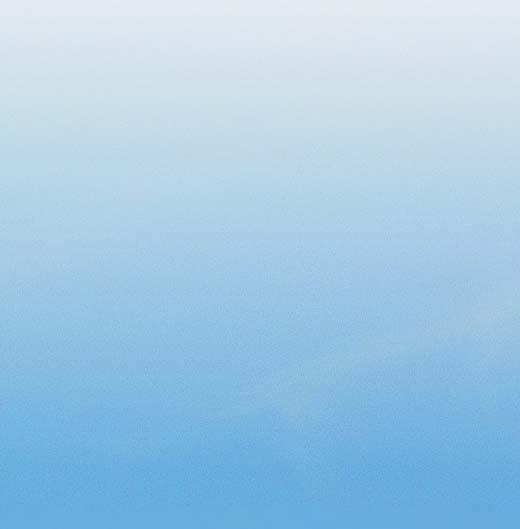
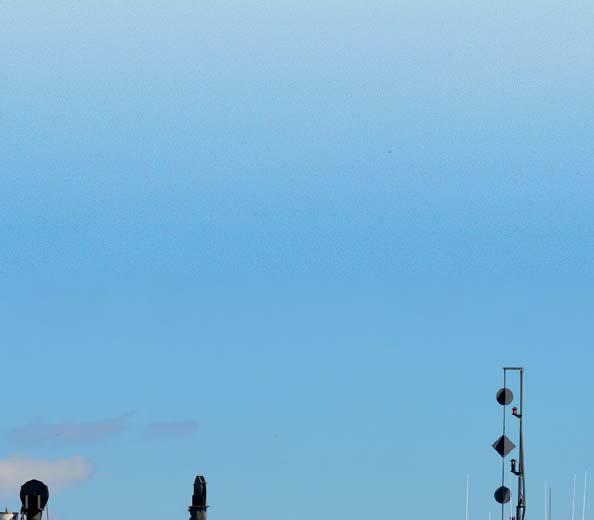
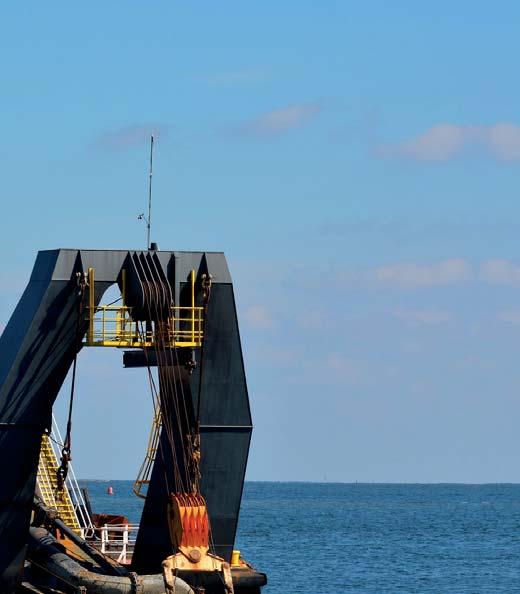

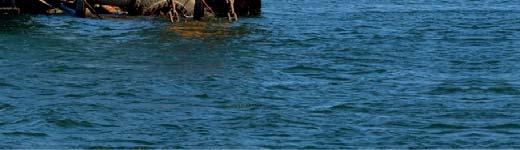

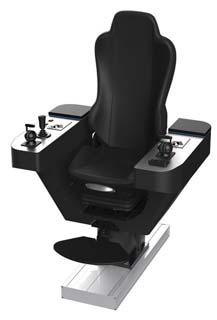
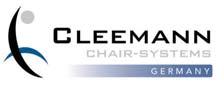

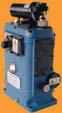

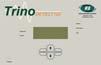
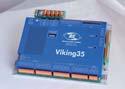
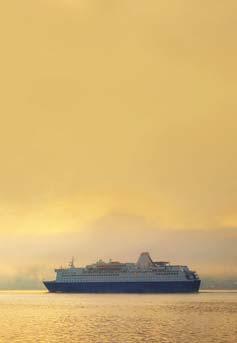


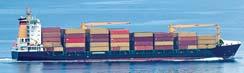


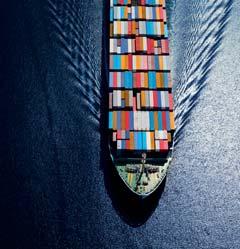

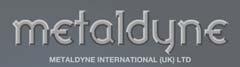

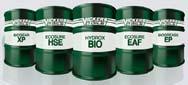


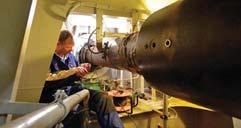
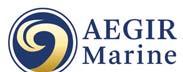



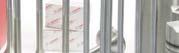

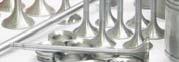

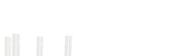

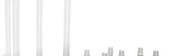
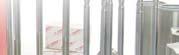

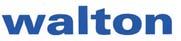
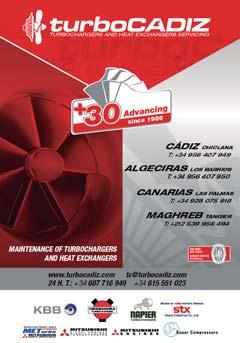
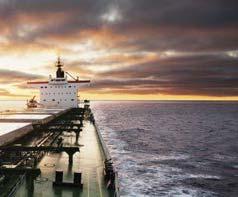

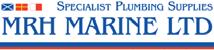
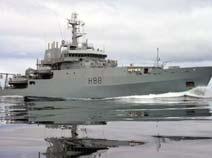

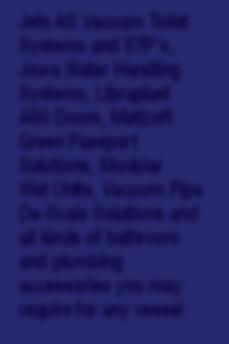

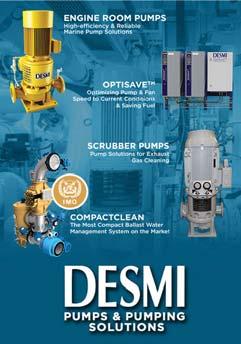


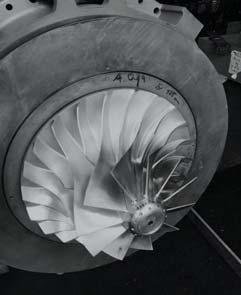


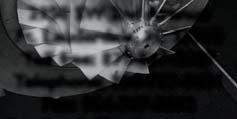
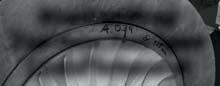


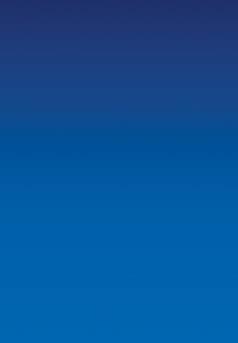



THE ENGINEROOM OF THE FUTURE
The international magazine for senior marine engineers
EDITORIAL & CONTENT
Editor: Nick Edstrom editor@mercatormedia.com
Correspondents
Please contact our correspondents at editor@motorship.com
Bill Thomson, David Tinsley, Tom Todd, Stevie Knight, Wendy Laursen
The Motorship, November 1972, contained a special supplement centred on B&W engines. It began, rather boldly, with an article by a technical adviser to a shipowner group considering the requirements of engine plants in the future.
The article suggested that the industry was emerging from a period of abnormal disruption with the introduction of container ships, extra-large tankers and bulkers, and various types of specialised tonnage. On the other hand, there was a trend for reduced numbers of technical staff. Therefore ease of maintenance and reliability were the prime considerations for forward-looking shipowners. This, said the author, could be addressed by more standardisation in ship and machinery design.
The demand for more power was paramount – this could be met by diesel engines up to about 30,000 bhp, but above that, geared steam turbines would predominate. With the possible power demand from a large container ship seen as 175,000 bhp, the marine machinery sector would need to carry out considerable improvement and development, with the low speed diesel engine remaining the prime choice, though medium speed units were gaining support. The idea of standardised safety and pollution rules was floated, but conversely this could restrict competition and lead to complacency by designers.
Other factors which needed to be addressed were noise, increasing the power output per engine cylinder without compromising reliability (maybe more emphasis on planned maintenance) and keeping down cost, size and weight – something which would apply additionally to spare parts, which could be air-freighted in future.
Container ship propulsion occupied its usual space in the main body of the magazine. First was news of two new vessels for Sea-Land, first in a series of eight. These were designed to travel at 33 knots, for which a twin-screw plant of 120,000 bhp was needed. One forward-thinking aspect of their construction was that the stern half and fore part were built separately – in different yards - and subsequently joined. However, as container capacity was a mere 1096 TEU, the economic aspect of such vessels was somewhat doubtful. But if more business could be attracted by the higher speeds and increased number of voyages, the high initial cost, as well as fuel and insurance bills, could well be offset.
Another article described the experience of the first operating year , of four container ships powered by aero-derivative gas turbines. The twin-screw Euroliner class ships ran between the US and Europe for Seatrain Lines. The 30,200 bhp Pratt &

Whitney gas turbines had the advantage, compared with diesel propulsion, of lower capital cost, smaller size, permitting a extra 120 TEU capacity, and simpler maintenance, with a complete engine swap being possible in a relatively short time. The engines themselves had performed well and mostly reliably, but the gas generators had suffered from ingress of salt and foreign objects. Most of the engine problems were down to design and build issues resulting from converting aircraft engines to a marine environment, and could be solved through experience. The effects of these problems were more than offset by the ease of changing the engines. The conclusion was one of success, as long as the salt corrosion issues could be solved.
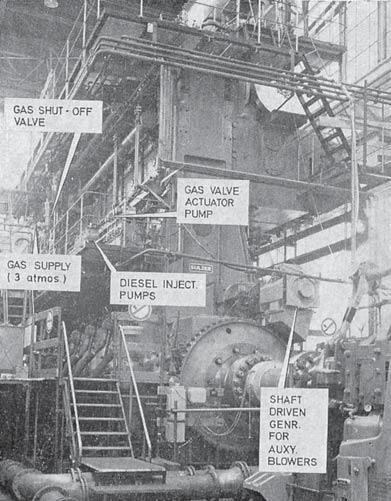
Dual fuel engines are seen as a relatively modern development, but a 14,000 bhp engine for a Norwegian LNG carrier had been successfully developed and tested by Sulzer on both normal fuel oils and LNG, in the form of cargo boil-off gases. Although not strictly dual fuel in the modern sense, the 7RNMD90 engine could operate with as little as 5% liquid fuel, the remainder provided through boil-off
Production
David Blake, Paul Dunnington production@mercatormedia.com
SALES & MARKETING
t +44 1329 825335 f +44 1329 550192
Brand manager: Sue Stevens sstevens@mercatormedia.com

Marketing marketing@mercatormedia.com
EXECUTIVE
Chief Executive: Andrew Webster awebster@mercatormedia.com
TMS magazine is published monthly by Mercator Media Limited Spinnaker House, Waterside Gardens, Fareham, Hampshire PO16 8SD, UK
t +44 1329 825335 f +44 1329 550192
info@mercatormedia.com www.mercatormedia.com
Subscriptions
Subscriptions@motorship.com or subscribe online at www.motorship.com Also, sign up to the weekly TMS E-Newsletter
1 year’s magazine subscription Digital Edition: £GBP177.00
© Mercator Media Limited 2022. ISSN 2633-4488
a
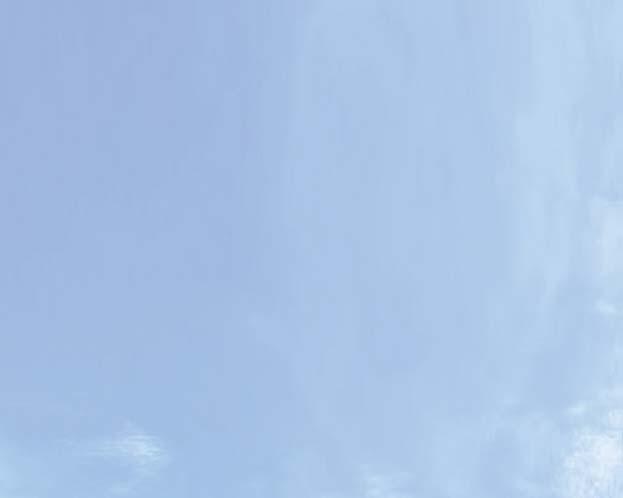
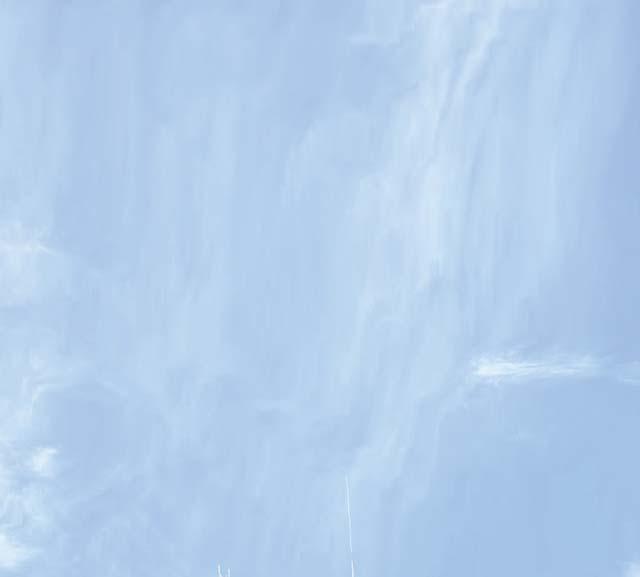
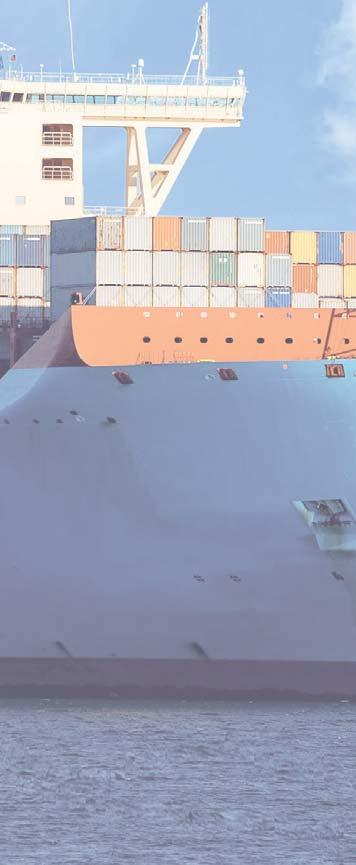
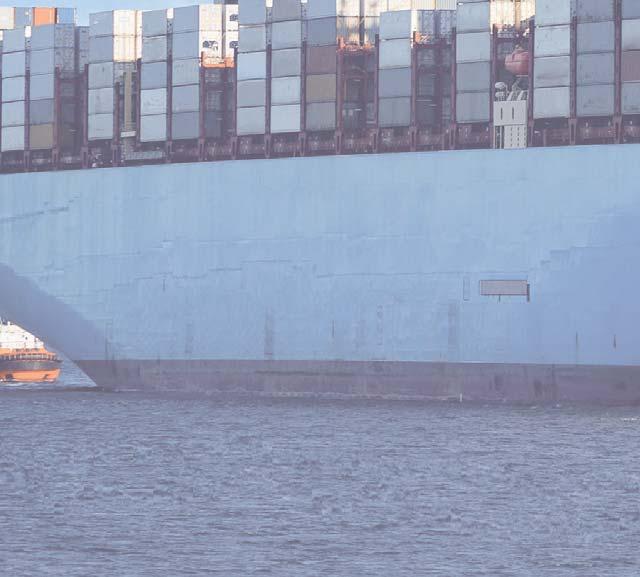
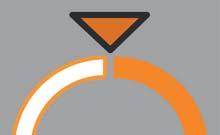
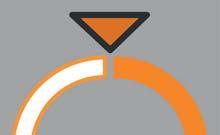

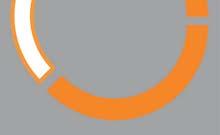
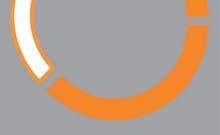
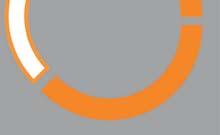