
22 minute read
Debut RCCI for Cat 3512
FIRST COMMERCIAL RCCI INSTALLATION GOES LIVE
The subject of many test-bench projects has broken out of the lab, writes Stevie Knight
Deen Shipping’s MTS Argonon is a fairly ordinary-looking 6,100dwt bunker tanker. But beneath its placid exterior, beats a long-awaited world fi rst: a commercial, reactively controlled compression ignition (RCCI) engine.
So, what could have prompted a pragmatic carrier to risk a perfectly serviceable, Caterpillar 3512 engine in order to explore something so exotic?
In fact, there are a couple of very good reasons: one is fuel flexibility, another is emission regulation. And then there’s also efficiency.
In a standard engine quite a lot of energy goes missing during the power stroke, whether that’s spark or diesel ignition. It’s a fairly simple mechanical issue centring on crank angle: at what point in the cycle the combustion delivers its main thrust.
Ideally “what you want is all the fuel burnt at once, at around top-dead-centre (TDC), then you have the highest efficiency; no ignition before that point, and no delay”, says Paul Nooijen of ArenaRed, the innovation company behind the RCCI solution.
However, SI engines can spark as much as 40 degrees before TDC, and most of the fuel is actually burned some way after, 10% lagging till plus-90 degrees. “You lose twice: not just all the pressure build-up before TDC, but also the fuel that comes late into the combustion,” says Nooijen. “Diesel is more efficient, ignition tends to start at its earliest 20 degrees before TDC, and by 70 degrees after TDC it’s usually burned 90% of the fuel in the chamber.”
But both could do better, with a little help.
Therefore, ArenaRed’s RCCI retrofit completes the whole process, from ignition to combustion, in a short, 23 degree
Image: Deen Shipping
crank arc. So, what does this fairly small bit of kit actually do that enables an engine to radically alter its behaviour?
“The RCCI works by taking a low reactivity fuel, whether that’s hydrogen, gasoline, methanol, ethanol or propane, and bringing it into the combustion chamber via a very simple port fuel injector,” he explains: this happens across the entire intake stroke, giving it plenty of time to mix with the incoming air. In the case of the Argonon, “the main fuel is LNG” he says.
Then 1% diesel is added via a special injection head, but not as a trigger for the classic, dual-fuel pilot ignition. “Instead, you bring in this small amount of diesel at around 100 degrees before TDC, this gives it enough time to move completely into its gas phase,” says Nooijen. “This is important, because if you work on a diesel principle, you inject the fuel at a very high pressure to optimise atomisation... but you are still talking about droplets, which form NOx on the outside and soot on the inside during combustion.”
It is only when the piston rises to just before TDC that this now homogenous charge ignites, and it does so fairly promptly. According to Nooijen, “You have ignition three degrees before TDC, and its combusted 90% of the fuel by 20 degrees after TDC.”
Interestingly, the lack of an advancing flame front reduces thermal stresses, lowers heat loss from the exhaust, and the very complete burn also mitigates methane slip. Together, hitting the right point on the crank angle, avoiding NOx generating hotspots and cold areas of unburned hydrocarbons means an RCCI retrofit can deliver up to around a third more power, at the same time as gaining another 10% in sheer efficiency. And it doesn’t need expensive after-treatment either, ditching the SCR.
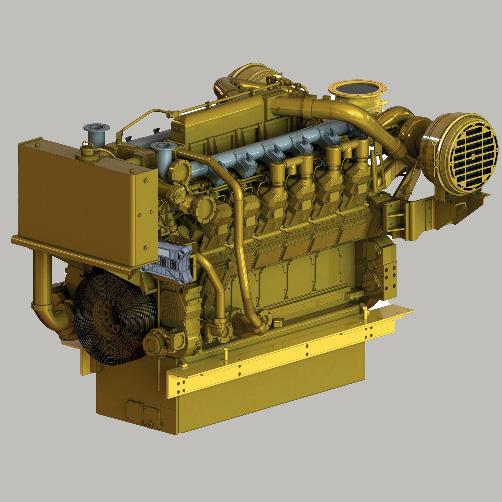
8 The MTS
Argonon has been successfully adapted to run in RCCI mode, allowing the tanker future fuel fl exibility as well as cleaner, more effi cient operation. Inset: The neat ArenaRed RCCI retrofi t is fairly small but eff ective for its size
In fact, it gets very close to the holy grail of the engine manufacturing industry: complete, clean homogenous combustion. However, if ignition isn’t triggered by spark or valve timing, how is control actually achieved?
At the centre of the magic is ArenaRed’s diesel injection head. This combines three elements; injector, tip cooler (stopping the nozzle itself from becoming a hot spot) and most importantly, a combustion pressure sensor plus a very clever bit of software. Nooijen explains this marries pressure data with volume information to tell the system how much diesel to inject, adapting the charge on the fly and keeping parameters such as pressure rise rate per cylinder and per stroke “within tolerance specifications”.
Moreover, it can iron out otherwise problematic fuel variations: after all, it only takes a couple of percent more moisture than expected, a slightly raised compression ratio or a two-degree advance in ignition timing, and an engine would usually wander into either soot or NOx formation badlands.
So, how does it work out in practice? “We’ve seen that if the ignition starts to come in too early, say from three to five degrees BTDC, the diesel portion drops down from 1% to 0.98% lowering the overall reactivity of the fuel... and as a result the combustion walks back two-degrees to the right point over the next few cycles,” says Nooijen.
Obviously, the RCCI’s responsiveness to changing conditions means a fairly sophisticated software operation; he adds that “around 1GB of information is processed every hour” by the CPBC.
However, there’s another advantage that should wow ship owners: the system, by its nature, has incredible fuel flexibility as any variations in combustion characteristics are handled in a direct fashion by what’s actually happening in the chamber. “You don’t even need to empty your tank, the combustion will adapt to the mix inside something like two seconds,” he explains, adding “that works even if you’re running methanol”, typically one of the hardest fuels to utilise in a standard engine.
While MTS Argonon is running LNG as that suits its current route, Nooijen favours cost-effective propane for first movers. However, he believes that biofuels, especially alcohols like ethanol, “are the future”, and of course, the RCCI doesn’t need any hardware changes in order to adapt.
While the RCCI retrofit will mean many engines can squeeze out a bit more than the rated power, there are some considerations for load points given the different characteristics of these alternative fuels. For example, “propane will ignite earlier than LNG, so rather than getting an output of, say, 100kW maximum per cylinder, it will be limited to 60kW” he explains. There is a contingency operation: above this, the engine will revert to more standard dual fuel operation.
Intriguingly, “whether it’s a two stroke, or a new automotive with variable turbos, common rail actuators and so on, the RCCI retrofit stays basically the same” says Nooijen: a port intake, the CPBC controller and injection head. Given such a minimal intervention, it seems likely that other owners will be very interested in applying the technology.
The last word should go to Gerard Deen of Deen Shipping, who is rather reassuringly offhand about his world first: “No problems,” he says, “everything is working fine.”

Copenhagen-headquartered freight and passenger ferry operator DFDS is evaluating a system that injects methanol and hydrogen as a solution for its conventional four-stroke engines.
The FS+ system, developed by Germanybased technology developer FuelSave, injects hydrogen, oxygen and methanol mix at three precisely calibrated different locations along the air intake of a four-stroke engine.
The solution uses an onboard hydrogen synthgas generator to produce hydrogen as needed, eliminating hydrogen bunkering requirements. The Motorship featured an interview with FuelSave in May.
“We have seen the results of a trial installation, and they are very promising,” Jacob Pedersen, Head of Projects & Implementation in DFDS’ Technical
GREENPORT
BALANCING ENVIRONMENTAL CHALLENGES WITH ECONOMIC DEMANDS
SUBSCRIBE NOW to receive a trial copy of GreenPort • Instant access to industry news • Expert opinion • Quarterly features • Weekly eNewsletter
TO SIGN UP FOR YOUR FREE TRIAL COPY visit greenport.com email subscriptions@greenport.com or call +44 1329 825 335 Organization told The Motorship.
One of the key advantages of the FuelSave solution is that it offers significant fuel efficiencies for DFDS’s existing vessels.
“It could reduce our consumption of black fuel by 15%, with only a 3-4% increase in methanol consumption,” Pedersen said, adding that the limited space requirements of the FS+ equipment was a particular advantage for DFDS’s existing vessels.
DFDS is waiting for additional data on the
DFDS EYES FS+ METHANOL INJECTION SOLUTION FOR FOUR-STROKES
performance of the system with different engine designs from various four-stroke engine manufacturers.
“We haven’t put any FuelSave equipment on our ships yet but, so long as the data is acceptable, I would expect us to begin a pilot project in Q3 2021,” Pedersen said.
The solution was far from being the only technology on Pedersen’s agenda. “We had 50 projects on our long list, and 29 projects have made the cut: we love to cooperate with
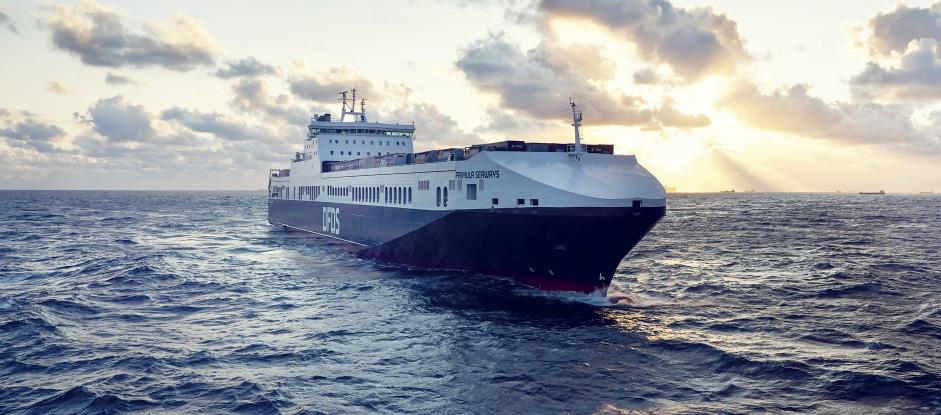
8 DFDS is evaluating FuelSave’s FS+ system that
injects methanol and hydrogen as a solution for its conventional four-stroke engines
companies developing promising technology.”
The innovative solution is only one part of the company’s ambitious plans to lower environmental emissions. The company is also planning to achieve fuel efficiencies through the introduction of route optimisation software on board vessels, supplanting the company’s

existing fuel consumption reports. GreenPort magazine provides key insights into environmental best practice and corporate responsibility centred around the marine ports and terminals industry.
Informing over

port and terminal
professionals around the world
greenport.com
CLIMBING THE VLSFO LEARNING CURVE HAS TAKEN TIME
BIMCO’s recent survey of early VLSFO experience amongst shoreside technical staff testify that the transition to low-sulphur fuel oil has not been without problems
Conducted in partnership with INTERTANKO, INTERCARGO and the International Chamber of Shipping, and based on 192 responses, the survey indicates that over 60% have experienced increased sludge deposits, over 30% have experienced wax in fuel oil tanks or fi lters, and over 30% have experienced increased wear on cylinder linings, piston rings or other components probably as a result of increased amounts of cat fi nes.
Around 20% have de-bunkered fuel as a result of fuel oil properties. Around 20% have had problems with fuel injection or poor combustion. Around 20% have experienced fuel oil pump seizures, and 10% have experienced loss of propulsion or black outs.
These percentages cannot be considered to represent the frequency of problems in the world fleet but do give an indication of the challenges and the extra effort required to manage the new fuels. In the words of the respondents: 5 Vessel faced increase in sludge generation to an extent that need to clean filters and purifier every day. 5 Increase wear and tear at piston ring, need to renew piston rings more frequently. 5 1,200 man-hours spent by vessel crews on handling problematic fuels. The additional onboard workload affected the vessels normal maintenance time schedule. 5 Additional workload in sampling, testing, re-testing, arguing test results and in collecting evidence and documenting the complete process.
The situation is being monitored across the industry. Data from Lloyd’s Register’s Fuel Oil Bunker Analysis & Advisory
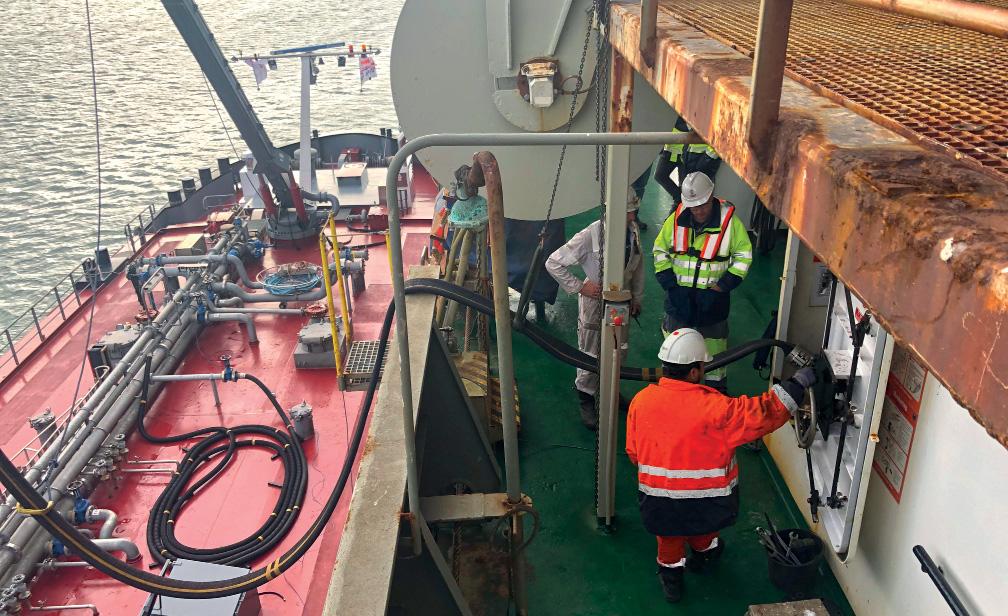
Credit: BunkerTrace
Service (FOBAS) indicates that just over 5% of VLSFOs tested between January-July 2020 were off-spec. About half of the cases were due to high sediment levels, a problem that was approximately 8% in pre-2020 fuels. Around 30% of the cases related to higher than maximum allowed sulphur content. This was approximately 5% in pre-2020 fuels.
Mark Smith, Loss Prevention Executive at North P&I Club, highlights cases where VLSFO met ISO 8217 specification limits for Total Sediment Potential (TSP) at the time of bunkering but then became unstable within weeks. “The shelf life of some fuels has decreased significantly, which couldn’t come at a worse time when some operators are placing their vessels into lay-up because of the economic impact of the COVID-19 pandemic.”
Data from ExxonMobil’s Mobil Serv℠ Cylinder Condition Monitoring service, indicates, based on over 650,000 samples, that only 11% of vessels are now operating at the correct feed rate, down from 50% last year. This is likely to be the result of vessel operators having to develop experience with the new low sulphur fuels and lubricants, says the company.
The data also shows that 51% of vessels have cat fines above OEM limits, a 19% increase on 2019. ExxonMobil says that this indicates that onboard preventative measures are insufficient, as the global average cat fine content of 2020 delivered samples is similar to that of 2019. To reduce this risk, ExxonMobil’s guidance is to always bunker fuel that meets ISO 8217:2017 specifications, and if damaging levels of cat fines are detected, run both purifiers in parallel with minimum throughput.
8 BunkerTrace
conducted a trial of its innovative blockchain and synthetic DNA technology in a trial with Cooperative Bebeka in 2019
In contrast, Christos Koliaridis, Business Developer at Vecom Marine Chemicals in the Netherlands, explains what he believes the problem with cat fines continues to be. “In our observation of the market, due to the pandemic, the issues with VLSFO have not actually been improved upon. Perhaps also as an outcome of the recent oil crisis. As the demand for oil has fluctuated unexpectedly, we believe oil producers were primarily predisposed on that front, and improvements upon these blends will be slow and few. The biggest indicator of that is the cat fines which continue to be very much present in VLSFOs. This is evidence of not-up-to standard production process.”
There appears to have been few real surprises in the problems encountered. BIMCO says the survey result show that the issues addressed prior to 1 January 1 in ISO/PAS 23263:2019 Petroleum products — Fuels (class F) — Considerations for fuel suppliers and users regarding marine fuel quality in view of the implementation of maximum 0,50 % sulfur in 2020 and the Joint Industry Guidance on the supply and use of 0.50% sulphur marine fuel, such as instability, impaired cold flow properties and high levels of cat fines have turned out to be the problems also faced by the industry in reality after 1 January.
Christian Bækmark Schiolborg, BIMCO’s Manager, Marine Environment, says: “The survey results confirm what BIMCO had expected, that there would be quality and safety issues as a consequence of the new VLSFO fuel types. However, none of the problems identified in the survey results are new problems to the industry.”
He says there is a lot of uncertainty and little transparency when it comes to fuel quality and any potential impaired properties of fuel oil available in various bunker ports. “An initiative that could create some transparency and harmonisation would be to amend ISO standard 8217 so that the applicable limits were changed from max or minimum limits to acceptable value ranges for the different characteristics, e.g. viscosity and pour point.”
In September last year, it was confirmed that existing ISO 8217 specifications would still apply, and the Publicly Available Specification (PAS 23263) from ISO did not introduce any new specifications but rather help explain how ISO 8217 would continue to apply. This year, though, a working group has begun evaluating how VLSFO can be better categorised. The work is expected to take around three years.
Schiolborg continues: “The right way forward, to protect human lives, the environment and ships, would be for countries to introduce and enforce compulsory licensing schemes for fuel oil suppliers operating within their jurisdiction to ensure transparency and a certain level of quality of fuel oil delivered to ships.”
Calls for extra diligence continue to echo around the industry: Ilkka Rytkölä, Chief Technology Officer at fuel supply system provider Auramarine, says: “The need to future-proof operations and seek expert advice in relation to all elements affecting the health of a vessel’s fuel supply systems are more important now than ever.”
New services are being developed to help with either fuel choice. In August, Veritas Petroleum Services Group announce the launch of PortStats, a new interactive dashboarding service where users can access near real-time fuel quality statistics and compare fuel quality data from any fuel supplier, from any bunkering port where VPS has performed fuel quality testing (currently over 2,600 ports).
VPS is also offering marine fuel storage monitoring to fuel suppliers and operators with vessels in layup. The COVID-19 pandemic has led to a reduced demand for all refined products including marine fuels, and longer-term storage
Credit: North P&I Club
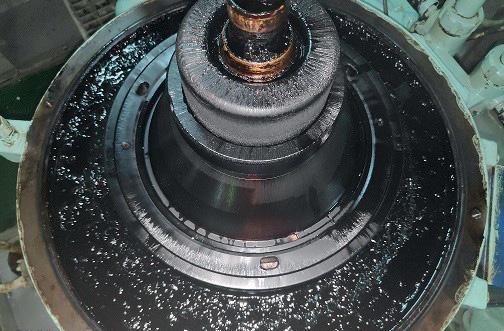

increases the risk of fuel quality issues arising from temperature, stratification, fuel stability, cat fine settling, waxing and microbial growth.
BunkerTrace offers another solution, combining blockchain with synthetic DNA technology to link together digital and physical chains of information for traceability on fuel quality. “Our solution offers full visibility into bunkering operations,” says Deanna MacDonald, Co-founder of BunkerTrace. It works by tagging the fuel with synthetic-DNA markers associated with quality metrics, flagging the fuel using a highly sensitive molecular label that allows for on the spot instant verification, and tracing the transactions and hand offs with a web and mobile application powered by the company’s blockchain-based Bunker Delivery Note.
“Taken together this creates end-to-end oversight and control of the marine fuel supply chain for owners, port operators, and bunker suppliers, while giving buyers confidence that the fuel meets the given specification,” she says. “Not only does the solution prove compliance with the sulphur cap for those purchasing traced compliant fuels, it also helps to avoid potential contamination issues associated with low sulphur fuels.”
BunkerTrace conducted a pilot trial with Cooperative Bebeka last year. “The trials we are currently undertaking with our partners and clients have successfully proven the technology in the field and showcased that this unique combination of technologies is both easy to use, and effective,” says MacDonald.
Scrubber manufacturer Kamelia Cleantech anticipates shipowners reconsidering scrubbers as a solution. The company says current experience with the use of VLSFO is mostly limited to the past six pandemic-ridden months, where there have been unusually low levels of marine traffic. The industry is still on a learning curve when it comes to best practices for VLSFO, with engineers attempting to quickly adapt to the new regime; but now is not the time for complacency, says the company. Shipowners and operators have the option of a future proof, long-term savings strategy, - that is continuing to use reliable HFO by choosing to install scrubbers.
Despite the issues, positive stories of the industry’s y adaptability to the new fuels are also being told: Ashish Nair, are also being told: Ashish Nair, Operations Manager at marine fuel services ne fuel services provider KPI OceanConnect, says that while says that while the information available on specifications specifications and blends of VLSFO varies widely from s widely from port to port, most of the company’s e company’s customers and supply partners have rtners have managed the transition well.
BIMCO’s Schiolborg agrees. “The grees. “The implementation of the sulphur cap has overall cap has overall been a success. The entire industry did ndustry did everything possible to be ready and to dy and to ensure it became a success.”
8 Some fuels had high sediment levels
8 Christian Bækmark
Schiolborg, Manager, Marine Environment at BIMCO
TRANSPARENCY AT HEART OF WINGD CYLINDER OIL GUIDANCE
Winterthur-based engine designer WinGD has published a new format of their list of validated cylinder oils which now shows oil specifi c usage guidelines for each product
Introduced in July 2020, this move has led to improved transparency for customers, clarifying oil usage recommendations and ending previous uncertainty about product specifi c limitations, Frank Venter, WinGD Project Engineer Tribology Fuels & Lubricants discussed in an interview with The Motorship in September.
The revision has improved the transparency around specific oil usage restrictions as stipulated in No Objection Letters for cylinder oils. “Previously, we were at times unable to fully answer customers’ queries around specific oil usage restrictions, due to the confidential nature of NOL restrictions,” Venter noted, adding that the previous steady flow of customer queries had slowed to a trickle since the publication of the guidance.
The engine designer’s decision to adopt a more transparent approach was discussed beforehand and welcomed by oil majors and smaller lubricant suppliers as well.
“We began the process of revising the list of validated lubricating oils in late 2019. It required going through every single cylinder oil, corresponding laboratory analyses, and the conditions in which that oil was validated. It was a painstaking and sometimes arduous process,” Venter noted.
AMENDMENTS TO CYLINDER OIL GUIDANCE
In addition to now openly showing oil specific limitations, the revised guidance highlighted changes in the BN15-25 ranges, and in the BN70 category, where the maximum sulphur content of fuel oil was lowered from 2.5% to 2.0%
The main consequence of amendments to usage guidance for BN15-25 cylinder oils was that these are no longer permitted for fuels with up to 0.50% S. They are only suitable for gas and liquid fuels containing <0.10% S.
“The revisions in maximum sulphur contents were based on operational experience, and in part pre-empted by the entry of IMO 2020 fuels into the market, as well as broader engine developments, which have increased the stresses on lubricating oils,” Venter commented.
The Motorship notes that an additional category, labelled as ‘DF validated’ shows whether the oil has passed a validation trial while burning gas as the predominant fuel during that trial. This does not preclude certain other oils, while validated on liquid fuels, from being used in gas mode. The newly published list clearly indicates this.
While other two-stroke engine manufacturers have also revised their lubrication oil guidance in 2020, Konrad Räss, Head Engine Technology and Development at WinGD noted that WinGD’s guidance did not differentiate between engine designs, for example older or newer ones.
“We haven’t changed our tuning strategy since I’ve been at WinGD and the previous companies (NSD, Wärtsilä). Highly efficient tunings for lowest fuel oil consumption is our standard. The appetite for BN and oil feed rate depends, among others, on the in-cylinder purity which is influenced by the tuning. Our latest design engines behaviour regarding feed rate and BN is comparable to our previous designs,” Räss said.
In fact, both Venter and Räss stressed that the revised list of validated cylinder oils did not suggest that any products were ineffective. The goal of the revision was to include previously undisclosed information, held in the NOL, to the customer.
“We are simply offering guidance, but if our customers
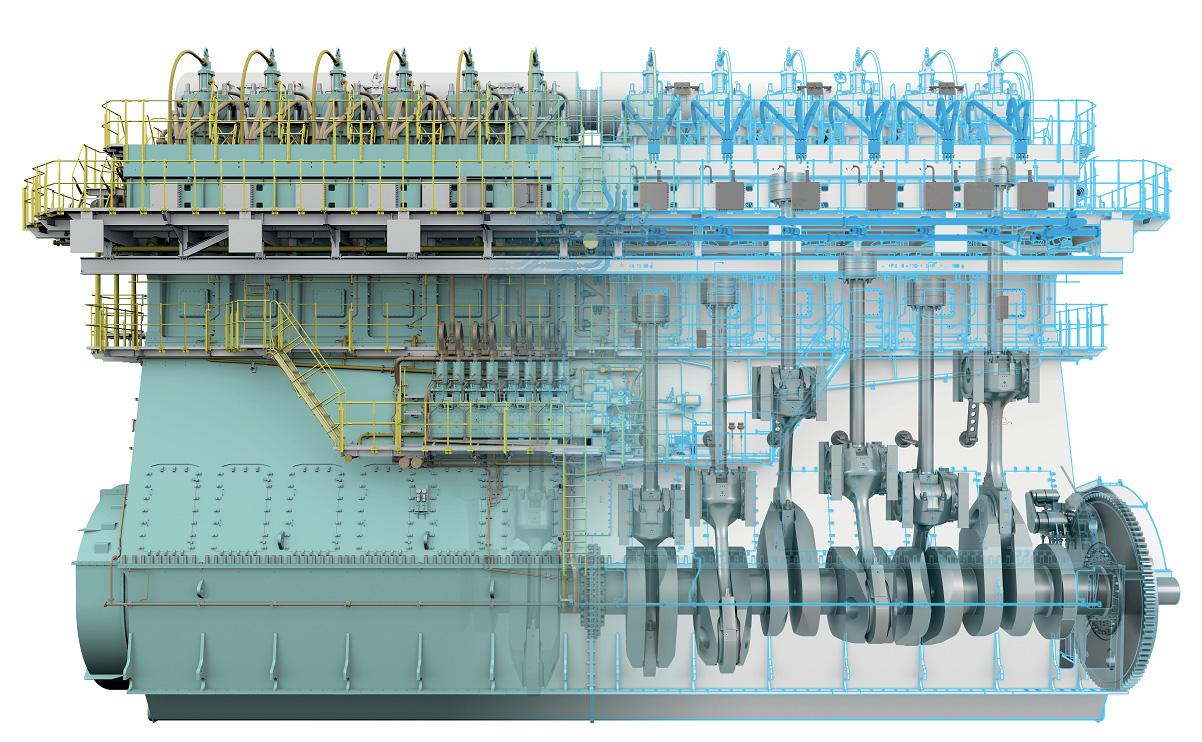
8 WinGD is
developing systems to combine real time engine performance data with real time fuel and cylinder oil data, WinGD’s Konrad Rass noted
have a product that they have been using with a certain fuel with good results, there is no problem with continuing to use it,” Räss said.
However, he noted that by closely looking at the usage recommendations of lube oil products, technical managers or ship superintendents might be able to safely lower feed rates. The Motorship notes that separating the procurement of consumables from operational considerations meant operators risked missing out on efficiency savings.
Venter concurred. “You could feed [some cylinder oils] in at feed rates of 0.60g/kWh, as opposed to pouring it in at 1.0-1.1 g/kWh, with better performance.”
Räss noted that WinGD continued to support piston underside analysis as a tool to gain insight into the performance of cylinder oils.
“We still stick to the piston underside analysis,” Räss noted, adding that this provides data on wear particles and on the usage of the BN. “This still provides the best support for our customers who want to reduce feed rates,” Räss added.
Declining sulphur levels have improved the ability of piston underside analysis to analyse lube oil performance. “The lower the sulphur in the fuel, the easier it will become in the future,” Räss added.
However, looking further ahead, WinGD is developing systems to combined real time engine performance data with real time fuel and cylinder oil data.
“The dream would be to develop a system where the customer never has to adjust the feed rate. The feed rate would be adjusted automatically by an algorithm drawing on the vessels’ previous operational data,” Räss said.
While WinGD has introduced real-time digitalisation solutions, such as its WiDE system – digital onboard monitoring system – which feeds into a database that provides real time data, incorporating cylinder oil data into this poses some challenges.
“One of the challenges is developing sensors to track different parameters of lube oil during operation. It is one thing to install a digital temperature gauge that can send data to an engine management system, but it is another to assess retrospectively the real time multiple interacting parameters of the fuel, engine performance and feed rates, and integrating this with scrape-down oil analysis,” Venter noted.
However, WinGD is continuing to work with “certain oil majors” to develop real time measurement data of cylinder oil in- or post-use to complement engine running data. “Watch this space – it is quite exciting,” Venter concluded.
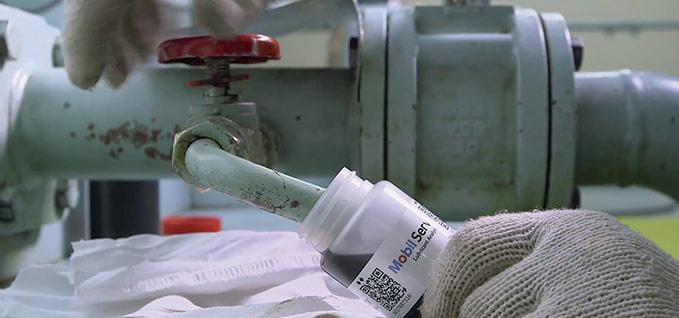
Credit: ExxonMobil
8 WinGD is
continuing to work with “certain oil majors” to develop real time measurement data of cylinder oil in- or post-use to complement engine running data
Saving fuel means saving the environment
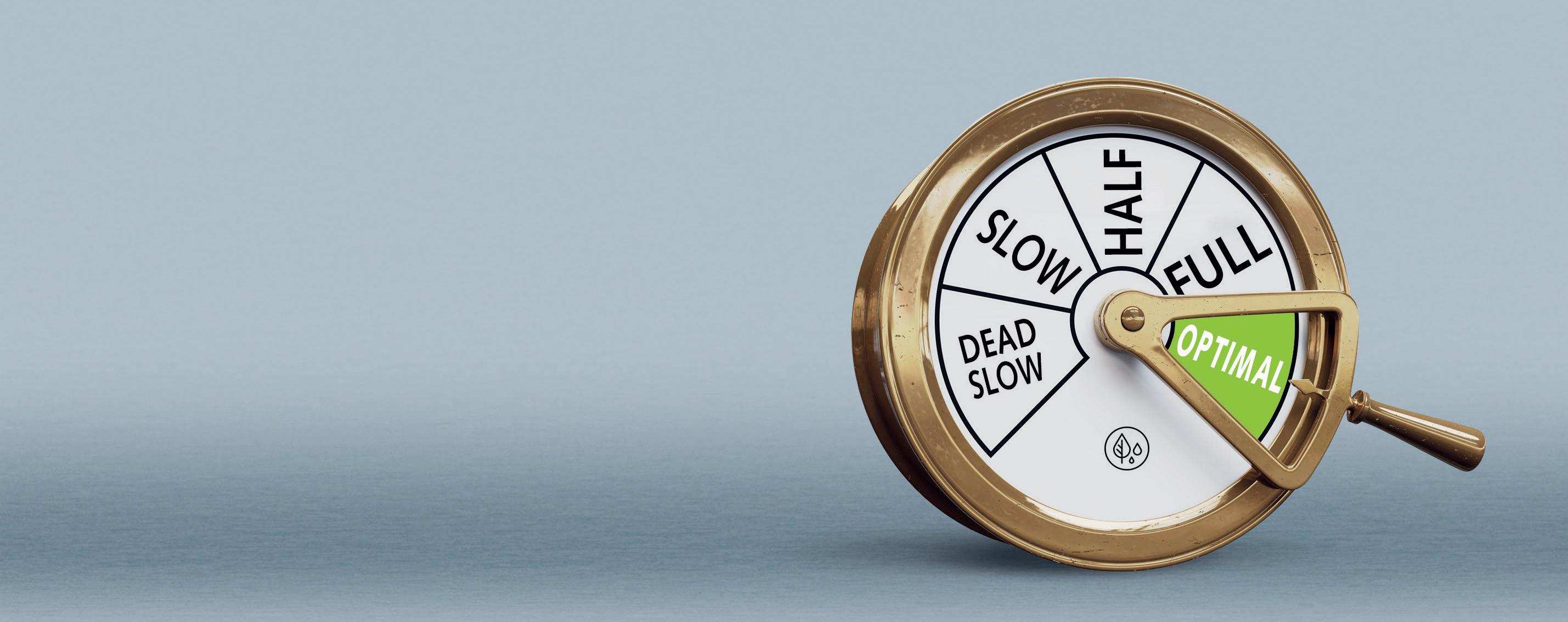
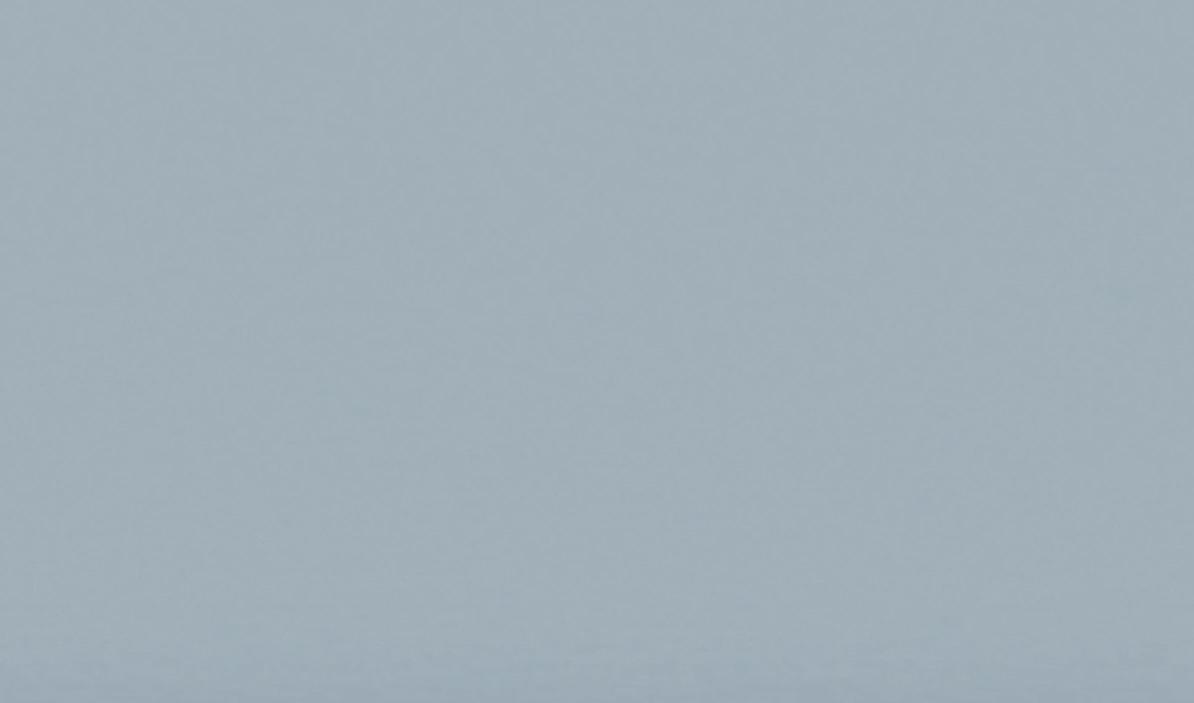
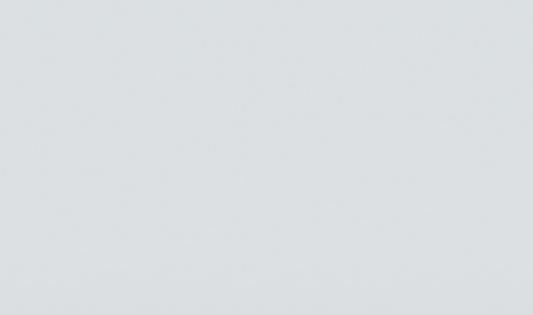
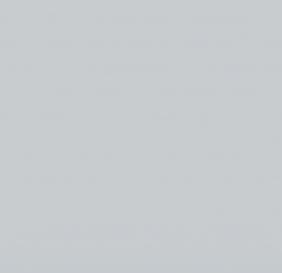

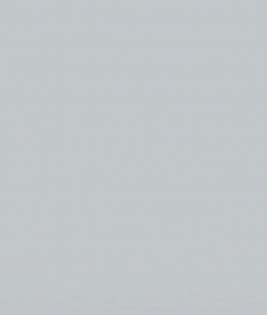
With solutions from Kistler, considerable fuel savings can be achieved – this reduces the environmental impact and increases efficiency. Wherever and whenever you need technical support, we are at your disposal with our complete, tailor-made solutions and our comprehensive professional service across the globe.