
29 minute read
Under pressure
The development of modern gas engines has been closely connected to the measurement and processing of cylinder pressure, which has in turn driven advances in sensor technology
At fi rst, cylinder pressure sensors were used within gas engines management to identify peak pressure and for the detection of knocking and misfi ring. The primary goal was to balance the diff erent cylinders and thus to ensure the smooth operation of the engine.
During the last 5-10 years the development of gas engines has reached operating ranges where it has become critical to have real-time insight into the combustion process of every cylinder. Moreover, the trend to higher indicated mean effective pressure (IMEP) for gas engines in the broad range of 100... 1800 rpm comes along with additional challenges to the cylinder pressure sensors. Beside the IMEP, also the Heat Release Rate (HRR), Mass Fraction Burned (MFB) as well as other specific thermodynamic values gain more and more importance for gas engine control, even for serial applications.
Meanwhile, engine manufacturers requirements regarding the robustness of cylinder pressure sensors are also becoming increasingly challenging. Some examples here are (regular) peak pressures of up to 300 bar, high vibration load, shocks up to 1000g and maximum speed of pressure change of up to 1.000 bar/ms.
IMES as a leading manufacturer of cylinder pressure sensors has developed its new cylinder pressure sensor generation type HTT-06CA and CPS-1CA incl. IP69 protection class to satisfy engine manufacturer requirements for application on new high efficiency gas engines. The new sensors are extremely robust and fulfil the demand of high accuracy with low dynamic- and static zero drift. The sensor membrane can withstand static pressure up to 800 bar and has a natural frequency range of 80 - 100 kHz.
At the heart of the sensor is a high temperature strain gauge thin film measuring element based on TION (Titanium oxynitride) which is designed for very good temperature stability. The measuring elements of the new cylinder pressure sensor generation are located in the front of the sensor thread (M10x1 and M14x1.25). A new connection method was developed to withstand temperatures up to 400 °C as well as high shock levels, which has been successfully tested on laboratory equipment and on test engines.
For application on pressure controlled high efficiency gas engines it is necessary to have a good long-life stability and a good accuracy of sensor for thermodynamic calculations. At the Paul-Scherrer-Institut in Switzerland (LCC) comparisons between IMES FPS-03CA sensors and high accuracy piezoelectric type sensors were carried out in June 2020 on a Wärtsilä 6L20DF engine. The thermodynamic comparison @ 18 bar IMEP showed to the reference sensor deviation of 0.4 bar in Pmax and 0.5bar IMEP.
One of the outstanding capabilities of the IMES new sensor is its long-term stability with constant measuring characteristics. The sensor is able to run for 20,000 hours in gas, diesel and
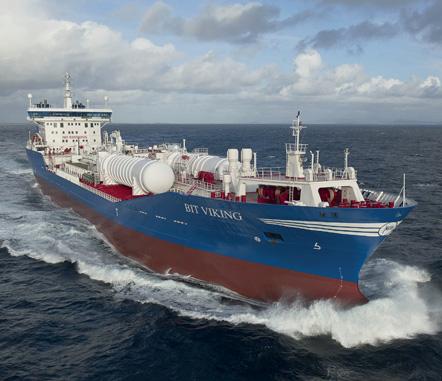
dual fuel 4-Stroke engines with a power range equal to or bigger than 100 kW/cylinder. The life-time of the pressure sensor depends typically on the service interval, which is 16,000 to 20,000 running hours which corresponds to an operational life of 2-5 years. Together with IMES “Check-box” solution, the operator can check with a static pressure device actual span- and offset condition of installed cylinder pressure sensors via serial interface of sensor electronic.
The long-time operation tests were conducted aboard Bit Viking on two Wärtsilä 6L50DF engines. During the longterm operation the sensors were taken off from the engine after 6,000 hours and sent back to IMES to check the original calibration data. The span and offset of each sensor were measured over the full temperature range. The experienced drifts in span and offset were minor, which is very important for the use on control loops on engines.
The cylinder pressure sensor manufacturer noted that both HTT-06CA and CPS-03CA are waiting to receive type approvals.
IMES noted that solutions can be developed for the different challenges facing the industry, including the impact of alternative fuels, evolving engine designs as well as the miniaturization of the sensors for low cylinder power of only 50 kW/cylinder. The company identified the need to achieve competitive costs for serial applications in gas engines as another challenge.
8 Long-time
operation tests have been conducted on two Wärtsilä 6L50DF engines aboard the Bit Viking. Inset: Cylinder pressure sensor HTT-06CA
STEP CHANGES IN TURBO TECHNOLOGY OVER TIME
Christoph Rofka, Senior Vice President - Head of Global Product Group Medium, Low Speed and Rail, ABB Turbocharging discusses previous step changes in turbocharging technology
QFrom an engine design and operation perspective, what do you think have been the most important
technological innovations during your career?
AI’m a mechanical engineer by training, with a specialisation in turbomachinery, so one example from my own experience would be the improvement in the reliability of equipment for 4-stroke medium-speed engines operating on heavy fuel oil (HFO) starting in the late 90s. It’s funny to think about it with the challenges of zero-carbon and new fuel types that we’re facing now, but that work took us a decade.
From a wider turbocharging perspective, you could point at the IMO Tier II legislation, which led to a quantum leap in turbocharger performance. We had previously become used to incremental improvements in pressure ratios, and suddenly the legislation created an incentive for engine designers to utilise extremely high-pressure ratios, without loading the engine more. For a company like ours, which prides itself on its technological leadership, that was a great time. The quantum leap in pressure ratios meant we could bring to market our performance enhancements.
And after that we had the introduction of two-stage turbocharging, which has also led to a step change in performance. The technology is slowly becoming established in medium speed commercial engines: the genie is out of the bottle, and the technology will become increasingly widely used.
Finally, if we look away from turbocharging towards wider engine developments, the introduction of electronic controls, such as common rail, and variable valve timing have been significant.
QAs a mechanical engineer by training, how do you see the future role of the internal combustion engine? Will
it remain the main mover for marine transportation in the future?
AI expect engine technology will remain the prime mover of marine propulsion, particularly for deep-sea shipping. I have not seen any alternatives that come even close to the capabilities of today’s propulsion systems for deep-sea ships.
We might see the emergence of alternative solutions in the short-sea market like fuel cells. These might be complementary to auxiliary engines in deep-sea shipping, although they are only likely to gain a small place in the market.
There is likely to be a greater range of solutions in the short-sea market, where we are seeing some fragmentation, or in the high-speed market. But that range of solutions brings with it its own challenges - it is hard for OEMs to benefit from economies of scale with too many options.
So, we expect the prime movers of deep-sea vessels will continue to be fuelled by fuels with a low to zero carbon footprint. The transition will definitely be in the fuels. Q How do you see the increasing focus on emissions reduction
infl uencing fuel choices and product design considerations?
AIf we are serious about reducing emissions, we need to develop solutions that address emissions from the deep-sea fleet, which accounts for around 80 per cent of emissions from shipping.
From the big picture, we are in a transition phase. We do not know what the eventual future fuel or fuels will be and there are different perspectives within the industry. One interesting aspect of working at ABB is that we can see increasing demand for alternative fuel from outside the marine industry, from players looking at transportation solutions for alternative fuels.
But we have seen greater cooperation between different parts of the industry, to ensure that the industry can make its voice heard. This is important - we know at ABB that shipping’s comparatively small share of overall fuel consumption means our influence over the supply side is limited. Fuel availability will be just as important as technical solutions in a potential fuel transition.
From a product design perspective, when the topic of fuel transition was first raised, we were concerned that there would be a very wide choice of different fuels, forcing the industry to manage a wide range of fuels.
We are pleased that the choice has narrowed down to a level that the industry can handle, as we have now moved beyond discussion into development. The main engine developers are all developing solutions capable of burning alternative fuels, and we are involved in a range of development projects.
And positively we have seen much closer collaboration

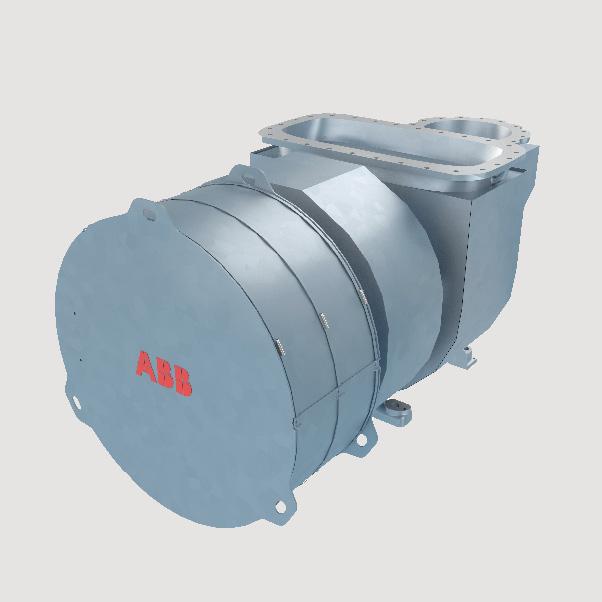
8 ABB’s Power2
800-M two-stage turbocharging Inset: ABB Turbocharging’s small- and medium-size turbocharger solutions for 3MW to 7MW output engines, such as the A255-L, have market-leading effi ciencies
between OEMs, engine designers, and other system suppliers in order to develop solutions.
QYou have spoken previously about the challenges of prioritising the development of solutions for
diff erent fuel types. How is ABB Turbocharging prioritising the development of solutions for the varying demands of ammonia, methanol and other fuels?
AAt ABB, we are concentrating on the development of solutions for a smaller number of fuels. You’ll be surprised to learn we are not investing in technology to deal with heavy fuels any longer. [Laughs]
We are closely working with OEMS to understand the impact of different fuels on combustion, to see where turbochargers can help support combustion and emissions. We know ammonia and hydrogen have different combustion characteristics. Ammonia combustion is relatively slow and challenging to maintain while combustion of hydrogen is fast and prone to knocking and glow ignition. This is likely requiring differentiated turbocharging solutions starting with quite different air-to-fuel ratios. However, this is not far enough advanced to lead to specific product development.
In parallel with this research, we are focusing on developing the performance of core turbine and compressor technologies, looking at higher efficiency and higher specific capacity.
This is leading us to focus on component level advances, so that we have a suite of components that can be introduced when the specific requirements of a turbocharger for an ammonia or hydrogen-fuelled engine are defined. The development of a suite of components around a core is also a cost-effective approach to managing development amid uncertainty - the largest proportion of the costs of product development occur during the final stages of a commercial launch.
But when it comes to commercial developments, we still have to avoid proliferation within our product range. I don’t see much scope for taking competing products to market, the range where fuel efficiency is not a decisive factor, the
such as two turbocharger families within the same output range for different fuel types.
Apart from the fuels, we have introduced a new way of developing products to shorten the lead time to develop technology demonstrators and test engine installations before bringing new solutions to market.
This should shorten the development cycle to under two and a half years, compared with the previous typical five-year development cycle.
QAway from alternative fuels, how do you see the rise in interest in battery hybridisation solutions infl uencing
ABB Turbocharging solutions?
AThere are likely to be a range of different hybrid solutions. From a product perspective, we expect base engines to operate with a relatively high-power density. But the way I see it, the effect will be more of a simplification.
The greater risk is that the market fragments, both in terms of products and also variants, which would lower the potential volumes for new products, and ultimately impact the economic case. So you have to find a way to launch your product in a modular way to obtain some scale effect.
QTurning to the two-stroke market, how is ABB’s focus on improving fuel effi ciency and lowering emissions in
its single-stage solutions progressing?
AWe have been continuing with the development of sequential turbocharging. We concluded the first official engine test of the Flexible integrated Turbocharging System to commission the first installation of the solution aboard a vessel in Q1 2021. We have established that the system offers fuel efficiency savings of up to 6 grams per kWh (3 - 5 percent). Both the major two-stroke engine designers have approved the system.
Looking further ahead, we are continuing to develop new single-stage solutions for 4-stroke diesel & gas engines. As part of our development project, we are targeting a higher maximum pressure ratio of 6.5 for single stage solutions from today’s 5.8, combined with efficiencies of over 70 percent for up to 5 MW output small- and medium-size turbochargers.
The prototyping process is far advanced, and we are planning to demonstrate its capabilities to the engine OEMs. This may lead to us beginning product development. This would represent the single largest step change in turbocharger performance for decades.


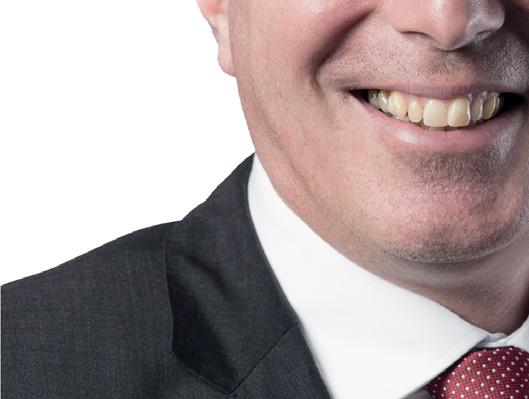

QFinally, how is ABB planning to develop its two-stage solution for the four-stroke market? A While our two-stage solution offers significant advantages in terms of engine power density and fuel efficiency, the higher CAPEX and greater complexity of the solution has slowed uptake. We are undertaking development to make the two-stage turbocharging product more compact, lighter and modular.
With the exception of some 4-strokes at the lower end of for Two-Stroke Engines (FiTS2) a few weeks ago and expect
development of a simplified design, which will improve its on-engine accommodation, will improve its applicability, on-engine accommodation, will improve its applicability, particularly among upper range engines. particularly among upper range engines.
Credit: ABB Turbocharging 8 ABB Turbocharging
is conducting research with OEMs to understand the impact of diff erent fuels on combustion, to see where turbochargers can help support combustion and emissions
8 Christoph
Rofka, Senior Vice President - Head of Global Product Group Medium, Low Speed and Rail, ABB Turbocharging discusses discussed past and present step changes in turbocharging technology
NOT JUST BATTERIES: MODELS KEY TO ROPAX SAVINGS
Giulio Tirelli, Director Business Development at Marine Power, Wärtsilä, discusses the current outlook for battery hybridisation in the Ro-Ro and Ro-Pax vessel segments
While battery hybrid installations off er the potential of double-digit fuel effi ciency savings for newbuildings, the potential savings for retrofi ts was even greater in some cases, Giulio Tirelli, Director Business Development at Marine Power, Wärtsilä told The Motorship.
BROADER TRENDS IN RO-PAX
Tirelli noted that interest in battery hybridisation among operators in the passenger ferry has picked up within the RoRo and Ro-Pax segment. “We have seen a radical change in appetite for new systems in the last ten years,” he said.
Tirelli suggested that shifts in the Ro-Ro and Ro-Pax segment were being pushed by regulatory changes, including IMO Tier III environmental regulations, as well as concerns about how EEDI regulations will be applied to existing tonnage.
“It will not be easy [for Ro-Pax vessels] to achieve the standards because of the way in which the formulas apply to passenger and vehicle shipping,” Tirelli noted.
Looking further ahead, shipowners are looking at solutions that ensure the continuity of their company and services, given concern about upcoming environmental regulations, as well as how to meet their demands.
Reconciling regulatory pressures with economics was more complicated in public-facing vessel segments, such as passenger ferries, than in other segments, such as tankers or bulkers. “Environmental considerations are likely to play a part in owner considerations in the Ro-Pax market, along with underlying economics,” Tirelli said.
Popular attitudes towards environmental emissions from vessels in port were becoming an increasingly relevant issue in a number of countries worldwide. “Because passenger ferries and Ro-Pax vessels often berth in or close to major population centres, and especially in Europe , emissions are coming under closer scrutiny. Particularly as some urban centres, both in US and Asia, are following the example set by the EU and are developing plans to reduce overall emissions in their urban centres.”
Finally, The Motorship notes that the expansion of shoreside power connections in some regional markets was also likely to have encourage shipowners to consider diesel-electric configurations in Ro-Pax vessel design. One of the principle benefits of the application of battery systems was the possibility of eliminating environmental emissions in port if shoreside connections supplied green electricity to the vessel.
MORE THAN COMPONENTS
However, Tirelli noted that the creation of a detailed use case was necessary to accurately assess the potential benefits of adopting battery hybridisation for any given vessel.
potential benefits of integrating energy storage systems into diesel-mechanic, diesel-electric (or even potential fullelectric) configurations for newbuildings, rather than narrowly focusing on component level advances in battery power density, life span and weight and footprint reductions.
Before embarking on a new project, Wärtsilä develops highly sophisticated models of the energy consumption of individual ships, based on integrating ship system level data with wider ship navigation data and wider route-specific data on sea state, current and weather conditions.
As few ship owners are able to supply such data at the once per second frequency upon which Wärtsilä’s analysis team prefers to work, Wärtsilä is able to offer a proprietary Wärtsilä Data Collection Unit (WDCU) that can retrieve operational data from a given vessel, retrieving everything from load ramps to the start up and shut down of equipment.
The extraction of meaningful data from these extensive data sets draws on Wärtsilä’s advanced digital capabilities. Tirelli noted that “this step was impossible before”.
One of the main focuses of Wärtsilä’s analytical tool was on the impact of fuel types on overall vessel performance. “The introduction of LNG-fuelled engines often coincides with wider changes, as LNG impacts vessel design, operation and fuel availability,” Tirelli noted.
The analytical tool also allowed shipowners to accurately gauge how investments would impact operational performance, and ultimately the bottom line. “Through our simulation tool, we are able to demonstrate whether a new energy source, such as a PV panels, or an energy consumer, such as enlarged tunnel thrusters, would make economic sense or not,” Tirelli added. This systemic approach was key to understanding the
The process of data collection and analysis did not stop once an HY system was installed. The system continued to collect data during operation. “The last vessel becomes the starting point for planning the next vessel,” Tirelli said simply.
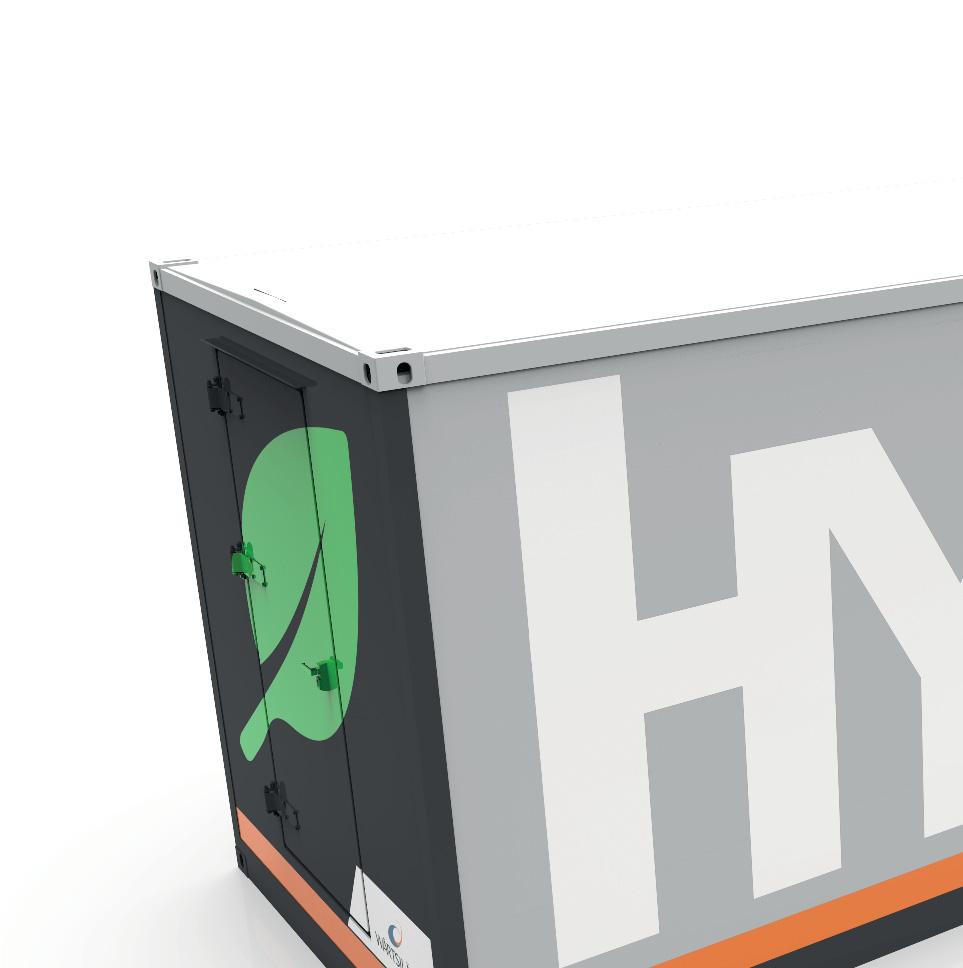

RO-RO/RO-PAX BENEFITS
Turning to the Ro-Pax and Ro-Ro sectors, Tirelli noted that while there was a difference between short-haul ferries and longer distance vessels, the difference between the two
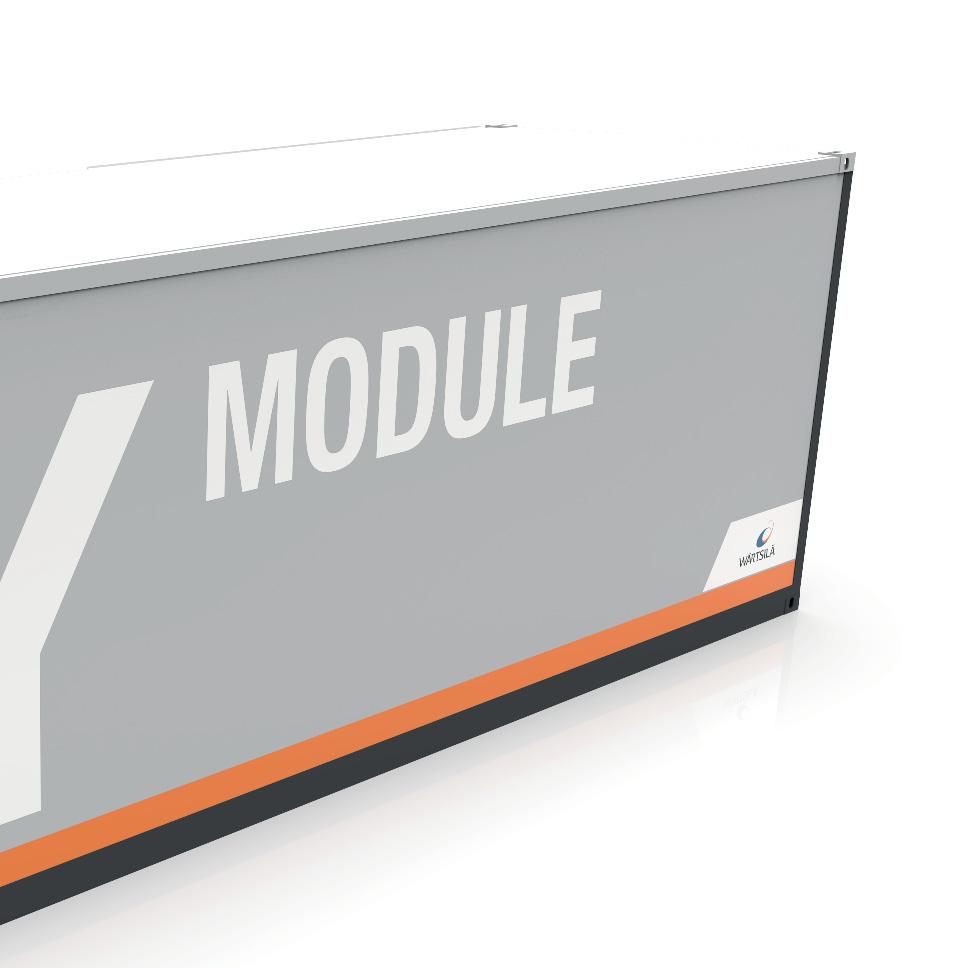
8 Wärtsilä’s
“HY Module” modularised energy storage system solution limits the amount of lost cargo capacity aboard a RoPax
types of vessel did not reflect hotel load so much as the proportion of the voyage which was spent operating at normal operating speeds, rather than slowing before port, manoeuvring or loading alongside.
“The economics of an installation is not related to the size of the vessel, but rather according to its specific operational patterns.”
However, while the operational fuel efficiencies were clear for smaller short-haul ferries, the additional CAPEX cost of installing ESS, EMS and electrical systems is proportionately greater, Tirelli admitted.
Turning to older tonnage, Tirelli noted that the collecting data from a WDCU on operational vessels offered significant efficiency savings: in fact, the potential for efficiency savings offered by hybrid solutions for older vessels greatly exceeded those offered for newbuildings.
“For retrofits, the potential is huge: while newbuildings are designed with efficiencies in mind, some older vessels were not designed with the same perspective,” Tirelli explained.
Tirelli noted that the optimisation analysis offered of the highly detailed second-by-second data collected from Wärtsilä’s WDCU was likely to be more detailed than that currently collected by older vessels’ systems, and route optimisation solutions.
A further consideration for owners of older tonnage was the potential payback period for HY solutions. Once again, Tirelli noted that the payback period varied - and that there may well be a variation between short-haul ferries and larger Ro-Pax ferries with a greater number of cabins, and a correspondingly higher hotel load.
“Speaking very generally, I would confidently predict that the payback period would be less than five years, and lower than that in some specific cases.”
One of the reasons for the confidence is that Wärtsilä is offering a modularised energy storage system solution, the “HY Module”, that importantly limits the amount of lost cargo capacity. “It occupies the same space of a TEU, and many operators are looking at installing it on the truck deck of a Ro-Pax,” Tirelli said.
The containerised solution is also an elegant solution to both classification society requirements and space limitations aboard some vessels that were not designed with separate battery rooms, Tirelli concluded. y


8 Giulio Tirelli,
Director Business Development at Marine Power, Wärtsilä



35 YEARS
Genuine & OEM quality spares from stock to keep your separators up and running
Outstanding quality parts and reliable service since 1985 20.000 items for Westfalia and Alfa Laval ex. Stock Holland / Singapore Worldwide technical support & service solutions on demand
www.ketmarine.com | info@ketmarine.com
PLEDGE TO LNG REINFORCED BY NEW RO-PAX
As it targets wholesale fleet adoption of LNG fuel, Balearia’s forthcoming addition blends a potent dual-fuel power installation with very high service speed, writes David Tinsley
Scheduled to enter service during the opening quarter of 2021, the 123m catamaran ro-pax ferry Eleanor Roosevelt will provide a showcase for LNG-fuelled, four-stroke engine propulsion in the high-speed vessel sector.
Spanish-built to an Australian design, the Eleanor Roosevelt will rank among the world’s largest twin-hulled ferries, potentially taking the crown among such vessels with a dualfuel reciprocating main engine plant.
While the Buquebus-owned, 99m wavepiercer Francisco heralded the opening of a new chapter in fast ferry powering in 2013, by employing a dual-fuel gas turbine installation, the impending entrant to the Balearia fleet signals a further important stage in the uptake of LNG by way of her multiengine, DF medium-speed machinery.She incorporates Incat Crowther catamaran technology for a top speed of 40 knots.
Based in the Mediterranean port of Denia, in Alicante province, Balearia has to date amply demonstrated its commitment to the LNG option through conversion projects involving six existing vessels, plus three DF newbuilds. Eleanor Roosevelt is the third new ship, and follows the two Visentini-type, conventional ro-pax ferries Hypatia de Alejandria and Marie Curie, commissioned last year. Hypatia de Alejandria was the first LNG-powered ferry to enter service in the Mediterranean.
Total investment in the programme for nine LNG-capable vessels to date amounts to €362m (US$422m). The strategy does not end there, however, as the company expects to have all its fleet running on LNG within the next eight years.
While Balearia has received a measure of subsidisation from the EU for the power conversion projects, the scale of its expenditure in LNG powering is scarcely matched

Credit: Balearia
anywhere worldwide. The endorsement of LNG on mainly environmental grounds not only reflects the increasing legislative pressures on the industry but also corporate goals as to social responsibility and economic profitability.
Albeit a hydrocarbon fuel, use of LNG implies a reduction of CO2 by 30%, NOx by 35%, and the elimination of sulphur and particles, having an immediate effect on air quality and greenhouse gas creation.
Commanding a contract price of around €90 million (US$90m), Eleanor Roosevelt was launched during September from the Gijon premises of Astilleros Armon. Capacity for 1,200 passengers is complemented by vehicle deck space corresponding to a ro-ro payload of 450 cars, or up to 500 lane-metres of trucks plus 250 cars.
The newbuild is a testament to the versatility of the productive shipbuilding and allied sector in northwest Spain, drawing on outside fields of particular expertise, not least Wartsila’s engineering and propulsion technology and Australian designer Incat Crowther’s know-how in fast, lightweight forms. Inputs from the domestic cluster have included engineering support by Cotenaval of Valencia and architectural and interior work by Oliver Design of Madrid.
Eleanor Roosevelt provides a further reference for the Wartsila 31 four-stroke, medium-speed engine platform, distinguished by its class-leading fuel efficiency rating, modular design and availability in diesel, dual-fuel and pure gas versions. While the diesel yields the highest cylinder power in its segment, at 610kW, the dual-fuel variant still gives a relatively potent 550kW per cylinder at the crankshaft speed of 750rpm.
The adoption of four 16-cylinder models in the Balearia
8 Eleanor Roosevelt, constructed by the Armon yard in Gijon
cat, at 8,800kW per unit, thereby makes for a primary power concentration of 35,200kW, transmitted through four Reintjes SLVJ850 gearboxes to a corresponding number of Wartsila waterjets of the LJX1500SR type.
In gas mode, the W31DF installation ensures IMO Tier III compliance, and the proprietary Wartsila LNGPac system’s storage tanks give the ferry a range of 400 nautical miles sailing only on natural gas. The reach is increased to 1,900 nautical miles with switchover to diesel, conferring both deployment flexibility throughout Balearia’s route network and service dependability in the event of any fuel supply issues. As a long-term contingency, the engine type lends itself to ready adaptation to pure gas operation, if required, or to the ingestion of renewable fuels.
The integrated power and propulsion system provides for schedules requiring laden service speeds of 35 knots, and a top speed in the order of 40 knots.
The isolated superstructure lessens transmission of noise and vibration to the passenger areas, while the latest iteration of Incat Crowther’s proven hull form, applicationspecific centreline bow, and retractable centre T-foil are designed to enhance comfort in difficult sea conditions. Hydrodynamic modelling and testing was carried out in Norway by Marintek-Sintef.
Certain features of the passenger spaces and seating layout have been adapted in light of the ongoing health crisis. On a fleet-wide basis, the company has taken an initiative that puts it in the vanguard of the industry for pandemic protection measures. Bureau Veritas (BV) certification to the society’s Global Safe Site Covid 19 criteria confirms that Balearia has implemented specific procedures, cleaning plans, organisational and personnel measures to combat Covid 19 aboard its ships and at terminals under the company’s management.
The level of certification, designated Excellence, means that periodic testing will be carried out for the presence of the virus on surfaces, using laboratory analysis.
While €290m (US$338m) of capital expenditure is encapsulated in the Italian-built sisters Hypatia de Alejandria and Marie Curie plus the Eleanor Roosevelt, the €72m (US$84m) commanded by the LNG dual-fuel retrofits to six of the existing fleet has attracted 20% in grant aid under the EU’s Connecting Europe Facility (CEF) provisions. Engine refitting began with the Napoles in 2019, followed by the Abel
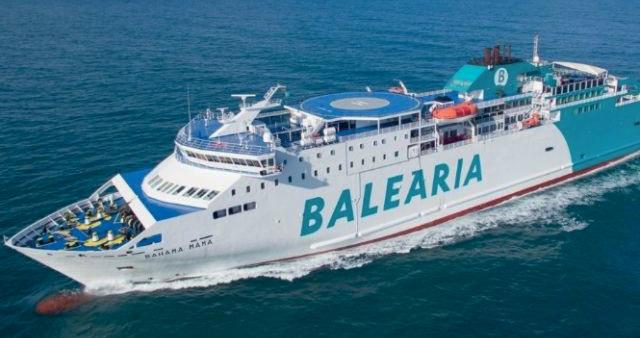
Matutes and Bahama Mama later that year, the Sicilia and Martin i Soler in 2020, with work on the Hedy Lamarr scheduled for next year.
Towards the end of last December, Balearia introduced the Multi Truck to Ship (MTTS) bunkering method at the port of Valencia. With MTTS, using Kosan Crisplant’s Y-piece solution, LNG can be supplied to the ship from two road tankers simultaneously. This raises the transfer speed of fuel to between 80 and 120m3/h, depending on the size of the trucks’ onboard pumps.
By comparison, the more usual way of bunkering from the quayside from a single tank trailer at a time typically means a transfer rate of some 30-50m3/h. The MTTS modus operandi thereby expedites the whole process, and does not entail high investment relative to the efficiencies gained. At Valencia, the initial fuelling was made to the Hypatia de Alejandria, engaged at the time on the Valencia/Ibiza/Palma run. Balearia signed a 10-year LNG supply agreement with Naturgy (formerly Gas Natural Fenosa) in January 2018.
Balearia’s traditional sphere of influence lies in the routes linking the Spanish mainland with the Balearic Islands (Majorca, Minorca and Ibiza). The company also connects Andalucian ports with northern Africa and the Canary Islands, and runs a service between Fort Lauderdale and the Bahamas. Expansion in foreign markets is a key goal, such that new connections are planned to North Africa and in the Caribbean.
PRINCIPAL PARTICULARS - Eleanor Roosevelt
Length overall 123.3m Beam 26.0m Depth 7.8m Draught 3.4m Passenger capacity 1,200 Ro-ro capacity (cars) 400 cars Ro-ro capacity (mixed) 500 lane-m (trucks) + 250 cars Propulsion machinery LNG dual-fuel medium-speed Main engine power 4 x 8,800kW Propulsors 4 x waterjets Speed, service 35kts Speed, maximum 40kts Generators 2 x 210ekW + 2 x 236ekW Class BV Flag Cyprus
8 The Bahama
Mama is one of six Balearia vessels which will be converted from diesel to LNG dual fuel
FLEXIBILITY AND VERSATILTY
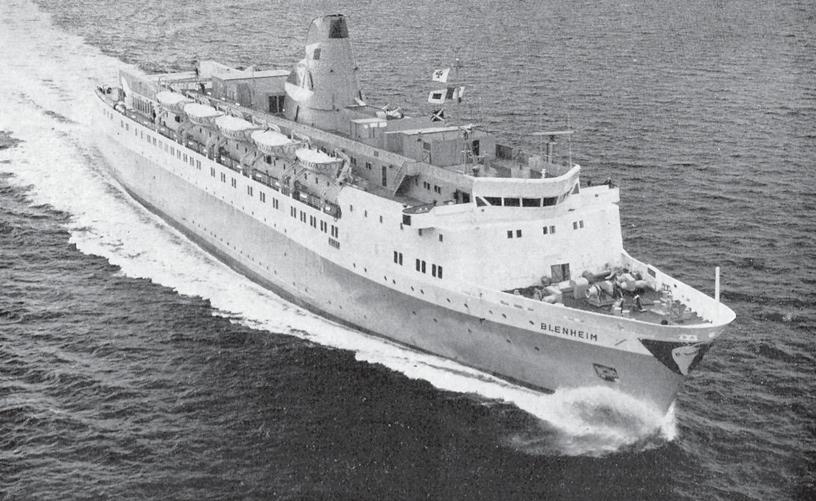
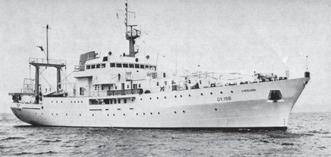
MOTORSHIPTHE
INSIGHT FOR MARINE TECHNOLOGY PROFESSIONALS
The international magazine for senior marine engineers
EDITORIAL & CONTENT
Editor: Nick Edstrom editor@mercatormedia.com
News Reporter: Rebecca Jeff rey rjeff rey@mercatormedia.com
Correspondents
Please contact our correspondents at editor@motorship.com Bill Thomson, David Tinsley, Tom Todd, Stevie Knight, Wendy Laursen
Production
Ian Swain, David Blake, Gary Betteridge production@mercatormedia.com
SALES & MARKETING t +44 1329 825335 f +44 1329 550192
Looking at the various vessels which were subjects of detailed reports in The Motor Ship, October 1970, ‘multi-functional’ is a phrase which frequently cropped up.
Fred. Olsen Lines had taken delivery of the Blenheim, designed to act as a car ferry or cargo liner in summer and cruise ship in winter. She was fitted out to carry 396 or 995 passengers, depending on configuration, while down below the ship transported either 300 cars or a “large quantity” of refrigerated vegetable containers. The concept had been tried before with two of the operator’s fleet, the Black Watch and Black Prince, the Blenheim being basically a stretched version of the earlier ships, with completely redesigned layout offering a greatly increased cargo capacity. Built at Upper Clyde Shipbuilders she was powered by a twin-screw Crossley-Pielstick plant, each of the 18PC2V engines rated at 9,000bhp to give a 23-knot maximum speed. All machinery featured a high level of automation, and was capable of unmanned engine room operation, although this was still not permitted under British Board of Trade standards. Most of the design effort had gone into the passenger and cargo accommodation, most cabins for the former being convertible from single or twin-berth for cruising into double- or four-berth units respectively for ferry duties. Similarly, the cargo space featured six refrigerated compartments below the main deck, aft of the machinery, and a further two compartments either side of the main deck. The garage space, accessed from a stern door, was two decks high, allowing high vehicles to be carried, while the forward half was equipped with a hydraulic hoistable ramp allowing cars to be carried on two levels or, with the ramp raised, full height cargoes.
Other reports concerned a new class of four Belgian-built 18,000 dwt product tankers for Stolt-Neilsen, equipped with complex cargo handling and tank cleaning systems, which were claimed to allow the ships to carry any of 400 different oil and
8 The Blenheim, a true multi-purpose vessel for
Fred. Olsen Lines. Inset: Cirolana, built to a trawler design, featured electric propulsion and was employed on research duties
chemical products in the 36 tanks, nine of which were of stainless steel construction. The MAN K7Z70 main engine was rated at 9800 bhp, and drove a Kamewa CP propeller with automatic adjustment to maintain engine torque load at a pre-determined value.
Another interesting vessel, for the time, was built at Ferguson of Port Glasgow as a stern trawler, but was to be employed primarily for fisheries research and oceanographic survey. In keeping with this role, a diesel-electric propulsion plant was specified, with the aim of minimising noise and vibration. Three 1100 bhp Allen-engined generating sets each drove a constant-current generator, two of the gensets including an alternator connected in tandem for auxiliary electrical load. These were supplemented by a further 460 bhp Paxman-driven alternator. The main gensets powered a 2200hp electric propulsion motor, plus the 400hp trawl winch motor and a 350hp bow thruster. To aid navigation and position-keeping, a sophisticated suite of electronics was installed on the bridge, including two radars, echo sounders, gyro and autopilot, Decca navigator and electromagnetic log.
Finally, the issue included a 52-page supplement on ‘British Shipbuilding Today’, taking a notunnaturally optimistic view of changes made to increase competitiveness in world markets, such as grouping of yards into eight companies, helped by grants and loans, and a planned move from ‘prestige’ vessels to standardised designs. Despite the upbeat tone of the various reports, structural shifts in the industry led to an erosion in the competitiveness of UK merchant shipbuilding. This would accelerate in the 1970s as Brazil, South Korea and subsequently China used shipbuilding as a demand driver for the creation of domestic steel industries, while a distracted UK government allowed the UK’s position in shipbuilding to diminish.
Brand manager: Toni-Rhiannon Sibley tsibley @mercatormedia.com
Marketing marketing@mercatormedia.com
EXECUTIVE
Chief Executive: Andrew Webster awebster@mercatormedia.com
TMS magazine is published monthly by Mercator Media Limited Spinnaker House, Waterside Gardens, Fareham, Hampshire PO16 8SD, UK
t +44 1329 825335 f +44 1329 550192
info@mercatormedia.com www.mercatormedia.com
Subscriptions
Subscriptions@motorship.com or subscribe online at www.motorship.com Also, sign up to the weekly TMS E-Newsletter 1 year’s magazine subscription £GBP178.50 UK & EURO Post area £GBP178.50 Rest of the World
© Mercator Media Limited 2020. ISSN 0027-2000 (print) ISSN 2633-4488 (online). Established 1920. The Motorship is a trade mark of Mercator Media Ltd. All rights reserved. No part of this magazine can be reproduced without the written consent of Mercator Media Ltd. Registered in England Company Number 2427909. Registered offi ce: Spinnaker House, Waterside Gardens, Fareham, Hampshire PO16 8SD, UK. Printed in the UK by Holbrooks Printers Ltd, Portsmouth, PO3 5HX. Distributed by Mail Options Ltd, Unit 41, Waterside Trading Centre, Trumpers Way, London W7 2QD, UK.


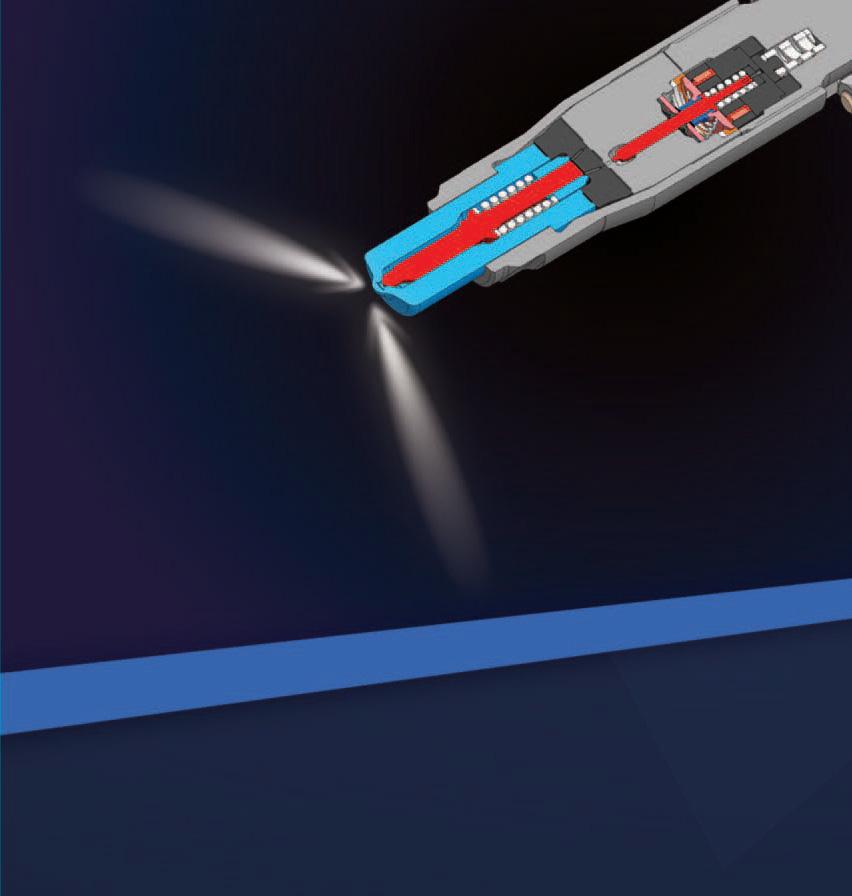
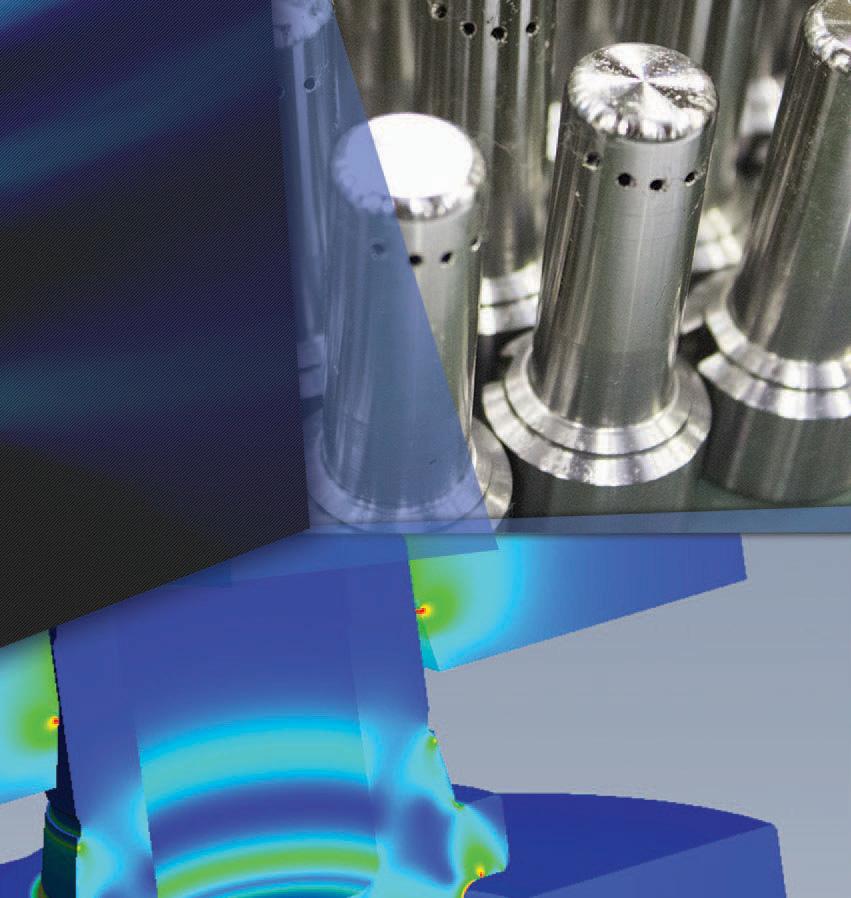
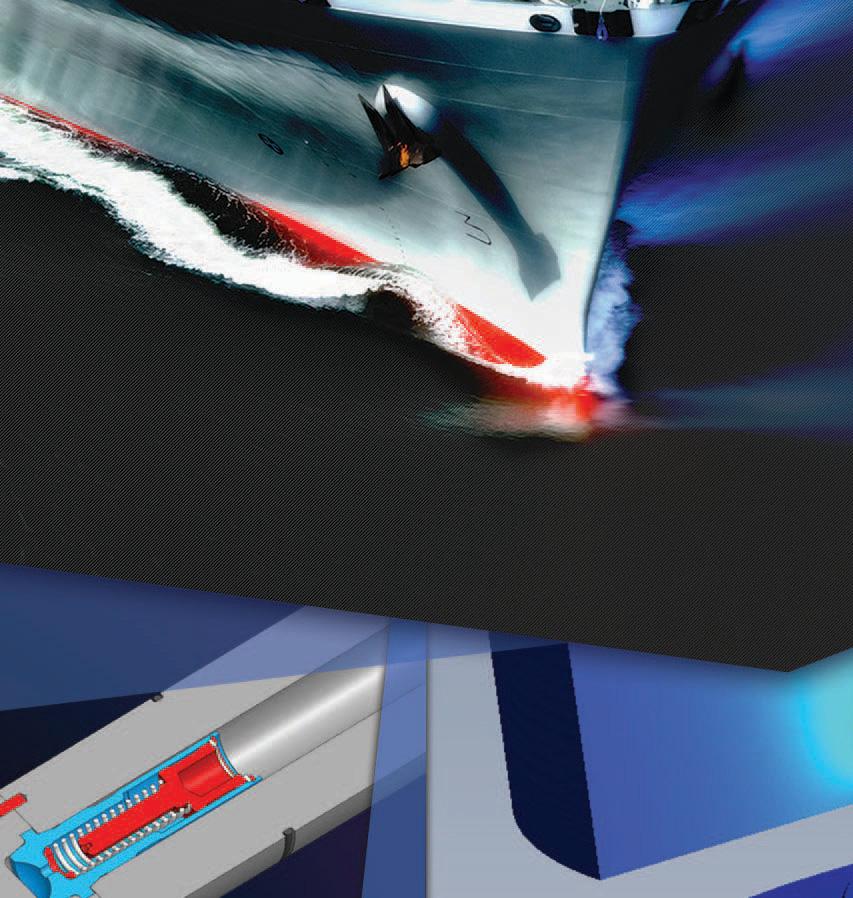
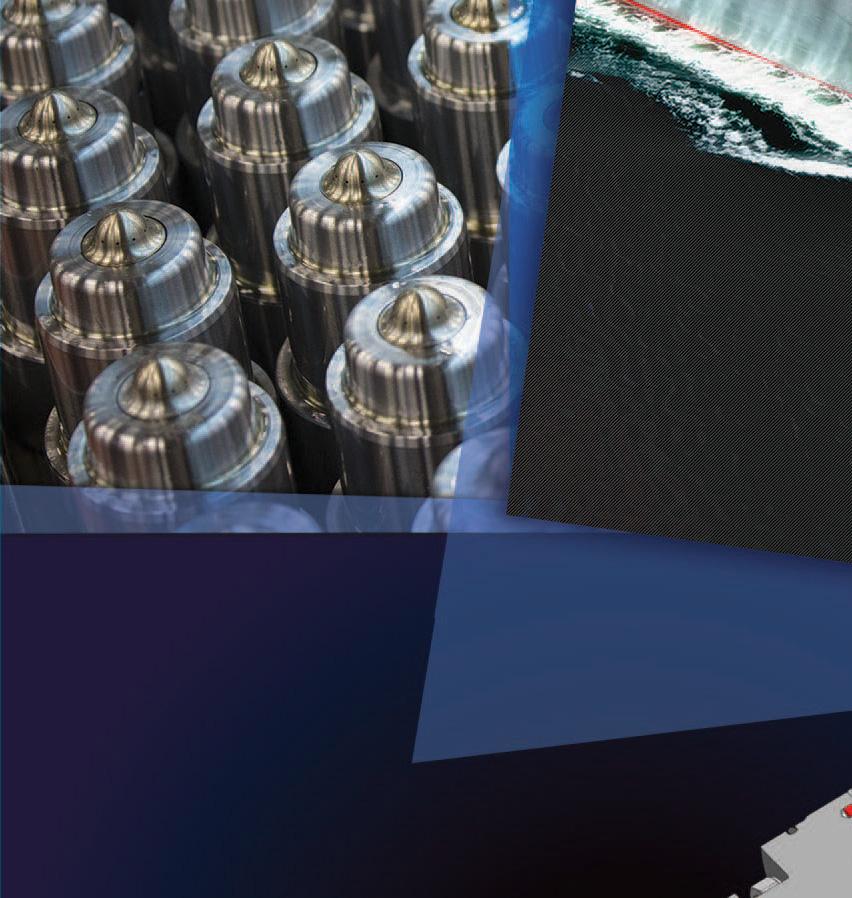
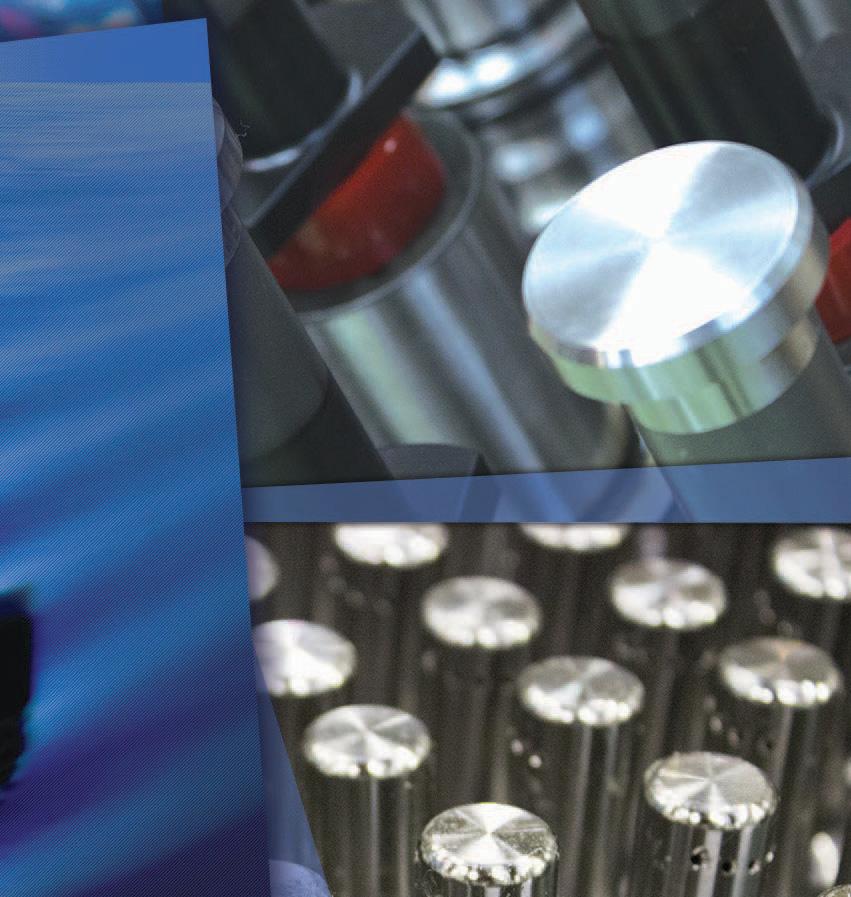

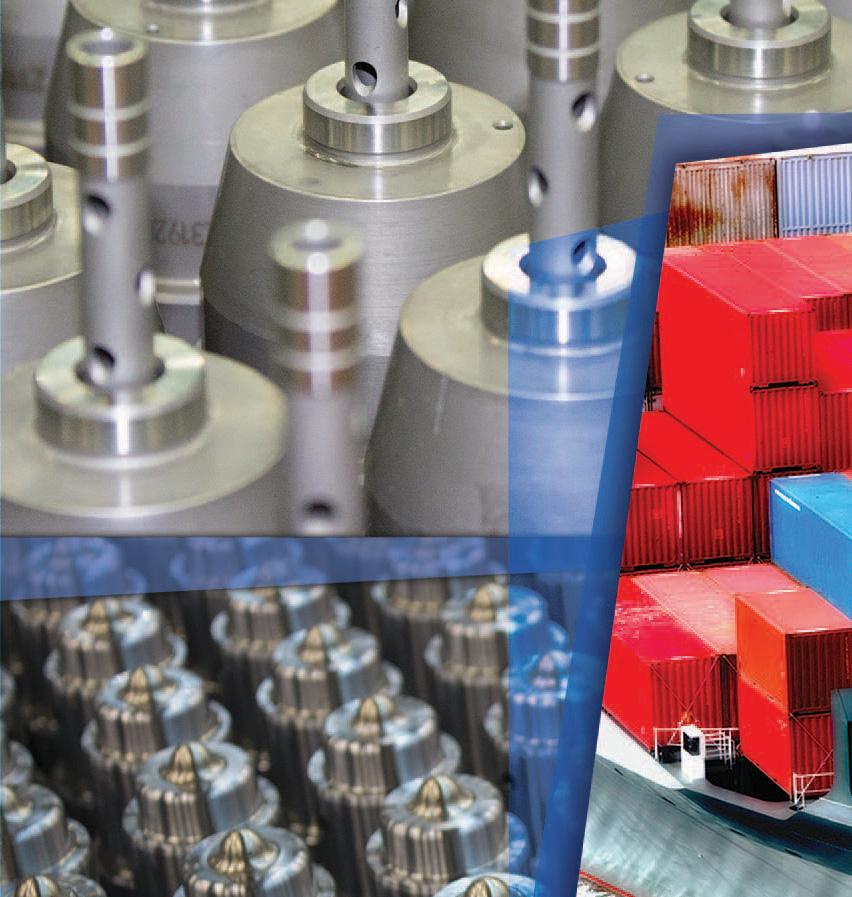
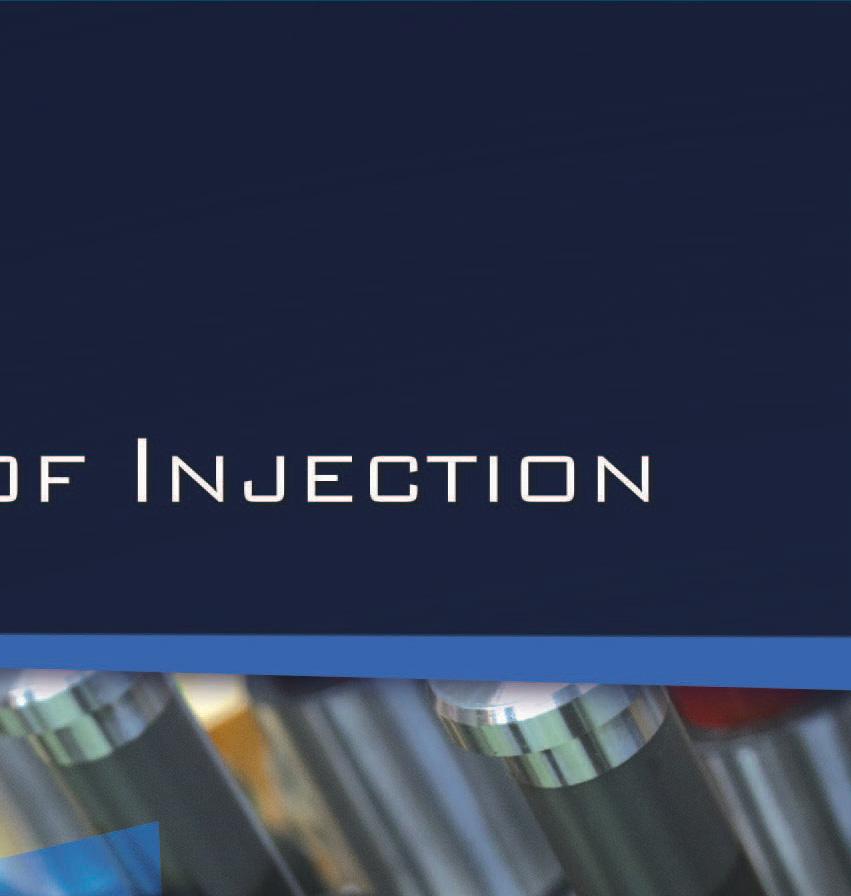

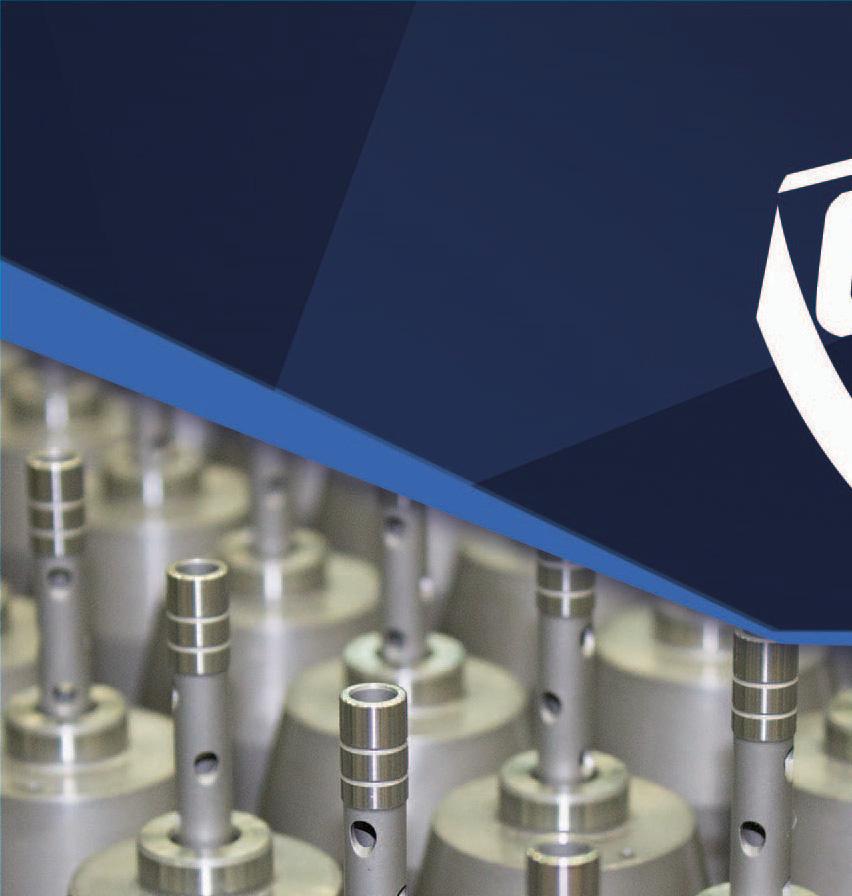