
5 minute read
BCMPA
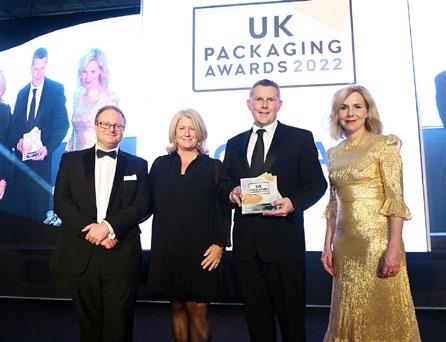
The BCMPA was proud to announce Staci UK as this year’s ‘Co-Pack & Fulfilment Company of the Year’ at the UK Packaging Awards 2022, with Granby Marketing Services being Highly Commended.
The awards recognise the extraordinary support that contract packing and fulfilment firms provide to the brand owners and the wider retail sector, services which have become increasingly vital in the current uncertain and turbulent world of commerce.
The prestigious black-tie event held at London’s Grosvenor House on Park Lane saw the BCMPA, the Association for Contract Manufacturing, Packing, Fulfilment & Logistics, as proud sponsors of ‘Co-Pack & Fulfilment Company of the Year’ one of 27 categories at the 2022 UK Packaging Awards.
The five finalists in this hotly contested category – Complete Co-Packing Services, Expac, Granby Marketing Services, Staci UK, and Worldwide Logistics – were all represented and enjoyed the event along with 600 guests from across the packaging industry. Director of the BCMPA, was delighted to present the winners with their awards. In congratulating Staci UK on their win, Emma commented; “We are thrilled and honoured to be sponsors of the Co-Pack & Fulfilment Company of the Year Award at this year’s UK Packaging Awards. It is particularly rewarding to be able to shine a light on the huge and growing contribution that the co-packing and logistics sector makes in supporting businesses running efficiently and effectively in such challenging times.”
Overall winners, Staci UK, are one of Europe’s leading fulfilment and logistics specialists, with 56 fulfilment centres across 8 countries. Also highly commended at the event were BCMPA members Granby Marketing Services.
Emma added; “The amazing quality of all the finalists this year demonstrates the fundamental importance and relevance of contract packing & fulfilment in the packaging industry, and the increased collaboration between brands and their third-party partners has now become a necessity for many. With the multiple challenges ahead, I have no doubt that this collaboration will continue to strengthen in 2023.
“Congratulations to all our 200 members for their commitment and sterling efforts this year, and in particular our winners and finalists at this year’s UK Packaging Awards.”
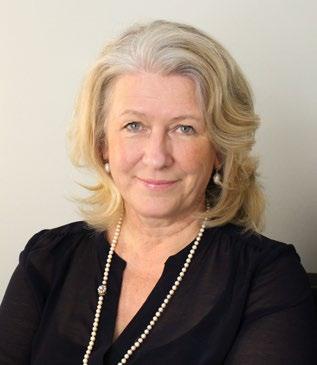

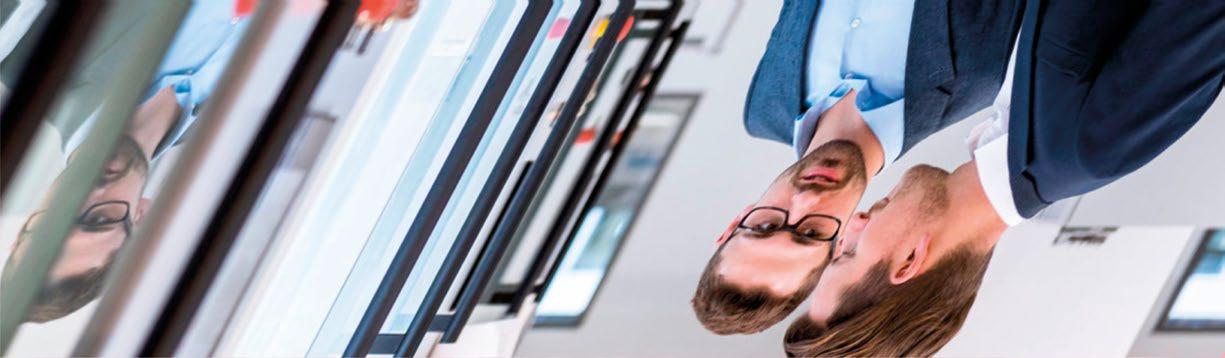
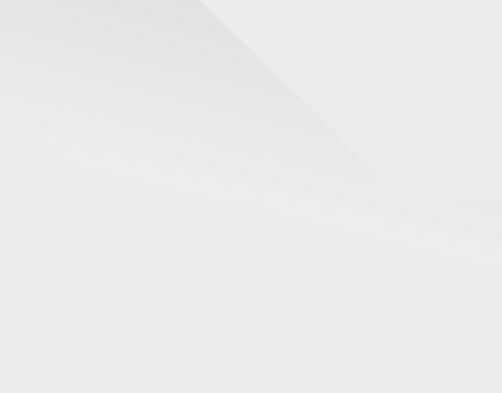
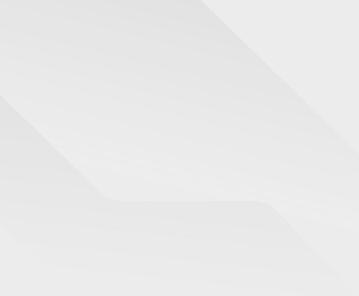
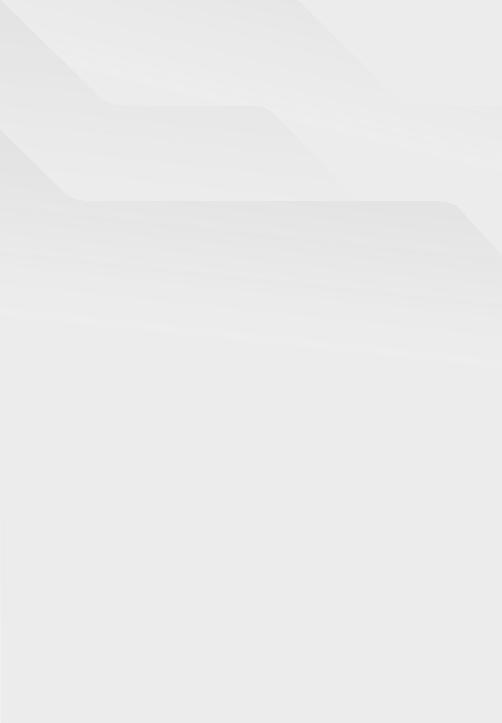
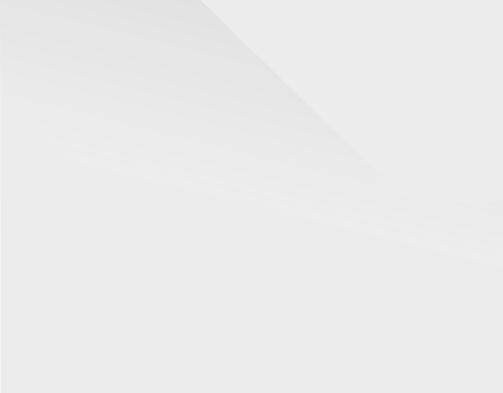
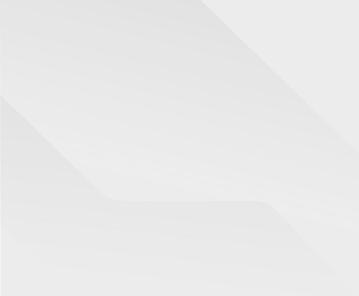
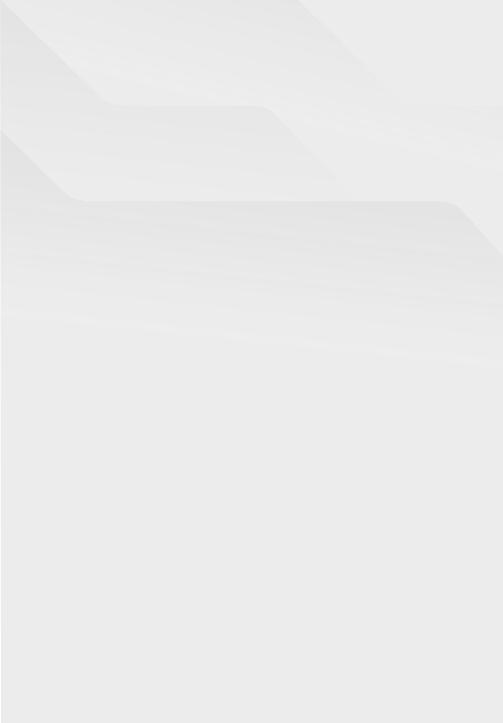
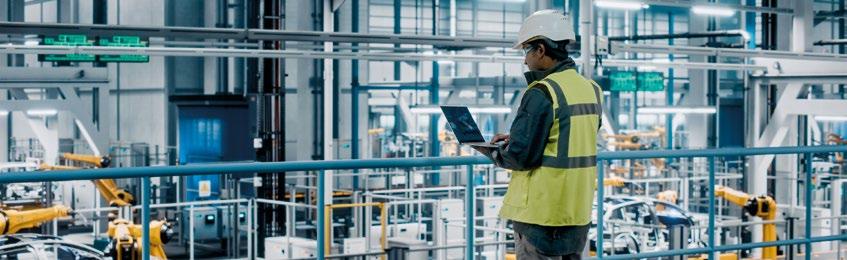
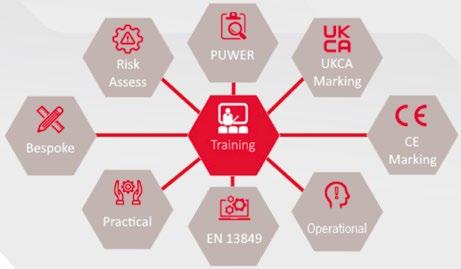
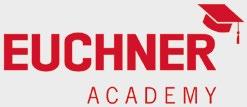
Gappscan G2 from EIT International can help overcome the common issues encountered when testing PHEs
ISSUE AND SOLUTION:
1. There is no visible sign of a PHE defect Probably the most regularly encountered and significant issue with PHEs is that they often show no outward sign of defect. Rather than obvious external leaks, generally the corrosion and expansion/ contraction defects occur inside the PHE meaning contamination sites happen unseen. The Gappscan uses software to detect minute pressure changes within the PHE which allows for a more effective maintenance programme that is proactive rather than reactive.
2. Downtime associated with testing can be a headache
PHE testing, when units need to be dismantled, decontaminated, and reassembled takes PHEs out of use for long periods, obviously affecting production time. The Gappscan doesn’t require dismantling of the PHE for full testing to be conducted, nor does it need to use any invasive chemicals. This results in testing that is very quick, meaning the PHE can be back in productive operation fast, and multiple PHEs can be completed in one visit, improving the ROI drastically on traditional testing methods.
3. Testing is labour intensive and takes time to produce results The Gappscan only requires the PHE to be disconnected not dismantled and the testing can be carried out by one person in less than 5 minutes, with the results available immediately.
Traditionally labour-intensive testing methods using substances whether dye, chemical or gas can be time consuming as each PHE must be dismantled for these penetrants to be applied and be allowed time to penetrate each section for results to be reviewed for defects.
4. Environmental accountability: “I have to dispose of chemicals/dyes/gases and ensure the PHEs are thoroughly clear of any residues before reintroducing the PHE to production” The Gappscan test uses water under pressure... that is all. Traditional testing methods employing dye penetrants and other substances/ gases, need disposing safely and responsibly once all tests are complete. Additionally, thorough cleaning protocols need to be carried out before the PHE can be brought back into service. By using water under pressure, Gappscan not only gets your PHEs back into productive use quickly, it does so safely with low environmental impact.
5. “Tests that only produce pass or fail results, mean I can’t plan maintenance or replacements” The Gappscan testing method can identify and report numerous cracks and defects in a PHE using varying levels of pressure, and detect defects as small as a few microns, so the reporting is more granular and each test is saved securely to monitor changes in PHE behaviour and performance over time, allowing effective of preventative maintenance.
For further information on Gappscan™ G2, please get in touch or visit www.eit-international.com
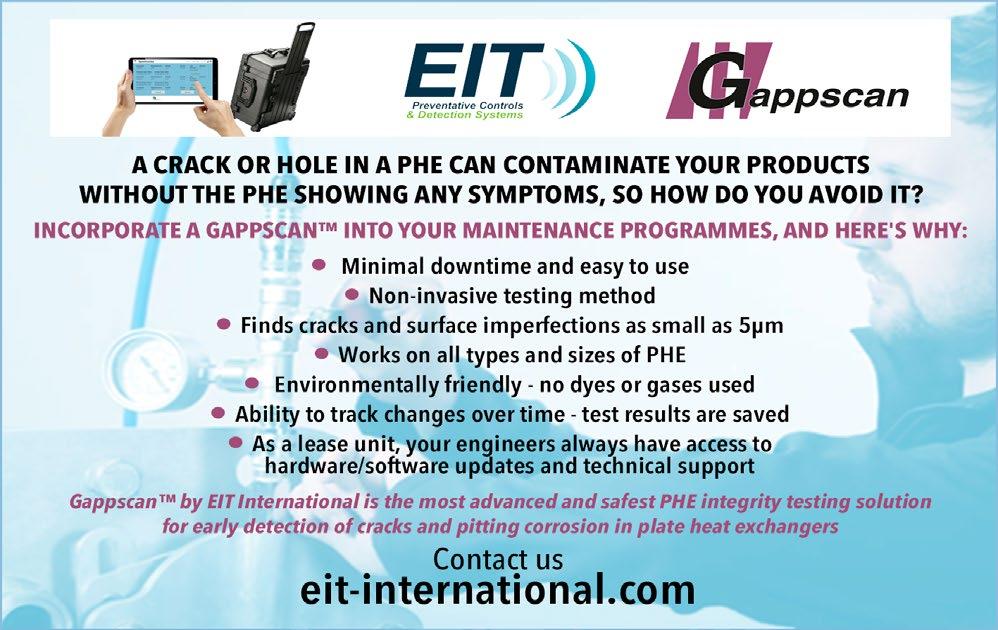