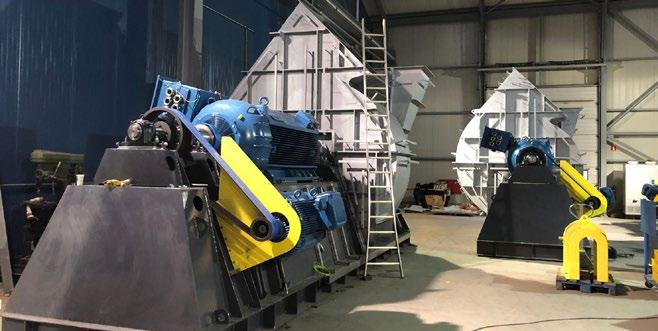
4 minute read
WEG
Energy-efficient motors power Hong Kong’s sustainable development
Global motor producer WEG contributes twelve motors to state-of-the-art WTE facility
CBV, in partnership with motor and drive manufacturer WEG, has contributed to developing a self-sustaining waste to energy (WTE) island for Hong Kong’s residual waste. It is estimated the island will save 440,000 tonnes of carbon emissions per year, the equivalent of the yearly carbon emissions produced by 2.2 million gas-based cars.
In response to the Paris Agreement, the Government of Hong Kong’s Climate Action Plan set a target of reducing the country’s carbon intensity by 65 to 70 per cent, compared to 2005, by 2030. The country is progressing steadily in meeting this ambitious goal. In 2019, it had already reduced its carbon emissions by 35 per cent.
The new WTE facility will represent another step in the right direction. The facility will consist of six lines supplying mainland Hong Kong with two GWh of electricity per day, thanks to a highly efficient WTE process. This is complemented by a state-of-the-art flue gas cleaning system that complies with strict emissions standards.
Waste heat, which is generated as a byproduct of working machines, will be used to dry the waste going to mechanical sorting for material recovery. Part of the heat will also be used to power the cooling system of the buildings on the island. A wastewater treatment plant will ensure that no water needs to be disposed of, while solar panels will guarantee that the power requirements of people working on the island are met. of desalinated water per hour, which will be used for processes, building services, and irrigation of the green spaces covering the entire island, including the facades of the WTE facility. The project will also prevent the landfilling of 1,2 million tonnes of residual waste, generated by one-third of the citizens of Hong Kong, which is unsuitable for recycling.
The WTE plant is composed of three process modules, each consisting of two incineration lines. Each line needs one induced draught (ID) fan and one secondary fan, both of which require motors.
The project used a total of twelve electric motors from WEG, six 1300 kW model HGF 500 motor, and six 132 kW model W22 315S/M motors. The motors will drive the ID and secondary fans supplied by CBV, which are essential components of the incineration trains.
The design-build-operate (DBO) contract for Phase 1 of the integrated waste management facility (IWMF) was awarded in November 2017, and in November 2021 the motors were delivered. According to the Environmental Protection Department of the Government of Hong Kong, Phase 1 of the project is expected to be fully commissioned by 2025, with the contract including a 15-year operation period.
“The new WTE island will massively contribute to Hong Kong’s sustainability targets, but more importantly it will help reduce carbon emissions globally, taking us one step closer to the goals established by the Paris Agreement,” explained Marek Lukaszczyk, European and Middle East marketing manager at WEG. “Efficient and reliable electric motors are at the core of complex WTE technology, and WEG represents a natural choice for projects that require durability, efficiency and costeffectiveness. We are confident that the motors supplied will serve the island well for many years to come,” he concluded.
For more information about WEG’s wide range of electric motors and to schedule a meeting with a representative from WEG, visit www.weg.net.
Food
for thought...
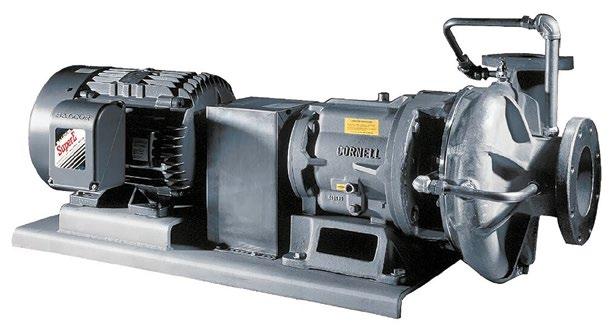
Fluid thinking from the Hydromarque team
Peterborough based, Hydromarque Ltd have 30 years’ experience providing specialist pump solutions to food processing companies.
Hydromarque’s expert engineering team understand the important role food handling pumps play in today’s marketplace and the need for pumps capable of transporting even the most delicate food products.
Pumping food products has an overriding issue – any food product damage can result in degradation to the final product and profit losses for food processing plants. Continuous and trouble-free pumping operation is critical.
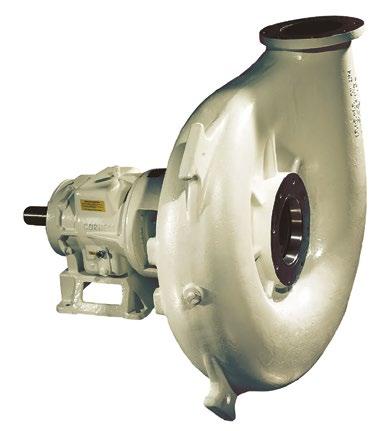
Hydromarque ltd are the sole UK and Eire agent, stockist and service provider for Cornell hydro-transport and hot oil pumps. Unlike solids handling pumps that are sometimes used in the food industry, the Cornell P and PP series pumps are designed and manufactured with the sole purpose of pumping food products. Cornell food process pumps have the lowest product damage rates in the industry and are the pump of choice for food processors around the world. Their innovative single port impeller configuration with unique offset volute* provides the end user with a food handling pump capable of transporting even the most delicate food products.
Hydromarque are proud to supply Cornell’s hot oil pumps offering enhanced vapour handling and improved sealing technology. This prevents entrained steam from impacting pump head and flow which is central to Cornell’s innovative cooking oil pump developments.
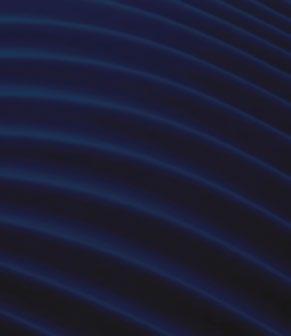
Working alongside many larger potato chip, potato crisp, fried snack and vegetable processing companies, Hydromarque have extensive experience providing tailored solutions to improve food processing pumping.
Whether you make potato products, process vegetables, produce ready meals, snacks or process poultry or other livestock, the Hydromarque team will recommend the best solution to enhance your efficiency and reduce your production downtime.