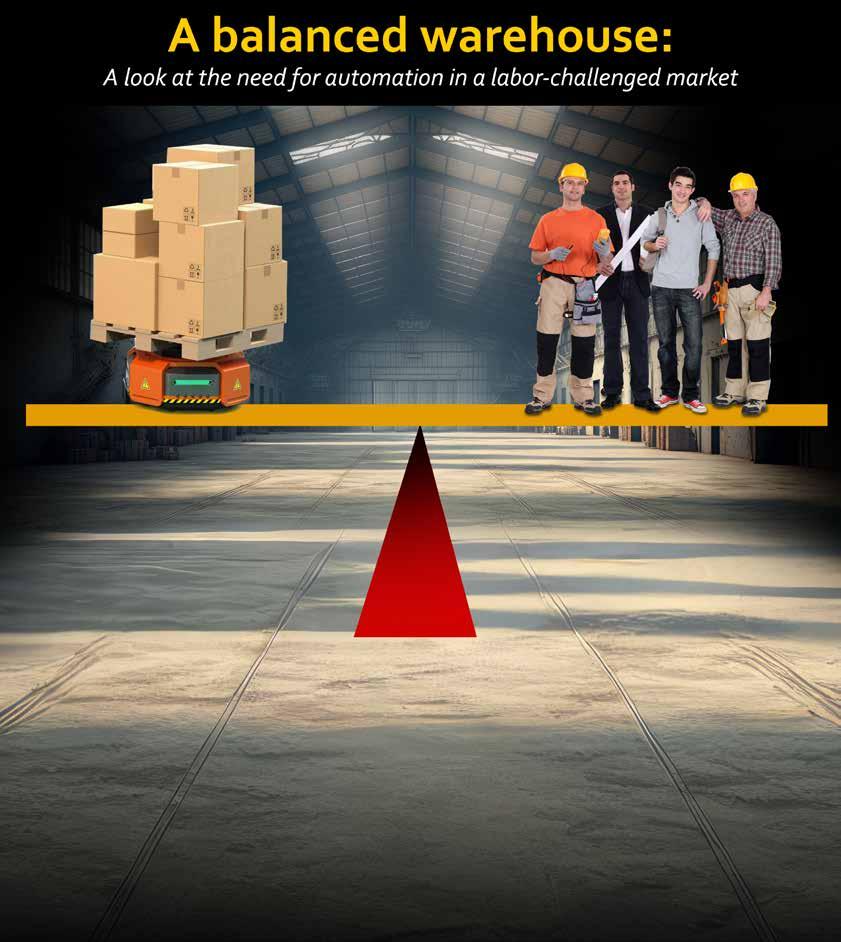
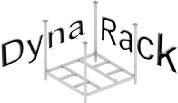
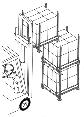
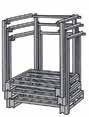
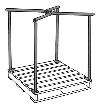
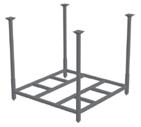

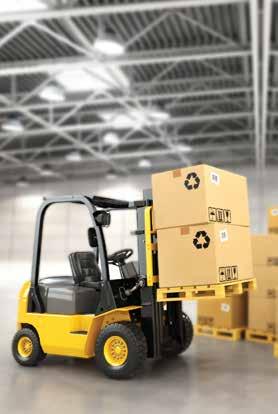
Whether you’re storing, conveying, picking or handling, there’s not a corner of the warehouse that our robots and solutions will not fit.
categories at Wolter include automated vehicles, robotics, conveyors and automated handling, automated storage and retrieval systems, software and sensing, and applications by job function, according to the website.
Personnel and automation technology now are both a familiar presence in many warehouses. So how should warehouse leaders plan for a balanced co-existence? For some, the answer to mapping it out starts with the topic on many minds lately. “The number one thing is the labor shortage,” said Kelly Shattuck, automation and dynamic storage solutions corporate sales manager at Wolter Inc.
The company, originally known as Wisconsin Lift Truck, was started in 1962 by CEO and founder Otto Wolter. In the years since, operations have expanded into Illinois and beyond. “The last five to ten years, it has expanded drastically through acquisition,” said Shattuck, who said the company was renamed Wolter Inc. after growing into an operation with 600 employees across seven states.
Today, the company includes “an extensive suite of operational productivity solutions, including material handling, automation and robotics, cranes and hoists, engineered systems, storage and handling, rail car movers, power systems, workplace storage, service, parts and accessories, rentals and training,” according to the business website. Automation and robotics solutions
While some associate the labor shortage with the recent pandemic, Shattuck noted broader trends. “Depending on the particular market, there’s been a shortage of welders for 30 years,” he said. “In the Midwest it’s been a common practice that when a business grows you throw a lot of people at it. We don’t have that luxury anymore.” Shattuck said he will often hear from customers with anywhere from “five or 10 all the way up to hundreds” of open positions.
“When we talk about automation, it’s not about people losing jobs,” he added. In the U.S. labor market as a whole, a recent study echoed the concept. The shortage of American workers is the result of demographic and other trends that predate the COVID-19 pandemic, according to a Brookings Institute study released last spring by Katharine G. Abraham and Lea Rendell of the University of Maryland. While the study found that the labor market has “changed significantly” since the start of the pandemic, “much of the decline in the labor force participation over the past three years should have been anticipated even absent the pandemic,” the study’s authors wrote.
In warehousing, Shattuck noted that a typical question for customers is to assess not just what they’re experiencing on the shop floor but how many sales dollars have been lost because of not having enough personnel. The answers he has heard range from hundreds up to thousands “if not millions” of dollars. “It’s amazing even after
fighting labor shortages for more than five years or 10 years, you still have to point it out,” Shattuck said.
For some, there has been a phenomenon since the downturn of 2007 to 2009 of people taking on multiple jobs, Shattuck added. “It’s just keep your head down and just keep working,” he said, describing the approach. For those who are adopting more automation, a second consideration after labor is safety, according to Shattuck. “Anytime you have pedestrians and manned forklifts in the same area, it’s a huge safety concern,” he said.
A third motivating factor for automating is often mandates within larger companies, according to Shattuck. For smaller companies, he said automation cost can be a factor and implementation typically focuses on the return on
Another piece of the labor puzzle for companies of all sizes is an aging workforce, according to Shattuck. “Right now, if you go into any facility, a large part of the labor force is within five to ten years of retirement,” he said, adding that there is not a large pool of workers to backfill those positions. Shattuck said it is key to get information to younger workers about opportunities in the industry. “If a younger person right now was thinking about what they want to do when graduating, I would tell them to go into an automation tech position,” he said. “It’s not like an engineering degree; it requires some basic knowledge of how vehicles work and some basic coding, and even those systems are getting super easy now. “It’s a huge need going forward; people who can work on automation systems.”
Overall, Shattuck encouraged companies to think expansively about how automation may be of value in warehouse needs now and in the future. “What can be automated is based on how much imagination you have,” he said.
Employees should be permitted to wear pants or jeans in the warehouse, provided they are wellfitting. Baggy pants can create a serious safety concern, so this should be explained in your dress code. You can decide whether you will limit employees to a specific color. For example, darker colors are better at hiding dirt and stains, so they may appear more professional.
Most warehouse jobs will require that workers be on their feet for long periods and do some repetitive lifting. So, it's important to dress in comfortable clothing that allows movement. But many warehouses also have dress codes and value safety. Some even require employees to wear uniforms. Here are some tips for appropriate clothes for a warehouse job, whether you decide everyone should wear the same thing or not.
Requiring everyone in your warehouse to wear exactly the same thing probably isn't necessary. Instead, it will end up being costly for you and an inconvenience for your workers. Employees come in all shapes and sizes, so having uniforms on hand in dozens of sizes isn't always practical. Instead, many warehouses opt for a strict dress code that considers productivity, safety, and comfort.
A warehouse dress code needs to be as practical as possible. When your business is reasonable about allowing employees some choice in how they dress, it will go a long way in improving your organization's overall culture. Here are a few essential components of a warehouse dress code.
Your business will need to decide what type of shirts are appropriate for your warehouse employees to wear. Do you want to provide everyone with logo shirts to create some team camaraderie? If not, be specific about whether polo shirts or t-shirts are permitted as part of your dress code. It's also important to note whether you will disallow certain things like political messages or images that may be considered offensive.
Proper footwear is essential for warehouse work for several reasons — comfort and safety. Employees spend many hours at a time on their feet, so they must wear high-quality footwear to prevent foot and back issues. Shoes with wedge soles provide excellent support. Safety is another concern. If a heavy object falls on an employee's foot or they get too close to moving equipment, it can lead to a serious injury. Steel-toed shoes can provide significant protection from these hazards.
Many warehouses overlook headwear, but this is an essential part of your dress code. Employees should be permitted to wear hats and beanies to keep their core body temperature warm during cold weather. Headware can also move unruly hair out of the way so that it doesn't get caught on machinery or end up in a consumer's box during order fulfillment.
Safety should be a priority in every warehouse and distribution center. While personal protective equipment (PPE) isn't necessarily a dress code requirement, it makes sense to include this so you can drive home its importance. Remind workers what equipment they will be required to wear, depending on their job duties. These might include things like:
• Hard hats
• Safety vests
• Eye protection
• Hearing protection
Many workers are also asked to wear technological equipment, like wireless headsets and sensors, to assist with work. Their choice of clothing should be compatible with this equipment.
Some warehouse attire should be required (see above). But, depending on the conditions in your warehouse and your worker's preferences, other items might be optional. Here are a few examples.
If your employees are asked to work in a cold warehouse during the winter months or deal with refrigerated items, they'll probably want to wear jackets. This is about worker comfort but can also be a safety issue depending on the temperature extremes.
Gloves
Gloves may also be necessary to keep workers' hands warm in cold temperatures. Many workers will also opt to wear gloves to protect their hands from minor scratches or drying out. These are generally accepted as long as they don't interfere with productivity.
If your workers are doing particularly dirty work, such as machinery maintenance or driving forklifts, you may wish to provide coveralls. These go over regular street clothes to provide additional protection from grime and some minor hazards.
Even if you don't have a warehouse uniform, it's a good idea to create a dress code that outlines what employees should wear in the warehouse to improve safety and productivity. There should also be a list of items that aren't appropriate for warehouse work. These might include:
• Open-toed shoes — Shoes like flip-flops are unacceptable in a warehouse. They don't protect workers' feet and can lead to trip and fall injuries.
• Baggy clothing — Clothing that isn't wellfitting can present a safety issue because it can get caught on machinery or shelves or create a tripping hazard.
• Shorts — Some warehouses don't allow workers to wear shorts of a certain length (too short) or ones that are too baggy.
• Jewelry — Wearing jewelry is considered a hazard in many warehouses because it can get caught on shelving or machinery and lead to serious injuries.
Employees want to be dressed comfortably at work. In a warehouse, this is certainly possible. But there must be a balance between comfort, utility, and safety. You can create a dress code or uniform that strikes that balance to ensure efficiency and satisfy your workers.
Newcastle Systems, Inc. is a provider of workplace mobility solutions that include a range of mobile carts for every workstation need with a unique, integrated power system that enables companies to maximize workplace efficiencies with minimal investment. Newcastle Systems mobility solutions are in place around the world helping reduce footsteps in warehouses, speed up receiving, picking, and shipping operations, improve staffing efficiencies on the retail floor, and provide convenience and ergonomic benefits for employees in manufacturing, education, distribution, military, and government sectors. For more information, visit http://www.newcastlesys.com or e-mail sales@ newcastlesys.com.
A robust WMS empowers you with real-time visibility into inventory levels, locations, and movements. You can optimize storage space by strategically placing products based on demand patterns and automatically replenishing stock. For example, a WMS can analyze historical sales data and predict demand, ensuring that popular products are stored near the picking area, reducing travel time and improving efficiency.
Efficient warehouse operations are essential for optimizing productivity and meeting customer demands. Harnessing the power of automation is key, and three types of automation systems stand out: Warehouse Management Systems (WMS), Warehouse Execution Systems (WES), and Warehouse Control Systems (WCS). In this article, we will delve into each system's unique value proposition, explore their roles, and uncover how they work together to streamline warehouse operations.
The WMS can be likened to the brain of the warehouse operations. Just as the brain coordinates and controls various functions of the body, the WMS oversees and manages the entire warehouse. It processes information, analyzes data, and makes strategic decisions to ensure efficient inventory management, order processing, and overall operational optimization. Similar to how the brain communicates with different body parts to coordinate their actions, the WMS communicates with different areas of the warehouse to coordinate tasks, allocate resources, and maintain smooth operations.
With a WMS, you can streamline the order fulfillment process. The system manages order prioritization, wave planning, and batch picking, allowing you to optimize order cycles and minimize errors. For instance, in an e-commerce warehouse, a WMS can automatically group orders by proximity to minimize travel time, ensuring faster order fulfillment and improved customer satisfaction.
The WES can be compared to the limbs of the warehouse. Just as limbs are responsible for executing tasks, the WES is responsible for executing and coordinating the tasks within the warehouse. It ensures that tasks are assigned to the right resources, workflows are optimized, and operations are streamlined.
A WES takes dynamic task allocation to the next level. By dynamically assigning tasks to available resources, such as automated equipment and human workers, a WES optimizes task sequences, routes, and priorities. For example, in a retail distribution center, a WES can intelligently allocate picking tasks based on the location of items and the availability of pickers, reducing travel time and increasing throughput.
A cutting-edge WES optimizes workflows by synchronizing activities across different warehouse areas. It ensures a seamless flow of materials by coordinating receiving, put-away, picking, and shipping processes. For instance, in a crossdocking operation, a WES can automatically direct incoming shipments to outbound docks based on customer demand, minimizing storage time and improving order turnaround.
The Nervous System: Warehouse Control Systems (WCS)
The WCS can be likened to the nervous system of the warehouse. Just as the nervous system controls and coordinates the movement and functions of the body, the WCS controls and coordinates the movement and functions of the automated equipment in the warehouse. It ensures that the equipment operates smoothly, efficiently, and in synchronization with other operations.
A WCS provides comprehensive control and optimization of material handling equipment. These systems interface with automated equipment such as conveyors, sorters, and robotics to ensure seamless integration and efficient utilization of resources. For example, in an apparel warehouse, a WCS can control the conveyor system, directing the flow of garments from the sorting area to the packing stations, improving efficiency and reducing manual handling.
With a WCS, you gain real-time data from sensors and scanners, enabling informed decisionmaking. The system can dynamically route materials based on factors like order priority, equipment availability, and congestion levels. For instance, in a high-throughput distribution center, a WCS can dynamically re-route a carton to an alternate conveyor line if there is a temporary jam, ensuring smooth material flow and avoiding disruptions.
When WMS, WES, and WCS work together in harmony, the result is an optimized and streamlined warehouse operation, a perfect triad. The WMS provides strategic oversight, ensuring accurate inventory control and efficient order management. The WES adds operational agility
and optimization by dynamically assigning tasks, coordinating workflows, and synchronizing processes. The WCS ensures efficient control over automation equipment, orchestrating their movements and optimizing resource utilization.
Integration between these systems allows for seamless data sharing and task coordination. The WMS feeds information to the WES, which dynamically assigns tasks to available resources based on real-time inventory and order data. The WCS interfaces with both systems, enabling real-time equipment control based on the overall warehouse operation. For example, if the WES identifies a surge in order volume, it can notify the WCS to prioritize certain automated processes, ensuring smooth operations during peak periods.
In the quest for efficient warehouse operations, Warehouse Management Systems (WMS), Warehouse Execution Systems (WES), and Warehouse Control Systems (WCS) are indispensable. A robust WMS streamlines inventory management and order processing, ensuring accurate inventory control and optimized order fulfillment. A dynamic WES optimizes workflows, task allocation, and resource utilization, increasing productivity and reducing errors. WCS ensures efficient control over automation equipment, orchestrating their movements and optimizing resource utilization. When these systems synergize and integrate, warehouses unlock the power of automation, achieving optimized operations, increased productivity, and superior customer satisfaction. Embrace the potential of WMS, WES, and WCS to elevate your warehouse operations to new heights of efficiency and effectiveness.
Bill Denbigh serves as the vice president of product marketing at Tecsys. Bill started working in supply chain software some 30 years ago; his entire career has been laser-focused on designing and building pragmatic supply chain solutions that address the real problems that customers are facing in their supply chain operations. Bill has worked on virtually every aspect of the software in the supply chain, gaining insight into the inner workings of some of the industry’s most complex challenges; Bill, however, tackles those challenges with a no-nonsense levelheadedness that has earned him great repute both internally and among customers.
At long last, there are signs that companies are increasing employee training and participating in talent development programs. Why is this finally happening?
A recent Federal Reserve program held in Chicago focused on how companies in four Midwestern states are partnering with their local communities to upskill younger entry-level workers. Companies from many businesses sectors are collaborating with K-12 and post-secondary institutions to offer both career information and educational programs aligned with current job requirements.
This program also included a public high school graduate who told the audience how mentorships and a career exploration program interested him in pursuing a STEM career. He is now eager to begin post-secondary education that will qualify him for a career in information technology.
A barrier that discourages publicly traded corporations from developing human capital is now being challenged. Arcane financial
accounting rules currently classify employees of these companies as costs rather than assets. The Securities and Exchange Commission (SEC) is now considering proposals to require publicly listed companies to report spending on training and other human capital outlays. This may be a step toward moving the Financial Standards Accounting Board (FASB) to change accounting rules thereby giving companies the option of capitalizing and depreciating employee development as an investment, rather than expensing it as a cost that reduces earnings.
Employer job training is also growing as an answer to the unprecedented demographic meltdown. Over this decade 10,000 workers are retiring each year (approximately 3.6 million workers annually). This will continue into the 2030s. Up to 66 percent of job openings are to replace these retirees.
A recent National Federation of Independent Business survey reported that 42 percent of their
members (companies with 500 or fewer workers) had vacancies they cannot fill. The number-one problem facing members of the Association of General Contractors is the shortage of skilled labor. Contractors are reporting that this is causing them to turn down new construction projects.
In 2021 U.S. business experienced over 8 million job vacancies that resulted in a profit and productivity loss of over $1 trillion. By 2022 this had risen to over 12 million jobs and a $2 trillion loss. This trend seems to have abated somewhat this year. However, labor cost per unit rose to 6 percent in 2023. Average hourly earnings have increased 4.3 percent above last year as employers have raised wages to find qualified workers. Wage inflation is likely to continue unless businesses begin to enlarge the pool of skilled workers.
But where can this “hidden workforce” be found? According to U.S. Department of Labor reports, about 100 million Americans of working age are not participating in the labor force. Our research shows that at least 20 million of these workers have given up looking for employment because they lack some of the specific skills a job requires. They are capable of filling such job vacancies if employers offer the job training needed to mobilize these skilled workers.
As many other nations are dealing with a declining working-age population and significant skills shortages, it is important to develop all our own resources. There are hidden workers in our midst who could become productive employees if their skills are updated. Are U.S. businesses now beginning to realize that persistent job vacancies cost them more than it would to start entry-level skills training or to participate in community partnerships that are renewing local talent pipelines?
Edward E. Gordon is the founder and president of Imperial Consulting Corporation in Chicago. His firm’s clients have included companies of all sizes from small businesses to Fortune 500 corporations, U.S. government agencies, state governments, and professional/trade associations. He taught in higher education for 20 years and is the author of numerous books and articles. More information on his background can be found at www.imperialcorp. com. As a professional speaker, he is available to provide customized presentations on contemporary workforce issues.
Irish materials handling manufacturer Combilift has launched its first autonomous vehicle at the annual Fabtech trade show. Developed by Combilift’s dedicated automation team, the CombiAGT is a 4-wheel electric stand-on model, which is the world’s first autonomous dual operational sideloader for long loads. Celebrating 25 years in business, Combilift is acknowledged as being at the forefront of innovation in the global material handling sector with its wide range of customized products, and the CombiAGT harnesses the very latest smart technology to meet customer demands for driverless sideloader capability. These were driven in part by safety to eliminate the presence of personnel in aisles, consistency in handling procedures and to maximize order fulfilment, while also having a backup manual mode in case of power outages or internet disruptions.
www.combilift.com
Hangcha Forklift Canada, a provider of material handling equipment, announces the grand opening of its Mississauga warehouse on October 3, 2023. The spacious 30,000 sq ft facility is poised to make a substantial impact in Ontario and extend the Company’s reach throughout Canada. The new addition complements the existing warehouses in Vaudreuil-Dorion and Vancouver, allowing the Company to maintain an inventory of 550 units at any given time.
www.hcforkliftcanada.com
Wauseon Machine, Inc. announces an increase in the capacity and capability of its Aftermarket Services through the formal consolidation of McAlister Design and Automation (MDA) and WM. This merger will significantly streamline the process for customers to receive goods and services such as preventive maintenance, repair, training, support, and spare parts for automation equipment.
www.wauseonmachine.com
Toyota Material Handling was named a 2023 G75 Green Supply Chain Partner for leading the way in sustainability programs. The G75 list, curated annually by the editors of Inbound Logistics, recognizes 75 companies that go above and beyond to prioritize green initiatives and help global supply chains become more sustainable. “Being named a Green Supply Chain Partner is an honor for Toyota. One of our guiding principles is our commitment to creating a sustainable tomorrow. That commitment is part of our contribution to society, the communities we work in and our industry,” said Bill Finerty, Toyota Material Handling President and CEO. “Through our parent company, Toyota Industries Corporation, we have committed to contributing to Environmental Vision 2050, an ongoing company-wide leadership initiative to create a carbon-neutral society, a recycling-based company, harmony with nature and the promotion of environmental management.”
www.ARArental.org
AutoScheduler.AI
announces being named as a Top Choice for CSCMP’s Best Innovative Startup/Early-Stage Award. As a Top Choice, AutoScheduler is listed in the top five judges’ picks for the best companies that meet the award criteria showcasing innovation and great potential.
“It is truly an honor to be named to this prestigious list that recognizes innovation for delivering value. Our technology has deployed successfully to the largest CPGs, manufacturers and distributors, helping better meet on time, infull deliveries, reduce overall warehouse touches, and improve efficiencies.” ~
Keith Moore, Chief Executive Officer, AutoSchedulerwww.autoscheduler.ai
New orders of manufacturing technology totaled $353.9 million in July 2023, according to the latest U.S. Manufacturing Technology Orders Report published by AMT – The Association For Manufacturing Technology. July orders declined 12.4% from June 2023 but were only 10.5% lower than July 2022. Year-to-date orders reached $2.83 billion, 12.7% lower than this point last year.
www.amtonline.org
Rockwell Automation, Inc. has announced it has signed a definitive agreement to acquire Ontario, Canada-based Clearpath Robotics Inc., a provider in autonomous robotics for industrial applications. Autonomous mobile robots (AMRs) are the next frontier in industrial automation and transformation, and this acquisition will supercharge Rockwell’s lead in bringing the Connected Enterprise to life.
Transporting parts and materials to assembly lines and between manufacturing cells is one of the industry’s most complex and inefficient tasks, often resulting in production bottlenecks. Autonomous production logistics will transform the workflow throughout a manufacturing plant, enabling substantial reductions in cost and greater operational efficiency. Clearpath’s OTTO Motors Division offers AMRs and fleet management and navigation software, which dramatically increase throughput and reduce costs by ensuring components and subassemblies are in place when needed and by transporting finished goods to a truck or warehouse upon completion.
www.rockwellautomation.com
www.clearpathrobotics.com
Hess Auctioneers shared the sad news that one of its founding partners has passed away.
James “Jim” Germak, 72, of Elizabethtown, PA died on Saturday, September 2, 2023.
From an early age, Jim wanted to be a truck driver and started his trucking career at the age of eighteen. In 1982, Jim founded Jagtrux, Inc. of Marietta, Pa. Jim was also a founding partner of Hess Auctioneers in Marietta, Pa.
Jim graduated from Middletown Area High School in 1968. He was a member of PMTA, and served on the state board of directors and Lancaster PMTA Chapter. Jim loved spending time at his cabin and enjoyed various outdoor activities including hunting, boating, and driving his ranger. Jim had a passion for auctions and a “good deal.” The biggest enjoyment in his life was spending time with his children and grandchildren and sharing stories with friends.
www.hessauctioneers.com
Felling Trailers Inc., a manufacturer of industrial and commercial trailers, has appointed Jim Capobinaco as their Northeastern Regional Sales Manager. In his new role, Jim will be responsible for all sales development, activity, and dealer support within Maine, New Hampshire, Vermont, New York, Rhode Island, Massachusetts, New Jersey, Maryland, Delaware, Connecticut, Pennsylvania, and Washington D.C.
www.felling.com
Metalcraft announced a planned leadership transition reflecting the ongoing elevation of the employeeowned company’s dedicated team. Effective October 1, president Kyle Bermel will add Chief Executive Officer to his title, succeeding Steve Doerfler, who will become board chairman. This transition reflects Metalcraft’s commitment to a customer-centric team inspiring customers to unleash the power of their data with the most effective identification products.
Doerfler joined Metalcraft in 1990 and served as CEO since 2012. His leadership championed a culture that prioritizes employee well-being, nurturing a thriving work environment that propelled the Iowa-based manufacturer to a global leadership position in identification products. As Chairman, Steve will continue guiding Metalcraft University, an initiative empowering memberowners’ personal development, cultivating leadership potential, and enhancing skill sets to ensure Metalcraft remains at the forefront of ID technology.
Bermel brings a background in innovation and technology to his leadership responsibilities. He joined Metalcraft as an RFID engineer in 2012, becoming Metalcraft’s first Chief Operating Officer in 2019. Bermel led the development of subsidiaries ARK Business Systems and Inlay Innovation, offering software and the Iowa-based design and manufacture of custom RFID inlays, respectively.
www.idplate.com
Data provided by SalesLeads
SalesLeads announced the August 2023 results for the new planned capital project spending report for the Distribution and Supply Chain industry. The Firm tracks North American planned industrial capital project activity; including facility expansions, new plant construction and significant equipment modernization projects. Research confirms 198 new projects in the Distribution and Supply Chain sector compared to 196 in July 2023.
ONTARIO: Trucking company is investing $250 million for the construction of a 1.1 million sf warehouse and maintenance facility in BRADFORD, ON. They are currently seeking approval for the project. Completion is slated for 2026.
TENNESSEE: Global shipping company is planning to invest $220 million for the construction of a 1.3 million sf warehouse at 2776 Sprankel Ave. in MEMPHIS, TN. They are currently seeking approval for the project. Construction is expected to start in early 2024.
The following are selected highlights on new Distribution Center and Warehouse construction news.
Distribution and Supply Chain - By Project Type
• Distribution/Fulfillment Centers - 27 New Projects
• Industrial Warehouse - 173 New Projects
Distribution and Supply Chain - By Project Scope/Activity
• New Construction - 103 New Projects
• Expansion - 33 New Projects
• Renovations/Equipment Upgrades - 60 New Projects
• Closings - 6 New Projects
Distribution and Supply Chain - By Project Location (Top 5 States)
• Texas - 15
• California - 12
• Indiana - 11
Largest Planned Project
• Georgia - 13
• Florida - 11
During the month of August, our research team identified 10 new Distribution and Supply Chain facility construction projects with an estimated value of $100 million or more.
The largest project is owned by Maxeon Solar Technologies, who is planning to invest $1 billion for the construction of a 2-million sf manufacturing, warehouse. and office complex in ALBUQUERQUE, NM. Construction is expected to start in early 2024.
TEXAS: Beverage contract processing and packaging company is planning to invest $452 million for the construction of 2 processing and distribution facilities in FORT WORTH, TX. They are currently seeking approval for the project.
WASHINGTON: Biotechnology company is investing $215 million for the construction of a 269,000 SF processing, warehouse, and office facility at 215 Shuksan Way in EVERETT, WA. Completion is slated for late 2024.
KENTUCKY: Global logistics company is planning to invest $192 million for the expansion of their warehouse and maintenance hangar at CVG Airport in HEBRON, KY by 305,000 SF. They are currently seeking approval for the project.
TEXAS: Industrial equipment supplier is planning to invest $180 million for the construction of a distribution and office facility at 4894 Litsey Rd. in FORT WORTH, TX. They are currently seeking approval for the project.
PENNSYLVANIA: Port Authority is planning to invest $100 million for the construction of a 277,000 SF warehouse facility at 3060 S. 61st St. in PHILADELPHIA, PA. The project includes the construction of a 175,000 SF cold storage facility at their terminal in PHILADELPHIA, PA. They are currently seeking approval for the project.
RHODE ISLAND: Airport Authority is planning to invest $100 million for the construction of a 131,000-square-foot terminal complex and cargo facility at their airport in WARWICK, RI. They are currently seeking approval for the project. They will relocate their operations upon completion.
TEXAS: Waste recycling service provider is planning to invest $60 million for the construction of a 120,000 SF processing and warehouse facility in MCKINNEY, TX. They are currently seeking approval for the project. Completion is slated for 2026.
OHIO: Chemical supply chain service provider is planning to invest $50 million for the construction of a 122,000 SF warehouse at 3447 Clover Valley Rd. in JOHNSTOWN, OH. Construction is expected to start in early 2024, with completion slated for early 2025.
Since 1959, SalesLeads, based in Jacksonville, FL is a leader in delivering industrial capital project intelligence and prospecting services for sales and marketing teams to ensure a predictable and scalable pipeline.
SalesLeads announced the August 2023 results for the new planned capital project spending report for the Food and Beverage industry. The Firm tracks North American planned industrial capital project activity; including facility expansions, new plant construction and significant equipment modernization projects. Research confirms 77 new projects in the Food and Beverage sector as compared to 78 in July
MANITOBA: Meat processing company is planning to invest $53 million for the expansion and equipment upgrades on their processing facility in WINKLER, MB. They are currently seeking approval for the project.
OKLAHOMA: Membership-only grocery and retail chain is planning to invest $40 million for the renovation and equipment upgrades on a 300,000 SF distribution center on SW 29th Street in OKLAHOMA CITY, OK. Completion is slated for early 2024.
The following are selected highlights on new industrial construction news and project opportunities throughout North America.
Food and Beverage Project Type
• Processing Facilities - 46 New Projects
• Distribution and Industrial Warehouse - 35 New Projects
Food and Beverage Project Scope/Activity
• New Construction - 28 New Projects
• Expansion - 15 New Projects
• Renovations/Equipment Upgrades - 36 New Projects
• Plant Closing - 4 New Projects
Food and Beverage Project Location (Top 10 States)
• New York - 8
• Michigan - 5
• Indiana - 4
• Georgia - 3
• Missouri - 3
• Florida - 6
• California - 4
• Connecticut - 3
• Iowa - 3
• North Carolina - 3
During the month of August, our research team identified 3 new Food and Beverage facility construction projects with an estimated value of $100 million or more.
The largest project is owned by DrinkPAK, who is planning to invest $452 million for the construction of 2 processing and distribution facilities in FORT WORTH, TX. They are currently seeking approval for the project.
Beverage Projects
UTAH: Snack food MFR. is planning to invest $160 million for the expansion and equipment upgrades on their processing and warehouse facility in RICHMOND, UT. Completion is slated for late 2024.
CALIFORNIA: Grocery retailer is planning for the renovation and equipment upgrades on a recently leased 1.4 million sf distribution and office facility at 12434 Fourth Street in RANCHO
CUCAMONGA, CA. They will relocate their operations upon completion in Summer 2024.
CONNECTICUT: Retail and grocery store chain is planning for the construction of a 530,000 SF distribution center at 500 Groton Rd. in WINDSOR, CT. They are currently seeking approval for the project.
IOWA: Custom spray drying, blending, and packaging service provider is planning to invest $23 million for the expansion and equipment upgrades of their warehouse in OSAGE, IA. They have recently received approval for the project.
ONTARIO: Bakery company is planning to invest $18 million for the construction of a 105,000 SF processing and warehouse facility in SCARBOROUGH, ON. They have recently received approval for the project.
GEORGIA: Foodservice distributor and restaurant chain is planning for the renovation and equipment upgrades on a 100,000 SF warehouse and office facility at 2715 Brown Rd. in BUFORD, GA. They are currently seeking approval for the project. They will relocate their HQ operations upon completion in Spring 2024.
WASHINGTON: Produce company is planning for the expansion of their processing and warehouse facilities at 1064 Birch Bay in LYNDEN, WA by 65,000 SF. They have recently received approval for the project.
MISSOURI: Supplement MFR. is planning to invest $9 million for the renovation of their warehouse and office facility at 650 Assembly Pkwy. in FENTON, MO. They are currently seeking approval for the project.
Since 1959, IMI SalesLeads, based in Jacksonville, FL is a leader in delivering industrial capital project intelligence and prospecting services for sales and marketing teams to ensure a predictable and scalable pipeline. The Outsourced Prospecting Services, an extension to your sales team, is designed to drive growth with qualified meetings and appointments for your internal sales team. Visit us at salesleadsinc.com.
Data provided by SalesLeads
SalesLeads announced the August 2023 results for the new planned capital project spending report for the Industrial Manufacturing industry. The Firm tracks North American planned industrial capital project activity; including facility expansions, new plant construction and significant equipment modernization projects. Research confirms 151 new projects in August as compared to 140 in July, an increase in the Industrial Manufacturing sector.
MANITOBA: Biotechnology company is planning to invest $1 billion for the construction of a processing facility in MANITOBA. They are currently seeking approval for the project.
NEW MEXICO: Solar panel MFR. is planning to invest $1 billion for the construction of a 2-million SF manufacturing, warehouse. and office complex in ALBUQUERQUE, NM. Construction is expected to start in early 2024.
The following are selected highlights on new Industrial Manufacturing industry construction news.
Industrial Manufacturing - By Project Type
• Manufacturing/Production Facilities - 135 New Projects
• Distribution and Industrial Warehouse - 74 New Projects
Industrial Manufacturing - By Project Scope/Activity
• New Construction - 57 New Projects
• Expansion - 34 New Projects
• Renovations/Equipment Upgrades - 53 New Projects
• Plant Closings - 20 New Projects
Industrial Manufacturing - By Project Location (Top 10 States)
• Michigan - 10
• Indiana - 8
• Ohio - 8
• Tennessee - 7
• Georgia - 6
Largest Planned Project
• New York - 10
• North Carolina - 8
• Arizona - 7
• Florida - 6
• Texas - 6
During the month of August, our research team identified 20 new Industrial Manufacturing facility construction projects with an estimated value of $100 million or more.
The largest project is owned by Gotion, Inc., who is planning to invest $2 billion for the construction of an EV battery manufacturing facility in MANTENO, IL. They are currently seeking approval for the project.
LOUISIANA: Solar panel MFR. is planning to invest $1 billion for the construction of a manufacturing and warehouse facility at Acadiana Regional Airport in NEW IBERIA, LA. They have recently received approval for the project. Completion is slated for Spring 2026.
FLORIDA: Defense contractor is planning to invest $294 million for a 198,000 SF expansion and equipment upgrades on their manufacturing facility at 2400 Palm Bay Rd. NE in PALM BAY, FL. They are currently seeking approval for the project.
PENNSYLVANIA: Biotechnology company is planning to invest $260 million for the construction of an 80,000 SF processing, laboratory, and office campus in PHILADELPHIA, PA. The project includes the construction of a 150,000 sf co-working biotechnology and office facility at the site. They are currently seeking approval for the project.
MISSISSIPPI: Wood pellet MFR. is planning to invest $250 million for the construction of a manufacturing facility in BOND, MS. They have recently received approval for the project. Completion is slated for Fall 2025.
TENNESSEE: Automotive component MFR. is planning to invest $170 million for the renovation and equipment upgrades on a manufacturing facility in LOUDON, TN. They are currently seeking approval for the project.
MICHIGAN: Automotive parts MFR. is planning to invest $170 million for the renovation and equipment upgrades on a recently pre-leased 200,000 sf manufacturing facility in GRAND BLANC, MI. The project includes establishing a 50,000 SF testing and research facility and they are currently seeking a site in the FLINT, MI area.
MINNESOTA: Medical device MFR. is planning to invest $170 million for the construction of a 400,000 SF laboratory, processing, training, and office campus on 73rd Place in MAPLE GROVE, MN. They are currently seeking approval for the project. The site will allow for a future 150,000 SF expansion.
KENTUCKY: Automotive parts MFR. is planning to invest $131 million for a 320,000 SF expansion and equipment upgrades on their manufacturing facility in BARDSTOWN, KY. They have recently received approval for the project. Completion is slated for early Fall 2024.
Since 1959, SalesLeads, based in Jacksonville, FL is a leader in delivering industrial capital project intelligence and prospecting services for sales and marketing teams to ensure a predictable and scalable pipeline.
Application specific cut standards remain the only way to specify cutresistant protective gloves; however, A4 cut resistance has quickly become the de facto minimum standard for work gloves used in many applications. Foremen and plant managers alike trust its performance and feel confident putting their people in it when setting out for another hard day at work. Brass Knuckle® SmartCut™ (BKCR4420) offers this highly desirable A4 cut resistance PLUS a whole lot more.
www.brassknuckleprotection.com
Mitsubishi Logisnext
launches new UniCarriers® Forklift
Mitsubishi Logisnext Americas, the exclusive manufacturer and provider of UniCarriers Forklifts across North, Central and South America, announced the launch of the new cutting-edge SCX N2 Series of Electric Stand-up Counterbalanced Lift Trucks. This addition further enhances the company’s comprehensive portfolio of warehouse products, offering customers an array of benefits that redefine efficiency and flexibility in material handling operations.
www.logisnextamericas.com
HC Forklift America Corporation (HCFA) has announced the new XE Series Electric Lithium-Ion Pneumatic Forklift with a 4,000-7,600lb capacity. The new XE Series of lithium-ion pneumatic forklifts were designed from the ground up to provide operators with a true lithium-ion alternative to I.C. pneumatic forklifts. Because of this, the integrated 80V lithiumion forklift features lift speeds, travel speeds, gradeability, ground clearance, and a competitive price point that rivals comparable I.C. pneumatic forklifts. www.ozliftingproducts.com
Sentry Protection Products introduces the next generation of collision warning systems – the Collision Sentry® MultiZone. Like earlier models of the Collision Sentry, the Multi-Zone is designed to create a safer work environment by reducing or eliminating blind spot collisions. The difference is the Multi-Zone expands the possibilities for preventing collisions in multiple areas, not just corner intersections.
www.sentrypro.com
Big Joe Forklifts in partnership with Thoro.ai continues to rapidly advance the features on their flagship AMR and invest in key staff to help deliver easy to deploy automation for their customers. At Pack Expo, visitors could see and experience the latest Big Joe Pallet Mover AMR first-hand including several new features such as dynamic on-the-fly rerouting, onboard viewable maps and configurable zone rules to further enhance productivity, ease of operation and control for users. Additionally, Big Joe will be showcasing other unique vehicles in its standard lineup that are ideal for supporting packaging operations in manufacturing, warehousing or logistics environments.
www.bigjoeforklifts.com
The choice is yours. Collision protection where you need it.
ROPAX Roto-Compactors from Epax Systems compact recyclable material and waste at the source where it is generated. These industrial grade machines use a rotating drum with metal teeth to tear, rip, shred and compact a wide variety of items including cardboard boxes, fruit and vegetable crates, plastic waste, packing filler (polystyrene), and more. As the drum rotates it swivels left and right while keeping items under constant pressure to ensure maximum compaction.
www.epaxsystems.com
LEDtronics® Inc. announces the latest product in its line of Tunable LED Post Top Lamps with even, omnidirectional lighting that offers energy savings of up to 85 percent over MH and HPS counterparts. Additional features multi-wattage and multi-color temperature versatility with the ability to choose from three different CCTs — 3000K Warm White, 4000K Natural White and 5000K Pure White, and variable wattage options of 45, 54 or 63 Watts.
www.ledtronics.com
Columbia/Okura LLC just announced the miniPAL+ ™, a new collaborative solution utilizing Universal Robot’s UR20 cobot arm, providing a 44 lbs. (20kg) lifting capacity. This new palletizing solution enables handling heavy payloads at higher rates than previous collaborative systems and with flexible tooling allow for multi-pick options. The design features a 10’ x 11’ footprint, and an intuitive pattern building software by Rocketfarm for ease of use.
www.columbiaokura.com
CASSEL Inspection highlights the breadth and depth of the company’s line of inspection products, including configurable and customizable solutions in metal detection, X-ray inspection, and checkweighers. The inspection system highlights include the latest technology advancements in detection capabilities – the Shark MultiSense Metal Detector.
www.cassel-inspection.com
The Qimarox Highrunner HR9 is the only solution in the market that comes complete with a unique pattern generator allowing the system to stack boxes of almost any size on pallets at high speed without specially trained technicians generating a fresh pallet pattern for each new product. CKF Systems is the sole Silver Partner for Qimarox in the UK and has a wealth of experience integrating Qimarox product lifts and layer palletisers. The manual unloading of ‘loose loaded’ containers is physically demanding, time-consuming, and unattractive work. The removal process from the containers one by one and then manually stacked onto pallets can lead to damaged packaging and goods if stacked carelessly or dropped. www.signode.com