
2 minute read
Ground support for deep-level mining operations A practical alternative to resin grouted rockbolting
Ground support systems have been used for over a century in mines across the world. The use of rockbolts has been documented as early as the late 19th century, where reinforced steel was used to stabilise rock walls in mines.
The technology has evolved, as mine operations tunnel deeper, requiring new support for different ground conditions. In such environments, effective ground support equipment is required to reinforce the rock around excavated tunnels, to facilitate safer and more efficient operations, and successful installation is critical to ensuring the capacity of the rock reinforcement element.
Advertisement
The traditional installation of resin grouted rockbolts requires a support hole to be pre-drilled followed by the installation of the resin capsule. The rockbolt is then spun into the grout, mixing the resin completely.
Challenges when installing resin capsule grouted rockbolt
Epiroc Ground Support has extensive experience with testing the integrity of resin grouting solutions in varied environments. The research has noted the typical challenges facing miners installing resin capsule grouted rockbolts as follows:
• Ensuring a quality installation, the diameter of the support hole, the rate of rotation, rate of insertion and spin time must be monitored to ensure an effective installation. Mistakes can prove costly, as any deviation from the manufacturers specifications may result in a reduction of resin strength, and failure of the support system.
• In highly stressed, poor ground conditions, the presence of fractures, shear features and altered rock can lead to unravelling of the support hole, resulting in blockages preventing the installation of the resin capsules. Efficiency is then affected, as support holes may need to be re-drilled, leading to oversized holes, increased installation times and poor installation quality.
• Lastly, the resin within the capsules is fixed, therefore variations in hole diameter and resin losses into voids may cause a failure to achieve a full column bond.
The solution
Having observed the challenges that impact the integrity of the rock reinforcement system when using resin capsule grouted rockbolts, the experts at Weber Mining and Tunnelling and Epiroc partnered up to develop a high strength polyurea silicate resin, Potentia® Thixo. Potentia® Thixo, in combination with the high performance Boltec and post-grouted rockbolts developed by Epiroc, offers an effective solution to overcome the challenges faced with capsule resin installation.
Achieve full column
This installation process is more resilient to changes in the rock mass. When the rockbolt is inserted into the predrilled bore hole and the pumpable resin is then injected through the rockbolt filling the bore hole from the back to the collar. Post grouting ensures that a full column is achieved as resin is injected through the bolt until resin is observed at the perimeter of the plate. The thixotropic nature of the resin ensures the resin remains in the borehole whilst rapidly curing to strengths in excess of 35 MPa.
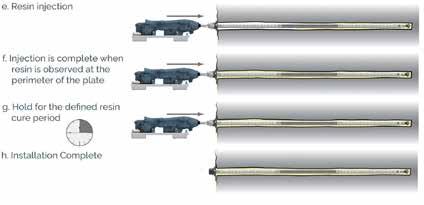
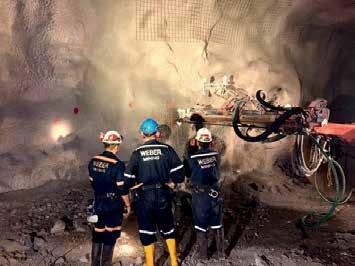

Easy to transpor t
Additionally, the resin and catalyst, which are the two components of Potentia® Thixo resin are stored and transported in IBC.
Shelf life
The 2-year shelf life is not affected by changes in temperature, which simplify logistics and supply chain.
Quality
The quality of the mixed Potentia® Thixo is auditable and assured as the two components are mixed in a 1:1 ratio by a digitally controlled pumping system on the Boltec. This ensures the quality of the resin mixture is established prior to injection into the rockbolt and remains consistent through varying ground conditions. With a setting time that can be tailored from 35 seconds for bolting applications to 900 seconds for cable bolting applications.
